概要
近年では物流倉庫の中に部品加工や食品加工などの工場を設置した、所謂、PDC型の物流倉庫が増加しています。PDC型物流倉庫は、企業が自社の配送倉庫や工場を持つかわりに、物流業者の所有する物流倉庫内に工場を設置し、配送や出荷は物流会社にアウトソーシングし、在庫は物流倉庫内に保管する形態となります。このような場合、倉庫への入出荷作業のタイミングは入居企業ではなく、大家である物流企業の都合で決定されることが多くなります。契約次第ですが、本来、決まっている時刻以外に入出荷を行おうとすれば、大きな追加費用が発生することが考えられ、決められた時刻に行われる入荷・出荷に対応することが、コスト削減には重要なファクターとなります。また、故障や事故などの不測の事態により、計画に遅延が生じた場合の復旧作業も重要です。今回はassimeeを使って、入出荷時刻に対応したスケジュールや人員配置の確認、予期せぬ故障でスケジュールが遅延した場合の出荷計画の立て直しをシミュレーションと最適化を使って行う方法について解説します。
モデル
今回作成するモデルは下図の通りとなります。

モデルの前提
モデルを作成するにあたって以下の条件を仮定します。
- PDC型倉庫は8時から18時まで稼働(10時間、600分)
- 倉庫内で部品を組立て、製品を出荷
- 毎日の入荷数と出荷数は同数
- 外部から倉庫への入荷時刻は9時と13時
- 倉庫から外部への出荷時刻は19時(18時までに出荷のための作業を終える)
- 加工やデバンニング、バンニングなど倉庫内作業の人員配置は前日に決定
- 簡単のため人員シフトや昼休憩、倉庫内の部品や製品在庫は考えない
モデルの作成
各プロセスを配置し、設定して行きます。
入荷プロセス:
プロセス名を「000入荷」へ変更、
入荷数を倉庫の稼働時間(8時から18時)と「部品」の入荷時間(9時と13時)から以下のように考えて、図のように設定します。
- 0-60:0個
- 60-120:500個
- 120-180:0個
- 180-240:0個
- 240-300:0個
- 300-360:500個
- 360-420:0個
- 420-480:0個
- 480-540:0個
- 540-600:0個
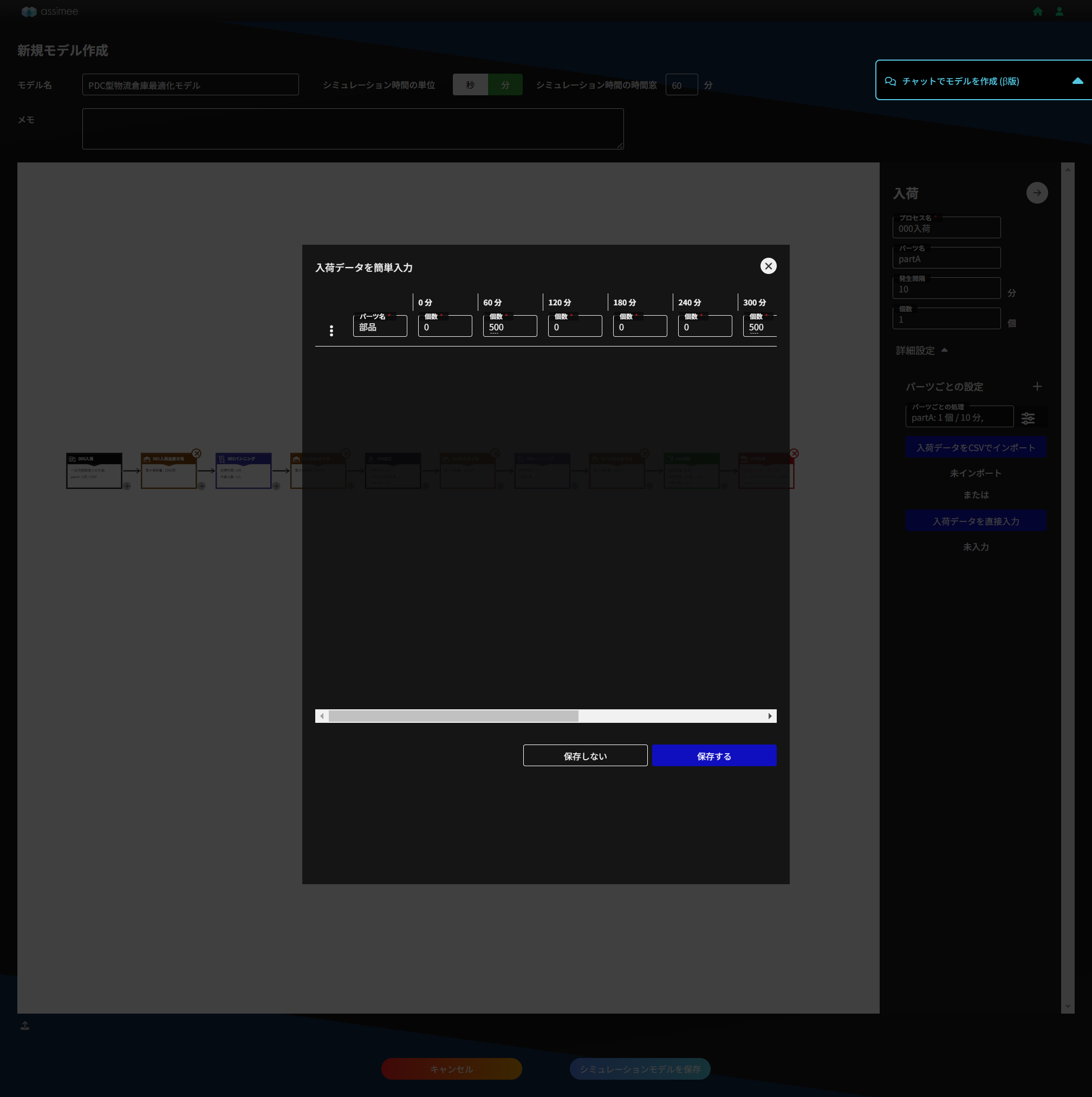
置き場プロセス:
プロセス名を「001入荷品置き場」へ変更、容量を「1000個」と設定
作業プロセス:
プロセス名を「002デバンニング」へ変更、処理時間を「10分」、作業人数を「1人」と設定
置き場プロセス:
プロセス名を「003部品置き場」へ変更、容量を「1000個」と設定
加工プロセス:
プロセス名を「004加工」へ変更、処理時間を「10分」、作業人数を「1人」と設定、
対象パーツ名称を「部品」、個数を「1個」、
出力パーツ名称を「製品」、個数を「1個」と設定
置き場プロセス:
プロセス名を「005製品倉庫」へ変更、容量を「1000個」と設定
作業プロセス:
プロセス名を「006バンニング」へ変更、処理時間を「10分」、作業人数を「1人」と設定
置き場プロセス:
プロセス名を「007出荷品倉庫」へ変更、容量を「1000個」と設定
運搬プロセス(人):
プロセス名を「008運搬」へ変更、積荷容量を「50個」、処理時間を「5分」、作業人数を「20人」と設定
出荷プロセス:
プロセス名を「009出荷」へ変更
シミュレーションと入出荷スケジュールの確認
シミュレーションは以下のような結果となりました。
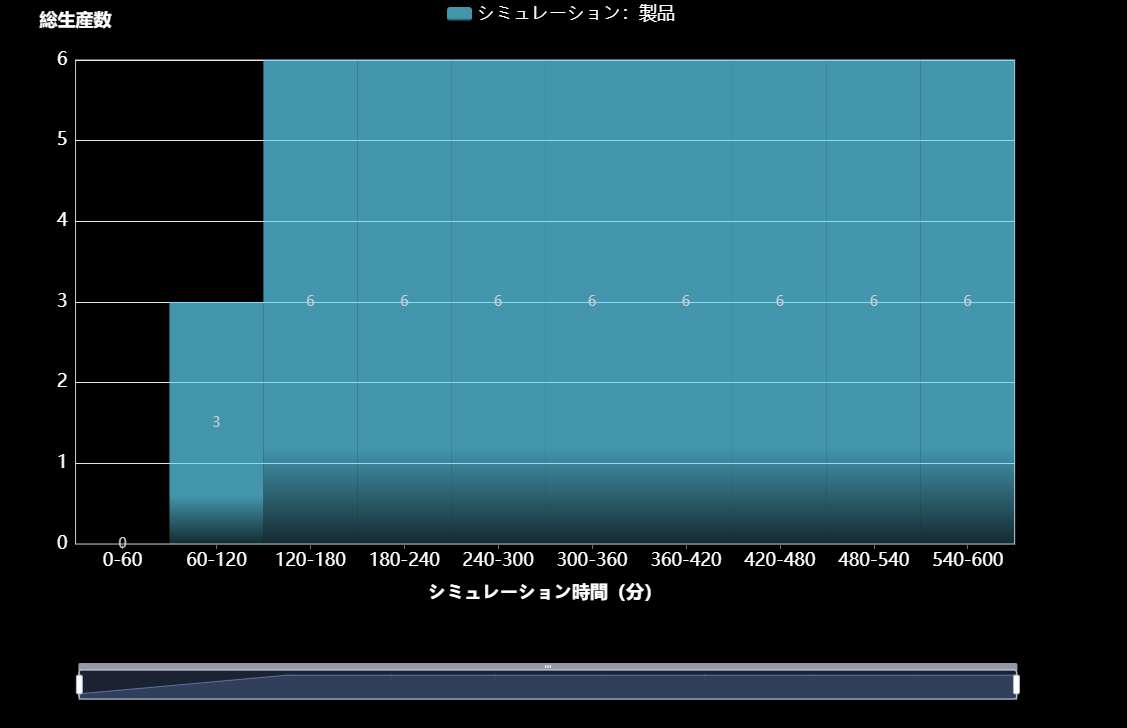
次に「002デバンニング」、「004加工」、「006バンニング」の人員配置を最適化で決めていきましょう。まず、その日の出荷目標を以下のように決め、「出荷データの直接入力」を使って設定します。
- 0-60:0個(入荷前の為)
- 60-120:110個
- 120-180:110個
- 180-240:110個
- 240-300:110個
- 300-360:120個
- 360-420:120個
- 420-480:120個
- 480-540:120個
- 540-600:120個
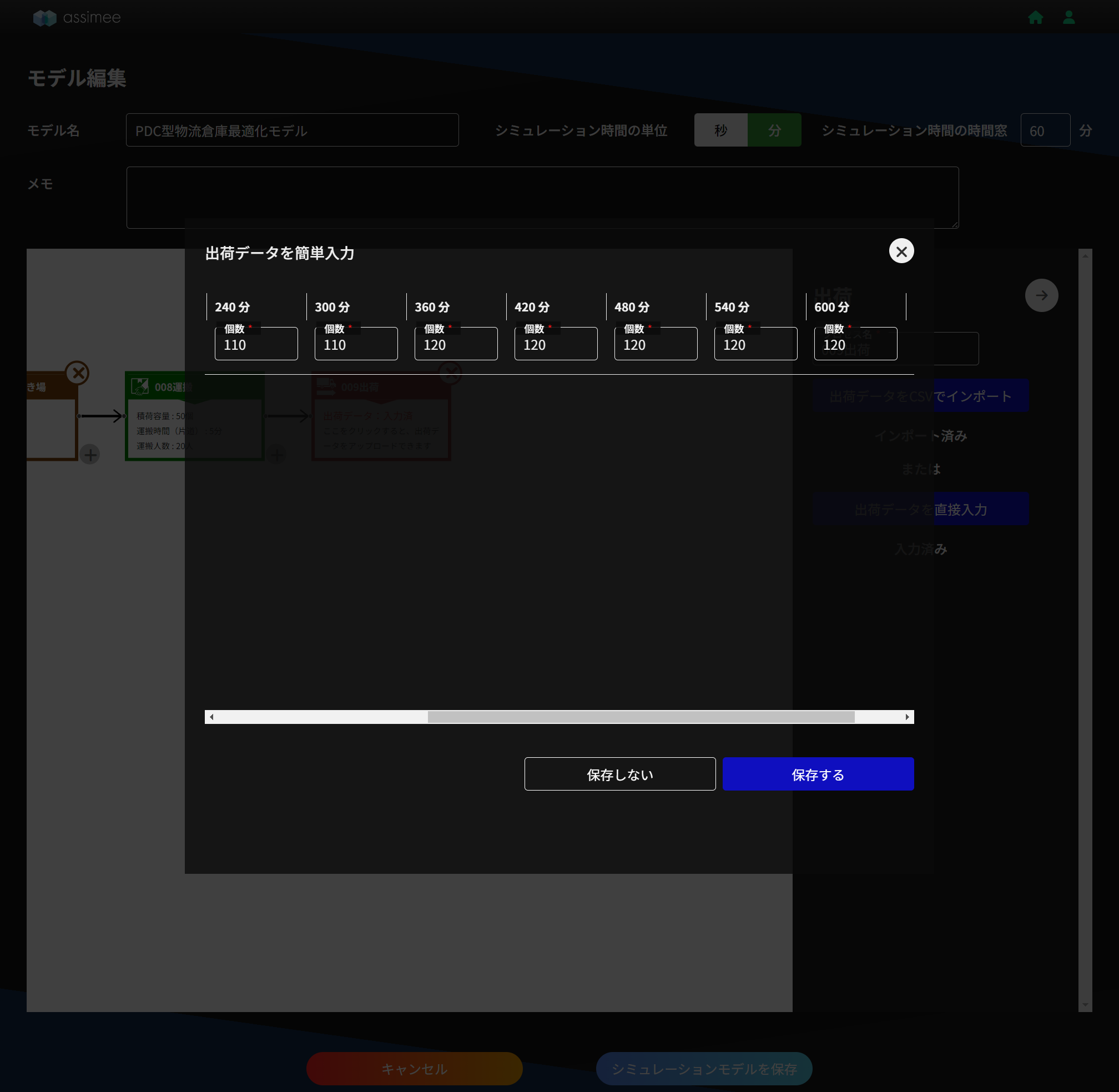
出荷目標を入力し、モデルの名前を「PDC型物流倉庫最適化モデル」として保存します。次に600分の時間でシミュレーションすると結果が以下のようになります。

この出荷目標を達成するように作業人数を最適化します。人員配置最適化タブを選び最適化を行います。
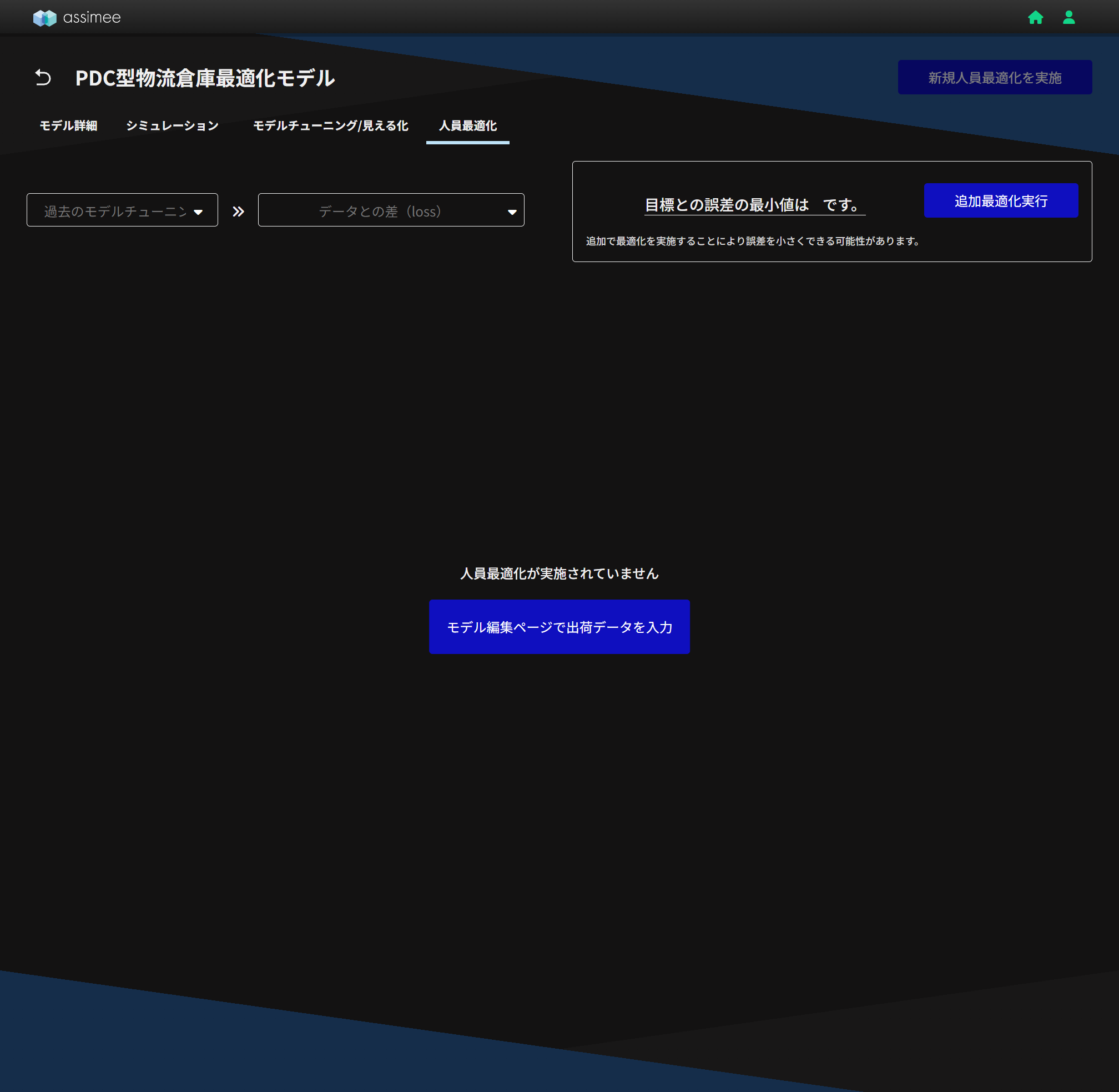
「002デバンニング」、「004加工」、「006バンニング」の作業人数の部分にチェックを入れ、上限値と下限値を以下の図のように設定して「モデルチューニング実行」ボタンを押して最適化を行います。
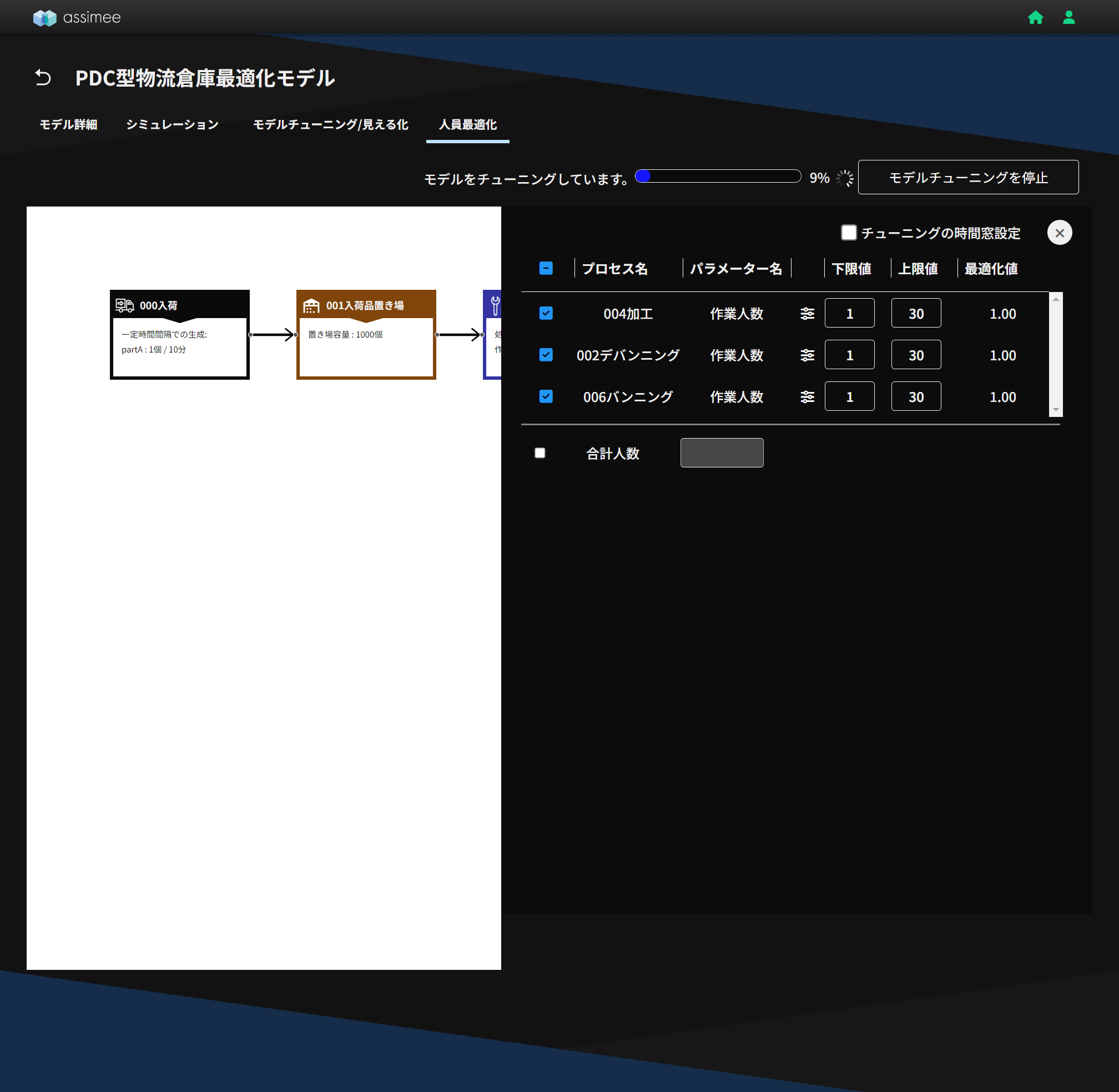
最適化の結果以下の図が得られます。
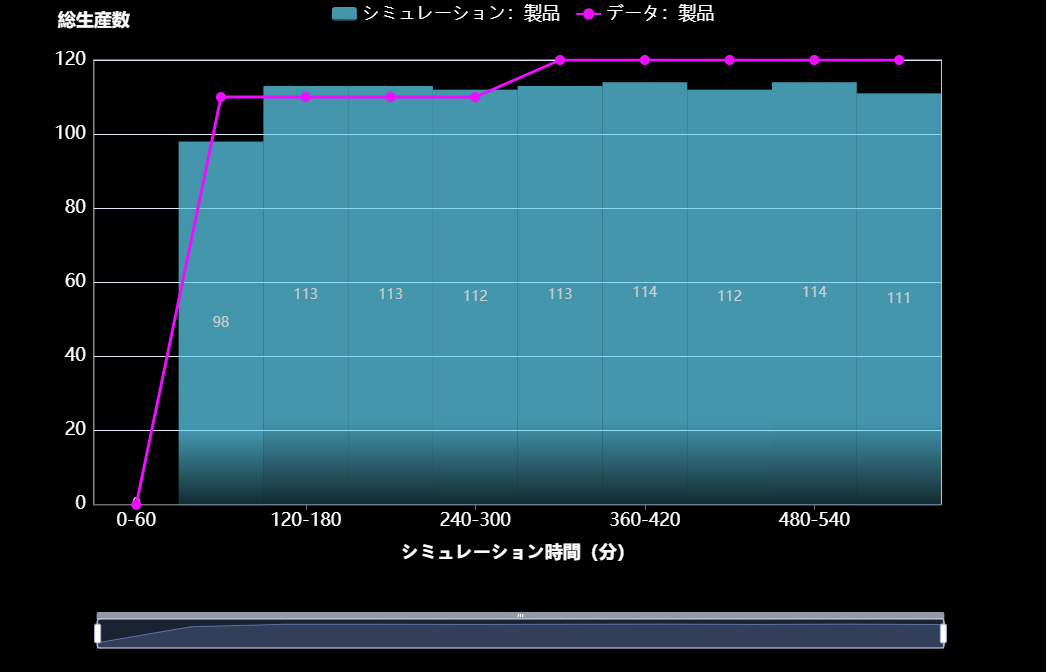
「009出荷」のパーツ数推移を確認すると確かに1000個出荷されていることが分かります。
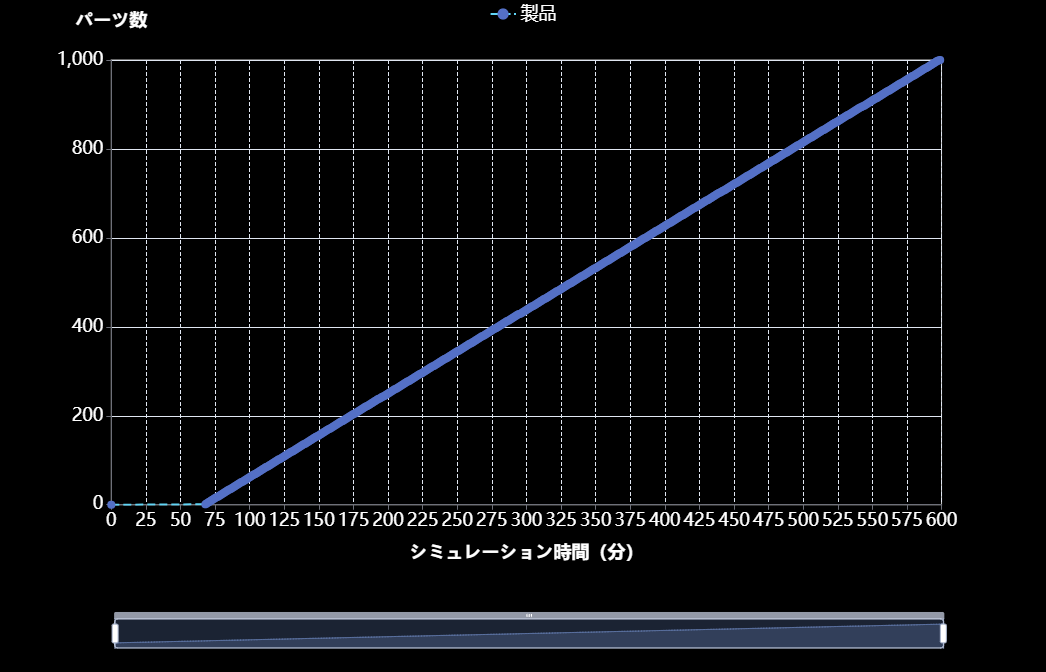
この結果、作業人数を以下のように設定すれば、物流倉庫の出荷時間である19時に十分な余裕がある形で、加工と出荷作業が終了することが分かりました。*最適化には乱数が使用されているため、結果が一致しないことがあります。
- 002デバンニング:1人→29.09人
- 004加工:1人→18.82人
- 006バンニング:1人→18.89人
次に、イレギュラーな故障を発生させて出荷に遅延を起こし、翌日の出荷スケジュールを立て直すという想定で最適化を行ってみましょう。
故障の発生と修正計画の立案
故障の発生と現状の確認
ここでは、倉庫内の加工プロセスに故障を発生させ影響を分析します。
ダッシュボードからモデルをコピーします。
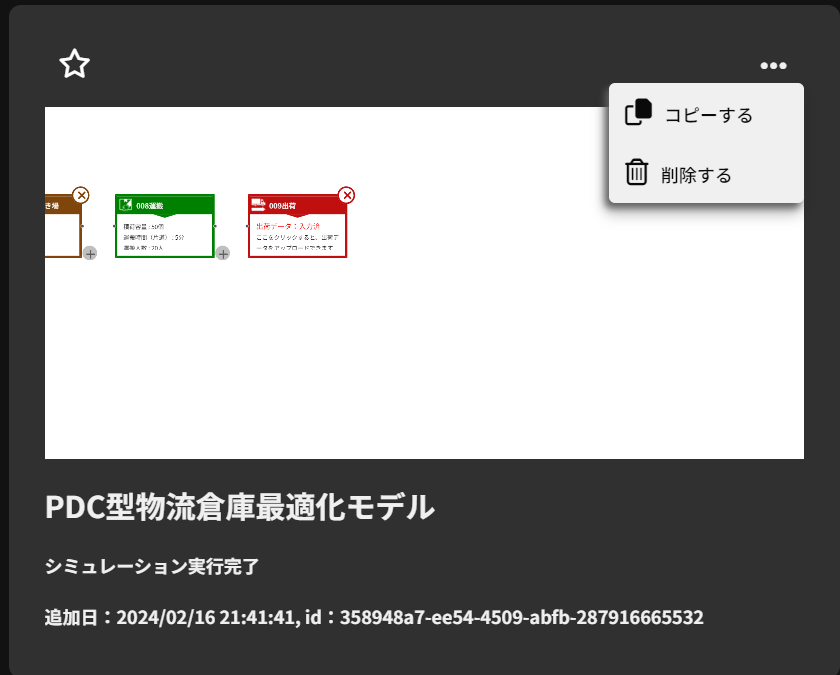
次に「002デバンニング」、「004加工」、「006バンニング」の作業人数を以下のように設定します。
- 002デバンニング:29人
- 004加工:19人
- 006バンニング:19人
また、故障を再現するため「004加工」の詳細設定から故障と修理のパラメーターを以下のように設定します。
- 故障時間(加工プロセス稼働から故障までの時間):300分
- 修理時間:240分
- 修理グループ:作業効率を1、作業人数を1
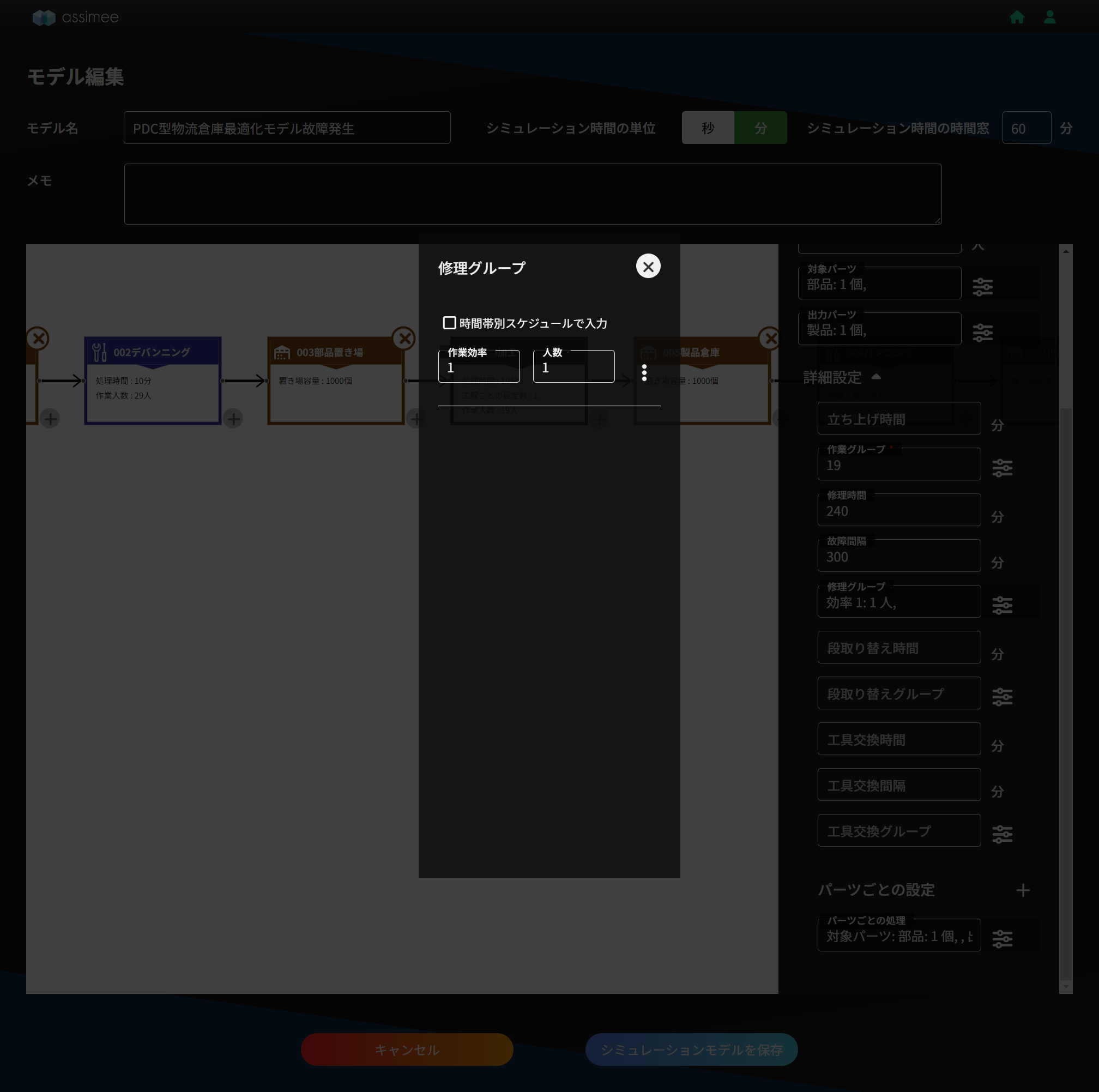
モデルを最初とは別名で保存(ここではPDC型物流倉庫最適化モデル故障発生としました)し、シミュレーションをやり直すと現状を確認することができます。
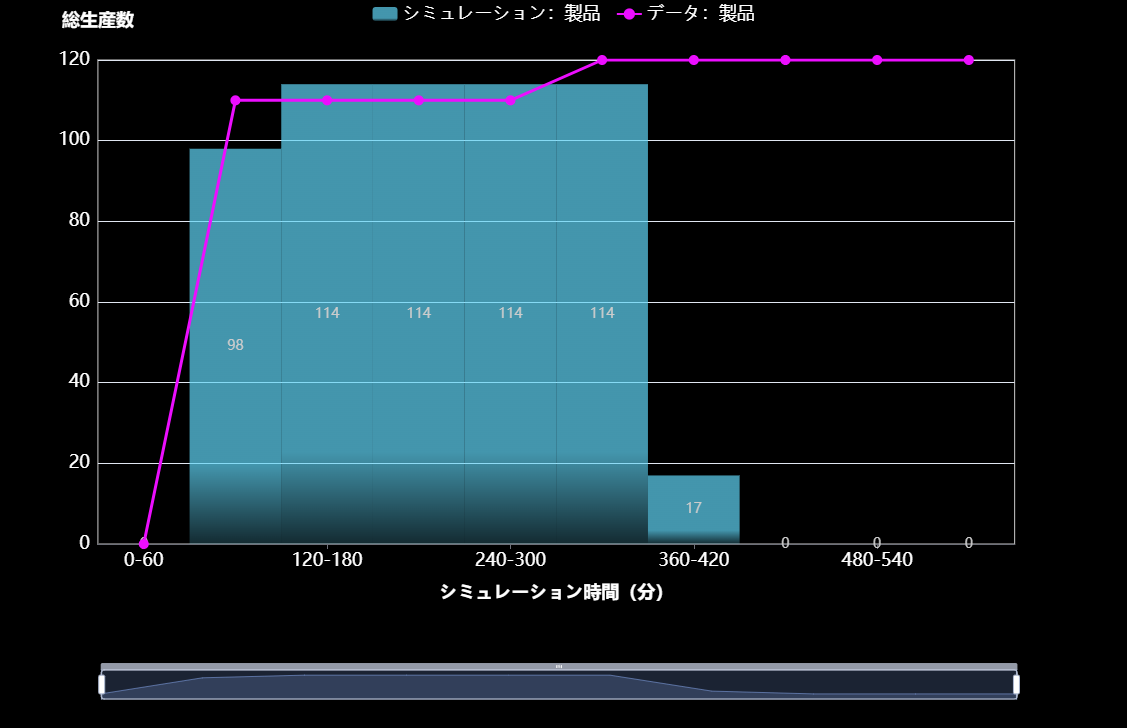
倉庫の稼働(シミュレーション開始)から6時間、部品の入荷から5時間経った頃で故障が発生し、その後は倉庫の稼働が終了するまで修理が終わらなかったことが分かります。
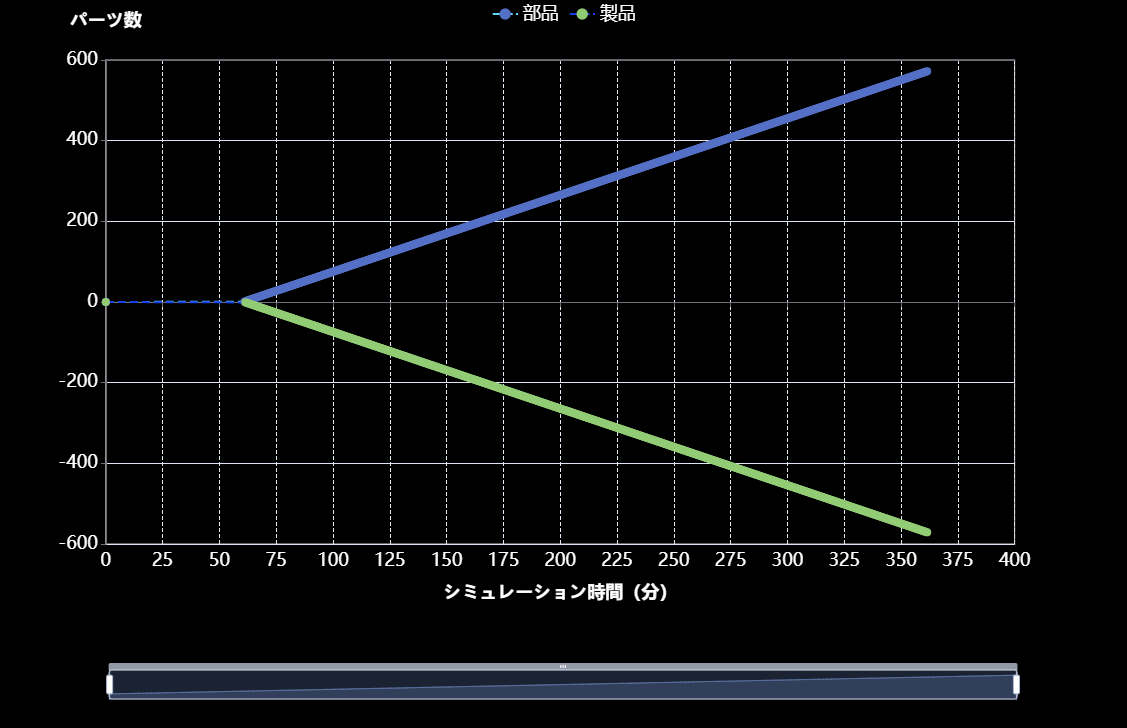
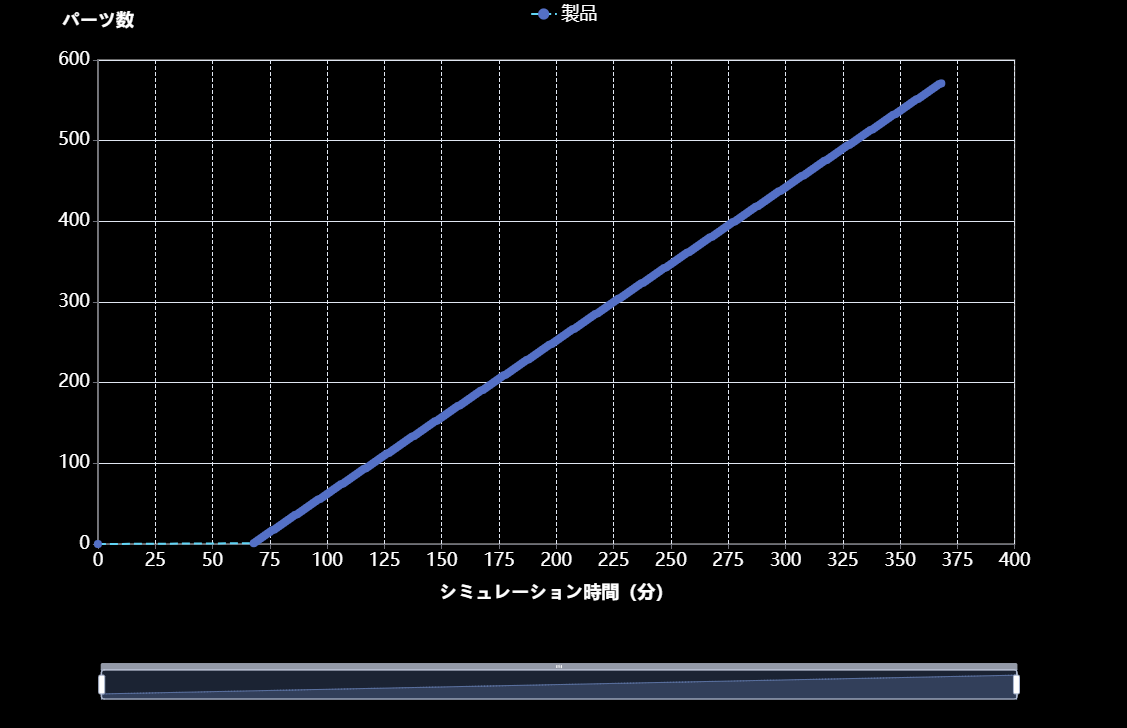
また、「004加工」のパーツ数推移のグラフから、シミュレーション開始から362分経ち571個加工したところで故障が発生し、「009出荷」のパーツ数推移から、故障の前後で出荷できる個数は以下のように変動しました。
- 故障設定前:1000個
- 故障設定後:571個
この結果、出荷できない製品が429個発生し、出荷計画に大きな遅延が生じました。これを取り戻すためには修理が終了した翌日以降の加工を増やす必要があります。しかし、人員手配を行うには時限があるため、なるべく早く関連部署に連絡をする必要があります。このような時にassimeeが使えれば、故障が起きた時点で即シミュレーションを行なって翌日の人員配置を計画することが可能です。それでは設定と最適化を行なって人員配置を決めてみましょう。
翌日の出荷計画の最適化
ダッシュボードから再度モデルをコピーし、入荷したものの、故障発生で使われず残った「部品」429個を、「003部品置き場」に初期仕掛かりとして配置します。
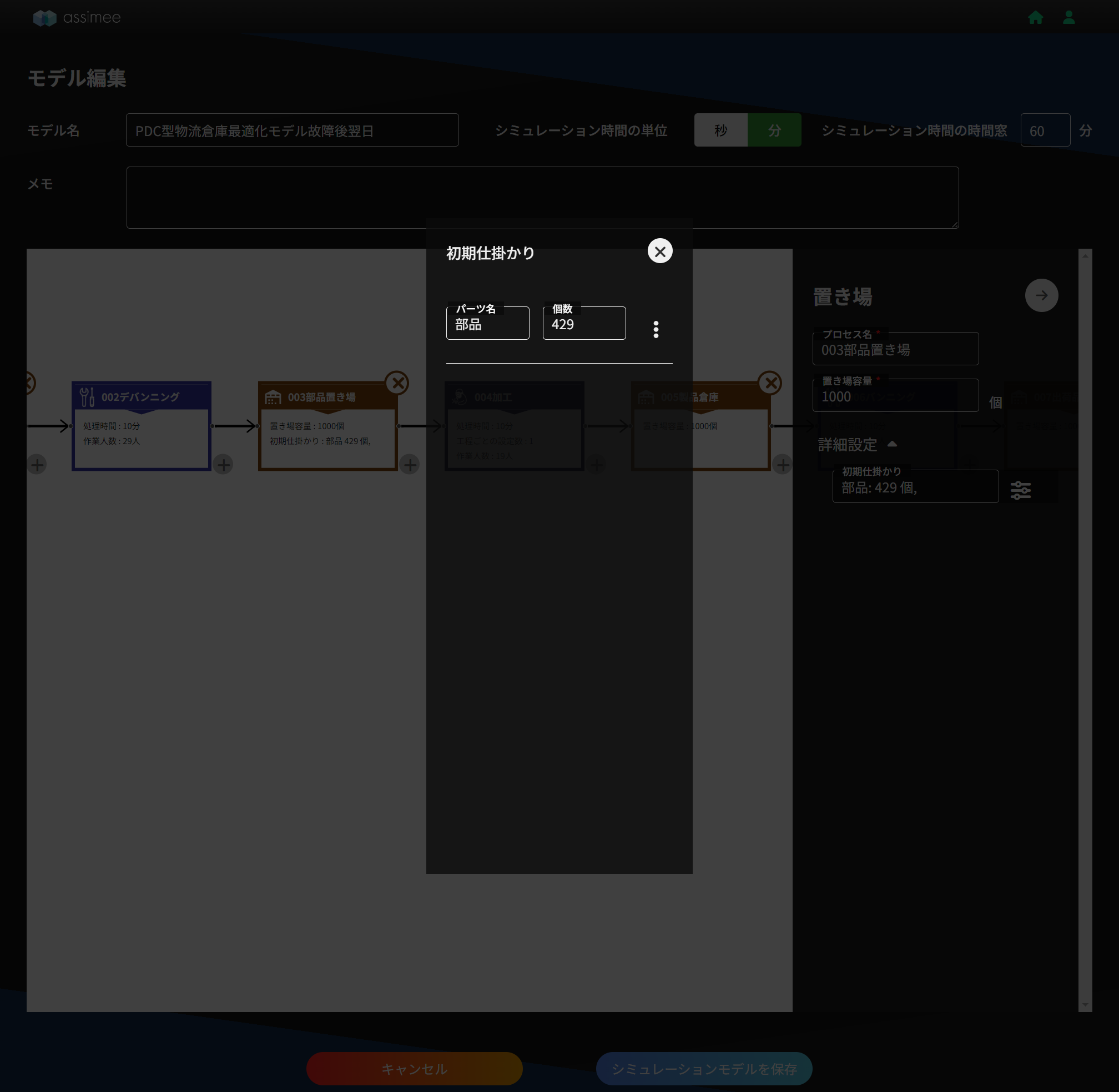
また、新しい出荷目標を編集画面から以下のように修正します。前回と異なり既に仕掛かり品があるため倉庫稼働直後から加工を行うことが可能となります。*この時、「004加工」の故障に関するパラメーター(修理時間と故障間隔)の設定を削除することを忘れないでください。assimeeの仕様のため、一旦「009出荷」を削除し、再配置してください。「002デバンニング」の作業人数、「004加工」の作業人数と修理グループ、「006バンニング」の作業人数はそのままにします。
- 0-60:150個(前回と違って仕掛かりがある為)
- 60-120:150個
- 120-180:150個
- 180-240:150個
- 240-300:150個
- 300-360:150個
- 360-420:150個
- 420-480:150個
- 480-540:150個
- 540-600:150個
パラメーターを設定したら、モデルを再度別名で保存(ここではPDC型物流倉庫最適化モデル故障発生としました)し、シミュレーション結果に新しい目標値に変わったグラフが表示されたのを確認します。当然ながら新しい出荷目標を出荷が下回っていることが分かります。
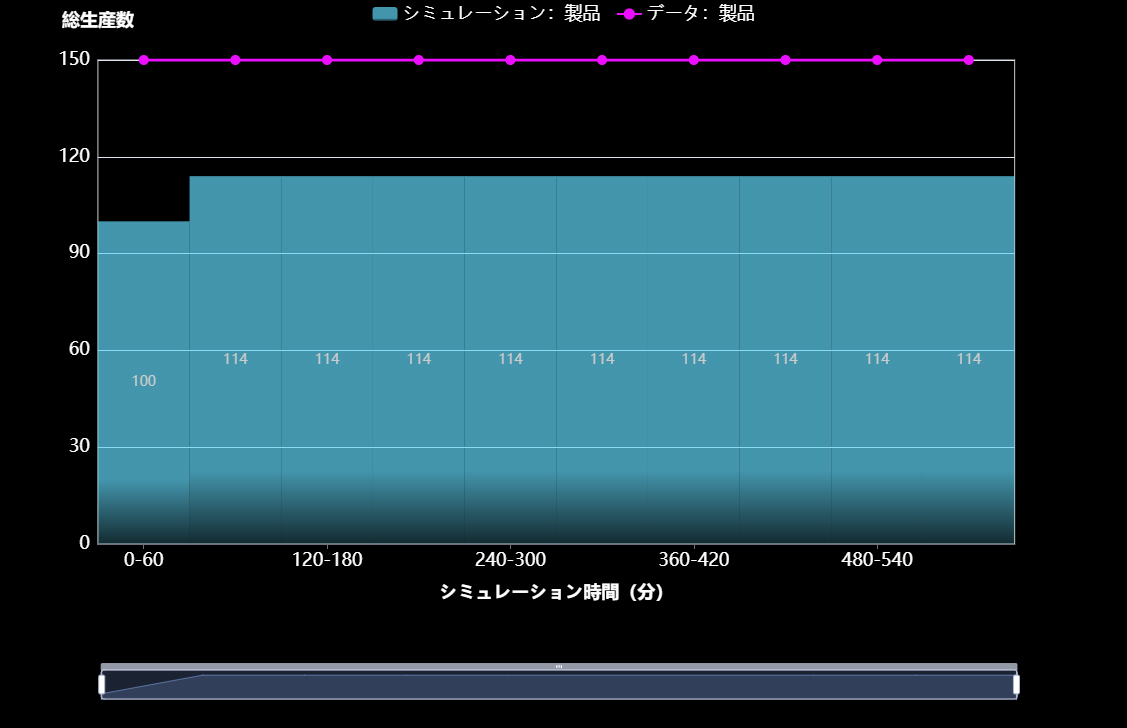
人員最適化タブから再度最適化を行いします。前回と同様にパラメーターの上限値と下限値を以下のように設定します。修理人数が表示されていますが、無視してください。
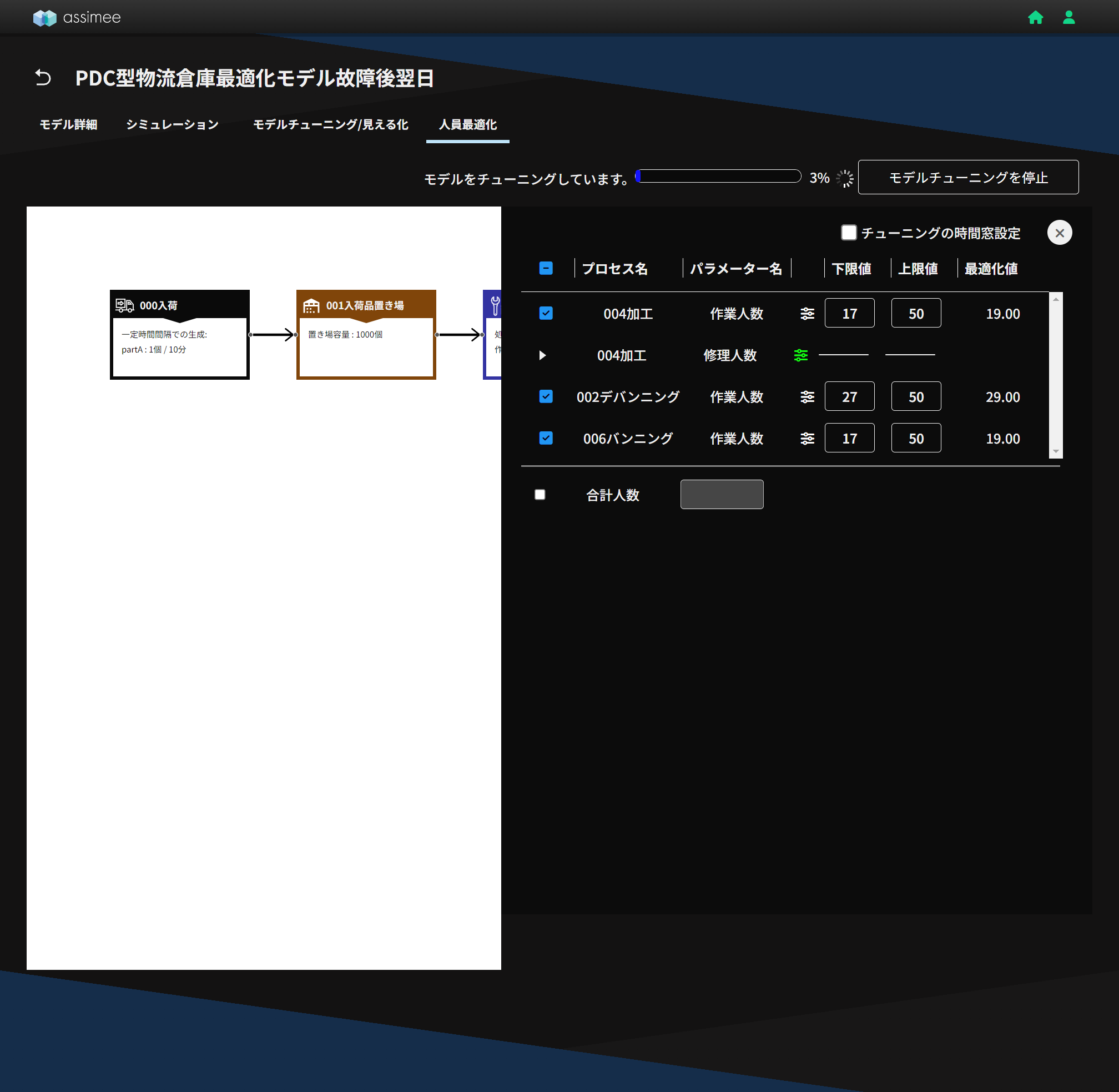
最適化が終わると以下のような図が表示されます。*最適化には乱数が使用されているため、結果が一致しないことがあります。
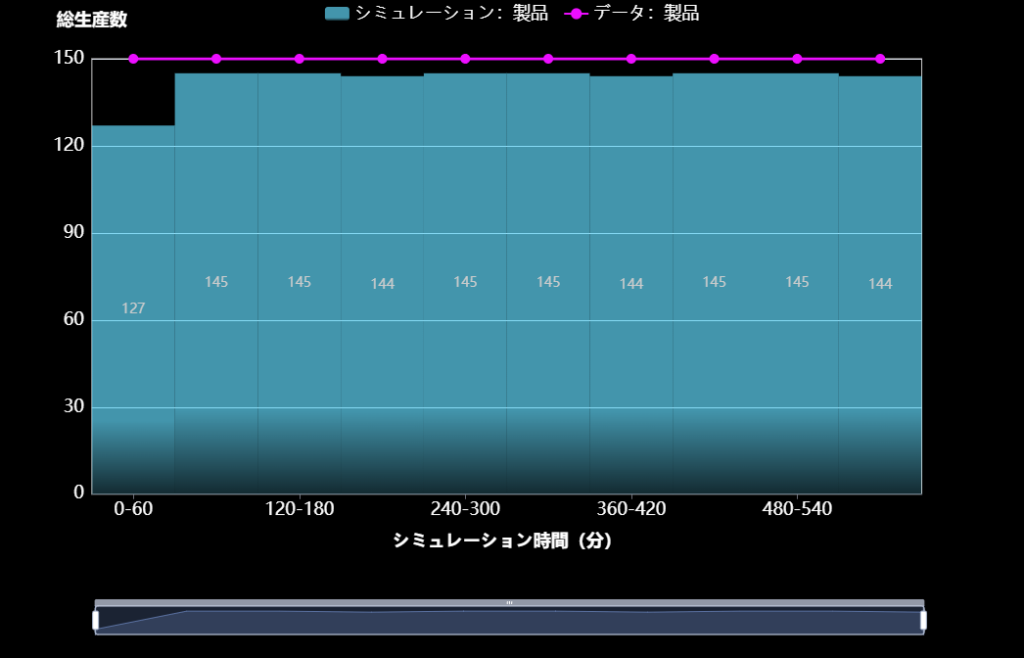
また、「009出荷」のパーツ数推移を確認すると以下の通りになります。
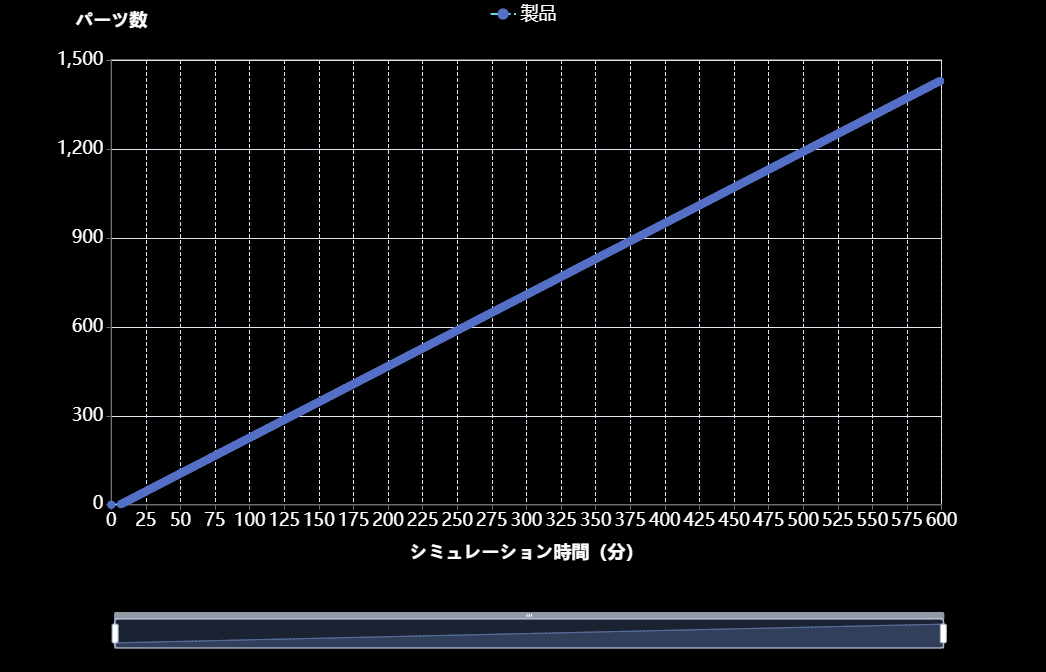
これらの結果から、600分後までに目標数である1429個が出荷されており、人員を以下のように増員すれば、故障翌日の作業で故障による出荷計画の遅れを全て取り戻すことが可能なことが分かりました。
- 002デバンニング:29人→40.31人
- 004加工:19人→48.56人
- 006バンニング:19人→24.12人
まとめ
今回はassimeeを使ってPDC型物流倉庫内で行われる加工作業のシミュレーションを行い、スケジュールの検証や故障が発生した場合に翌日のスケジュールを修正を行う方法を解説しました。PCとブラウザさえあれば、assimeeを使ったシミュレーションは誰にでも簡単に、かつ、現場で行うことが可能です。これにより、事前のスケジュールの立案だけでなく、突発的な事故や故障やタイムスケジュールが狂った場合の迅速な修正対応の実施に役立ちます。