概要
この記事では、石油精製所のモデルを作成し、シミュレーションを行います。主眼は、assimeeを使用して連続的な反応をシミュレーションすること、複数の分岐、上流側へのフィードバック、プロセスの合流を含む大規模で複雑なモデルを作成することです。今回作成するモデルは以下のようになります。
モデルの作成
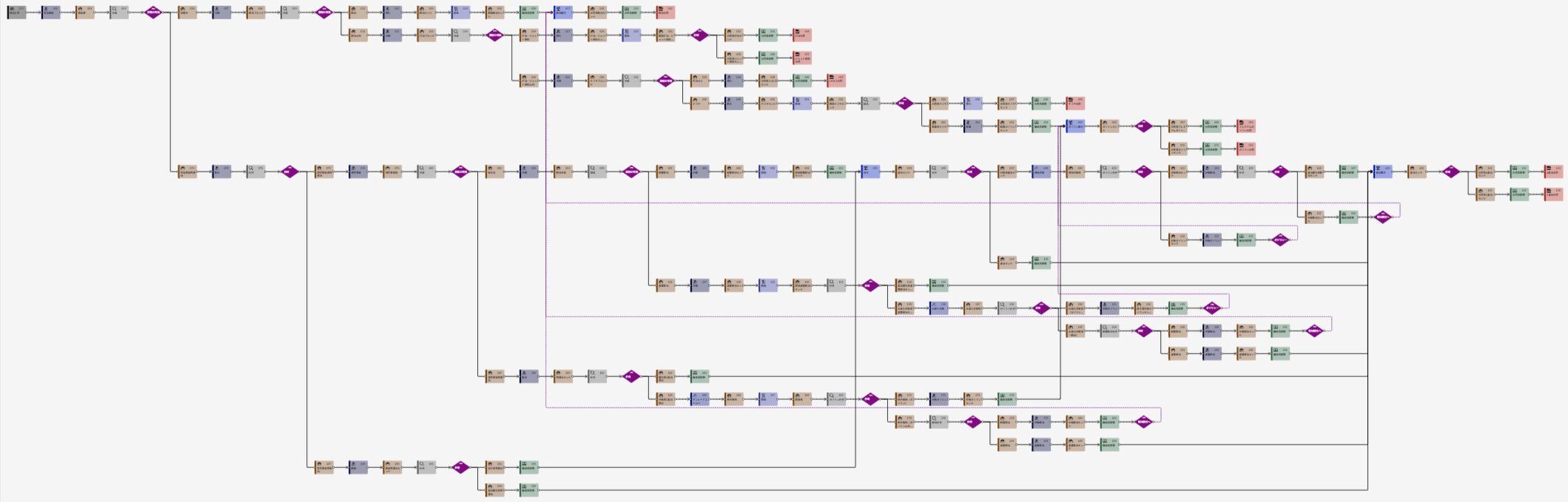
モデルの前提
今回は以下のような設定となるようにモデルを構成し、設定を行います。
- 入荷量:1分間に50
- 稼働時間(シミュレーション時間):1日(1440分)
- 原油を入荷し精製、大きく分けてLPガス、ナフサ、ガソリン、灯油、軽油、重油を出荷
- 常圧蒸留での分留の他、残渣油(重油)に対する減圧蒸留、水素化分解、接触分解、ディレードコーカーのプロセスで入分解することでガソリンを得る工程を追加
モデルの作成は大きく分けて以下の5つのブロックに分けて解説と設定を行います。簡略化されている部分もありますが、実際の製油所を再現したものになっています。
- 常圧蒸留ブロック
LPガス、ナフサ、ガソリン(プレミアムガソリンとガソリン)、灯油とジェット燃料、軽油の出荷 - 減圧蒸留ブロック
残渣油の再蒸留 - 接触分解ブロック
減圧蒸留でえられた軽質留出油の分解 - 水素化分解ブロック
減圧蒸留でえられた重質留出油の分解 - ディレードコーカーによる分解ブロック
減圧蒸留で残った残渣油の分解
シミュレーション結果と分析
パラメーターの設定が終了したら、モデル名を「石油精製所モデル」に変更し、保存します。今回のシミュレーションは、一日に相当する「1440分」で行います。
シミュレーションを行うと、以下のような結果が表示されます。今回のモデルにはランダム変数を含む多数の分岐があり、ガソリンや重油の調合などのプロセスで必要な品目が複数存在するため、シミュレーションが複雑になっています。そのため、必ずしもシミュレーション結果が下図と一致しないことに注意してください。実際にシミュレーションを繰り返すと、結果が毎回大きく異なることが分かります。このような場合、各プロセスの品目とその数を確認することがより重要となります。
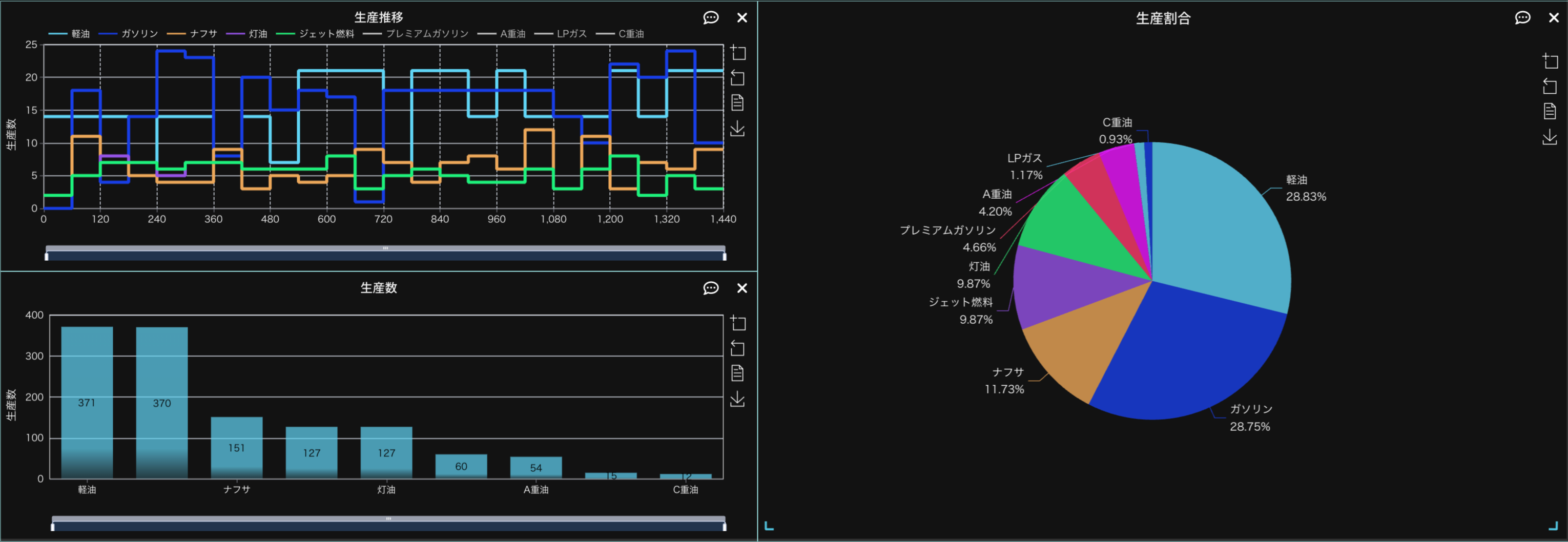
シミュレーションすると同時に各プロセスのステータスを確認することが出来ます。例えば、ガソリン調合、軽油調合、重油調合の各プロセスに入力される品目と出力品目は累積組立推移のグラフを用いることで、以下のように表示できます。これによりプロセス内の品目の流れが順調かどうかを確認することが出来ます。
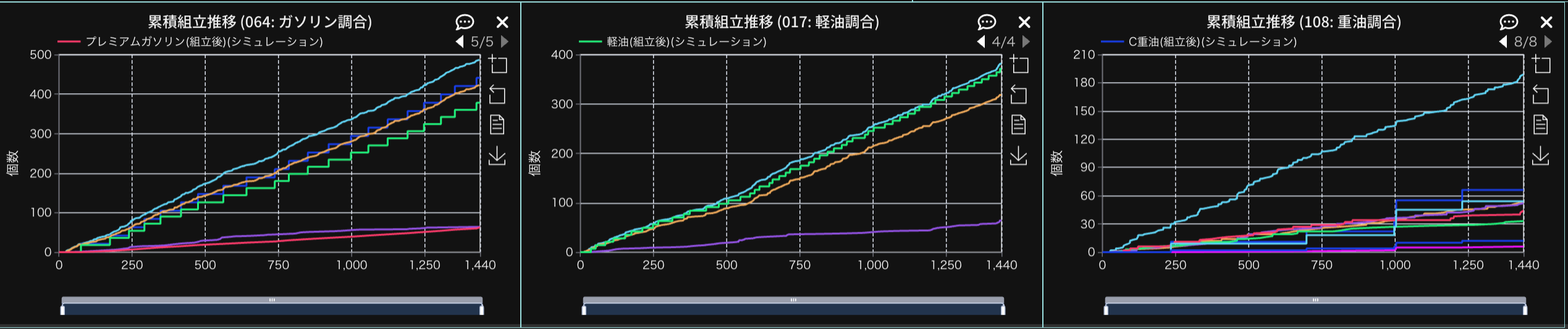
また、前回の記事と同様にステータス推移グラフを見ることで、全てのプロセスのステータスを一覧で見ることで、ボトルネックが発生しているかどうかの確認(当たり付け)をすることが出来ます。今回のモデルでは、短時間の送り出し待ち(赤)が散見されるものの、大きなブロック(処理待ち)や置き場のオーバーフローなどが発生しておらず、生産を支障するようなボトルネックが生じていないことが分かります。
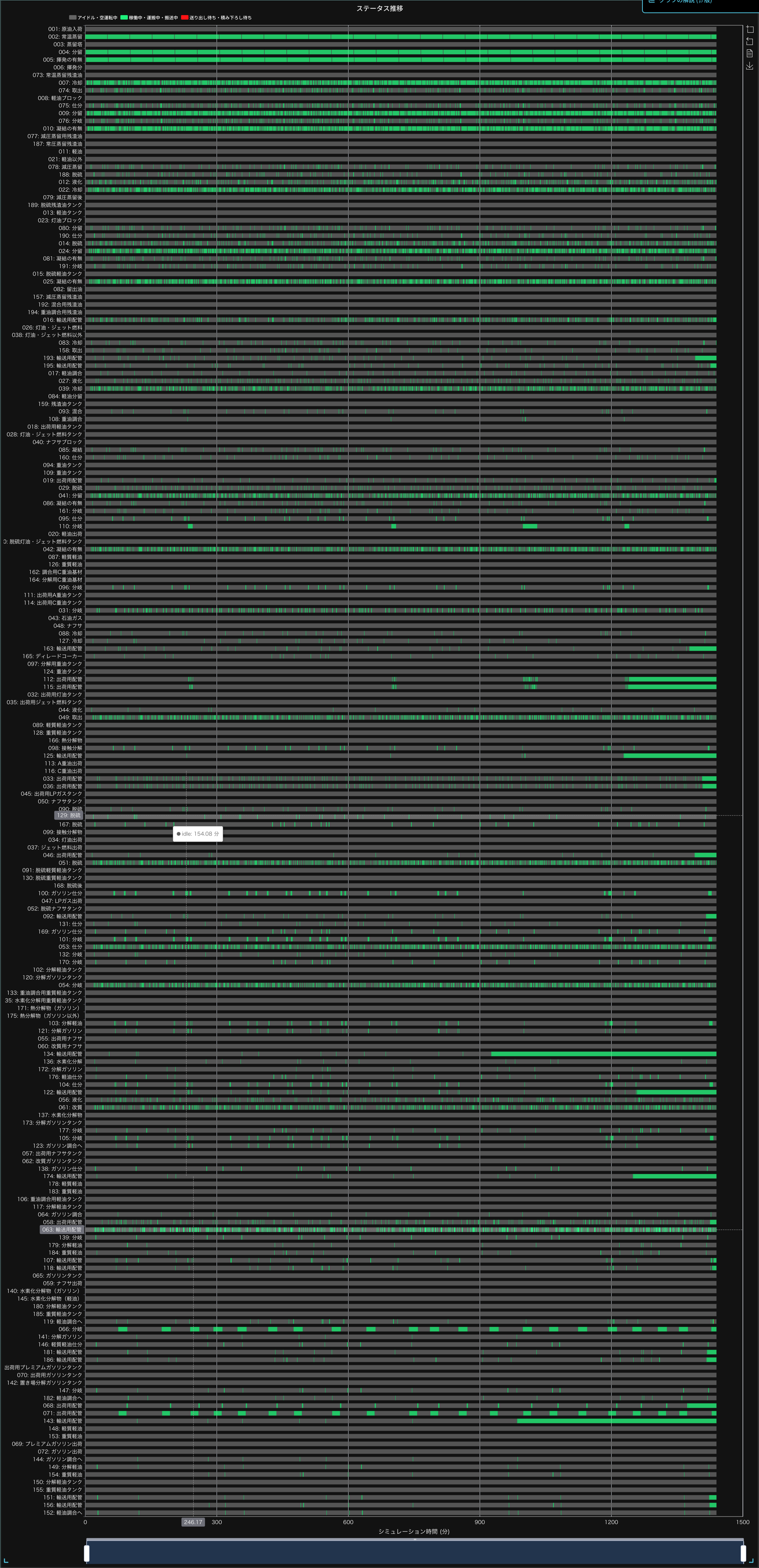
このようにプロセスを可視化することで、各プロセスに潜む課題やボトルネックなどを洗い出すことが可能となり、製造プロセス全体の効率化を行うことに繋がります。
まとめ
今回は、大規模なモデルを再現してシミュレーションを行う例として、石油精製所のモデルを作成し、シミュレーションを行いました。このように、assimeeでは200枚近い多数のプロセスカードを使った大規模なモデルであっても、PC上で手軽に作成し、短時間でシミュレーションを行うことができます。さらに、モデルのパラメーター(設定条件)を変更することも容易なので、反応条件を変えながら繰り返しシミュレーションを行い、状況の変化を確認することができます。これにより、生産ラインの組み換えや新設前のボトルネックの有無の確認、ボトルネック対策の立案が可能です。
assimeeでは、実際の製造プロセスをモデル化し、シミュレーションすることで、プロセスの見える化や潜在的な課題の洗い出しを行うことができます。製造プロセスのデジタル化や課題解決でお悩みの方は、ぜひお問い合わせください。