概要
製造現場では、製品を構成する要素によって管理単位が異なることがよくあります。たとえば、ボトルやキャップのように1つずつ数量で管理する部品、粒状の原料のように重量で管理する材料、液体のように容積で扱う材料など、それぞれ異なる単位で管理されながら同じ生産ラインで使われるケースは少なくありません。こうした異なる単位の材料を組み合わせて製品を完成させる工程では、在庫管理や生産計画、補充のタイミングなどに独自の難しさが生じます。今回の記事では、数量で管理するハカマ付きの容器とキャップ、重量で管理される粒状原料、容積で扱う液体という複数の要素を組み合わせたボトル詰め工程をモデル化し、そのシミュレーション方法を解説します。
モデル
以下が、今回作成したモデルの図とその概要です。
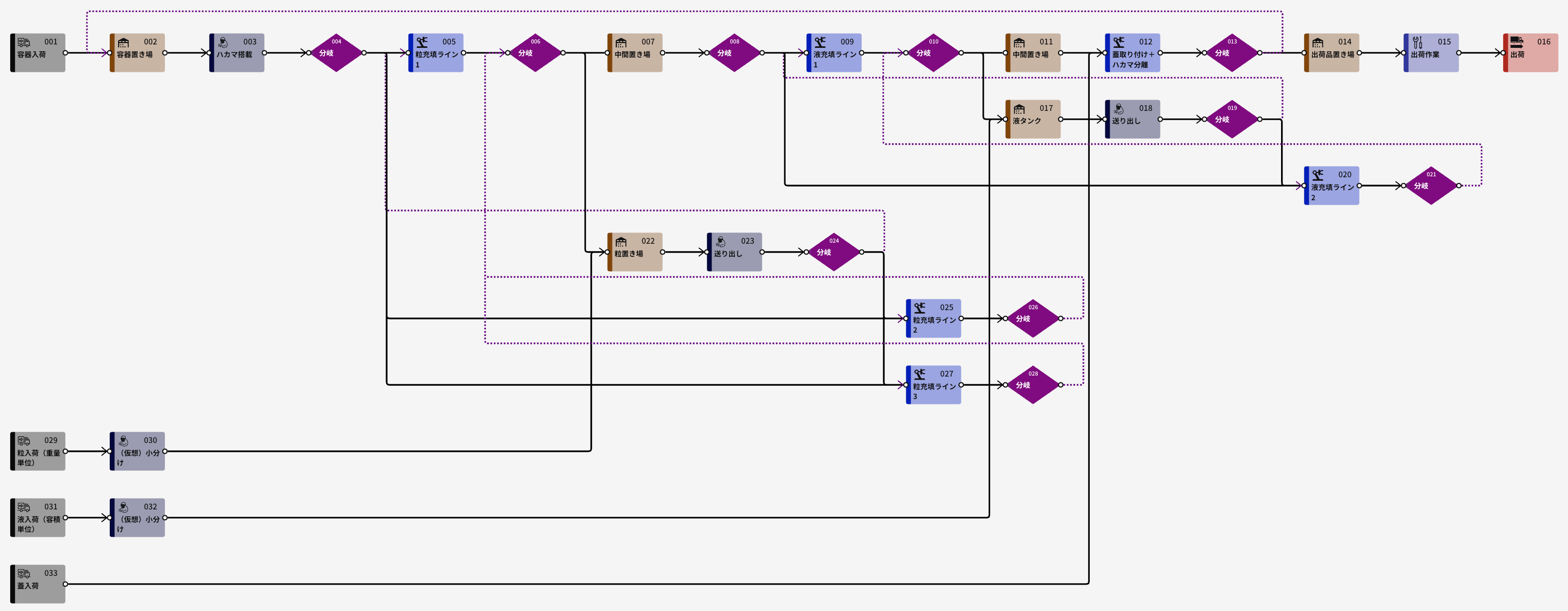
生産ラインの主軸は、ハカマ付きの容器を基準に構成されており、容器に対してまず粒状原料、次に液体を順番に充填し、その後キャップを取り付け、60個単位で箱詰めして出荷する工程となっています。
このモデルは、以下の前提条件に基づいて構築されています:
- 使用するハカマ付き容器は3個
- 粒状原料の充填は3本の並列ラインで行い、サイクルタイムは1.5分
- 粒状原料は10kg単位で供給され、製品1個あたり100gを使用
- 液体の充填は2本の並列ラインで行い、サイクルタイムは2.0分
- 液体は10L単位で供給され、製品1個あたり100mLを使用
- キャップの取り付けは1ラインで行い、サイクルタイムは1分
- 出荷工程では、製品60個を1単位として箱詰めし、サイクルタイムは10分
これらの条件をassimee上で設定し、ライン全体のバランスやボトルネックの発生状況を検証可能なモデルを構築しています。
シミュレーション
モデルの作成が終わったら、シミュレーション時間を480分に設定してシミュレーションを行います。シミュレーション結果は以下の通りとなります。
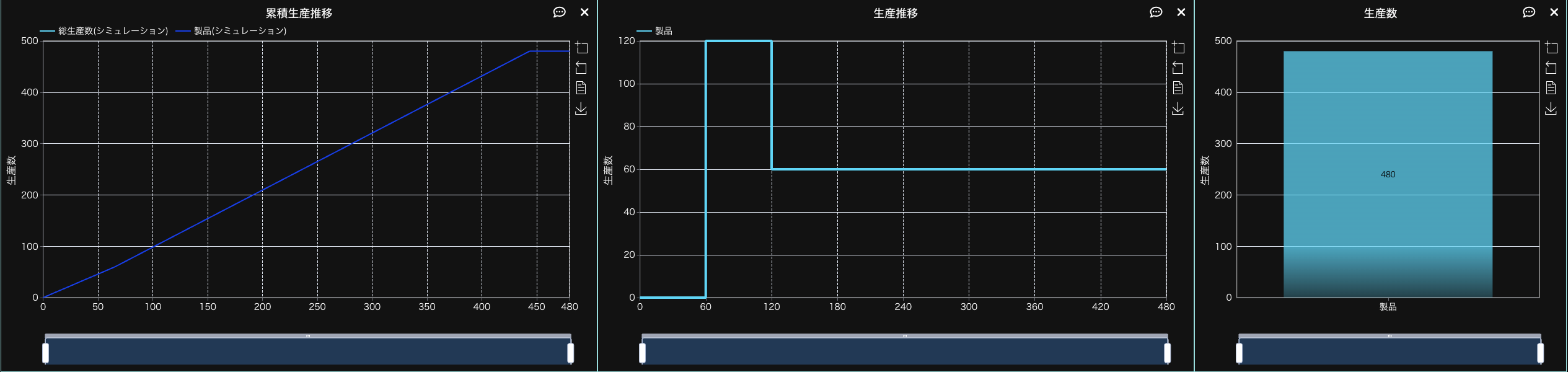
次に各プロセスのステータス推移を確認してみましょう。
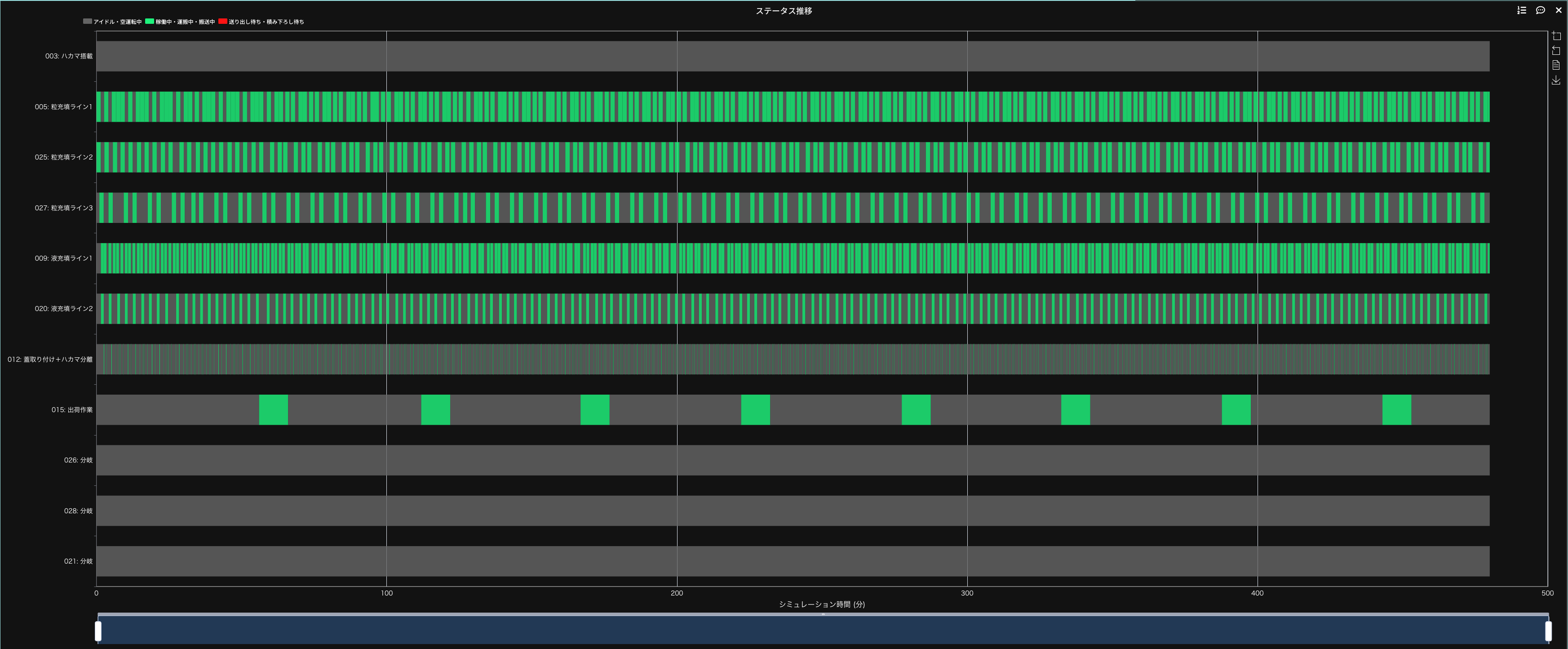
シミュレーション結果では、3本ある粒充填ラインのうち、ライン3の生産量が他のラインに比べて少なくなっています。これは、並列ラインの割り振りにおいて優先順位が「ライン1 → ライン2 → ライン3」の順に設定されており、さらにハカマ付き容器の初期到着タイミングが均等ではなく、粒充填のサイクルタイム(1.5分)より長い間隔で到着しているためです。その結果、ハカマは優先度の高いライン1に集中し、ライン3には十分な数が割り当てられません。ライン3に割り当てられるにはライン1、ライン2が作業中である必要があるからで、これは液充填ラインも同様です。
逆に言うと、粒充填のライン3や液充填のライン2にはまだハカマを入れることができるので、生産力の余裕があると言うこともできます。
まとめ
今回の記事では、「ボトル詰め製品の生産ライン」をテーマに、工程モデルの作成に取り組みました。このラインでは、数量で管理されるハカマ付き容器とキャップに加え、重量で管理される粒状原料、容積で管理される液体を組み合わせて1つの製品を完成させる構成となっています。assimeeを用いて、異なる管理単位を持つ要素をそれぞれ適切に設定し、現実の生産方式を再現するモデルを構築しました。
このようにassimeeでは、さまざまなプロセスカードを柔軟に組み合わせて、実際に現場で使用されているラインをモデル化することが容易に可能です。加えて、シミュレーションを行うことで実際のラインを使用せずにラインの動作の検証を行うことができます。
assimeeでは、実際の製造プロセスをモデル化し、シミュレーションすることで、プロセスの見える化や潜在的な課題の洗い出しを行うことができます。製造プロセスのデジタル化や課題解決でお悩みの方は、ぜひお問い合わせください。