概要
今回の記事では、据え置き型生産方式のモデルを作成し、シミュレーションを行う方法を解説します。
据え置き型生産方式とは、製品を特定の場所に固定し、作業員や機械が製品の周りや内部を移動しながら作業を行う生産方式です。この方式は製品仕様の柔軟な変更が可能で、オーダーメイド製品や少品種少量生産に適しています。一方で、大量生産には不向きです。
この方式は、移動が困難な大型製品(船や航空機など)の生産に適用されるほか、橋やトンネルといった移動しない大型建築物の施工にも用いられます。
メリット
- 動かしづらい大型製品向き
- 製品のカスタマイズが容易
- コンベアーなどの設備投資が少ない
- 複数の作業を並行して行うことも可能
デメリット
- 生産効率が低い
- 作業工程の管理や材料管理にスキルが必要
モデル
下図がモデルです。今回は3つの製品を同時に生産するケースについて解説します。
まず、入荷した本体部品に10分の加工を行った後、製品ごとに分岐し、3つの製品を並行して組み立てます。この組立工程では、配線工事、パーツ取付、内装工事の3つの工程をそれぞれ20分の作業時間で行うように設定します。
*なお、この組立工程を「ライン」と呼びます。
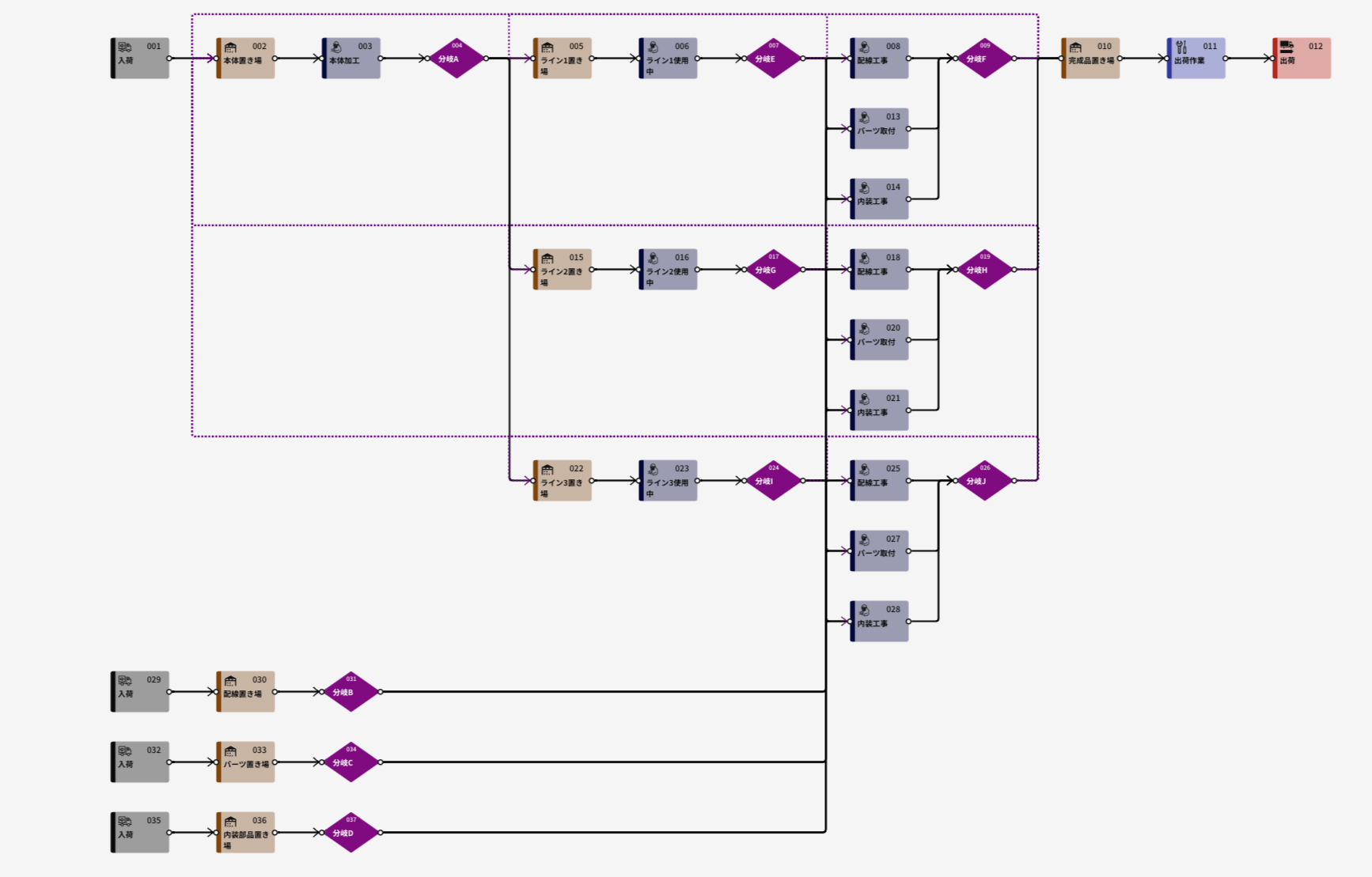
3つの製品は、3つのラインで並行して組み立てられますが、モデルでは「ライン1 → ライン2 → ライン3 → ライン1 → …」のようにサイクルを作り、順番に組み立てる設定にしています。また、配線工事、パーツ取付、内装工事の3つの工程は、ランダムにどの工程からでも始められるように設定しています。
このようにassimeeでは組立順や作業順を柔軟に設定することが可能です。
シミュレーションと分析
モデルの作成が終わったら、シミュレーション時間を1日に相当する1440分に設定して、シミュレーションを行います。シミュレーションの結果は以下の通りとなりました。
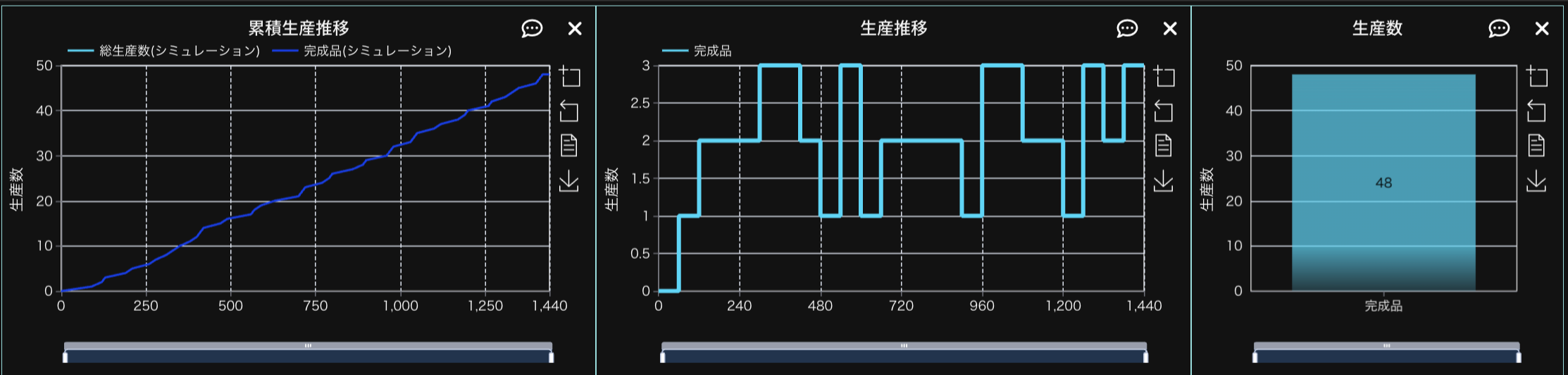
1440分で41個の製品が出荷されていることがわかります。次に、各プロセスのステータス推移を確認してみましょう。
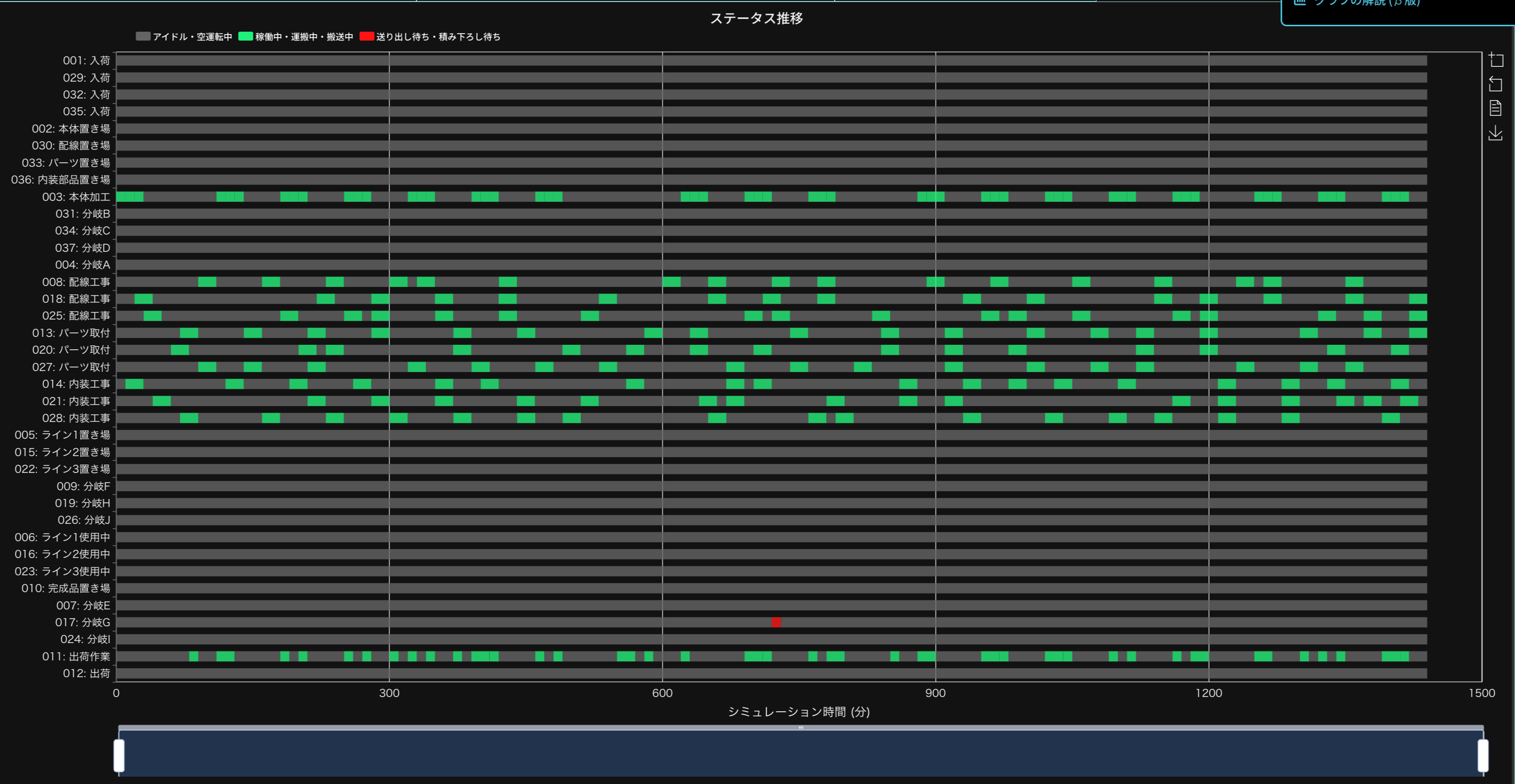
ステータス推移を見ると、「003加工」の処理時間である10分ずつ時間をずらした形で、
ライン1 → ライン2 → ライン3 → ライン1 → …
の順で生産が進んでいることが確認できます。
また、それぞれのライン内では、配線工事、パーツ取付、内装工事の3つの工程が、想定通りランダムに実行されていることも分かります。
まとめ
今回は、据え置き型生産方式のシミュレーション(見える化)方法について解説しました。また、複数のラインで生産が順番に行われる仕組みや、ライン内での組立工程がランダムに進む設定を加え、想定通りに動作していることを確認しました。assimeeでは、用意されたプロセスカードを自由に組み合わせることで、実際の生産工程を簡単かつ柔軟に再現できます。
assimeeでは、実際の製造プロセスをモデル化し、シミュレーションすることで、プロセスの見える化や潜在的な課題の洗い出しを行うことができます。製造プロセスのデジタル化や課題解決でお悩みの方は、ぜひお問い合わせください。