概要
この記事では前回の記事で計算した結果を活用し、assimeeを使って生産ラインのボトルネックを分析する方法を解説します。assimeeでは、シミュレーションや最適化を行った後に、各プロセスの結果(グラフ)を基にボトルネックを分析することが可能です。従来、ボトルネックの分析は一定の経験や勘を必要とする作業でしたが、LLMを活用したボトルネック特定機能を使用することで、AIがボトルネックの場所を推定します。これにより、ボトルネック分析の業務効率が向上し、生産ラインの改善がより簡単に行えるようになります。
モデル
モデルは以下の通りです。
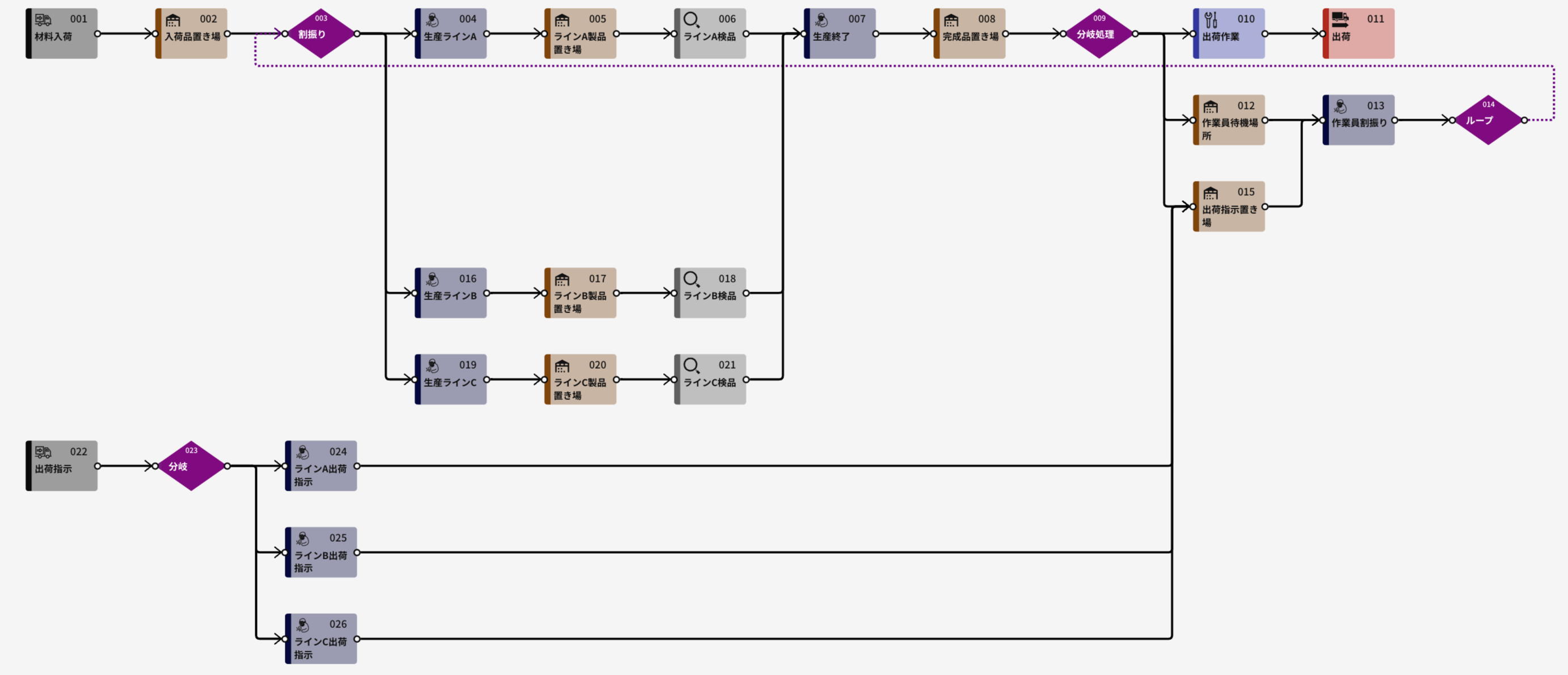
モデルに使用するパラメーターは、前回の最適化結果(012作業員待機場所の初期仕掛=作業員57人)とその際の設定値を使用します。
ボトルネックの探索と生産ラインの改善
シミュレーションの結果画面に表示されるボトルネック特定タブを選択すると以下の画面が表示されます。
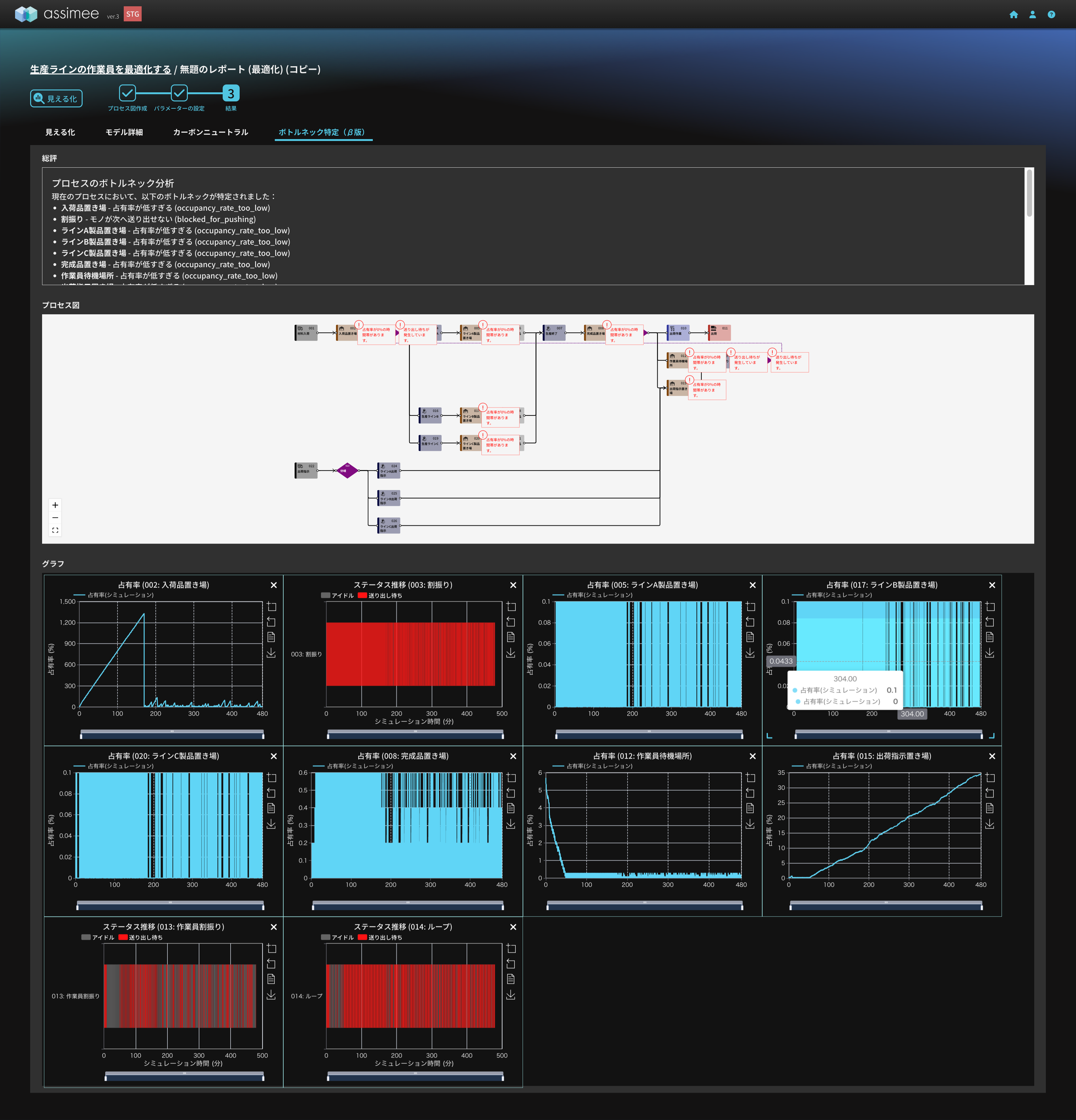
LLM機能によるボトルネックの可能性が高い場所の指摘が、総評には文章で、プロセス図には吹き出しで、最下段には関連するプロセスカードのグラフが表示されます。
ここでは得られた指摘の内、関係がありそうなものを並べてみましょう。
- 「002入荷品置き場」の占有率が低い
- 「003分岐」に送り出し待ちが発生している
- 「005ラインA製品置き場」、「017ラインB製品置き場」、「020ラインC製品置き場」の占有率が低い
- 「014ループ」に送り出し待ちが発生している
- 「015出荷指示置き場」に送り出し待ちが発生している
これらの情報を元にモデルの設定や各プロセスカードの在庫数、稼働率などのグラフを確認して見ると以下のような分析をすることができます。
- 「002入荷品置き場」の占有率が低い
→入荷した材料が全て使用されている - 「003分岐」に送り出し待ちが発生している
→ループで入ってくる出荷指示が滞留 - 「005ラインA製品置き場」、「017ラインB製品置き場」、「020ラインC製品置き場」の占有率が低い
→「004生産ラインA」、「016生産ラインB」、「019生産ラインC」の稼働率を確認→材料がないため生産が停止している時がある - 「014ループ」に送り出し待ちが発生している
→出荷指示が滞留 - 「015出荷指示置き場」に送り出し待ちが発生している
→出荷指示が滞留
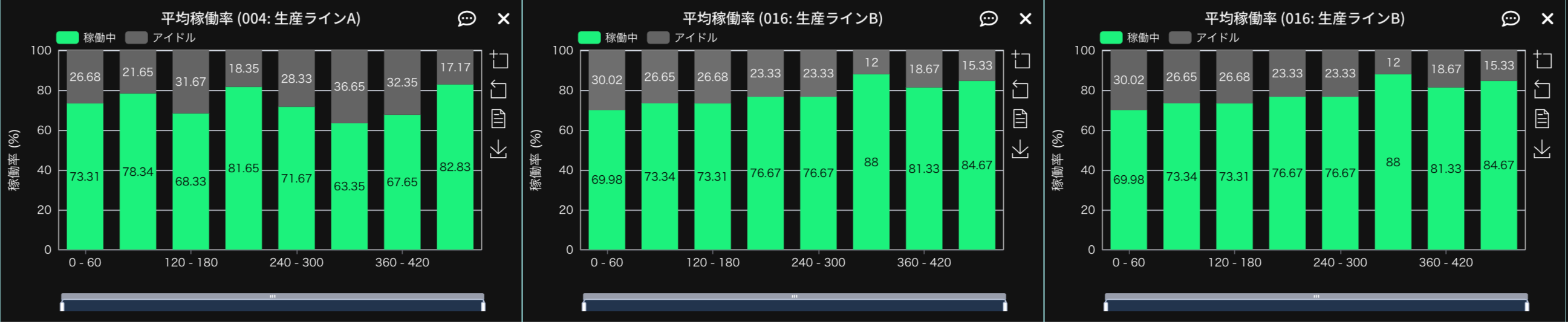
まとめると、以下のようになります。
- 出荷指示に対して材料が足りないため、3つの生産ラインでの生産が行われず、上流の「003分岐」で出荷指示が滞留している
- 「004生産ラインA」、「016生産ラインB」、「019生産ラインC」の稼働率を確認すると、まだ生産能力に余裕が存在する
これらのことから、モデルに入荷する「材料」の数を増加させることで、生産ラインの稼働率を上げ、生産数が増加する可能性があることがわかります。そこで、「001入荷」の設定を以下のように変更して再度シミュレーションを行なってみます。
変更前:入荷品目「材料」、個数「10個」、時間間隔「1分」
生産数:「製品A」358個、「製品B」323個、「製品C」358個
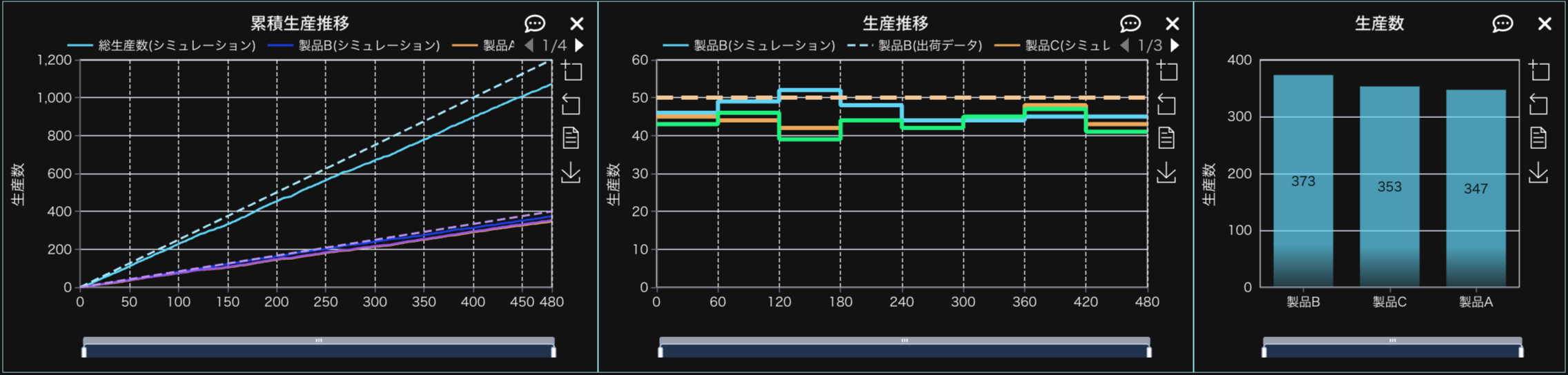
変更後:入荷品目「材料」、個数「20個」、時間間隔「1分」、生産数
生産数:「製品A」373個、「製品B」353個、「製品C」347個
*出荷指示にランダム変数が含まれるため結果一致しないことがあります。
変更後、生産数がやや増加していることが確認できます。このようにボトルネックを探索することで、生産数を増加させるだけでなく、過剰な人員や部品を削減するといった対策を講じることが可能です。また、ボトルネックを繰り返し探索することで、より効率的な生産ラインの構築につなげることができます。
まとめ
今回の記事では、生産ラインのボトルネックを探索し、ボトルネックを解消するためにパラメーターを改善する方法について解説しました。assimeeではLLM機能を活用することで、生産ラインに潜むボトルネック要因を容易に洗い出すことが可能です。従来、ボトルネック要因の特定には経験や勘が必要でしたが、assimeeを活用することで業務の標準化や平準化を実現することができます。
assimeeでは、実際の製造プロセスをモデル化し、シミュレーションすることで、プロセスの見える化や潜在的な課題の洗い出しを行うことができます。製造プロセスのデジタル化や課題解決でお悩みの方は、ぜひお問い合わせください。