概要
物流倉庫では毎日、出荷目標が変化します。このような倉庫では出荷量が作業人数に左右されるため、担当者は翌日の出荷目標を考慮して人員の手配を行う必要があります。この業務は毎日発生しますが、作業効率の異なる作業員が混在するため、人員手配業務に経験や勘が必要となり、業務の属人化や平準化が問題となっていました。今回の記事では、assimeeを使って出荷目標に合わせて時間帯別の人員配置を最適化する方法や、作業効率の異なる人員が混在する場合の人員配置のプロセスを効率化する方法について解説します。
モデル
今回、使用するモデルは下図の通りでDC型の倉庫の出荷作業を想定して、ピッキングプロセスを3つ用意します。
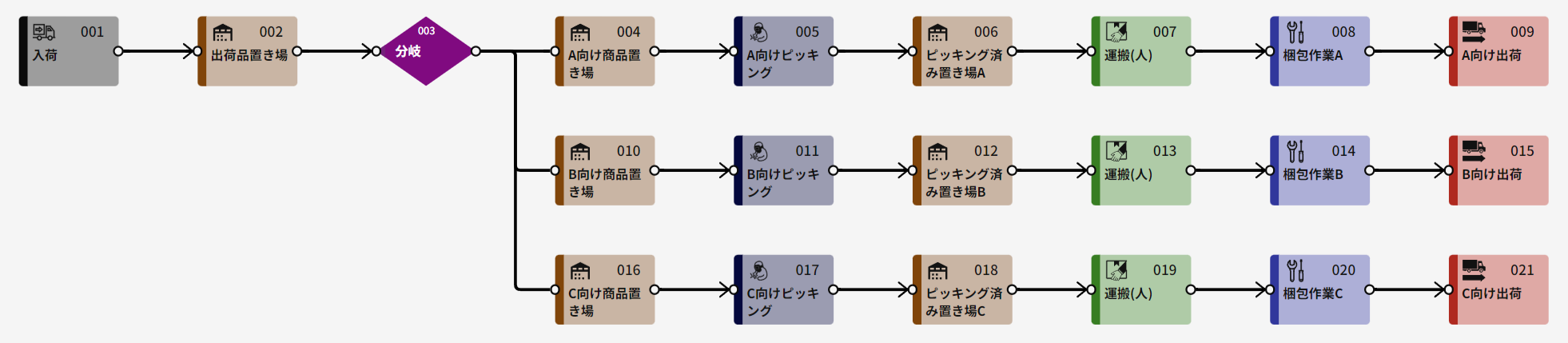
また、それぞれの以下のようにプロセスに異なる作業効率を設定することで、作業効率の異なる作業員が混在する状況を再現します。
- 005A向けピッキングプロセス:作業効率1
- 011B向けピッキングプロセス:作業効率0.75
- 017C向けピッキングプロセス:作業効率0.5
シミュレーションと最適化
モデルを作成したら最初にシミュレーションを行います。今回は8時間に相当する480分でシミュレーションを行いました。
ダッシュボードからシミュレーション結果を確認します。生産量を確認するとピッキングの作業効率1のA向けパレットと比べて、作業効率が0.75であるB向けは75%、0.5であるC向けのパレットは出荷量がA向けの半分となっていることが分かります。
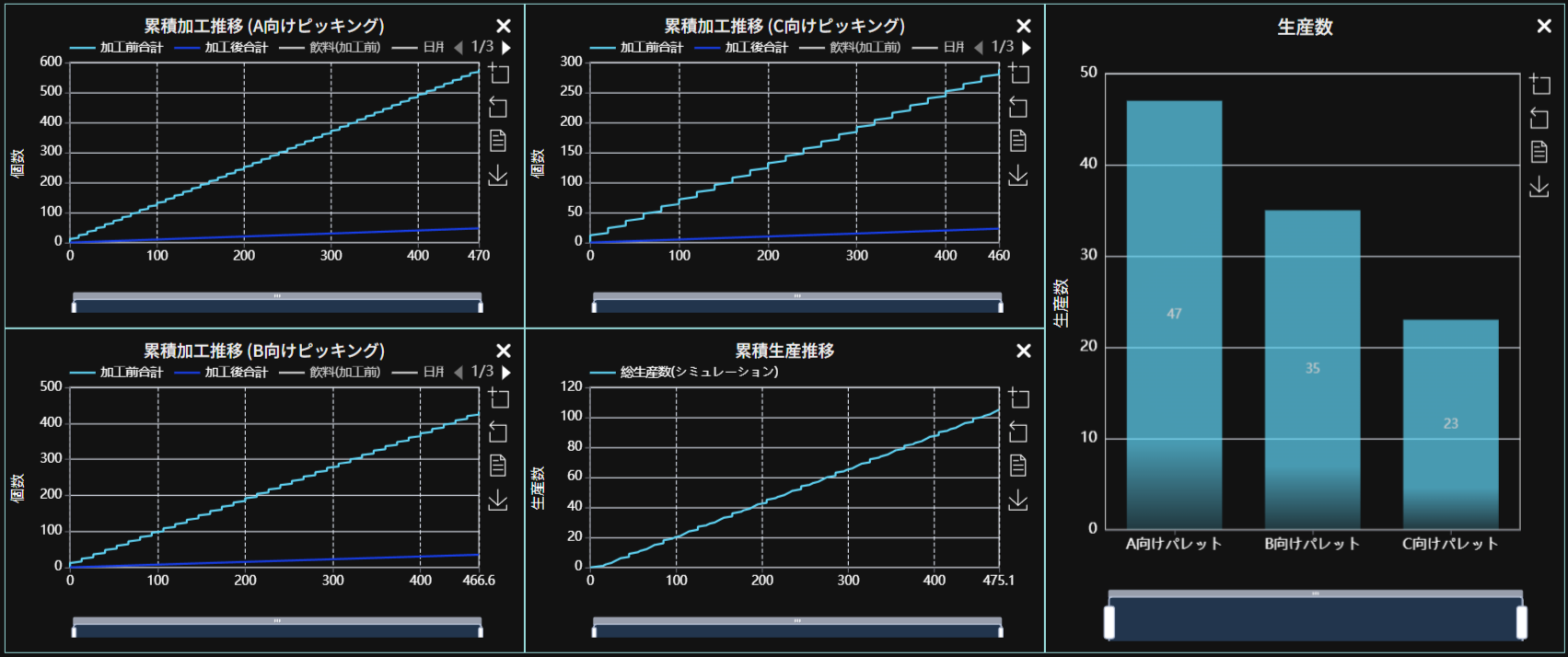
次に、時間帯別に人員配置の最適化を行いましょう。今回は、3つのピッキングプロセスの作業人員の最適化を行います。それぞれの作業効率は、モデルの欄に書いた値(A向け1、B向け0.75、C向け0.5)を使用し、パラメーターの移動範囲を1~50人に設定します。今回は、480分までのすべての時間帯に対して、1から50人という設定を行います。*次回以降に解説しますが、作業員の上限を設定することも可能です。
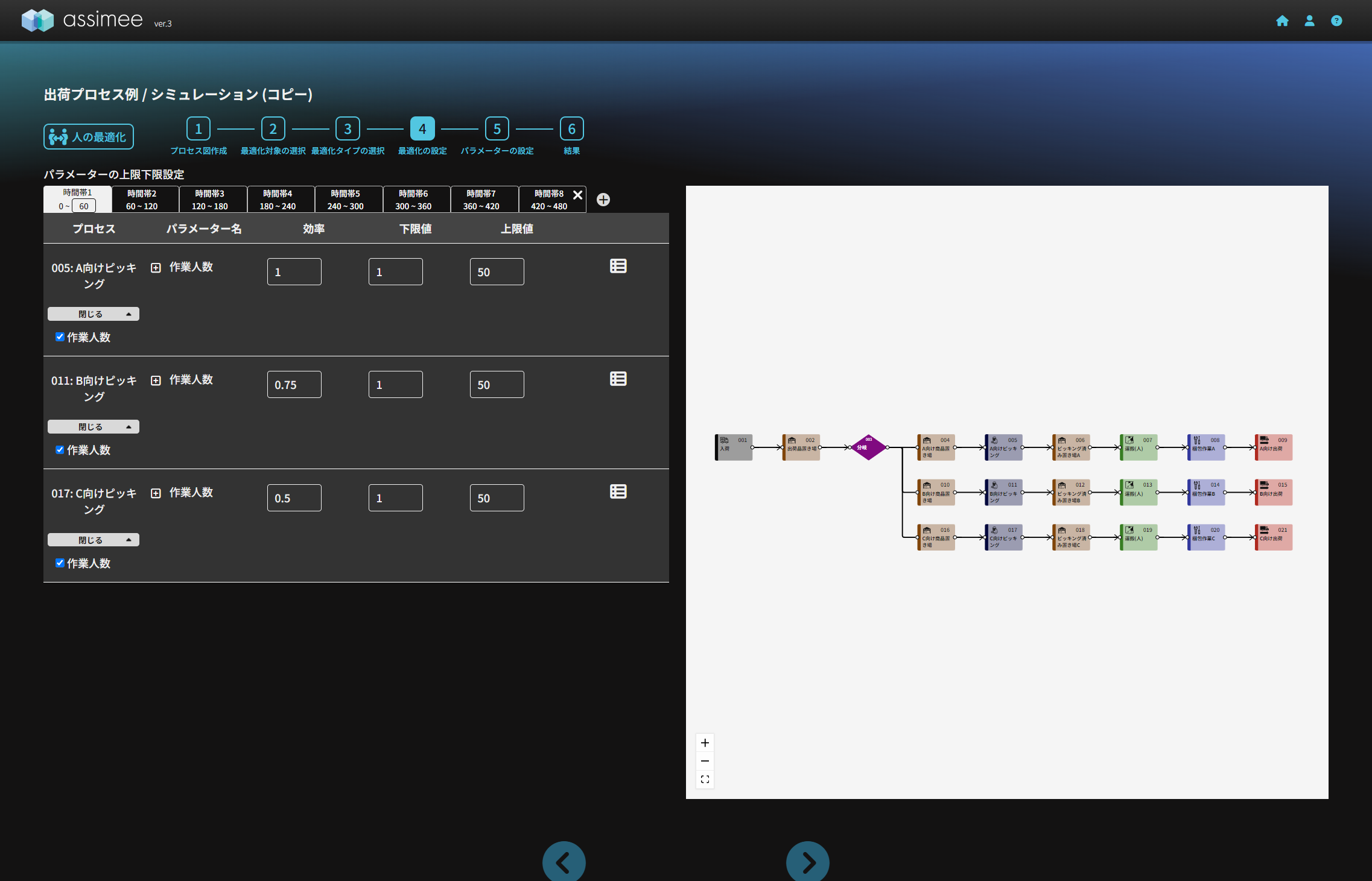
次に作業人数のパラメーターを変更します。以下のプロセスカードの詳細設置を開き作業人数を10人に変更します。
- 008梱包作業A
- 014梱包作業B
- 020梱包作業C
最期にパラメーター設定で、下図のような出荷目標を全てラインの出荷に対して適用します。こうすることで目標の達成に必要な作業員の数の変化を比較することが可能です。
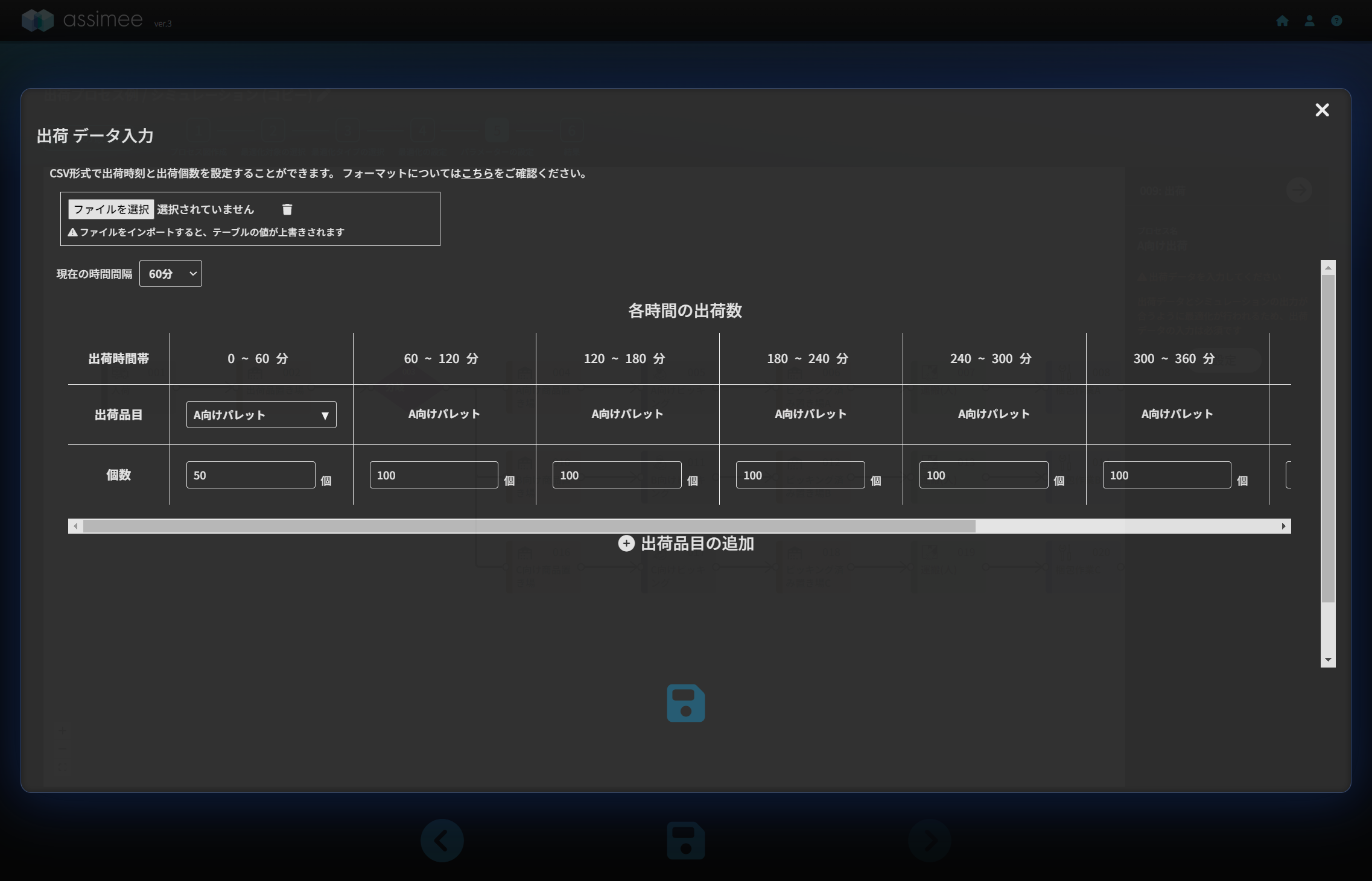
出荷目標が決まったら、最適化を始めます。シミュレーションと同じように、最適化が終了したらダッシュボードから結果を確認します。まず、生産量の推移を見ます。点線(出荷目標)と実線(シミュレーション結果)を比較すると、出荷目標が達成できていることが分かります。
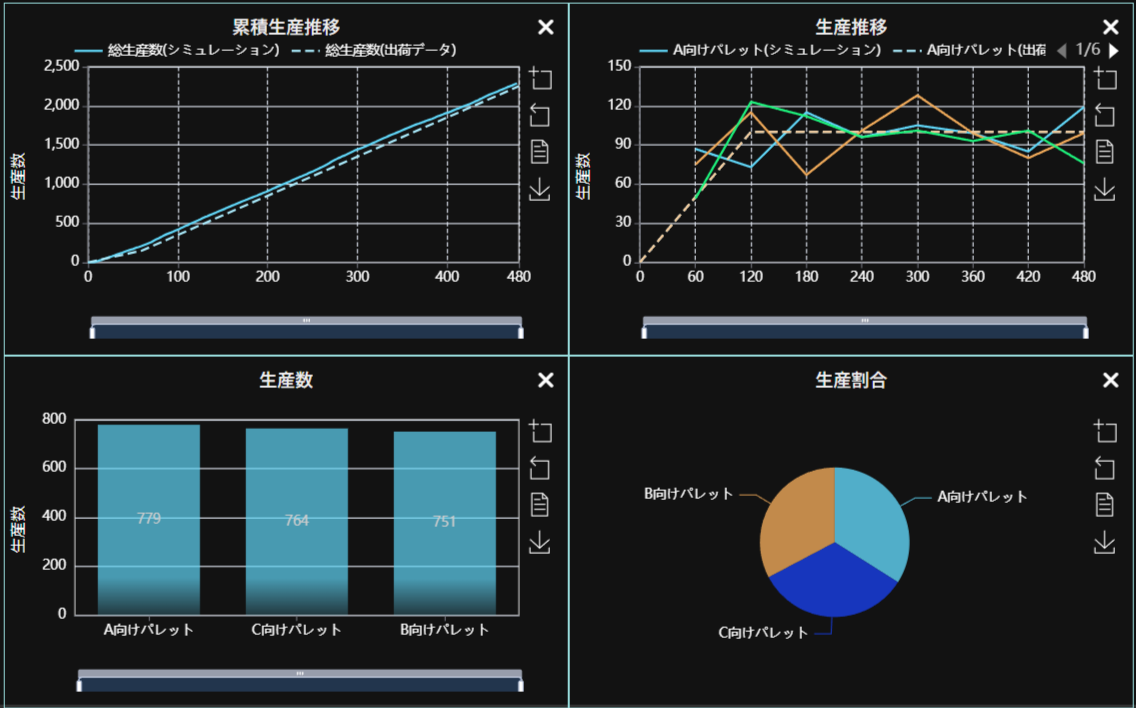
またこの時の作業人数を確認してみます。



以上のようになり、作業効率に反比例して作業員の人数が増えていることが分かりました。このようにassimeeを使うことで時間ごとに変化する出荷目標に対して最適な人員数を配置することが可能です。
まとめ
今回の記事では、assimeeを使って出荷目標に合わせた時間帯別人員配置の最適化、および作業効率の異なる人員が混在している場合の最適化について解説しました。今回想定したような、作業効率の異なる作業員が混在する人員手配業務において、assimeeを使って人員配置を決めるための最適化を行うことで、このような業務から属人化や平準化を排除するのに役立ちます。
assimeeでは、実際の製造プロセスをモデル化し、シミュレーションすることで、プロセスの見える化や潜在的な課題の洗い出しを行うことができます。製造プロセスのデジタル化や課題解決でお悩みの方は、ぜひお問い合わせください。