概要
今回の記事では自動車工場を再現した大型のモデルを使って工場の効率化を行う方法について解説します。インターネット上で公開されているトヨタの生産ライン紹介ページでは鉄板から車を組み立てるために必要な工程として以下の6つの工程を挙げています。
- プレス
- 溶接
- 塗装
- 組立
- 検査
- 輸送
このうち、車の組立では約3万点に及ぶ部品を取り付ける必要があり、検査項目は2000に及ぶと紹介されています。今回のモデルでは組立と検査の工程を簡略化しますが、上記の工程を大枠でモデルとして再現していきます。このモデルは複数の部品の供給、複数回の検査と不良品の選別などを盛り込んだ非常に大きなモデルとなります。
モデルの作成
下図が完成したモデルとなります。鉄板の入荷から切り出し、プレス、溶接、車体の組立、各種部品の入荷とくみ上げなどを再現したため、全部でプロセスカードが150枚を超える大きなモデルとなりました。assimeeでは直感的な操作で容易にモデルの作成やパラメータの設定が出来ます。また、このような大型で複雑なモデルのシミュレーションも一日の時間に相当する1440分で行った場合にも2分で実行が終了するなど、手軽に行うことが可能となっています。
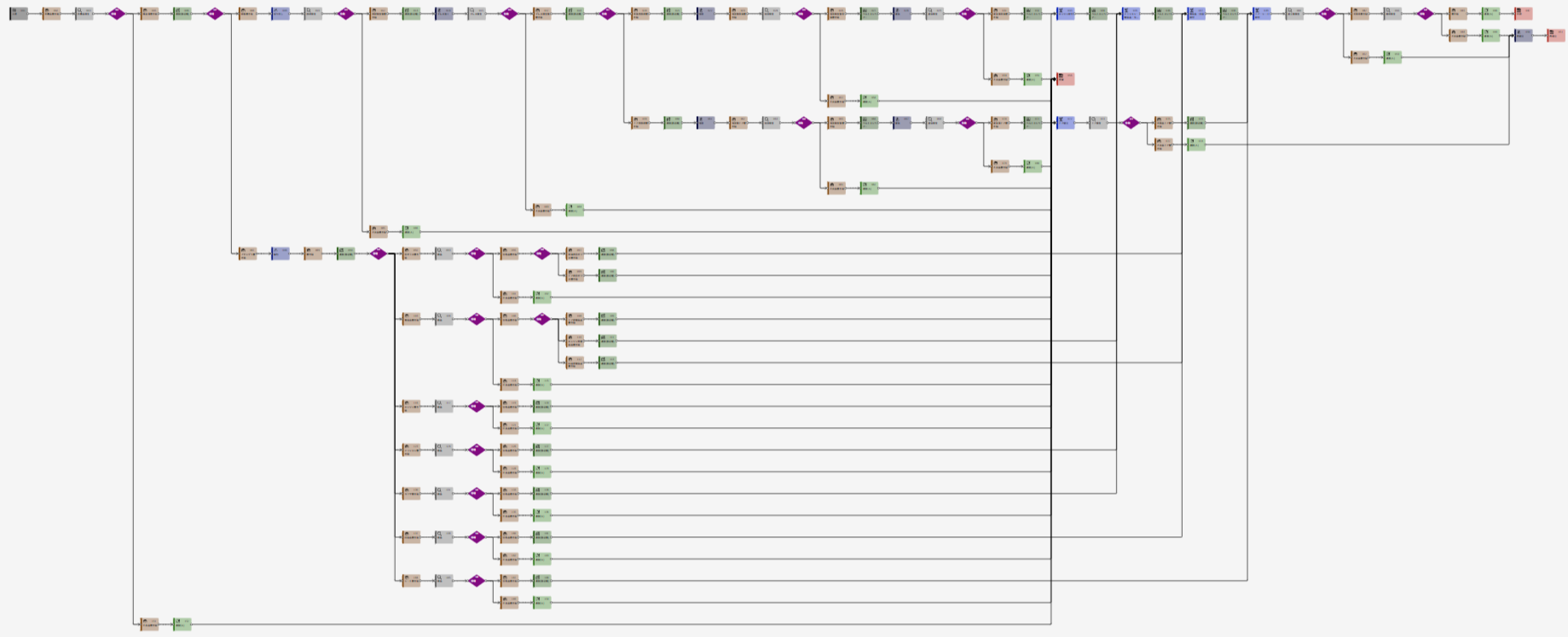
シミュレーション結果と分析
上のプロセス配置と設定が終わったらシミュレーションを行います。今回はシミュレーション期間として1日にあたる1440分を想定してシミュレーションを実行しました。適切に設定できていれば、以下の様なシミュレーション結果が表示されます。*不良品の発生にランダム変数が含まれるため毎回結果が異なり一致しません。
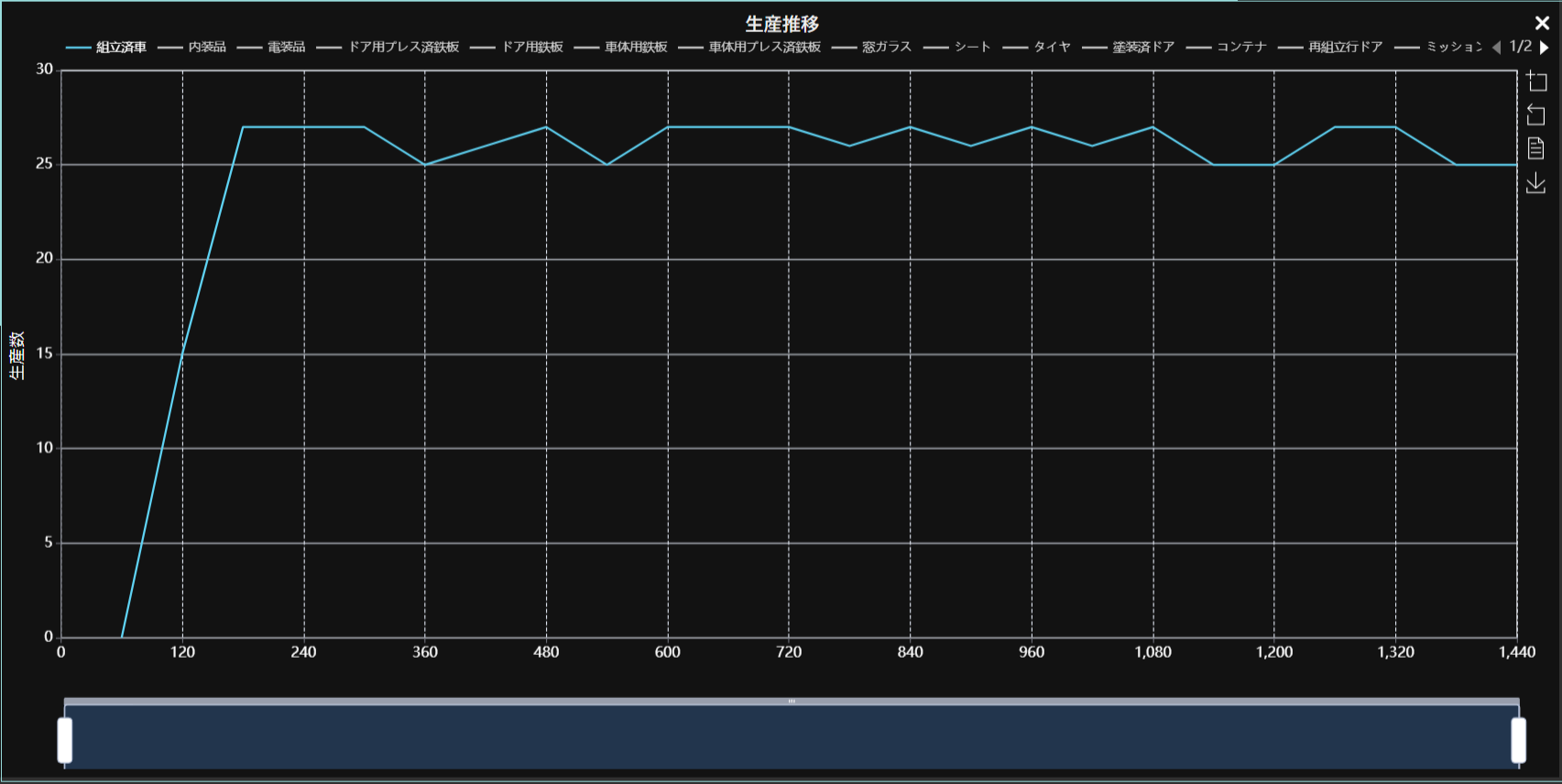
また、下図のように出荷される車や検品の結果廃棄される部品などを個別に表示することが可能です。
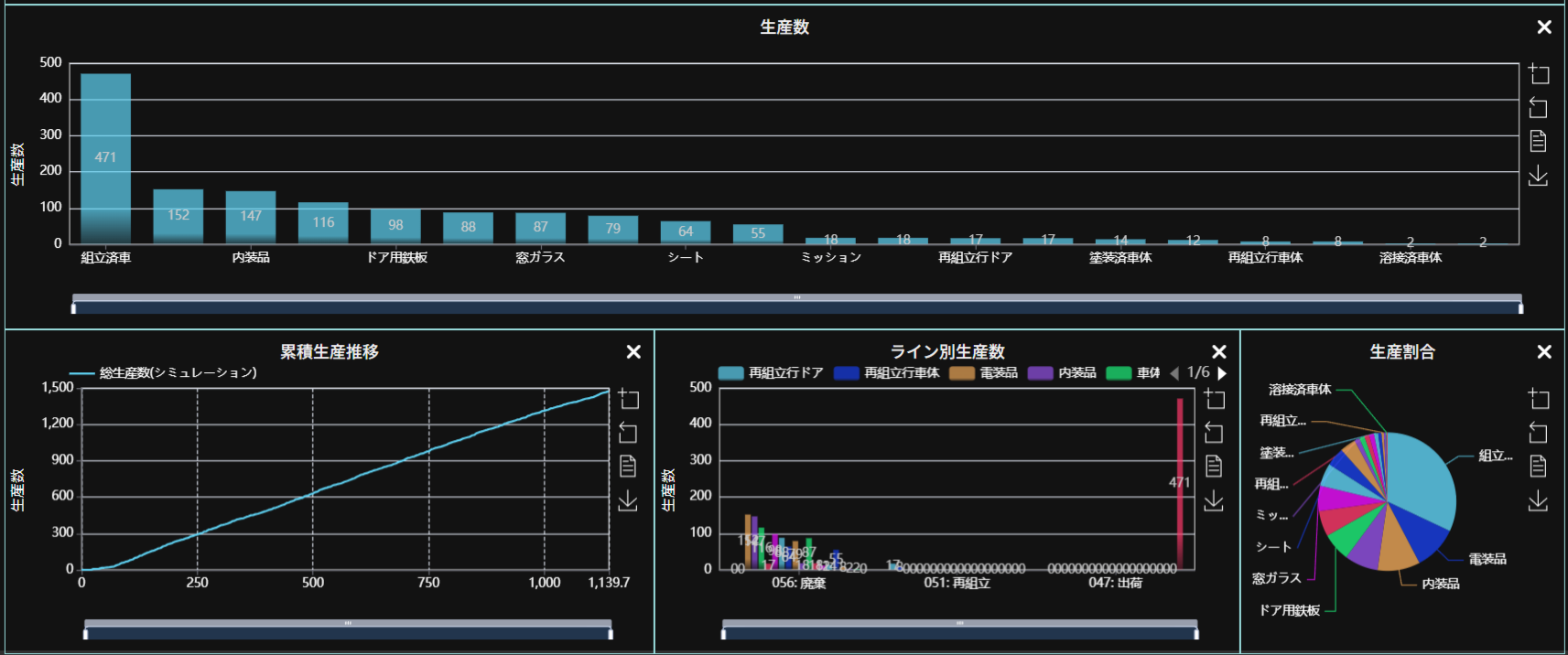
次に、各プロセスのステータス推移をみていくことで、設定したパラメーターに対して、各プロセスが順調に動いているかを判断することが可能です。先ずは自動車の組立に必要な車体の生産に必要な加工プロセスの稼働率を確認してみましょう。いずれの工程も稼働率が100%にはなっておらず、車体の生産には余裕がまだあることが分かります。
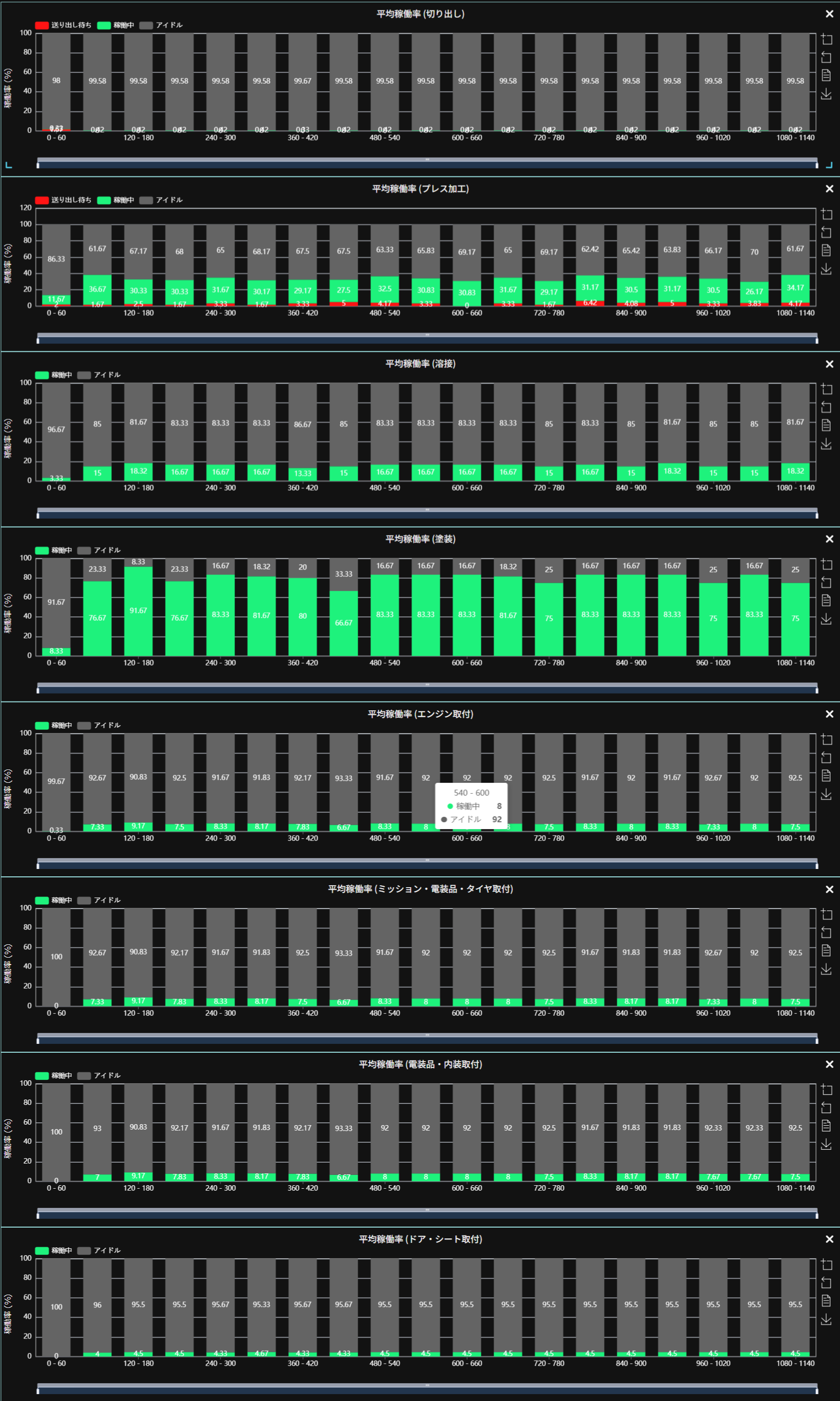
また、全体のステータス推移をみることで、どこかのプロセスに異常が生じていないかを確認することも出来ます。下図のステータス推移図をみると、008解包(内装品などの入荷部分)がブロックを示す赤色となっています。これは直後の009置き場が紫色(容量が一杯)になっていることから、現在の生産ラインの状態ではアセンブリパーツの数が多すぎて処理のボトルネックが生じていることが判明します。同様にして、ドア用の部材も余っていることがわかります。
以上のことから、アセンブリの入荷やドアの生産に対して、車体の生産数が足りておらず、車の生産数が伸び悩んでいるという分析を行うことが出来ます。このようにして、実際の生産ラインを動かす前にボトルネックが生じていないかを確認したり、ボトルネックを解消するための対策を立案することにより、効率的に生産ラインを運用することが可能になります。
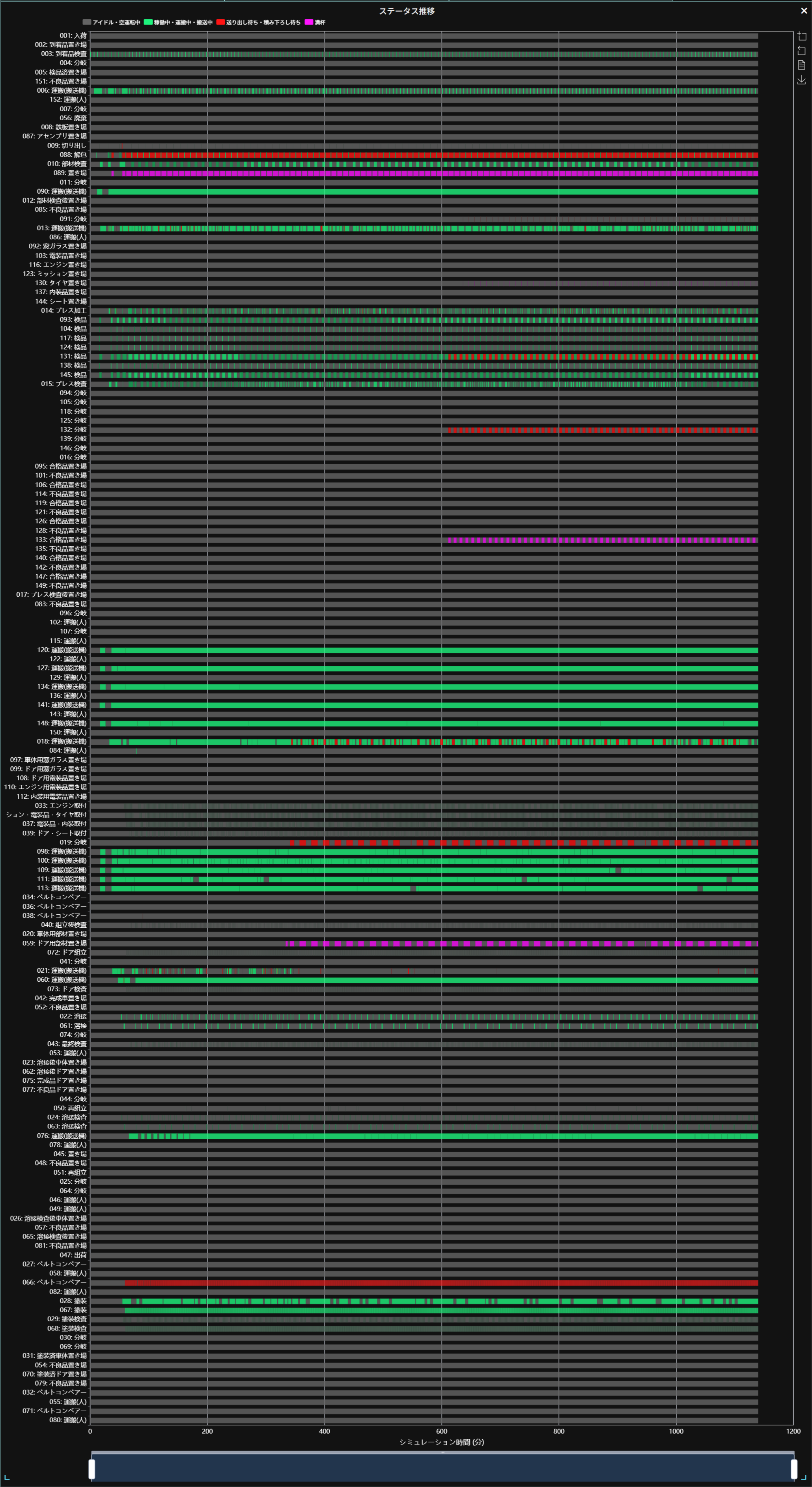
まとめ
今回は大規模な自動車生産ラインのモデルを作成しました。このような複雑な工程のシミュレーションを行うにはモデルの作成自体にも時間が必要な上、シミュレーションの実行にも大きな時間が必要でした。assimeeはプロセスカードと直感的な操作を組み合合わせることで、複雑かつ大きなモデルを使ったシミュレーションをブラウザ上でいつでもどこでも手軽に混粉うことが出来ます。これにより、作業現場でシミュレーションを使ったボトルネック対策などの業務効率化を毎日行うことが容易になります。