ー概要ー
物流業の人手不足が顕著になる中、効率的な輸送を行うためには出荷量だけでなく入荷量や入荷回数の調整も重要です。これまでは人手が十分にあり、在庫が切れないようにある程度多く入荷したり、回数を増やすことで問題を解決していました。しかし、輸送量や人手が不足し、輸送コストが上がる現状では、なるべく効率的な輸送を行いたいというニーズが高まっています。今回の記事では、生産目標に合わせてパラメーター推定を行い、生産に必要な部品の入荷量を調整する方法について解説します。
ーモデル作成ー
今回使用するモデルは下図のようなモデルとなります。このモデルの特徴は、検品を3回行い、各検品で発生した不良品を廃棄する点です。具体的には、中間製品に対して1回、完成品に対して2回の検品を実施します。そのため、担当者は出荷目標に加え、不良品の廃棄分も見込んだ入荷計画を立てる必要があります。また、初期設定では部品の入荷が1分間隔となっていますが、最終的には入荷回数を減らすことを検討します。

ーシミュレーション結果ー
今回は1日4時間で5日間、合計で20時間の稼働を想定して、1200分でシミュレーションを行ってみます。最適化にはやや時間がかかるので注意してください。下図が、シミュレーションの結果となります。ダッシュボード画面の左下のサマリーから「累積生産推移」と「生産推移」、3つの破棄と1つの出荷の「累積生産推移」を表示しています。

上段:累積生産推移、生産推移
中段:「019廃棄」の累積生産推移、「018廃棄」の累積生産推移
下段:「017廃棄」の累積生産推移、「016出荷」の累積生産推移
この結果自体には特に問題はありませんが、生産推移のグラフに表示されている出荷された正常な製品と廃棄される不良品の区別がつきにくい点に改善の余地があります。そこで、モデルを以下のように修正しましょう。加工プロセスを追加し、ここで製品の名称を「出荷製品」と変えることで、シミュレーションの分析やモデル内のパラメーターの推定が行いやすくなります。
特にパラメーター推定では、出荷品目が同名の場合、不良品が加算されることで出荷目標から大きくずれているように見えるため、製品の名前を変更することをお勧めします。さらに、廃棄品についてもどの検品で不良と判定されたかを知りたい場合は、それぞれに異なる名称を付けると分析が行いやすくなります。

上図のモデルでシミュレーションをやり直すと以下のようになります。出荷される製品が出荷製品として廃棄される不良製品と分離されたことで、上の結果よりシミュレーション結果を分析しやすくなっていることが分かります。
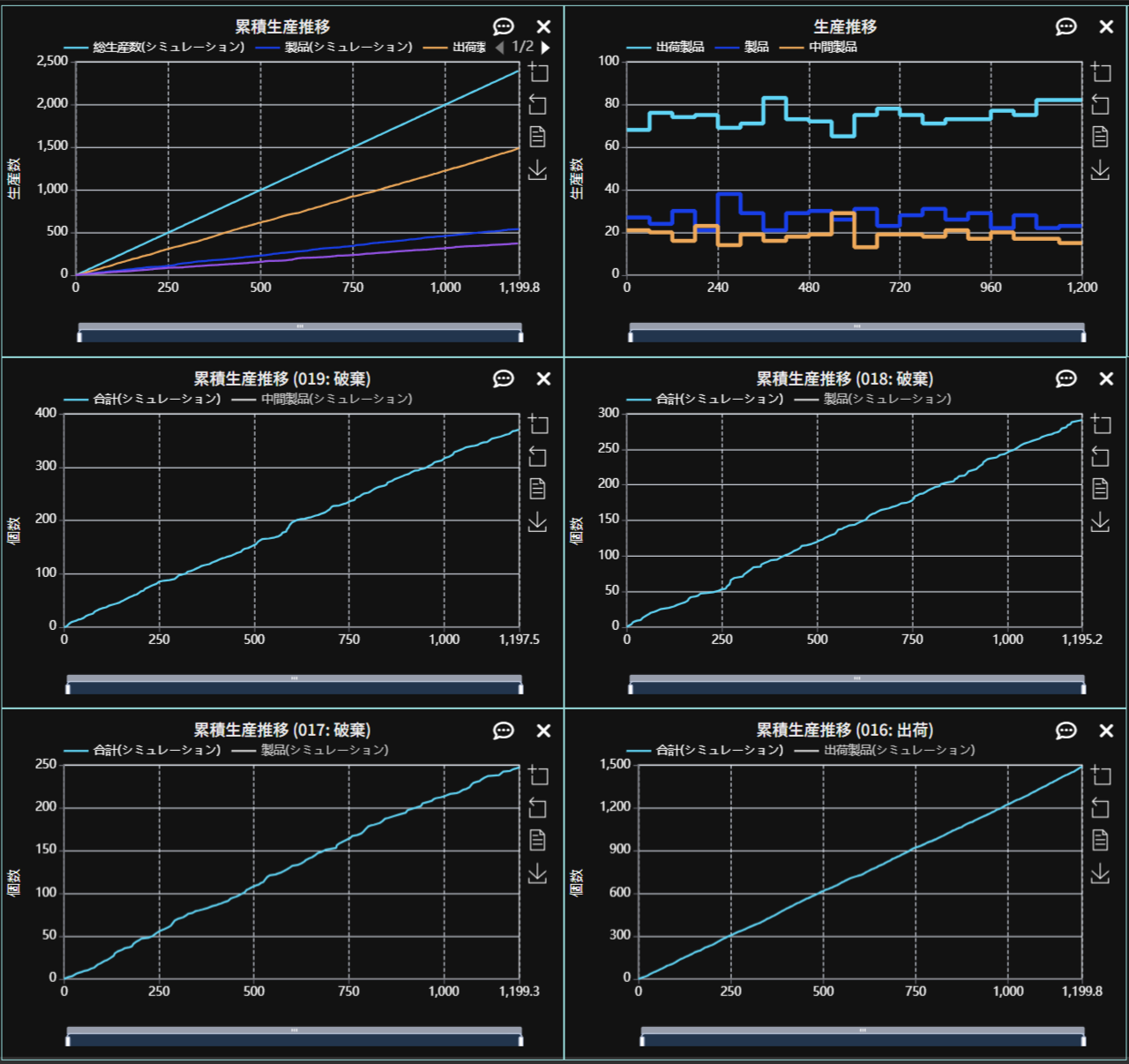
上段:累積生産推移、生産推移
中段:「019廃棄」の累積生産推移、「018廃棄」の累積生産推移
下段:「017廃棄」の累積生産推移、「016出荷」の累積生産推移
ーパラメーター推定ー
今回は以下のように「003第一次加工」と「007第二次加工」の処理時間を対象にパラメーター推定を行います。
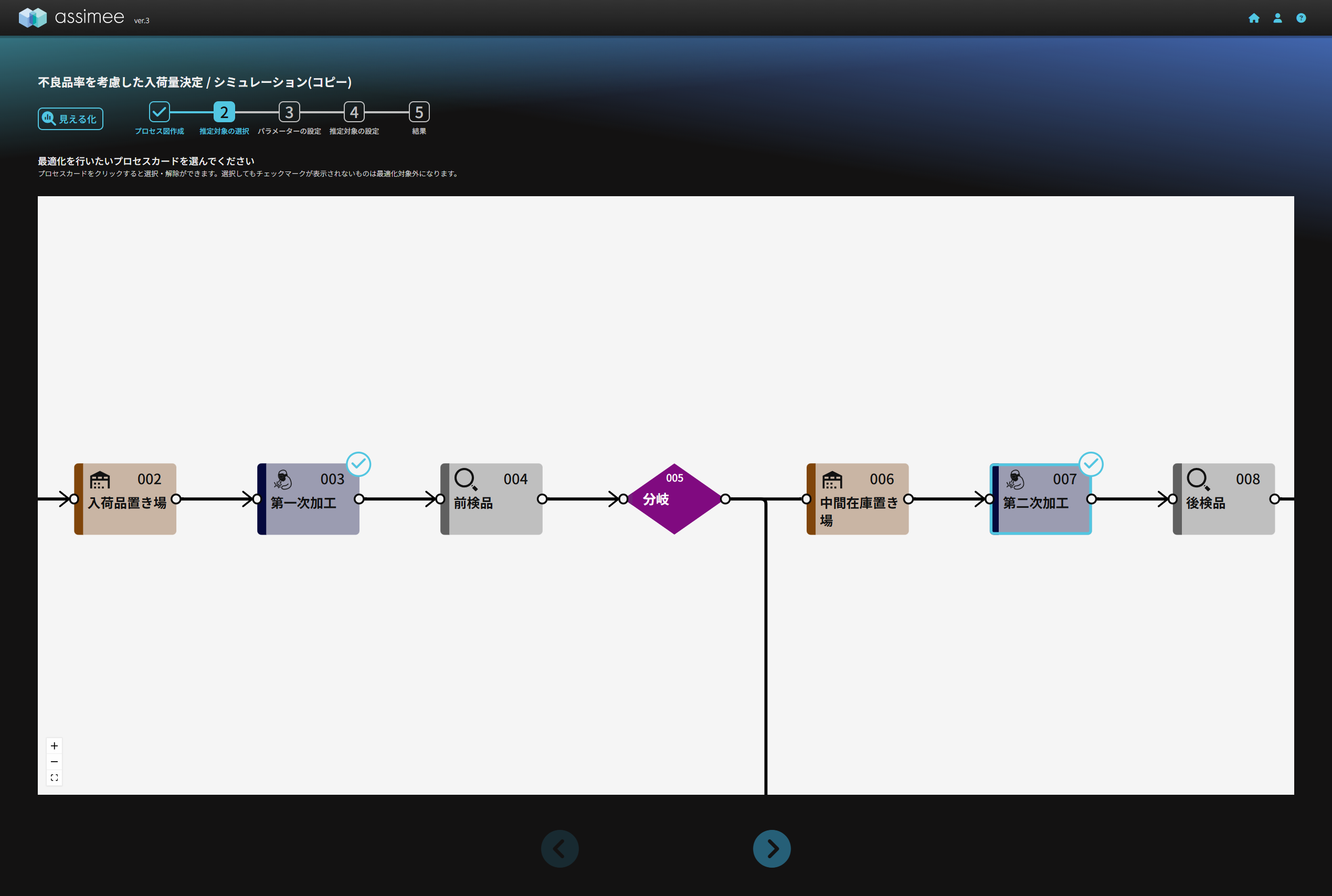
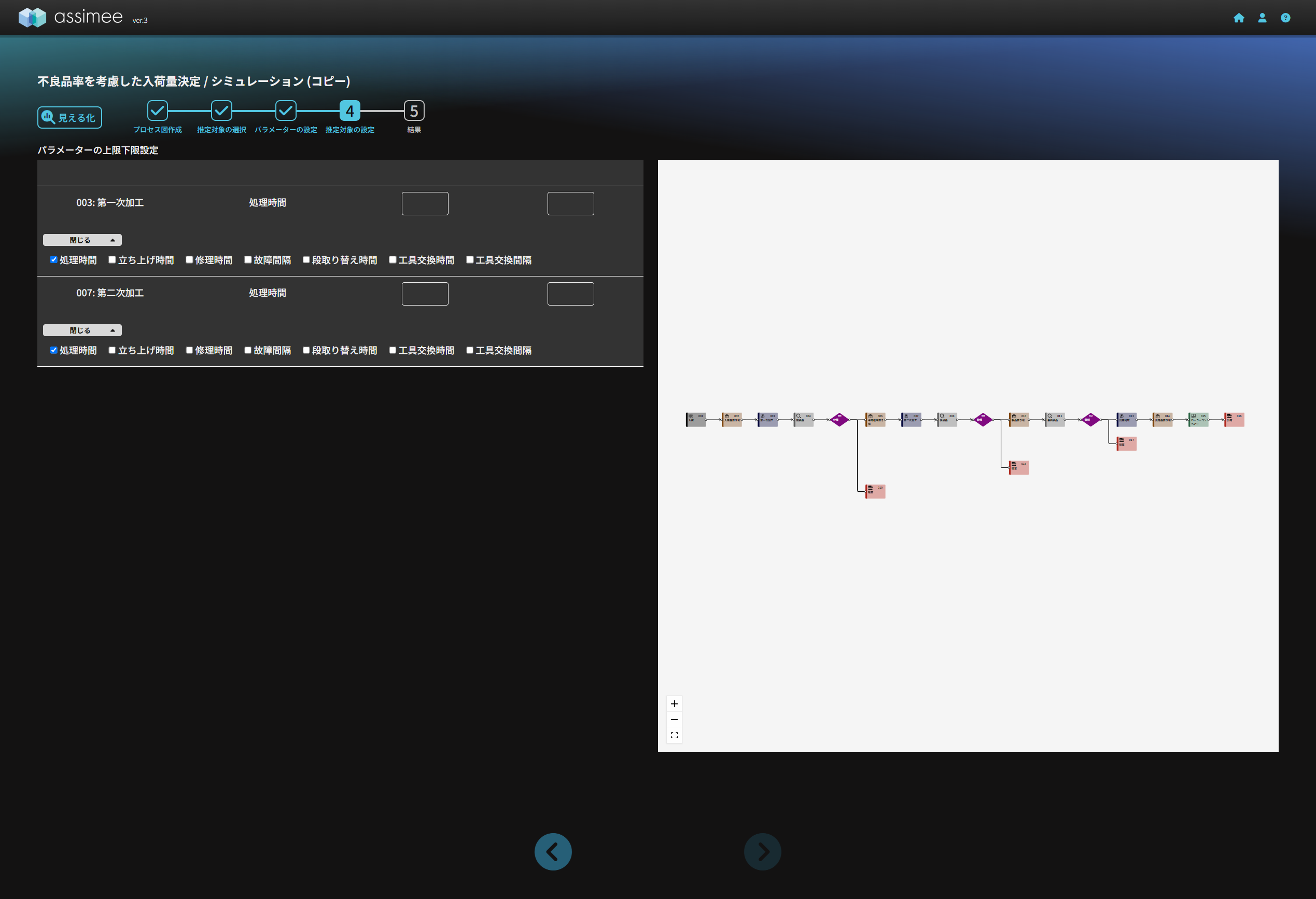
まず、出荷目標を60分あたり20個、すなわち1200分間で400個に設定します。
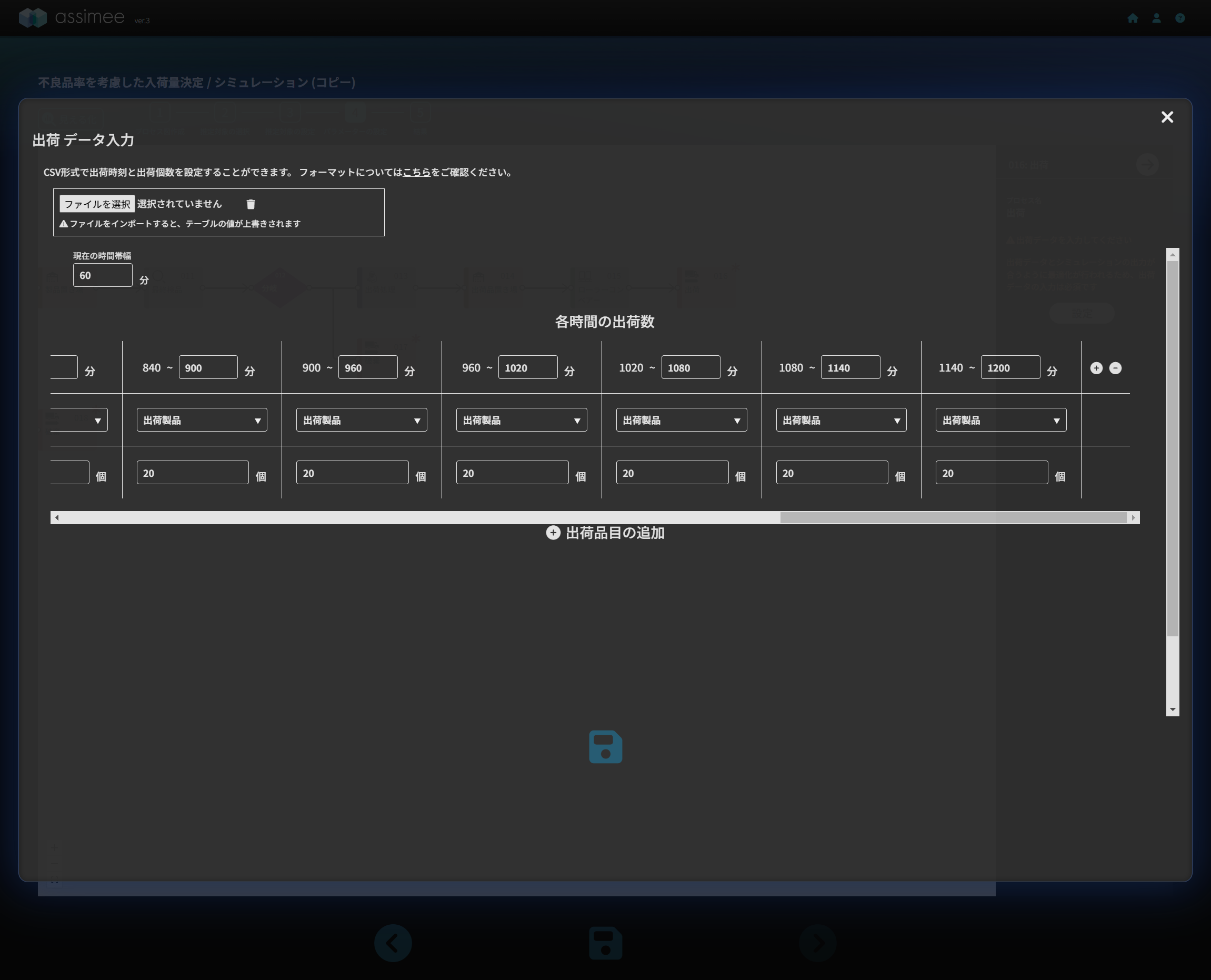
最適化結果は以下のようになりました。不良品の判定にランダムな要素が含まれるため、完全には一致しないのですが、概ね一致していることが分かります。
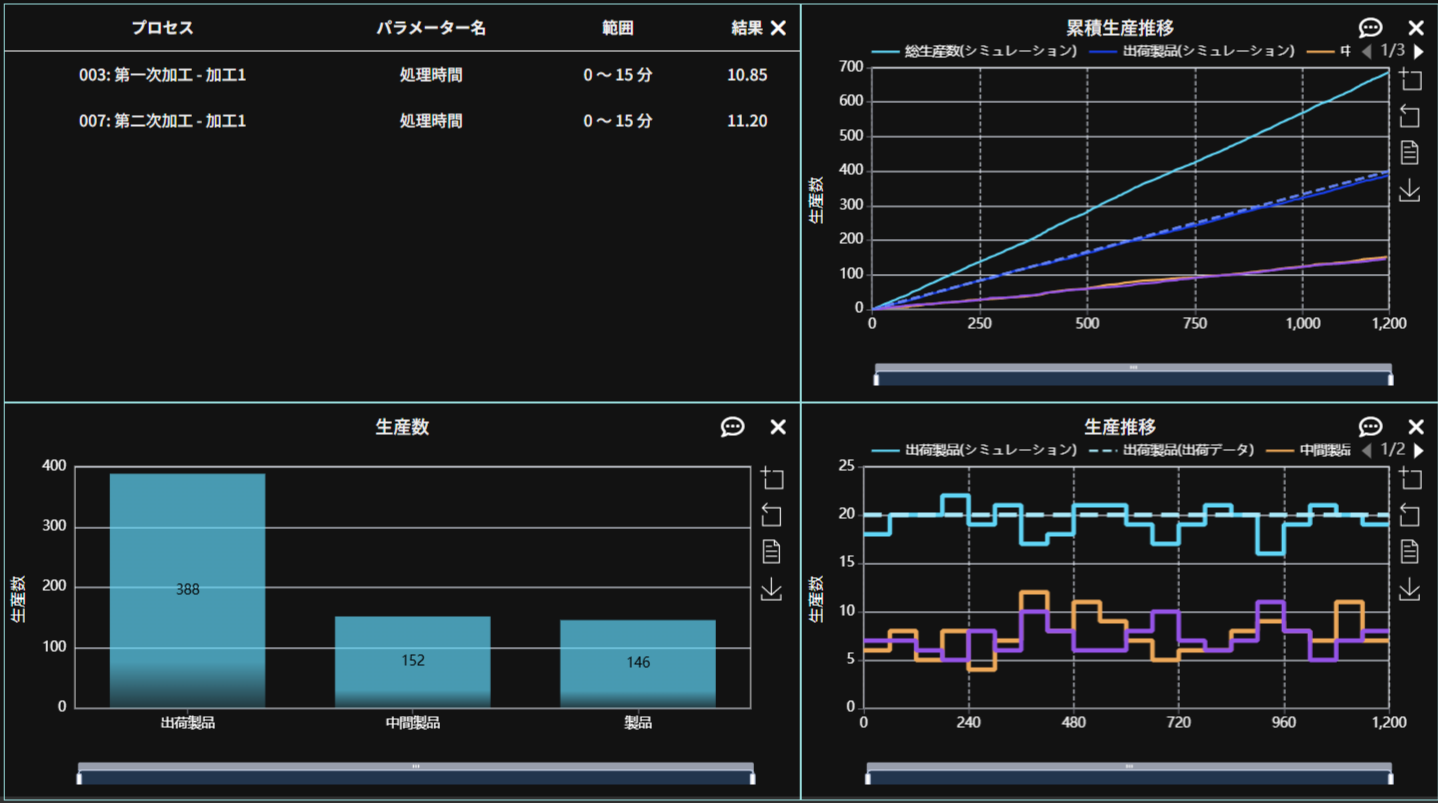
次に入荷量の設定のために、不良品の破棄を含めた4箇所すべての出荷プロセスの累積生産推移と「001入荷品置き場」の在庫数を確認してみましょう。すると以下の図のようになります。
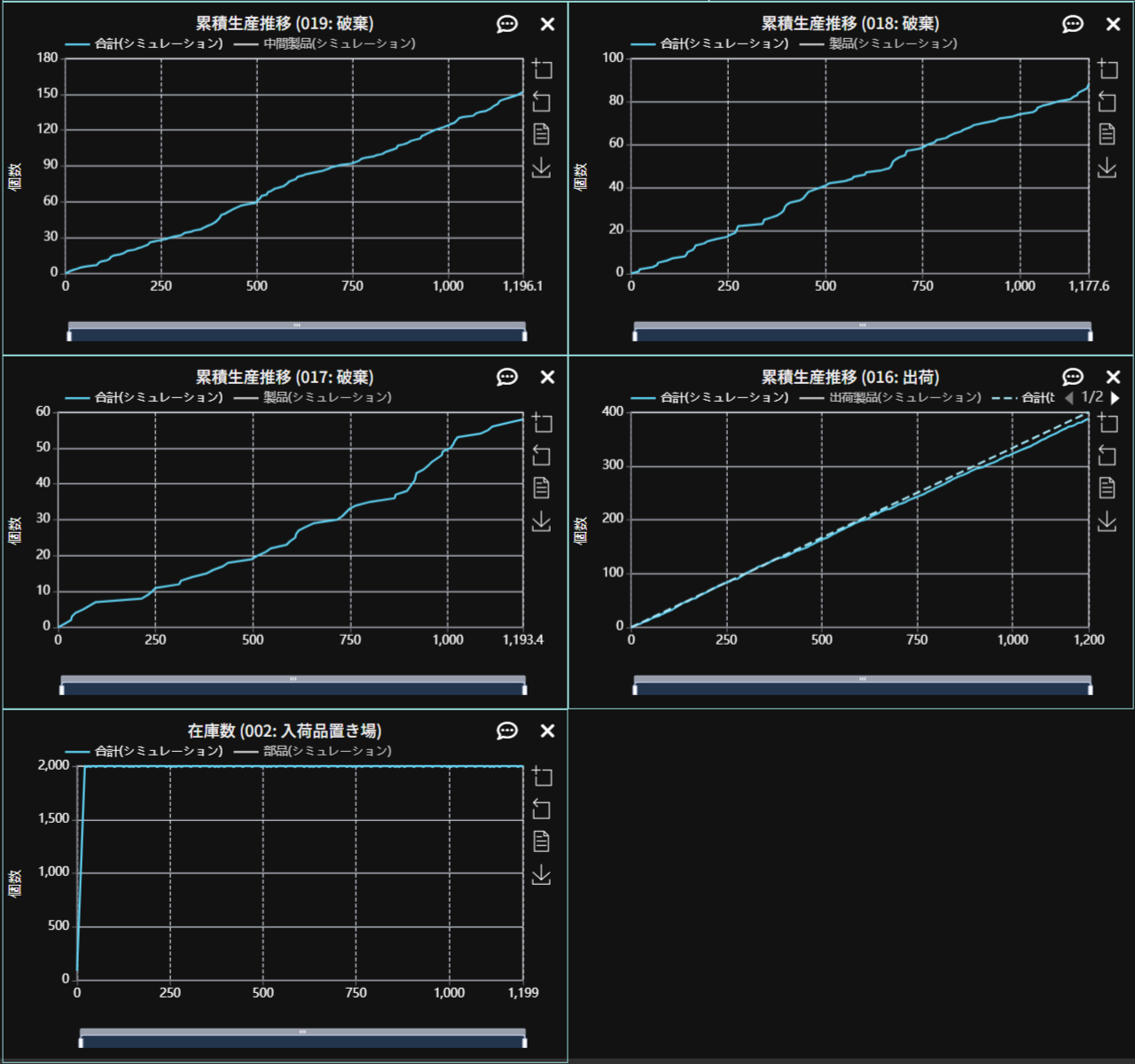
上段:「019廃棄」の累積生産推移、「018廃棄」の累積生産推移
中段:「017廃棄」の累積生産推移、「016出荷」の累積生産推移
下段:「002入荷品置き場」の在庫数
それでは、必要な部品の量はどのくらいになるでしょうか。今回のモデルでは、部品10個を「003第一次加工」で中間製品1個に加工し、中間製品1個を「007第二次加工」で製品1個に加工しています。したがって、不良品を含めたすべての出荷量に対して10倍の数の部品があれば、出荷目標である製品400個に対して部品不足が発生しないと考えられます。
今回の1200分のシミュレーションでは、不良品を含めた全ての出荷量は中間製品203個(不良品含む)、製品146個(不良品含む)、出荷製品393個で、合計で製品が742個となります。これに必要な部品は全部で7420個となります。不良品発生のランダム要素を考慮し、例えば、不良品の発生量のブレを
10%(製品約70個、部品約700個相当)と見積もると、約8200個、
20%(製品約140個、部品約1400個相当)と見積もると、約9000個、
部品があれば稼働に問題がないと推定されます。*検品やパラメーター推定にランダム要素が含まれるため、結果が一致しないことがあります。
これで全体の部品の数は決まります。今回は不良品の発生量のブレを10%と見積もって入荷量を8200個と決めます。5日稼働なので1日当たりの入荷個数は1640個になります。一方で、「002入荷品置き場」の容量は2000個あることから、今回は置き場の容量が十分であることが分かります。もし容量が不足する場合、選択肢としては主に以下の2つが考えられます。
- 「002入荷品置き場」の容量を2000個から増やして1日1回の入荷で済ませる
- 置き場容量の範囲内で、入荷を複数回分けて行う
入荷回数と入荷品の輸送手配などの手間を考えると、入荷回数が少ない1の選択の方が良い計画と考えられます。このようにして毎回変わる出荷目標に合わせて、入荷量や入荷回数の計画を決めることも可能です。
ーまとめー
今回は、生産目標に合わせてパラメーターの推定を行い、その結果に基づいて入荷方法(量や回数)を調整・決定する方法について解説しました。生産目標の達成だけでなく、必要な部品数を計算したり、入荷の計画を立てることで、assimeeを使って生産計画の業務を効率化させることができます。
assimeeでは、実際の製造プロセスをモデル化し、シミュレーションすることで、プロセスの見える化や潜在的な課題の洗い出しを行うことができます。製造プロセスのデジタル化や課題解決でお悩みの方は、ぜひお問い合わせください。