概要
生産工程では、加工順序が決まっている場合もありますが、順序に関係なく、加工さえ完了すれば良い工程も存在します。このように、任意の順番で加工を開始できる工程をランダムショップと呼びます。
今回は、ランダムショップ型の生産方式のモデルを作成し、シミュレーションを実施して結果を分析します。また、通常の生産ラインとの比較も行い、その特徴や違いを検証してみましょう。
モデル
今回使用するモデルは以下の通りです。
3つの工程(ショップ)で材料を加工し、製品とする生産ラインを想定します。各工程の処理時間は以下の通りです:
- 加工1:処理時間 10分
- 加工2:処理時間 15分
- 加工3:処理時間 12分
このモデルでは、これらの工程をランダムな順序で実行できるように設計します。また、仕掛品(すでに3つのうちどれかの加工が済んでいる材料)を、無加工品よりも優先して加工するように設定しています。
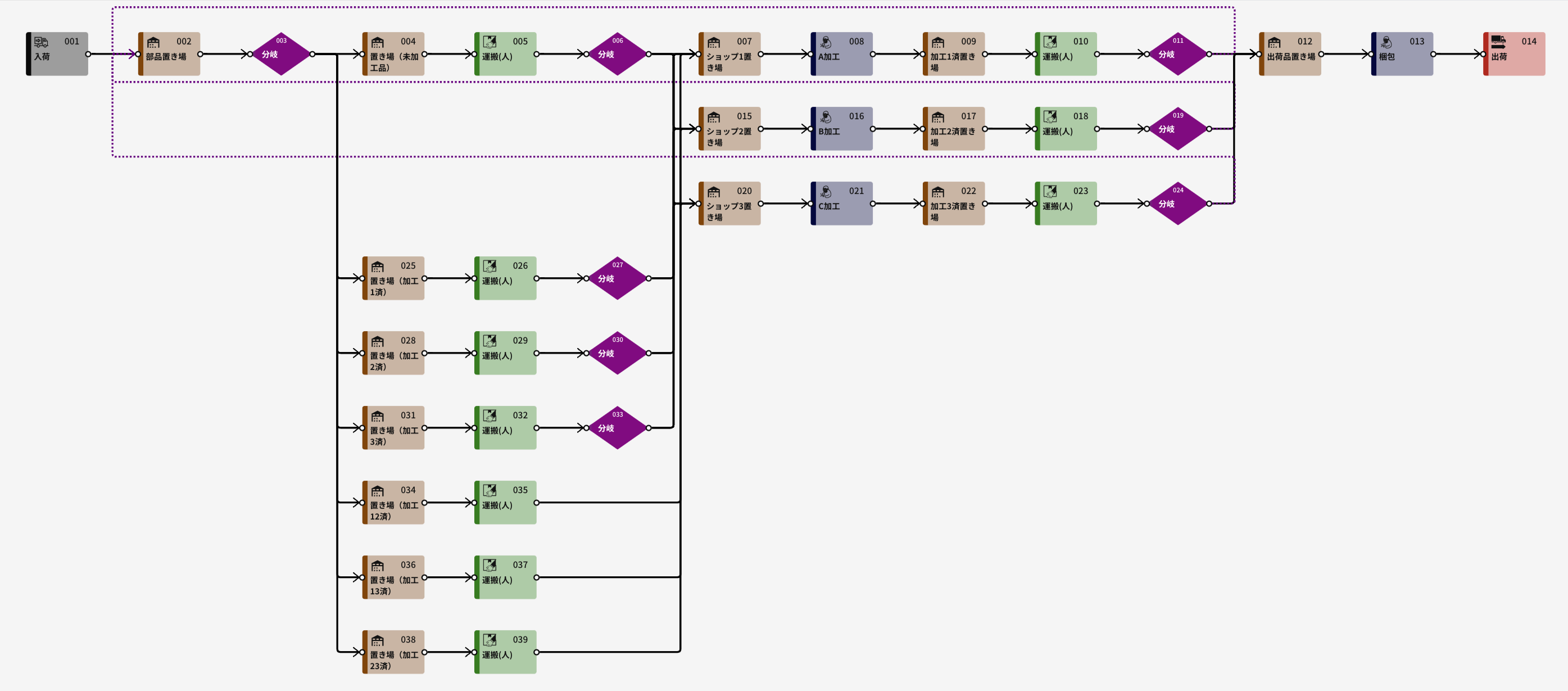
上流から加工を順番に行うフローショップ型の生産ラインを先ほどのランダムショップ型と同様になるようにモデル化すると、以下のようになります。
このモデルは、ランダムショップ型に比べて構造が簡素で、工程の流れが直線的であることが特徴です。

それぞれの加工時間を同一に設定した上で、これら2つのモデル(ランダムショップ型とフローショップ型)の生産量にどのような差が生じるか、シミュレーションで確認してみましょう。
なお、材料の入荷は、フローショップ型の加工1に在庫が発生しないよう調整しています。
シミュレーションと分析
モデルの作成が完了したら、次にシミュレーションを行います。2つのモデルについて、シミュレーション時間を480分に設定して実行しました。
以下は、そのシミュレーション結果です。
ランダムショップ型
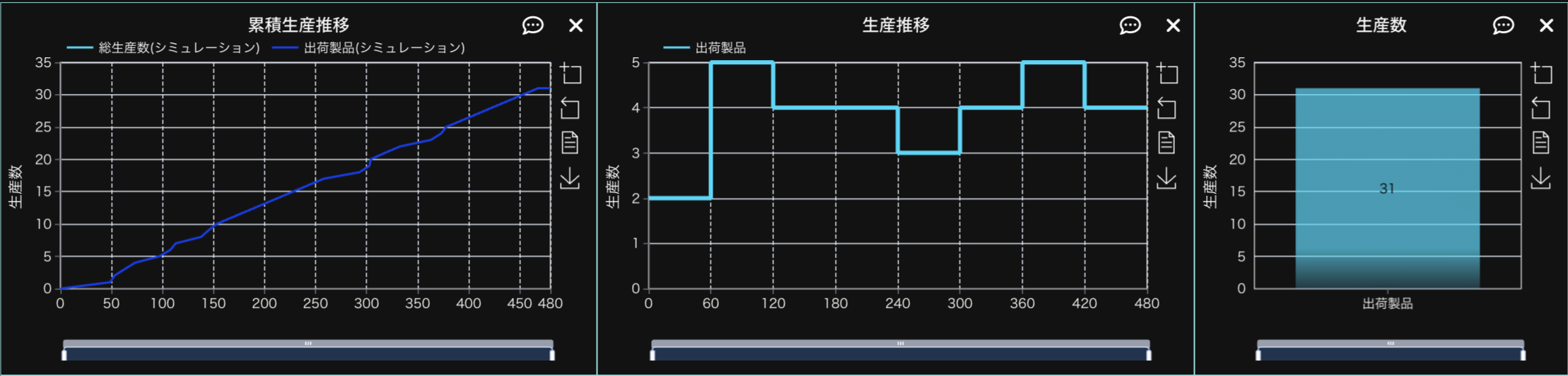
ランダムショップ型の生産数は31個となりました。また各プロセスの稼働率と各ショップの加工在庫(加工前の置き場の在庫)は以下のようになりました。各ショップの稼働率はどれも高くなります。一方で、どのショップにも加工在庫が発生していることが分かります。
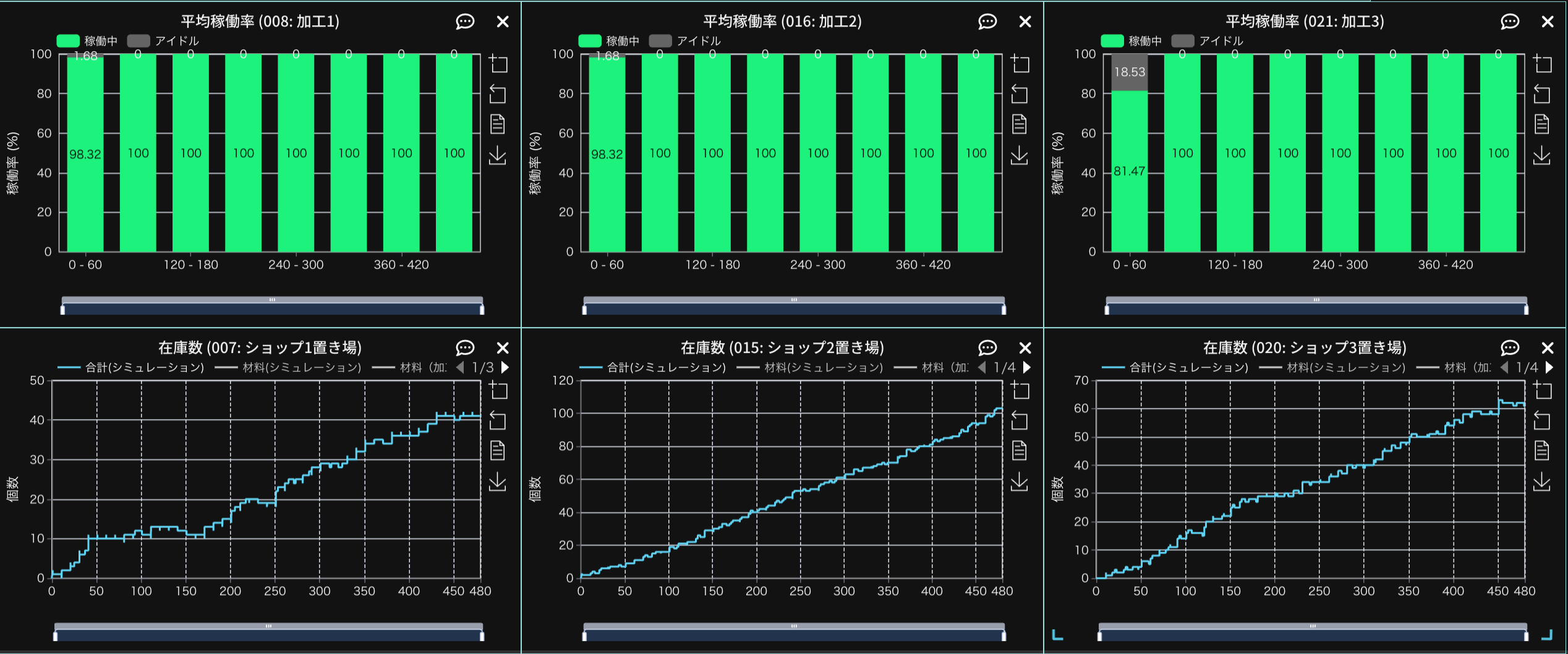
フローショップ型
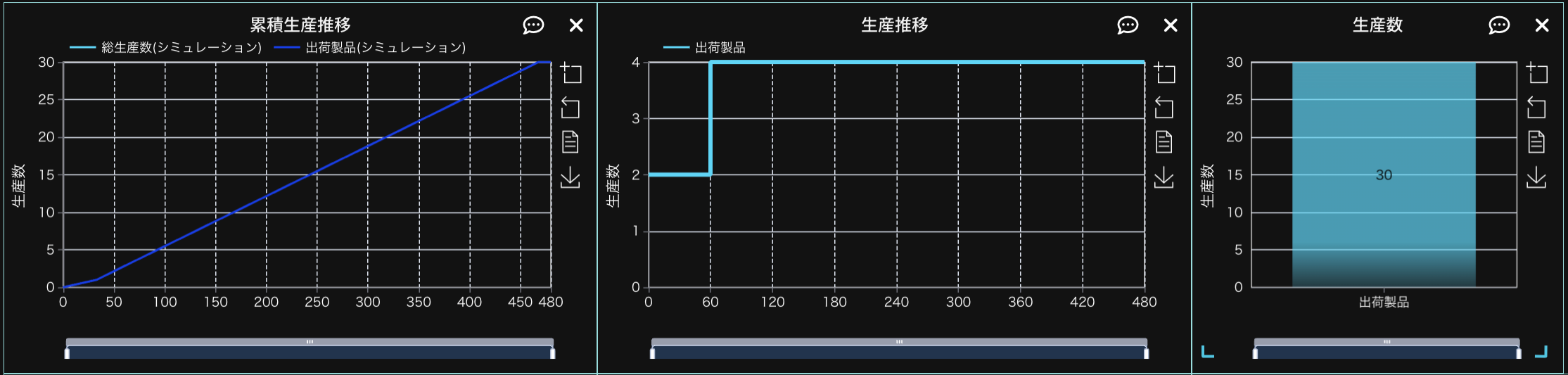
フローショップ型の生産数は30個、稼働率と在庫は以下のようになります。ランダムショップ型と比べると最も加工時間の長いショップ2がボトルネックとなるため、ショップ3の稼働率が低くなります。一方で在庫の面ではショップ3置き場には在庫が生じず、加工時間の長いショップ2とその前のショップ1に在庫が発生していることが分かります。
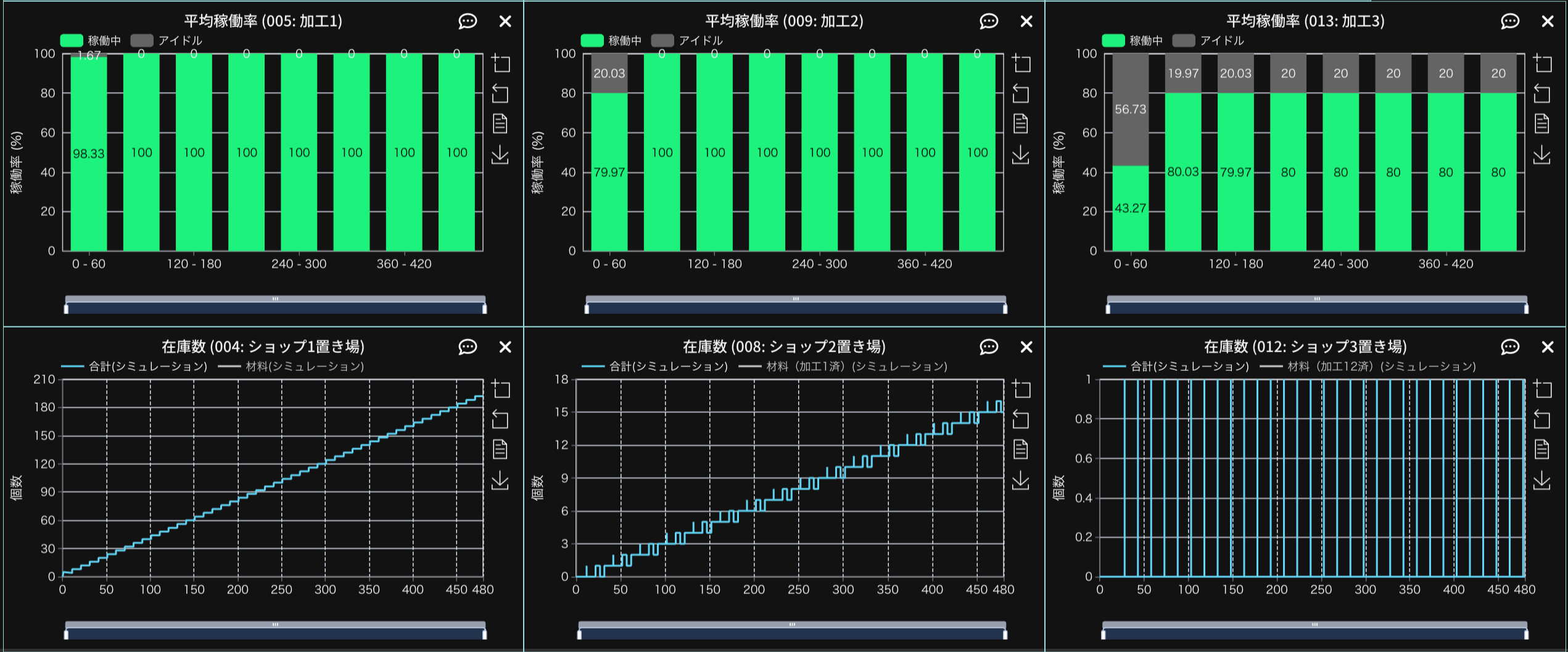
今回のシミュレーション結果から、ランダムショップ型の方がやや生産量が多くなり、各ショップを平均すると稼働率がやや高くなることが確認されました。ランダムショップ型の方が無駄なく設備が活用されていると言うことができます。一方で、各ショップで在庫が増加してしまう点も「見える化」されました。これは、効率性と在庫管理の間でトレードオフが生じることを示しています。
まとめ
この記事では、ランダムショップ型生産方式の「見える化」を行い、通常のフローショップ型生産ラインとの生産量の比較について解説しました。今回の解説でも示した通り、assimeeを活用すれば、生産プロセスの順番やパラメーターを簡単に変更し、シミュレーションを通じて生産量や稼働率を「見える化」することが可能です。また、モデル間の比較も手軽に行うことができます。これにより、生産ラインの改善や改造の検討といった業務を効率的に進めることができます。
assimeeでは、実際の製造プロセスをモデル化し、シミュレーションすることで、プロセスの見える化や潜在的な課題の洗い出しを行うことができます。製造プロセスのデジタル化や課題解決でお悩みの方は、ぜひお問い合わせください。