概要
製造ラインの省人化や自動化は進んでいますが、輸送や検品、仕上げ加工など要所要所に人が介在している製造ラインも数多く存在しています。そのような工程の生産量を効率的に上げるためには、機械の処理時間だけでなく、機械間の移動や検査を行う人員の配置を同時に最適化する必要があります。今回から全2回の連載を予定しており、自動化された工程と、人が行う工程が混在した生産ラインのモデルを作成し、プロセスの処理時間や人員配置に対してパラメーター推定や人の最適化を行うところまでを解説します。第1弾となる今回の記事では製造ラインのモデルを作成し、シミュレーションを行うまでを解説します。
モデル
下図が今回想定している製造ラインのモデルです。素材の加工は主に全自動の加工機械が行い、仕上げ加工や機械間の移動、検査などを人力で行うことを想定しています。


モデル図は2つに分かれており、前半部分は加工、後半部分は出荷用検査となっています。
*今回のモデルは長いので、プロセス図を横目で見ながら作成することをお勧めします
STEP1 フロー図作成
入荷プロセス:
プロセス名を「入荷」へ変更
置き場プロセス:
プロセス名を「入荷品置き場」へ変更
運搬(人)プロセス:
プロセス名を「運搬(人)」へ変更
加工プロセス:(機械加工を想定)
プロセス名を「切断」へ変更
置き場プロセス:
プロセス名を「切断後置き場」へ変更
運搬(人)プロセス:
プロセス名を「運搬(人)」へ変更
作業プロセス:(機械加工を想定)
プロセス名を「加熱」へ変更
置き場プロセス:
プロセス名を「加熱後置き場」へ変更
運搬(人)プロセス:
プロセス名を「運搬(人)」へ変更
加工プロセス:(機械加工を想定)
プロセス名を「ハンマー」へ変更
置き場プロセス:
プロセス名を「加工後置き場」へ変更
運搬(人)プロセス:
プロセス名を「運搬(人)」へ変更
作業プロセス:(機械加工を想定)
プロセス名を「熱処理」へ変更
置き場プロセス:
プロセス名を「熱処理後置き場」へ変更
運搬(人)プロセス:
プロセス名を「運搬(人)」へ変更
加工プロセス:(人の加工を想定)
プロセス名を「仕上げ」へ変更
置き場プロセス:
プロセス名を「製品置き場」へ変更
運搬(人)プロセス:
プロセス名を「運搬(人)」へ変更
検品プロセス:
プロセス名を「探傷検査」へ変更
分岐プロセス:
プロセス名を「分岐」へ変更
最後に「不合格品置き場」と接続
置き場プロセス:
プロセス名を「置き場」へ変更
検品プロセス:
プロセス名を「超音波検査」へ変更
分岐プロセス:
プロセス名を「分岐」へ変更
最後に「不合格品置き場」と接続
置き場プロセス:
プロセス名を「置き場」へ変更
検品プロセス:
プロセス名を「電気伝導度検査」へ変更
分岐プロセス:
プロセス名を「分岐」へ変更
最後に「不合格品置き場」と接続
置き場プロセス:
プロセス名を「置き場」へ変更
検品プロセス:
プロセス名を「硬さ検査」へ変更
分岐プロセス:
プロセス名を「分岐」へ変更
最後に「不合格品置き場」と接続
置き場プロセス:
プロセス名を「置き場」へ変更
検品プロセス:
プロセス名を「材料測定」へ変更
分岐プロセス:
プロセス名を「分岐」へ変更
最後に「不合格品置き場」と接続
置き場プロセス:
プロセス名を「置き場」へ変更
検品プロセス:
プロセス名を「寸法検査」へ変更
分岐プロセス:
プロセス名を「分岐」へ変更
製品出荷と不良品破棄のプロセスを分岐
製品出荷側
置き場プロセス:
プロセス名を「出荷品置き場」へ変更
加工プロセス:
プロセス名を「梱包」へ変更
出荷プロセス:
プロセス名を「出荷」へ変更
不良品破棄側
置き場プロセス:
プロセス名を「不合格品置き場」へ変更
加工プロセス:
プロセス名を「破棄」へ変更
出荷プロセス:
プロセス名を「スクラップ出荷」へ変更
STEP2 パラメーターの設定
001入荷:
入荷が一定周期の場合を選択、入荷品目名を「素材」、個数を「1個」、時間間隔を「1分」に設定
002入荷品置き場:
置き場容量を「1000個」と設定
003運搬(人):
最大運搬量を「5個」、人数を「5人」、搬送時間(片道)を「5分」と設定
004切断:
1回あたりの処理時間を「10分」、
対象品目名を「素材」、個数を「1個」、
出力品目名を「切断後素材」、個数を「1個」と設定
005切断後置き場:
置き場容量を「1000個」と設定
006運搬(人):
最大運搬量を「10個」、人数を「5人」、搬送時間(片道)を「5分」と設定
007加熱:
1回あたりの処理時間を「10分」、
対象品目名を「切断後素材」、個数を「1個」と設定
008加熱後置き場:
置き場容量を「1000個」と設定
009運搬(人):
最大運搬量を「10個」、人数を「5人」、搬送時間(片道)を「5分」と設定
010加熱:
1回あたりの処理時間を「10分」、
対象品目名を「切断後素材」、個数を「1個」、
出力品目名を「鍛造後部品」、個数を「1個」と設定
011加熱後置き場:
置き場容量を「1000個」と設定
012運搬(人):
最大運搬量を「10個」、人数を「5人」、搬送時間(片道)を「5分」と設定
013熱処理:
1回あたりの処理時間を「10分」、
対象品目名を「鍛造後部品」、個数を「1個」と設定
014熱処理後置き場:
置き場容量を「1000個」と設定
015運搬(人):
最大運搬量を「10個」、人数を「5人」、搬送時間(片道)を「5分」と設定
016仕上げ:
1回あたりの処理時間を「15分」、
対象品目名を「鍛造後部品」、個数を「1個」、
出力品目名を「製品」、個数を「1個」と設定
017製品置き場:
置き場容量を「1000個」と設定
018運搬(人):
最大運搬量を「10個」、人数を「5人」、搬送時間(片道)を「5分」と設定
019探傷検査:
1回あたりの処理時間を「10分」、不良品率を「1%」と設定
020分岐:
1回あたりの処理時間を「1分」と設定
「正常:製品」を「021置き場」へ
「不良:製品」を「039不合格品置き場」へ
021置き場:
置き場容量を「1000個」と設定
022超音波検査:
1回あたりの処理時間を「10分」、不良品率を「1%」と設定
023分岐:
1回あたりの処理時間を「1分」と設定
「正常:製品」を「024置き場」へ
「不良:製品」を「039不合格品置き場」へ
024置き場:
置き場容量を「1000個」と設定
025電気伝導度検査:
1回あたりの処理時間を「10分」、不良品率を「1%」と設定
026分岐:
1回あたりの処理時間を「1分」と設定
「正常:製品」を「027置き場」へ
「不良:製品」を「039不合格品置き場」へ
027置き場:
置き場容量を「1000個」と設定
028硬さ検査:
1回あたりの処理時間を「15分」、不良品率を「1%」と設定
029分岐:
1回あたりの処理時間を「1分」と設定
「正常:製品」を「030置き場」へ
「不良:製品」を「039不合格品置き場」へ
030置き場:
置き場容量を「1000個」と設定
031材料測定:
1回あたりの処理時間を「15分」、不良品率を「1%」と設定
032分岐:
1回あたりの処理時間を「1分」と設定
「正常:製品」を「033置き場」へ
「不良:製品」を「039不合格品置き場」へ
033置き場:
置き場容量を「1000個」と設定
034寸法検査:
1回あたりの処理時間を「15分」、不良品率を「1%」と設定
035分岐:
1回あたりの処理時間を「1分」と設定
「正常:製品」を「036置き場」へ
「不良:製品」を「039不合格品置き場」へ
製品出荷側
036出荷品置き場:
置き場容量を「1000個」と設定
037梱包:
1回あたりの処理時間を「10分」、
対象品目名を「製品」、個数を「1個」、
出力品目名を「梱包済製品」、個数を「1個」と設定
038出荷:
設定項目なし
不良品破棄側
039不合格品置き場:
置き場容量を「1000個」と設定
040破棄:
1回あたりの処理時間を「10分」、
対象品目名を「製品」、個数を「1個」、
出力品目名を「スクラップ」、個数を「1個」と設定
041スクラップ出荷:
設定項目なし
STEP3 結果シミュレーション
モデルの作成が終了したら、次へボタン(右矢印)を押します。シミュレーションの時間設定ポップアップが立ち上がります。今回はシミュレーション時間を600分に設定して、シミュレーションを行います。シミュレーションが終了するとダッシュボードに自動的に移行します。
*今回のモデルでは不良品判定に乱数が含まれているため、完全に結果(特に生産推移の結果)が一致しません。
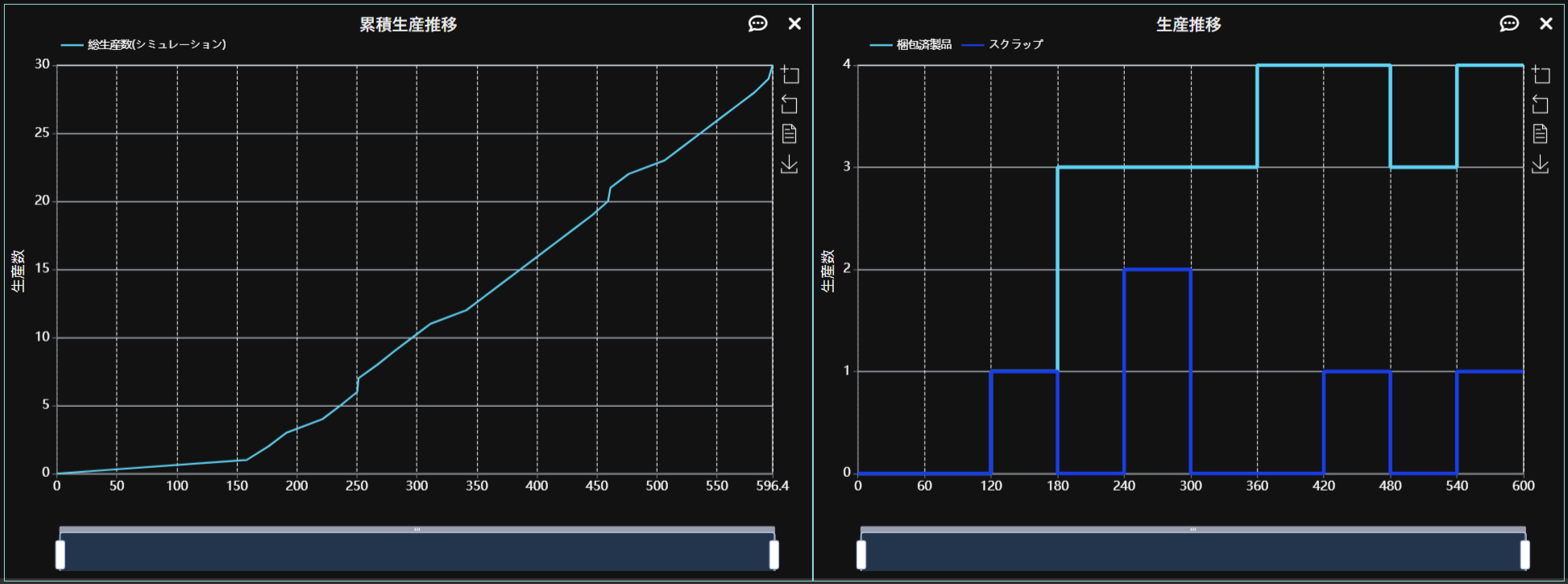
左:累積生産量推移、右:生産推移
ボトルネックの分析
ここからはシミュレーション結果を使って、生産ラインにボトルネックが生じていないか確認します。
置き場の在庫
まず製品が完成するまでの各置き場の在庫を確認してみます。
下図は上流から「002入荷品置き場」、「005切断後置き場」、「008加熱後置き場」、「011加工後置き場」、「014熱処理後置き場」、「017製品置き場」の在庫となります。
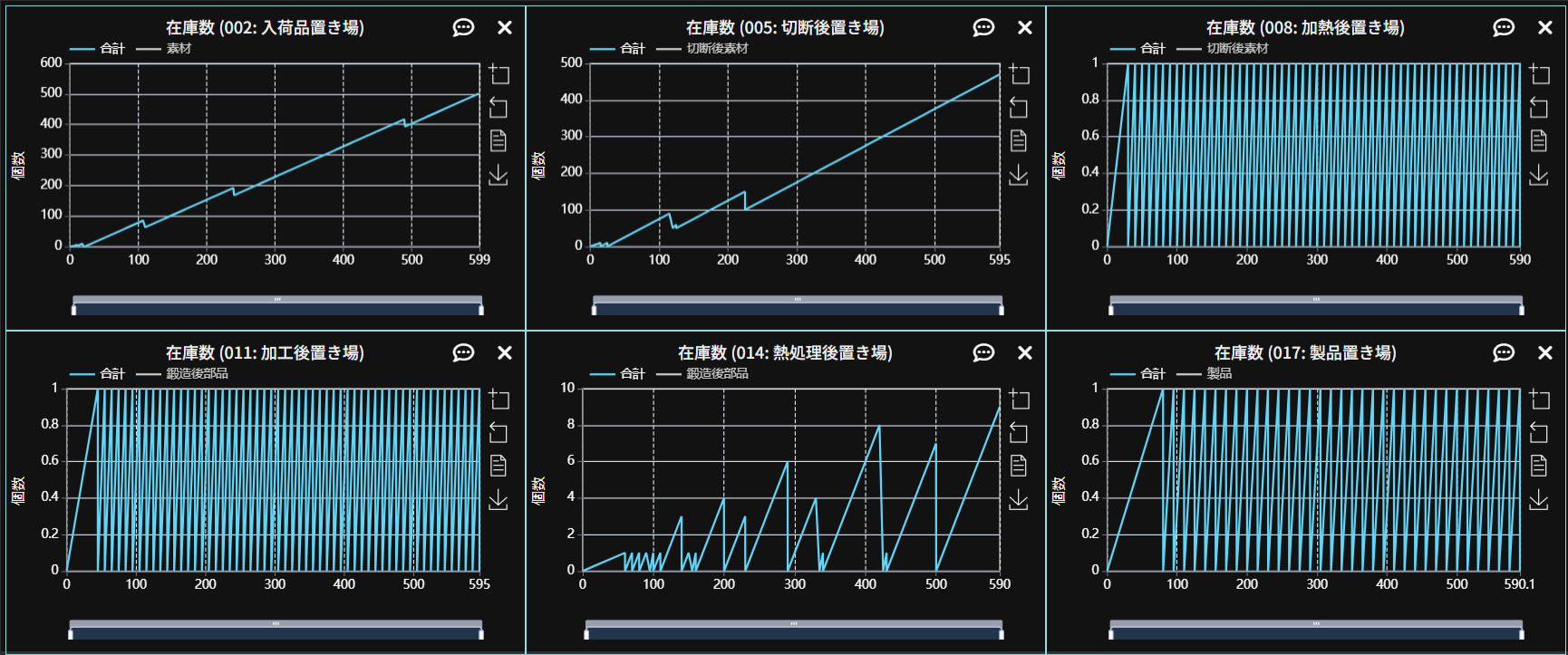
上段左:002入荷品置き場、上段中央:005切断後置き場、上段右:008加熱後置き場
下段左:011加工後置き場、下段中央:014熱処理後置き場、下段右:017製品置き場
図を見ると「002入荷品置き場」、「005切断後置き場」で在庫が右肩上がりで増加していることが分かります。これは、下流側にある、「004切断」と「007加熱」の処理能力が不足しているため、処理できない素材が在庫として溜まっていることを示しています。「008加熱後置き場」以降は「014熱処理後置き場」で在庫が増える傾向にありますが、概ね処理能力は足りていることから、「004切断」と「007加熱」がこの生産ラインのボトルネックになっていることが分かります。
稼働率
確認のため「004切断」と「007加熱」の平均稼働率を見ることで稼働状況を確認してみます。
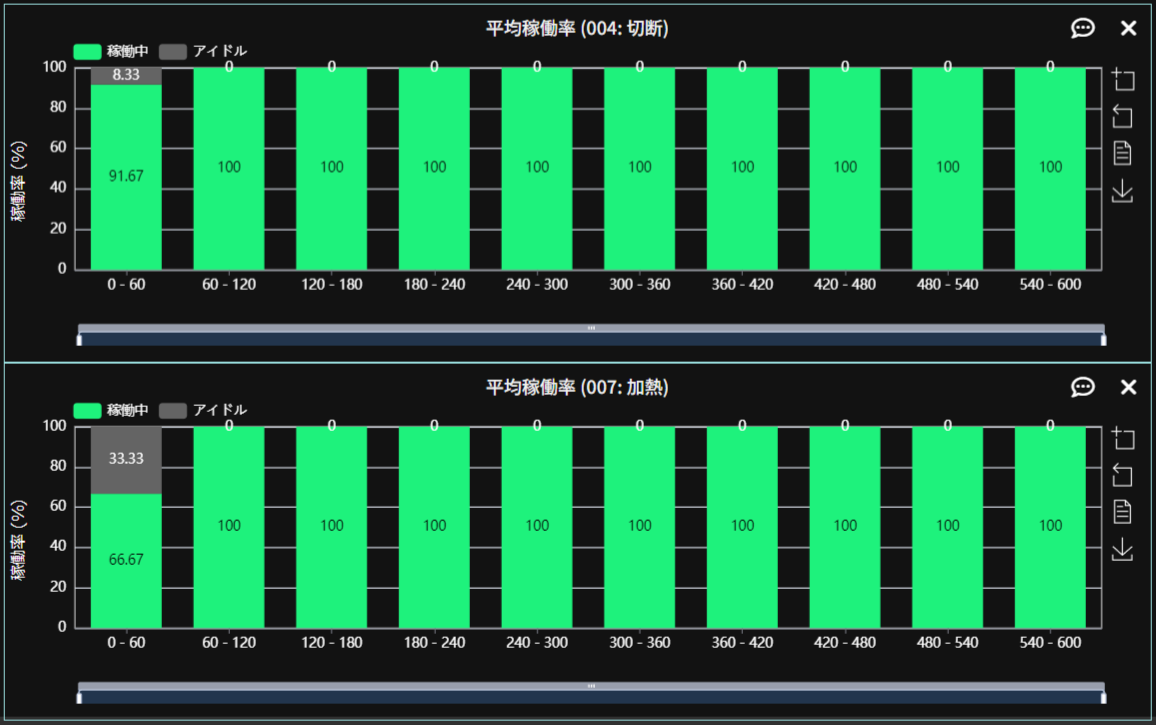
上:「004切断」の平均稼働率、下:「007加熱」の平均稼働率
ほぼ100%で稼働しており、処理能力が限界になっていることが確認できました。
これらの結果から加工や作業の人員や機械の処理能力を増やすことで生産量を増やす見込みがあることが分かります。
次に下流側の6カ所の検査「019探傷検査」、「022超音波検査」、「025電気伝導度検査」、「028硬さ検査」、「031材料測定」、「034寸法検査」の稼働率も確認してみます。
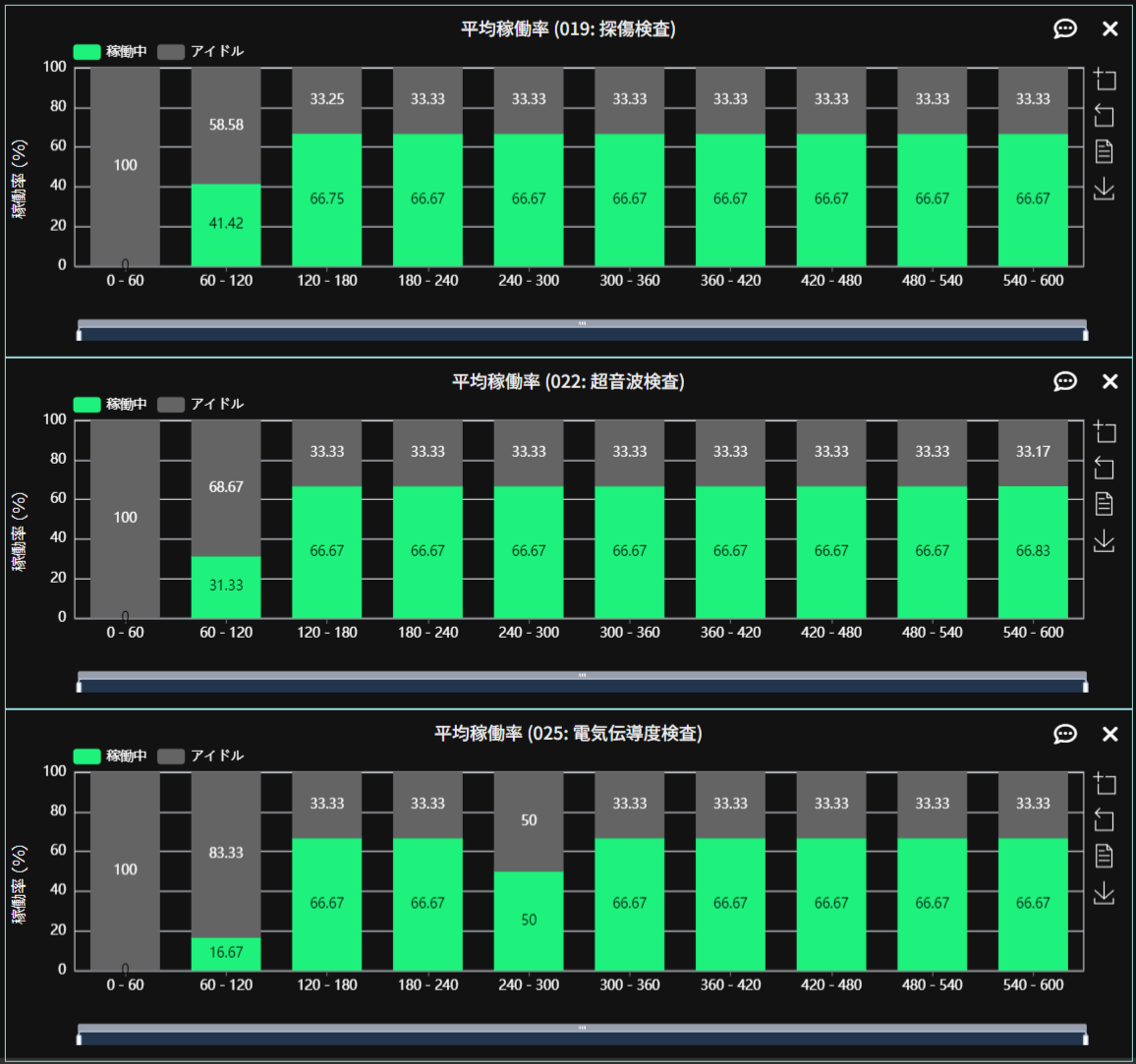
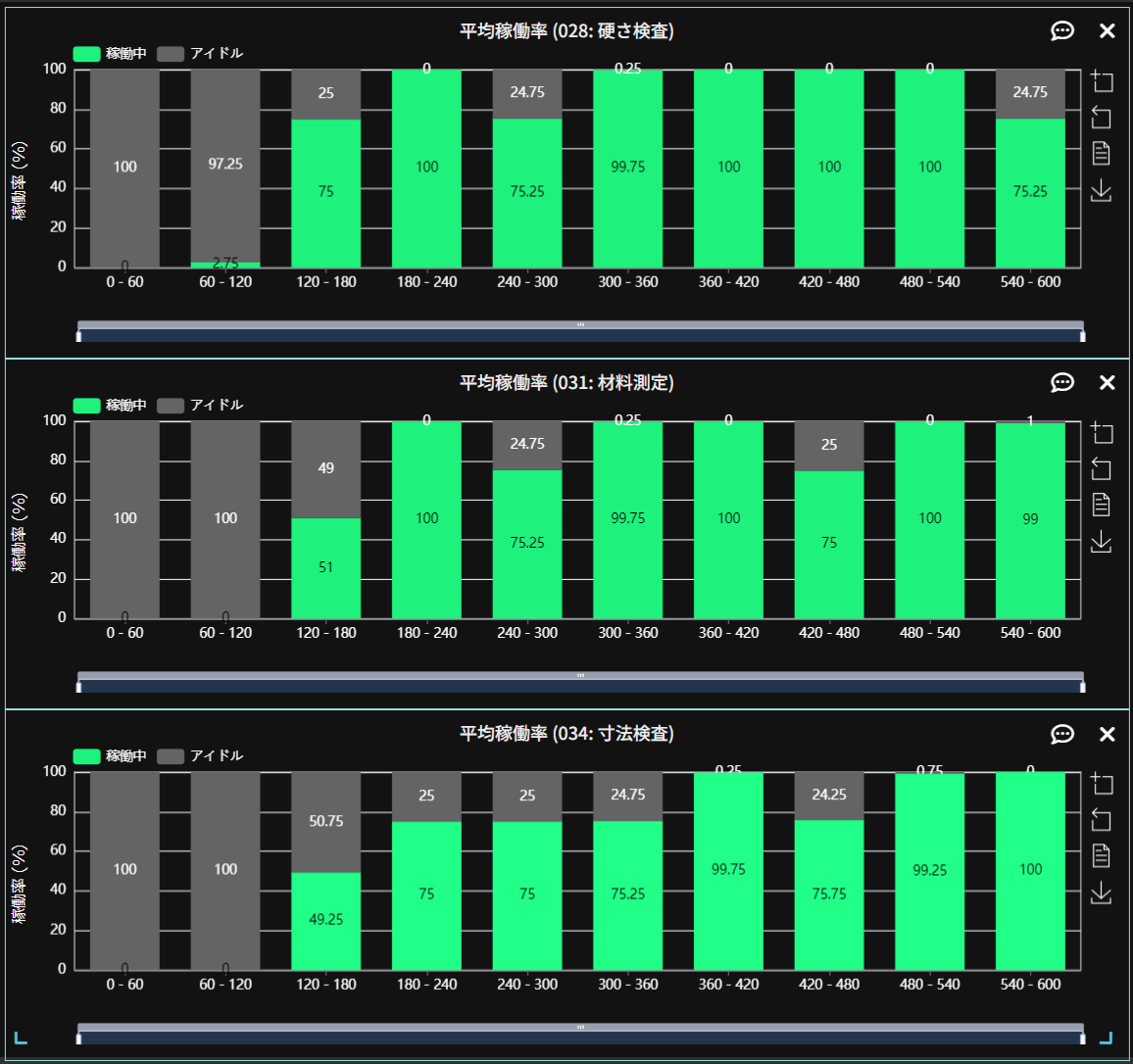
左上段:「022超音波検査」、左中段:「019探傷検査」、左下段:「025電気伝導度検査」
右上段:「028硬さ検査」、右中段:「031材料測定」、右下段:「034寸法検査」
6つの検査の内比較的検査時間の短い前半3つの検査には処理能力に余裕がありますが、後半3つの検査は100%で動いており、今の生産能力でも処理能力が足りないことが分かります。加えて、仮に生産能力が上昇し、検査すべき製品が増えると、6つの検査全てにおいて処理能力が足りなくなることが想定されます。
まとめ
今回は、自動化された工程と人が行う工程が混じった製造ラインの最適化と題して、製造ラインのモデルの作成までを解説しました。後編の記事では今回作成した製造ラインのモデルに対して、ボトルネックを探索し、様々な条件を想定した上でボトルネックを解消し最適な生産条件を決める方法について解説します。
assimeeでは、実際の製造プロセスをモデル化し、シミュレーションすることで、プロセスの見える化や潜在的な課題の洗い出しを行うことができます。製造プロセスのデジタル化や課題解決でお悩みの方は、ぜひお問い合わせください。