ー概要ー
製造業において出荷目標が頻繁に変わることは珍しくありません。このような変動に効率的に対応するためには、生産ラインの人員配置を柔軟に調整することが重要です。本記事では、ラインに配置される人員数によって生産数が変動するモデルを用いて、日々変化する出荷数に合わせて人員配置と入荷量を最適化する具体的な例について解説します。
ーモデルの紹介ー
下図は今回作成するモデルとなります。材料が入荷した後、製品Aの製造ライン、製品Bの製造ライン、製品Cの製造ラインに分岐します。一旦、製品を集めた後、それぞれの出荷先に応じて製品A、B、Cの梱包を行いパレットにまとめた上で出荷を行います。
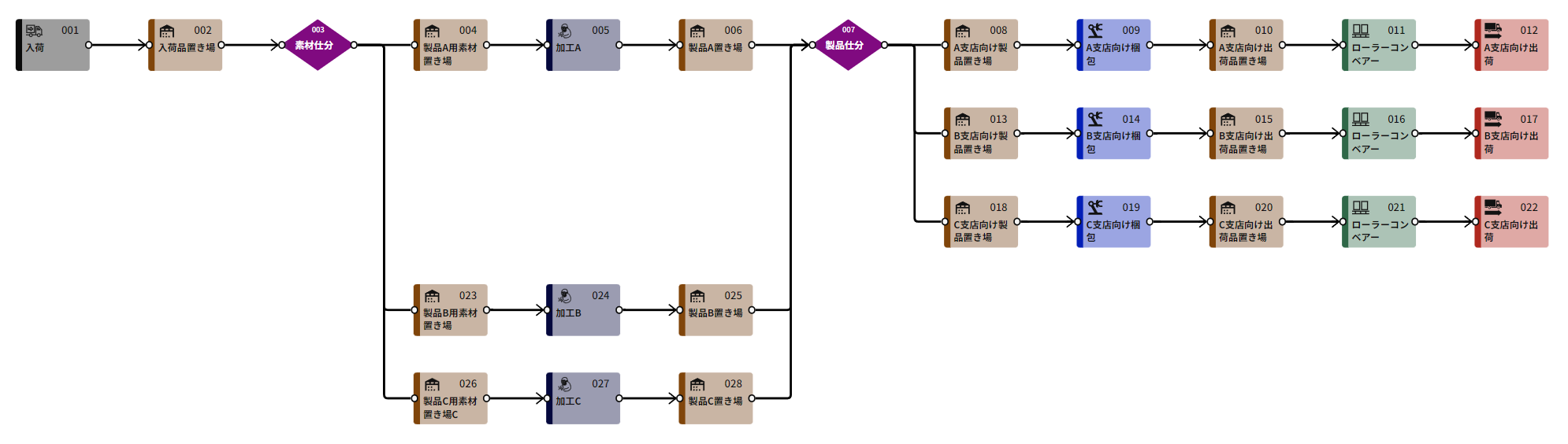
今回のモデルでは「005加工A」、「024加工B」、「027加工C」のそれぞれで作られる、製品A、製品B、製品Cの数と材料の数に違いをつけており、製品A<製品B<製品Cの順に生産量が多くなります。生産した製品はA支店、B支店、C支店へ向けてパレットにまとめてから送られますが、パレットを構成する個口にも差が付けてあり、A支店、B支店、C支店の順に送られる製品の数が多くなっています。モデルを作成したらシミュレーションを行います。今回はシミュレーション時間を8時間に相当する480分と設定します。
ーシミュレーション結果ー
以下が、シミュレーション結果となります。
ダッシュボードで「累積生産数」、「生産推移」、「ライン別生産数」、「生産割合」のグラフを選んで書かせると以下のような結果となります。パレットを構成する製品数の少ないA支店向けが他の行先と比べて多くなっています。
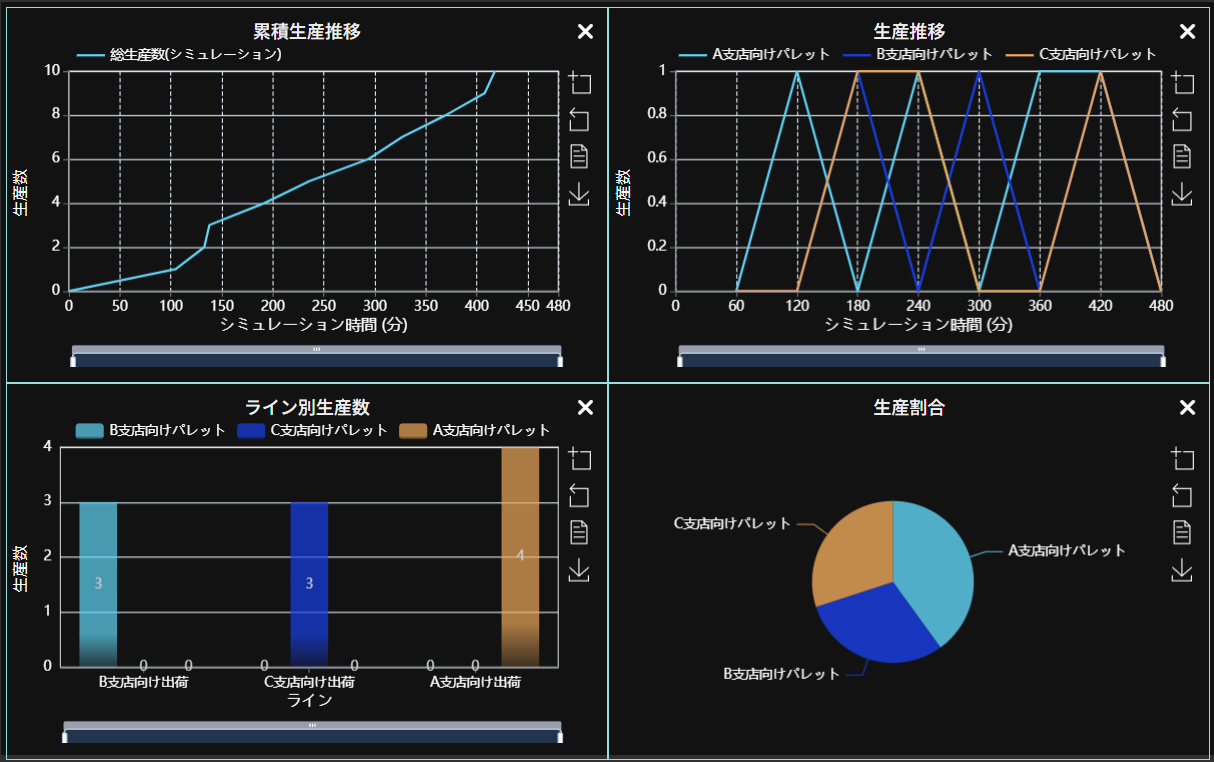
ー最適化ー
上のモデルをレポートとして保存した後、レポートを使って人の最適化を行います。まず、人員の範囲を設定します。今回は「005加工A」、「024加工B」、「027加工C」、「009A支社向け梱包」、「014B支社向け梱包」、「019C支社向け梱包」に対して1人から10人の範囲で人員の変更を可能にします。
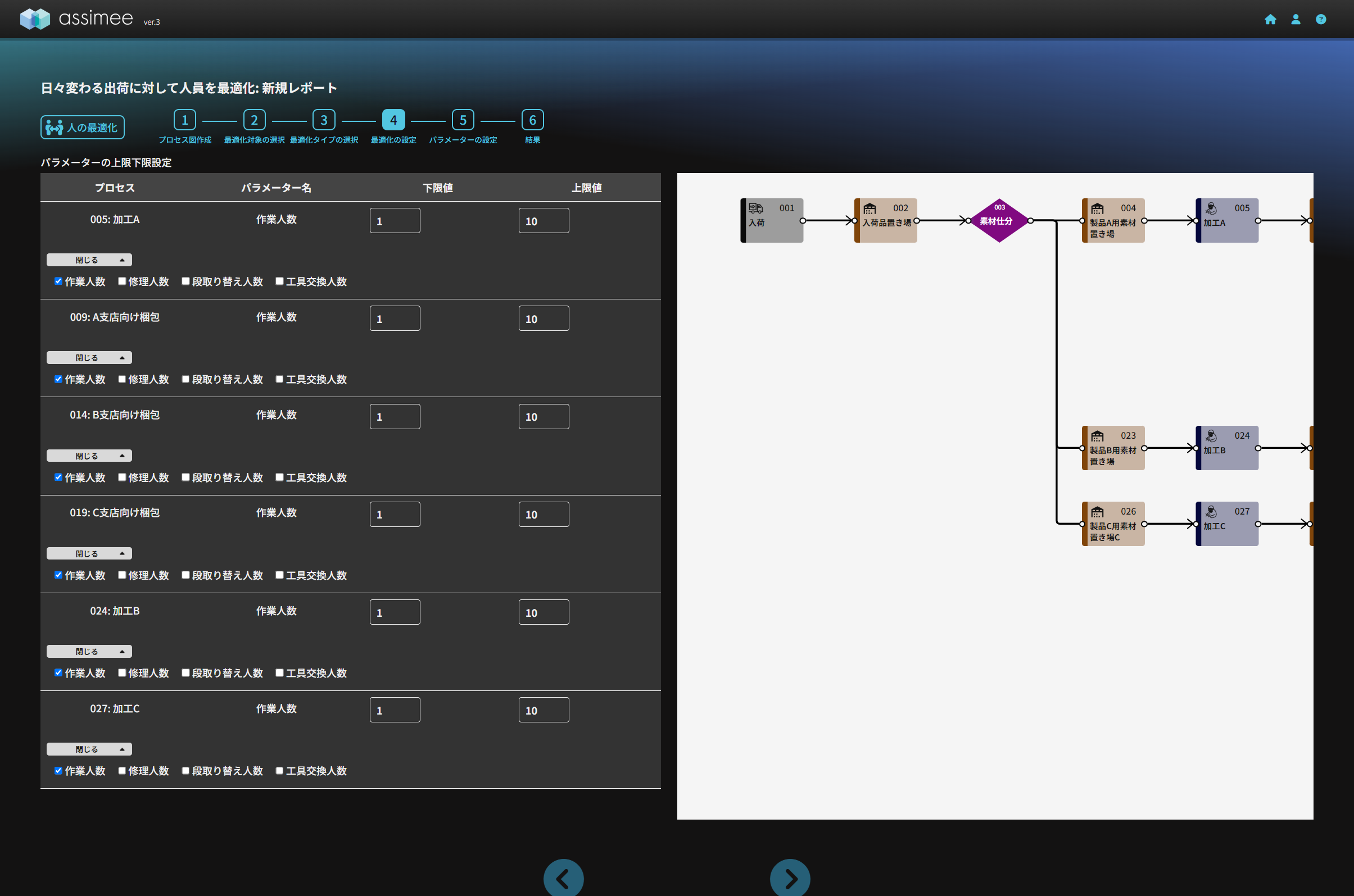
次に出荷目標を入力します。まず、A支店、B支店、C支店に向けて以下のような出荷目標を入力します。
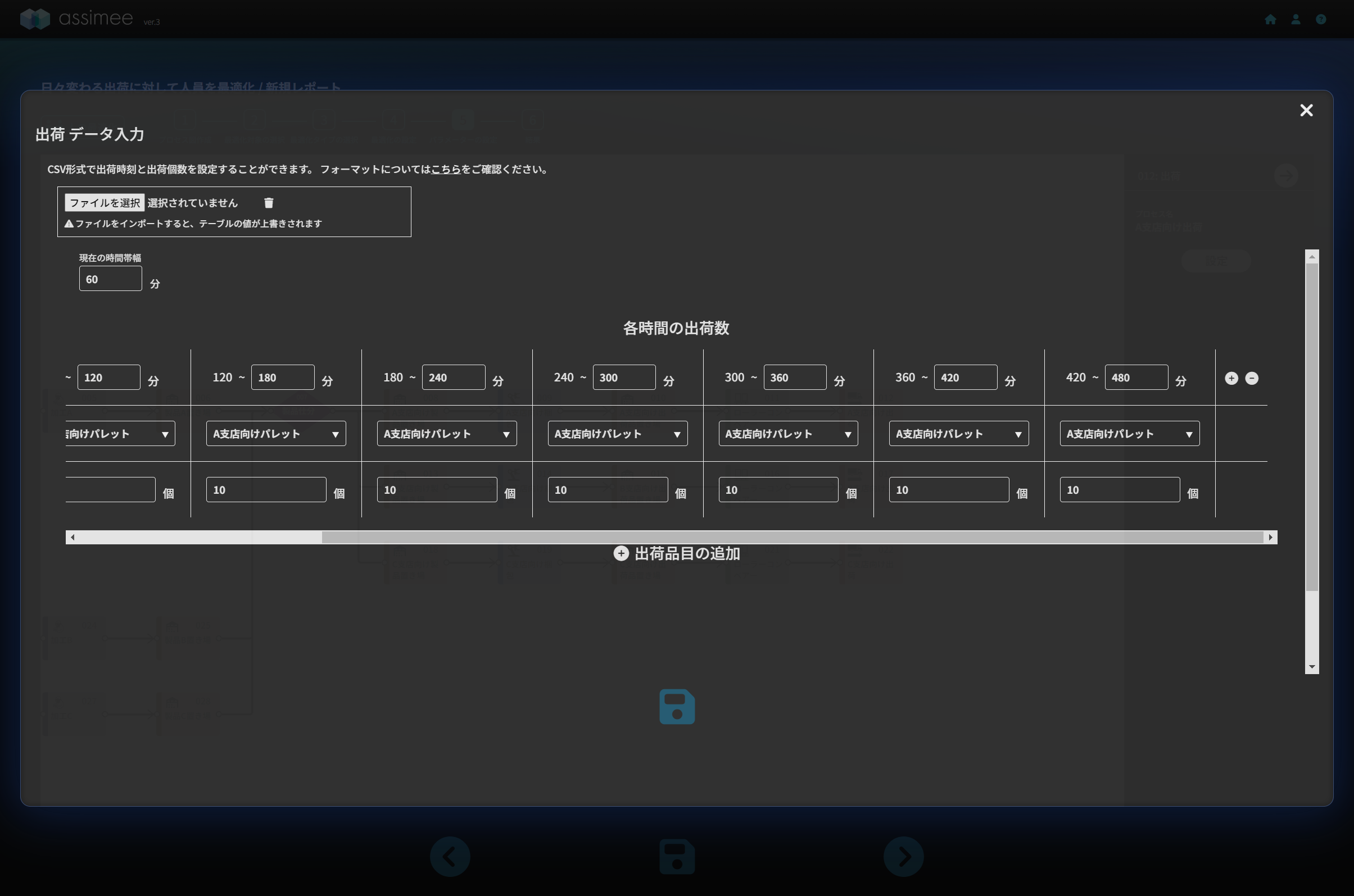
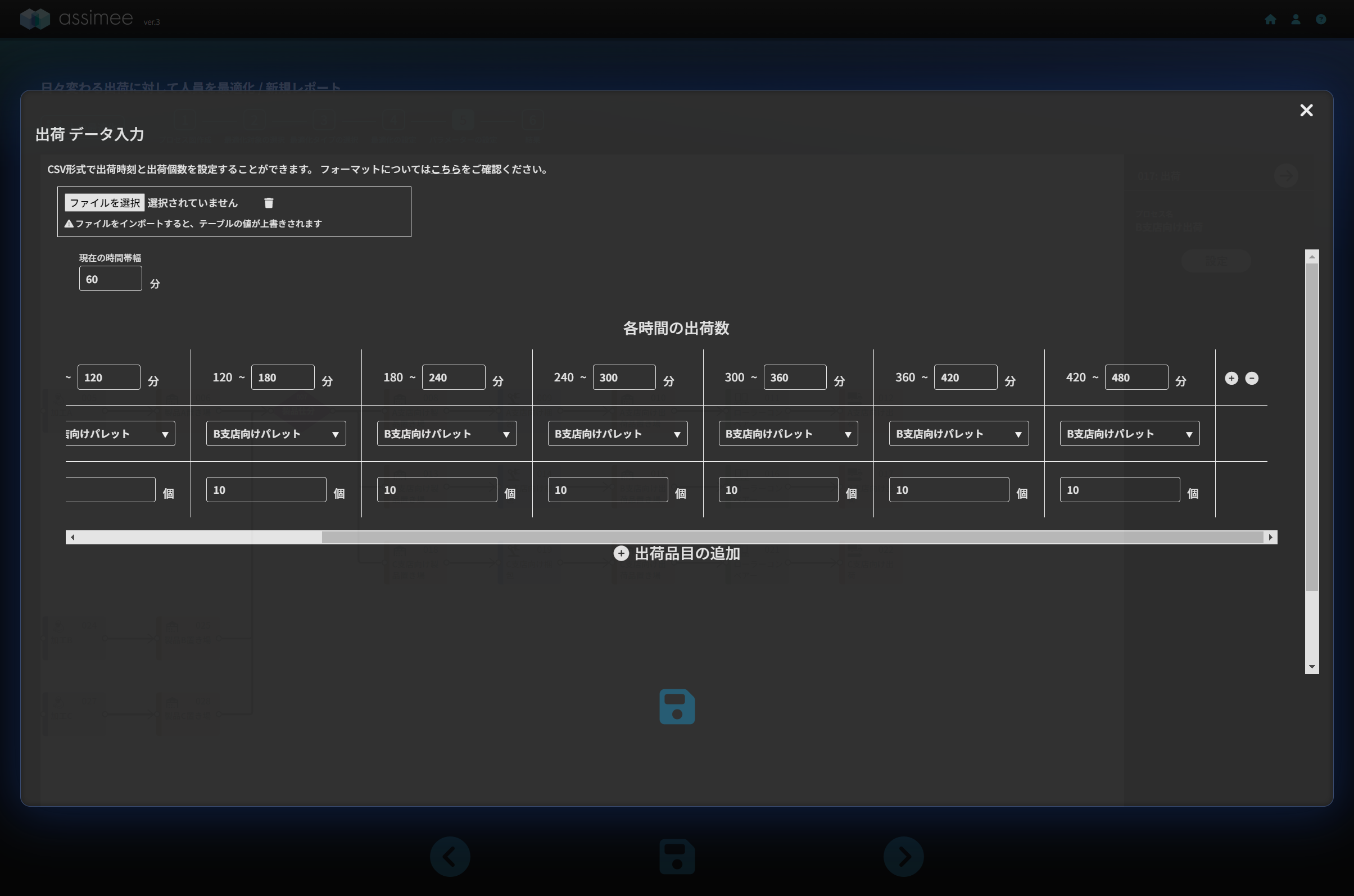
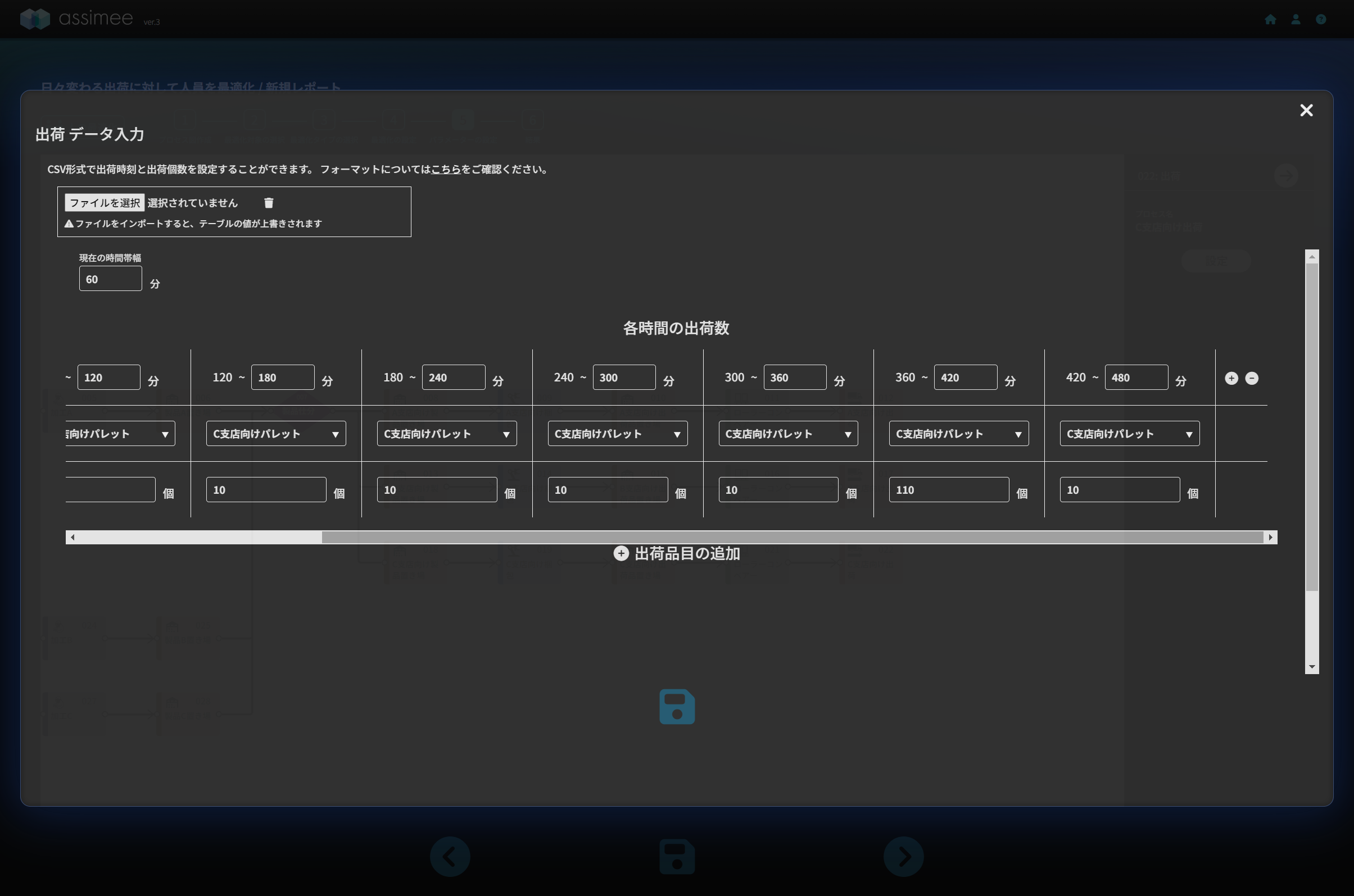
それぞれの出荷プロセスに出荷目標を設定したら最適化を行います。
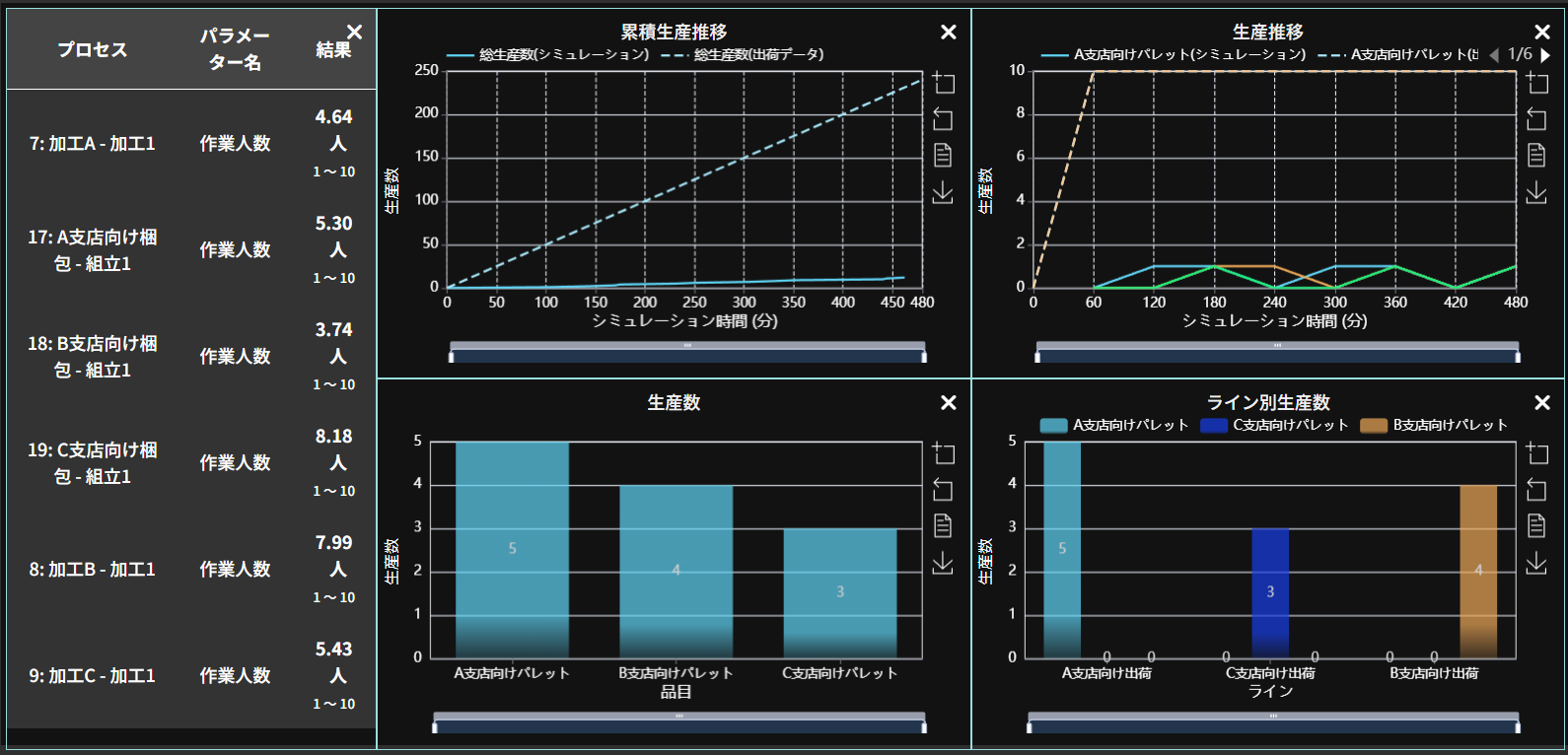
累積生産数推移、生産推移を見ると出荷量が目標に足りません。一方で、最適化結果の数字を見ると加工などに配置される人員数にはまだ余裕があるため、どこかにボトルネックが存在し、材料の供給などが滞っていることが分かります。下流側から順に確認していくと、「003素材仕分」「007製品仕分」のステータスがBusyになっていることが分かります。
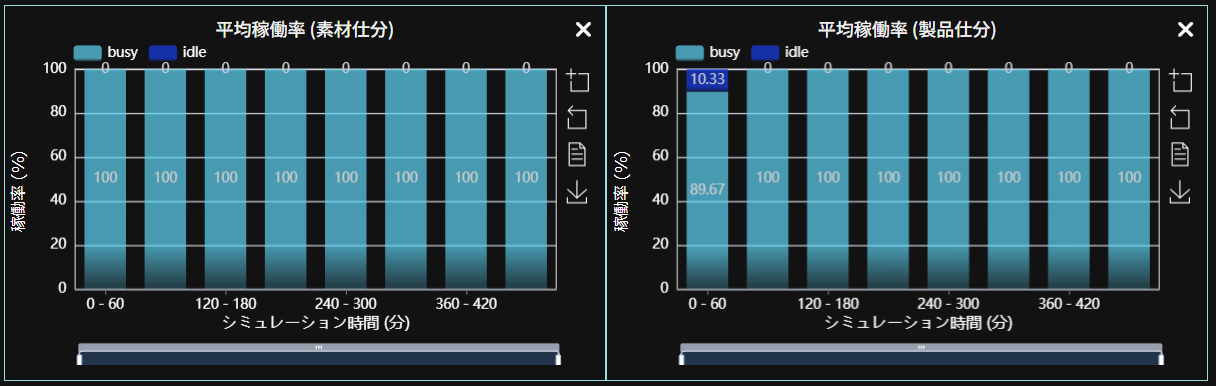
そこで、これら2つの分岐の人員数を1人から10人へ増加させて、処理能力を増やし再度最適化を行ってみます。
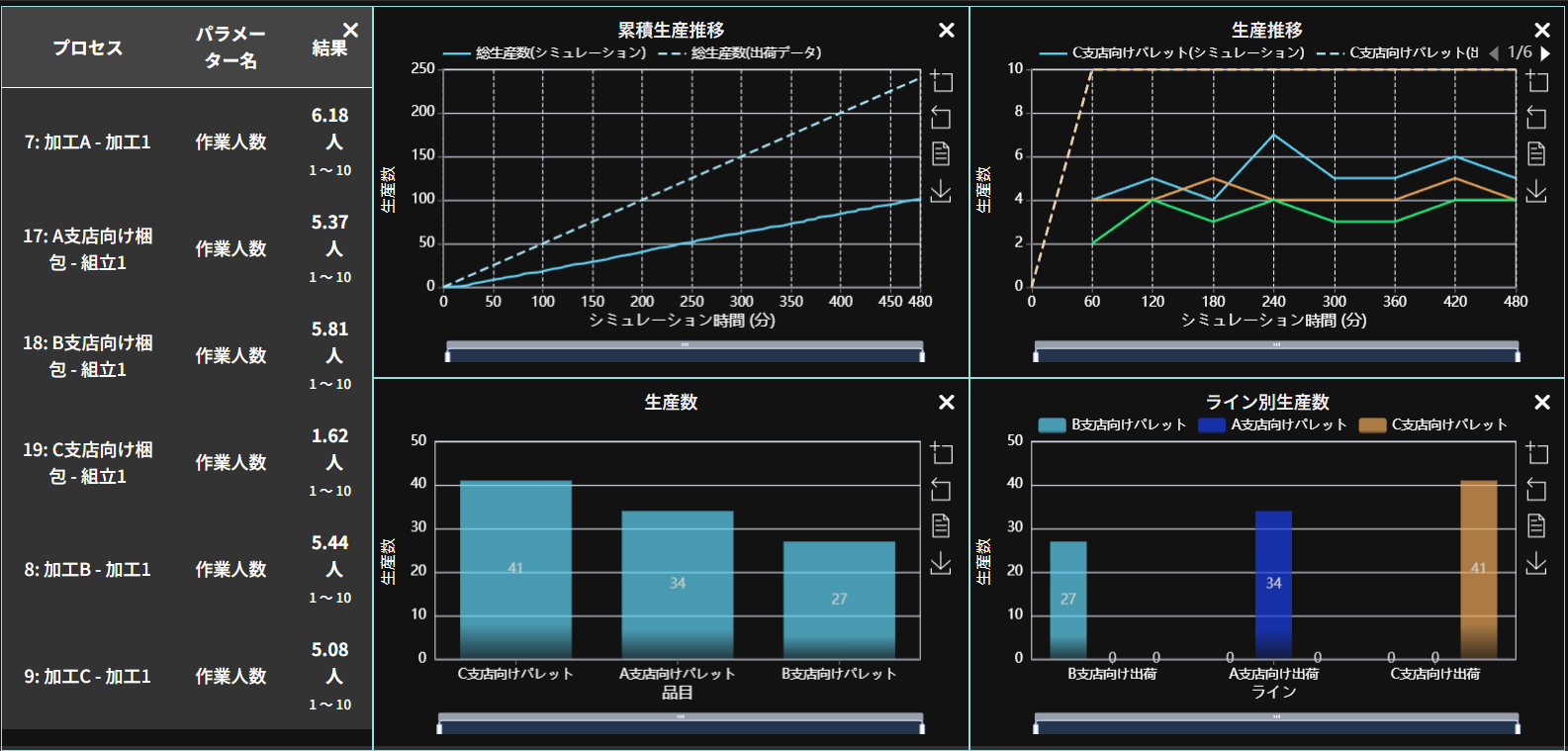
しかし、再度最適化を行った結果を見ても、まだ出荷目標に届きません。再び下流側から確認を行います。先ほどの2つの分岐と最も上流にある「002入荷品置き場」の在庫数を見てみます。
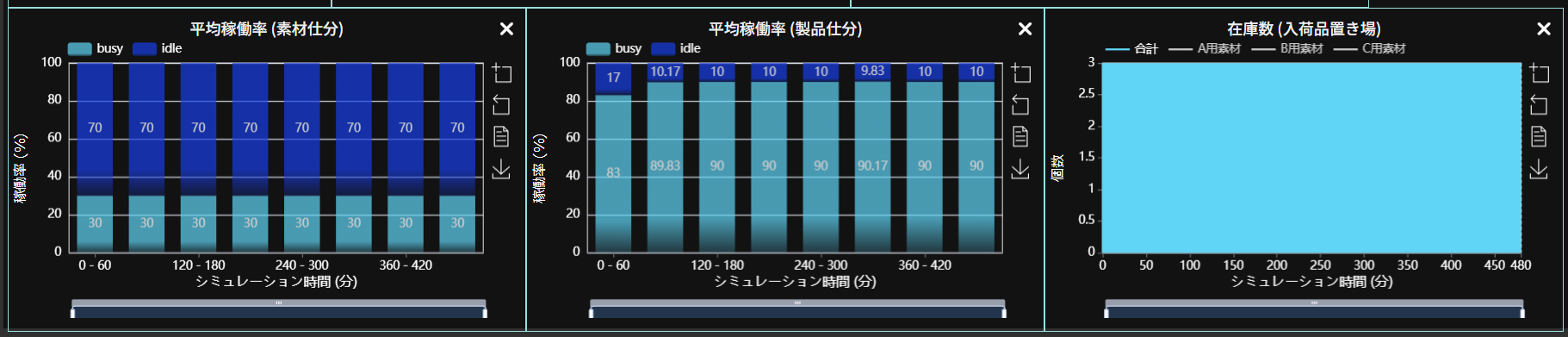
これらから分岐のステータスには余裕があるものの、入荷置き場の方には在庫がなく入荷品不足で出荷が足りないことが分かりました。そこで、入荷量を初期設定より3倍(毎分1個→毎分3個)に増やして再び最適化してみます。

やや出荷量が増えましたが、まだ、足りません。以降、上と同様の手順でボトルネックを改善したり、場合によっては最適化範囲を変更するなどして目標を達成するように調整して行きます。最終的には「005加工A」の人員上限を10人から20人へ、「024加工B」、「027加工C」の人員上限を10人から15人へ、「007製品仕分」の作業人数を30人へ増やし、「008A支社向け製品置き場」、「013B支社向け製品置き場」、「018C支社向け製品置き場」の容量を1000個から2000個へ拡張することで以下のように目標をほぼ満足する結果が得られました。
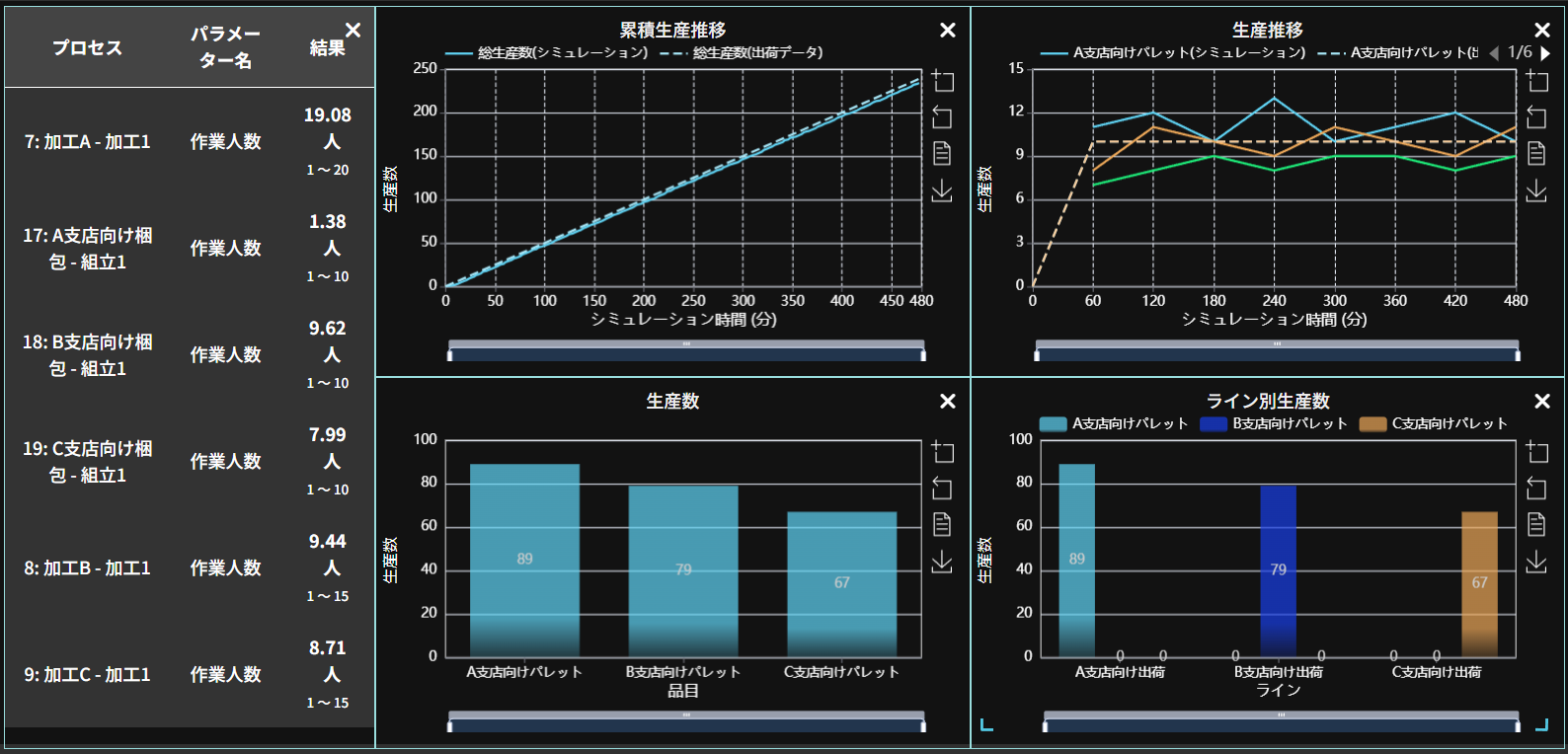
ーまとめー
今回は日々変わる生産目標に対して人員配置を最適にする方法について解説しました。生産目標に対して生産ラインへの人員の適切な配置だけでなく、入荷量の調整にも役立つことが分かります。assimeeはPCとブラウザがあれば、どこでも簡単に実行できるため、実際に実行するのは難しい、生産ラインの変更や極端な生産設定などを気兼ねなく実行することが出来ます。このようなことから、日々異なる人員配置のような毎日の業務に利用するには最適なツールとなっています。