概要
以前の記事では、セル生産方式をサンプルとしたモデル作成を解説しました。このモデルでは、1つのセルを1人の作業員が担当する想定で作成しています。今回のチュートリアルでは、1つのセルを2人で分業する場合を考えて、モデルを作成してみましょう。
モデル
以前作成したセル生産方式のモデルは以下の通りとなります。5つの組立プロセスからなる生産用セルが2つあるカメラ組立工場を想定したモデルとなっています。
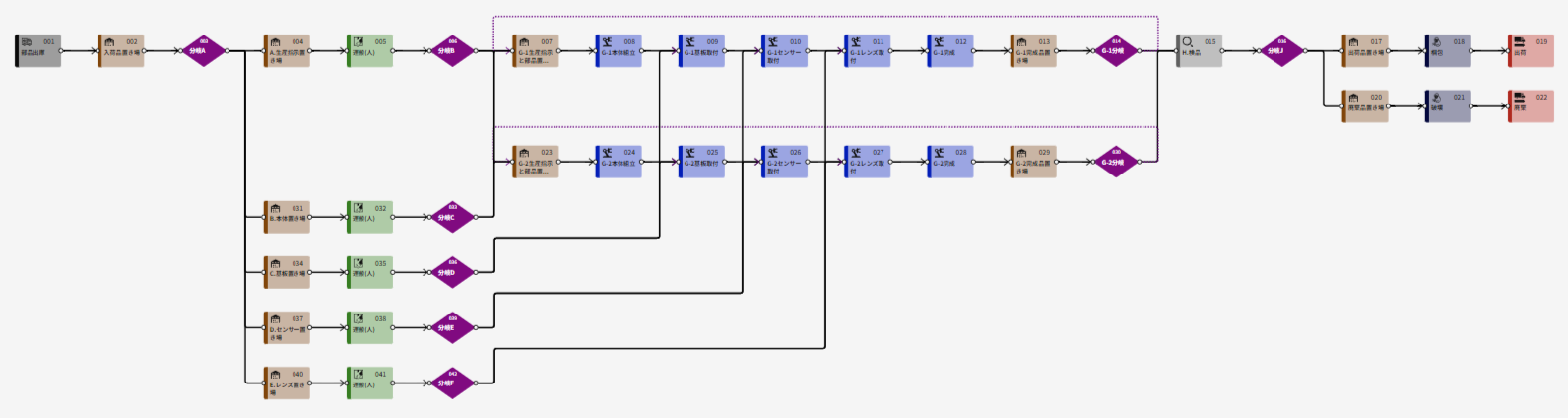
このモデルに、以下の要素を追加します。
- 5つの組立プロセスと1つの検品プロセスを設定し、作業員Aが3つの組立プロセス、作業員Bが2つの組立プロセスと検品プロセスを担当するように変更します。
- 作業員Aと作業員Bはそれぞれ独立して組立作業を行い、作業員Aは作業員Bの作業終了を待たずに進行します。
以下が変更されたモデルとなります。
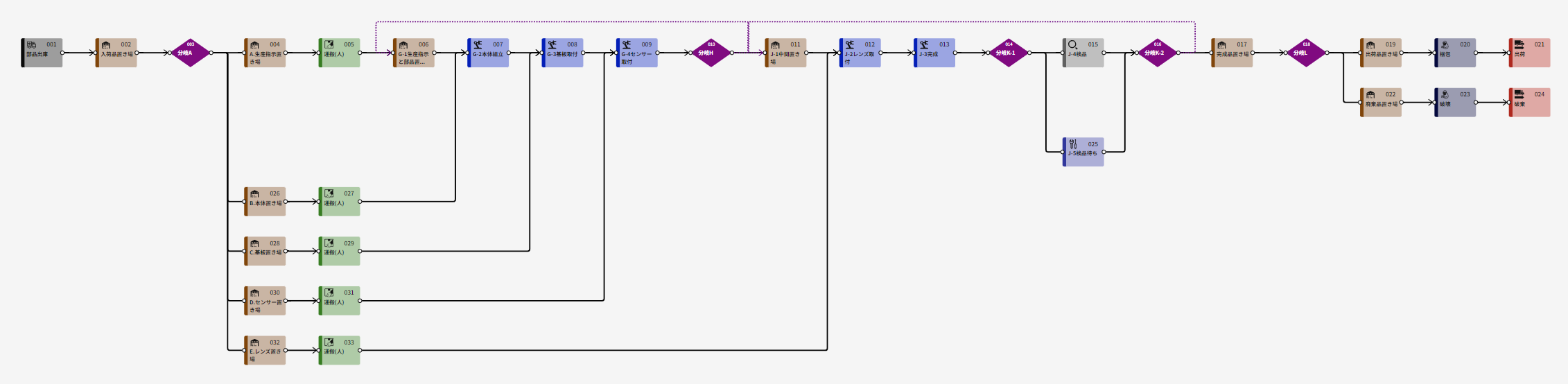
STEP1 プロセス図の作成
プロセスカードを設置し、設定することでモデルを作成して行きます。今回のモデルではフィードバックを利用して作業員Aと作業員Bが担当する作業ブロックを2つ作成します。
入荷プロセス:
プロセス名を「部品出庫」へ変更
置き場プロセス:
プロセス名を「入荷品置き場」へ変更
分岐プロセス:
プロセス名を「分岐」へ変更
分岐先として5つのプロセスを設置:
置き場プロセス:
プロセス名を「A.生産指示置き場」へ変更
以降はA.生産指示へ
置き場プロセス:
プロセス名を「B.本体置き場」へ変更
以降はB.本体(部品)へ
置き場プロセス:
プロセス名を「C.基板置き場」へ変更
以降はC.基板(部品)へ
置き場プロセス:
プロセス名を「D.センサー置き場」へ変更
以降はD.センサー(部品)へ
置き場プロセス:
プロセス名を「E.レンズ置き場」へ変更
以降はE.レンズ(部品)へ
A.生産指示
生産指示の処理を行います。ここから生産セルG-1用と生産セルG-2用の指示をそれぞれ分岐させます。
置き場プロセス(再掲):
プロセス名を「A.生産指示置き場」へ変更
運搬プロセス(人):
特に変更なし
B.本体(部品)
部品の供給を再現する部分です。生産用セルの組立プロセスに接続しますが、接続は組立プロセスの設置後に行ってください。
置き場プロセス(再掲):
プロセス名を「B.本体置き場」へ変更
運搬プロセス(人):
特に変更なし
「G-2本体組立」へ接続
C.基板(部品)
こちらも生産用セルの組立プロセスに接続しますが、接続は組立プロセスの設置後に行ってください。
置き場プロセス(再掲):
プロセス名を「C.基板置き場」へ変更
運搬プロセス(人):
特に変更なし
「G-3基板取付」へ接続
D.センサー(部品)
こちらも生産用セルの組立プロセスに接続しますが、接続は組立プロセスの設置後に行ってください。
置き場プロセス(再掲):
プロセス名を「D.センサー置き場」へ変更
運搬プロセス(人):
特に変更なし
「G-4センサー取付」へ接続
E.レンズ(部品)
こちらも生産用セル後半の組立プロセスに接続しますが、接続は組立プロセスの設置後に行ってください。
置き場プロセス(再掲):
プロセス名を「E.置き場」へ変更
運搬プロセス(人):
特に変更なし
「J-2レンズ取付」へ接続
生産セル前半
置き場プロセス(再掲):
プロセス名を「G-1生産指示と部品置き場」へ変更
「分岐」よりプロセスを接続
組立プロセス:
プロセス名を「G-2本体組立」へ変更
「027運搬(人)」よりプロセスを接続
組立プロセス:
プロセス名を「G-3基板取付」へ変更
「029運搬(人)」よりプロセスを接続
組立プロセス:
プロセス名を「G-4センサー取付」へ変更
「031運搬(人)」よりプロセスを接続
分岐プロセス:
プロセス名を「分岐H」へ変更
分岐先として2つのプロセスを設置:
置き場プロセス:
プロセス名を「中間置き場」へ変更
置き場プロセス(再掲):
プロセス「G-1生産指示と部品置き場」へ接続
置き場プロセス(再掲):
プロセス名を「完成品置き場」へ変更
生産セル後半
組立プロセス:
プロセス名を「J-2レンズ取付」へ変更
「033運搬(人)」よりプロセスを接続
組立プロセス:
プロセス名を「J-3完成」へ変更
分岐プロセス:
プロセス名を「分岐K-1」へ変更
分岐先として2つのプロセスを設置:
検品プロセス:
プロセス名を「J-4検品」へ変更
作業プロセス:
プロセス名を「J-5検品待ち」へ変更
両プロセスは次の「分岐K-2」で合流
分岐プロセス:
プロセス名を「分岐K-2」へ変更
「J-5検品待ち」から合流
分岐先として2つのプロセスを設置:
置き場プロセス:
プロセス「J-1中間置き場」へ接続
置き場プロセス:
プロセス名を「完成品置き場」へ変更
出荷
置き場プロセス:
プロセス名を「完成品置き場」へ変更
分岐プロセス:
プロセス名を「分岐L」へ変更
分岐先として2つのプロセスを設置:
置き場プロセス:
プロセス名を「出荷品置き場」へ変更
以降は出荷品へ
置き場プロセス:
プロセス名を「廃棄品置き場」へ変更
以降は不良品へ
出荷品
置き場プロセス(再掲):
プロセス名を「出荷品置き場」へ変更
加工プロセス:
プロセス名を「梱包」へ変更
出荷プロセス:
特に変更なし
不良品
置き場プロセス(再掲):
プロセス名を「廃棄品置き場」へ変更
加工プロセス:
プロセス名を「破壊」へ変更
出荷プロセス:
プロセス名を「廃棄」へ変更
STEP2 パラメーターの設定
001部品出庫:
詳細設定から入荷するパーツを6種類、図のように設定します。
1つ目:品目「生産指示A」、個数「2個」、入荷間隔「25分」、
2つ目:品目「本体」、個数「8個」、入荷間隔「30分」、
3つ目:品目「基板」、個数「12個」、入荷間隔「30分」、
4つ目:品目「センサー」、個数「12個」、入荷間隔「30分」、
5つ目:品目「レンズ」、個数「8個」、入荷間隔「30分」
002入荷品置き場:
容量を「1000個」と設定
003分岐:
1回あたりの処理時間を「0.5分」、詳細設定を開き、作業員にチェックを入れ人数を「30人」と設定
分岐条件:
条件1:
・対象品目:生産指示A
・送り先:004A.生産指示置き場
条件2:
・対象品目:本体
・送り先:026B.本体置き場
条件3:
・対象品目:基板
・送り先:028C.基板置き場
条件4:
・対象品目:センサー
・送り先:030D.センサー置き場
条件5:
・対象品目:レンズ
・送り先:032E.レンズ置き場
A.生産指示
004A.生産指示置き場:
容量を「1000個」と設定
005運搬(人):
最大運搬量を「10個」、人数「1人」、搬送時間「1分」と設定
B.本体(部品)
部品の供給を再現する部分です。
026B.本体置き場:
容量を「1000個」と設定
027運搬(人):
最大運搬量を「10個」、人数「1人」、搬送時間「1分」と設定
C.基板(部品)
028C.基板置き場:
容量を「1000個」と設定
029運搬(人):
最大運搬量を「10個」、人数「1人」、搬送時間「1分」と設定
D.センサー(部品)
030D.センサー置き場:
容量を「1000個」と設定
031運搬(人):
最大運搬量を「10個」、人数「1人」、搬送時間「1分」と設定
E.レンズ(部品)
032E.レンズ置き場:
容量を「1000個」と設定
033運搬(人):
最大運搬量を「10個」、人数「1人」、搬送時間「1分」と設定
生産セル前半
セルを設置します。生産指示に従ってカメラを生産して行きます。また、作業員1人でのセルでの組み立てを再現するため生産伝票がなければ、組立が進まないようにモデルを設定します。
006G-1生産指示と部品置き場:
容量を「1000個」と設定、
初期仕掛にパーツ名「生産伝票A」、個数「1個」を設定
007G-2本体組立:
1回あたりの処理時間を「1分」と設定
1つ目の対象品目を「本体」、個数を「1個」、
2つ目の対象品目を「生産指示A」、個数を「1個」、
3つ目の対象品目を「生産伝票A」、個数を「1個」、
出力品目を「組立中本体」、個数を「1個」と設定
008G-3基板取付:
1回あたりの処理時間を「2分」と設定
1つ目の対象品目を「組立中本体」、個数を「1個」、
2つ目の対象品目を「基板」、個数を「2個」、
出力品目を「基板取付済本体」、個数を「1個」と設定
009G-4センサー取付:
1回あたりの処理時間を「2分」と設定
1つ目の対象品目を「基板取付済本体」、個数を「1個」、
2つ目の対象品目を「センサー」、個数を「2個」、
出力品目を「センサー取付済本体」、個数を「1個」と設定
010分岐H:
1回あたりの処理時間を「1分」と設定
分岐条件を以下のように設定
分岐条件:
条件1:
・品目:生産伝票A
・送り先:006G-1生産指示と部品置き場
条件2:
・品目:カメラA完成品
・送り先:011J-1中間置き場
生産セル後半
011J-1中間置き場:
容量を「1000個」と設定、
初期仕掛にパーツ名「生産伝票B」、個数「1個」を設定
012J-2レンズ取付:
1回あたりの処理時間を「5分」と設定
1つ目の対象品目を「センサー取付済本体」、個数を「1個」、
2つ目の対象品目を「レンズ」、個数を「1個」、
3つ目の対象品目を「生産伝票B」、個数を「1個」、
出力品目を「レンズ取付済本体」、個数を「1個」と設定
013J-3完成:
1回あたりの処理時間を「5分」と設定、
対象品目を「レンズ取付済本体」、個数を「1個」、
1つ目の出力品目を「カメラA完成品」、個数を「1個」、
2つ目の出力品目を「生産伝票A」、個数を「1個」と設定
014分岐K-1:
1回あたりの処理時間を「0分」と設定
分岐条件を以下のように設定
分岐条件:
条件1:
・品目:生産伝票B
・送り先:025J-5検品待ち
条件2:
・品目:カメラA完成品
・送り先:015J-4検品
015J-4検品:
1回あたりの処理時間を「10分」、不良品率を0.1%と設定
025J-5検品待ち:
1回あたりの処理時間を「10分」、
対象品目を「生産伝票B」、個数を「1個」と設定
016分岐K-2:
1回あたりの処理時間を「1分」と設定
分岐条件を以下のように設定
分岐条件:
条件1:
・品目:生産伝票B
・送り先:011J-1中間置き場
条件2:
・品目:カメラA完成品
・送り先:017完成品置き場
検品と出荷
017完成品置き場:
容量を「1000個」と設定、
018分岐L:
1回あたりの処理時間を「1分」と設定
分岐条件を以下のように設定
分岐条件:
条件1:
・対象品目:正常:カメラA完成品
・送り先:019出荷品置き場
条件2:
・対象品目:不良:カメラA完成品
・送り先:022廃棄品置き場
出荷品
019出荷品置き場:
容量を「1000個」と設定
020梱包:
1回あたりの処理時間を「1分」と設定、
対象品目を「カメラA完成品」、個数を「1個」、
出力品目を「出荷品」、個数を「1個」と設定
021出荷:
特に変更なし
不良品
022廃棄品置き場:
容量を「1000個」と設定
023破壊:
1回あたりの処理時間を「1分」と設定、
対象品目を「カメラA完成品」、個数を「1個」、
出力品目を「破棄品」、個数を「1個」と設定
024廃棄:
特に変更なし
シミュレーションと分析
モデルを作成したら、シミュレーションを実行します。今回も前回の記事と同様に、シミュレーション時間を480分(8時間)に設定します。シミュレーションが終了すると、以下の画面が表示されます。*なお、パーツの仕分けなどに乱数が含まれるため、若干の誤差が生じる可能性があります。
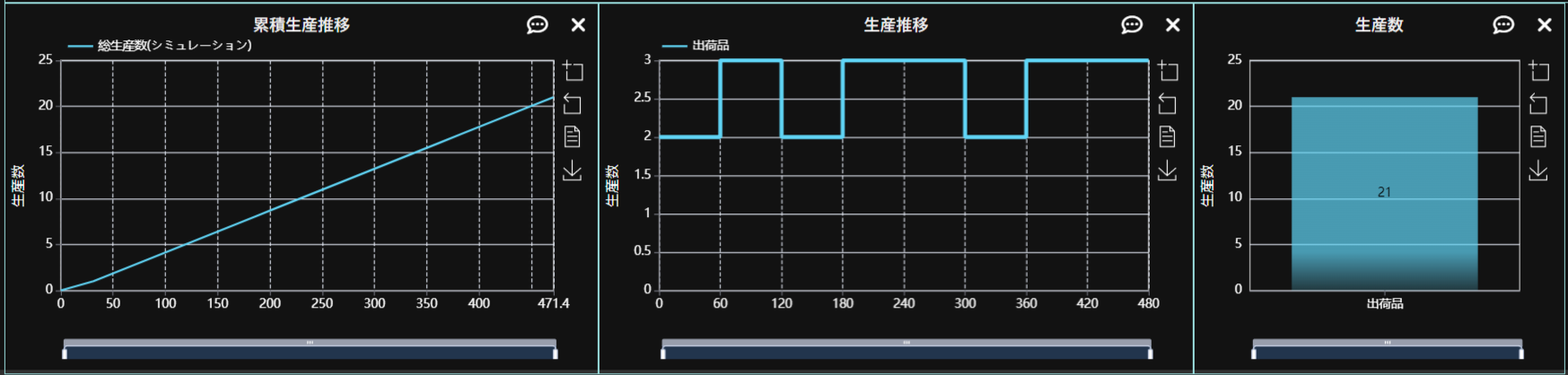
シミュレーション結果を確認した後は、どこかにボトルネックがないか、「ステータス推移」と「011J-1中間置き場」の容量をチェックしてみましょう。
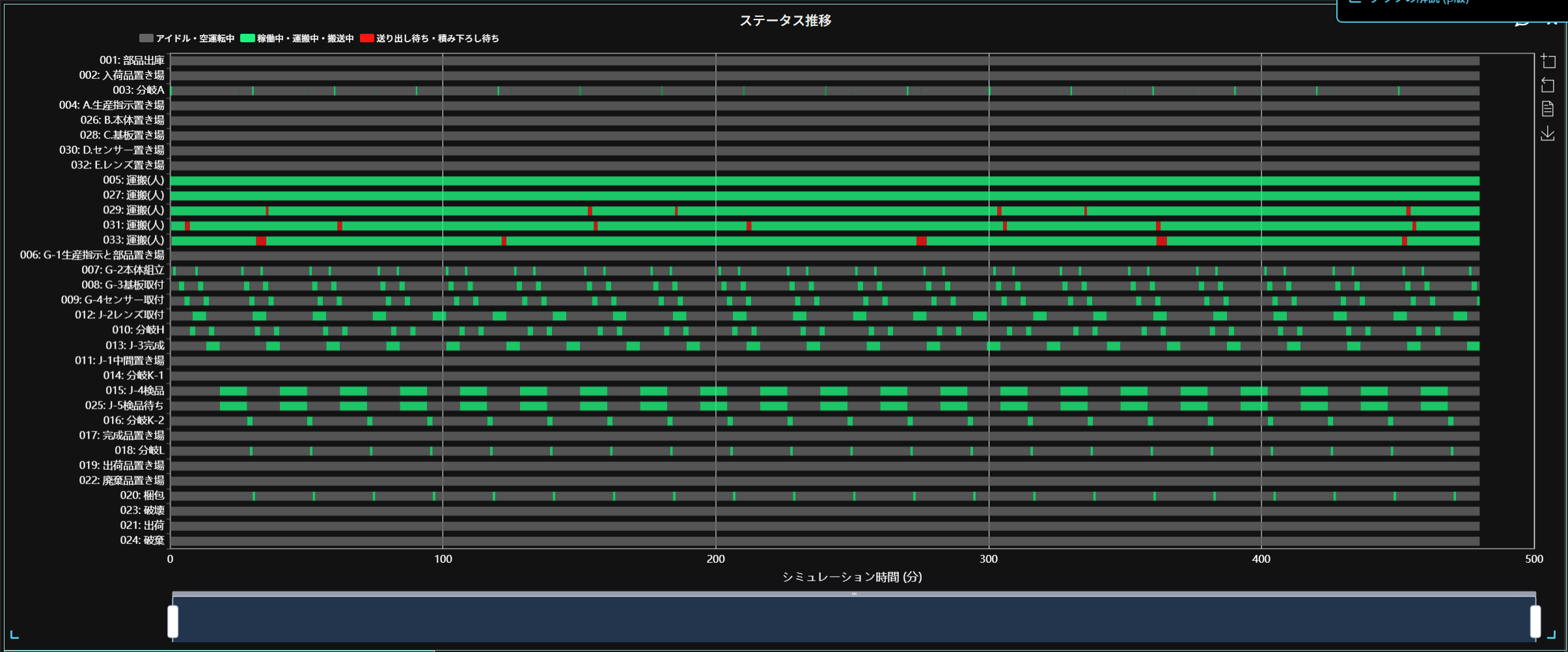
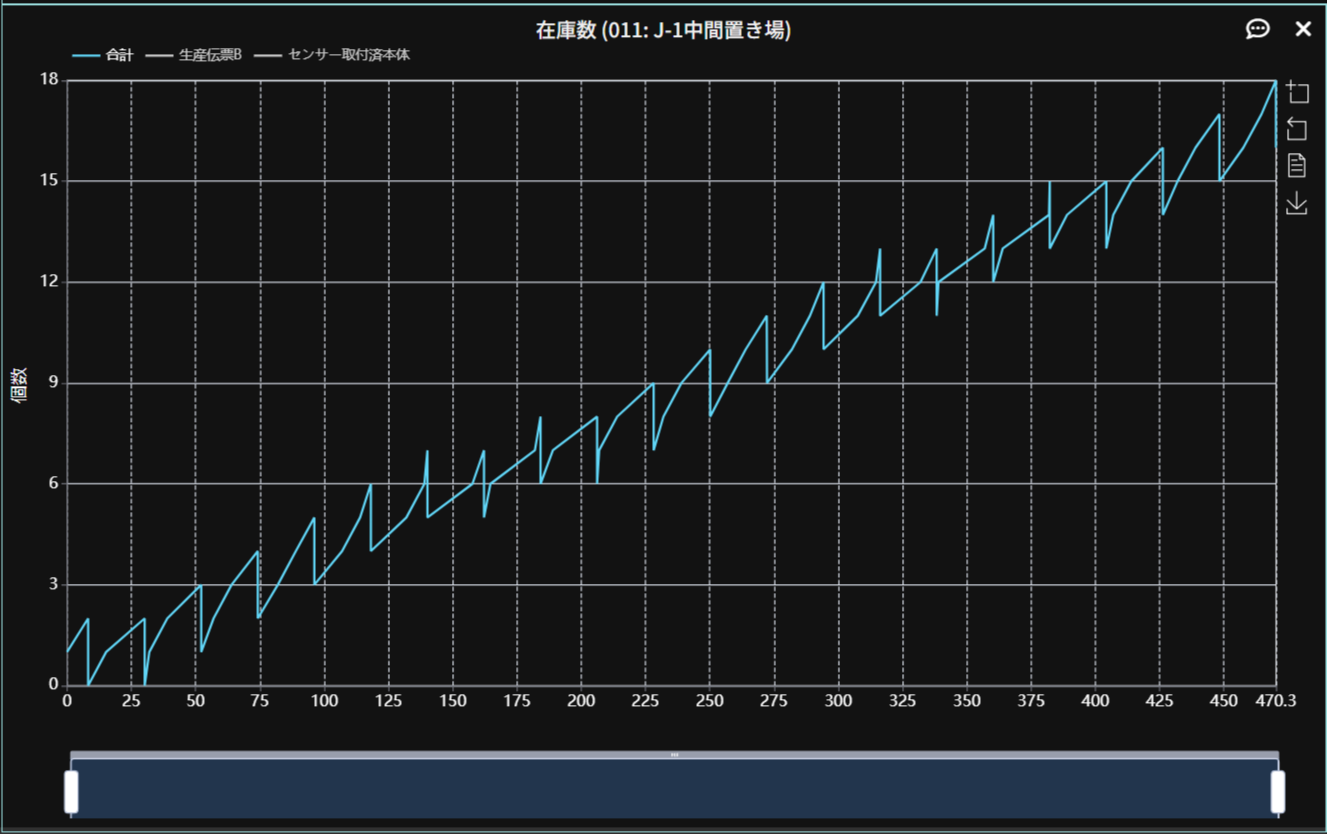
「011J-1中間置き場」の容量を見ると、在庫量が右肩上がりで増加しており、作業員Bが担当するセルの下流工程で処理が追いついていないことがわかりました。このボトルネックを解消するためにモデルを変更してみましょう。
モデルの再変更
「011J-1中間置き場」に溜まった在庫を消費するため、作業員Bが担当していた下流工程に新たに作業員Cが担当するラインを追加し、下流工程を並列で動作させてみましょう。
以下のようにモデルを変更します。
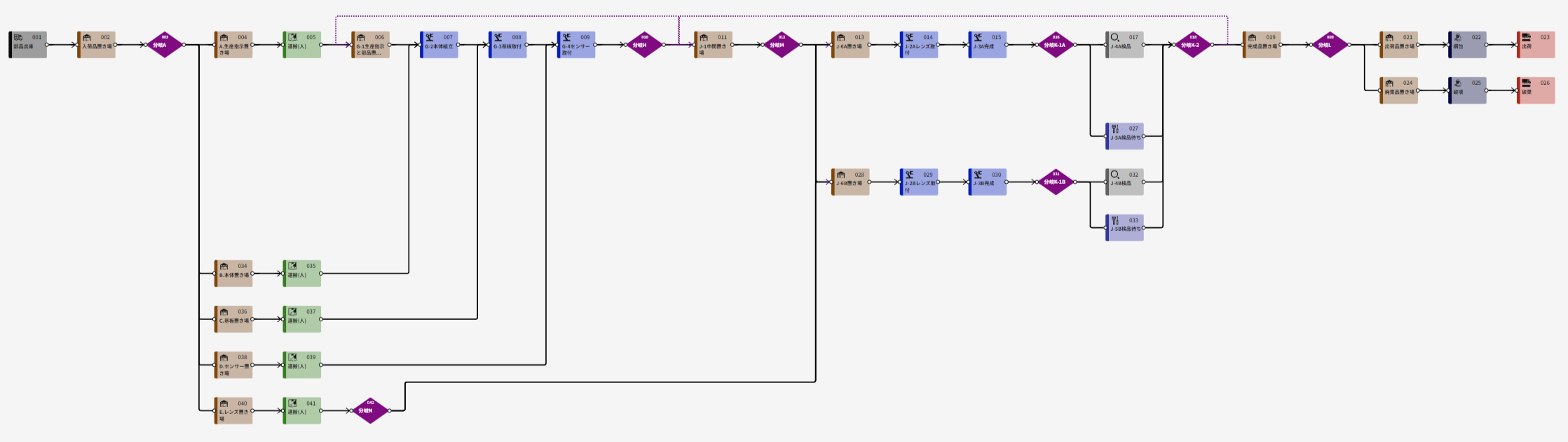
この変更前は、「011J-1中間置き場」に初期仕掛けとして生産伝票Bを1個配置し、作業員Bが担当する後半部分の生産をコントロールしていました。しかし、新たに作業員Cが加わったため、置き場に初期仕掛け(生産伝票B、生産伝票C)を配置するなど、プロセスの設定を変更します。これにより、作業員Bと作業員Cが担当するラインで、それぞれ1個ずつ製品が作られるように調整されます。
シミュレーション結果は以下の通りとなり、生産量は最初の18個と比べてほぼ倍の33個になりました。
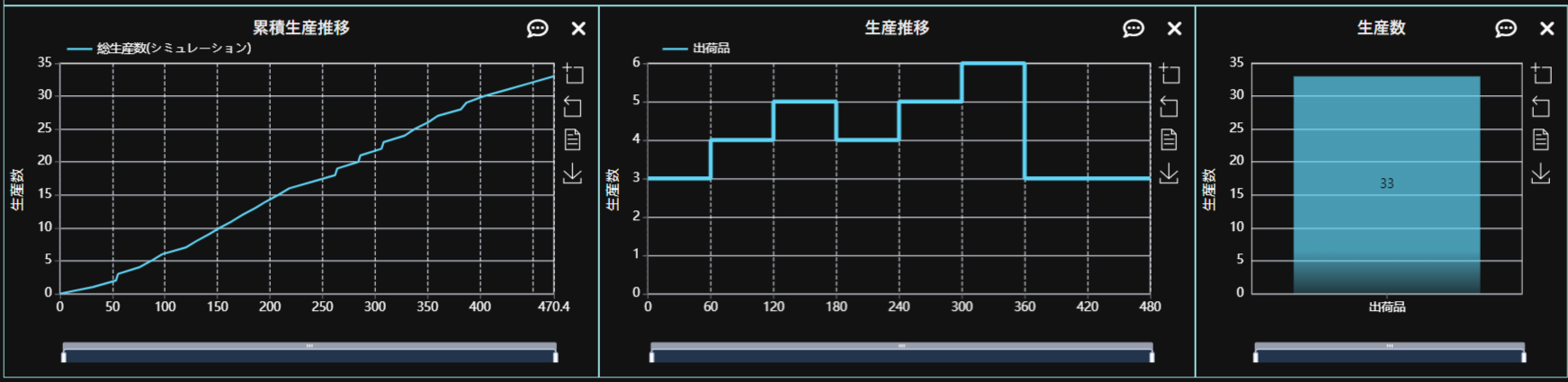
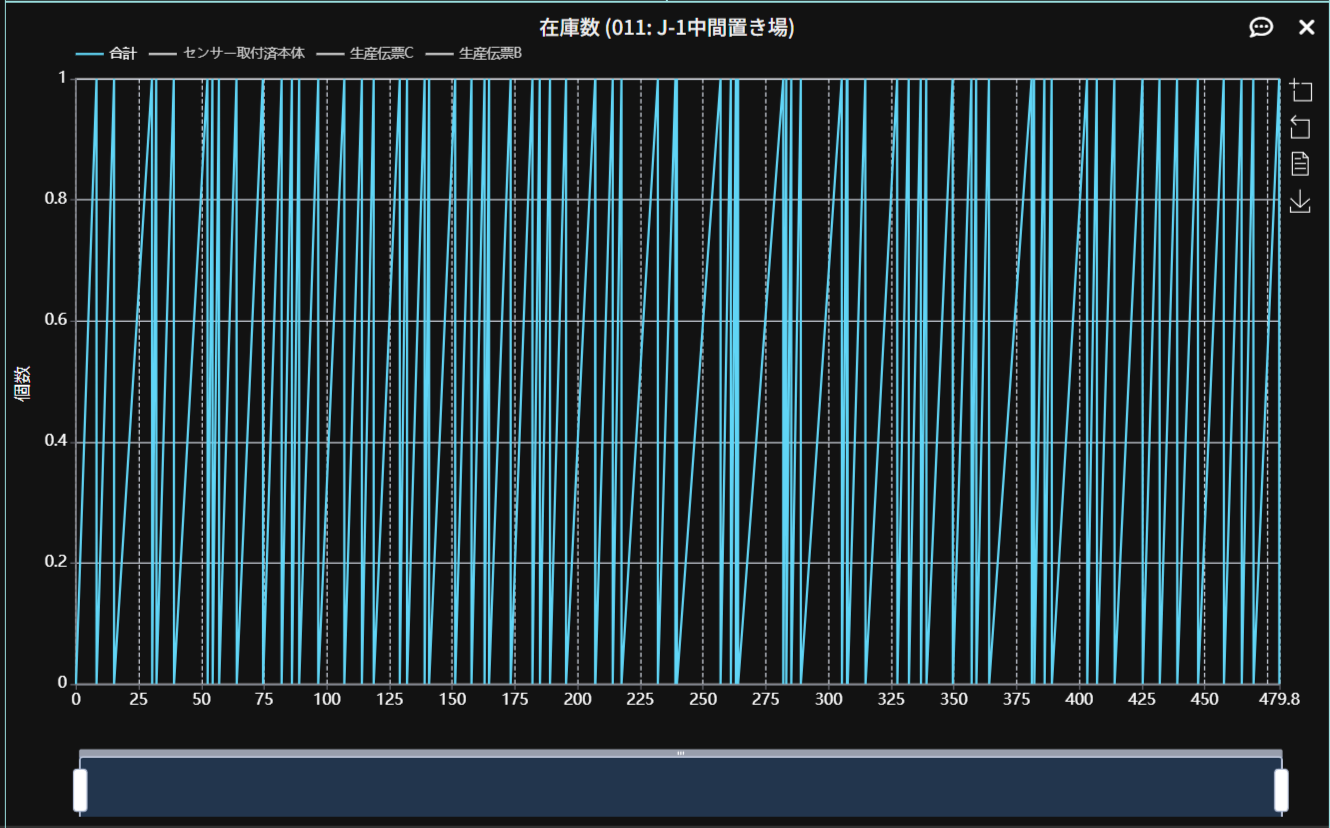
「011J-1中間置き場」の在庫の滞留が無くなったことも分かりました。
「ステータス推移」を確認すると、作業員Bと作業員Cが担当するラインで製品が並行して組み立てられるようになったことがわかります。また、前半の材料入力に合わせて、それぞれのラインで1個ずつ製品が作成されるようになっていることも確認できます。
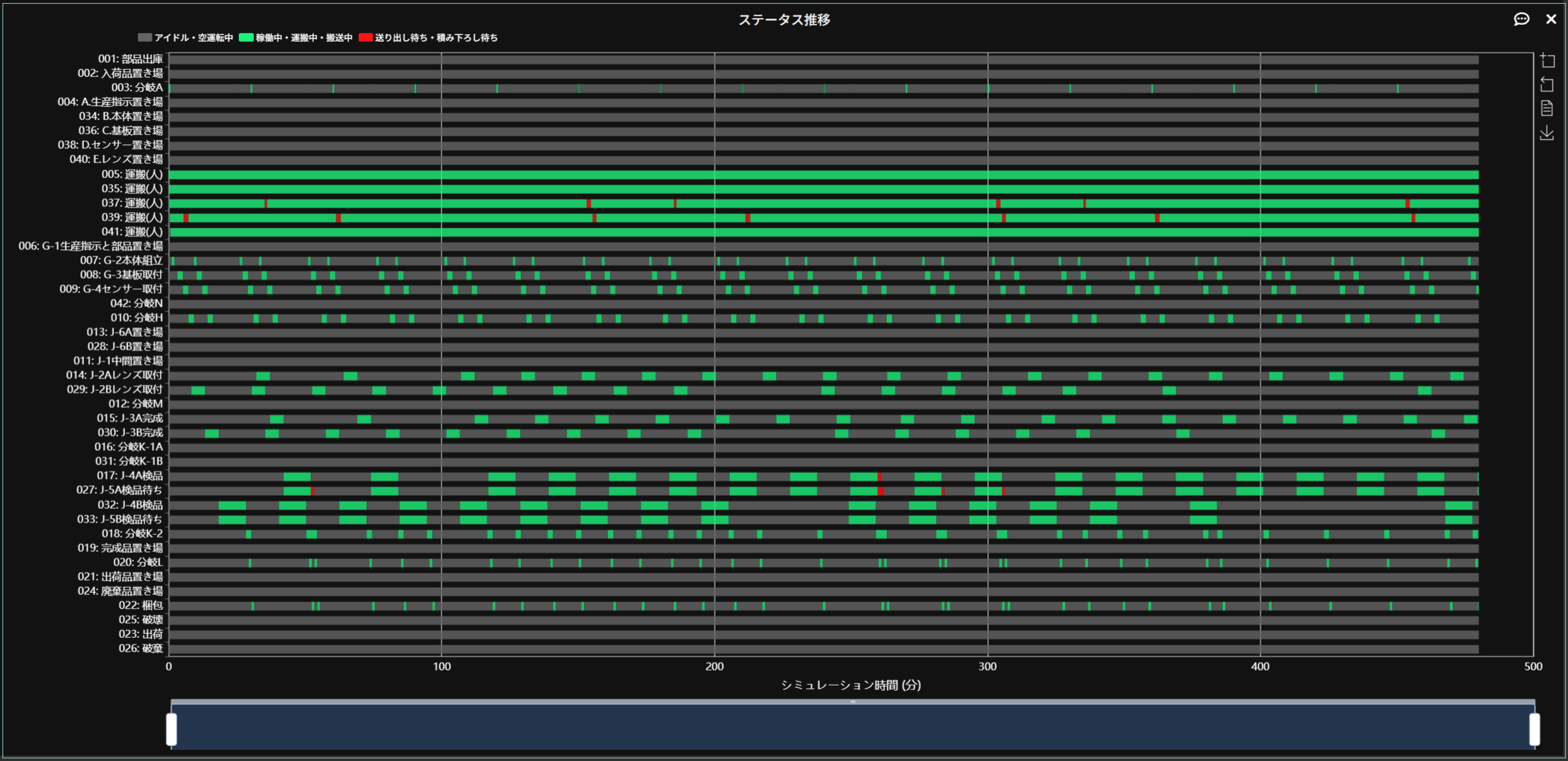
まとめ
今回は、セル生産方式を改良し、複数人で分業するセル生産をシミュレーション(見える化)のモデルを作成しました。このように、assimeeでは既存のモデルを基に、プロセスの追加や組み換えなど、さまざまな変更を容易に行うこともできます。