概要
今回の記事ではassimeeを使ってライン生産方式のプロセスのシミュレーションを実行し、最適化を行うまで解説します。まず、ライン生産方式の概要、メリットとデメリット、モデルの作成とシミュレーションの実行、結果の分析とパラメーター推定によってラインのプロセスを最適化するまで解説します。
*この記事は以前に公開した記事を再編集および更新したものです。
ライン生産方式の解説
ライン生産方式とは
ライン生産方式は、各プロセスが1つのラインに連続して並び、工程ごとに配置された作業者が部品を取り付けていくことで連続的に製品の生産を行う方式です。生産ラインでは、製品が各プロセスのゾーンを通過しつつ、ベルトコンベア上を流れていきます。作業者は製品の周りを移動しながら、決められた手順に沿って部品を取り付けていきます。また、製品がラインを自走していく場合や、AGV(無人搬送車)に積載される場合などもあります。ライン生産方式の代表的な事例としては、1900年代初めにフォードがT型フォードを大量生産するために導入したものが有名です。日本でも1960年代頃から自動車や家電製品の大量生産を行うために導入され、現在でも自動車産業や航空機産業などの多くの工場で使用されている生産方式です。
ライン生産方式のメリットとデメリット
ライン生産方式のメリットとデメリットを以下に挙げていきます。
メリット
- 高い生産効率:工程ごとに作業者や機械を配置することで、生産効率が向上
- 作業の特化化:各工程ごとに作業内容を特化させることで、作業者の専門化が進み、品質や生産性が向上
- ボトルネックの可視化:ライン上のボトルネック工程を特定しやすく、改善の余地を見つけやすい
デメリット
- フレキシブルさの低下:ライン生産方式では、工程ごとに固定の順序が必要です。そのため、生産の変更や製品のバリエーションに対応する際には柔軟性に欠ける
- ボトルネックの影響:ライン上の一つの工程で問題が生じると、全体の生産性に影響を及ぼす可能性
- 初期投資の大きさ:ラインや機械の設備投資が必要で初期投資が大きくなる
モデル作成
今回はライン生産方式を使った生産工程として入荷、在庫(置き場)、作業、在庫、検品、出荷のプロセスからなる下図のようなモデルを考えます。

プロセス図を作成した後、各プロセスカードにパラメーターを設定します。
シミュレーション結果
今回はシミュレーション時間を300分と設定してシミュレーションを実行します。
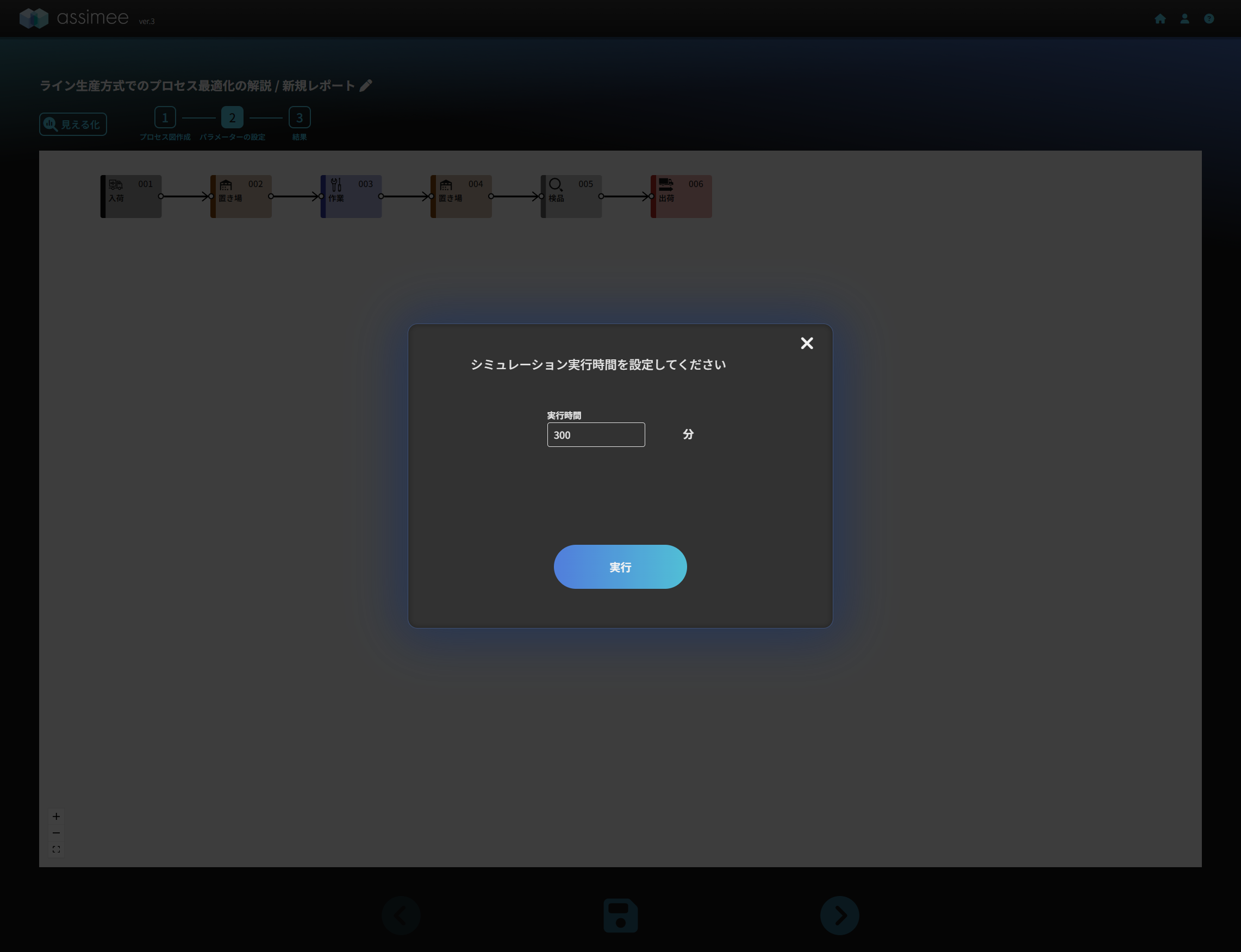
シミュレーションが終わるとダッシュボードが表示され、シミュレーション全体の結果やプロセス毎の結果を確認することが出来ます。ダッシュボード左下のサマリーから希望のグラフを選択することで確認することが出来ます。
ここでは「累積生産推移」、「生産推移」、「生産数」、「生産割合」の4つのグラフを表示しています。
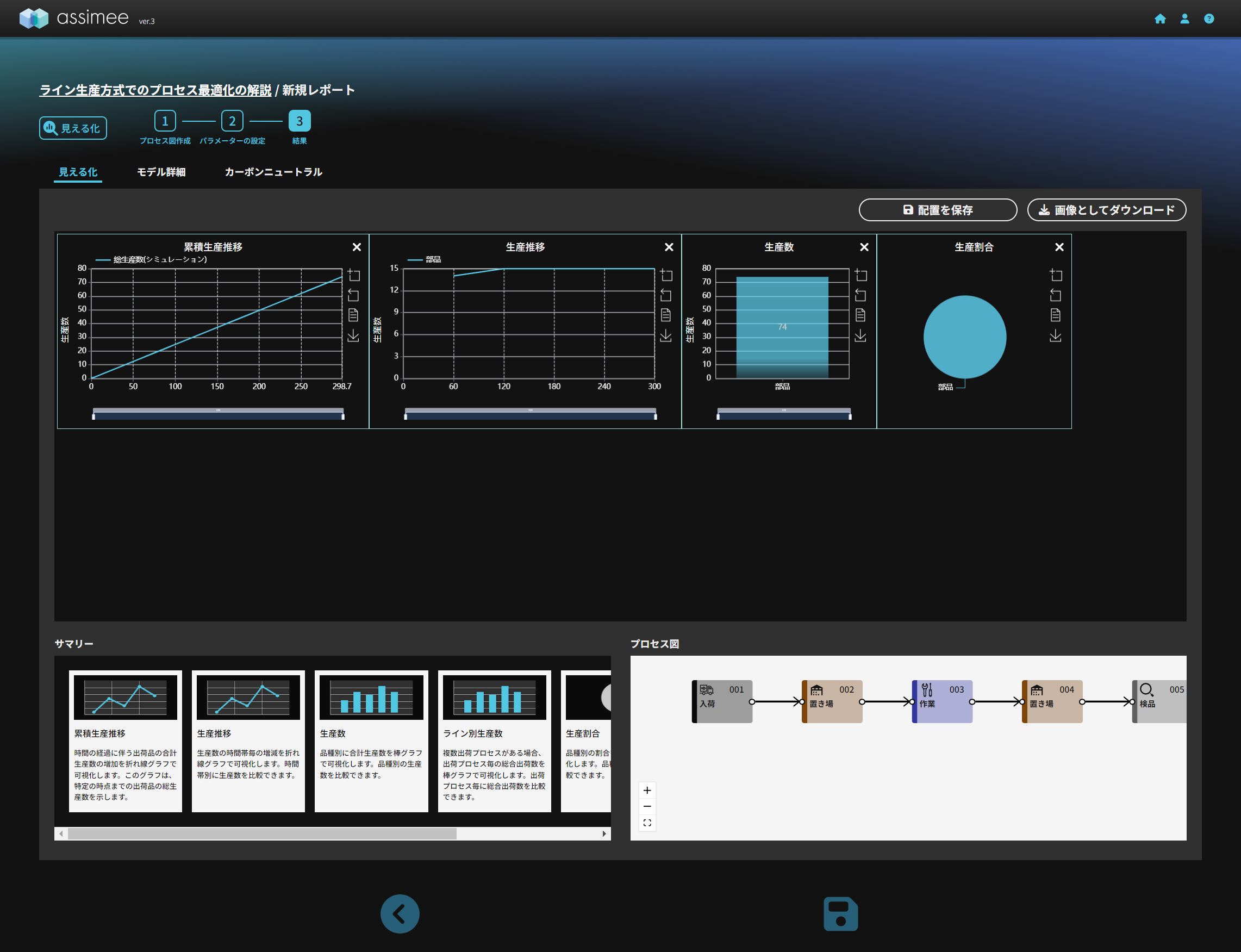
このようにassimeeでは様々なプロセスカードを使ってモデルを作成し、パラメーターを設定してシミュレーションを行うことで、生産ラインを実際に変更しなくても生産推移や生産数を計算することが出来ます。
次は最適化機能を使ってモデルのパラメーターを推定してみます。
パラメーター推定
今回のパラメーター推定では、下図のように「003作業」を選択します。
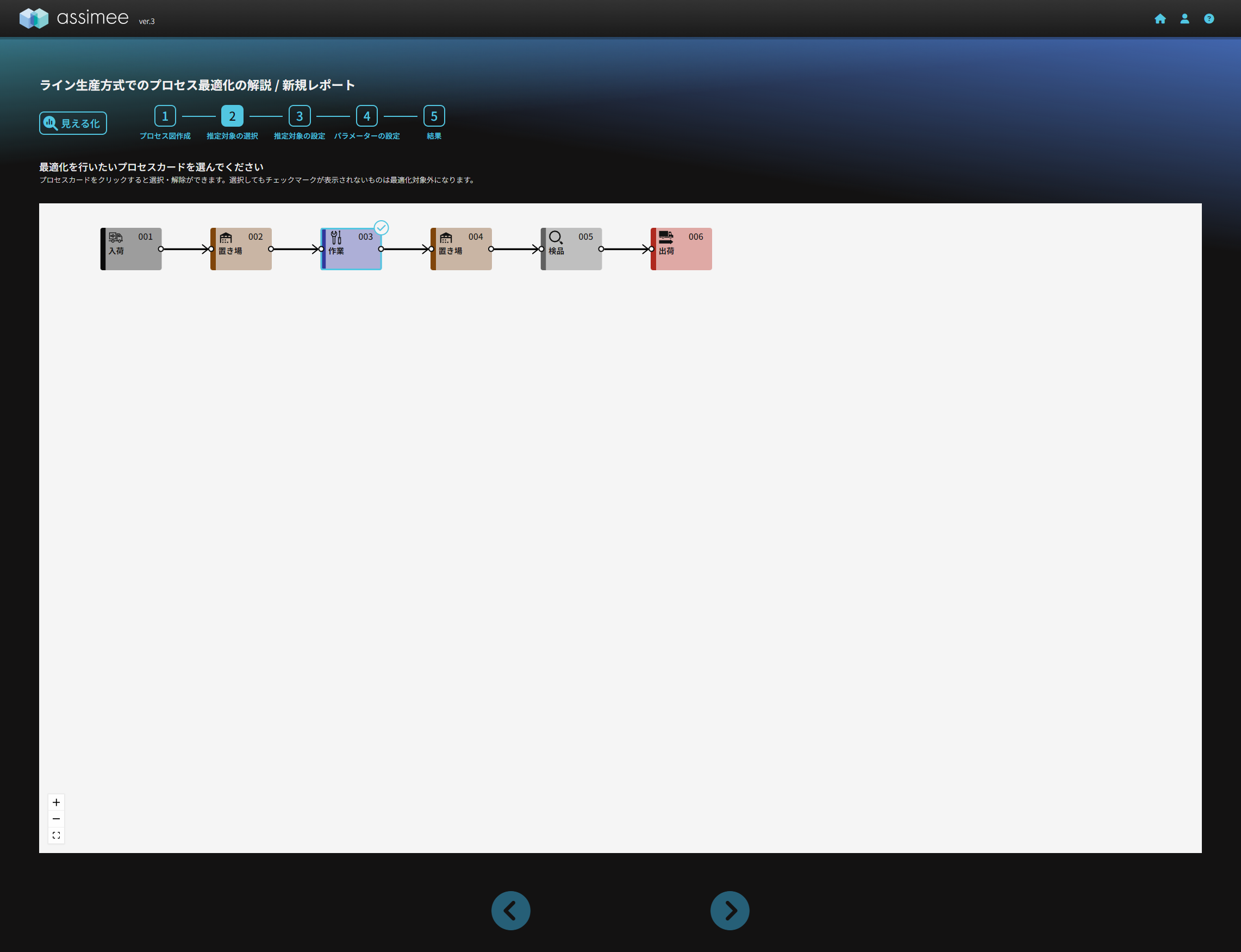
次にパラメーター推定を行うパラメーターを選択します。選択したプロセスに対して、最適化が可能なパラメーターの一覧が表示されます。「処理時間」、「立ち上げ時間」、「修理時間」、「故障時間」、「段取り替え時間」、「工具交換時間」、「工具交換間隔」など様々なパラメーターを対象にパラメーター推定をすることが出来ます。
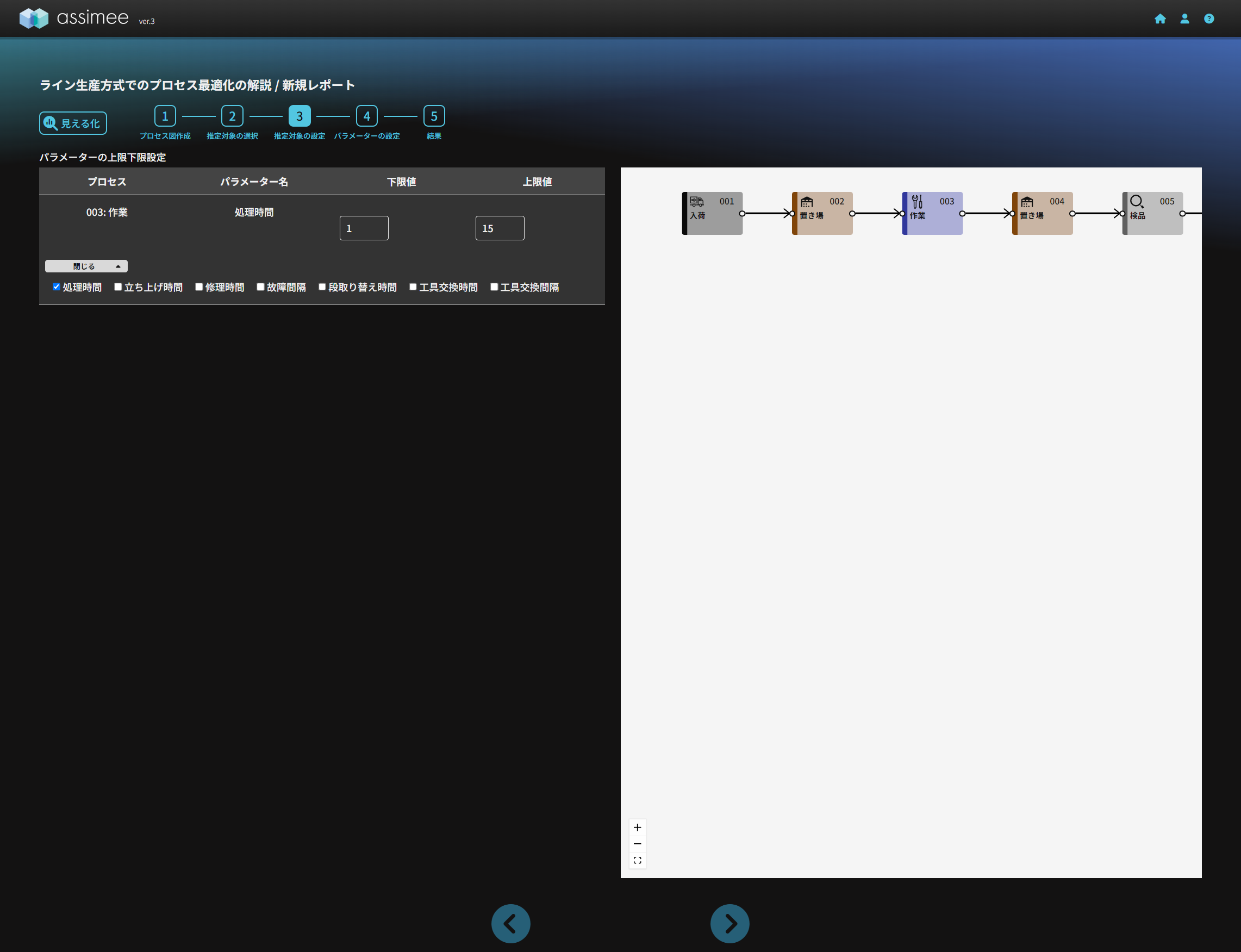
次にパラメーターの上下限値を設定します。今回は、下限値を1、上限値を15としました。
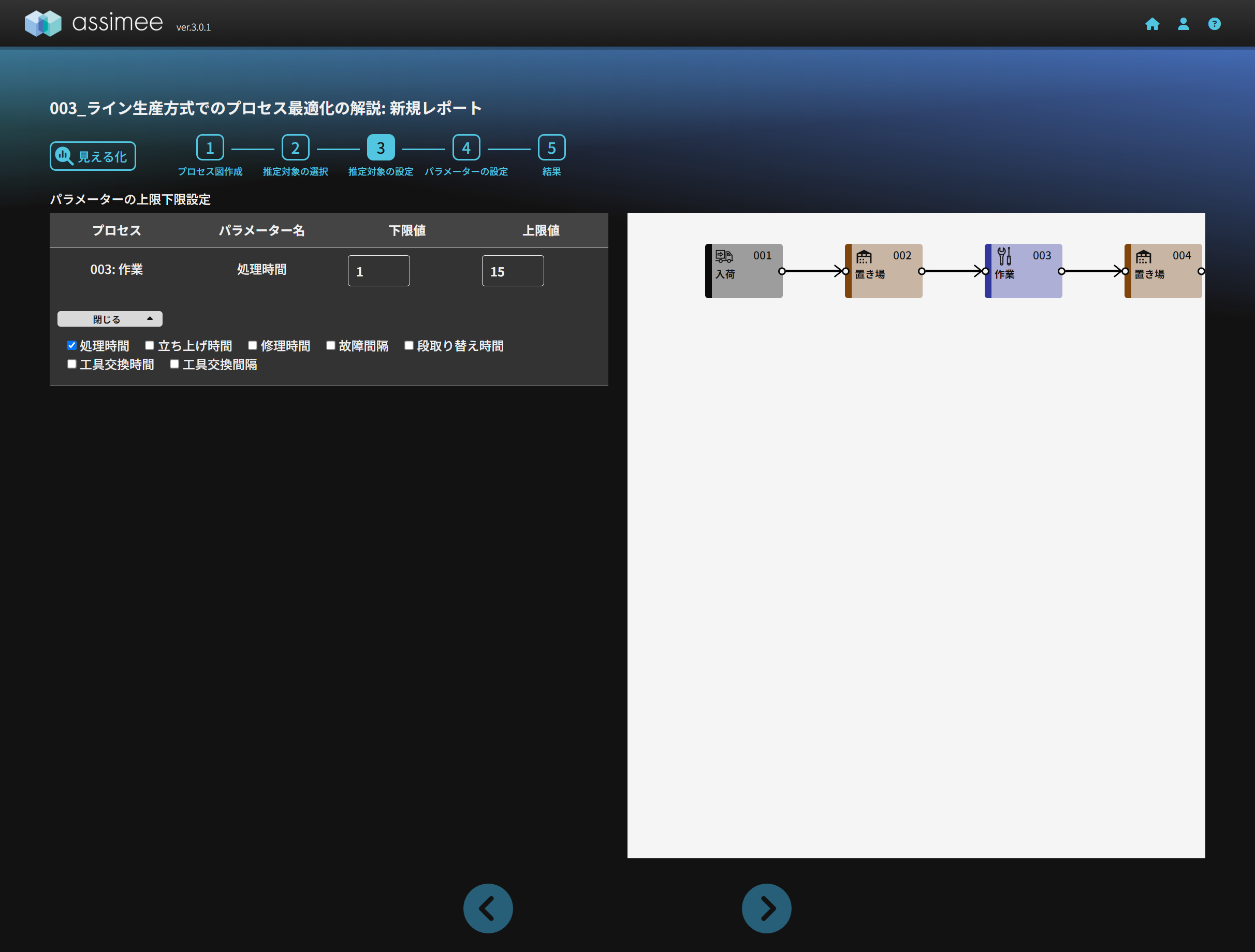
assimeeでは以下の図のように出荷目標を設定した後、任意のプロセスのパラメーターを対象に出荷目標を満たすようにパラメーター推定(最適化)を行うことが出来ます。出荷目標を設定したらパラメーター推定を行います。
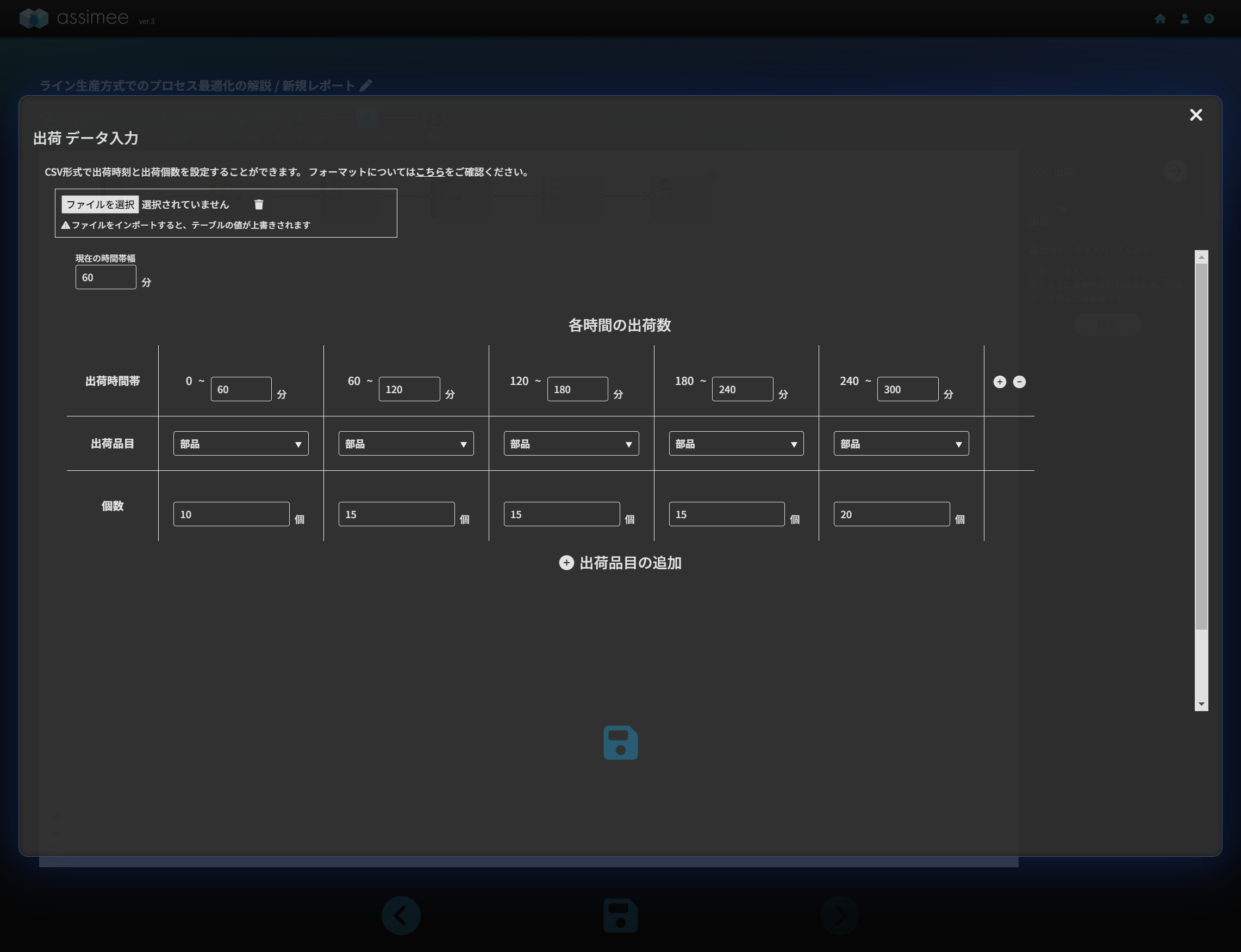
パラメーター推定が終了すると再びダッシュボード画面が表示されパラメーター推定の結果を分析することが出来ます。
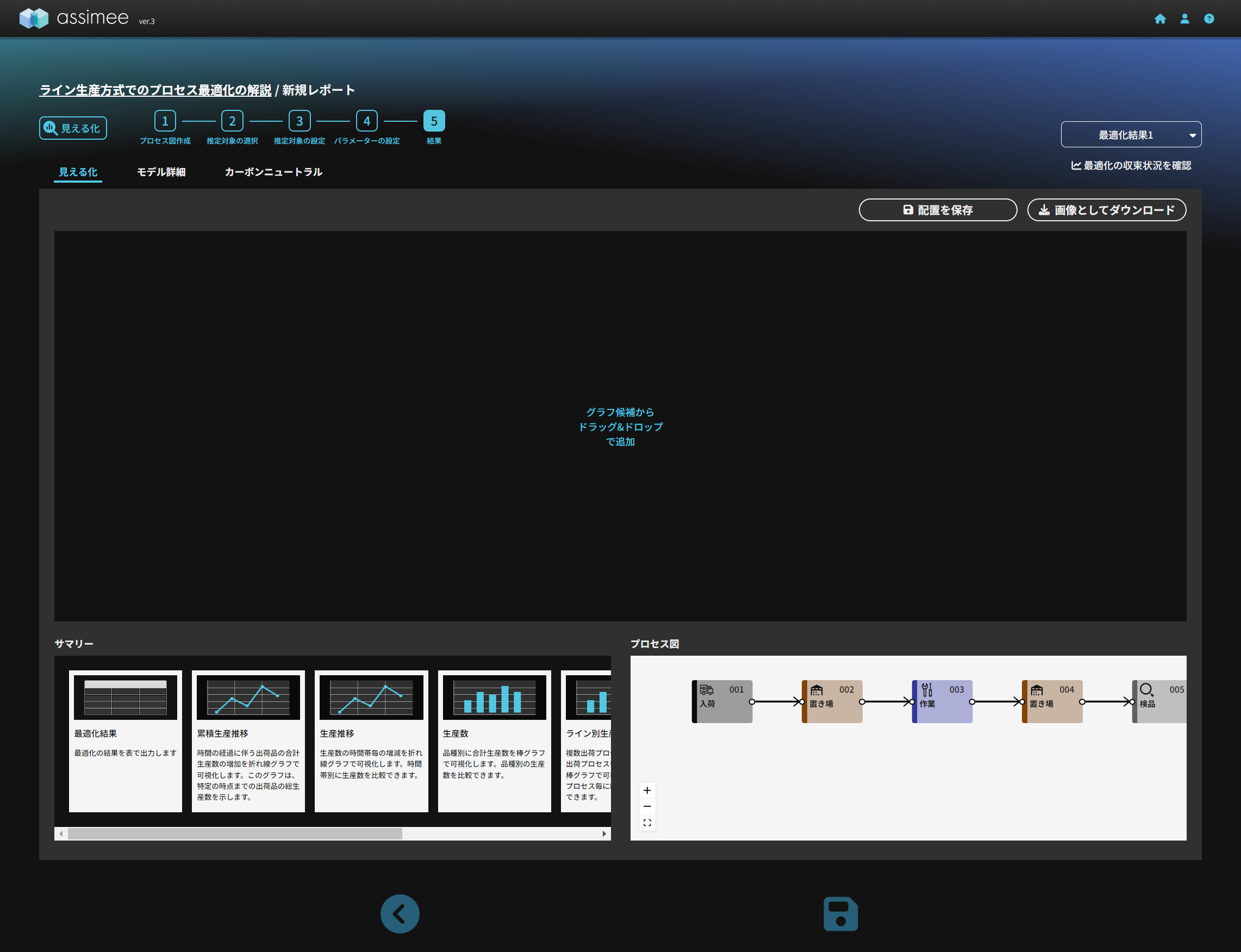
ここでは「最適化結果」、「累積生産推移」、「生産推移」の3つのグラフを表示してみました。「累積生産数推移」や「生産推移」のグラフに生産目標が同時に表示されており、生産目標が満たされていることが分かります。
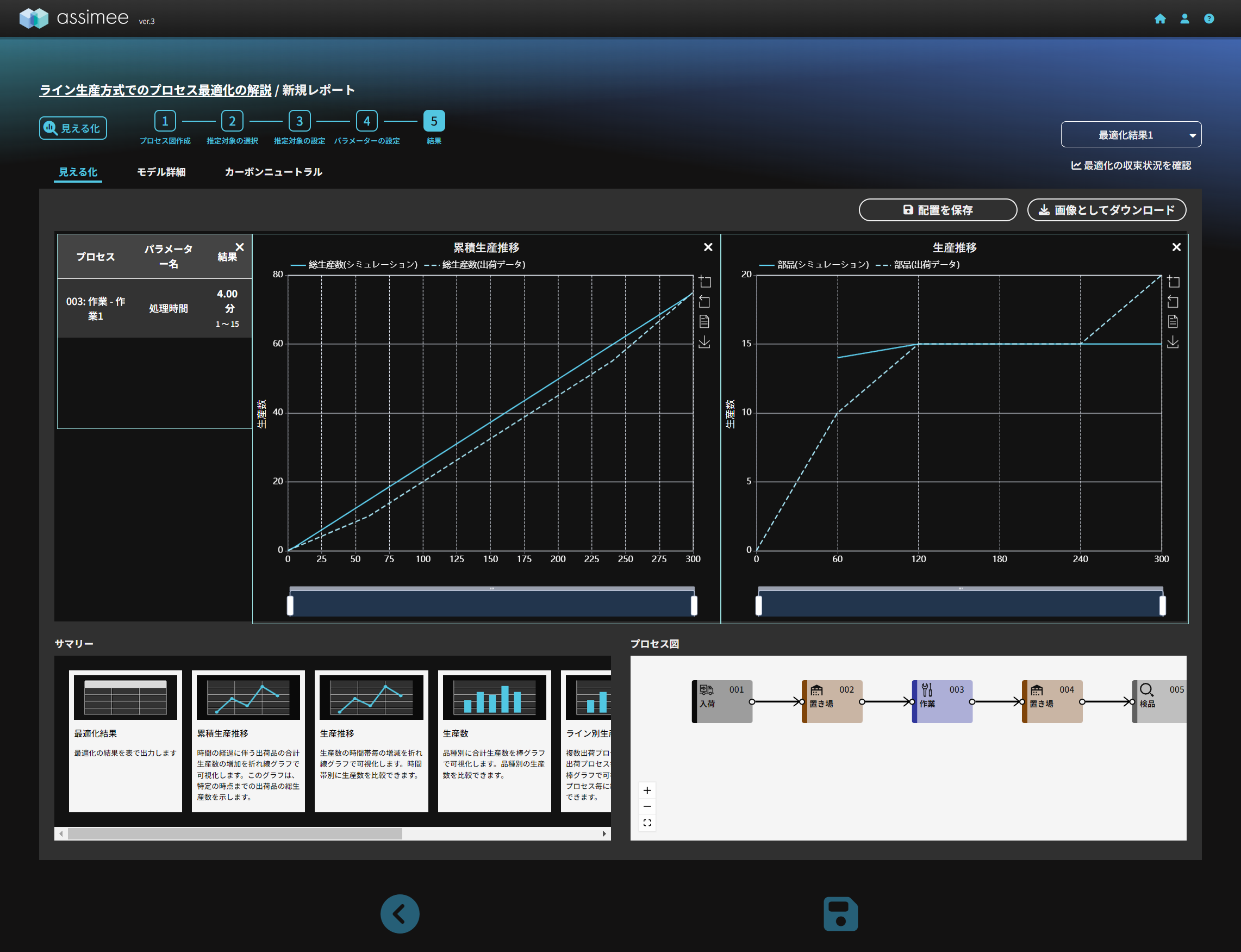
最適化の状態と別なシナリオの確認
ダッシュボード画面の右上のボックスに「最適化結果1」などと表示されます。この部分には今回行ったパラメーター推定の結果の一覧が最大120通り保存されており、ドロップダウンメニューで選択することで、他の結果を確認することが可能です。一番上に表示されるのは最善の結果(上図)で一番下は120番目に良い(一番悪い)結果(下図)となります。結果を比較してみると、120番目の方が明らかに実際の生産量が遥かに多く、生産目標との合いが悪くなっていることが分かります。
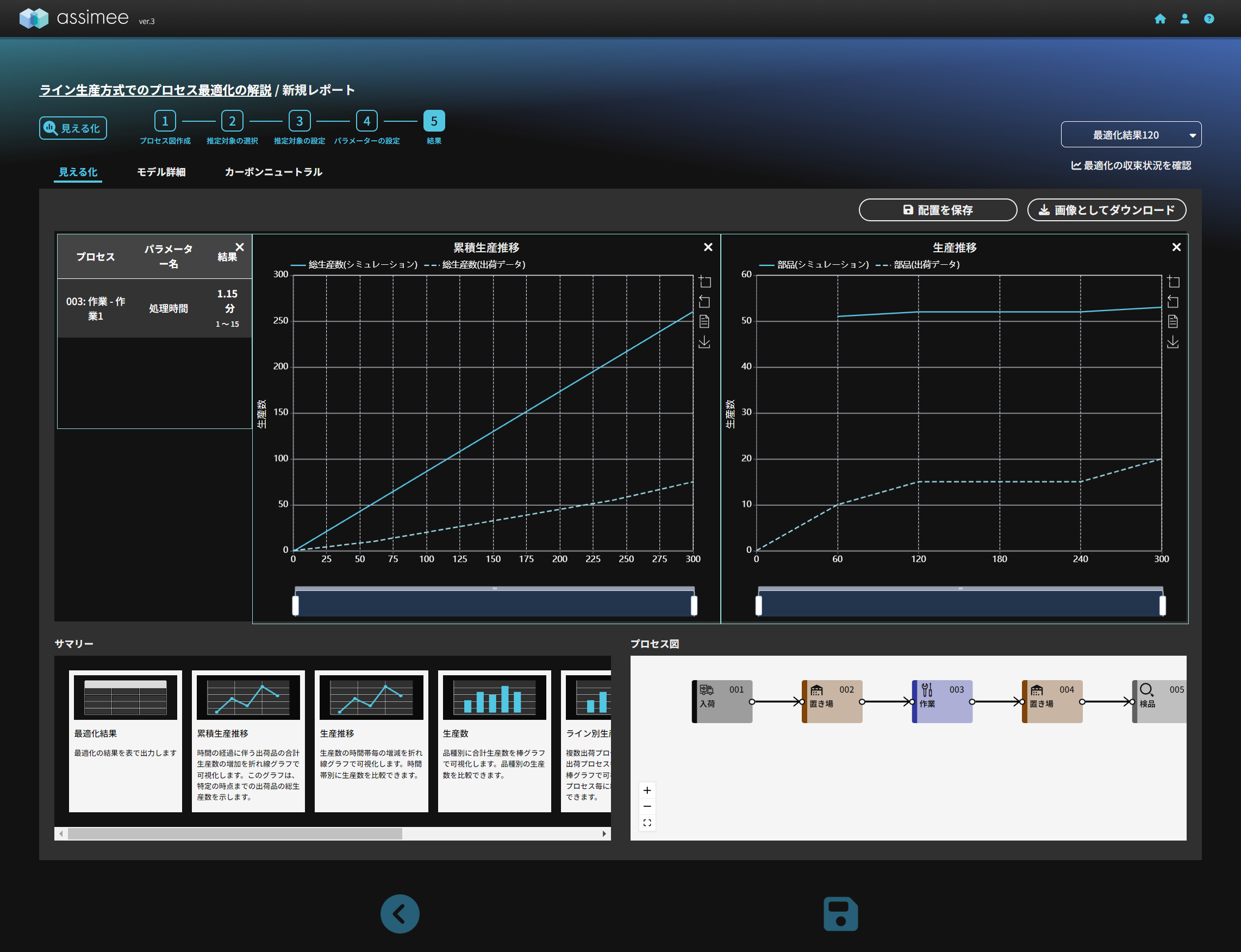
今回の例では、プロセスが単純でパラメーターが1つしかないことから最適と考えられる結果は1つしか得られませんが、複数のパラメーターが存在する場合には、最適と考えられる結果が複数得られる可能性があります。ユーザーはこれらの結果を元に条件に合ったパラメーターを選択することができます。
また、ダッシュボードの右上から最適化の収束状況を確認することが出来ます。まだ改善の余地があると思われる場合は「追加実行する」ボタンを押して最適化を継続することで、結果が改善することがあります。
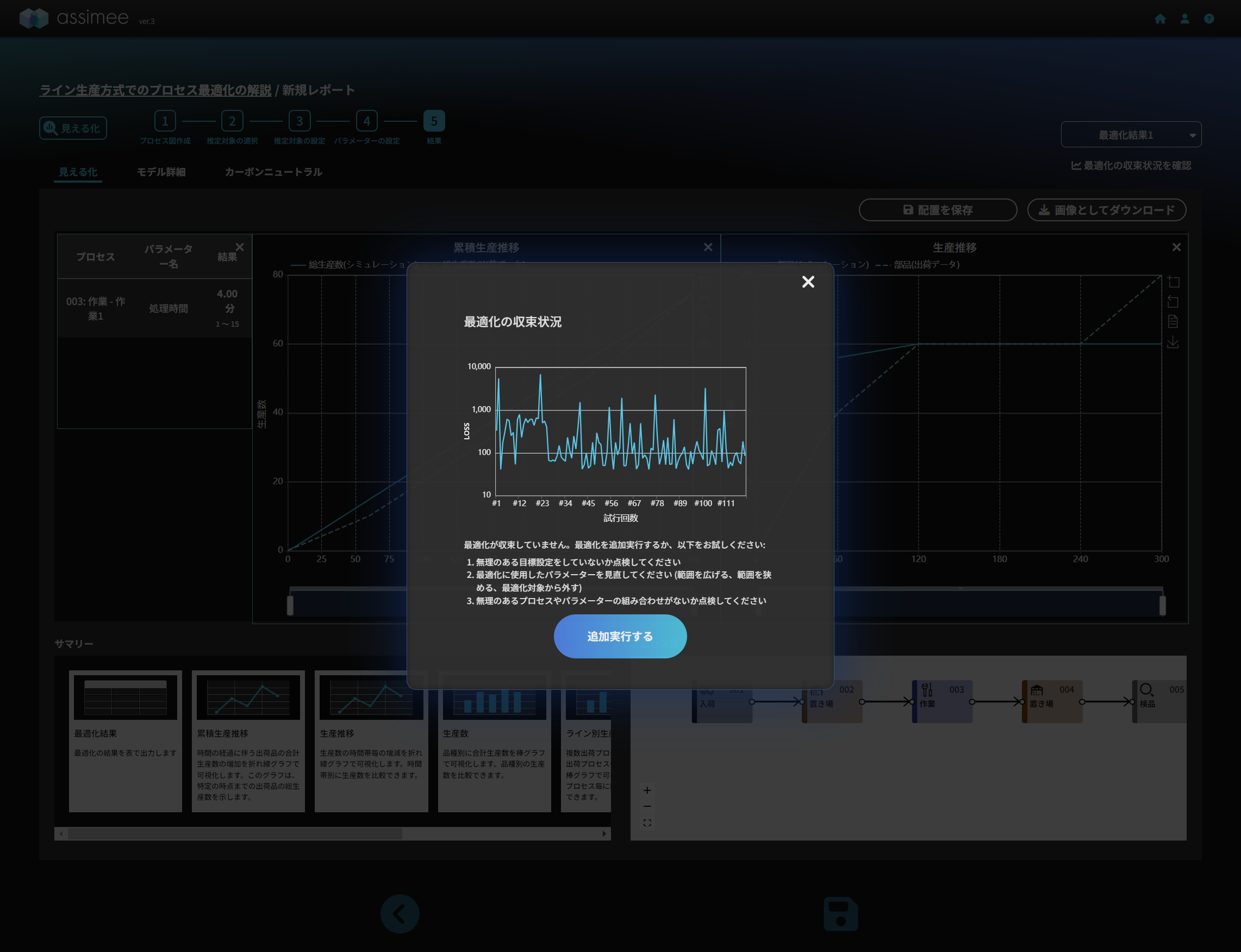
まとめ
今回の記事ではライン生産方式を例に挙げて、assimeeによるモデルの作成、シミュレーションとパラメーターの推定までを解説しました。assimeeではブラウザを使うことさえできれば、PC上に手軽に生産ラインを再現してシミュレーションによってモデルを検証したり、モデルのパラメーターを決定することが出来ます。今回は作業の処理時間を対象にパラメーターを推定しましたが、プロセスに必要な人員を人の最適化で決定することも可能です。