概要
assimeeは製造業や物流だけでなく、様々な業務のフローを再現することが可能です。今回の記事ではISO9001で定義された会社の監査プロセスをサンプルにモデルを作成してみましょう。
今回のモデルは下図のようになります。
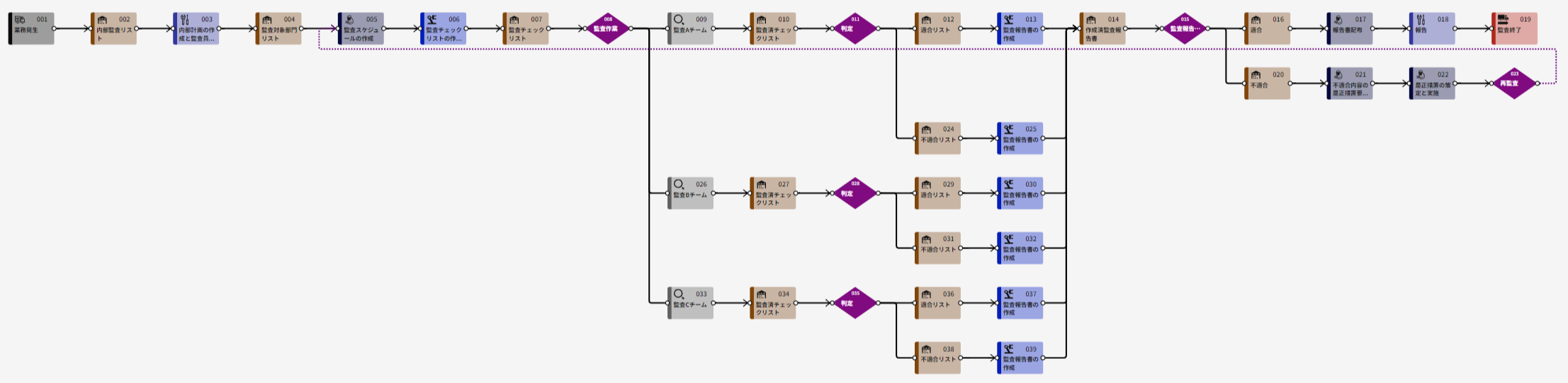
モデルの作成
モデルの前提
今回は以下のような設定となるようにモデルを構成し、設定を行います。
- 入荷量:5日(2400分)に5業務
- 稼働時間:1日当たり8時間稼働で5日(2400分)
- 監査チームを3つ用意
- 監査で不具合がある場合は再監査
モデルの作成は以下の3つのブロックに分けて解説と設定を行います。
- 準備ブロック
- 監査ブロック
- 報告ブロック
STEP1 プロセス図を作成する
準備ブロック
準備ブロックは監査業務の発生からスケジューリング、監査用のチェックリストの作成業務を想定して以下の図のようにプロセスカードを配置します。
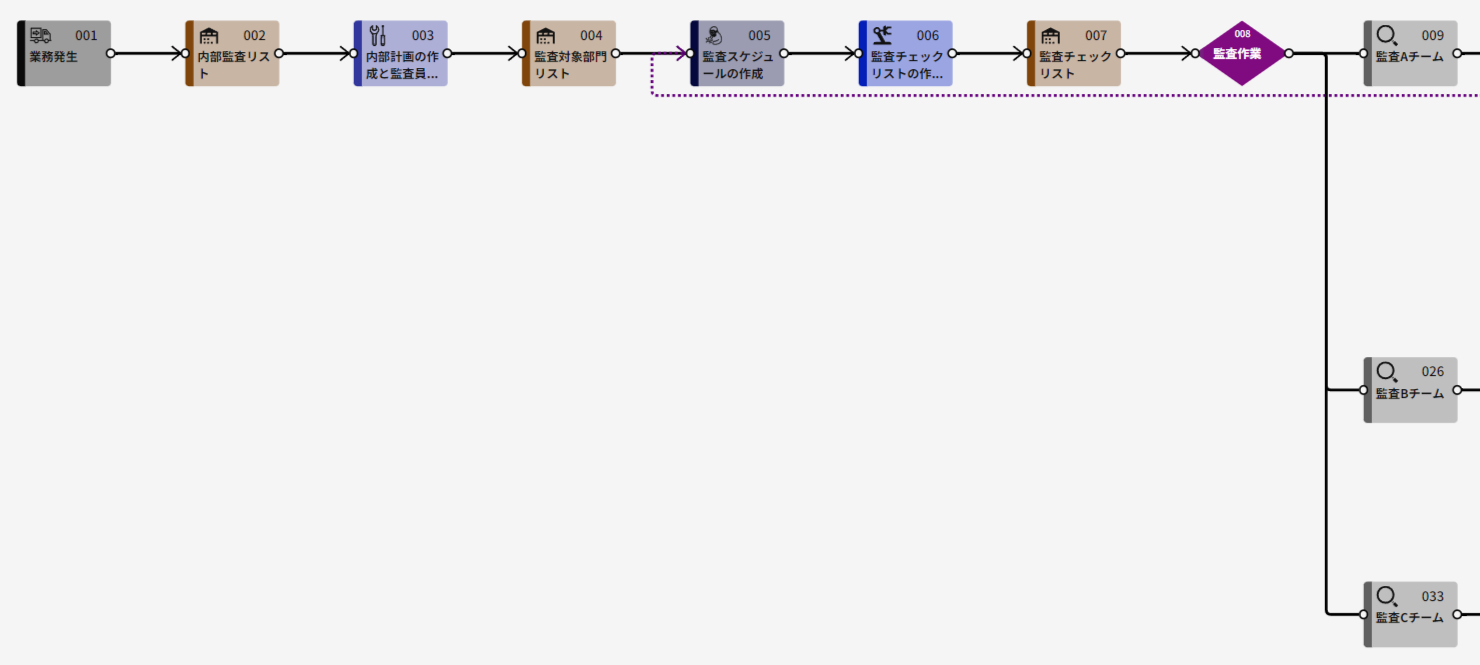
入荷プロセス:
プロセス名を「業務発生」へ変更
置き場プロセス:
プロセス名を「内部監査リスト」へ変更
作業プロセス:
プロセス名を「内部計画の作成と監査員の選定」へ変更
置き場プロセス:
プロセス名を「監査対象部門リスト」へ変更
加工プロセス:
プロセス名を「監査スケジュールの作成」へ変更
組立プロセス:
プロセス名を「監査チェックリストの作成」へ変更
置き場プロセス:
プロセス名を「監査チェックリスト」へ変更
分岐プロセス:
プロセス名を「監査作業」へ変更
分岐先として3つのプロセスを設置:
検品プロセス:
プロセス名を「監査Aチーム」へ変更
検品プロセス:
プロセス名を「監査Bチーム」へ変更
検品プロセス:
プロセス名を「監査Cチーム」へ変更
以降は監査ブロックで設定します。
監査ブロック
監査ブロックは実際の監査を行う部分で、今回は3つの監査チームを配置してそれぞれ監査と監査の報告書を作成する業務を想定して、以下の図のようにプロセスカードを配置します。シミュレーション後に監査に適合と不適合の件数が分かるように分岐を使って、適合と不適合を別々のリスト(置き場)に入れてから報告書を作成するように配置します。
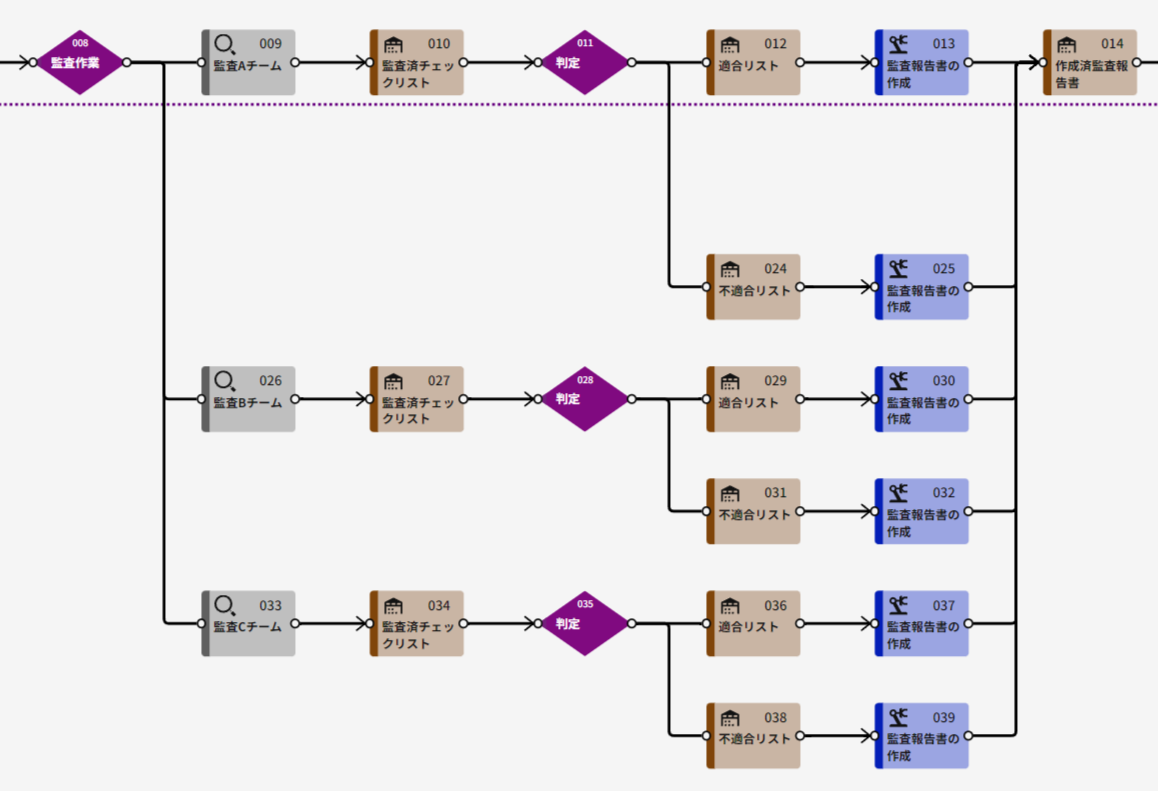
監査チームA
検品プロセス(再掲):
プロセス名を「監査Aチーム」へ変更
置き場プロセス:
プロセス名を「監査済チェックリスト」へ変更
分岐プロセス:
プロセス名を「判定」へ変更
分岐先として2つのプロセスを設置:
置き場プロセス:
プロセス名を「適合リスト」へ変更
置き場プロセス:
プロセス名を「不適合リスト」へ変更
・適合側
置き場プロセス(再掲):
プロセス名を「適合リスト」へ変更
組立プロセス:
プロセス名を「監査報告書の作成」へ変更
・不適合側
置き場プロセス(再掲):
プロセス名を「不適合リスト」へ変更
組立プロセス:
プロセス名を「監査報告書の作成」へ変更
監査チームB
検品プロセス(再掲):
プロセス名を「監査Bチーム」へ変更
置き場プロセス:
プロセス名を「監査済チェックリスト」へ変更
分岐プロセス:
プロセス名を「判定」へ変更
分岐先として2つのプロセスを設置:
置き場プロセス:
プロセス名を「適合リスト」へ変更
置き場プロセス:
プロセス名を「不適合リスト」へ変更
・適合側
置き場プロセス(再掲):
プロセス名を「適合リスト」へ変更
組立プロセス:
プロセス名を「監査報告書の作成」へ変更
・不適合側
置き場プロセス(再掲):
プロセス名を「不適合リスト」へ変更
組立プロセス:
プロセス名を「監査報告書の作成」へ変更
監査チームC
検品プロセス(再掲):
プロセス名を「監査Cチーム」へ変更
置き場プロセス:
プロセス名を「監査済チェックリスト」へ変更
分岐プロセス:
プロセス名を「判定」へ変更
分岐先として2つのプロセスを設置:
置き場プロセス:
プロセス名を「適合リスト」へ変更
置き場プロセス:
プロセス名を「不適合リスト」へ変更
・適合側
置き場プロセス(再掲):
プロセス名を「適合リスト」へ変更
組立プロセス:
プロセス名を「監査報告書の作成」へ変更
・不適合側
置き場プロセス(再掲):
プロセス名を「適合リスト」へ変更
組立プロセス:
プロセス名を「監査報告書の作成」へ変更
6つある監査報告書の作成プロセスからは次に作成する置き場「作成済監査報告書」へ合流させます。
報告ブロック
報告ブロックは監査全体の判定と、監査の適合ケースに対しては報告、不適合ケースに対しては改善策の作成と実施、改善策実施後の再監査の実施を想定して以下の図のようにプロセスカードを配置します。再監査は業務の再発生と想定して、監査スケジュールの作成までフローを戻すように配置しました。

置き場プロセス:
プロセス名を「作成済監査報告書」へ変更
上図中の013など、6つある監査報告書の作成プロセスから合流
分岐プロセス:
プロセス名を「監査報告書の検討」へ変更
分岐先として2つのプロセスを設置:
置き場プロセス:
プロセス名を「適合」へ変更
置き場プロセス:
プロセス名を「不適合」へ変更
適合側
置き場プロセス(再掲):
プロセス名を「適合」へ変更
加工プロセス:
プロセス名を「報告書配布」へ変更
作業プロセス:
プロセス名を「報告」へ変更
出荷プロセス:
プロセス名を「監査終了」へ変更
不適合側
置き場プロセス(再掲):
プロセス名を「不適合」へ変更
加工プロセス:
プロセス名を「不適合内容の是正措置要求書の作成」へ変更
加工プロセス:
プロセス名を「是正措置の策定と実施」へ変更
分岐プロセス:
プロセス名を「再監査」へ変更
既プロセスへ接続を使用し上流側の「監査スケジュールの作成」へ接続
STEP2 パラメーターを設定する
準備ブロック
001業務発生:
入荷品目を「監査業務」、個数を「5個」、時間間隔を「2400分」と設定
002内部監査リスト:
容量を「1000個」と設定
003内部計画の作成と監査員の選定:
1回あたりの処理時間を「60分」、対象品目を「監査業務」、個数を「1個」と設定
004監査対象部門リスト:
容量を「1000個」と設定
005監査スケジュールの作成:
1回あたりの処理時間を「60分」と設定、
対象品目を「監査業務」、個数を「1個」、
出力品目を「監査スケジュール」、個数を「1個」と設定
006監査チェックリストの作成:
1回あたりの処理時間を「60分」と設定、
対象品目を「監査スケジュール」、個数を「1個」、
出力品目を「監査チェックリスト」、個数を「1個」と設定
007監査チェックリスト:
容量を「1000個」と設定
008監査作業:
1回あたりの処理時間を「1分」と設定
分岐条件:
ランダムに設定(デフォルトのまま変更なし)
以降は次の監査ブロックで設定します。
監査ブロック
監査チームA
009監査Aチーム:
1回あたりの処理時間を「480分」、不良品率を「10%」と設定
010監査済チェックリスト:
容量を「1000個」と設定
011判定:
1回あたりの処理時間を「1分」と設定
分岐条件:
条件1:
対象品目:正常:監査チェックリスト
送り先:012適合リスト
条件2:
対象品目:不良:監査チェックリスト
送り先:024不適合リスト
・適合側
012適合リスト:
容量を「1000個」と設定
013監査報告書の作成:
1回あたりの処理時間を「480分」と設定、
対象品目を「監査チェックリスト」、個数を「1個」、
出力品目を「監査報告書(適合)」、個数を「1個」と設定
・不適合側
024不適合リスト:
容量を「1000個」と設定
025監査報告書の作成:
1回あたりの処理時間を「480分」と設定、
対象品目を「監査チェックリスト」、個数を「1個」、
出力品目を「監査報告書(不適合)」、個数を「1個」と設定
監査チームB
026監査Bチーム:
1回あたりの処理時間を「480分」、不良品率を「10%」と設定
027監査済チェックリスト:
容量を「1000個」と設定
028判定:
1回あたりの処理時間を「1分」と設定
分岐条件:
条件1:
対象品目:正常:監査チェックリスト
送り先:029適合リスト
条件2:
対象品目:不良:監査チェックリスト
送り先:031不適合リスト
・適合側
029適合リスト:
容量を「1000個」と設定
030監査報告書の作成:
1回あたりの処理時間を「480分」と設定、
対象品目を「監査チェックリスト」、個数を「1個」、
出力品目を「監査報告書(適合)」、個数を「1個」と設定
・不適合側
031不適合リスト:
容量を「1000個」と設定
032監査報告書の作成:
1回あたりの処理時間を「480分」と設定、
対象品目を「監査チェックリスト」、個数を「1個」、
出力品目を「監査報告書(不適合)」、個数を「1個」と設定
監査チームC
033監査Aチーム:
1回あたりの処理時間を「480分」、不良品率を「10%」と設定
034監査済チェックリスト:
容量を「1000個」と設定
035判定:
1回あたりの処理時間を「1分」と設定
分岐条件:
条件1:
対象品目:正常:監査チェックリスト
送り先:036適合リスト
条件2:
対象品目:不良:監査チェックリスト
送り先:038不適合リスト
・適合側
036適合リスト:
容量を「1000個」と設定
037監査報告書の作成:
1回あたりの処理時間を「480分」と設定、
対象品目を「監査チェックリスト」、個数を「1個」、
出力品目を「監査報告書(適合)」、個数を「1個」と設定
・不適合側
038不適合リスト:
容量を「1000個」と設定
039監査報告書の作成:
1回あたりの処理時間を「480分」と設定、
対象品目を「監査チェックリスト」、個数を「1個」、
出力品目を「監査報告書(不適合)」、個数を「1個」と設定
6つ監査報告書の作成プロセスから「014監査報告書の作成」へ合流しているかチェックしてください。
報告ブロック
014作成済監査報告書」:
容量を「1000個」と設定
015監査報告書の検討:
1回あたりの処理時間を「60分」と設定
分岐条件:
条件1:
品目:監査報告書(適合)
送り先:016適合
条件2:
品目:監査報告書(不適合)
送り先:020不適合
適合側
016適合:
容量を「1000個」と設定
017報告書配布:
1回あたりの処理時間を「60分」と設定、
対象品目を「監査報告書(適合)」、個数を「1個」、
出力品目を「監査報告書」、個数を「1個」と設定
018報告:
1回あたりの処理時間を「1分」、対象品目を「監査報告書」、個数を「1個」と設定
019監査終了:
特に設定なし
不適合側
020不適合:
容量を「1000個」と設定
021不適合内容の是正措置要求書の作成:
1回あたりの処理時間を「60分」と設定、
対象品目を「監査報告書(不適合)」、個数を「1個」、
出力品目を「改善点リスト」、個数を「1個」と設定
022是正措置の策定と実施:
1回あたりの処理時間を「480分」と設定、
対象品目を「改善点リスト」、個数を「1個」、
出力品目を「改善業務」、個数を「1個」と設定
023再監査:
1回あたりの処理時間を「1分」と設定、
上流側の「005監査スケジュールの作成」へ接続されているか確認
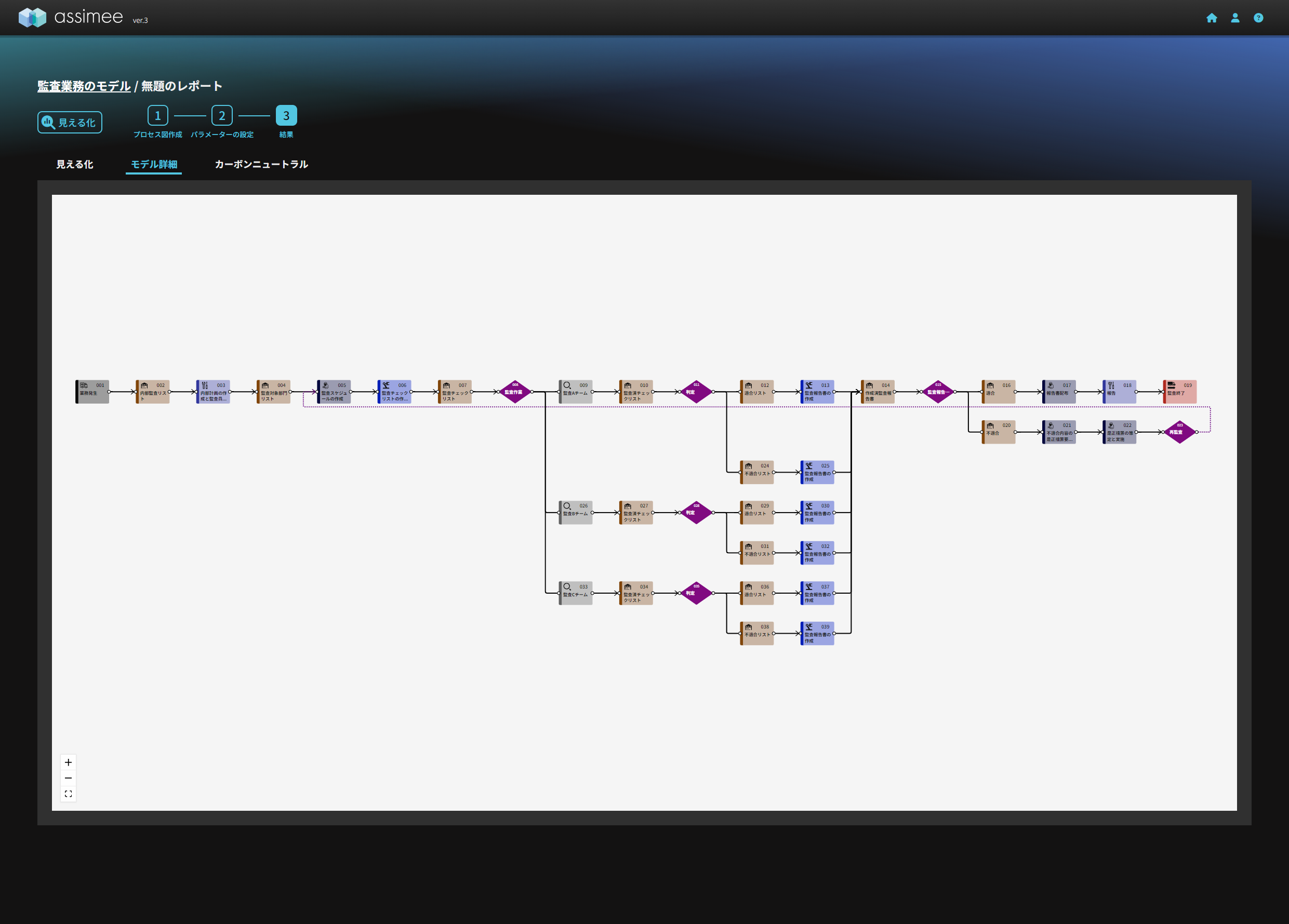
シミュレーション
モデルのパラメーター設定が終了したら、モデル名を「監査業務のモデル」に変更し、シミュレーション時間を5日の業務時間に相当する2400分に変更してシミュレーションを行います。シミュ―ションが終了するダッシュボード画面が表示され、結果を確認することができます。*再監査の発生にランダム変数が含まれるため、シミュ―ション結果が一致しないことがあります。
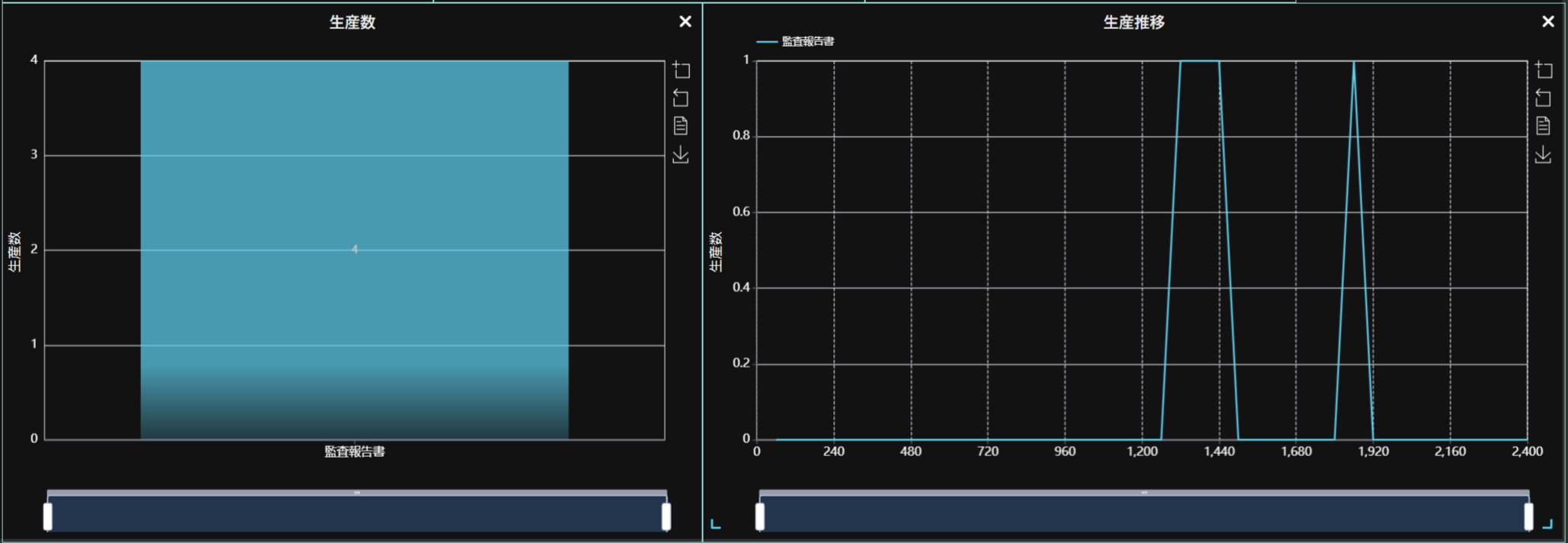
このモデルでは5日間(2400分)で5件の業務が発生していますが、ランダムに全件が再監査となり、0件と表示される場合があります。その場合は再度シミュレーションを実施してみてください。何回シミュレーションを行っても0件が表示される場合は、モデルに問題があると考えられるのでシミュレーションの設定を再度確認してください。
まとめ
今回はISO9001に従った会社の監査プロセスをサンプルにassimeeでモデルを作る方法について解説しました。このようにassimeeでは製造業や物流以外にも様々な分野の業務をモデル化してシミュレーションや最適化を行うことが可能です。