概要
タクトタイムとは、生産工程で製品1個を生産する際の基準となる時間です。これは、ラインの稼働時間を1日に必要な生産数で割ることで計算されます。サイクルタイムが生産プロセスを中心に考える指標であるのに対し、タクトタイムは顧客や市場の要求を基準にした指標です。
本記事では、生産ラインを再現し、そのタクトタイムをシミュレーションで求めたサイクルタイムと比較することで、需要に基づいた生産計画の立案していく方法を解説します。
モデルと想定
以下の図が今回使用するモデルとなります。置き場と加工、出荷作業からなる工程を再現した直線的なモデルとなります。

このモデルでは、1個の部品から1個の製品を組み立てます。今回は、2000個の製品を納品するために、2000個の部品を一度だけ入荷する条件でシミュレーションを行います(不良品率は考慮しないものとします)。
この記事では以下の手順で生産計画を検討します:
- 生産数の確認
- サイクルタイムとタクトタイムの比較
- ボトルネック箇所の特定
- 生産能力向上のための施策の実施
- 再度のシミュレーション
これらを通じて、効率的な生産計画の立案方法を検討していきましょう。
シミュレーションと分析
まず、稼働時間8時間(480分)を想定してシミュレーションを行います。シミュレーションの結果は以下のようになります。
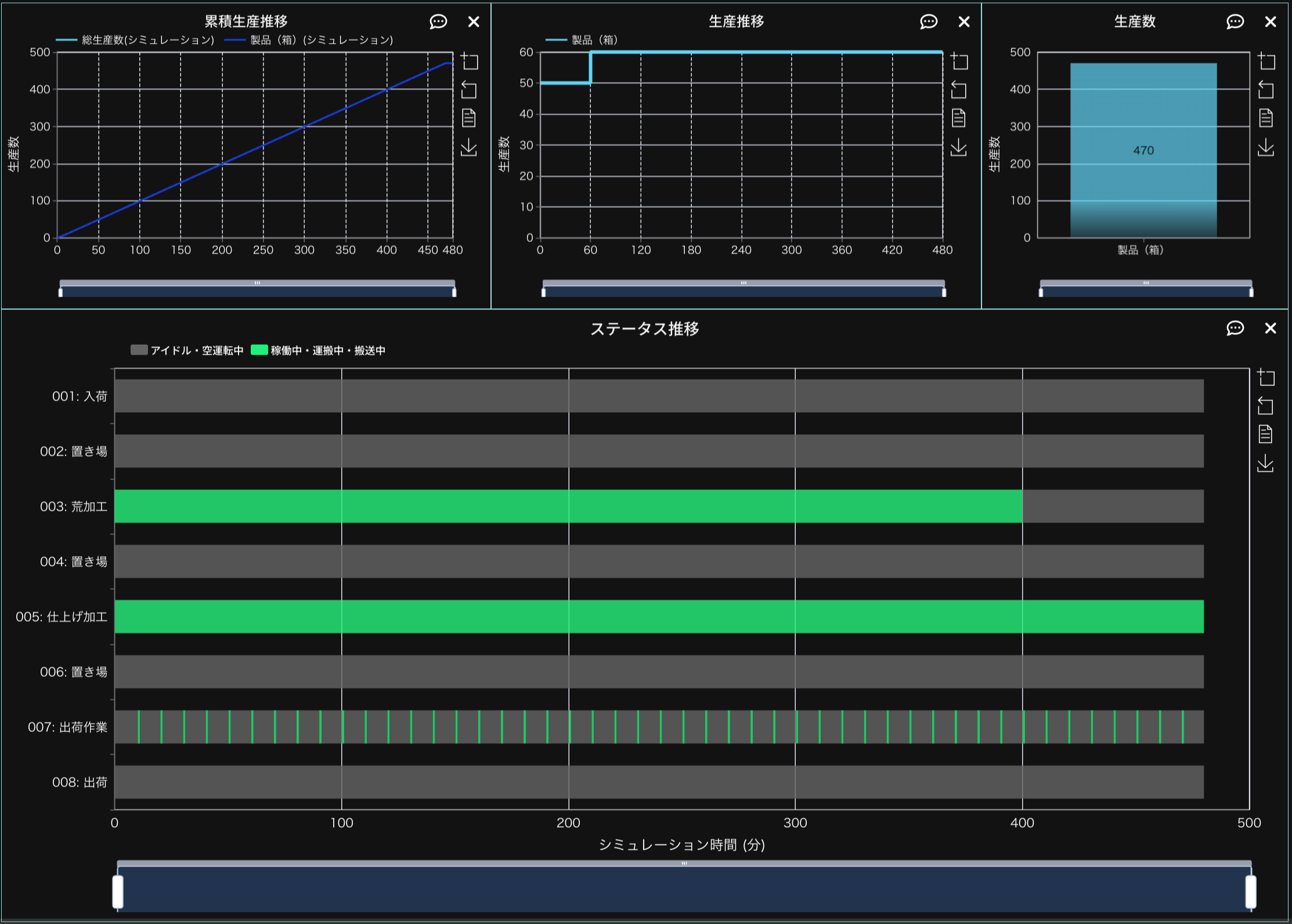
480分間で470個の製品が出荷されているため、このラインのサイクルタイムは1.02分となります。一方、タクトタイムは480分 ÷ 2000個 = 0.24分となり、顧客の要求を満たすためにはサイクルタイムを半分以下にする必要があることがわかります。次に、このラインのボトルネックがどこにあるかを確認してみましょう。
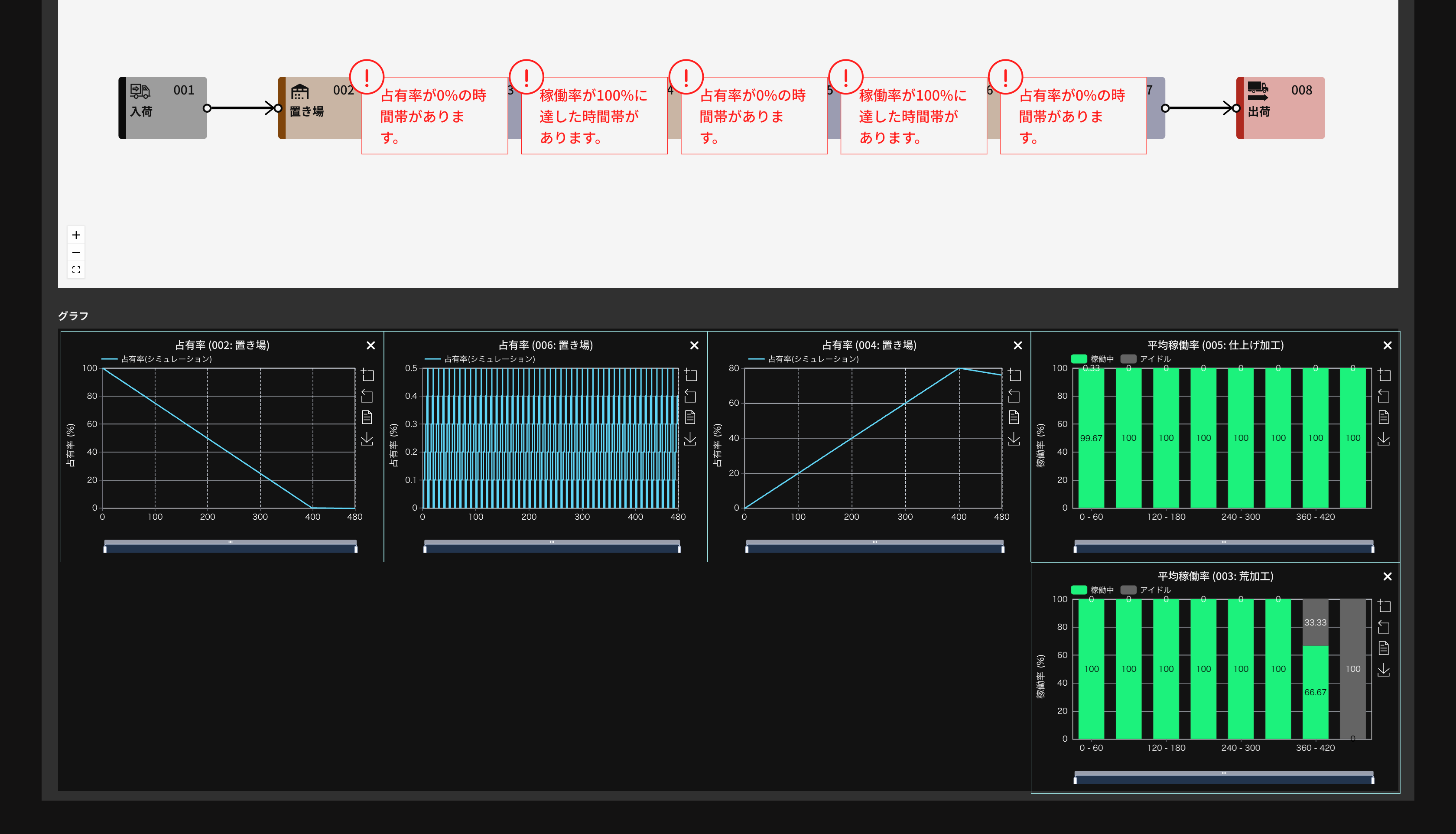
ボトルネック特定機能と、先ほどのシミュレーション結果のステータス推移グラフを分析したところ、005仕上げ加工が稼働率100%の時間が続いているため、ボトルネックであると考えられます。一方、003荒加工は稼働途中で2000個の加工が完了しており、稼働率が100%でもボトルネックとなる可能性は低いと判断できます。
そこで、005仕上げ加工をボトルネックとして改善策を検討します。
現実的にはサイクルタイムを大幅に削減するのは困難ですが、005仕上げ加工の内部ラインを大幅に増強することで処理時間を短縮できると仮定します。具体的には、現在1分の処理時間を、タクトタイムと同じになるように0.24分に変更します。その上で、再度シミュレーションを実施し、結果を確認してみましょう。
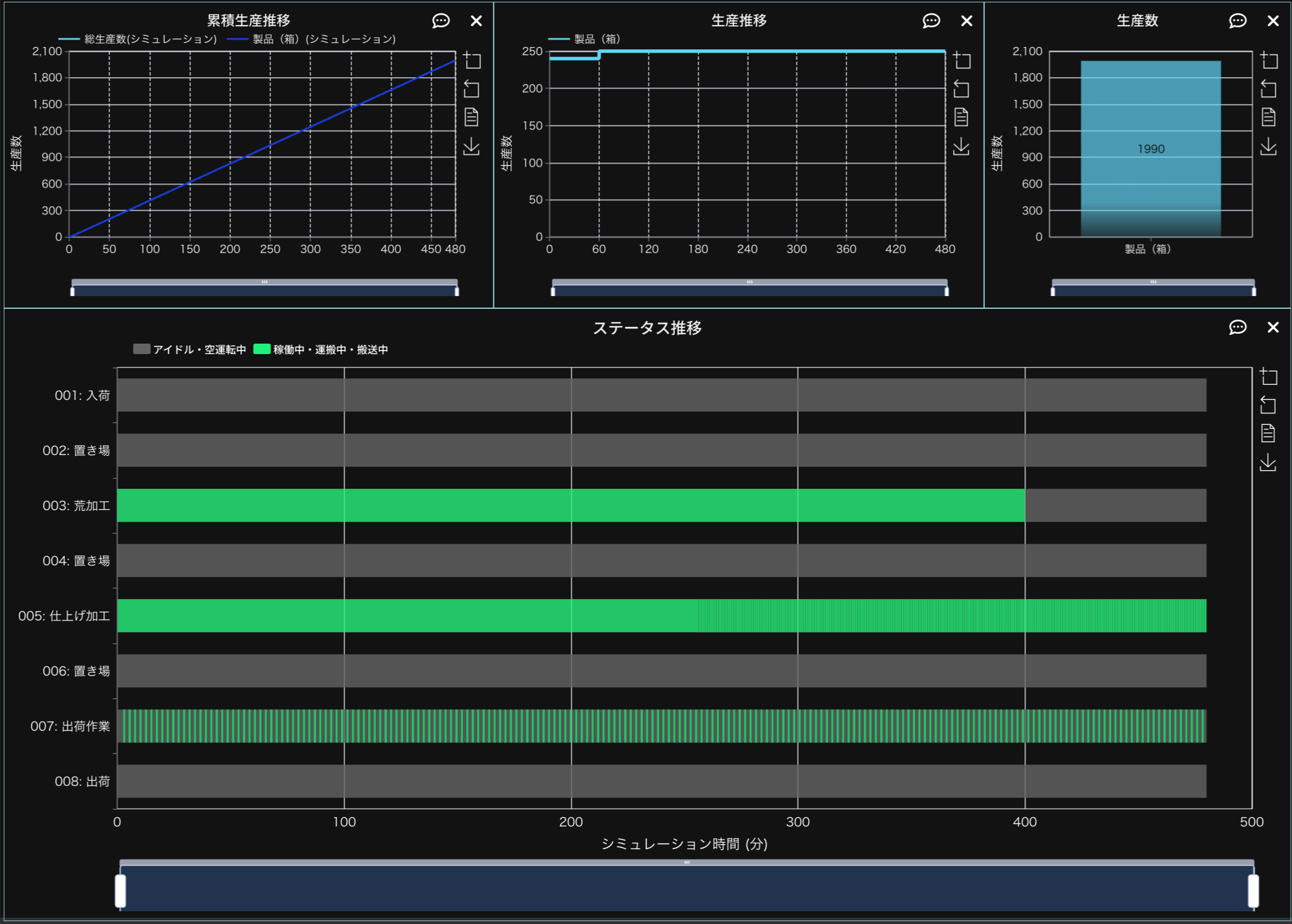
シミュレーションの結果、480分の時点で1990個が出荷され、サイクルタイムは0.241分となりました。これにより、2000個という出荷目標をほぼ達成できていることがわかります。わずかな差異は、生産ラインの立ち上がり時間によるものと考えられます。このように、ボトルネックを特定し、適切な対策を講じる手順を繰り返すことで、生産目標を効率的に達成することが可能です。
まとめ
今回は、シミュレーションを活用して、タクトタイムとサイクルタイムの短縮を妨げる要因を「見える化」する方法について解説しました。例では極端なケースを用いましたが、assimeeを使って生産ラインをモデル化することで、さまざまな条件下でシミュレーションを行い、生産計画を立案することが可能です。さらに、パラメーターを変更しながらシミュレーションを繰り返すことで、より現実的で効率的な生産計画を検討できます。また、ネットワーク環境さえ整っていれば、シミュレーションを誰でもどこからでも簡単に実施できるため、生産計画業務の効率化や平準化にも大いに役立ちます。
assimeeでは、実際の製造プロセスをモデル化し、シミュレーションすることで、プロセスの見える化や潜在的な課題の洗い出しを行うことができます。製造プロセスのデジタル化や課題解決でお悩みの方は、ぜひお問い合わせください。