概要
前回の記事では、人員の生産性を考慮して人員配置を決定する方法について解説しました。今回は生産性を考慮して作業レイアウトを決める方法を解説します。作業レイアウトの簡単な変更をすることで、生産性が向上する場合があるものの、レイアウトを実際の生産ラインを使って検証することは難しいので、レイアウト決めは現場担当者の経験や勘に頼っていました。また、どんなレイアウトが最適かを決めることも困難でした。assimeeのシミュレーションを使うことで、最適なレイアウト配置を根拠を持って決めることが、誰にでも可能になります。
モデル
今回は前回の記事で使った以下のモデルを基本に配置の変更の結果を確認します。

図:モデル
このラインは入荷した部品をプレス作業と曲げ作業で加工して製品にしています。それぞれの作業プロセスは1人の担当となっています。また、ラインが2本設置してあり、モデル全体では2つのプレス作業と2つの曲げ作業を担当する作業員が1人ずつ合計で4人いる設定です。2つのラインは同じ製品を生産していますが、ラインの間には部品のやり取りはありません。
前回の結果を元に、ボトルネックが発生しているかを確認してみます。たとえば組み合わせの1つ目は以下のような組み合わせです。
ラインA担当と時間 (プレス作業-曲げ作業) | ラインB担当と時間 (プレス作業-曲げ作業) | 300分での総生産数 | |
組合わせ1 | A-B(5-20) | C-D(15-10) | 33 |
この設定で動かした際にプレス作業と曲げ作業の間で発生する中間在庫が置かれる「006置き場」と「014置き場」のアイテム数を見てみましょう。
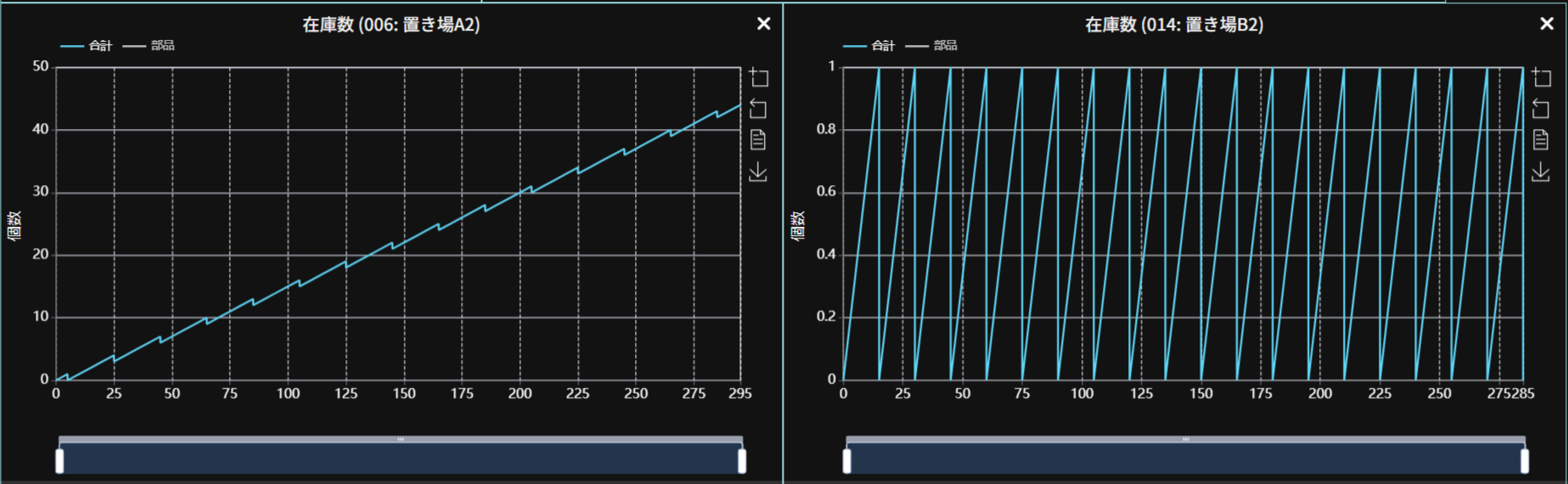
「014置き場」の在庫はほぼないのですが、「006置き場」で中間在庫が発生、かつ増え続けていることが分かります。これはプレス作業と曲げ作業の能力にミスマッチがあるからです。次に「007曲げ作業B」の稼働率と「015曲げ作業D」の稼働率のステータスを確認します。
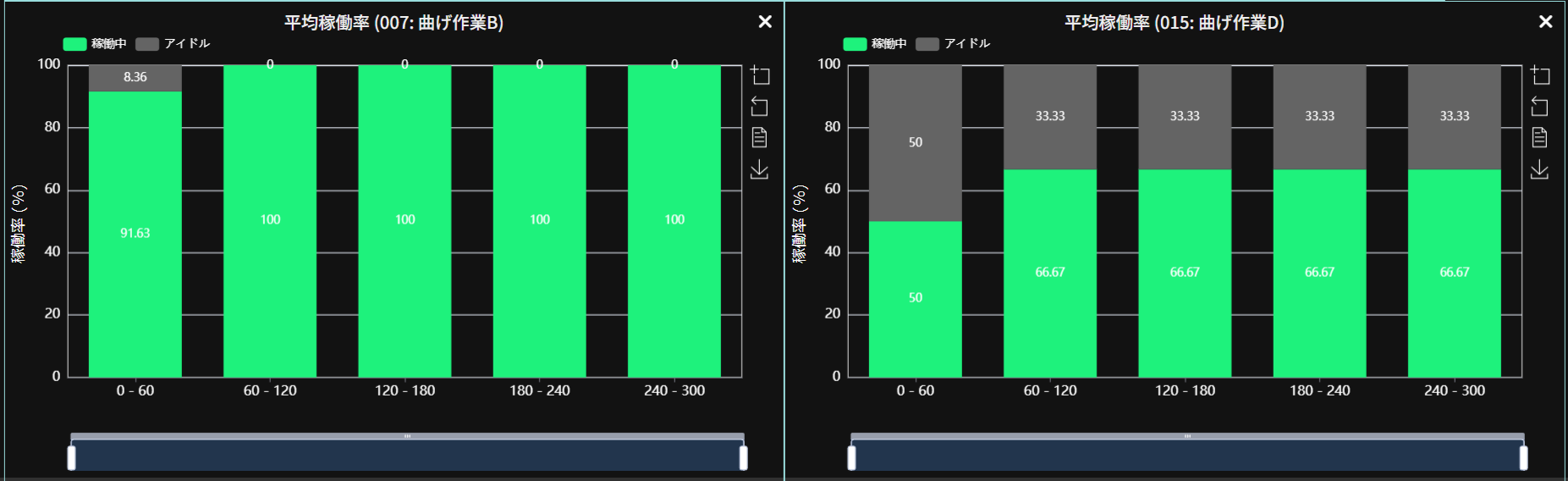
「007曲げ作業」の稼働率を見るとほぼ全力操業になっていますが、「015曲げ作業」の稼働率には部品待ち、つまり、中間在庫がなくて動かしたくても動かない時間があることが分かります。一方で「006置き場」には使われていない中間在庫があるため、在庫を共通化するようなレイアウトにすれば、「015曲げ作業」の稼働率が上げることが可能に見えます。そこで、モデルのレイアウトを変更して実際にどれだけの効果があるか確認することします。
モデルの変更
下図のように中間在庫を共有できるように「202置き場」と「302置き場」を統合した置き場を作ったうえで、そこから曲げ作業に部品を供給するようにモデルを変更し、作り直します。このモデルでもAとBがあるラインごとの違いを分かりやすくするために、それぞれのラインの製品名に対して「製品A」、「製品B」といった違いを付けます。

STEP1 プロセス図を作成する
以下のようにプロセスカードを設置してモデルを作成していきます。
入荷プロセス:
特に変更なし
置き場プロセス:
プロセス名を「入荷品置き場」へ変更
分岐プロセス:
分岐先として2つのプロセスを設置:
分岐先として2つの置き場プロセスを用意します。
置き場プロセス:
プロセス名を「置き場A1」へ変更
以下はラインAの項へ
置き場プロセス:
プロセス名を「置き場B1」へ変更
以下はラインBの項へ
ラインA
置き場プロセス(再掲):
プロセス名を「置き場A1」へ変更
作業プロセス:
プロセス名を「プレス作業A」へ変更
置き場プロセス:
プロセス名を「中間在庫置き場」へ変更
*この置き場を共通の中間在庫置き場とします。
分岐プロセス:
分岐先として2つのプロセスを設置:
分岐先として2つの置き場プロセスを用意します。
作業プロセス:
プロセス名を「曲げ作業B」へ変更
後に組立プロセスを配置
作業プロセス:
プロセス名を「曲げ作業D」へ変更
以下はラインBの項へ
組立プロセス:
プロセス名を「梱包A」へ変更
置き場プロセス:
プロセス名を「出荷品置き場」へ変更
ラインB
置き場プロセス(再掲):
プロセス名を「置き場B1」へ変更
作業プロセス:
プロセス名を「プレス作業C」へ変更
「中間在庫置き場」へ合流
「分岐」で再分岐後
作業プロセス(再掲):
プロセス名を「曲げ作業D」へ変更
組立プロセス:
プロセス名を「梱包B」へ変更
「出荷品置き場」へ合流
合流後
ローラーコンベアー:
特に変更なし
出荷プロセス:
特に変更なし
STEP2 パラメーターを設定する
以下のようにモデルにパラメーターを設定します。
001入荷:
入荷品目を「部品」、個数を「20個」、時間間隔を「1分」と設定
002入荷品置き場:
容量を「1000個」と設定
003分岐:
1回あたりの処理時間を「0分」と設定
*処理時間を「0」とすることでパススルーとなります。
分岐条件:
ランダム設定(変更せず)
ラインA
004置き場A1:
容量を「1000個」と設定
005プレス作業A:
1回あたりの処理時間を「5分」、
対象品目を「部品」、個数を「1個」と設定
006中間在庫置き場:
容量を「1000個」と設定
*この置き場を共通の中間在庫置き場とします。
007分岐:
1回あたりの処理時間を「0分」と設定
分岐条件:
ランダム設定(変更せず)
008曲げ作業B:
1回あたりの処理時間を「20分」、
対象品目を「部品」、個数を「1個」と設定
009梱包:
1回あたりの処理時間を「1分」と設定、
対象品目を「部品」、個数を「1個」、
出力品目を「製品B」、個数を「1個」と設定
010出荷品置き場:
容量を「1000個」と設定
ラインB
015置き場B1:
容量を「1000個」と設定
016プレス作業C:
1回あたりの処理時間を「15分」、
対象品目を「部品」、個数を「1個」と設定
「006中間在庫置き場」へ合流
「007分岐」で再分岐後
013曲げ作業D:
1回あたりの処理時間を「10分」、
対象品目を「部品」、個数を「1個」と設定
014梱包:
1回あたりの処理時間を「1分」と設定
対象品目を「部品」、個数を「1個」、
出力品目の名称を「製品A」、個数を「1個」と設定
「010出荷品置き場」へ合流
合流後
011ローラーコンベアー:
搬送時間を「1分」、最大積荷個数を「10個」と設定
012出荷:
特に変更なし
シミュレーション結果の分析をする
シミュレーションの結果を確認する
モデルを作成したら保存を行い、シミュレーション時間を300分に設定してシミュレーションを行います。上記のようにパラメーターが設定されていれば、以下のような図が表示されます。*今回のモデルでは分岐に乱数が含まれているため、完全に一致しない可能性があります。
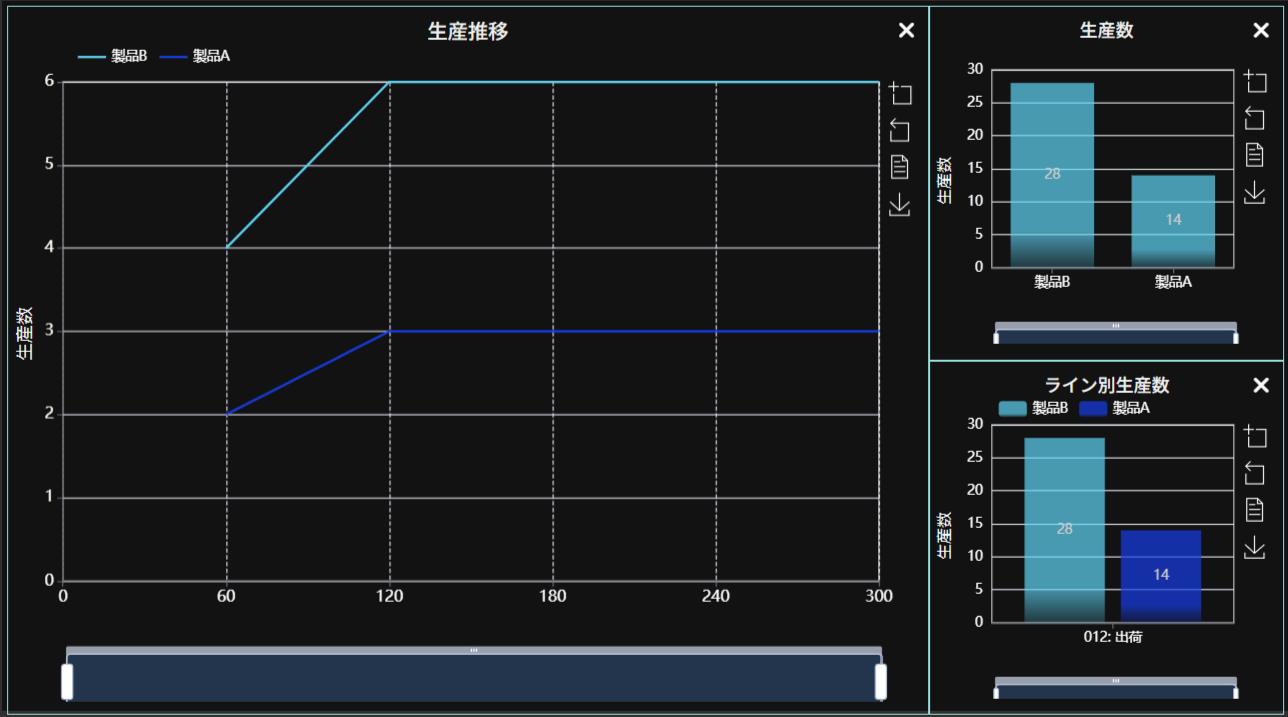
人員の生産性を変えてレイアウト変更の効果を確認する
次に前回の記事と同じ設定で、人員を4つの作業プロセス(「005プレス作業A」、「008曲げ作業B」、「016プレス作業C」、「013曲げ作業D」)に配置することを仮定し、シミュレーションを行ってレイアウト変更の結果を比較してみましょう。前回と同様に12通りのシミュレーションを行います。
結果は以下の通りとなりました。
ラインA担当と時間 (プレス作業-曲げ作業) | ラインB担当と時間 (プレス作業-曲げ作業) | 300分での総生産数 (レイアウト変更前) | 300分での総生産数 (レイアウト変更後) | |
組合わせ1 (モデル作成時の設定) | A-B(5-20) | C-D(15-10) | 33 | 42 |
組合わせ2 | A-B(5-20) | D-C(20-5) | 28 | 71 |
組合わせ3 | B-A(10-15) | D-C(20-5) | 33 | 43 |
組合わせ4 | B-A(10-15) | C-D(15-10) | 36 | 46 |
組合わせ5 | A-C(5-5) | B-D(10-10) | 86 | 86 |
組合わせ6 | A-C(5-5) | D-B(20-20) | 71 | 71 |
組合わせ7 | C-A(15-15) | D-B(20-20) | 31 | 31 |
組合わせ8 | C-A(15-15) | B-D(10-10) | 46 | 46 |
組合わせ9 | A-D(5-10) | B-C(10-5) | 58 | 86 |
組合わせ10 | A-D(5-10) | C-B(15-20) | 43 | 43 |
組合わせ11 | D-A(20-15) | C-B(15-20) | 28 | 31 |
組合わせ12 | D-A(20-15) | B-C(10-5) | 43 | 43 |
シミュレーションの結果、もっとも生産数が多い作業員の組み合わせは、
ラインA担当と時間 (プレス作業-曲げ作業) | ラインB担当と時間 (プレス作業-曲げ作業) | 300分での総生産数 (レイアウト変更前) | 300分での総生産数 (レイアウト変更後) | |
組合わせ5 | A-C(5-5) | B-D(10-10) | 86 | 86 |
で変わらなかったものの、レイアウトを変更する前の結果と後の結果を比較すると、レイアウト変更後で全ての組み合わせで生産性が高くなるか同等となっており、変更前より良いレイアウトであると言うことが出来ます。
まとめ
今回はassimeeのシミュレーションを使ってレイアウト配置が変わった時の生産性を確認する方法について解説しました。シミュレーションを使うことで、実際の生産ラインで試すことなく、PCの中で、レイアウトを自由に変更しながら、最善のレイアウトを検討することが可能です。また、変更前後の生産性の違いを根拠として示すことで、費用や手間の必要な生産ラインの変更が、採算に見合うかどうかを判定することもできるので、生産ラインのレイアウト決定業務の平準化に役立ちます。
assimeeでは、実際の製造プロセスをモデル化し、シミュレーションすることで、プロセスの見える化や潜在的な課題の洗い出しを行うことができます。製造プロセスのデジタル化や課題解決でお悩みの方は、ぜひお問い合わせください。