ー概要ー
工場内においてAGVによる輸送を行うケースが増えています。このような場合、必要な輸送需要に対してAGVの台数を柔軟に調整することが重要です。本記事では、assimeeのパラメーター推定機能を使ってAGVの台数の最適化を行う方法について解説します。
ーモデルの紹介ー
下図は今回作成するモデルとなります。材料がまとまって入荷した後、デバンニングによる解包、加工、バンニングを経て荷造りされた製品を出荷する製造ラインを想定しています。入荷とデバンニングの間、デバンニングと加工の間、加工とバンニング、バンニングと出荷の間には在庫置き場が設置されており、置き場間の輸送をAGVが担うモデルです。

今回のモデルでは梱包されたコンテナを輸送する「003輸送経路1」と「015輸送経路4」、部品や製品を輸送する「007輸送経路2」と「011輸送経路3」にAGVを使った輸送を配置します。
AGVの搬送容量には以下のように差をつけてあります。
「003輸送経路1」と「015輸送経路4」:最大積載量1
「007輸送経路2」と「011輸送経路3」:最大積載量100
台数に関しては4つの経路それぞれに10台のAGV、合計で40台のAGVが配置されています。モデルを作成したらシミュレーションを行います。シミュレーション時間は一般的な勤務時間である8時間に相当する480分に設定します。また、最適化の際の出荷目標として60分間に20個の出荷を設定します。
ーシミュレーションー
シミュレーション完了時にダッシュボードが表示されます。サマリーから生産推移や生産数のグラフ、プロセス図から運搬プロセスの直前にある置き場の品目数を確認することで、状況を確認します。
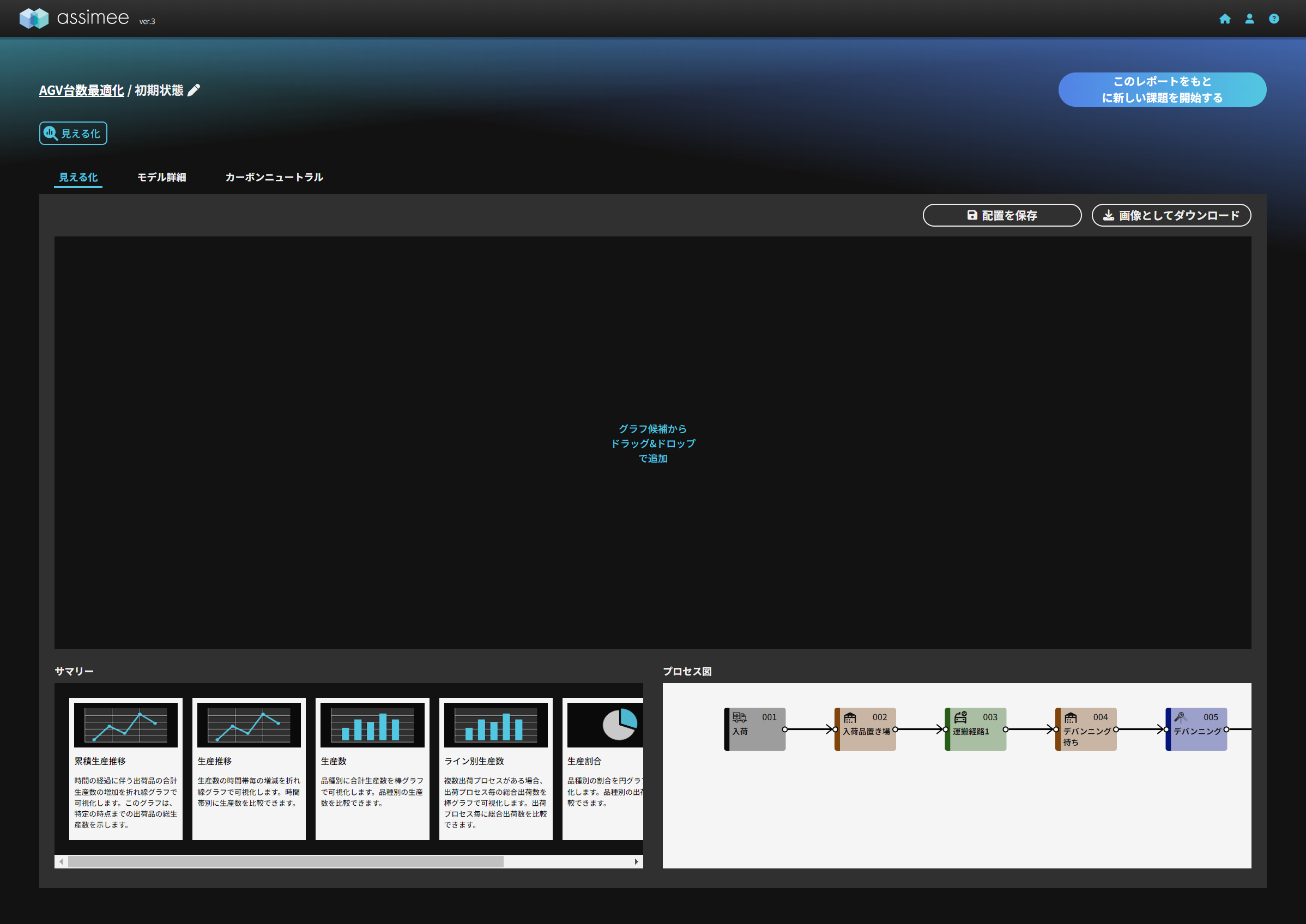
サマリーから「累積生産数」、「生産推移」のグラフ、プロセス図から「002入荷品置き場」、「006部品置き場」、「010加工品置き場」、「014出荷品置き場」を選び、ダッシュボードにそれぞれの在庫数のグラフを選択して表示させると以下のような結果となります。
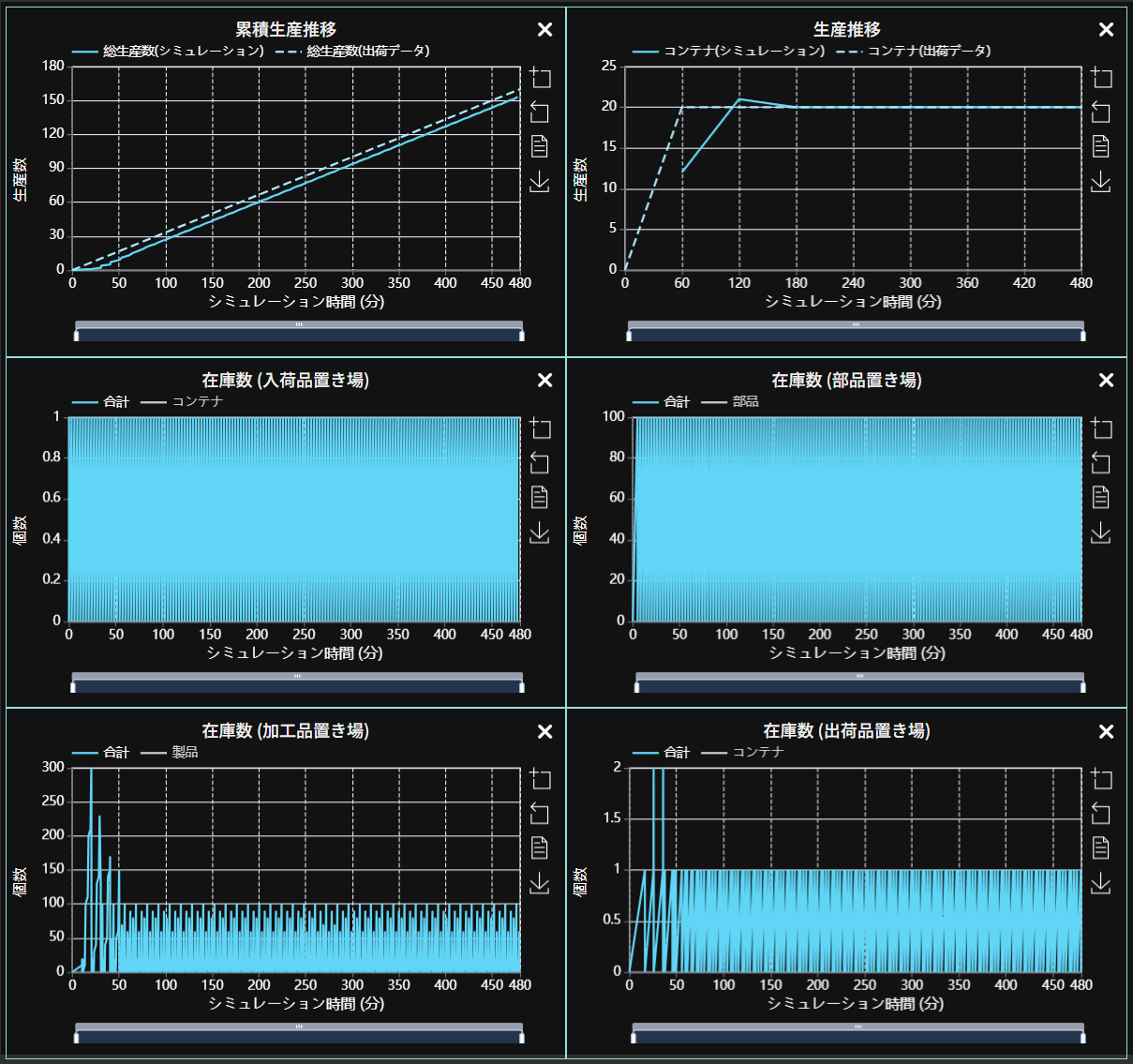
出荷目標として60分間に20個の出荷を設定しており、480分で160個のコンテナが出荷されます。対して、処理プロセスに大きな問題はないため、累積生産数が出荷目標にほとんど同じとなっています。今回はこの状態を起点として、累積生産数を維持しつつAGV台数の削減を行っていきます。
ーAGV台数の最適化ー
1回目のパラメーター推定(AGV台数の最適化)
AGVの台数を現在の10台から減らせるかを確認するためにパラメーター推定機能を使います。1回目のパラメーター推定では「003輸送経路1」、「007輸送経路2」、「011輸送経路3」、「015輸送経路4」のそれぞれのAGVの台数をパラメーターとし、上限を5台としてパラメーター推定を行いました。
*このように解(今回の場合はAGVの最適な台数)を求めるために、解を含む区間の中間点を求める操作を繰り返すことによって適切な値に迫る方法を二分法と言います。今回の場合、AGVの台数を5にした際に生産目標から乖離が見られれば、次は上限値を10、下限値を5として繰り返しパラメーター推定を行います。生産目標が達成される場合は次は上限値を5、下限値を3や4としてパラメーター推定を行います。
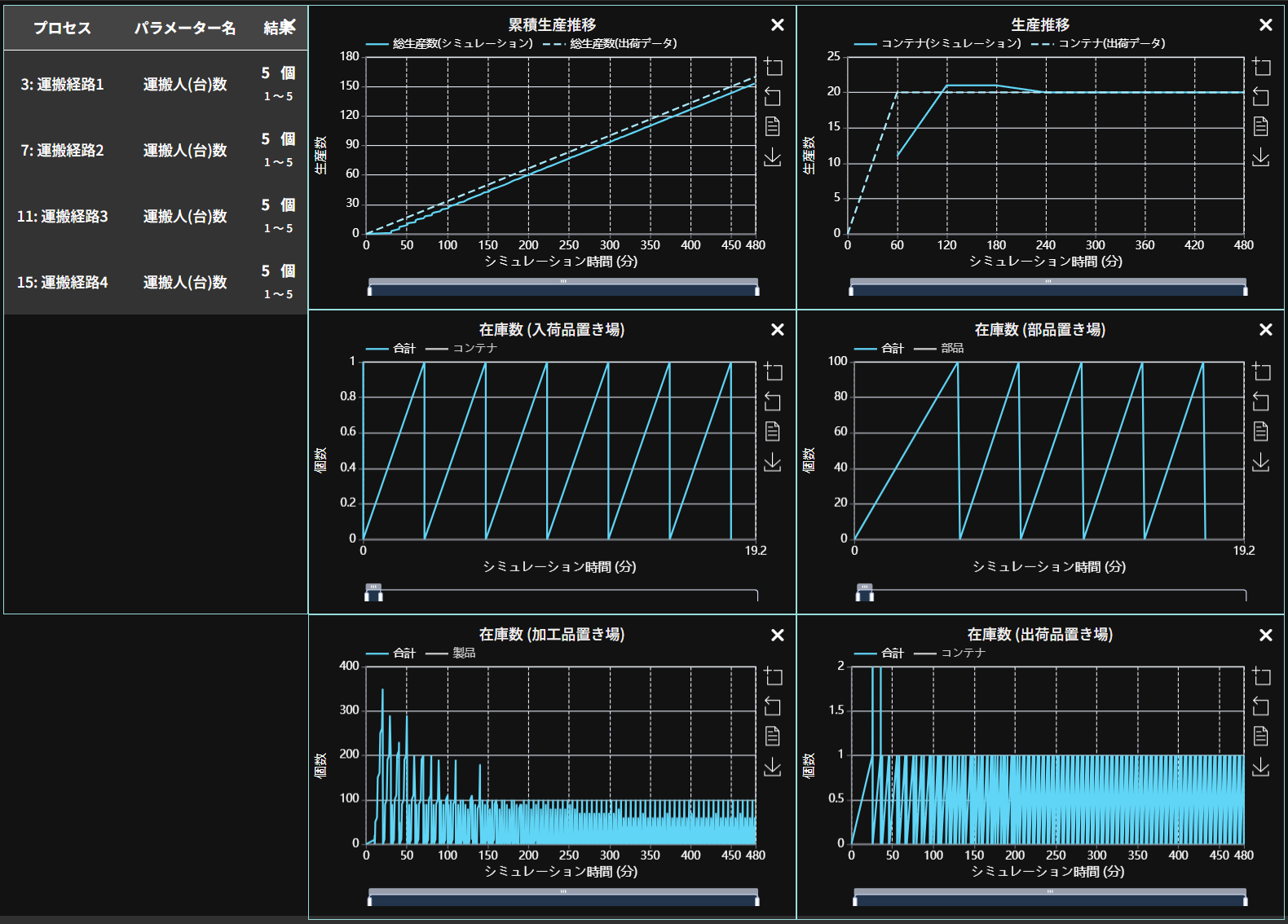
パラメーター推定の結果を見ると「003輸送経路1」、「007輸送経路2」、「011輸送経路3」、「015輸送経路4」のAGVの台数が上限の5台となっています。それぞれ5台ずつへ変更した後も、それぞれの運搬プロセスの直前にある「002入荷品置き場」、「006部品置き場」、「010加工品置き場」、「014出荷品置き場」の4か所の置き場の在庫数が輸送力の不足を示唆する右肩上がりになることはあります。このことはこの状態で問題なく運用できていることを意味しています。これで各10台から各5台まで台数を削減することが出来ましたが、さらに削減出来るかどうかパラメーター推定時の上限を変えて操作を繰り返します。
2回目のパラメーター推定(AGV台数の最適化)
AGVの台数を現在の各5台から削減できるかを確認するため、2回目のパラメーター推定では「003輸送経路1」、「007輸送経路2」、「011輸送経路3」、「015輸送経路4」のそれぞれのAGVの台数の上限を二分法に従って5台から3台としてパラメーター推定を行います。
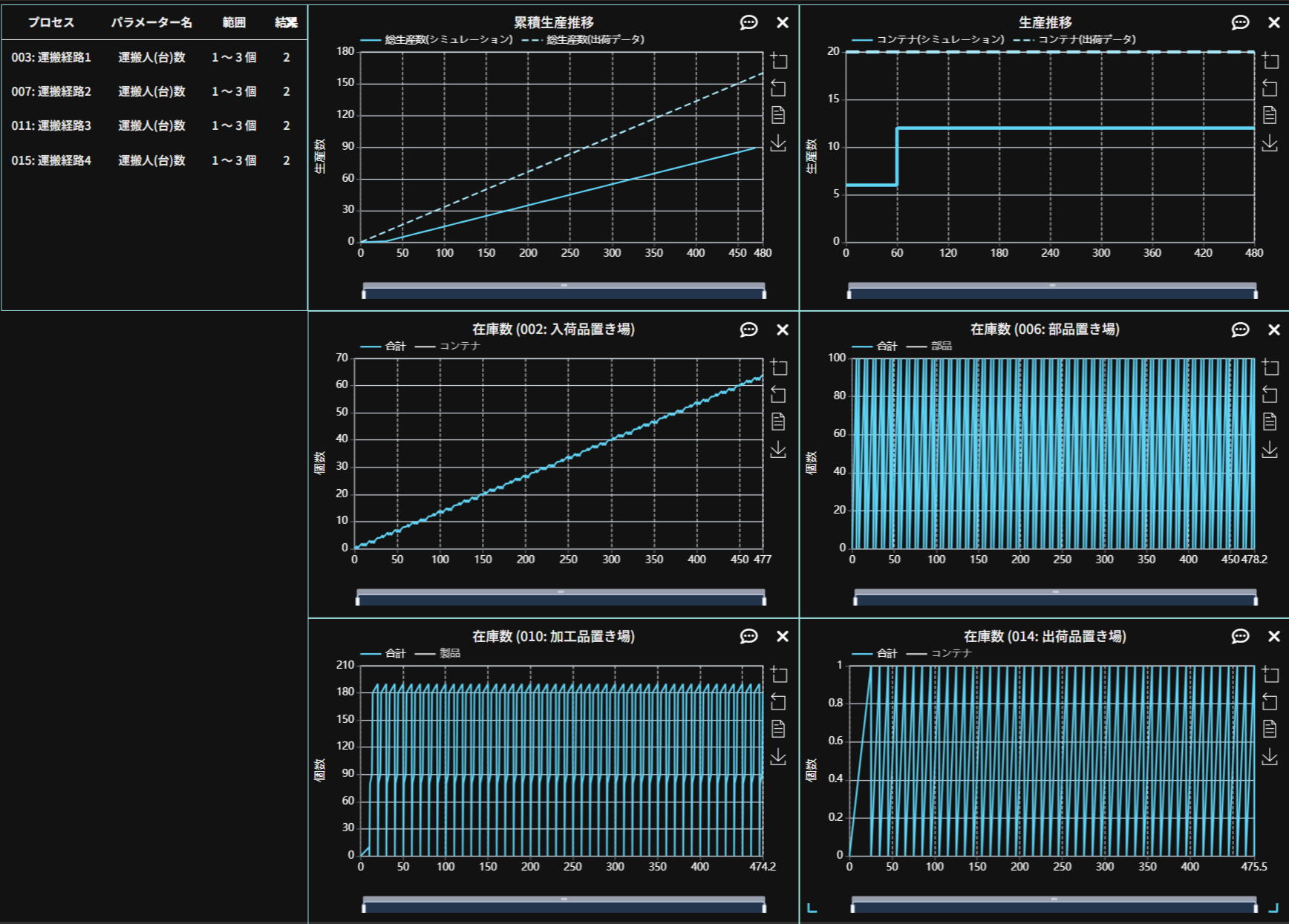
パラメーター推定の結果を見ると「003輸送経路1」、「007輸送経路2」、「011輸送経路3」、「015輸送経路4」のAGVの台数は上限の3台となっています。一方で「002入荷品置き場」、「006部品置き場」、「010加工品置き場」、「014出荷品置き場」の4か所の置き場の在庫数を見ると、一番上流側の「002入荷品置き場」の在庫数が右肩上がりになっていることに加えて出荷目標と実際の出荷量の間に開きが出ているため、3台では減らし過ぎであることが分かります。「006部品置き場」、「010加工品置き場」、「014出荷品置き場」については最も上流側の流量が絞られているため、在庫数が右肩上がりに増えていないと考えられるので、3台で十分とは言えません。
3回目のパラメーター推定(AGV台数の最適化)
AGVの台数上限を3台するのは減らし過ぎということが分かったため、次は「003輸送経路1」、「005輸送経路2」、「011輸送経路3」、「015輸送経路4」のそれぞれのAGVの台数の上限を5台と3台の中間である4台としてパラメーター推定を行います。

パラメーター推定の結果を見ると「003輸送経路1」、「007輸送経路2」、「015輸送経路4」のAGVの台数が上限の4台、「011輸送経路3」のAGVの台数が3台となっています。出荷目標と実際の出荷量の間に開きがある状態(ボトルネック発生中)も変わっていません。次に「002入荷品置き場」、「006部品置き場」、「010加工品置き場」、「014出荷品置き場」の4か所の置き場の在庫数をみると、「010入加工品置き場」の在庫数が右肩上がりになっているため、「011輸送経路3」がボトルネックになっており、ここのAGVの台数を3台にするのは減らし過ぎであることが分かります。よって「011輸送経路3」は4台で良いこと、「006部品置き場」が右肩上がりとなっておらず、荷物量が同じとなるはずの「007輸送経路2」も4台と決めることが出来ます。
4回目のパラメーター推定(AGV台数の最適化)
最後に確認として「007輸送経路2」と「011輸送経路3」のAGV台数を4台で固定した上で、「003輸送経路1」、「015輸送経路4」の2か所のAGVの台数の上限を4台として再度パラメーター推定を行ってみます。
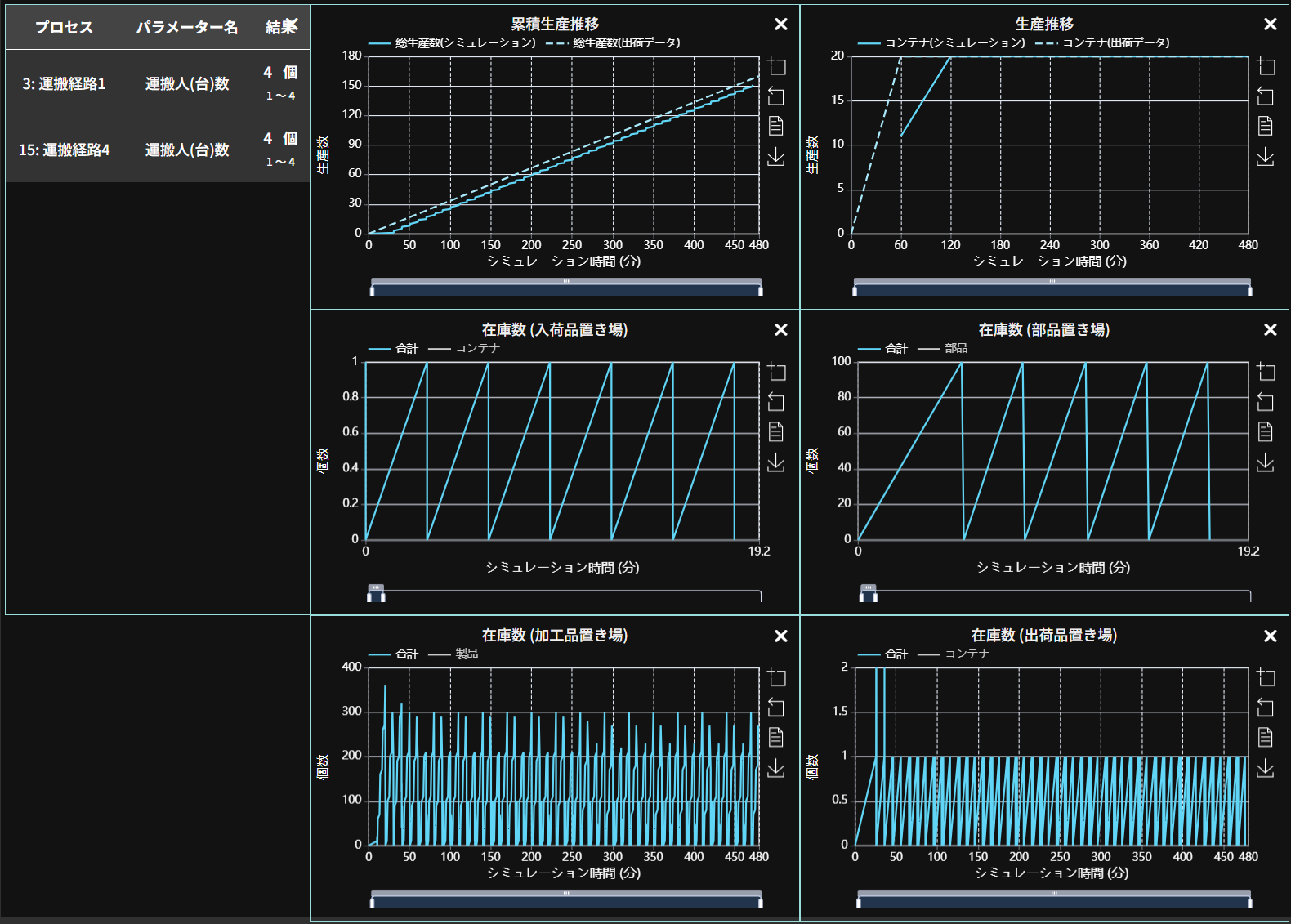
パラメーター推定の結果を見ると「003輸送経路1」、「015輸送経路4」のAGVの台数は共に4台となりました。出荷目標と実際の出荷量の間に開きは小さくなり、5台の時と同じように出荷目標を達成できていることが分かります。
また、「003輸送経路1」を3台にするのは減らし過ぎであることが分かっているので、「003輸送経路1」にはAGVが4台必要です。また「003輸送経路1」、「015輸送経路4」と荷物量は同じになると考えられるため、「015輸送経路4」にもAGVが4台必要と分かり、台数を決めることが出来ました。
パラメーター推定を繰り返すことで、「003輸送経路1」、「005輸送経路2」、「011輸送経路3」、「015輸送経路4」のAGV台数は各4台、合計16台となりました。このようにして、出荷目標を満たしつつ、初期の40台から24台少なくすることが出来ることが分かりました。
ーまとめー
今回は工場の生産ラインでの輸送に必要なAGVの台数を決める方法について解説しました。製造ラインが複雑になるにつれて、輸送に必要なAGVの台数や人員の数を決定するのは計算が複雑で難しくなります。しかし、ラインのモデル化を行っていれば、assimeeを使用することで、出荷する荷物量が毎日頻繁に変動するような場合でも、最適なAGV台数や人員数を簡単かつ迅速に(数分で)計算することが可能です。