概要
このチュートリアルでは、ブース生産方式のモデル作成し、シミュレーションによる見える化を行う手順について解説します。ブース生産方式とは、「ブース」と呼ばれる作業エリアを設け、あらかじめ用意された生産キットや工具を使用して製品の一部または全体を生産する方式です。製品や工程に応じた異なるブース、生産キット、スキルを持つ作業人員を用意することで、多品種少量生産が求められる現代において、柔軟な生産変更や作業効率の向上が期待できます。一方で、ブース間の搬送作業の煩雑化やスキルに応じた人員管理の必要性、ブース設置に広い作業スペースが求められるなどの課題もあります。
モデル
以下が、今回使用するブース生産方式のモデルとなります。
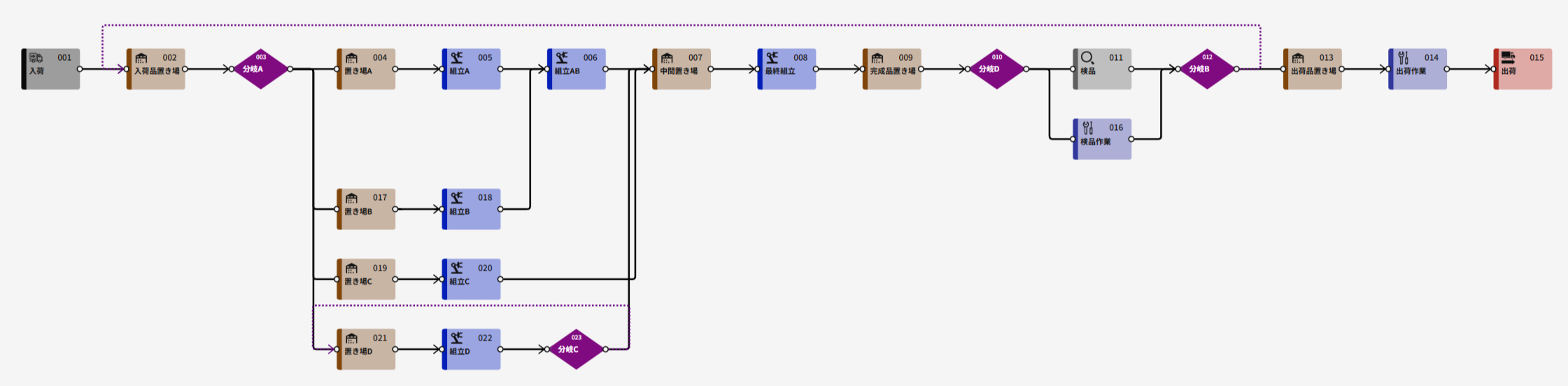
4人一組で作業を行うブースを考え、ブース内の組立プロセスで作業員が以下のような作業を担当します。
前半工程(括弧内は総所要時間)
組立A:作業員Aが組立キットAからパーツAを1個組立(15分)
組立B:作業員Bが組立キットBからパーツBを1個組立(20分)
組立AB:作業員Aと作業員BがパーツAとパーツBからパーツABを1個組立(30分)
組立C:作業員Cが組立キットCからパーツCを1個組立(30分)
組立D:作業員Dが組立キットDからパーツDを2個組立(10分×2)
後半工程(括弧内は総所要時間)
最終組み立て:4人の作業員でパーツAB1個、C1個、D2個から完成品を組立(50分)
検品:4人の作業員で検品(10分)
前半工程では、4人の作業員がそれぞれ自分の担当するパーツを組み立て、パーツ同士を組み合わせ(作業員AとB)、複数のパーツを準備する工程(作業員D)を行います。後半工程では、4人の作業員が協力して完成品1個を組み立て、検品を行います。完成品は完成品置き場に移され、その後出荷されます。
また、このモデルではセル生産方式のようにループを活用し、各作業員が完成品に必要なパーツを1つずつ作成するプロセスを再現しています。
STEP1 プロセス図の作成
プロセスカードを設置し、設定することでモデルを作成して行きます。今回のモデルではフィードバックを利用して作業員Aと作業員Bが担当する作業ブロックを2つ作成します。
入荷プロセス:
特に変更なし
置き場プロセス:
プロセス名を「入荷品置き場」へ変更
後述する「分岐B」からループが接続
分岐プロセス:
プロセス名を「分岐A」へ変更
分岐先として4つのプロセスを設置:
置き場プロセス:
プロセス名を「置き場A」へ変更
以降は組立ABで解説
置き場プロセス:
プロセス名を「置き場B」へ変更
以降は組立ABで解説
置き場プロセス:
プロセス名を「置き場C」へ変更
以降は組立Cで解説
置き場プロセス:
プロセス名を「置き場D」へ変更
以降は組立Dで解説
組立AB
置き場プロセス(再掲):
プロセス名を「置き場A」へ変更
組立プロセス:
プロセス名を「組立A」へ変更
置き場プロセス(再掲):
プロセス名を「置き場B」へ変更
組立プロセス:
プロセス名を「組立B」へ変更
組立プロセス:
「組立A」と「組立B」から接続
プロセス名を「組立AB」へ変更
置き場プロセス:
プロセス名を「中間置き場」へ変更
組立C
置き場プロセス:(再掲)
プロセス名を「置き場C」へ変更
組立プロセス:
プロセス名を「組立C」へ変更
「中間置き場」へ接続
組立D
置き場プロセス:
プロセス名を「置き場D」へ変更
後述する「分岐C」からループで接続
組立プロセス:
プロセス名を「組立D」へ変更
分岐プロセス:
プロセス名を「分岐C」へ変更
「置き場D」から接続
分岐先として2つのプロセスへ接続:
置き場プロセス:
プロセス名を「中間置き場」へ変更
以降は最終組立で解説
置き場プロセス(再掲):
「置き場D」へループで接続
最終組立
置き場プロセス(再掲):
プロセス名を「中間置き場」へ変更
組立プロセス:
プロセス名を「最終組立」へ変更
置き場プロセス:
プロセス名を「完成品置き場」へ変更
分岐プロセス:
プロセス名を「分岐D」へ変更
分岐先として2つのプロセスを設置:
検品プロセス:
プロセス名を「検品」へ変更
作業プロセス:
プロセス名を「検品作業」へ変更
分岐プロセス:
プロセス名を「分岐B」へ変更
「検品」と「検品作業」から接続
分岐先として2つのプロセスを設置:
置き場プロセス:
プロセス名を「出荷品置き場」へ変更
置き場プロセス(再掲):
「入荷品置き場」へループで接続
出荷
置き場プロセス(再掲):
プロセス名を「出荷品置き場」へ変更
作業プロセス:
プロセス名を「出荷作業」へ変更
出荷プロセス:
特に変更なし
STEP2 パラメーターの設定
001入荷:
詳細設定から入荷するパーツを4種類、以下のように設定します。
1つ目:品目「組立キットA」、個数「1個」、入荷間隔「120分」、
2つ目:品目「組立キットB」、個数「1個」、入荷間隔「120分」、
3つ目:品目「組立キットC」、個数「1個」、入荷間隔「120分」、
4つ目:品目「組立キットD」、個数「1個」、入荷間隔「120分」
002入荷品置き場:
容量を「1000個」と設定
初期仕掛に以下の4品目を設定
作業員A、1個
作業員B、1個
作業員C、1個
作業員D、1個
003分岐A:
1回あたりの処理時間を「0分」と設定
以下の8つの分岐条件を設定
分岐条件:
条件1:
・対象品目:組立キットAと作業員A
・送り先:004置き場A
条件2:
・対象品目:組立キットBと作業員B
・送り先:017置き場B
条件3:
・対象品目:組立キットCと作業員C
・送り先:019置き場C
条件4:
・対象品目:組立キットDと作業員D
・送り先:021置き場D
組立AB
004置き場A:
容量を「1000個」と設定
005組立A:
1回あたりの処理時間を「15分」と設定
対象品目:「作業員A」1個、「組立キットA」1個
出力品目:「作業員A」1個、「パーツA」1個
017置き場B:
容量を「1000個」と設定
018組立B:
1回あたりの処理時間を「20分」と設定
対象品目:「作業員B」1個、「組立キットB」1個
出力品目:「作業員B」1個、「パーツB」1個
006組立AB:
1回あたりの処理時間を「30分」と設定
対象品目:「作業員A」1個、「パーツA」1個、「作業員B」1個、「パーツB」1個
出力品目:「作業員A」1個、「作業員B」1個、「パーツAB」1個
組立C
019置き場C:
容量を「1000個」と設定
020組立C:
1回あたりの処理時間を「30分」と設定
対象品目:「作業員C」1個、「組立キットC」1個
出力品目:「作業員C」1個、「パーツC」1個
組立D
021置き場D:
容量を「1000個」と設定
022組立D:
1回あたりの処理時間を「10分」と設定
パターン1:
対象品目:「作業員D」1個、「組立キットD」1個
出力品目:「作業伝票D」1個、「パーツD」1個
パターン2:
対象品目:「作業伝票D」1個、「組立キットD」1個
出力品目:「作業員D」1個、「パーツD」1個
023分岐C:
1回あたりの処理時間を「0分」と設定
以下の2つの分岐条件を設定
分岐条件:
条件1:
・対象品目:作業伝票
・送り先:021置き場D
条件2:
・対象品目:パーツDと作業員D
・送り先:007置き場
最終組立
007中間置き場:
容量を「1000個」と設定
008最終組立:
1回あたりの処理時間を「50分」と設定
対象品目:「作業員A」1個、「作業員B」1個、「作業員C」1個、「作業員D」1個、「パーツAB」1個、「パーツC」1個、「パーツD」2個
出力品目:「作業員A」1個、「作業員B」1個、「作業員C」1個、「作業員D」1個、「完成品」1個
009完成品置き場:
容量を「1000個」と設定
010分岐D:
1回あたりの処理時間を「0分」と設定
以下の2つの分岐条件を設定
分岐条件:
条件1:
・対象品目:完成品
・送り先:011検品
条件2:
・対象品目:残り(「作業員A」、「作業員B」、「作業員C」、「作業員D」)
・送り先:016検品作業
011検品:
1回あたりの処理時間を「10分」、不良品率「0%」と設定
016検品作業:
1回あたりの処理時間を「10分」と設定
対象品目:「作業員A」1個、「作業員B」1個、「作業員C」1個、「作業員D」1個
012分岐B:
1回あたりの処理時間を「0分」と設定
以下の2つの分岐条件を設定
分岐条件:
条件1:
・対象品目:完成品
・送り先:013出荷品置き場
条件2:
・対象品目:残り(「作業員A」、「作業員B」、「作業員C」、「作業員D」)
・送り先:002入荷品置き場
出荷
013出荷品置き場D:
容量を「1000個」と設定
014出荷作業:
1回あたりの処理時間を「5分」と設定
対象品目:「完成品」1個
015出荷:
特に変更なし
シミュレーションと分析
上記のモデルが完成したらシミュレーションを行います。今回のシミュレーションは8時間に相当する480分で行いました。シミュレーションが終了すると以下の画面が表示されます。
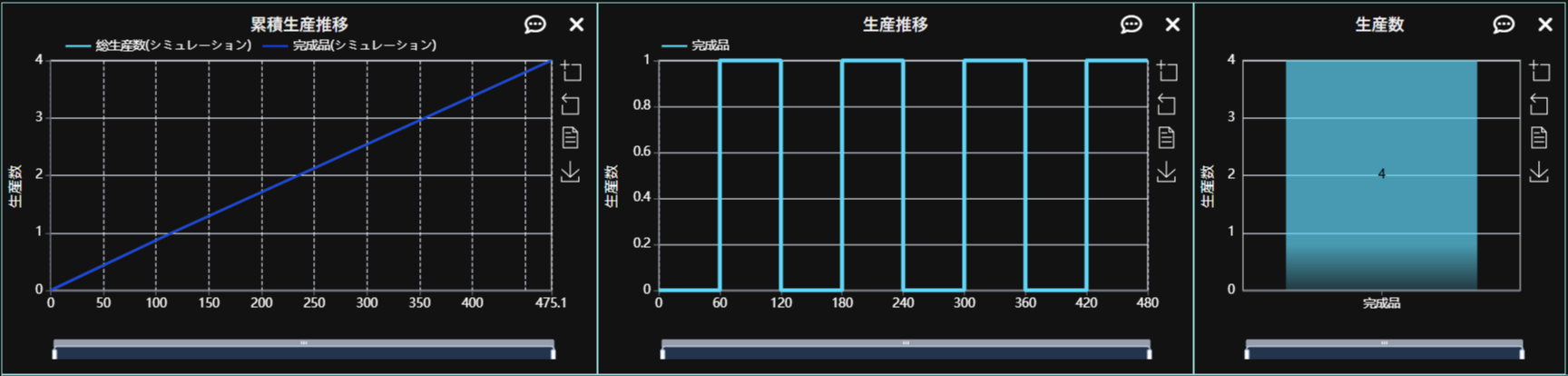
今回のモデルではおよそ60分で作業員4人がここに作業を行う前段作業と、60分で4人で1つの完成品を組み上げる後段作業がありますが、下図のようにステータス推移を確認するとそのプロセスが再現されていることが分かります。
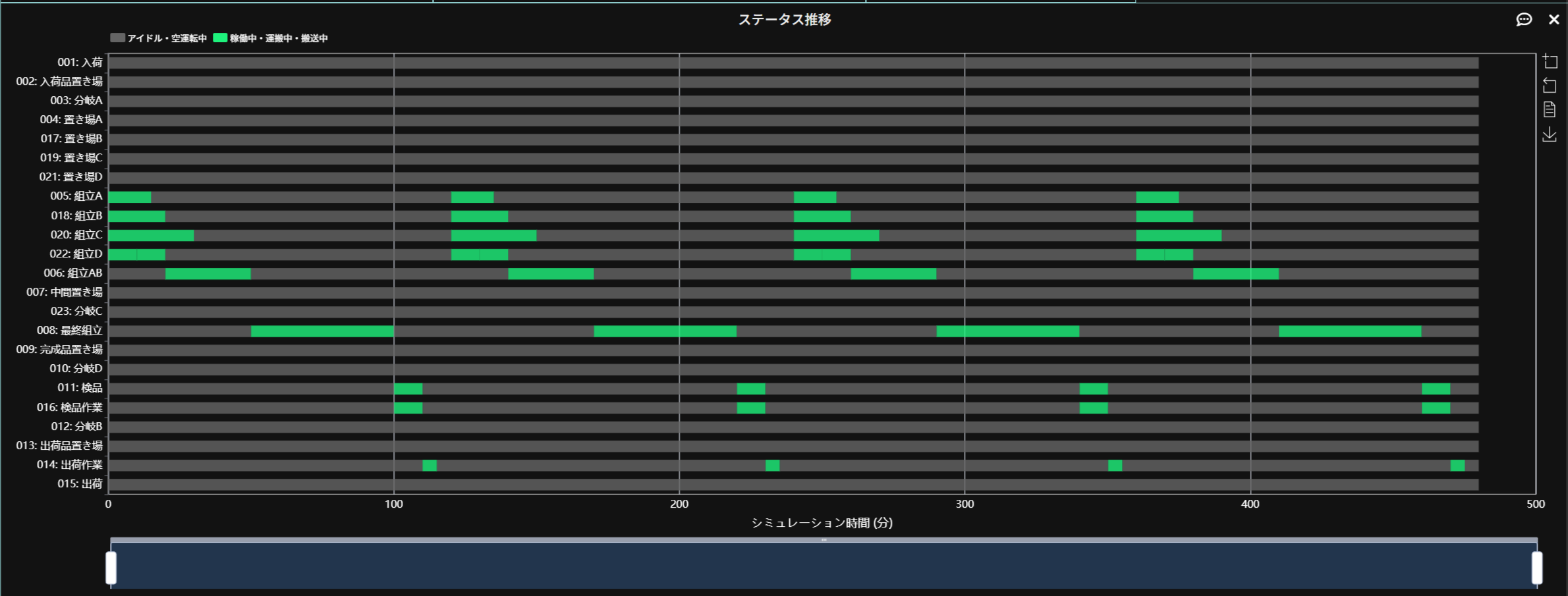
また、ステータス推移の詳細を確認することで、それぞれの作業員が、完成品が組み上がるまでにどのくらいの作業を行っているのかを確認することも出来ます。

今回の設定では、作業員C(作業量30分)およびD(作業量20分)の作業量がAやBと比べて少なく、それぞれ30分ほどの待ち時間があることが見える化されます。この可視化により、4人が必要な最終組立作業に問題がなければ、作業員CとDの作業を1人にまとめることや、他の作業が必要となった際に作業員CやDに優先的に作業を割り振るなどの、生産計画を視覚的に検討することが可能です。
今回のケースは比較的単純なモデルですが、作業員の担当工程がより複雑であっても、各作業の見える化を通じて、生産計画を効率的に検討することが可能です。
まとめ
今回のチュートリアルではブース型セル生産方式のモデルを作成し、シミュレーション結果を確認し、分析を行いました。assimeeでは、今回行ったように既存の生産ラインや変更後の生産ラインのモデルを作成し、シミュレーション結果を分析することで、生産計画を検討することが容易に可能です。