概要
今回の記事では、ブース生産方式のモデル作成と見える化について解説します。ブース生産方式とは、「ブース」と呼ばれる作業エリアを設け、あらかじめ用意された生産キットや工具を使用して製品の一部または全体を生産する方式です。この方式は多品種少量生産に適しており、製品や工程に応じた異なるブース、生産キット、スキルを持つ作業人員を用意することで、柔軟で効率的な生産が可能です。
ブース生産方式は、自動車、エレクトロニクス、アパレルなど、製品ごとに仕様が異なる可能性がある分野で多用されています。このように、多品種少量生産が求められる現代においては、柔軟な生産変更や作業効率の向上が期待できる一方で、ブース間の搬送作業の煩雑化やスキルに応じた人員管理の必要性、ブース設置に広い作業スペースが求められるなどの課題もあります。
モデル
4人一組で作業を行うブースを考え、以下のようなモデルを想定します。それぞれの組立プロセスで作業員が以下のような作業を担当します。
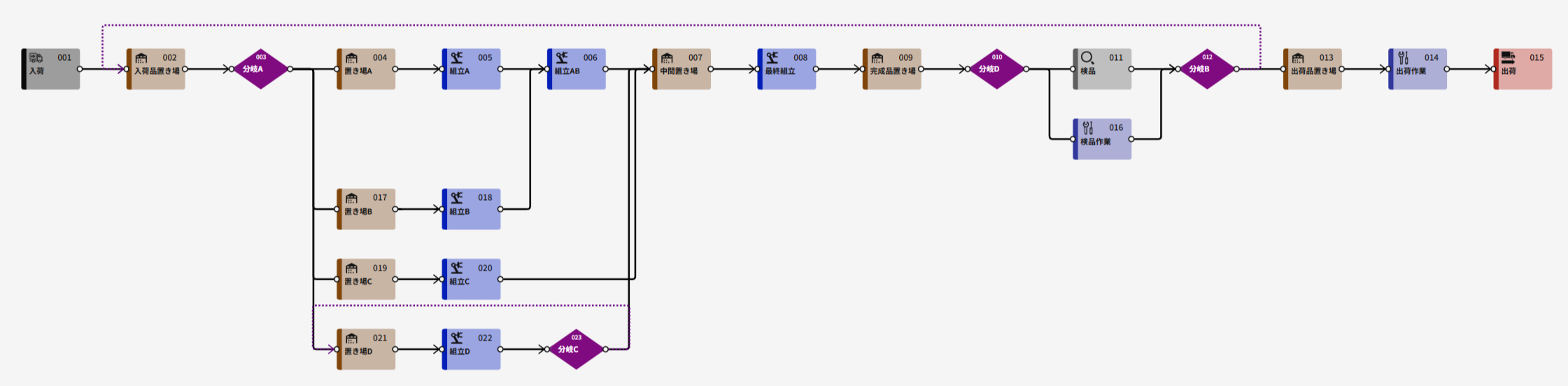
前半工程(括弧内は総所要時間)
組立A:作業員Aが組立キットAからパーツAを1個組立(15分)
組立B:作業員Bが組立キットBからパーツBを1個組立(20分)
組立AB:作業員Aと作業員BがパーツAとパーツBからパーツABを1個組立(30分)
組立C:作業員Cが組立キットCからパーツCを1個組立(30分)
組立D:作業員Dが組立キットDからパーツDを2個組立(10分×2)
後半工程(括弧内は総所要時間)
最終組み立て:4人の作業員でパーツAB1個、C1個、D2個から完成品を組立(50分)
検品:4人の作業員で検品(10分)
前半工程では、4人の作業員がそれぞれ自分の担当するパーツを組み立て、パーツ同士を組み合わせ(作業員AとB)、複数のパーツを準備する工程(作業員D)を行います。後半工程では、4人の作業員が協力して完成品1個を組み立て、検品を行います。完成品は完成品置き場に移され、その後出荷されます。
また、このモデルではセル生産方式のようにループを活用し、各作業員が完成品に必要なパーツを1つずつ作成するプロセスを再現しています。
シミュレーションと分析
上記のモデルを作ったらシミュレーションを行います。今回のシミュレーションは8時間に相当する480分で行いました。シミュレーションが終了すると以下の画面が表示されます。
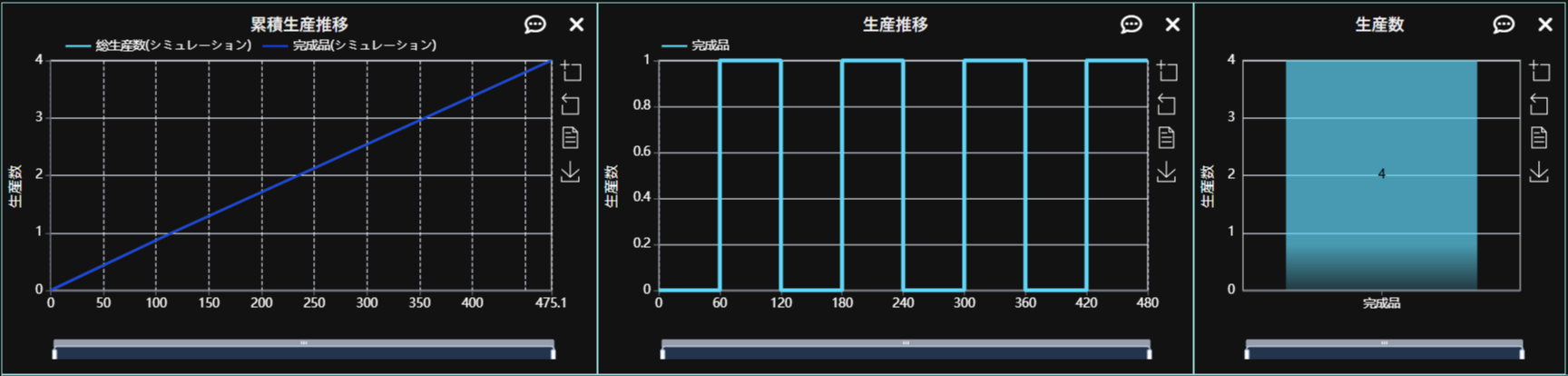
今回のモデルではおよそ60分で作業員4人がここに作業を行う前段作業と、60分で4人で1つの完成品を組み上げる後段作業がありますが、下図のようにステータス推移を確認するとそのプロセスが再現されていることが分かります。
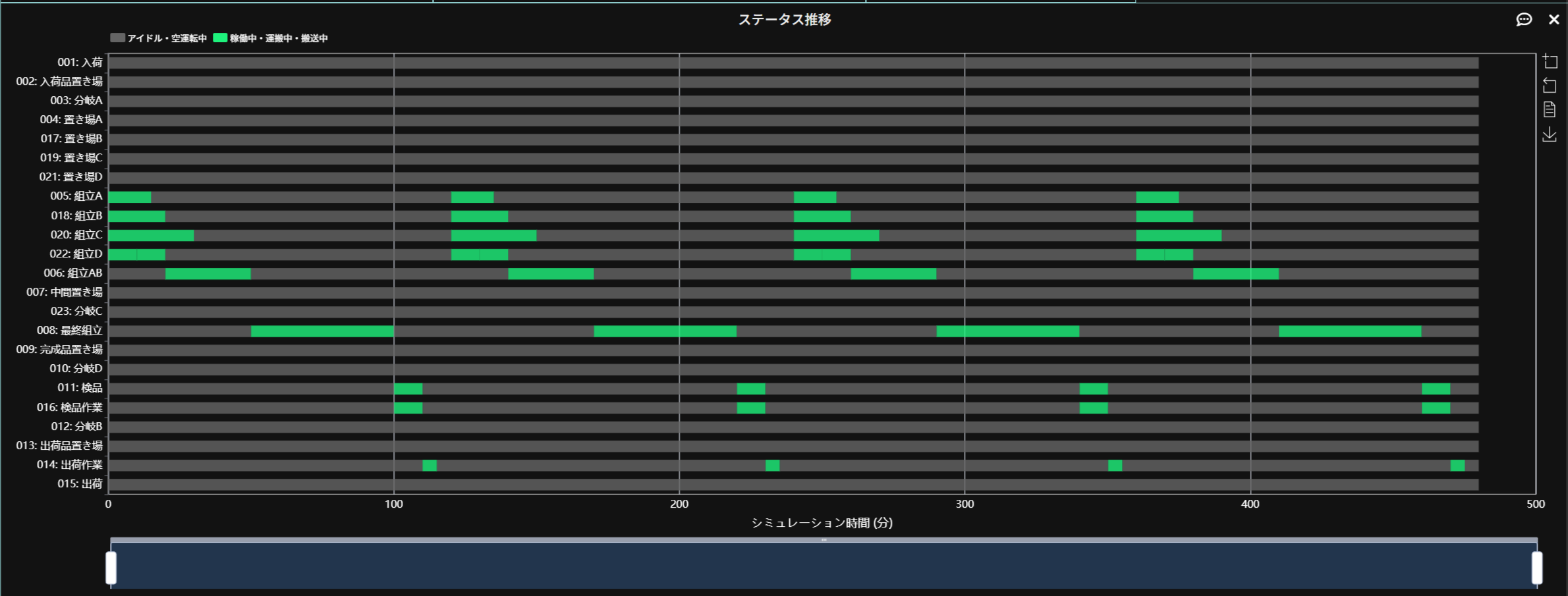
また、ステータス推移の詳細を確認することで、それぞれの作業員が、完成品が組み上がるまでにどのくらいの作業を行っているのかを確認することも出来ます。

今回の設定では、作業員C(作業量30分)およびD(作業量20分)の作業量がAやBと比べて少なく、それぞれ30分ほどの待ち時間があることが見える化されます。この可視化により、4人が必要な最終組立作業に問題がなければ、作業員CとDの作業を1人にまとめることや、他の作業が必要となった際に作業員CやDに優先的に作業を割り振るなどの、生産計画を視覚的に検討することが可能です。
今回のケースは比較的単純なモデルですが、作業員の担当工程がより複雑であっても、各作業の見える化を通じて、生産計画を効率的に検討することが可能です。
まとめ
今回の記事ではブース生産方式のモデルを作成しました。assimeeでは、作業員を品目としてモデル化することも可能です。これにより、各工程の処理時間や稼働率だけでなく、作業員の作業時間や作業効率も見える化し、工程内容の検討を行うことができます。このように、作業人数や処理時間、在庫量などの最適化にとどまらず、生産現場の作業の分析、作業の平準化、効率化、改善にも活用することができます。
assimeeでは、実際の製造プロセスをモデル化し、シミュレーションすることで、プロセスの見える化や潜在的な課題の洗い出しを行うことができます。製造プロセスのデジタル化や課題解決でお悩みの方は、ぜひお問い合わせください。