概要
製造現場では、ライン上から作業台へ、作業台から加工機へ、あるいはその逆方向といったように、ロボットアームがワークを1つずつ丁寧に掴んで搬送する作業が頻繁に行われています。これらの搬送は、従来は人手で行われていた作業の省人化、作業員の業務の軽減による生産性の向上を目的として、多くの現場で導入されている重要なプロセスです。
今回の記事では、このようなロボットアームによるワークのピック&プレース動作(把持と移動)を再現する方法について解説します。実際の現場の動きをシミュレーションで再現することで、搬送のタイミングやレイアウトの最適化など、工程設計や改善のヒントを得ることができます。
モデル
今回作成するモデルは下図のようになります。

このモデルは以下のようなプロセスが行われるラインを再現しています。
- ワーク入荷は3分に1個
- 入荷用パレットが空いていたら、パレットにワークを積載
- 入荷用パレットでロボットアーム1の場所までワークを搬送
- 作業台Aが空いている場合、ロボットアーム1を使ってパレットから作業台Aへ搬送(搬送時間1分)、パレットは次のワークを受け取りに帰還
- 加工機Aと加工機Bのどちらか一方でも空いている場合、ロボットアーム1を使って作業台Aから空いている加工機へ搬送(搬送時間1分)して加工(処理時間1分)
- 作業台Bが空いている場合、ロボットアーム2を使って加工機から作業台Bへ搬送(搬送時間1分)
- 出荷用パレットが空いている場合、ロボットアーム2を使って作業台Bから出荷用パレットへ搬送(搬送時間1分)
- 出荷用パレットを使って出荷、出荷後パレットは次のワークを受け取りに帰還
なお、入荷用パレットと出荷用パレットはそれぞれ1台、作業台Aと作業台B、加工1と加工2におけるワークは1個、ロボットアームが1度に掴めるワークは1個と仮定します。
シミュレーションと分析
モデルの作成が終わったらシミュレーションを行います。今回はシミュレーション時間を480分に設定します。
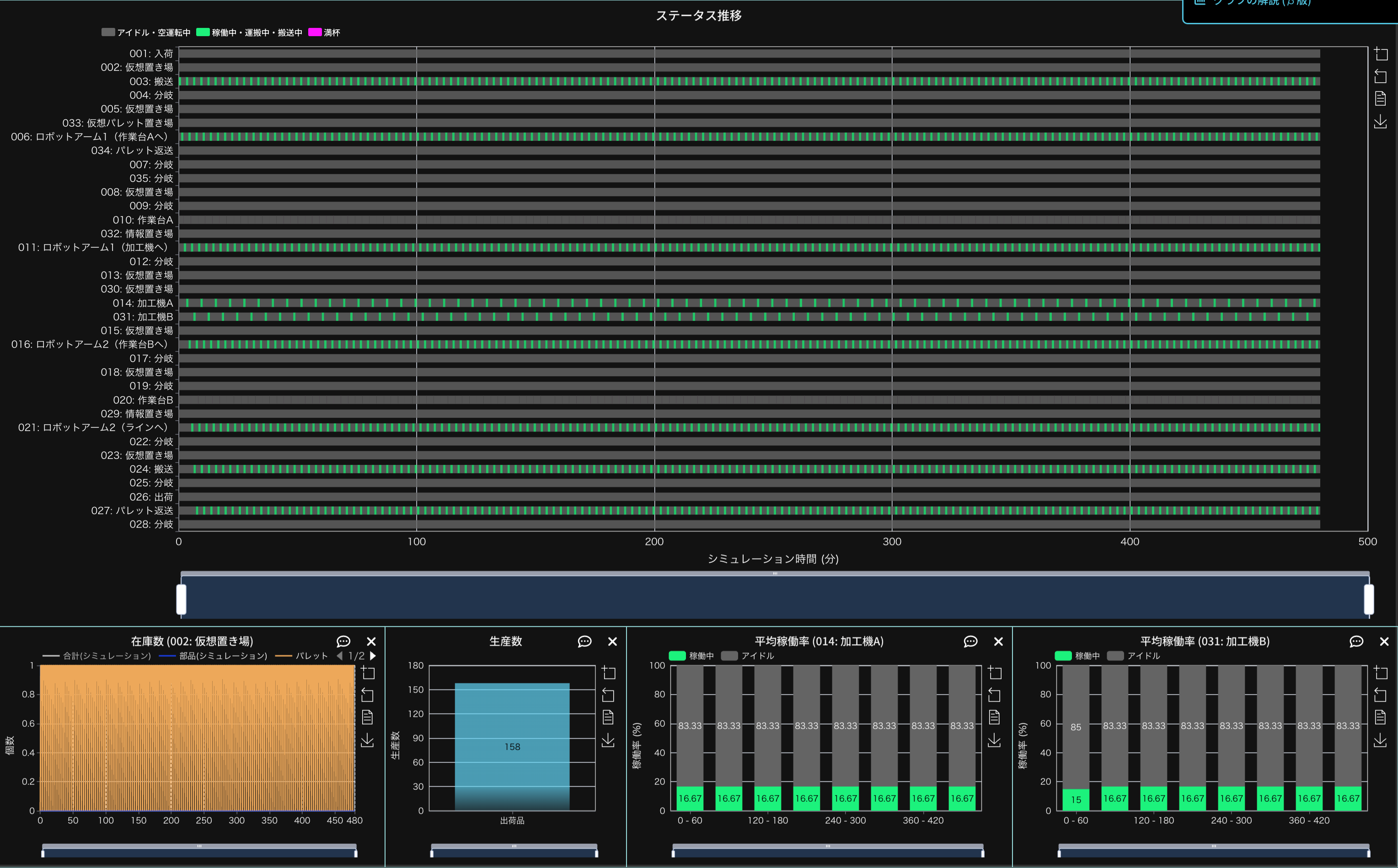
以上の結果から、入荷品置き場である「002仮想置き場」の在庫数が増えていないことから、入荷に対して十分な処理能力があることがわかります。また、480分間で158個の製品が生産されていることも確認できました。これは、480分間に供給された部品数(160個)とほぼ等しいですが、わずかに少ないのはラインの立ち上がりに時間がかかるためと考えられます。
次に、設定を変更してシミュレーションを行ってみましょう。入荷速度を「3分に1個」から「1分に1個」へ変更してみます。

同様に結果を確認すると、今回は入荷品が置かれる「002仮置き場」の在庫数が右肩上がりに増加していることがわかります。これは、ライン内でボトルネックが発生していることを示しています。ステータスの推移などを確認すると、以下の2点が同時にボトルネックとなっていると考えられます:
- 2台のロボットアームが、それぞれ2つの搬送工程(いずれも処理時間1分)を担当しているため、最低でも2分の搬送時間が必要になること。
- 入出荷用のパレット搬送に片道1分、往復で2分の搬送時間がかかること。
これらの要因により、480分で処理できるワークの上限は240個となり、現状の構成(生産数226個)では処理能力の限界に達していることが明らかです。これ以上生産数を増やすためには、ロボットアームの台数を増やす、あるいはパレット搬送能力を向上させるなど、搬送時間を削減するための対策が必要になります。
次に、2台の加工機の処理時間を1分から4分へ延長すると、どのような影響があるのかを確認してみましょう。
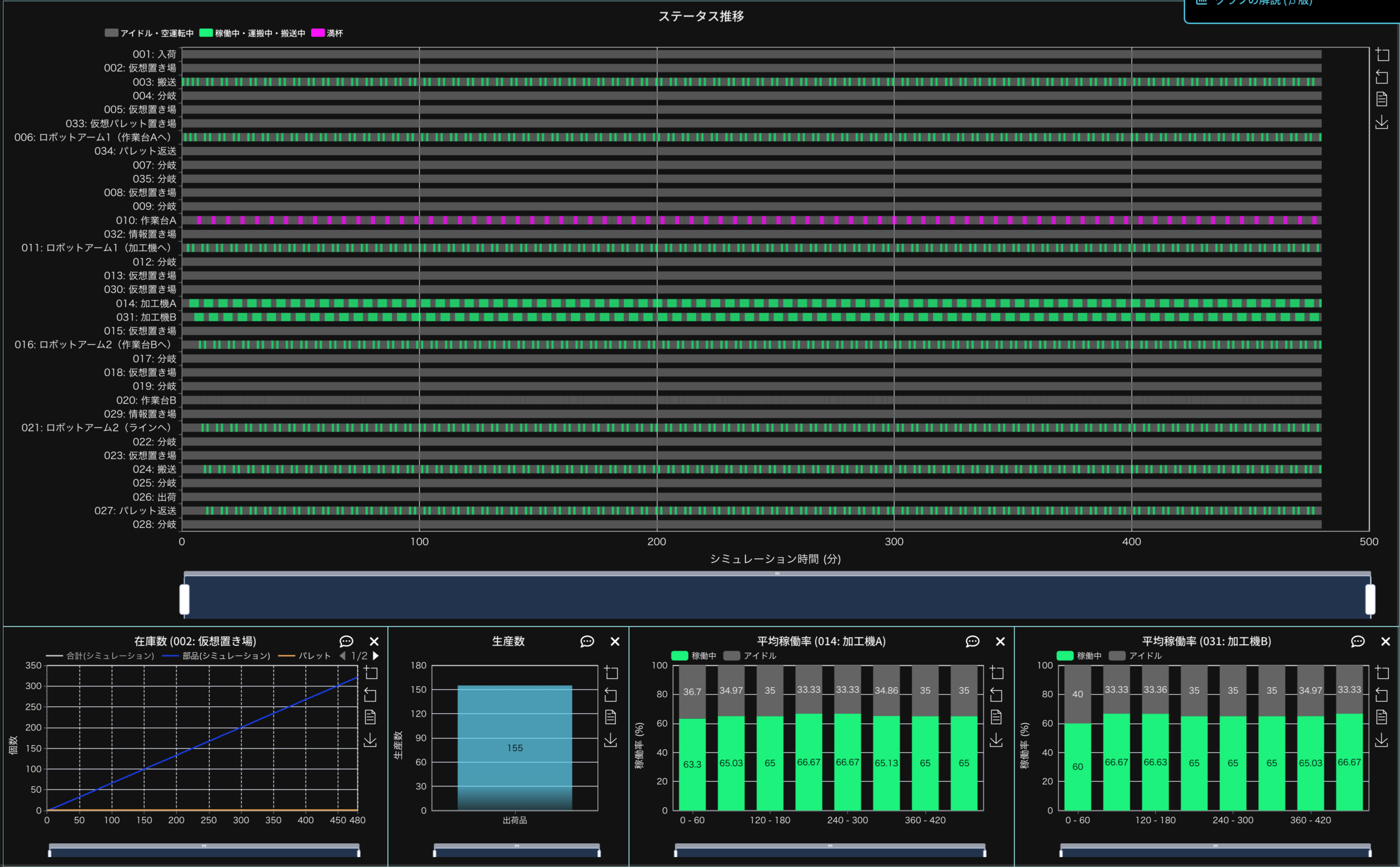
今回は加工機の処理時間が長くなったことにより、生産数が前回よりも減少しています。また、上流側の搬送時間に比べて加工機での処理時間が長いため、作業台Aにワークが滞留し、作業台Aへ新たなワークを搬送できない時間帯(桃色表示)=新たなボトルネックが発生していることが確認できます。このボトルネックを解消するには、上流側におけるワークの搬送タイミングや供給量を見直す必要があります。
このように、さまざまな状況を想定しながらパラメーターを変更したシミュレーションを繰り返し実施することで、生産ラインの性能を評価し、ボトルネックなどの課題を把握・検討することが可能になります。
まとめ
今回は、製造現場でよく使用されているロボットアームによる搬送を再現し、シミュレーションを行う手順について解説しました。assimeeを使用すれば、実際の現場で使われている搬送装置や加工機械を模したモデルを作成し、シミュレーションを実施することが可能です。また、各種設定を変更しながらシミュレーションを繰り返すことで、生産ラインの性能を可視化したり、故障時の影響やその対策を検討したりと、現場改善に役立つ分析を行うことができます。
assimeeでは、実際の製造プロセスをモデル化し、シミュレーションすることで、プロセスの見える化や潜在的な課題の洗い出しを行うことができます。製造プロセスのデジタル化や課題解決でお悩みの方は、ぜひお問い合わせください。