概要
生産計画のシミュレーション解説の3回目となる今回の記事では、部品から半完成品を作り、その半完成品を仕上げて製品を生産する工場に対する生産計画をシミュレーションする方法について解説します。1段階目の加工プロセスの生産結果を元に2段階目の加工プロセスの生産計画を決定する必要がありますが、このような場合こそ、デジタル上で試行錯誤の可能なシミュレーションの出番だと考えられます。
モデル
今回使用するモデルは以下の図のようになります。2つの段階の加工プロセスを再現するほか、前回の記事のように複数ラインでの部品生産を想定したモデルとなっています。1段階目である加工ラインで部品から半完成品を生産し、2段階目の仕上げ加工ラインで半完成品から製品を作ることを想定します。また、3つの品目(種類)の生産まで考えた生産計画を検討します。
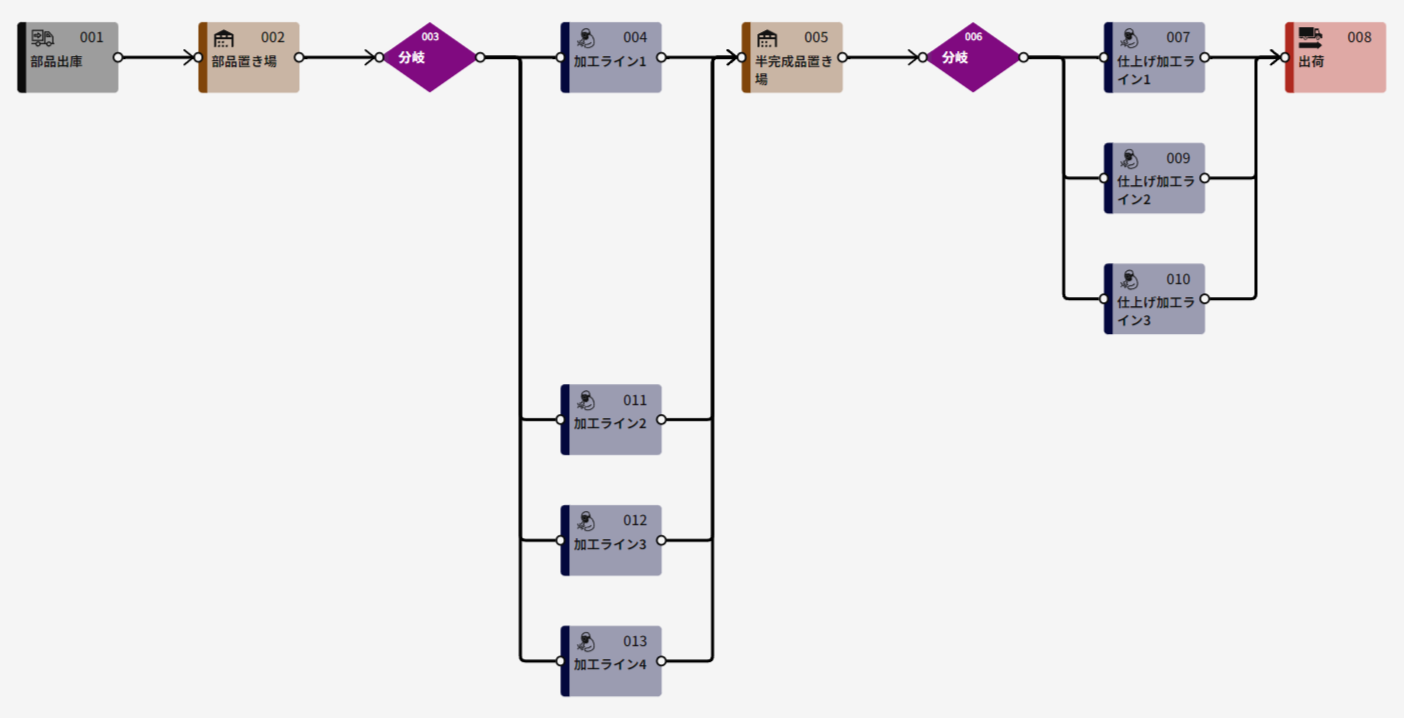
このモデルでも前回と同様に、それぞれの加工プロセスの段取り替え時間は「60分」と考えます。
生産計画
モデルを作る前に生産計画を用意します。最終的には3品目を生産しますが、まず1品目目の製品の生産計画を検討します。今回の生産計画は2段階に分かれています。
加工ライン
生産する製品:半完成品000
必要な部品:半完成品000用部品が1個
生産数:2000個
時間当たりの生産数:600個(平均処理時間0.1分)のラインを4並列で2400個
段取り替え時間(立ち上げ時間):60分
仕上げ加工ライン
生産する製品:製品000
必要な部品:半完成品000が1個
生産数:2000個
時間当たりの生産数:480個(1人当たり平均処理時間0.125分)のラインを3並列で1440個
段取り替え時間(立ち上げ時間):60分
この計画に応じてモデルを設定していきます。簡単のため不良品は発生しない前提とします。
STEP1 プロセス図の作成
入荷プロセス:
プロセス名を「部品出庫」へ変更
置き場プロセス:
プロセス名を「部品置き場」と設定
分岐プロセス:
特に変更なし
分岐先として4つのプロセスを設置:
分岐先として4つの加工プロセス(「加工ライン1」、「加工ライン2」、「加工ライン3」、「加工ライン4」)を用意します。「加工ライン1」の下流には置き場「半完成品置き場」を配置します。
加工プロセス:
プロセス名を「加工ライン1」へ変更
置き場プロセス:
プロセス名を「半完成品置き場」へ変更
加工プロセス:
プロセス名を「加工ライン2」へ変更し、「005半完成品置き場」へ合流
加工プロセス:
プロセス名を「加工ライン3」へ変更し、「005半完成品置き場」へ合流
加工プロセス:
プロセス名を「加工ライン4」へ変更し、「005半完成品置き場」へ合流
分岐プロセス:
特に変更なし
分岐先として3つのプロセスを設置:
分岐先として3つの加工プロセス(「仕上げ加工ライン1」、「仕上げ加工ライン2」、「仕上げ加工ライン3」)を用意します。「仕上げ加工ライン1」の下流には出荷プロセスを配置します。
加工プロセス:
プロセス名を「仕上げ加工ライン1」へ変更
出荷プロセス:
プロセス名を「出荷」へ変更
加工プロセス:
プロセス名を「仕上げ加工ライン2」へ変更し、008出荷へ合流
加工プロセス:
プロセス名を「仕上げ加工ライン3」へ変更し、008出荷へ合流
STEP2 パラメーターの設定
001部品出庫:
生産計画を入荷データに設定:
生産計画のうち部品の入庫数は入荷プロセスに設定します。前回の記事と同様に詳細設定から「開く」を選び、以下の図のように「0分」に2000個の「半完成品000用部品」が入荷するように設定します。これにより、0分の時点で2000個の「半完成品000用部品」がプロセスに入荷します。
*この設定は、他のプロセスの設定より先に行ってください。
002部品置き場:
容量を「10000個」と設定
003分岐:
1回あたりの処理時間を「0分」と設定
*処理時間を「0」とすることでパススルーとなります。
分岐条件:
ランダム設定(変更せず)
004加工ライン1:
こちらも前回の記事と同様に詳細設定を開き、1回あたりの処理時間を「0.05分」、「稼働開始時間を設定する」にチェックを入れ、稼働開始時間を「60分」、段取り替えにチェックを入れ、段取り替え時間を「60分」と設定
対象品目を「半完成品000用部品」、個数を「1個」、
出力品目を「半完成品000」、個数を「1個」と設定
011加工ライン2:
詳細設定を開き、1回あたりの処理時間を「0.1分」、「稼働開始時間を設定する」にチェックを入れ、稼働開始時間を「60分」、段取り替えにチェックを入れ、段取り替え時間を「60分」と設定
対象品目を「半完成品000用部品」、個数を「1個」、
出力品目を「半完成品000」、個数を「1個」と設定
012加工ライン3:
詳細設定を開き、1回あたりの処理時間を「0.1分」、「稼働開始時間を設定する」にチェックを入れ、稼働開始時間を「60分」、段取り替えにチェックを入れ、段取り替え時間を「60分」と設定
対象品目を「半完成品000用部品」、個数を「1個」、
出力品目を「半完成品000」、個数を「1個」と設定
013加工ライン4:
詳細設定を開き、1回あたりの処理時間を「0.15分」、「稼働開始時間を設定する」にチェックを入れ、稼働開始時間を「60分」、段取り替えにチェックを入れ、段取り替え時間を「60分」と設定
対象品目を「半完成品000用部品」、個数を「1個」、
出力品目を「半完成品000」、個数を「1個」と設定
005半完成品置き場:
容量を「10000個」と設定
006分岐:
1回あたりの処理時間を「0分」と設定
*処理時間を「0」とすることでパススルーとなります。
分岐条件:
ランダム設定(変更せず)
007仕上げ加工ライン1:
詳細設定を開き、1回あたりの処理時間を「0.5分」、作業人数にチェックを入れ、人数を「4人」、段取り替えにチェックを入れ、段取り替え時間を「60分」と設定
対象品目を「半完成品000」、個数を「1個」、
出力品目を「製品000」、個数を「1個」と設定
009仕上げ加工ライン2:
詳細設定を開き、1回あたりの処理時間を「0.5分」、作業人数にチェックを入れ、人数を「4人」、段取り替えにチェックを入れ、段取り替え時間を「60分」と設定
対象品目を「半完成品000」、個数を「1個」、
出力品目を「製品000」、個数を「1個」と設定
010仕上げ加工ライン3:
詳細設定を開き、1回あたりの処理時間を「0.5分」、作業人数にチェックを入れ、人数を「4人」、段取り替えにチェックを入れ、段取り替え時間を「60分」と設定
対象品目を「半完成品000」、個数を「1個」、
出力品目を「製品000」、個数を「1個」と設定
008出荷:
特に設定なし
シミュレーション
モデルが完成したら、シミュレーション実行時間を「480分」(8時間)に設定してシミュレーションを実行します。設定に問題がなければ、ダッシュボードから以下のように「生産数推移」のグラフ(上図左側)が表示できます。
*表示できない場合は設定を見直してください。

また、モデルの「004加工ライン1」や「007仕上げ加工ライン1」の「累積加工推移」も見てみましょう(上図右側)。このシミュレーションでは1段階目の加工プロセスが約105分で終了し、2段階目の加工プロセスが約145分で終了することが分かります。
製品2品目目の追加
モデルに適用する生産計画に下記の通り2品目目を追加します(レポートの複製と編集が便利です)。シミュレーションの結果から105分で1段階目の加工プロセスの手が空くので、シミュレーション開始から110分に次の部品を入荷すれば、170分に段取り替えが終了し次の生産が始まることが分かります。また、170分後には2段階目の加工プロセスの生産も終わっているので、混入がないことも分かります。よって110分に次の部品を入荷してみましょう。
生産計画と入荷データの設定
加工ライン
生産する製品:半完成品000
必要な部品:半完成品000用部品が1個
生産数:2000個
時間当たりの生産数:600個(平均処理時間0.1分)のラインを4並列で2400個
段取り替え時間(立ち上げ時間):60分
生産する製品:半完成品111
必要な部品:半完成品111用部品が1個
生産数:1000個
時間当たりの生産数:600個(平均処理時間0.1分)のラインを4並列で2400個
段取り替え時間(立ち上げ時間):60分
仕上げ加工ライン
生産する製品:製品000
必要な部品:半完成品000が1個
生産数:2000個
時間当たりの生産数:480個(1人当たり平均処理時間0.125分)のラインを3並列で1440個
段取り替え時間(立ち上げ時間):60分
生産する製品:製品111
必要な部品:半完成品111が1個
生産数:1000個
時間当たりの生産数:480個(1人当たり平均処理時間0.125分)のラインを3並列で1440個
段取り替え時間(立ち上げ時間):60分
次に、入荷数を変更します。詳細設定から「開く」を選び、「110分」に1000個の「半完成品111用部品」が入荷するように設定します。
加工ラインの設定
次に1段階目の加工プロセスに設定を追加して行きます。
004加工ライン1:
詳細設定に入り、加工パターン2を追加し、
下図のように1回あたりの処理時間を「0.05分」、「稼働開始時間を設定する」にチェックを入れ、稼働開始時間を「60分」、段取り替えにチェックを入れ、段取り替え時間を「60分」と設定
対象品目を「半完成品111用部品」、個数を「1個」、
出力品目を「半完成品111」、個数を「1個」と設定
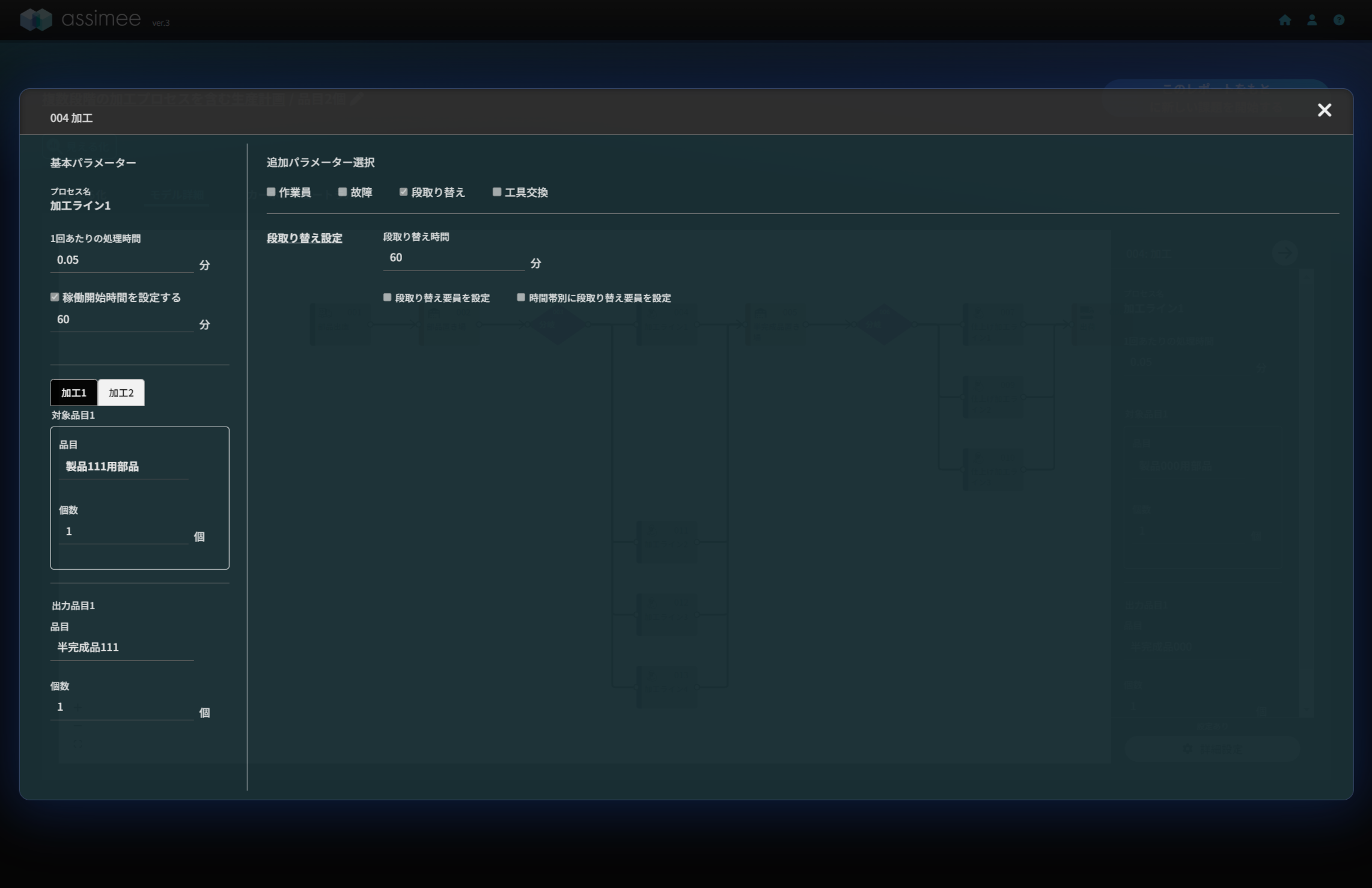
011加工ライン2:
詳細設定に入り、加工パターン2を追加し、
1回あたりの処理時間を「0.1分」、段取り替えにチェックを入れ、段取り替え時間を「60分」と設定
対象品目を「半完成品111用部品」、個数を「1個」、
出力品目を「半完成品111」、個数を「1個」と設定
012加工ライン3:
詳細設定に入り、加工パターン2を追加し、
1回あたりの処理時間を「0.1分」、段取り替えにチェックを入れ、段取り替え時間を「60分」と設定
対象品目を「半完成品111用部品」、個数を「1個」、
出力品目を「半完成品111」、個数を「1個」と設定
013加工ライン4:
詳細設定に入り、加工パターン2を追加し、
1回あたりの処理時間を「0.15分」、段取り替えにチェックを入れ、段取り替え時間を「60分」と設定
対象品目を「半完成品111用部品」、個数を「1個」、
出力品目を「半完成品111」、個数を「1個」と設定
仕上げ加工ラインの設定
次に2段階目の加工プロセスの設定を追加します。
007仕上げ加工ライン1:
先ほどと同様に詳細設定に入り、加工パターン2を追加し、
1回あたりの処理時間を「0.5分」、作業人数にチェックを入れ、人数を「4人」、段取り替えにチェックを入れ、段取り替え時間を「60分」と設定
対象品目を「半完成品111」、個数を「1個」、
出力品目を「製品111」、個数を「1個」と設定
009仕上げ加工ライン2:
詳細設定に入り、加工パターン2を追加し、
1回あたりの処理時間を「0.5分」、作業人数にチェックを入れ、人数を「4人」、段取り替えにチェックを入れ、段取り替え時間を「60分」と設定
対象品目を「半完成品111」、個数を「1個」、
出力品目を「製品111」、個数を「1個」と設定
010仕上げ加工ライン3:
詳細設定に入り、加工パターン2を追加し、
1回あたりの処理時間を「0.5分」、作業人数にチェックを入れ、人数を「4人」、段取り替えにチェックを入れ、段取り替え時間を「60分」と設定
対象品目を「半完成品111」、個数を「1個」、
出力品目を「製品111」、個数を「1個」と設定
2品目目追加後のシミュレーション
モデルの設定が終了したら、先ほどと同様にシミュレーション実行時間を「480分」(6時間)に設定してシミュレーションを実行します。設定に問題がなければ、ダッシュボードから以下のような「生産推移」びグラフが表示できます。*表示できない場合は設定を見直してください。
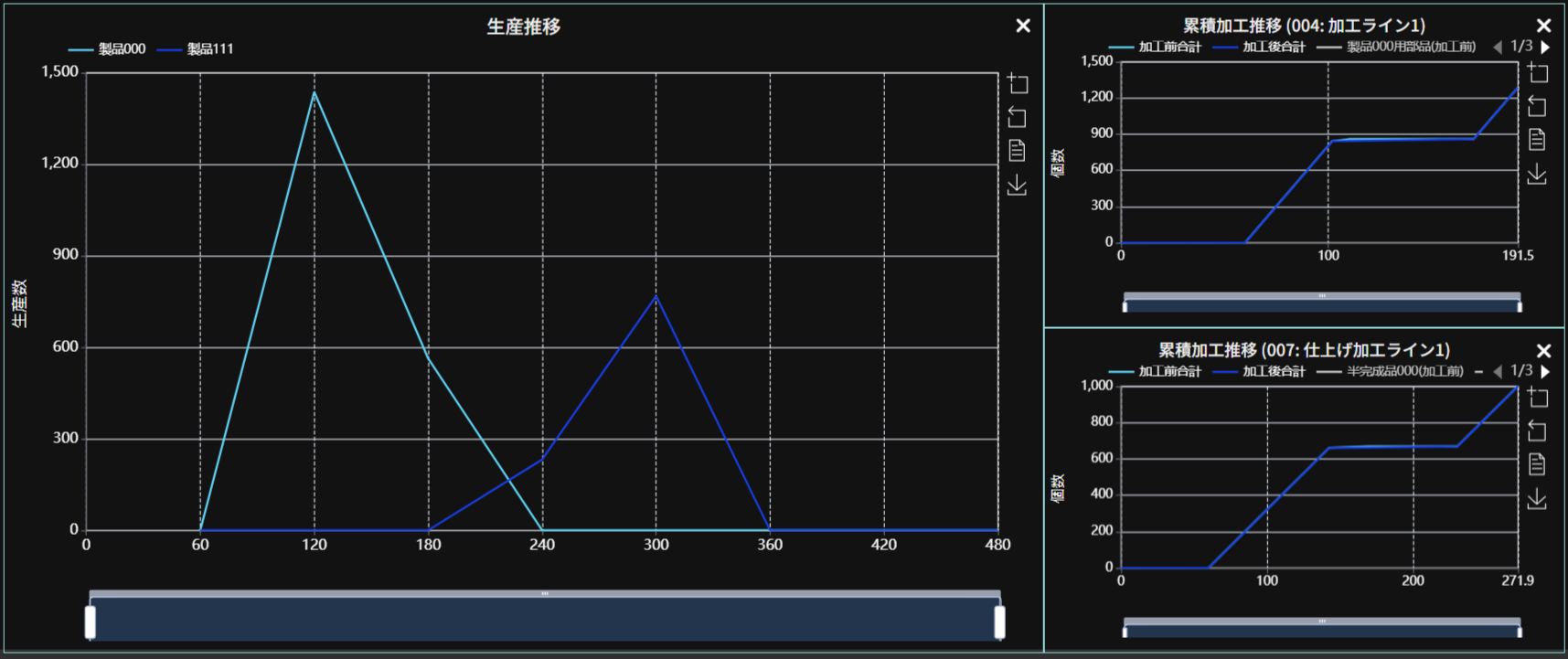
今回も同様にモデルの「004加工ライン1」や「007仕上げ加工ライン1」のルイ移籍加工推移を見てみましょう。このシミュレーションでは1段階目の加工プロセスが約192分で終了し、2段階目の加工プロセスが約272分で終了することが分かります。
製品3品目目の追加
2品目目と同様に3品目目を追加してみましょう。再度モデルを複製し、編集モードで、設定を変更して行きます。
モデルに適用する生産計画は下記の通り3品目目を追加します。シミュレーションの結果から192分で1段階目の加工プロセスの手が空くので、シミュレーション開始から200分に次の部品を入荷すれば、1段階目は260分に段取り替えが終了し次の生産が始まることが分かります。しかし、2段階目の加工プロセスの2品目目の生産が終わるのは273分の時点なので、このまま、200分に3品目目の生産を始めると2段階目の加工プロセスの入力に2品目目と3品目目の混入が生じてしまうことが分かります。混入が生じるとシミュレーションで段取り替えが複数回発生し、生産がマヒしてしまいます。よって220分に次の部品を入荷することにしてみましょう。この場合、280分に1段階目の3品目目の生産が始まるので、混入を回避することが出来ます。
生産計画と入荷データの設定
生産する製品:製品000
必要な部品:半完成品000用部品が1個
生産数:2000個
時間当たりの生産数:600個(処理時間0.1分)
段取り替え時間(立ち上げ時間):60分
生産する製品:製品111
必要な部品:半完成品111用部品が1個
生産数:1000個
時間当たりの生産数:600個(処理時間0.1分)
段取り替え時間(立ち上げ時間):60分
生産する製品:製品222
必要な部品:半完成品222用部品が1個
生産数:1200個
時間当たりの生産数:600個(処理時間0.1分)
段取り替え時間(立ち上げ時間):60分
次に、入荷数を変更します。先ほどと同様に詳細設定から「開く」を選び、「「220分」に1200個の「半完成品222用部品」が入荷するように設定します。
加工ラインの設定
次に加工ラインの設定を変更していきます。
004加工ライン1:
詳細設定に入り、加工パターン3を追加し、
1回あたりの処理時間を「0.05分」、段取り替えにチェックを入れ、段取り替え時間を「60分」と設定
対象品目を「半完成品222用部品」、個数を「1個」、
出力品目を「半完成品222」、個数を「1個」と設定
011加工ライン2:
詳細設定に入り、加工パターン3を追加し、
1回あたりの処理時間を「0.10分」、段取り替えにチェックを入れ、段取り替え時間を「60分」と設定
対象品目を「半完成品222用部品」、個数を「1個」、
出力品目を「半完成品222」、個数を「1個」と設定
012加工ライン3:
詳細設定に入り、加工パターン3を追加し、
1回あたりの処理時間を「0.10分」、段取り替えにチェックを入れ、段取り替え時間を「60分」と設定
対象品目を「半完成品222用部品」、個数を「1個」、
出力品目を「半完成品222」、個数を「1個」と設定
013加工ライン4:
詳細設定に入り、加工パターン3を追加し、
1回あたりの処理時間を「0.15分」、段取り替えにチェックを入れ、段取り替え時間を「60分」と設定
対象品目を「半完成品222用部品」、個数を「1個」、
出力品目を「半完成品222」、個数を「1個」と設定
仕上げ加工ラインの設定
次に仕上げ加工ラインの設定を変更します。今回も加工パターンを追加しますが、処理時間を「1分」とこれまでより長くしています。
007仕上げ加工ライン1:
詳細設定に入り、加工パターン3を追加し、
1回あたりの処理時間を「1分」、作業人数にチェックを入れ、人数を「4人」、段取り替えにチェックを入れ、段取り替え時間を「60分」と設定
対象品目を「半完成品222」、個数を「1個」、
出力品目を「製品222」、個数を「1個」と設定
009仕上げ加工ライン2:
詳細設定に入り、加工パターン3を追加し、
1回あたりの処理時間を「1分」、作業人数にチェックを入れ、人数を「4人」、段取り替えにチェックを入れ、段取り替え時間を「60分」と設定
対象品目を「半完成品222」、個数を「1個」、
出力品目を「製品222」、個数を「1個」と設定
010仕上げ加工ライン3:
詳細設定に入り、加工パターン3を追加し、
1回あたりの処理時間を「1分」、作業人数にチェックを入れ、人数を「4人」、段取り替えにチェックを入れ、
段取り替え時間を「60分」と設定対象品目を「半完成品222」、個数を「1個」、出力品目を「製品222」、個数を「1個」と設定
3品目目追加後のシミュレーション
モデルの設定が終了したら、再度シミュレーション実行時間を「480分」(6時間)に設定して「シミュレーションを実行」ボタンを押します。設定に問題がなければ、ダッシュボードから以下のような「生産数推移」のグラフが表示できます。*表示できない場合は設定を見直してください。
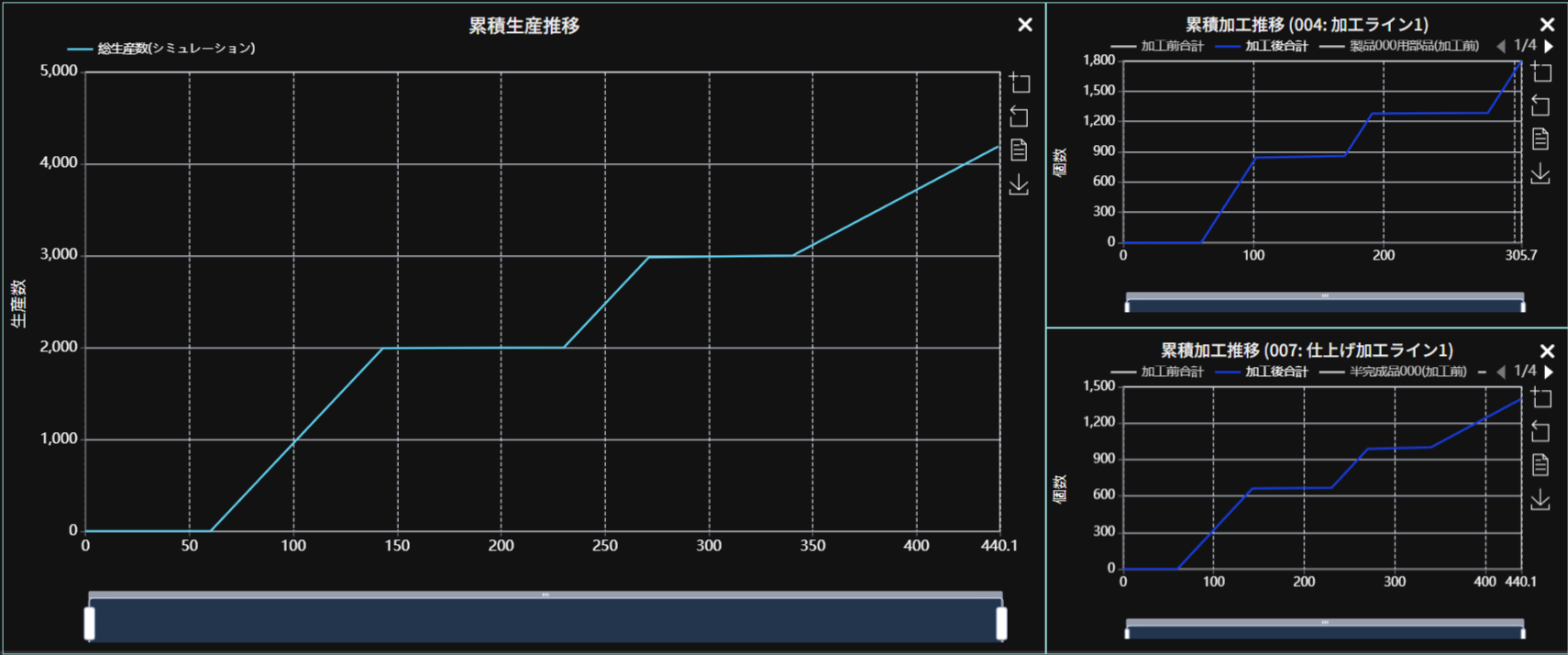
3品目目は2段階目の加工プロセスの処理時間が他より長いので生産数が少なくなっており、生産に時間がかかっていることが分かります。今回もモデルの「004仕上げ加工ライン1」や「011仕上げ加工ライン2」の累積加工推移を見てみましょう。このシミュレーションでは1段階目の加工プロセスが約306分で終了し、2段階目の加工プロセスが約441分で終了すること、2段回目の加工プロセスのアイテム数(出力アイテム数)の傾きが小さいことが分かります。
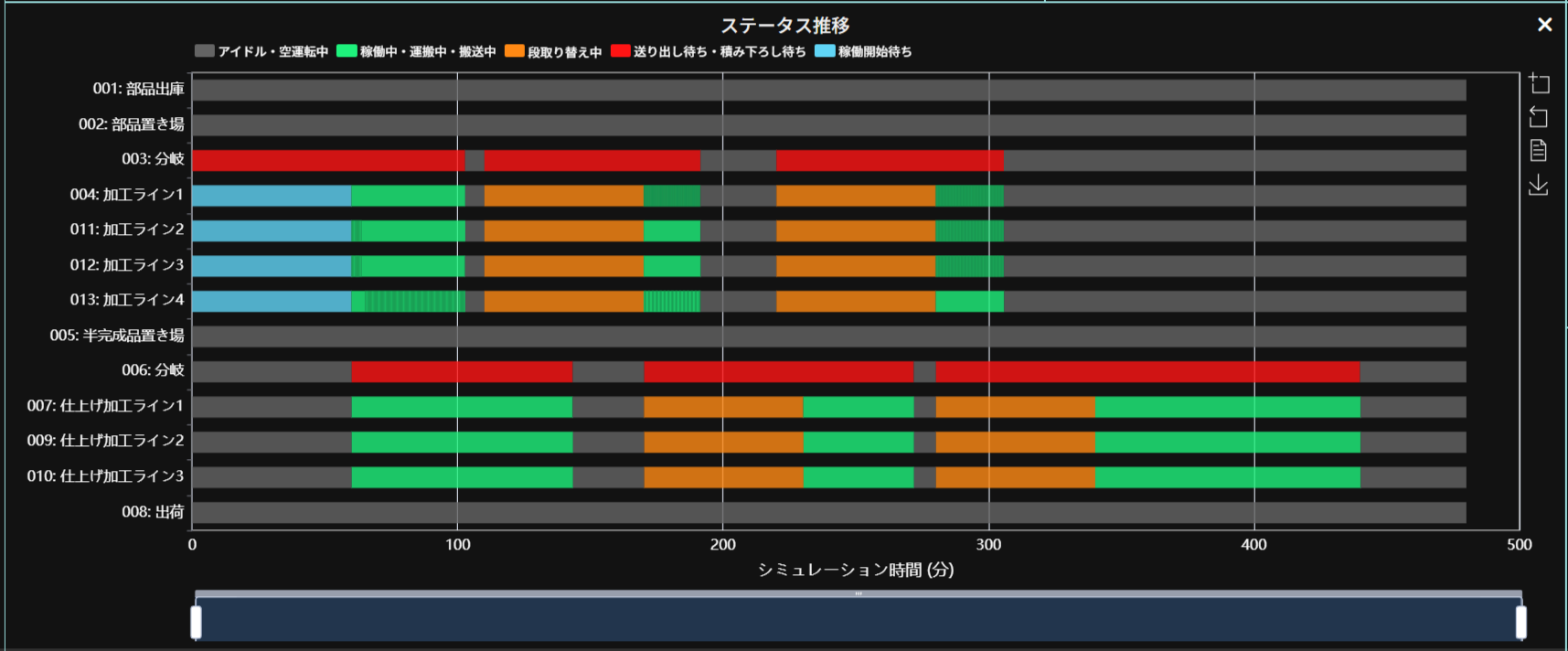
一方で「ステータス推移」のグラフを見ると今回の生産計画の場合、1段階目の加工ラインと2段階目の仕上げ加工ラインの処理時間に差があるため、加工作業の終わった1段階目の加工ラインが停止している時間が長くなってしまっています。この停止時間の長さは、これ以上生産効率を上げることを考える時のボトルネックになります。生産効率を改善するためには2段階目の仕上げ加工の時間の改善(人の配置を増やす、処理時間を短くするなど)を行う必要があることもシミュレーション結果の分析から分かります。
まとめ
今回は複数の生産ラインと複数回の加工プロセスが含まれる場合の生産計画の検討の方法について解説しました。生産効率や作業人数、段取り時間の異なる複雑な生産ラインでも、assimeeを使うことで簡単にモデルを作ることができ、シミュレーションによる生産計画の検討や、生産ラインのボトルネックの発見などが出来ます。
assimeeでは、実際の製造プロセスをモデル化し、シミュレーションすることで、プロセスの見える化や潜在的な課題の洗い出しを行うことができます。製造プロセスのデジタル化や課題解決でお悩みの方は、ぜひお問い合わせください。