概要
assimeeでは時間帯別に人員配置を行うこと、時間帯別に設定した出荷目標を使って時間帯別人員配置の最適化を行うことが可能です。今回の記事では時間帯別人員配置の方法と、時間帯別人員配置最適化の方法についてそれぞれ解説します。
モデル
使用するモデルは以下のようにすべてのプロセスが直線的に並んでいるモデルとなります。最適化対象は003加工と005梱包作業の2か所で行うことを想定します。

STEP1プロセス図の作成
入荷プロセス:
特に変更なし
置き場プロセス:
プロセス名を「置き場A」に変更
加工プロセス:
特に変更なし
置き場プロセス:
プロセス名を「置き場B」に変更
作業プロセス:
プロセス名を「梱包作業」に変更
ローラーコンベア―:
特に変更なし
出荷プロセス:
特に変更なし
STEP2パラメーターの設定
001入荷:
品目を「部品」、個数を「20個」、時間間隔を「1分」と設定
002置き場A:
容量を「1000個」に設定
003加工:
1回あたりの処理時間を「1分」、
対象品目を「部品」、個数を「1個」、
出力品目を「製品」、個数を「1個」と設定
004置き場B:
容量を「1000個」に設定
005梱包作業:
1回あたりの処理時間を「1分」、
対象品目を「製品」、個数を「1個」と設定
006ローラーコンベア―:
搬送時間を「1分」、最大積荷個数を「120個」と設定
007出荷:
特に変更なし
時間帯別の人員配置の設定
003加工の右下にある「詳細設定」ボタンを押し、詳細設定画面を開いて「作業員」にチェックを入れます。
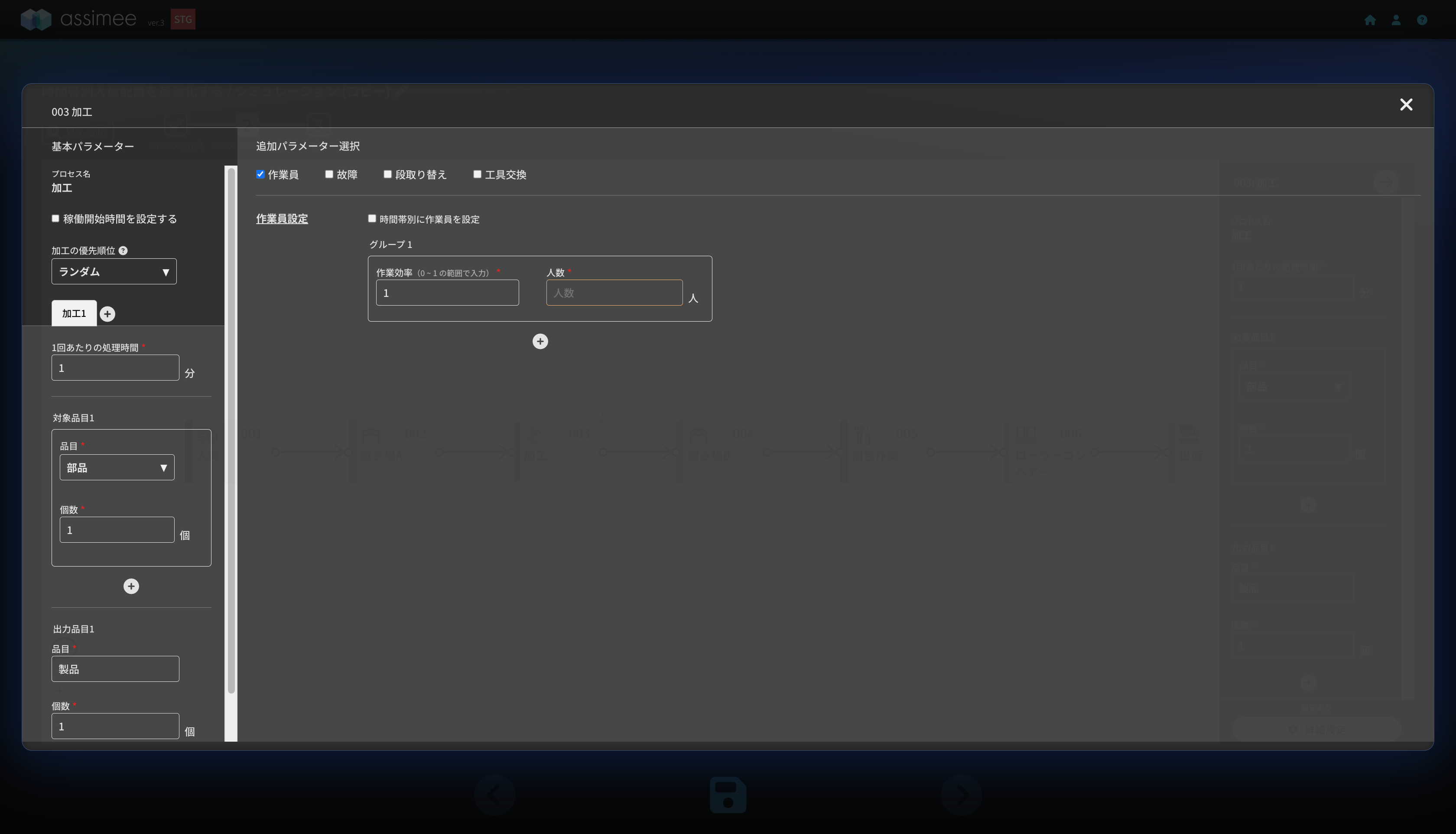
「時間帯別に作業員を設定」が表示されるのでこちらにもチェックを入れます。標準では60分間隔で0分から300分までが表示されるので、以下の図のように0分から180分まで作業人数を5人、180分から300分まで作業人数を10人と設定します。
*005梱包作業も同じ値を設定します。
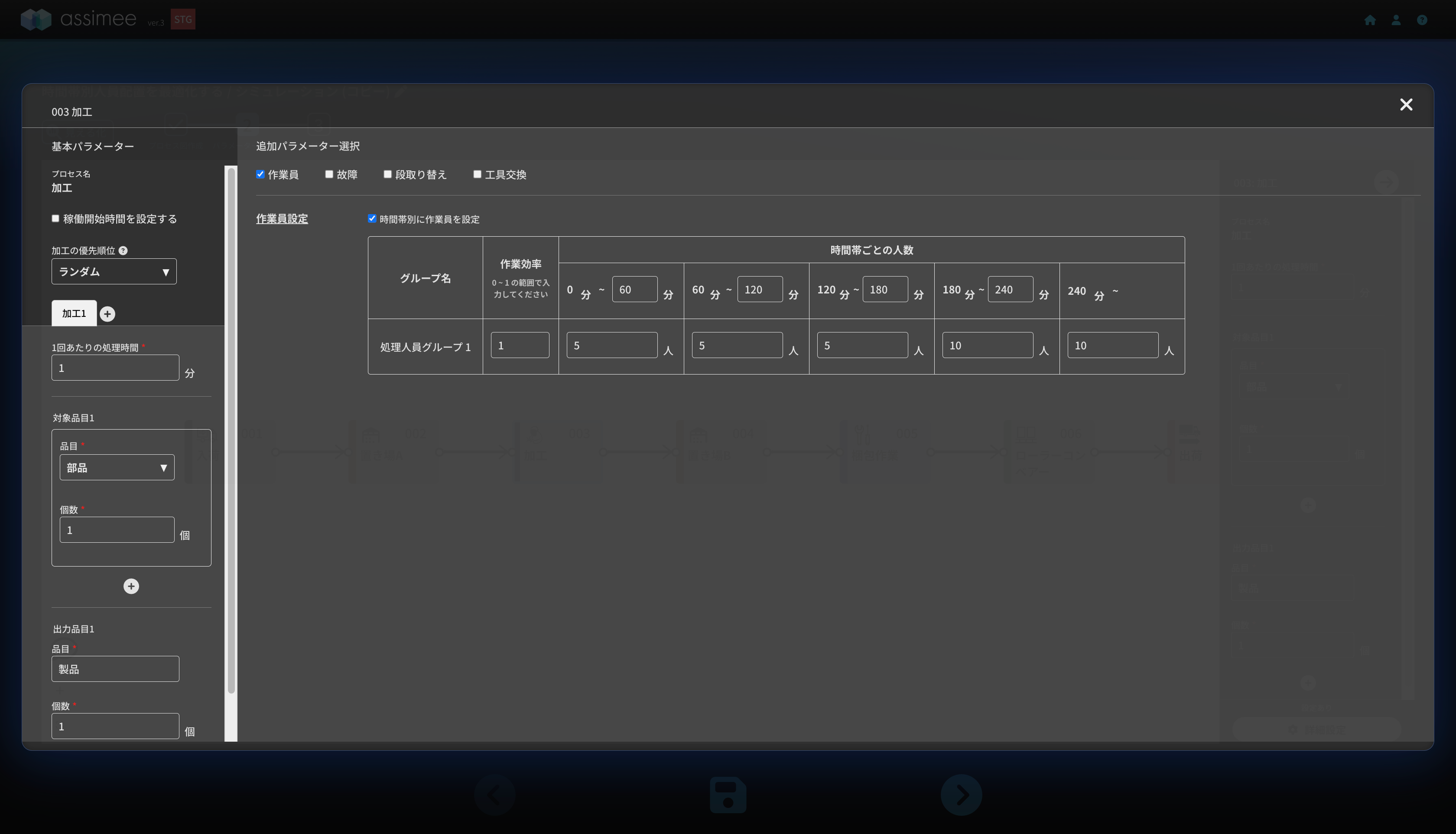
シミュレーション
パラメーターの設定が終わったら、シミュレーション時間を300分と設定しシミュレーションを実行します。実行後、ダッシュボードから結果を確認することが出来るので「生産推移」のグラフを選択します。
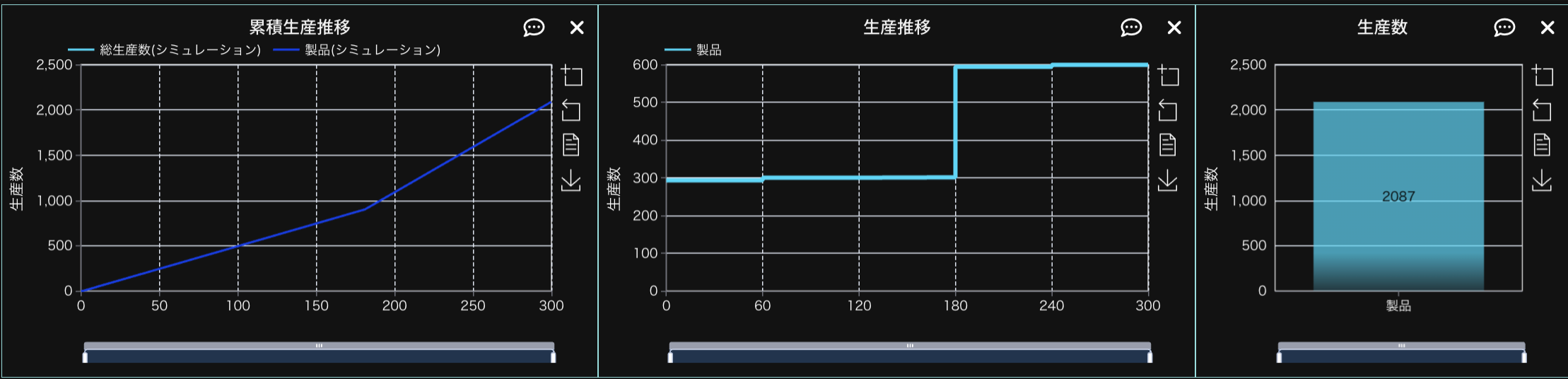
今回は入荷は出荷目標に対して十分にあるという前提の元、0分から180分まで作業人数を5人、180分から300分まで作業人数を10人と設定していました。「生産推移」のグラフを見ると配置した人員に応じて180分から300分までの生産量が、0分から180分までの生産量の2倍になっていることが分かります。
最適化
最適化の準備
最適化を行うためにはプロセスカードの選択と、最適化範囲の設定、出荷目標の設定を行う必要があります。まず、先に作成したシミュレーション用のモデルのレポートを保存します。次に保存したレポートから「新しい課題を開始」を選択し、「人の最適化」を選択します。次へをクリックすると最適化対象とするプロセスカードの選択画面が開くので、今度は以下のように「003加工」と「005梱包作業」を選択します。
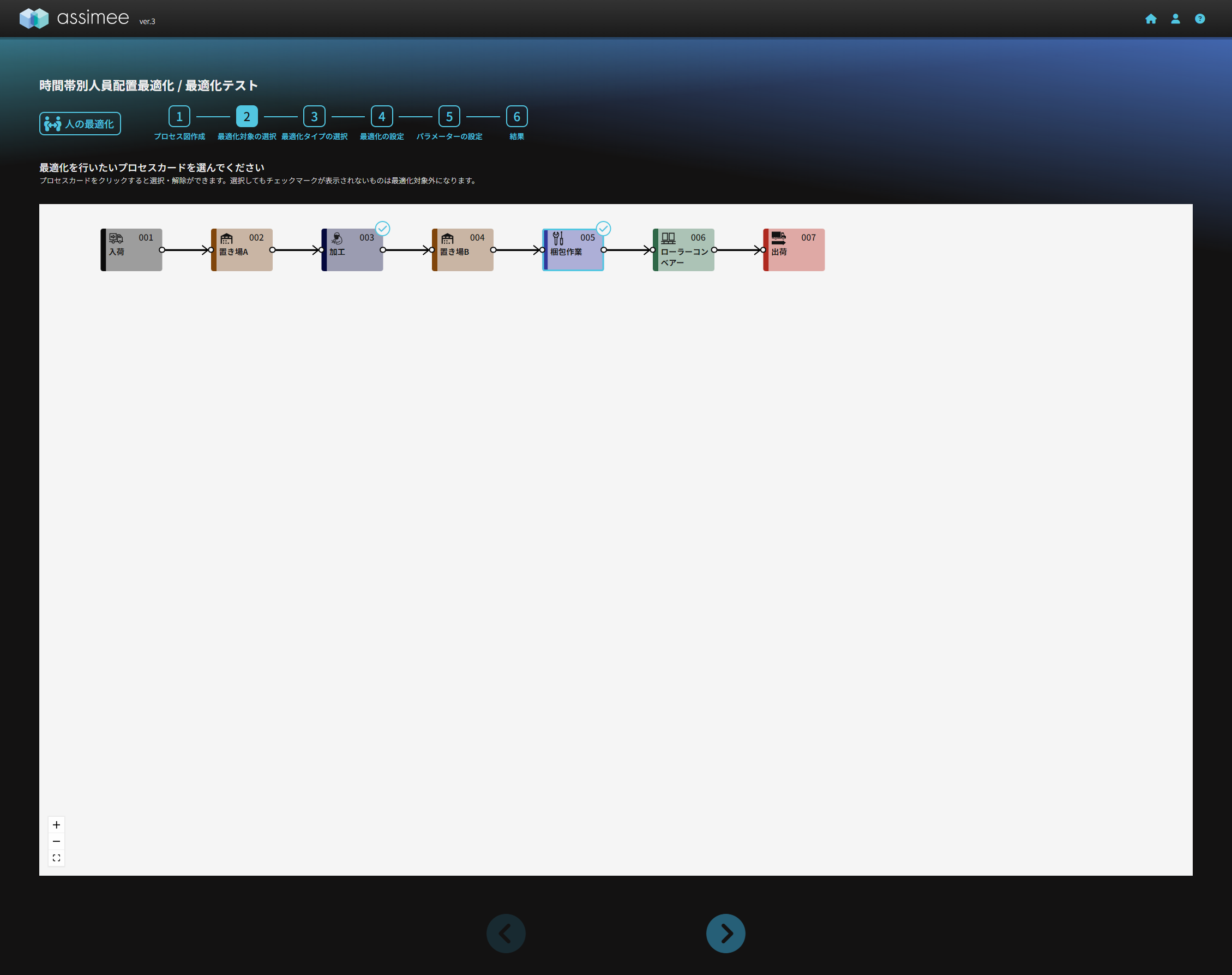
そうすると人の最適化のオプション設定画面が開くので、以下のように「時間帯ごとに人員配置の最適化を行う」を選びます。
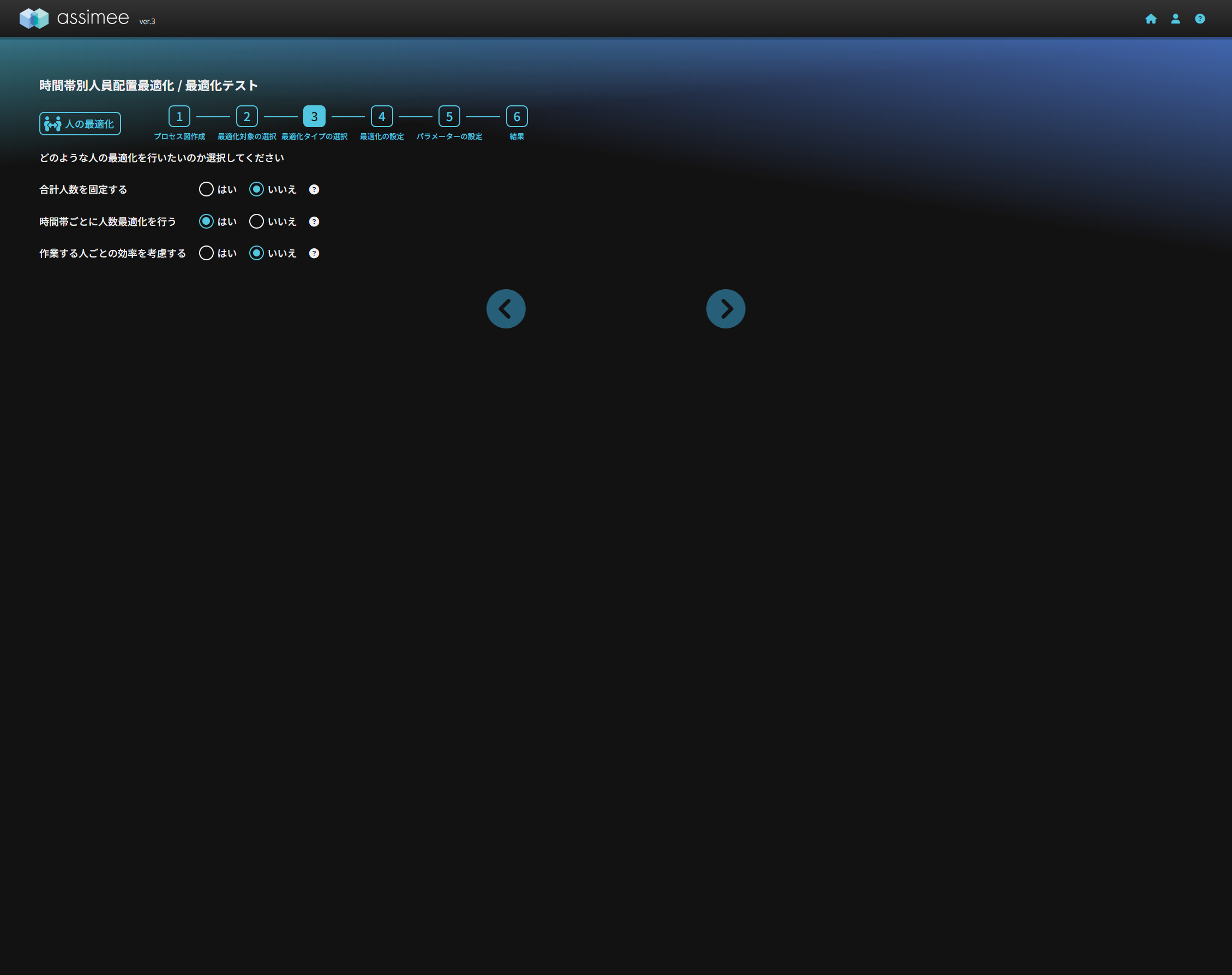
次にパラメーターの設定画面が開くので出荷プロセスを選択し、出荷目標を以下のように設定します。今回は生産量が60分で大きく変動する場合を想定します。
*なお、シミュレーションの項で設定した最適化対象のパラメーターは最適化には影響しません。
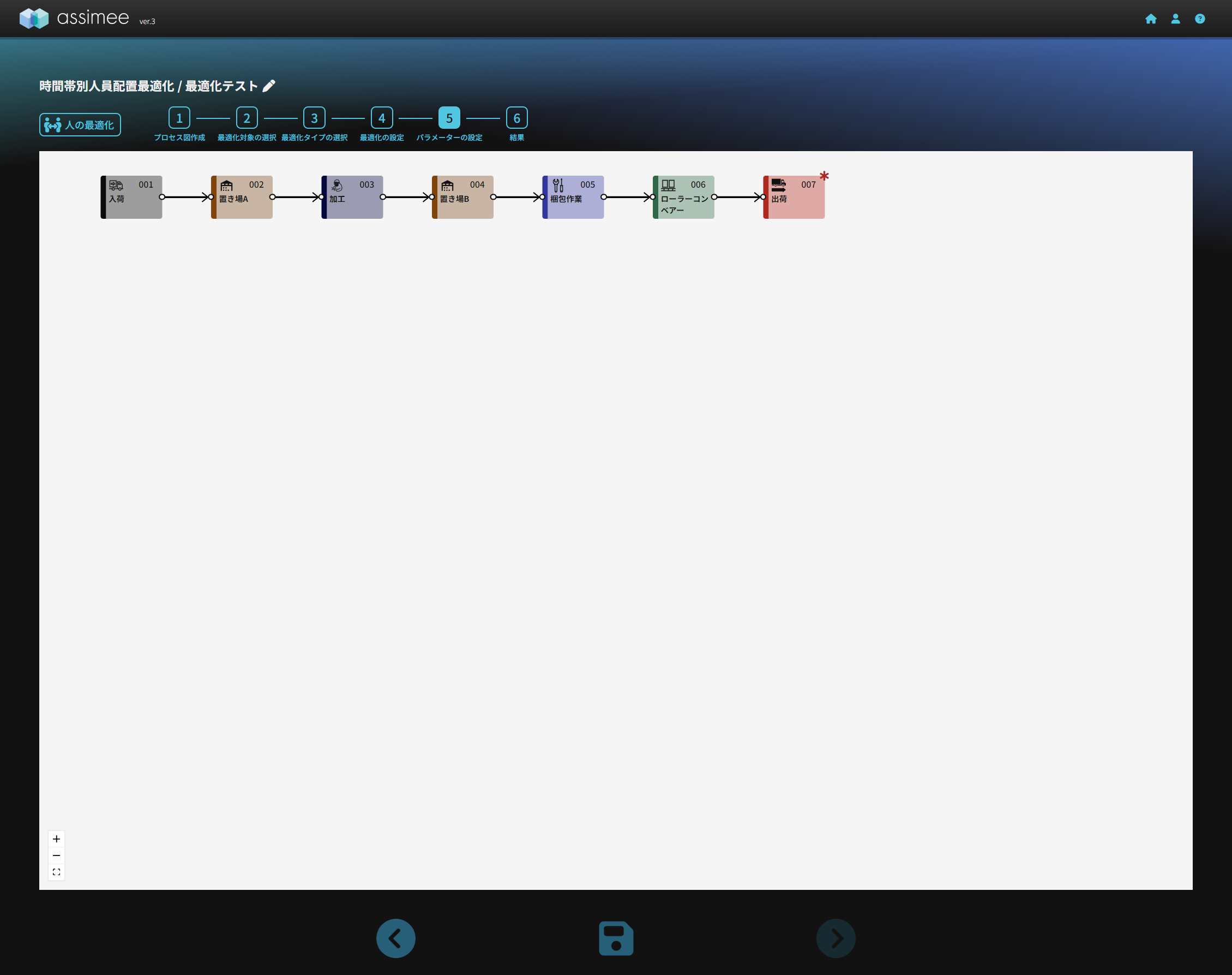
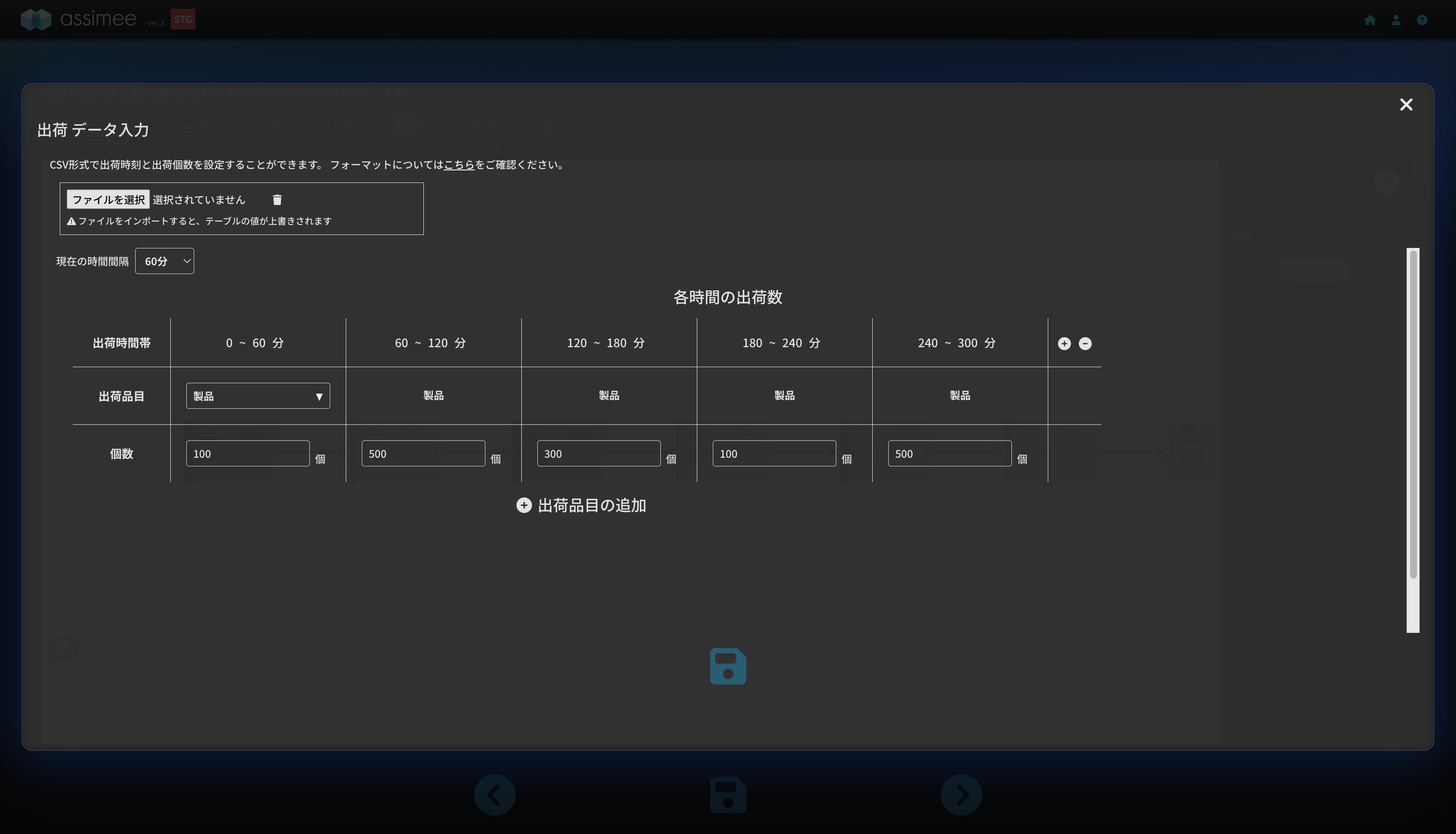
最後に、最適化範囲の設定を行います。「003加工」と「005梱包作業」の作業人数を選択すると以下の画面が開くので、人員の範囲を設定します。今回は下限値を「1人」、上限値を「10人」とします。
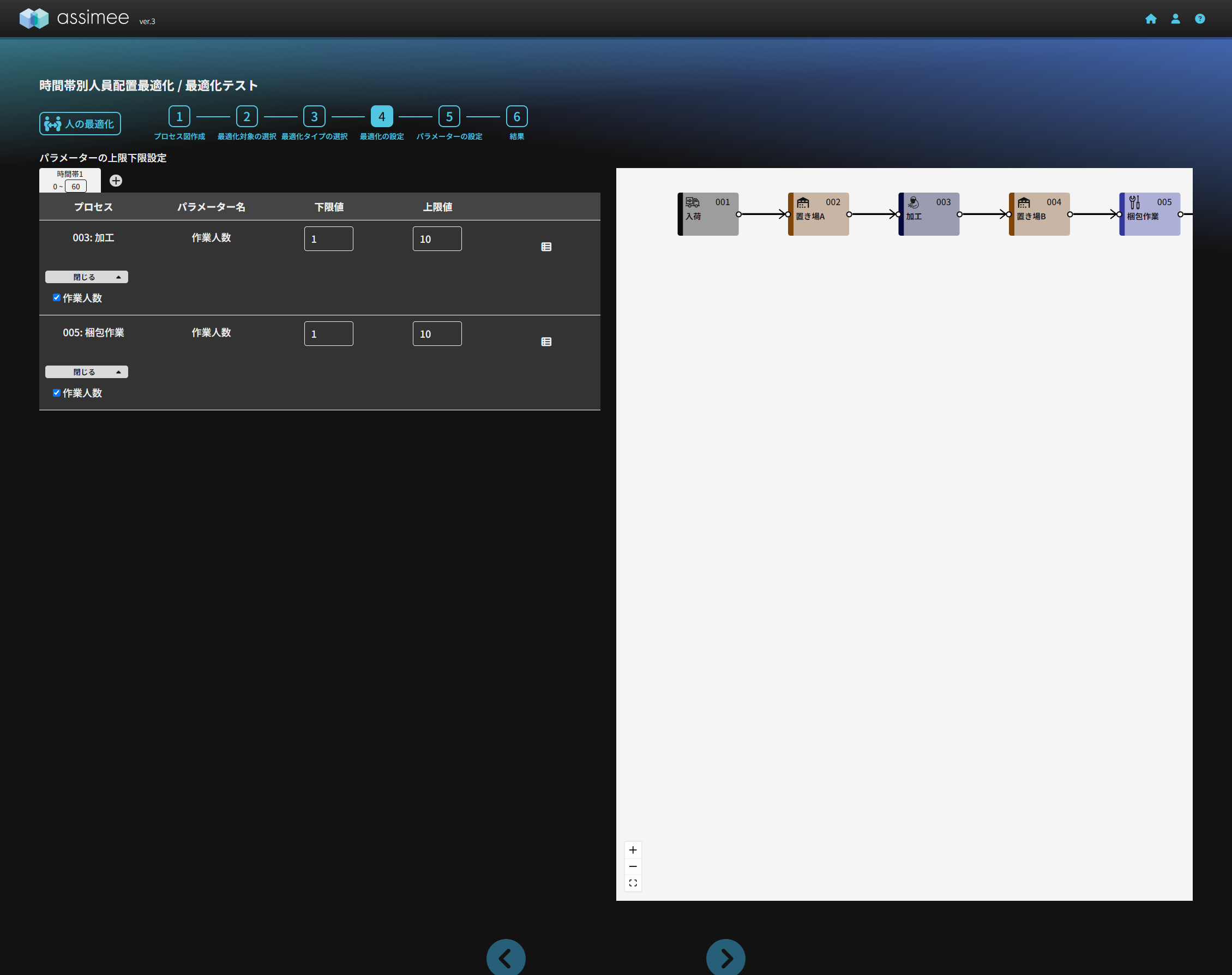
初期の状態だと最適化範囲が0から60分しかないので、+ボタンを押して、300分まで時間項目を増やします。右側の表マークをクリックすると個別に人員の範囲を設定できるので、エラーが起こった場合や異なる目標を設定したい場合はそこから行ってください。
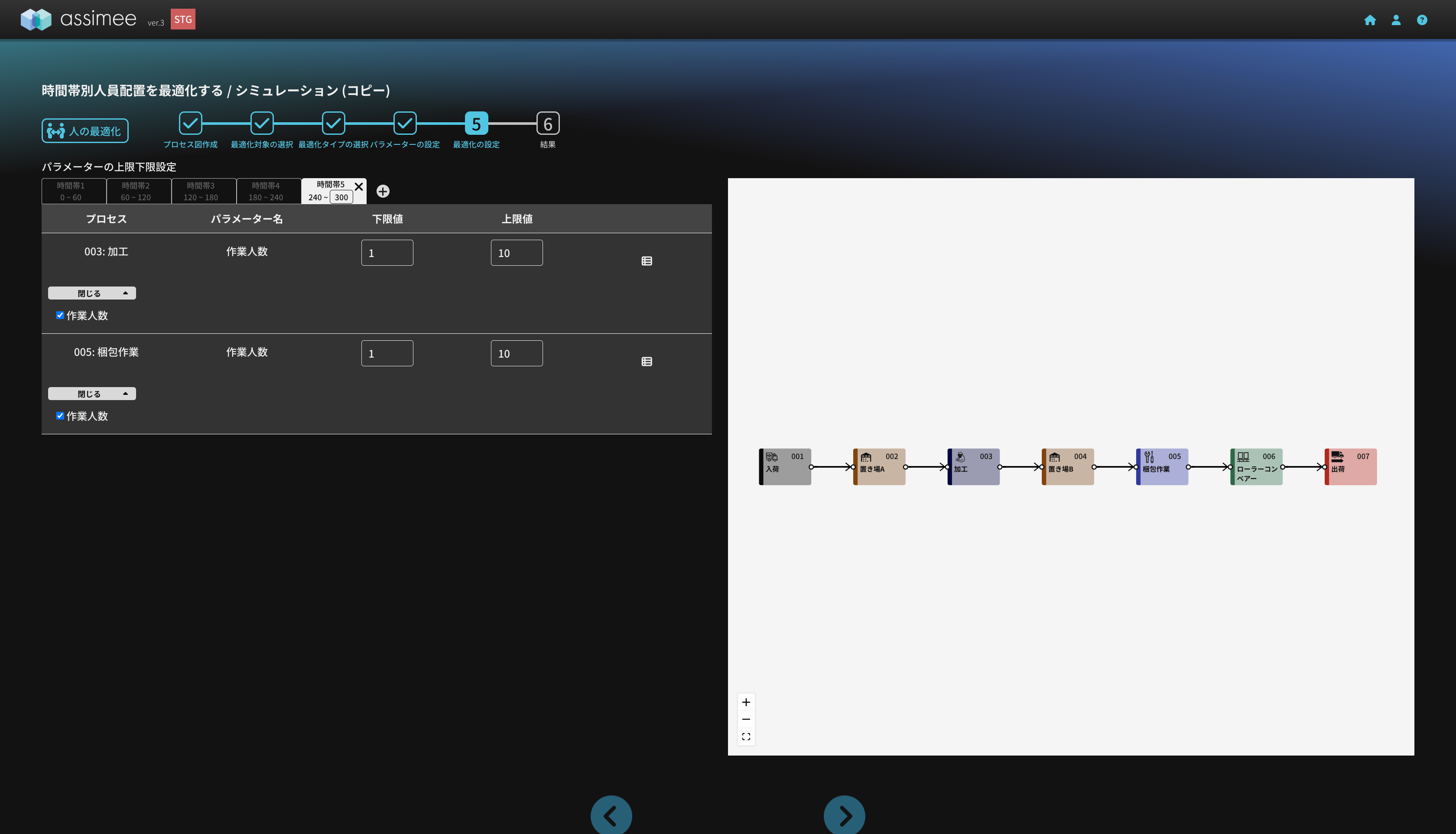
上下限値の設定が終了したら最適化を実行します。
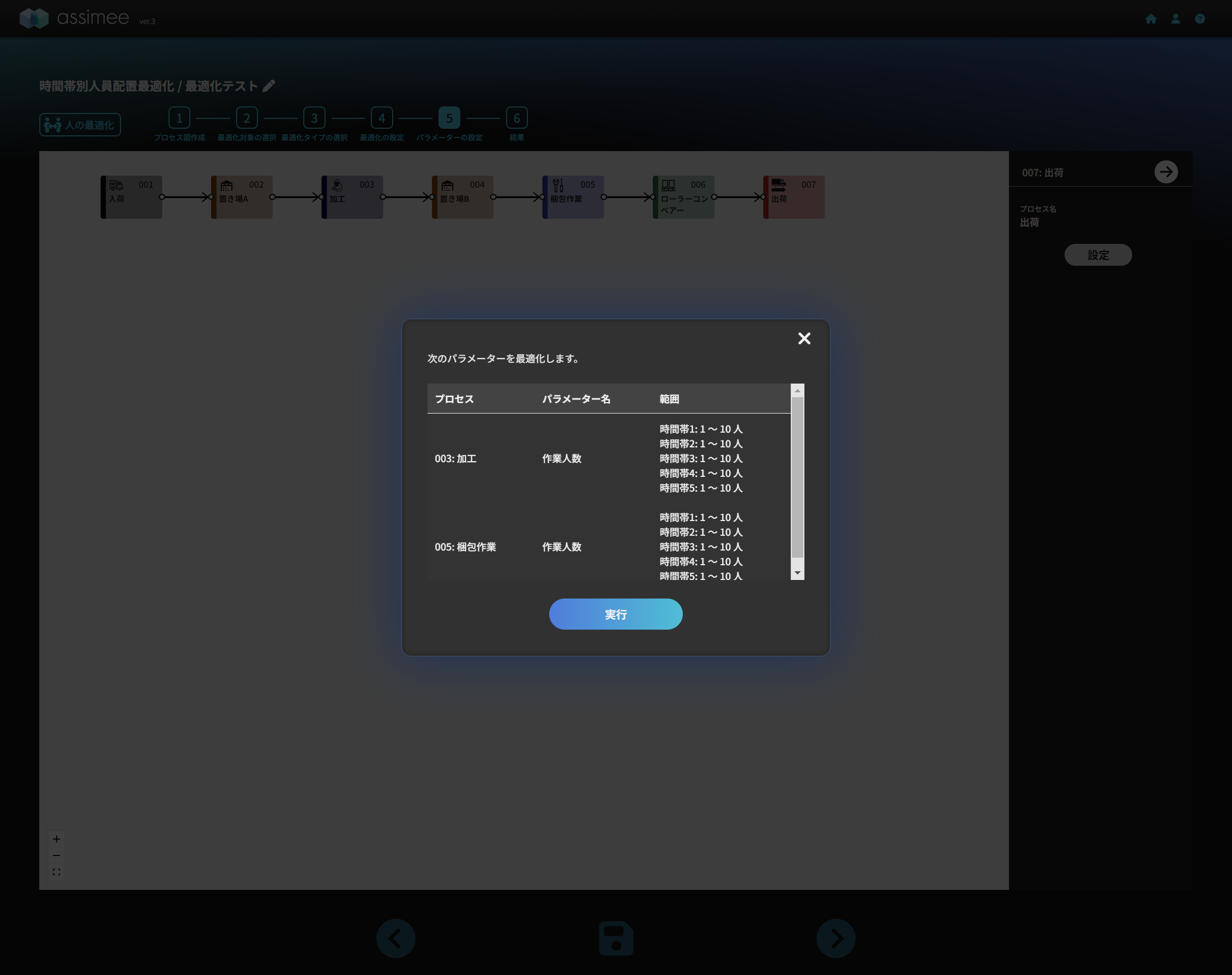
最適化の実行と分析
最適化が終了したら、ダッシュボードで結果を分析します。「累積生産数」と「累積生産数」と「生産推移」、「生産数」を表示させると以下のようになります。
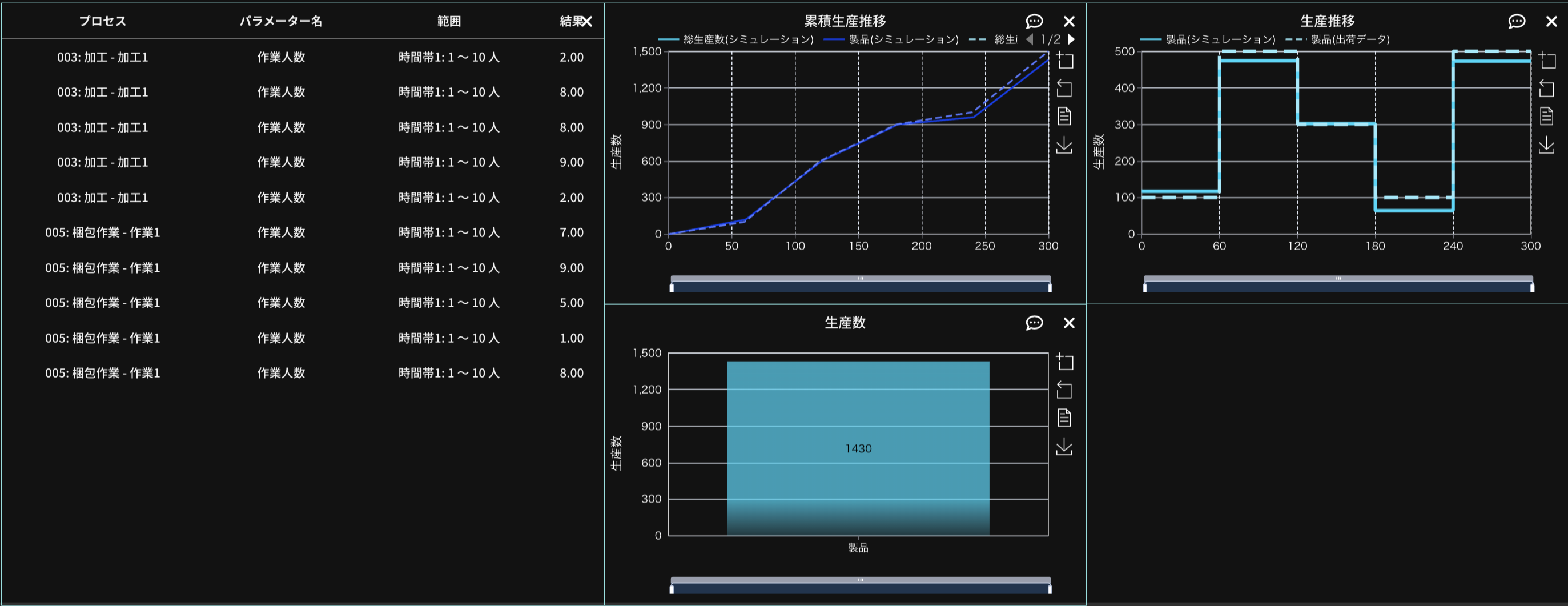
点線で表現される出荷目標に対して、実線で表現されるシミュレーション結果が一致していることがよくわかります。
*最適化結果に不満がある場合は右上の「最適化の収束状況を確認」から追加最適化を行うことが出来ます。それでも結果に不満がある場合は出荷目標や人数の上下限値の設定を見直してください。
まとめ
今回の記事では時間帯別人員配置のやり方と時間帯別人員配置最適化のやり方を解説しました。時間帯別に人員を配置するシミュレーションにより、人員配置が変動する場合のモデルの作成や時間別に細かく変動するような出荷目標に対応した効率的な人員配置が可能となります。また、出荷目標の変動による作業のボトルネックを効率的に探索し、ボトルネックの解消のために一時的に作業人員の割振りを変更するなどの対策を速やかに検討し、実行することも容易となります。