概要
今回の記事では、セル生産方式サンプルとしたモデルを作成し、作業員の生産性(時間あたりの生産数)のシミュレーション(見える化)を行う方法について解説します。今回例に挙げるセル生産方式で生産性を効果的に改善するためには、それぞれのセル内で組み立てを行う作業員1人ごとの細かい生産性の違いを見える化することが必要です。現場では製品ごとに標準生産数や効率を設定するなどの管理方法が行われていますが、作業員間で持っているスキル(生産性)に大きな差がある場合は、実際の組立作業を行いながら担当者の経験をもとに生産計画の修正をする必要があります。作業員ごとのスキルを反映したシミュレーションを行い事前に計画を綿密に立てることができれば、このような修正作業の回数を減らし業務負担の削減につなげることができると考えられます。
セル生産方式とは
セル生産方式はライン生産方式と並んで、生産現場で主流となっている方法です。ライン生産方式が、少量品種の大量生産に使われるのに対して、顧客の好みが多様化している現代で求められる多品種少量生産に向いています。また、ライン生産方式では1人の作業員が、例えばドアの取り付け作業を繰り返します。1つあるいは少数の作業しか求められないため、多様なスキルが必要ない一方で、単一の作業の繰り返しは作業モチベーションの低下が問題になるとされています。一方で、セル生産方式では作業員が複数の製品を組み立てる必要があるため、高度なスキルが要求されますが、作業モチベーションは維持しやすいとされています。
モデル
今回作成するモデルは以下の通りとなります。5つの組立プロセスからなる生産用セルが2つあるカメラ組立工場を想定しています。
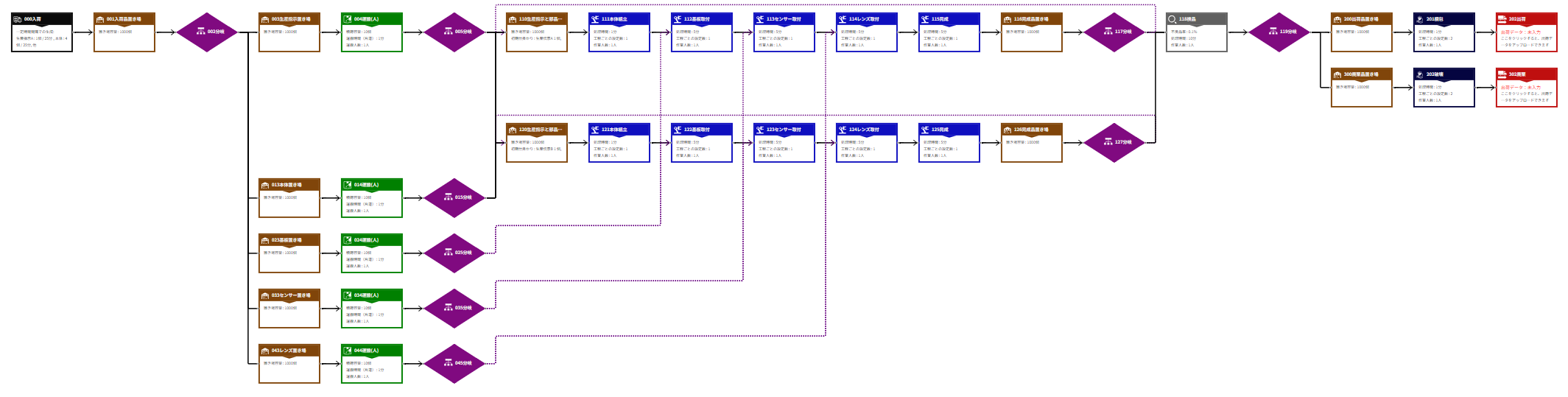
モデル作成の設定
今回、5つの組立プロセスは1人の作業員が作業する想定ですが、デフォルトの設定では入荷した部品の在庫置き場に部品がある限り、1つ目の組立プロセスが止まらず、次の組立工程が進んでしまいます。これは最後の組立終了時に完成品と共に生産伝票を出力し、フィードバックを利用して最初の組立プロセスに必要なパーツとして要求することで防ぐことが可能です。*このまま設定すると初回組立が行えないので、仕掛品として生産伝票の初期配置を行います。
モデル作成
プロセスカードを設置し、設定することでモデルを作成して行きます。
入荷プロセス:
プロセス名を「000部品出庫」へ変更、
詳細設定から入荷するパーツを6種類、図のように設定します。
1つ目:パーツ名「生産指示A」、個数「1個」、入荷間隔「25分」、
2つ目:パーツ名「生産指示B」、個数「1個」、入荷間隔「25分」、
3つ目:パーツ名「本体」、個数「4個」、入荷間隔「30分」、
4つ目:パーツ名「基板」、個数「6個」、入荷間隔「30分」、
5つ目:パーツ名「センサー」、個数「6個」、入荷間隔「30分」、
6つ目:パーツ名「レンズ」、個数「4個」、入荷間隔「30分」
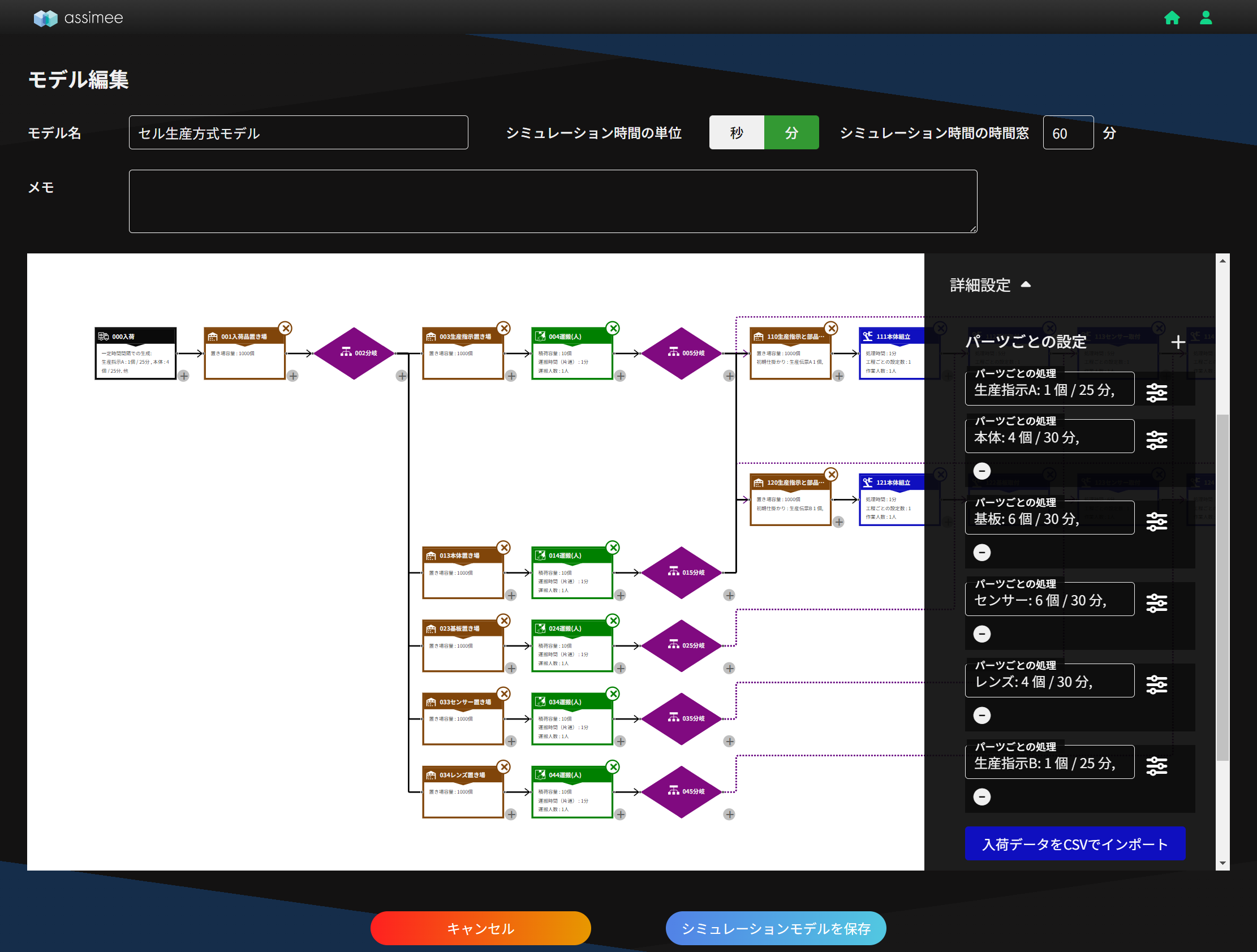
置き場プロセス:
プロセス名を「001入荷品置き場」へ変更、容量を「1000個」と設定
分岐プロセス:
プロセス名を「002分岐」へ変更、処理時間を「0.5分」、作業人数を「30人」と設定
分岐設定より分岐先と分岐条件を以下のように設定
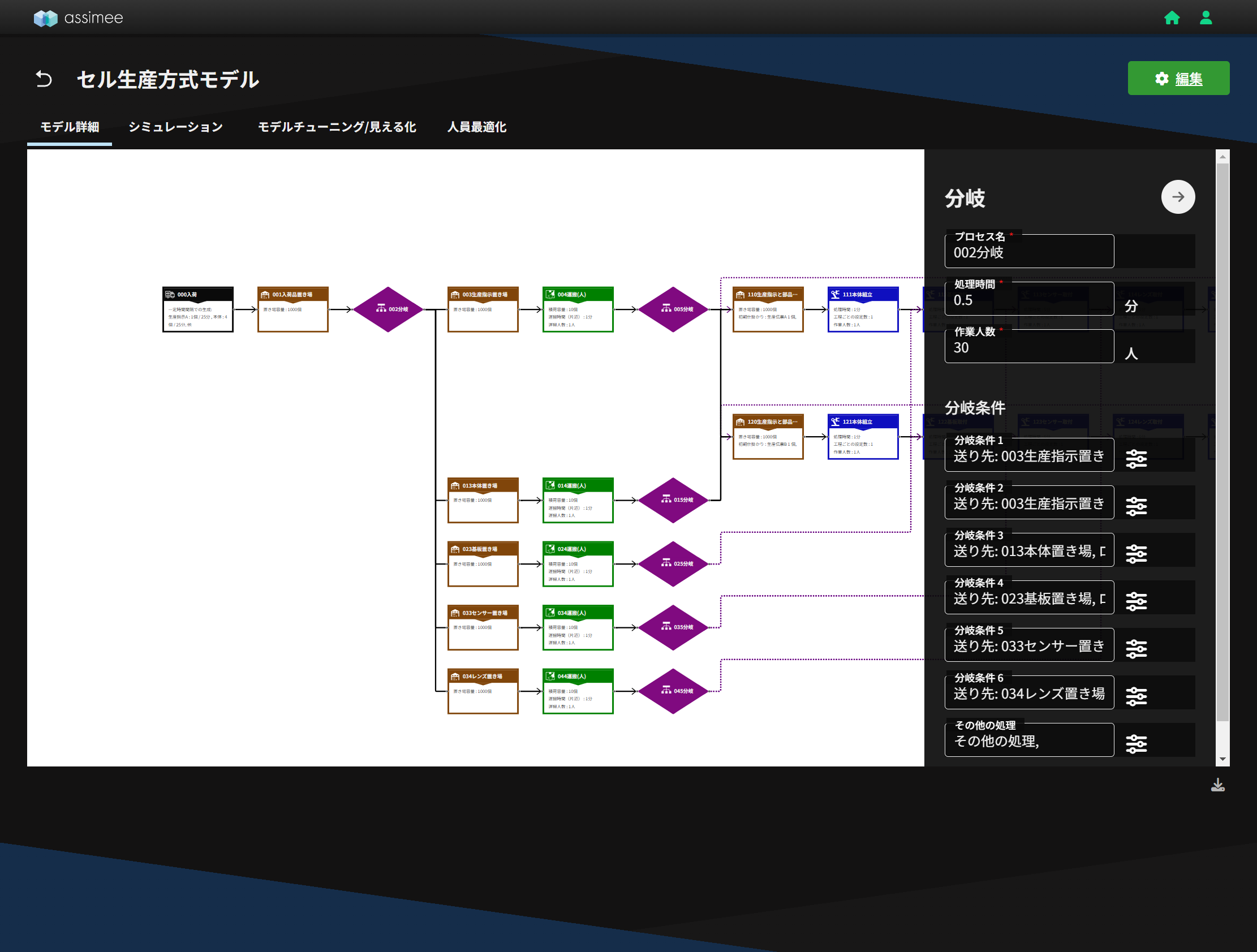
分岐先として5つのプロセスを設置:
置き場プロセス:
プロセス名を「003生産指示置き場」へ変更、容量を「1000個」と設定
以降は生産指示へ
置き場プロセス:
プロセス名を「013本体置き場」へ変更、容量を「1000個」と設定
以降は本体(部品)へ
置き場プロセス:
プロセス名を「023基板置き場」へ変更、容量を「1000個」と設定
以降は基板(部品)へ
置き場プロセス:
プロセス名を「033センサー置き場」へ変更、容量を「1000個」と設定
以降はセンサー(部品)へ
置き場プロセス:
プロセス名を「043レンズ置き場」へ変更、容量を「1000個」と設定
以降はレンズ(部品)へ
分岐条件:
条件1:
・送り先:003生産指示置き場
・分岐条件:パーツ名が一致
・パーツ名:生産指示A
条件2:
・送り先:003生産指示置き場
・分岐条件:パーツ名が一致
・パーツ名:生産指示B
条件3:
・送り先:013本体置き場
・分岐条件:パーツ名が一致
・パーツ名:本体
条件4:
・送り先:023基板置き場
・分岐条件:パーツ名が一致
・パーツ名:基板
条件5:
・送り先:033生産指示置き場
・分岐条件:パーツ名が一致
・パーツ名:センサー
条件6:
・送り先:043置き場
・分岐条件:パーツ名が一致
・パーツ名:レンズ
生産指示
生産指示の処理を行います。セルA用とセルB用の指示をそれぞれ分岐させます。
置き場プロセス(再掲):
プロセス名を「003生産指示置き場」へ変更、容量を「1000個」と設定
運搬プロセス(人):
プロセス名を「004運搬(人)」へ変更、積荷容量を「10個」、処理時間「1分」、運搬人数「1人」と設定
分岐プロセス:
プロセス名を「005分岐」へ変更、処理時間を「1分」、作業人数を「2人」と設定
分岐設定より分岐先と分岐条件を以下のように設定
分岐先として2つのプロセスを設置:
置き場プロセス:
プロセス名を「010生産指示と部品置き場」へ変更、容量を「1000個」と設定、
詳細設定より初期仕掛かりにパーツ名「生産伝票A」、個数「1個」を設定
置き場プロセス:
プロセス名を「020生産指示と部品置き場」へ変更、容量を「1000個」と設定、
詳細設定より初期仕掛かりにパーツ名「生産伝票A」、個数「1個」を設定
分岐条件:
条件1:
・送り先:010生産指示と部品置き場
・分岐条件:パーツ名が一致
・パーツ名:生産指示A
条件2:
・送り先:020生産指示と部品置き場
・分岐条件:パーツ名が一致
・パーツ名:生産指示B
本体(部品)
部品の供給を再現する部分です。生産用セルでの組立プロセスに接続しますが、接続は組立プロセスの設置後に行ってください。
置き場プロセス(再掲):
プロセス名を「013本体置き場」へ変更、容量を「1000個」と設定
運搬プロセス(人):
プロセス名を「014運搬(人)」へ変更、積荷容量を「10個」、処理時間「1分」、運搬人数「1人」と設定
分岐プロセス:
プロセス名を「015分岐」へ変更、処理時間を「5分」、作業人数を「1人」と設定
分岐設定より分岐先と分岐条件を以下のように設定
分岐先:
「010生産指示と部品置き場」と「020生産指示と部品置き場」の2つのプロセスへ接続
分岐条件:
ランダム(デフォルトのまま変更なし)
基板(部品)
置き場プロセス(再掲):
プロセス名を「023基板置き場」へ変更、容量を「1000個」と設定
運搬プロセス(人):
プロセス名を「024運搬(人)」へ変更、積荷容量を「10個」、処理時間「1分」、運搬人数「1人」と設定
分岐プロセス:
プロセス名を「025分岐」へ変更、処理時間を「5分」、作業人数を「1人」と設定
分岐設定より分岐先と分岐条件を以下のように設定
分岐先:
「112基板取付」と「122基板取付」の2つのプロセスへ接続
分岐条件:
ランダム(デフォルトのまま変更なし)
センサー(部品)
置き場プロセス(再掲):
プロセス名を「033センサー置き場」へ変更、容量を「1000個」と設定
運搬プロセス(人):
プロセス名を「034運搬(人)」へ変更、積荷容量を「10個」、処理時間「1分」、運搬人数「1人」と設定
分岐プロセス:
プロセス名を「035分岐」へ変更、処理時間を「5分」、作業人数を「1人」と設定
分岐設定より分岐先と分岐条件を以下のように設定
分岐先:
「113センサー取付」と「123センサー取付」の2つのプロセスへ接続
分岐条件:
ランダム(デフォルトのまま変更なし)
レンズ(部品)
置き場プロセス(再掲):
プロセス名を「043レンズ置き場」へ変更、容量を「1000個」と設定
運搬プロセス(人):
プロセス名を「044運搬(人)」へ変更、積荷容量を「10個」、処理時間「1分」、運搬人数「1人」と設定
分岐プロセス:
プロセス名を「045分岐」へ変更、処理時間を「5分」、作業人数を「1人」と設定
分岐設定より分岐先と分岐条件を以下のように設定
分岐先:
「114レンズ取付」と「124レンズ取付」の2つのプロセスへ接続
分岐条件:
ランダム(デフォルトのまま変更なし)
生産セルA
セルを設置します。生産指示に従ってカメラを生産して行きます。各組立プロセスを設置してから部品の供給のため分岐プロセスからプロセスを繋げてください。また、作業員1人での組み立てを再現するため生産伝票がなければ、組立が進まないようにモデルを設定します。
置き場プロセス(再掲):
プロセス名を「010生産指示と部品置き場」へ変更、容量を「1000個」と設定、
詳細設定より初期仕掛かりにパーツ名「生産伝票A」、個数「1個」を設定、
「015分岐」よりプロセスを接続
組立プロセス:
プロセス名を「111本体組立」へ変更、処理時間を「1分」、作業人数を「1人」と設定、
詳細設定より
対象パーツ1つ目の名称を「本体」、個数を「1個」、
対象パーツ2つ目の名称を「生産指示A」、個数を「1個」、
対象パーツ3つ目の名称を「生産伝票A」、個数を「1個」、*「115完成」を設定後に設定する
出力パーツの名称を「組立中本体」、個数を「1個」
組立プロセス:
プロセス名を「112基板取付」へ変更、処理時間を「5分」、作業人数を「1人」と設定、
「025分岐」よりプロセスを接続、*先に接続しないとパーツの選択が出ません。
詳細設定より
対象パーツ1つ目の名称を「組立中本体」、個数を「1個」、
対象パーツ2つ目の名称を「基板」、個数を「2個」、
出力パーツの名称を「基板取付済本体」、個数を「1個」、
組立プロセス:
プロセス名を「113センサー取付」へ変更、処理時間を「5分」、作業人数を「1人」と設定、
「035分岐」よりプロセスを接続、*先に接続しないとパーツの選択が出ません。
詳細設定より
対象パーツ1つ目の名称を「基板取付済本体」、個数を「1個」、
対象パーツ2つ目の名称を「センサー」、個数を「2個」、
出力パーツの名称を「センサー済本体」、個数を「1個」
組立プロセス:
プロセス名を「114レンズ取付」へ変更、処理時間を「5分」、作業人数を「1人」と設定、
「045分岐」よりプロセスを接続、*先に接続しないとパーツの選択が出ません。
詳細設定より
対象パーツ1つ目の名称を「センサー取付済本体」、個数を「1個」、
対象パーツ2つ目の名称を「レンズ」、個数を「1個」、
出力パーツの名称を「レンズ済本体」、個数を「1個」
組立プロセス:
プロセス名を「115完成」へ変更、処理時間を「5分」、作業人数を「1人」と設定、
詳細設定より
対象パーツ1つ目の名称を「レンズ取付済本体」、個数を「1個」、
出力パーツ1つ目の名称を「カメラ完成品A」、個数を「1個」、
対象パーツ2つ目の名称を「生産伝票A」、個数を「1個」
組立プロセス「111本体組立」修正:
対象パーツ3つ目の名称に「生産伝票A」、個数を「1個」を追加
置き場プロセス:
プロセス名を「116完成品置き場」へ変更、容量を「1000個」と設定、
分岐プロセス:
プロセス名を「117分岐」へ変更、処理時間を「1分」、作業人数を「1人」と設定
分岐設定より分岐先と分岐条件を以下のように設定
分岐先:
置き場プロセス:「010生産指示と部品置き場」へプロセスを接続
生産伝票をフィードバックすることで、「111本体組立」で次の組立作業が始まるようにしています。
検品プロセス:「118検品」
分岐条件:
条件1:
・送り先:010生産指示と部品置き場
・分岐条件:パーツ名が一致
・パーツ名:生産伝票A
条件2:
・送り先:118検品
・分岐条件:パーツ名が一致
・パーツ名:カメラ完成品A
生産セルB
セルAと同様に設定します。
置き場プロセス(再掲):
プロセス名を「020生産指示と部品置き場」へ変更、容量を「1000個」と設定、
詳細設定より初期仕掛かりにパーツ名「生産伝票B」、個数「1個」を設定、
「015分岐」よりプロセスを接続
組立プロセス:
プロセス名を「121本体組立」へ変更、処理時間を「1分」、作業人数を「1人」と設定、
詳細設定より
対象パーツ1つ目の名称を「本体」、個数を「1個」、
対象パーツ2つ目の名称を「生産指示B」、個数を「1個」、
対象パーツ3つ目の名称を「生産伝票B」、個数を「1個」、*「125完成」を設定後に設定する
出力パーツの名称を「組立中本体」、個数を「1個」
組立プロセス:
プロセス名を「122基板取付」へ変更、処理時間を「5分」、作業人数を「1人」と設定、
「025分岐」よりプロセスを接続、*先に接続しないとパーツの選択が出ません。
詳細設定より
対象パーツ1つ目の名称を「組立中本体」、個数を「1個」、
対象パーツ2つ目の名称を「基板」、個数を「2個」、
出力パーツの名称を「基板取付済本体」、個数を「1個」
組立プロセス:
プロセス名を「123センサー取付」へ変更、処理時間を「5分」、作業人数を「1人」と設定、
「035分岐」よりプロセスを接続、*先に接続しないとパーツの選択が出ません。
詳細設定より
対象パーツ1つ目の名称を「基板取付済本体」、個数を「1個」、
対象パーツ2つ目の名称を「センサー」、個数を「2個」、
出力パーツの名称を「センサー済本体」、個数を「1個」
組立プロセス:
プロセス名を「124レンズ取付」へ変更、処理時間を「5分」、作業人数を「1人」と設定、
「045分岐」よりプロセスを接続、*先に接続しないとパーツの選択が出ません。
詳細設定より
対象パーツ1つ目の名称を「センサー取付済本体」、個数を「1個」、
対象パーツ2つ目の名称を「レンズ」、個数を「1個」、
出力パーツの名称を「レンズ済本体」、個数を「1個」
組立プロセス:
プロセス名を「125完成」へ変更、処理時間を「5分」、作業人数を「1人」と設定、
詳細設定より
対象パーツ1つ目の名称を「レンズ取付済本体」、個数を「1個」、
出力パーツ1つ目の名称を「カメラ完成品B」、個数を「1個」、
対象パーツ2つ目の名称を「生産伝票B」、個数を「1個」
組立プロセス「121本体組立」修正:
対象パーツ3つ目の名称に「生産伝票B」、個数を「1個」を追加
置き場プロセス:
プロセス名を「126完成品置き場」へ変更、容量を「1000個」と設定、
分岐プロセス:
プロセス名を「127分岐」へ変更、処理時間を「1分」、作業人数を「1人」と設定
分岐設定より分岐先と分岐条件を以下のように設定
分岐先:
置き場プロセス:「020生産指示と部品置き場」へプロセスを接続
検品プロセス:「118検品」
分岐条件:
条件1:
・送り先:020生産指示と部品置き場
・分岐条件:パーツ名が一致
・パーツ名:生産伝票B
条件2:
・送り先:128検品
・分岐条件:パーツ名が一致
・パーツ名:カメラ完成品B
検品と出荷
検品プロセス:
プロセス名を「118検品」へ変更、不良品率を0.1%、処理時間を「10分」、作業人数を「1人」と設定
分岐プロセス:
プロセス名を「119分岐」へ変更、処理時間を「1分」、作業人数を「1人」と設定
分岐設定より分岐先と分岐条件を以下のように設定
分岐先として2つのプロセスを設置:
置き場プロセス:
プロセス名を「200出荷品置き場」へ変更、容量を「1000個」と設定
置き場プロセス:
プロセス名を「300廃棄品置き場」へ変更、容量を「1000個」と設定
分岐条件:
条件1:
・送り先:200出荷品置き場
・分岐条件:パーツステータスが一致
・パーツステータス:正常
条件2:
・送り先:300廃棄品置き場
・分岐条件:パーツステータスが一致
・パーツステータス:不良
出荷品
置き場プロセス(再掲):
プロセス名を「200出荷品置き場」へ変更、容量を「1000個」と設定
加工プロセス:
プロセス名を「201梱包」へ変更、処理時間を「1分」、作業人数を「1人」と設定、
詳細設定より
対象パーツ1つ目の名称を「カメラ完成品A」、個数を「1個」、
出力パーツ1つ目の名称を「出荷品A」、個数を「1個」、
対象パーツ2つ目の名称を「カメラ完成品B」、個数を「1個」、
出力パーツ2つ目の名称を「出荷品B」、個数を「1個」と設定
出荷プロセス:
プロセス名を「202出荷」へ変更
不良品
置き場プロセス(再掲):
プロセス名を「300廃棄品置き場」へ変更、容量を「1000個」と設定
加工プロセス:
プロセス名を「301破壊」へ変更、処理時間を「1分」、作業人数を「1人」と設定、
詳細設定より
対象パーツ1つ目の名称を「カメラ完成品A」、個数を「1個」、
出力パーツ1つ目の名称を「廃棄品」、個数を「1個」、
対象パーツ2つ目の名称を「カメラ完成品B」、個数を「1個」、
出力パーツ2つ目の名称を「廃棄品」、個数を「1個」と設定
出荷プロセス:
プロセス名を「302廃棄」へ変更
シミュレーションと分析
モデルを作成したらシミュレーションを行います。今回はシミュレーション時間を480分(8時間に)設定します。シミュレーションが終わると以下の画面が表示されます。*パーツの仕分けなどに乱数が含まれるため若干のずれが生じる可能性があります。
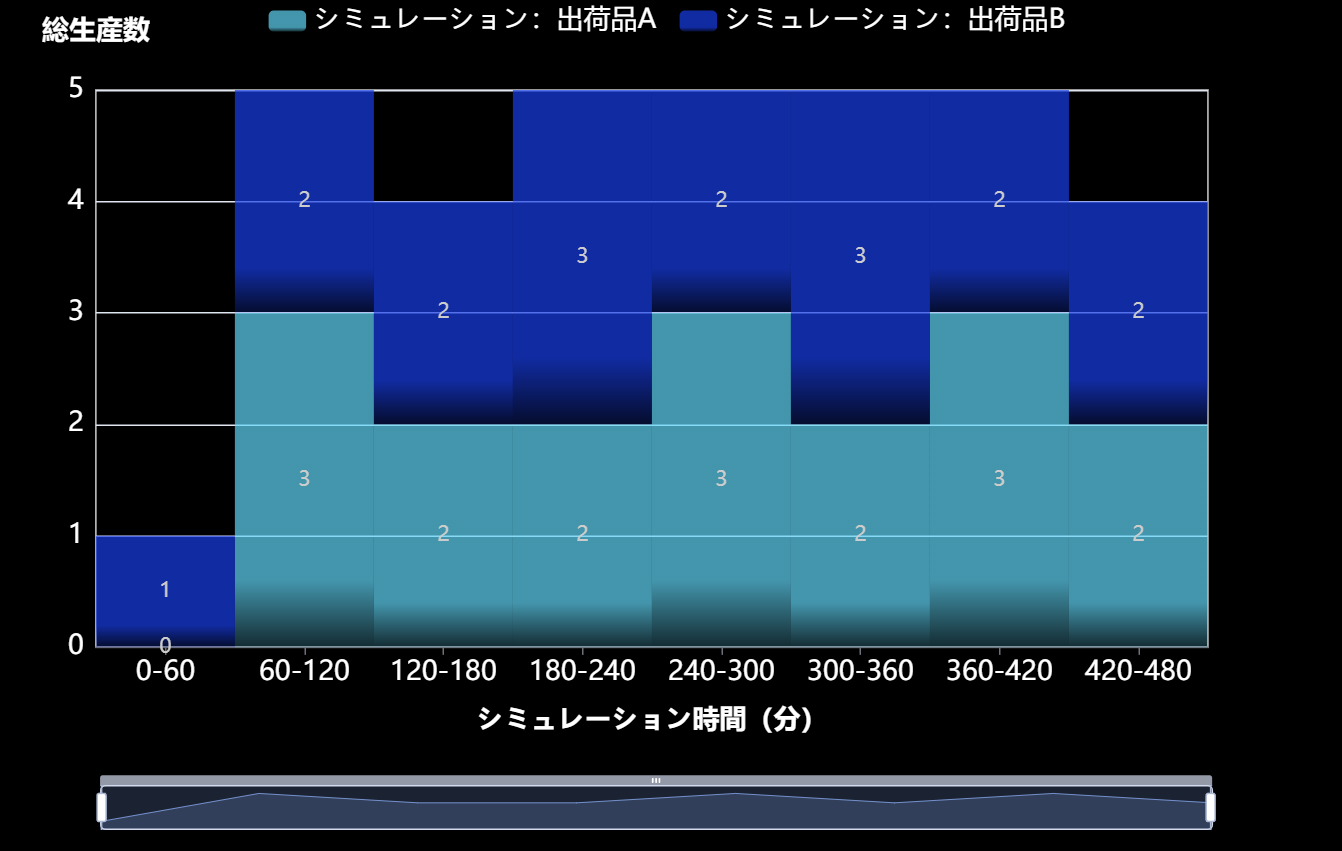
AとB、2つのセルの生産性が同じ場合には上記の結果のようにA(出荷品A)とB(出荷品B)の生産数が同数となる結果となります。これは当然の結果なので次に、セルBの方の生産性を悪化させることでシミュレーション結果がどうなるか見てみましょう。少々極端ですが、セルAに比べてセルBの各組立プロセスの処理時間を倍の時間とし、生産性を半分にします。この場合、以下のようにモデルの設定を変更します。
組立プロセス「121本体組立」の処理時間を「2分」に修正
組立プロセス「122基板取付」の処理時間を「10分」に修正
組立プロセス「123センサー取付」の処理時間を「10分」に修正
組立プロセス「124レンズ取付」の処理時間を「10分」に修正
組立プロセス「125完成」の処理時間を「10分」に修正
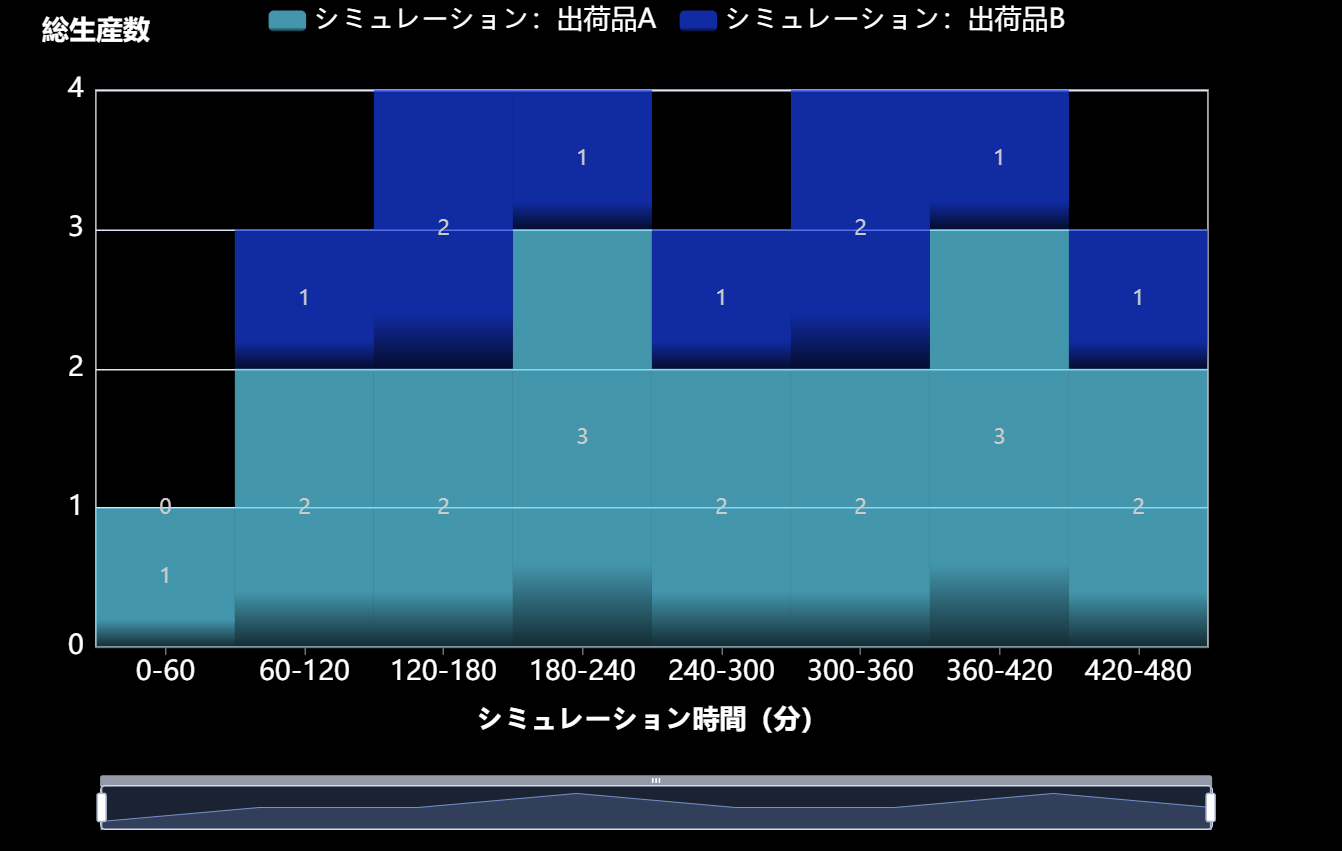
セルBの生産性をセルAの半分とした場合、シミュレーション結果でもセルBの生産数がセルAの約半分となっていることが分かります。このように、現実の作業員の生産性を設定すると、シミュレーションの結果(見える化)が直ぐに得られる評価できるので、標準生産数による管理と比べてより現実に近い生産計画を立てることが可能となります。
なお、今回の記事では簡単のため、セルで生産される生産品目を1つに絞っていますが、組立プロセスのバリエーションを増やしたり、製品ごとに異なる処理時間を設定するなど、より細かな設定を行うことでシミュレーションをより現実に近づけていくことが可能です。
まとめ
今回はセル生産方式を例に取って、セルごと(作業員ごと)の生産性をシミュレーションに反映する(見える化する)方法の解説を行いました。assimeeはこのように生産品目のバリエーションや処理時間などの生産に関する条件を変えながら、繰り返し生産結果のシミュレーションを行うことで、最適な生産条件を探索することのできるツールです。特定の日に出勤している作業員のスキルに合わせたシミュレーションなどを簡単に行うことが可能なので、その結果を踏まえて綿密な生産計画を誰でも立てることが可能となります。