概要
今回の記事では、人員の生産性を考慮して人員配置を決定する方法について解説します。作業員の配置を行う場合には、個人の能力を考慮する必要があります。しかし、実際に生産ラインを使って配置計画を検証することが出来ないので、現場担当者の経験や勘に頼る必要がありました。そのため、担当者の業務負担が大きくなったり、業務の属人化の問題が発生していました。個人の生産性を把握していれば、最適な人員の配置をassimeeを使ったシミュレーションで誰にでも簡単に決めることが可能です。
モデル
以下のようなモデルを使います。

入荷した部品をプレス作業と曲げ作業で加工して製品にするラインを仮定します。それぞれの作業は1人の担当です。また、ラインをAとBの2本設置しているので、モデル全体では2つのプレス作業と2つの曲げ作業を担当する作業員が1人ずつ合計で4人いる設定です。また、それぞれのラインの生産数の違いを分かりやすくするために、製品名にラインAでは「製品A」、ラインBでは「製品B」といった違いを付けます(区別用のラベルで製品名による違いはない想定です)。
STEP1 プロセス図を作成する
以下のようにプロセスカードを設置してモデルを作成していきます。
入荷プロセス:
特に変更なし
置き場プロセス:
プロセス名を「入荷品置き場」へ変更
分岐プロセス:
特に変更なし
分岐先として2つのプロセスを設置:
分岐先として2つの置き場プロセスを用意します。
置き場プロセス:
プロセス名を「置き場A1」へ変更
以下はラインAの項へ
置き場プロセス:
プロセス名を「置き場B1」へ変更
以下はラインBの項へ
ラインA
置き場プロセス(再掲):
プロセス名を「置き場A1」へ変更
作業プロセス:
プロセス名を「プレス作業A」へ変更
置き場プロセス:
プロセス名を「置き場A2」へ変更
作業プロセス:
プロセス名を「曲げ作業B」へ変更
組立プロセス:
プロセス名を「梱包」へ変更
置き場プロセス:
プロセス名を「出荷品置き場」へ変更
ラインB
置き場プロセス(再掲):
プロセス名を「置き場B1」へ変更
作業プロセス:
プロセス名を「プレス作業C」へ変更
置き場プロセス:
プロセス名を「置き場B2」へ変更
作業プロセス:
プロセス名を「曲げ作業D」へ変更
組立プロセス:
プロセス名を「梱包」へ変更
「出荷品置き場」へ合流
合流後
置き場プロセス(再掲):
プロセス名を「出荷品置き場」へ変更
ローラーコンベアー:
特に変更なし
出荷プロセス:
特に変更なし
STEP2 パラメーターを設定する
以下のようにモデルにパラメーターを設定します。
001入荷:
品目を「部品」、個数を「20個」、時間間隔を「1分」と設定
002入荷品置き場:
容量を「1000個」と設定
003分岐:
1回あたりの処理時間を「0分」と設定
*処理時間を「0」とすることでパススルーとなります。
分岐条件:
ランダム設定(変更せず)
ラインA
004置き場A1(再掲):
容量を「1000個」と設定
005プレス作業A:
1回あたりの処理時間を「5分」、
対象品目を「部品」、個数を「1個」と設定
006置き場A2:
容量を「1000個」と設定
007曲げ作業B:
1回あたりの処理時間を「20分」、
対象品目を「部品」、個数を「1個」と設定
008梱包:
1回あたりの処理時間を「1分」と設定、
対象品目を「部品」、個数を「1個」、
出力品目を「製品A」、個数を「1個」と設定
ラインB
012置き場B1(再掲):
容量を「1000個」と設定
013プレス作業C:
1回あたりの処理時間を「15分」、
対象品目を「部品」、個数を「1個」と設定
014置き場B2:
容量を「1000個」と設定
015曲げ作業D:
1回あたりの処理時間を「10分」、
対象品目を「部品」、個数を「1個」と設定
016組立梱包:
1回あたりの処理時間を「1分」、
対象品目を「部品」、個数を「1個」、
出力品目を「製品B」、個数を「1個」と設定
合流後
009出荷品置き場:
容量を「1000個」と設定
010ローラーコンベアー:
搬送時間を「1分」、最大積荷個数を「10個」と設定
011出荷:
特に設定なし
シミュレーション結果の分析をする
シミュレーションの結果を確認する
モデルを作成したら保存を行い、シミュレーション時間を300分に設定してシミュレーションを行います。上記のようにパラメーターが設定されていれば、以下のような図が表示されます。*今回のモデルでは分岐に乱数が含まれているため、完全に一致しない可能性があります。
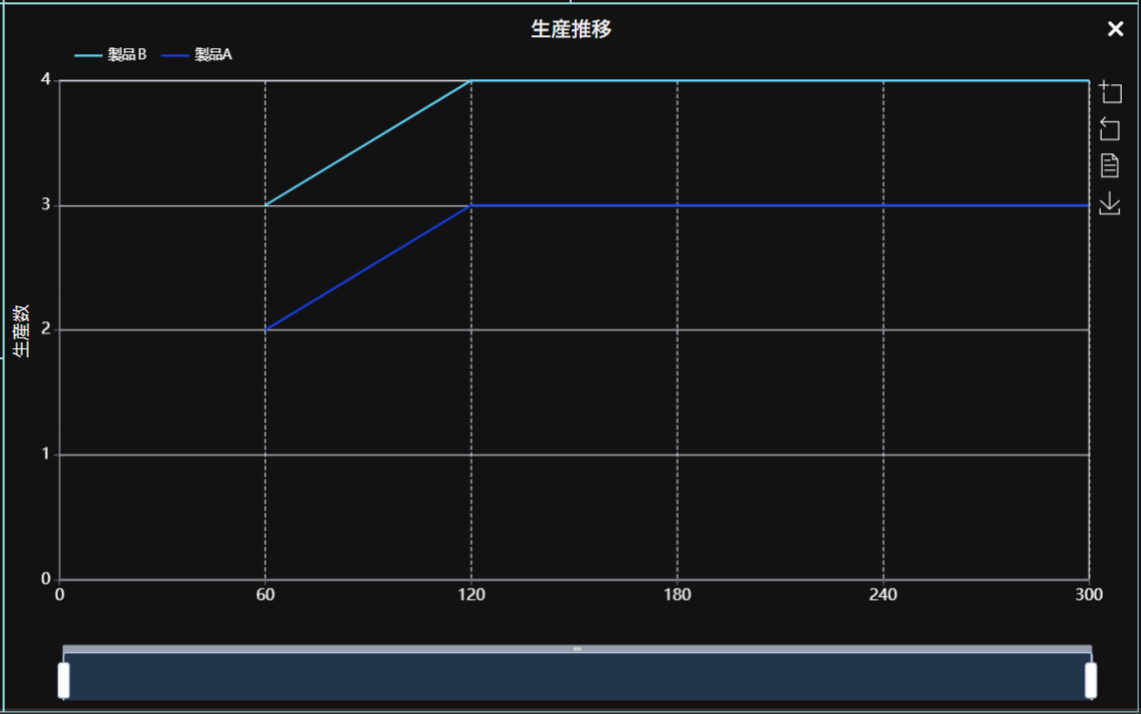
人員による生産性の違いを設定する
次に人員を4つの作業プロセス(「005プレス作業A」、「007曲げ作業B」、「013プレス作業C」、「015曲げ作業」)に配置することを仮定してシミュレーションを繰り返して最適な配置を考えてみましょう。今回の実験では組立プロセスへの人員配置は考えません。
配置する4人の作業員はプレス作業と曲げ作業に対して以下のスキル(処理時間)を持っていると仮定します。わかりやすくするため、処理時間に大きな差があるやや極端な設定になっています。
プレス処理時間(単位 分) | 曲げ処理時間(単位 分) | |
作業員A | 5 | 15 |
作業員B | 10 | 20 |
作業員C | 15 | 5 |
作業員D | 20 | 10 |
モデルに対する作業員の組み合わせを考えると次の12通りとなります。
ラインA担当 (プレス作業A-曲げ作業B) | ラインB担当 (プレス作業C-曲げ作業D) | |
組合わせ1 | A-B | C-D |
組合わせ2 | A-B | D-C |
組合わせ3 | B-A | D-C |
組合わせ4 | B-A | C-D |
組合わせ5 | A-C | B-D |
組合わせ6 | A-C | D-B |
組合わせ7 | C-A | D-B |
組合わせ8 | A-C | B-D |
組合わせ9 | A-D | B-C |
組合わせ10 | A-D | C-B |
組合わせ11 | D-A | C-B |
組合わせ12 | D-A | B-C |
シミュレーションで生産性を検証する
全ての組み合わせに対して総当たりで処理時間を変えながら、12回のシミュ―ションを行い結果(生産数)を比較してみます。*モデルをコピーしてそれぞれ作業プロセスの名前に添え字を入れて区別し、設定を変えていく方法が混同がなく便利です。
結果は以下の通りとなります。
ラインA担当と時間 (プレス作業A-曲げ作業B) | ラインB担当と時間 (プレス作業C-曲げ作業D) | 300分での総生産数 | |
組合わせ1 (モデル作成時の設定) | A-B(5-20) | C-D(15-10) | 33 |
組合わせ2 | A-B(5-20) | D-C(20-5) | 28 |
組合わせ3 | B-A(10-15) | D-C(20-5) | 33 |
組合わせ4 | B-A(10-15) | C-D(15-10) | 36 |
組合わせ5 | A-C(5-5) | B-D(10-10) | 86 |
組合わせ6 | A-C(5-5) | D-B(20-20) | 71 |
組合わせ7 | C-A(15-15) | D-B(20-20) | 31 |
組合わせ8 | C-A(15-15) | B-D(10-10) | 46 |
組合わせ9 | A-D(5-10) | B-C(10-5) | 58 |
組合わせ10 | A-D(5-10) | C-B(15-20) | 43 |
組合わせ11 | D-A(20-15) | C-B(15-20) | 28 |
組合わせ12 | D-A(20-15) | B-C(10-5) | 43 |
シミュレーションの結果、もっとも生産数が多いのは
組合わせ5 | A-C(5-5) | B-D(10-10) | 86 |
となりました。今回の例では作業員間の処理時間に大きな差があることもあり、比較的大きな差が付く明確な結果となりました。
このように、実際のラインで試すことなく、シミュレーションだけを使って人員配置を決めることが可能です。また、色々なパラメーターの組み合わせを試すことが出来るので、生産を優先する繁忙期の場合にはもっとも生産量の多い配置、作業員の経験を積ませてスキルをアップさせたい場合は、作業員にスキルの低い作業を割り当てて訓練するためにこの配置というように、ライン運用の切り替えを立案することも容易にできます。
まとめ
今回はassimeeのシミュレーションを使って個人の生産性を考慮して人員配置を決める方法について解説しました。同様にして現状の人員配置をシミュレーションに使うことで、生産のボトルネックを探索することも可能です。現実の生産ラインを使ってテストや試行錯誤を行うことは非常に難しいので、誰にでも実行可能なシミュレーションで最適な稼働条件を決めたり、ボトルネックを見つけることが、今後は更に重要になると予想されます。次の試みとして、作業員の配置ではなくラインの形状に変更を入れた場合にシミュレーションで確認・分析する方法を解説する予定です。
assimeeでは、実際の製造プロセスをモデル化し、シミュレーションすることで、プロセスの見える化や潜在的な課題の洗い出しを行うことができます。製造プロセスのデジタル化や課題解決でお悩みの方は、ぜひお問い合わせください。