概要
この記事では入荷は十分にある条件で、複数の出荷ラインをもつモデルの出荷量を人の最適化で調整する方法を解説します。このような、モデルに対しては出荷目標に合わせて人数などプロセスのパラメーターを調整するためには経験と勘が不可欠でした。assimeeでは人やパラメーターの最適化機能を使って現場の業務の効率化と平準化に加えて属人化の排除を行うことが可能です。今回は従来のassimeeを使った最適化に、新たに実装された生成AI(LLM)によるボトルネック解説機能を併用して最適化をより簡単に活用する方法についても解説します。
モデル

今回使用するモデルは上図のとおりです。入荷した商品を加工し、3つに分岐し、3つの出荷先に向けて出荷を行う出荷ラインを設置したモデルとなっています。大型の倉庫・置き場からの出庫を想定して入荷数は十分な数を用意しており、出荷目標に対しては出荷作業あるいは加工の人数を調整することで出荷を調整するようになっています。
シミュレーションとLLMによる分析
モデルが完成したら、シミュレーション時間を480分に設定することで、シミュレーションを行います。シミュレーションの結果は以下の通りとなりました(分岐にランダム変数が含まれるため完全一致はしません)。
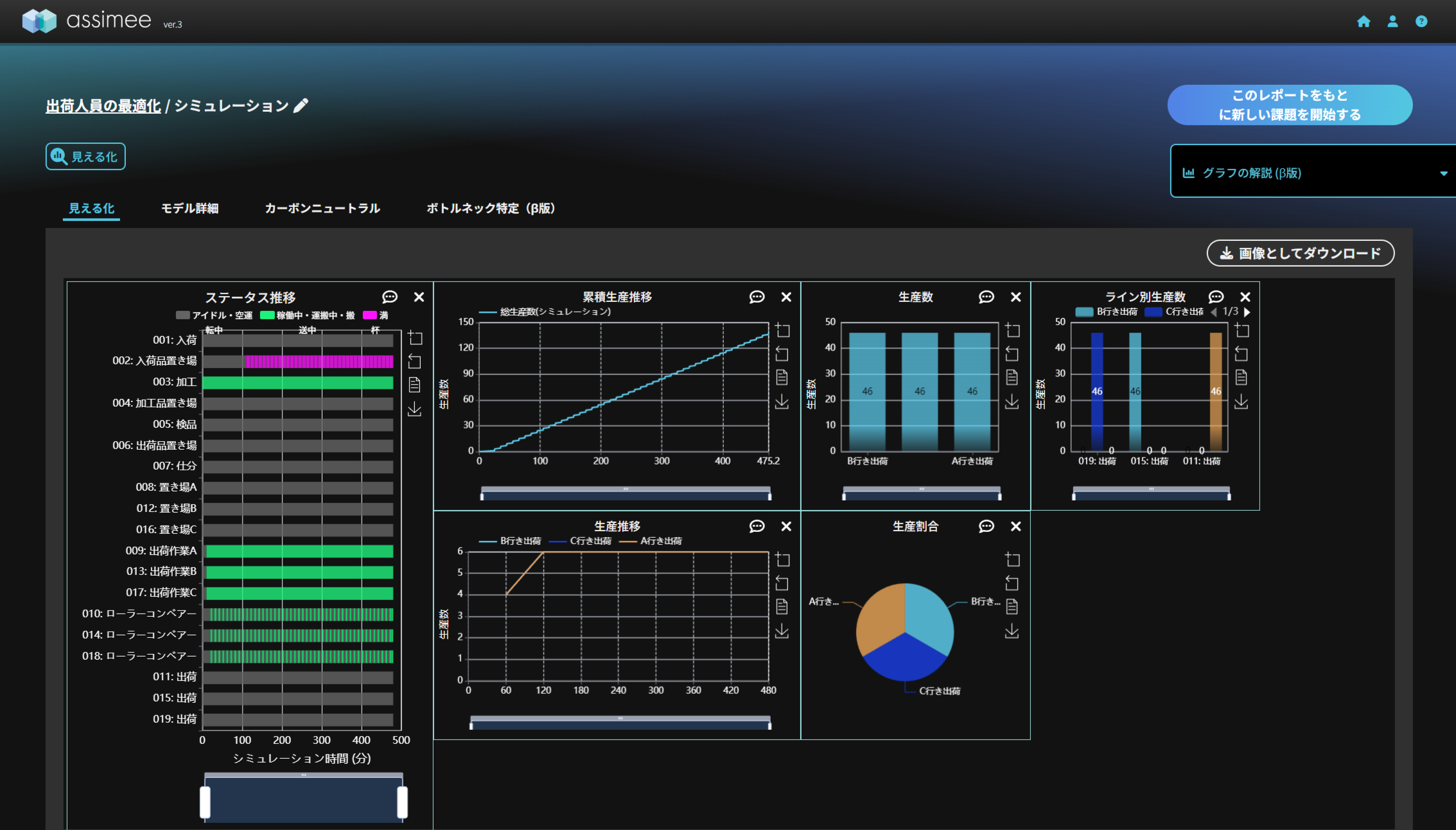
3つの出荷ライン(A、B、C)の出荷数は同数で、1時間に約6個、8時間で46個と設定しています。「ステータス推移」をみると入荷品置き場が十分に入荷を用意するとの設定どおり溢れていることが分かります。それでは「ボトルネック特定」のタブを選択してみましょう。
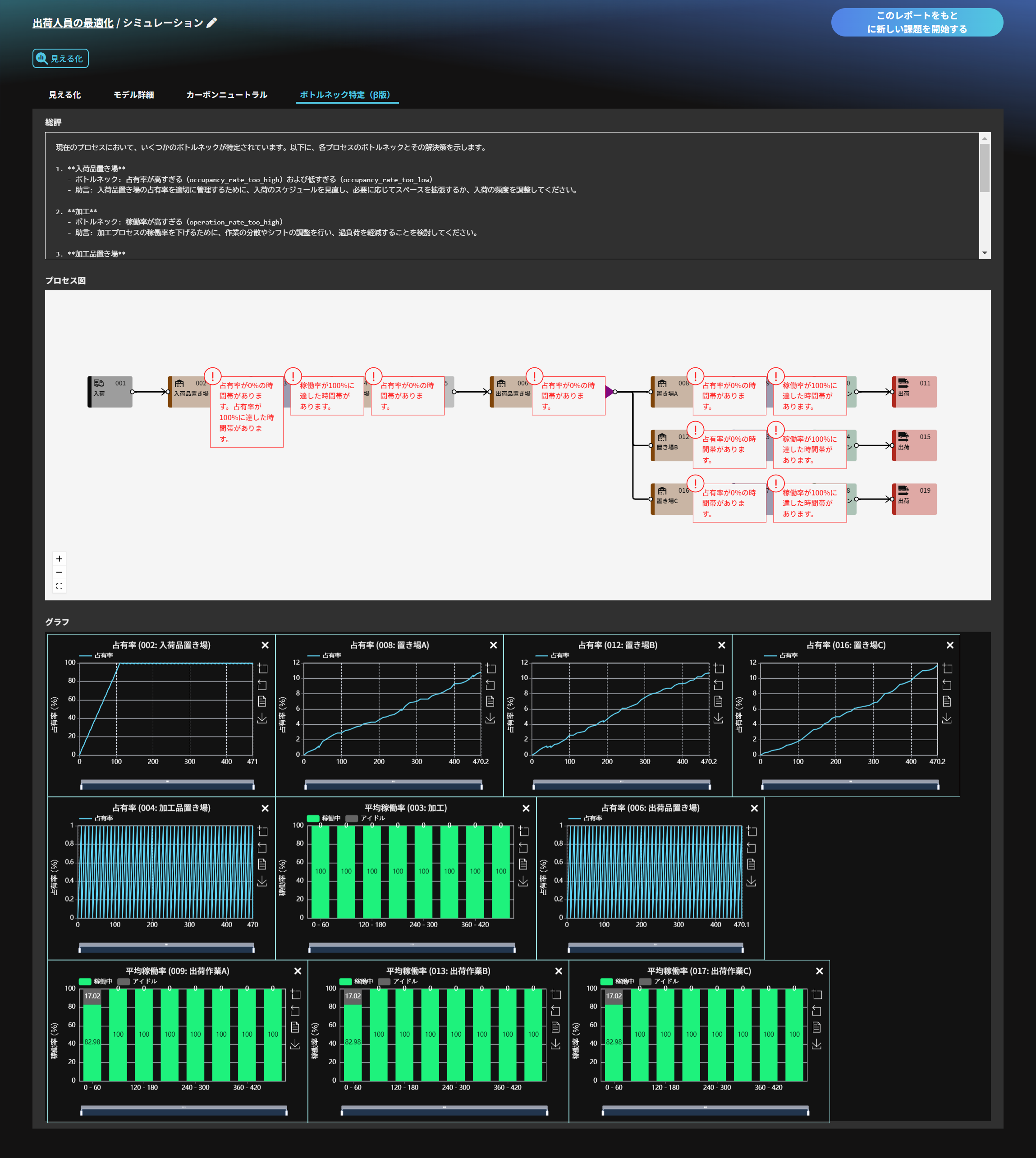
シミュレーション結果をAIが分析して、ボトルネックが発生して居そうな場所を推定し、モデルの総評、プロセス毎の分析結果、対応するグラフを表示してくれます。
今回の分析(AIのコメントとグラフ)を総合すると「003加工」、「009出荷作業A」、「013出荷作業B」、「017出荷作業C」の稼働率が高い一方で、出荷作業の直前にある置き場の占有率(在庫量)が増加しており、出荷作業の人数を増やすことで出荷量を増加させることが可能だと考えられます。
*他にも、出荷作業の処理能力や同時処理数を上げると言った解決策も考えられます。
人の最適化(出荷作業だけを対象)
まず出荷目標を考えます。現在の出荷能力は3つの出荷ラインそれぞれで毎時6個となっているので、約3倍となる20個にすることを考えて、3つの出荷作業の作業人数を増加させてみましょう。
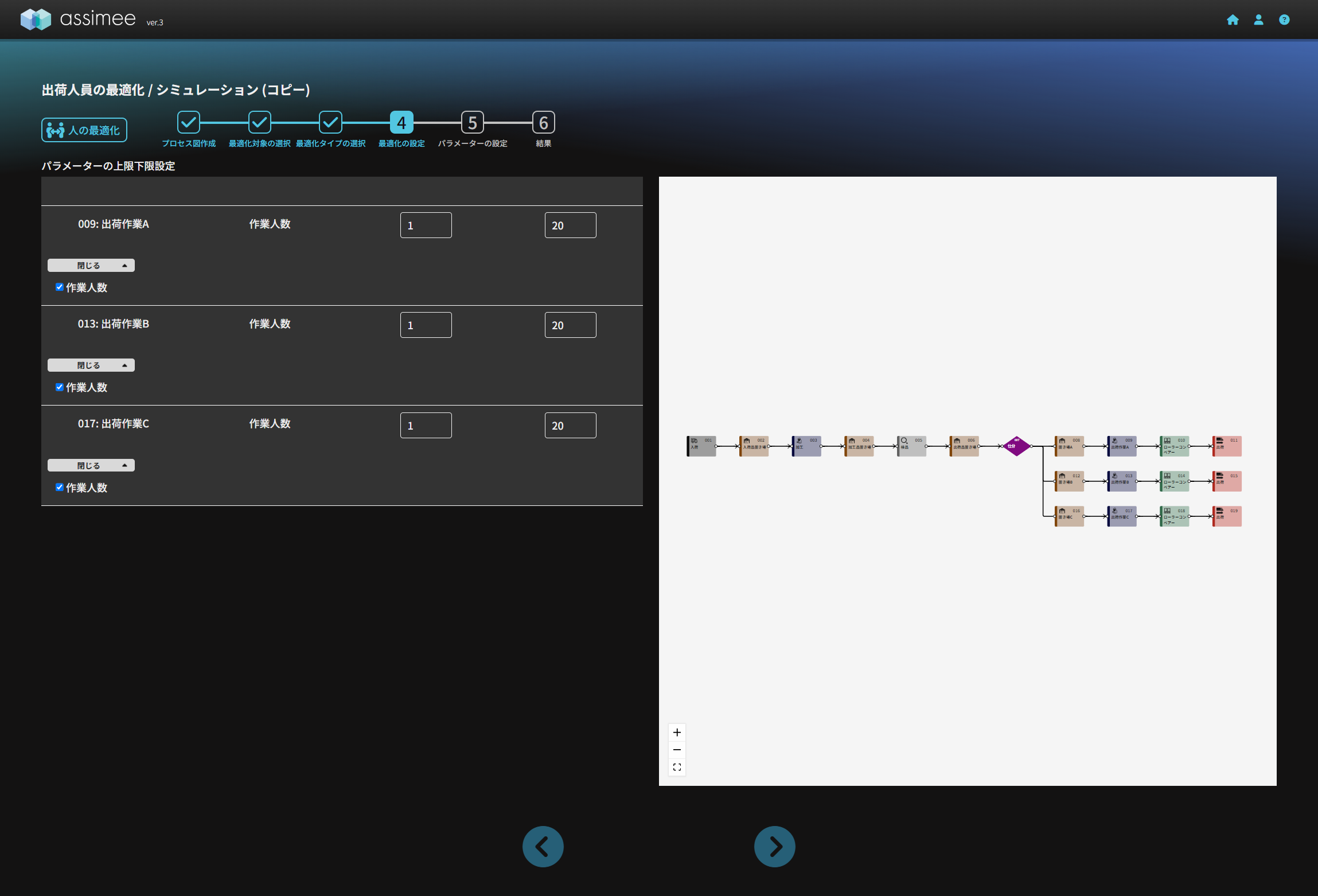
シミュレーション時点での人数は1人でしたが、生産数を6倍に増やすことを考えて、上記のように人の最適化のパラメーターの上下限値を設定して人の最適化を行ってみましょう。
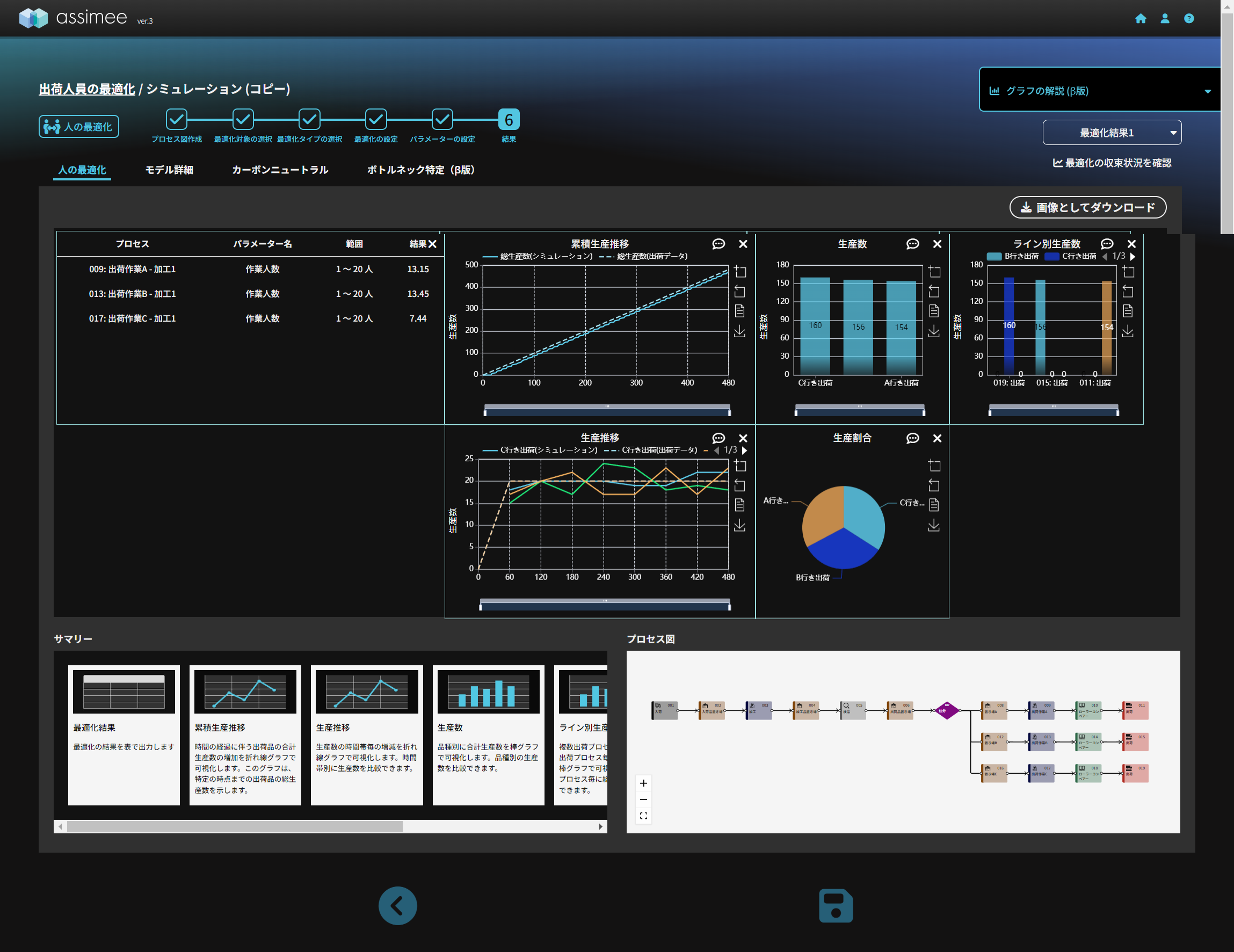
以上のような最適化結果が得られました(分岐や最適化にランダム変数が含まれるため完全一致はしません)。対象となった3つの出荷作業プロセスの作業人数は「最適化結果」から以下のようになったことが分かります。
- 「009出荷作業A」の作業人数:13.15人
- 「013出荷作業B」の作業人数:13.45人
- 「017出荷作業C」の作業人数:7.44人
一方で、「累積生産推移」と「生産推移」を見ると無事に出荷目標が達成されていることが分かります。
しかしながら、「009出荷作業A」と「013出荷作業B」の作業人数に比べて「017出荷作業C」の作業人数が少ないものの、出荷数が同じであることから、作業人数が多すぎる可能性がありそうです。そこで、少しやり方を変えて最適化を行ってみましょう。
人の最適化(加工作業を対象に追加、人数制限条件を追加)
次は、先ほどの最適化対象に加えて「003加工」を対象に加えた上で、作業人数の拘束条件を追加してみます。「003加工」を追加するのは先ほどの結果で「009出荷作業A」と「013出荷作業B」の作業人数に比べて「017出荷作業C」の作業人数が少ないものの、出荷数が同じであることから、作業人数をさらに絞ることが出来ると考えられること、AIの指摘している「003加工」はフル生産となっているため、ここの加工量を増やすことで、中間在庫を増やし、その結果としてモデル全体の人数を減らすことが出来る可能性があるからです。人数の拘束条件を入れるのは、条件を次第に厳しくすることで最適値を探索することが出来るからです。
実際には拘束条件を変え(減らし)ながら、複数回の最適化を行っていますが、ここでは最後の結果のみを解説します。
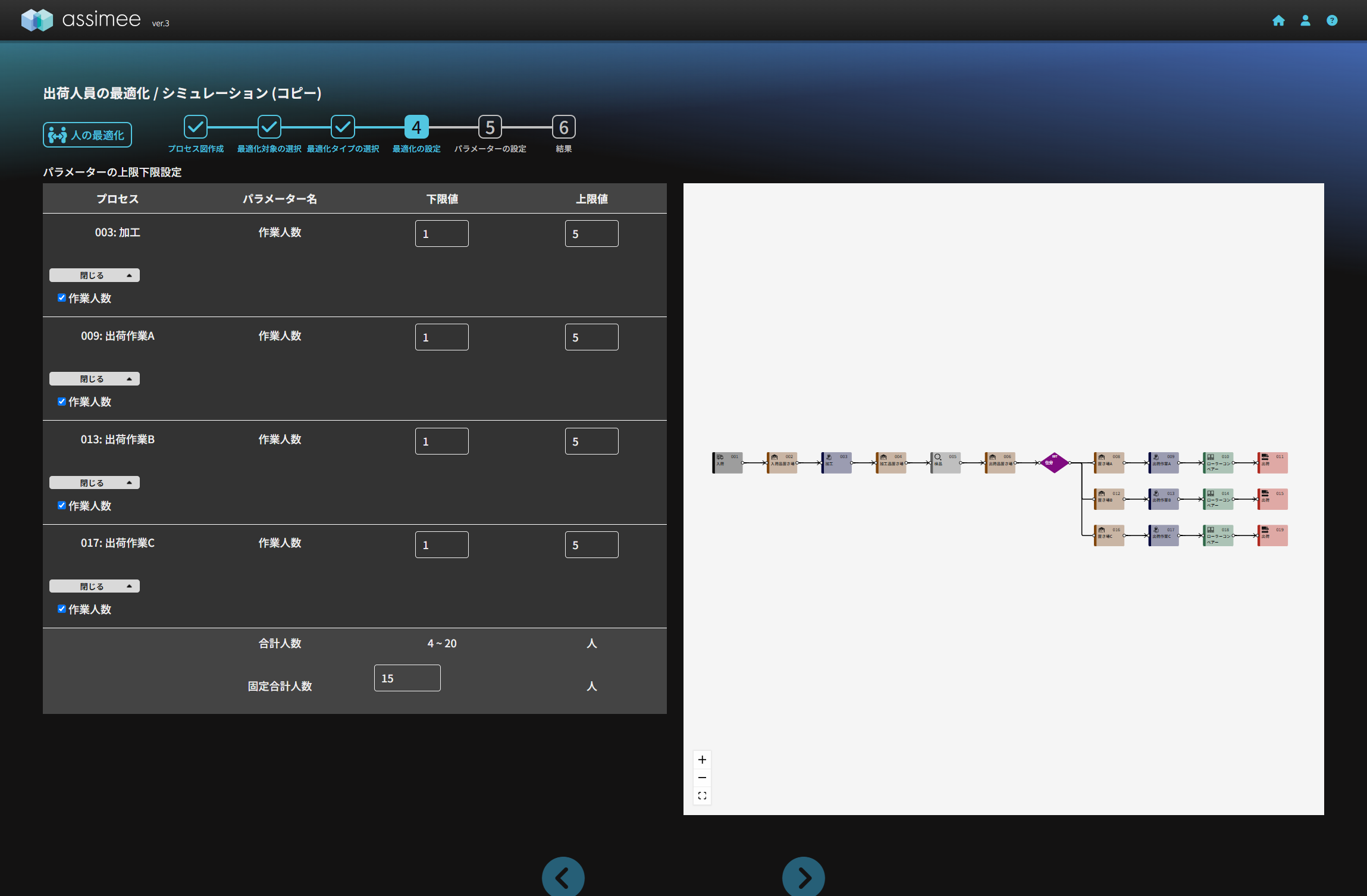
合計の作業人数の拘束条件として15人、それぞれプロセスの作業人数の上下限値が5人を先ほどの最適化より人数を絞ることが出来ていることが分かります。
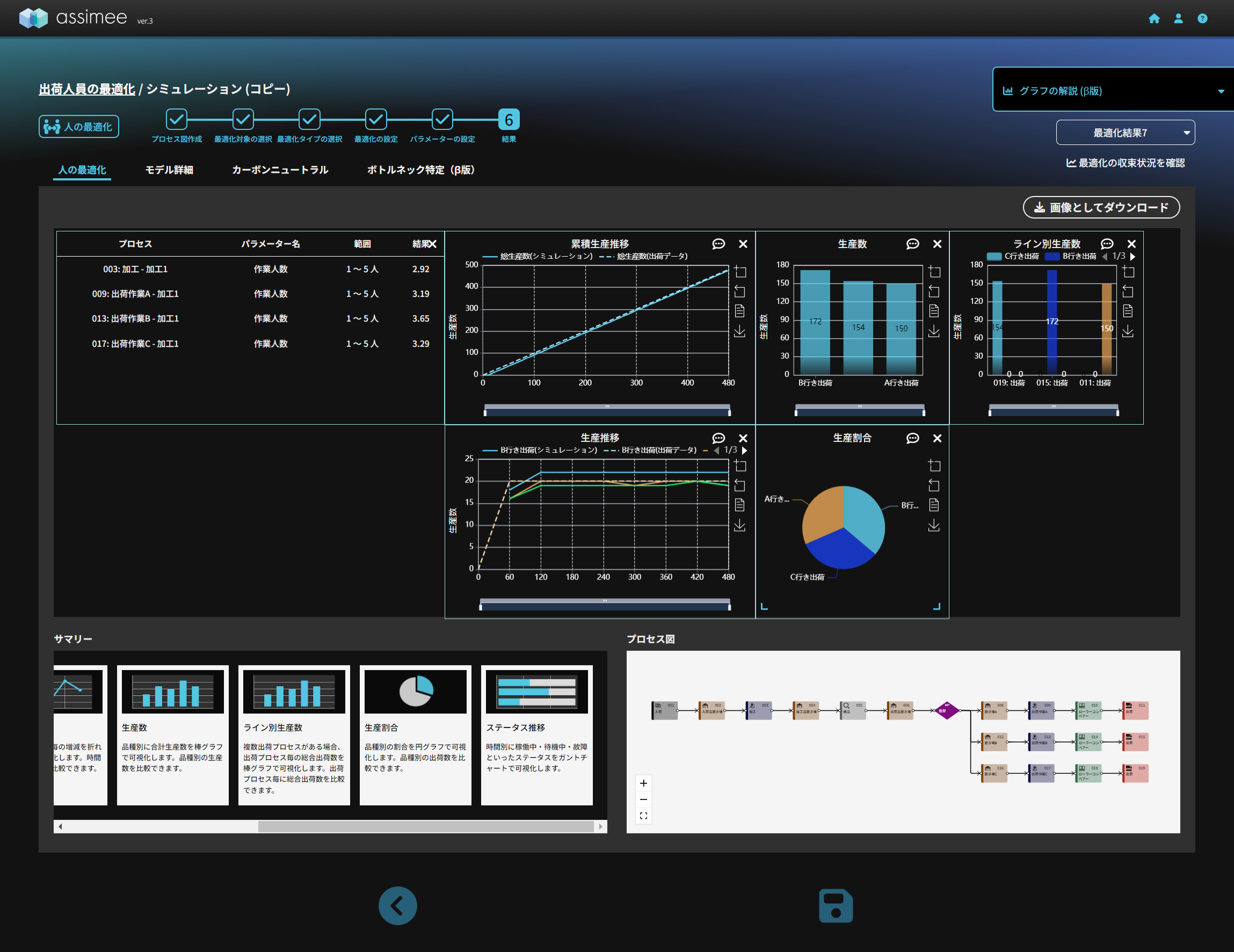
上のような最適化結果が得られました(分岐や最適化にランダム変数が含まれるため完全一致はしません)。「累積生産推移」と「生産推移」を見ると無事に出荷目標が達成されていることが分かります。一方で、対象となった1つの加工と3つの出荷作業プロセスの作業人数は「最適化結果」から以下のようになったことが分かります。
- 「003加工」の作業人数:2.92人
- 「009出荷作業A」の作業人数:3.19人
- 「013出荷作業B」の作業人数:3.65人
- 「017出荷作業C」の作業人数:3.29人
- 合計:13.05人
全体の人数が13.05人と拘束条件だった15人より若干人数が少なくなっていますが、最適化を繰り返すことで、出荷目標を達成しつつ、生産ラインのパラメーターを簡単に調整することが出来ました。
*最適化の結果が出荷目標と出荷数の誤差ではなく、拘束条件である15人からの誤差でソートされていることに注意して結果を分析します。
このように、これまでのような勘や経験に頼ったやり方でなく、あらかじめ決めておいた方法で、パラメーターを決めることが出来るため、業務の平準化や属人化の排除を行うことが出来ます。
まとめ
今回の記事では複数の出荷ラインをもつモデルに対して出荷量を人の最適化で調整する方法を解説しました。また、新しくassimeeに実装されたLLM機能を活用することで、ボトルネックの生じているプロセスの目星がつけやすくなり、最適化による課題解決が容易になりました。今回は、出荷作業だけを対象とした場合と、加工作業を対象に追加しモデル全体を対象+人数制限条件を追加した場合を検討しました。今回のようにボトルネックと指摘されている場所を多く含めるほど、人数を減らすことが出来る可能性が高まりますが、最適化の難度が上がる場合があること注意が必要です。
assimeeでは、実際の製造プロセスをモデル化し、シミュレーションすることで、プロセスの見える化や潜在的な課題の洗い出しを行うことができます。製造プロセスのデジタル化や課題解決でお悩みの方は、ぜひお問い合わせください。