概要
今回は一般的な自動車組立工場の自動車組み立てラインを再現するモデルを作成してみましょう。今回のモデルではパラメータを割り当てて、一般的な生産ラインの生産量となる1日800台の車を生産するようにモデルの設定を行います。*生産量だけを目標に近づけるように入荷や加工等のパラメータを設定しているため、現実の生産ラインを必ずしも反映していないことには注意してください。
自動車生産ラインの再現モデル
トヨタの生産ライン紹介ページでは鉄板から車体を組み立てるために以下の工程を挙げています。
- プレス
- 溶接
- 塗装
- 組立
- 検査
- 輸送
このうち、組立では約3万点に及ぶ部品を取り付ける必要があり、検査項目は2000に及びます。今回のモデルでは組立と検査は簡略化し、上記の工程を再現していきます。不良品の再組み立てなどのループ状のプロセスが省略されていますが、複数の部品の供給、複数回の検査などを盛り込んだ非常に大きなモデルとなります。今回も複数のブロックに分割してブロックごとにモデルを作成していきます。
モデルの作成
今回は想定するモデルが下図のようにプロセスカードで150枚を超える大きなモデルのため、以下のブロックに分割してモデルを作成します。
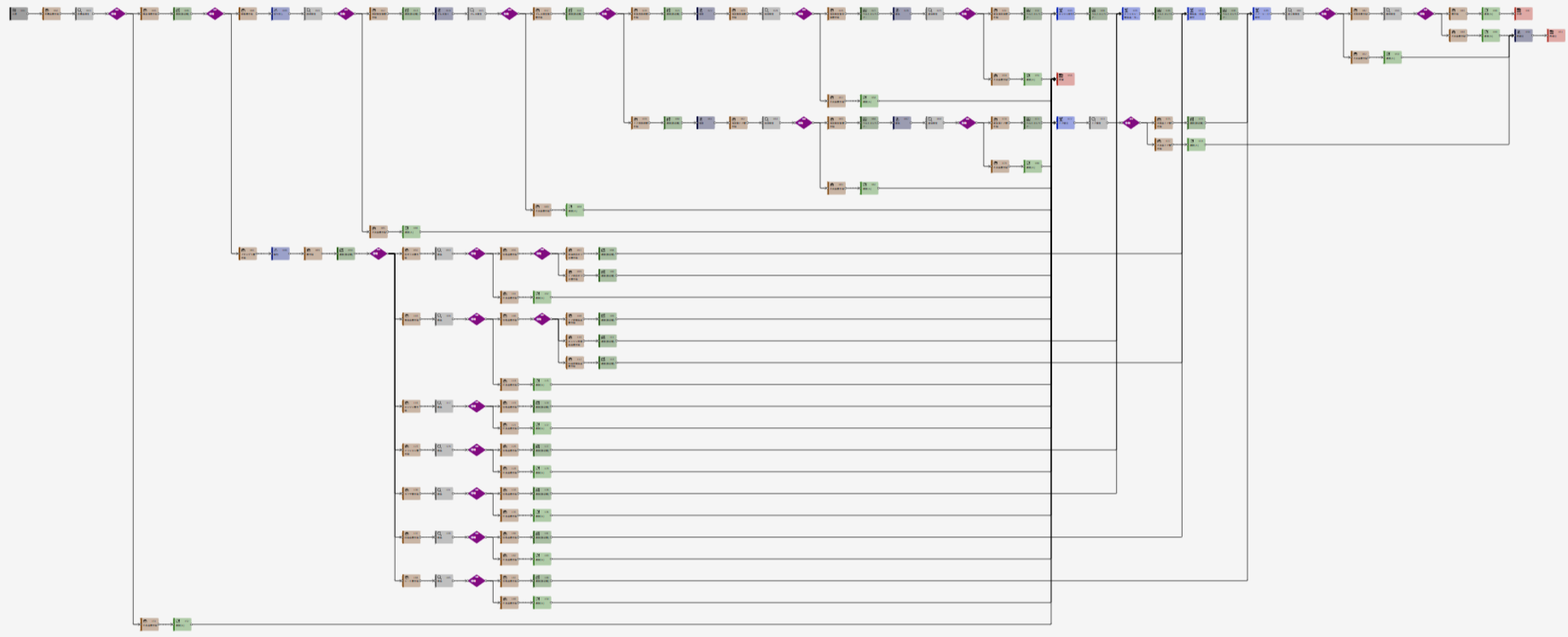
- 入荷ブロック
- 到着品の不良品処理小ブロック
- 到着品処理ブロック
- 鉄板加工ブロック
- 切り出しの不良品処理小ブロック
- プレス加工ブロック
- プレス加工小ブロック
- プレス加工後の処理小ブロック
- プレス加工後の不良品処理小ブロック
- 車体組立ブロック
- 車体溶接小ブロック
- 車体溶接後の不良品処理小ブロック
- 車体塗装小ブロック
- 車体塗装後の不良品処理小ブロック
- ドア組立ブロック
- ドア溶接小ブロック
- ドア塗装小ブロック
- ドア組立小ブロック
- ドア完成品検査ブロック
- アセンブリ管理ブロック
- 入荷品処理小ブロック
- 窓ガラスと電装品の検品小ブロック
- エンジンとミッションの検品小ブロック
- タイヤと内装品、シートの検品小ブロック
- 窓ガラスの管理と不良品処理小ブロック
- 電装品の管理と不良品処理小ブロック
- エンジンの管理と不良品処理小ブロック
- ミッションの管理と不良品処理小ブロック
- タイヤの管理と不良品処理小ブロック
- 内装品の管理と不良品処理小ブロック
- シートの不良品処理小ブロック
- 自動車組立ブロック
- エンジン取付とミッション取付小ブロック
- 不良品処理小ブロック
- 電装品の取付とドア・シートの取付小ブロック
- 完成品最終検査ブロック
- 完成品最終検査小ブロック
- 組立後の不良品処理小ブロック
- 出荷ブロック
*下流のプロセスカードを配置してから接続の設定をを行う必要があるプロセスカードがあることに注意してください。
STEP1 プロセス図の作成
1.入荷ブロック

図のように(入荷→置き場→検査→分岐)とプロセスを配置します。
入荷プロセス:
特に変更なし
置き場プロセス:
プロセス名を「到着品置き場」へ変更
検品プロセス:
プロセス名を「到着品検査」へ変更
分岐プロセス:
特に変更なし
分岐先2つ:
置き場プロセス(到着品処理ブロックへ):
プロセス名を「検品済置き場」へ変更
置き場プロセス(到着品の不良品処理小ブロックへ):
プロセス名を「不良品置き場」へ変更
到着品の不良品処理小ブロック

図のように(置き場→運搬)の順にプロセスを配置します。
置き場プロセス(再掲):
プロセス名を「不良品置き場」へ変更
運搬(人):
特に変更なし
運搬プロセス後:
後で8. 自動車組立ブロックで設置する出荷プロセス「廃棄」へ接続
2.到着品処理ブロック

図のように(置き場→運搬→分岐)の順にプロセスを配置します。
置き場プロセス(再掲):
プロセス名を「検品済置き場」へ変更
運搬(搬送機):
特に変更なし
分岐プロセス:
特に変更なし
分岐先2つ:
置き場プロセス(鉄板加工ブロックへ):
プロセス名を「鉄板置き場」へ変更
置き場プロセス(アセンブリ管理ブロックの入荷品処理小ブロックへ):
プロセス名を「アセンブリ置き場」へ変更
3.鉄板加工ブロック

鉄板を加工するため、図のように(置き場→分解→検品→分岐)の順にプロセスを配置します。
置き場プロセス(再掲):
プロセス名を「鉄板置き場」へ変更
分解プロセス:
プロセス名を「切り出し」へ変更
検品プロセス:
プロセス名を「部材検査」へ変更
分岐プロセス:
特に変更なし
分岐先2つ:
置き場プロセス(プレス加工小ブロックへ):
プロセス名を「部材検査後置き場」へ変更
置き場プロセス(切り出しの不良品処理小ブロックへ):
プロセス名を「不良品置き場」へ変更
切り出しの不良品処理小ブロック
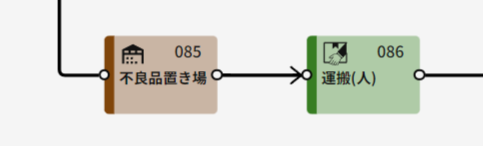
図のように切り出し後の検品での不良品を処理するために(置き場→運搬)の順にプロセスを配置します。
置き場プロセス(再掲):
プロセス名を「不良品置き場」へ変更
運搬(人):
特に変更なし
運搬プロセス後:
自動車組立ブロックで設置される出荷プロセス「廃棄」へ接続
4.プレス加工ブロック
このブロックでは鉄板のプレス加工の後、車体用鉄板とドア用鉄板の分岐を行うため、プレス加工小ブロックとプレス加工後の処理小ブロックに分けてプロセスの配置を行います。
ブレス加工小ブロック

鉄板をプレス加工する工程を再現し、図のように(置き場→運搬→加工→検品→分岐)の順でプロセスを配置します。
置き場プロセス(再掲):
プロセス名を「部材検査後置き場」へ変更
運搬(搬送機):
特に変更なし
加工プロセス:
プロセス名を「プレス加工」へ変更
検品プロセス:
プロセス名を「プレス検査」へ変更
分岐プロセス:
特に変更なし
分岐先2つ:
置き場プロセス(プレス加工後の処理小ブロックへ):
プロセス名を「プレス検査済置き場」へ変更
置き場プロセス(プレス加工後の不良品処理小ブロックへ):
プロセス名を「不良品置き場」へ変更
プレス加工後の処理小ブロック
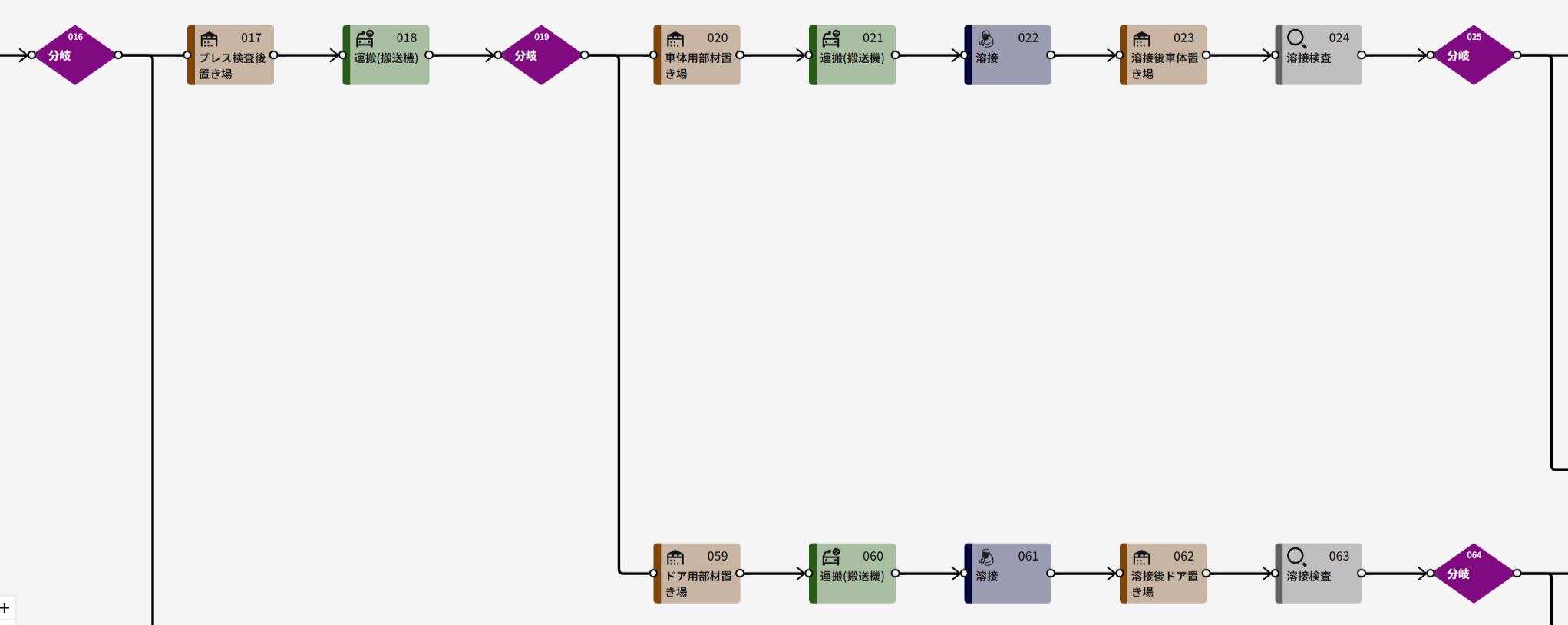
図のようにプレス加工後に検品を行い車体用の部材とドア用の部材の分岐までを考えて、(置き場→運搬→分岐)の順でプロセスを配置します。
置き場プロセス(再掲):
プロセス名を「プレス検査後置き場」へ変更
運搬(搬送機):
特に変更なし
分岐プロセス:
特に変更なし
分岐先2つ:
置き場プロセス(車体溶接小ブロックへ):
プロセス名を「車体用部材置き場」へ変更
置き場プロセス(車体溶接後の不良品処理小ブロックへ):
プロセス名を「ドア用部材置き場」へ変更
プレス加工後の不良品処理小ブロック
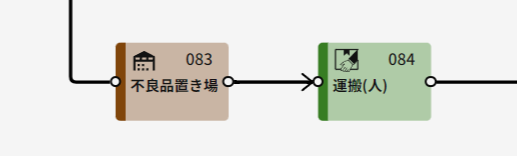
図のようにプレス加工後の検品での不良品を処理するために(置き場→運搬)の順にプロセスを配置します。
置き場プロセス(再掲):
プロセス名を「不良品置き場」へ変更
運搬(人):
特に変更なし
運搬プロセス後:
自動車組立ブロックで設置される出荷プロセス「廃棄」へ接続
5.車体組立ブロック
このブロックではプレス加工後の処理小ブロックで分岐した後、車体の溶接加工を車体溶接小ブロックで塗装を車体塗装小ブロックで行います。それぞれの小ブロックでは加工と検品、不良品の処理を行います。
車体溶接小ブロック
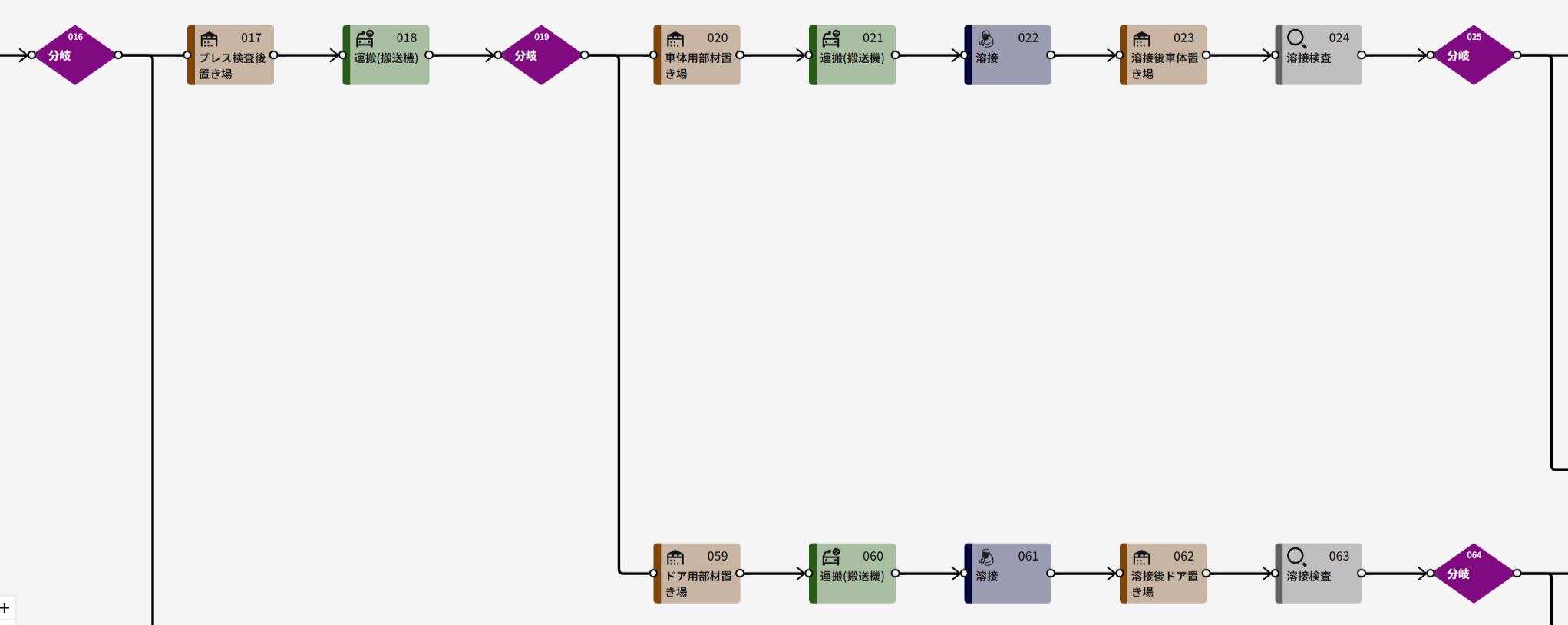
図のように合格品側の溶接工程に(置き場→運搬→加工→置き場→検品→分岐)の順でプロセスを配置します。
置き場プロセス(再掲):
プロセス名を「車体用部材置き場」へ変更
運搬(搬送機):
特に変更なし
加工プロセス:
プロセス名を「溶接」へ変更
置き場プロセス:
プロセス名を「溶接後車体置き場」へ変更
検品プロセス:
プロセス名を「溶接検査」へ変更
分岐プロセス:
特に変更なし
分岐先2つ:
置き場プロセス(車体塗装小ブロックへ):
プロセス名を「溶接検査後車体置き場」へ変更
置き場プロセス(車体溶接後の不良品処理小ブロックへ):
プロセス名を「不良品置き場」へ変更
車体溶接後の不良品処理小ブロック
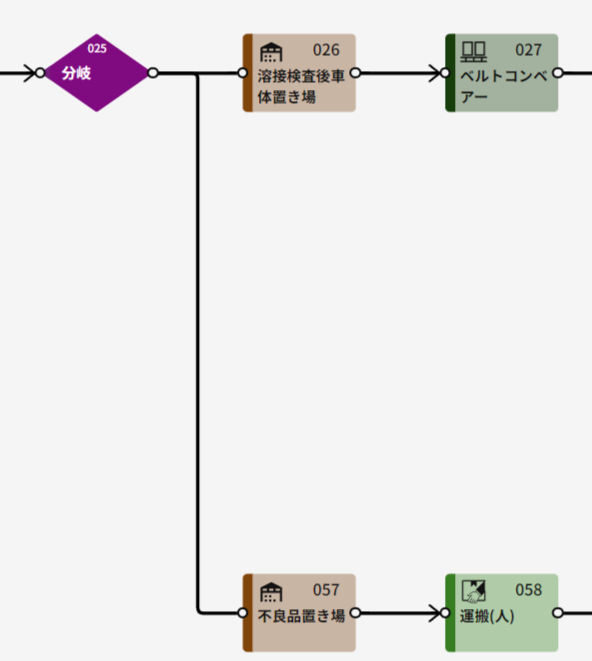
図のように車体溶接後の検品での不良品を処理するために(置き場→運搬)の順にプロセスを配置します。
置き場プロセス(再掲):
プロセス名を「不良品置き場」へ変更
運搬(人):
特に変更なし
運搬プロセス後:
自動車組立ブロックで設置される出荷プロセス「廃棄」へ接続
車体塗装小ブロック

図のように車体溶接小ブロックでの検品の結果により合格品側の塗装工程と不良品の処理の2つに分岐させ、それぞれにプロセスを配置します。
合格品側塗装工程:
置き場プロセス(再掲):
プロセス名を「溶接検査後車体置き場」へ変更
ベルトコンベアー:
特に変更なし
加工プロセス:
プロセス名を「塗装」へ変更
検品プロセス:
プロセス名を「塗装検査」へ変更
分岐プロセス:
特に変更なし
分岐先2つ:
置き場プロセス(エンジン取付とミッション取付小ブロックへ):
プロセス名を「塗装済車体置き場」へ変更
置き場プロセス(車体塗装後の不良品処理小ブロックへ):
プロセス名を「不良品置き場」へ変更
車体塗装後の不良品処理小ブロック
置き場プロセス(再掲):
プロセス名を「不良品置き場」へ変更
運搬(人):
特に変更なし
運搬プロセス後:
自動車組立ブロックで設置される出荷プロセス「廃棄」へ接続
6.ドア組立ブロック
このブロックではプレス加工後の処理小ブロックで分岐した後、ドアの溶接加工をドア溶接小ブロックでドアの塗装をドア塗装小ブロックで行いほか、ドアの組み立てをドア組立小ブロックで、ドアの完成品検査をドア完成品検査小ブロックで行います。
ドア溶接小ブロック
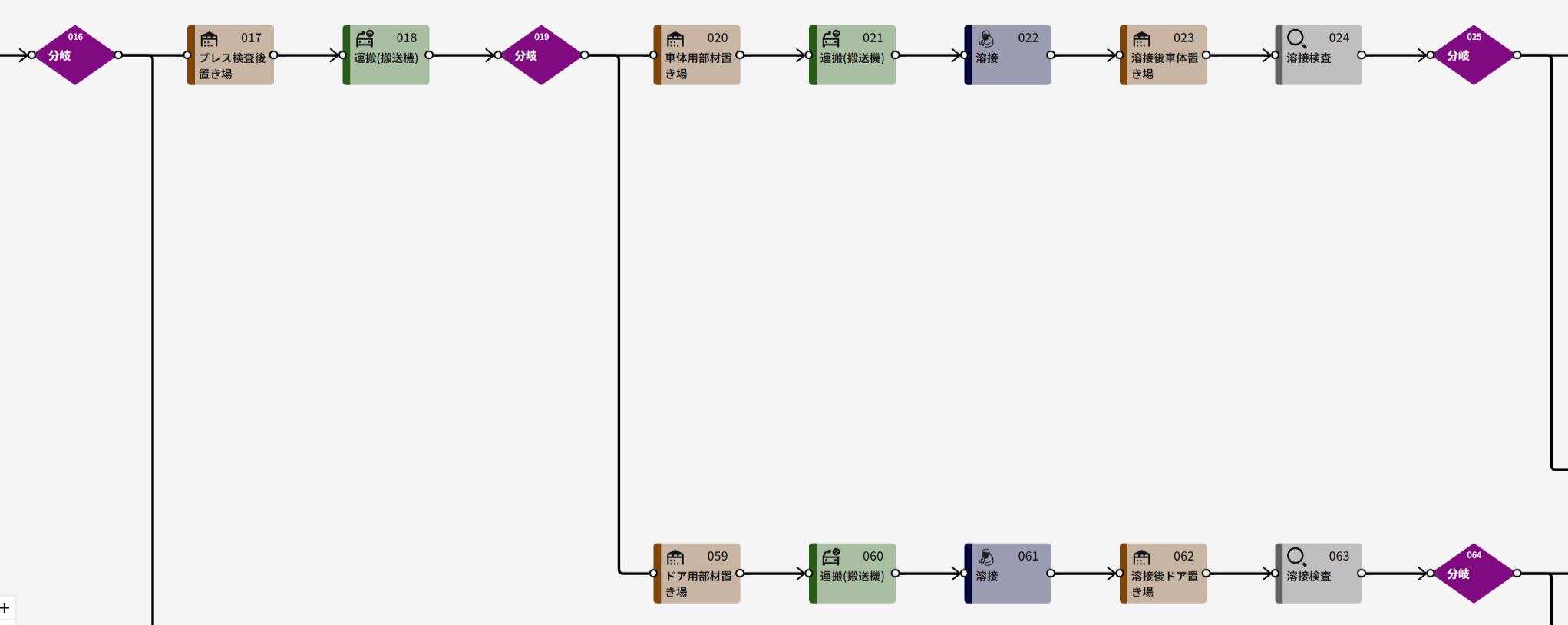
図のようにドア用の鉄板の溶接工程として置き場→運搬→加工→置き場→検品→分岐の順にプロセスを配置します。
置き場プロセス(再掲):
プロセス名を「ドア用部材置き場」へ変更
運搬(搬送機):
特に変更なし
加工プロセス:
プロセス名を「溶接」へ変更
置き場プロセス:
プロセス名を「溶接後ドア置き場」へ変更
検品プロセス:
プロセス名を「溶接検査」へ変更
分岐プロセス:
特に変更なし
分岐先2つ:
置き場プロセス(ドア塗装小ブロックへ):
プロセス名を「溶接検査後置き場」へ変更
置き場プロセス(ドア塗装小ブロックへ):
プロセス名を「不良品置き場」へ変更
ドア塗装小ブロック
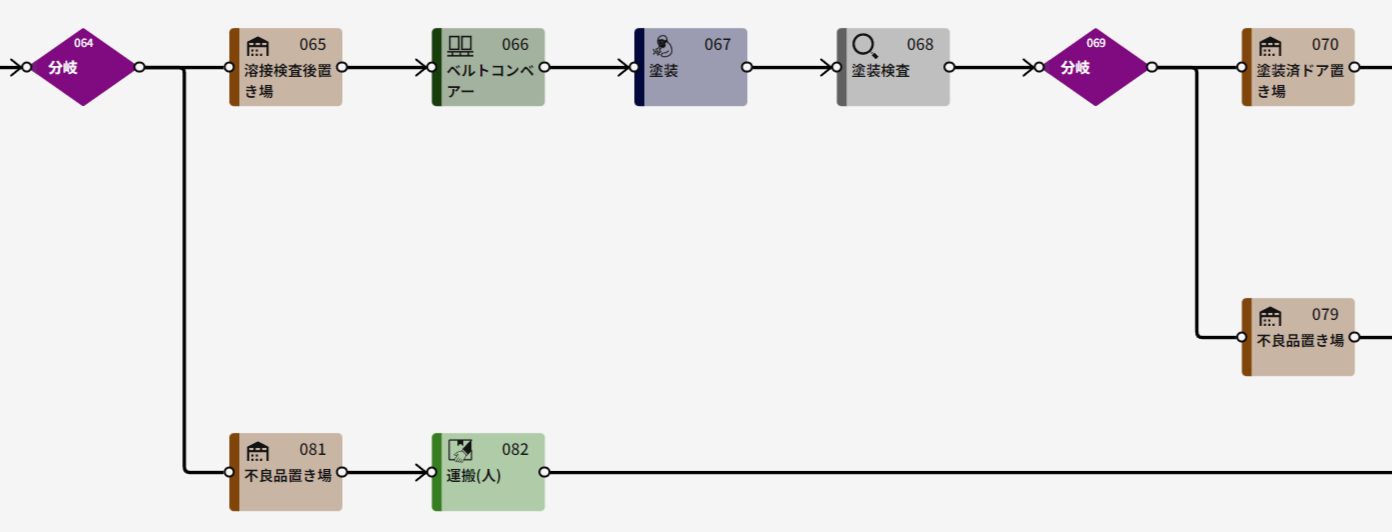
図のようにドア溶接小ブロックでの検品の結果により、塗装工程(置き場→運搬→加工→置き場→検品→分岐)と不良品処理(置き場→運搬)の2つに分岐します。
合格品側塗装工程:
置き場プロセス(再掲):
プロセス名を「溶接検査後置き場」へ変更
ベルトコンベアー:
特に変更なし
加工プロセス:
プロセス名を「塗装」へ変更
検品プロセス:
プロセス名を「塗装検査」へ変更
分岐プロセス:
特に変更なし
分岐先2つ:
置き場プロセス(ドア組立小ブロックへ):
プロセス名を「塗装済みドア置き場」へ変更
置き場プロセス(ドア組立小ブロックへ):
プロセス名を「不良品置き場」へ変更
不良品側:
置き場プロセス(再掲):
プロセス名を「不良品置き場」へ変更
運搬(人):
特に変更なし
運搬プロセス後:
自動車組立ブロックで設置される出荷プロセス「廃棄」へ接続
ドア組立小ブロック
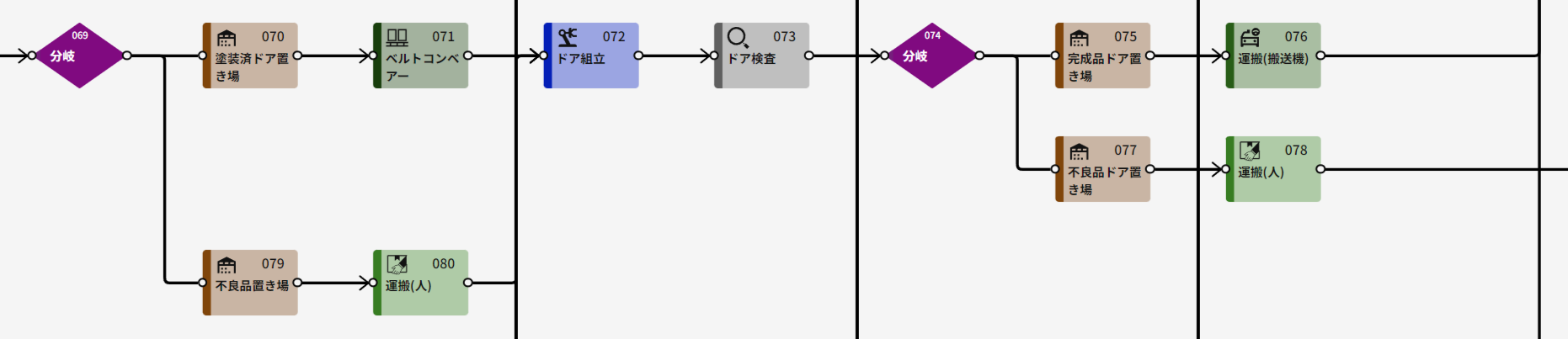
塗装後の検品の結果で、図のように合格品側のドア組立工程(置き場→運搬→組立→検品→分岐)と不良品処理(置き場→運搬)の2つに分岐します。
合格品側ドア組立工程:
置き場プロセス:
プロセス名を「塗装済ドア置き場」へ変更
ベルトコンベアー:
特に変更なし
組立プロセス:
プロセス名を「ドア組立」へ変更
検品プロセス:
プロセス名を「ドア検査」へ変更
分岐プロセス:
特に変更なし
分岐先2つ:
置き場プロセス(ドア完成品検査小ブロックへ):
プロセス名を「完成品ドア置き場」へ変更
置き場プロセス(ドア完成品検査小ブロックへ):
プロセス名を「不良品ドア置き場」へ変更
不良品側:
置き場プロセス(再掲):
プロセス名を「不良品置き場」へ変更
運搬(人):
特に変更なし
運搬プロセス後:
自動車組立ブロックで設置される出荷プロセス「廃棄」へ接続
ドア完成品検査ブロック
先述した図のようにドア組立後の分岐で合格側の完成品(置き場→運搬)と不良品処理(置き場→運搬)の2つに分岐します。
合格品側:
置き場プロセス(再掲):
プロセス名を「完成品ドア置き場」へ変更
運搬(搬送機):
特に変更なし
不良品側:
置き場プロセス(再掲):
プロセス名を「不良品ドア置き場」へ変更
運搬(人):
特に変更なし
運搬プロセス後:
検査不合格車の再組立小ブロックで設置される加工プロセス「再組立」へ接続
7.アセンブリ管理ブロック
このブロックでは入荷したコンテナを解包して各部品を取り出す処理を入荷品処理小ブロックで行うほか、各部品に分かれた検品と管理(入庫)、不良品の処理を行います。
入荷品処理小ブロック
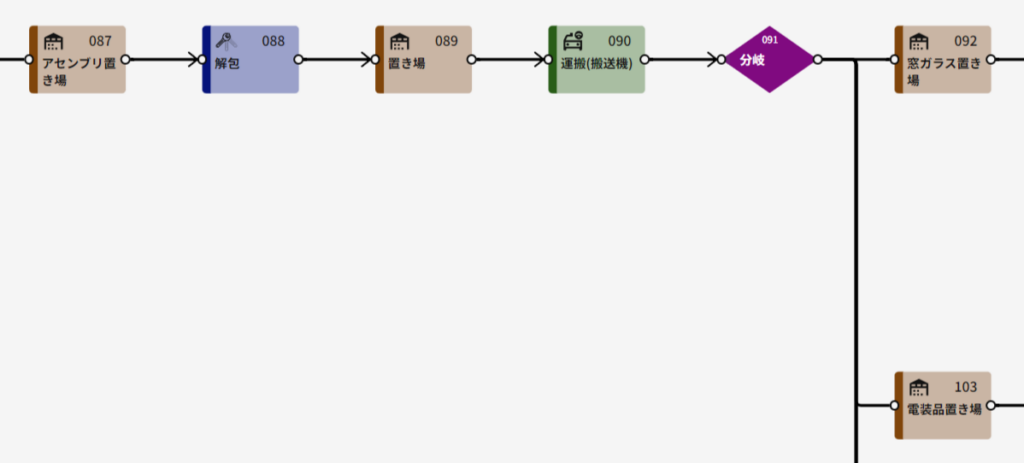
図のように入荷品処理ブロック内の分岐プロセスでコンテナを分岐させ、置き場→分解→置き場→運搬→分岐の各プロセスを設置します。
置き場プロセス(再掲):
プロセス名を「アセンブリ置き場」へ変更
分解プロセス:
プロセス名を「解包」へ変更
置き場プロセス:
プロセス名を「置き場」へ変更
運搬(搬送機):
特に変更なし
分岐プロセス:
特に変更なし
分岐先7つ:
置き場プロセス(窓ガラスと電装品検品小ブロックへ):
プロセス名を「窓ガラス置き場」へ変更
置き場プロセス(窓ガラスと電装品検品小ブロックへ):
プロセス名を「電装品置き場」へ変更
置き場プロセス(エンジンとミッション検品小ブロックへ):
プロセス名を「エンジン置き場」へ変更
置き場プロセス(エンジンとミッション検品小ブロックへ):
プロセス名を「ミッション置き場」へ変更
置き場プロセス(タイヤと内装品、シートの検品小ブロックへ):
プロセス名を「タイヤ置き場」へ変更
置き場プロセス(タイヤと内装品、シートの検品小ブロックへ):
プロセス名を「内装品置き場」へ変更
置き場プロセス(タイヤと内装品、シートの検品小ブロックへ):
プロセス名を「シート置き場」へ変更
窓ガラスと電装品の検品小ブロック
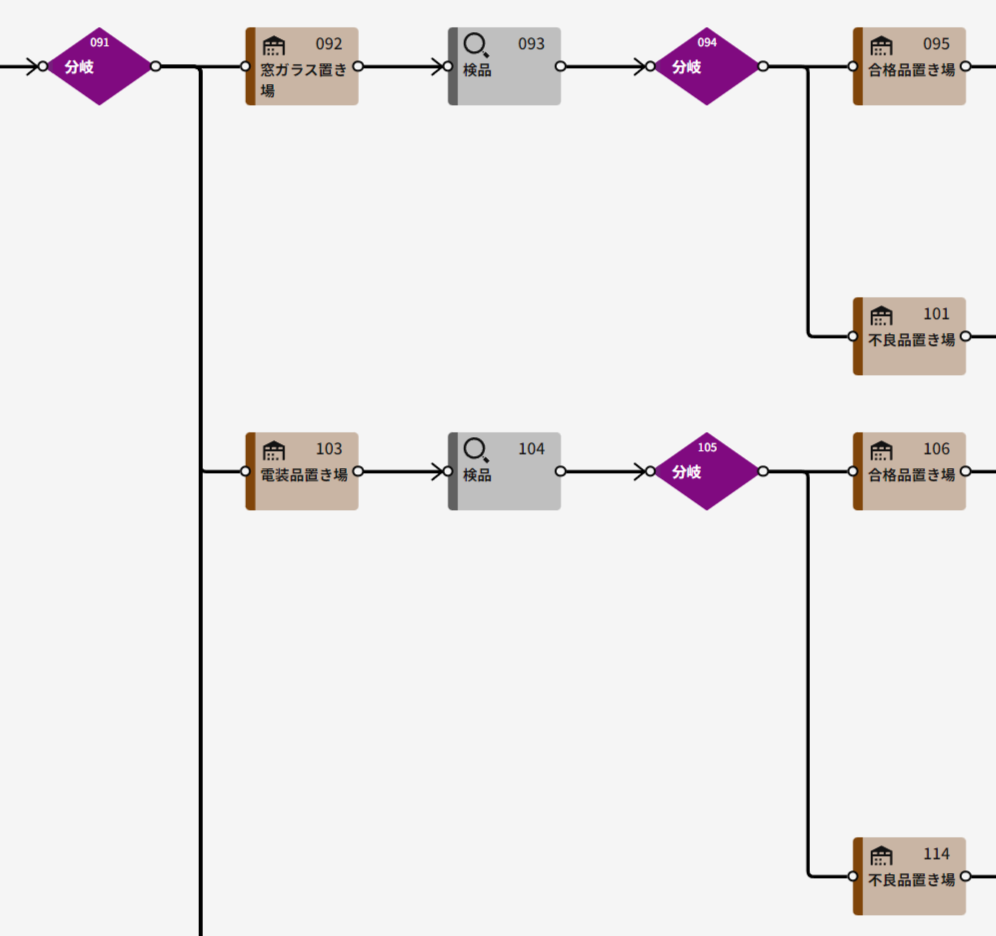
入荷品処理小ブロックの後、各部品に分けて検品を行います。
ここでは窓ガラスと電装品に対して、図のようにそれぞれ置き場→検品→分岐とプロセスを設置します。
窓ガラス:
置き場プロセス(再掲):
プロセス名を「窓ガラス置き場」へ変更
検品プロセス:
プロセス名を「検品」へ変更
分岐プロセス:
特に変更なし
分岐先2つ:
置き場プロセス(窓ガラスの管理と不良品処理小ブロックへ):
プロセス名を「合格品置き場」へ変更
置き場プロセス(窓ガラスの管理と不良品処理小ブロックへ):
プロセス名を「不良品置き場」へ変更
電装品:
置き場プロセス(再掲):
プロセス名を「電装品置き場」へ変更
検品プロセス:
プロセス名を「検品」へ変更
分岐プロセス:
特に変更なし
分岐先2つ:
置き場プロセス(電装品の管理と不良品処理小ブロックへ):
プロセス名を「合格品置き場」へ変更
置き場プロセス(電装品の管理と不良品処理小ブロックへ):
プロセス名を「不良品置き場」へ変更
エンジンとミッションの検品小ブロック

続いて、図のようにエンジンとミッションに対しても置き場→検品→分岐のようにプロセスを配置します。
エンジン:
置き場プロセス(再掲):
プロセス名を「エンジン置き場」へ変更
検品プロセス:
プロセス名を「検品」へ変更
分岐プロセス:
特に変更なし
分岐先2つ:
置き場プロセス(エンジンの管理と不良品処理小ブロックへ):
プロセス名を「合格品置き場」へ変更
置き場プロセス(エンジンの管理と不良品処理小ブロックへ):
プロセス名を「不良品置き場」へ変更
ミッション:
置き場プロセス(再掲):
プロセス名を「ミッション置き場」へ変更
検品プロセス:プロセス名を「検品」へ変更
分岐プロセス:
特に変更なし
分岐先2つ:
置き場プロセス(ミッションの管理と不良品処理小ブロックへ):
プロセス名を「合格品置き場」へ変更
置き場プロセス(ミッションの管理と不良品処理小ブロックへ):
プロセス名を「不良品置き場」へ変更
タイヤと内装品、シートの検品小ブロック
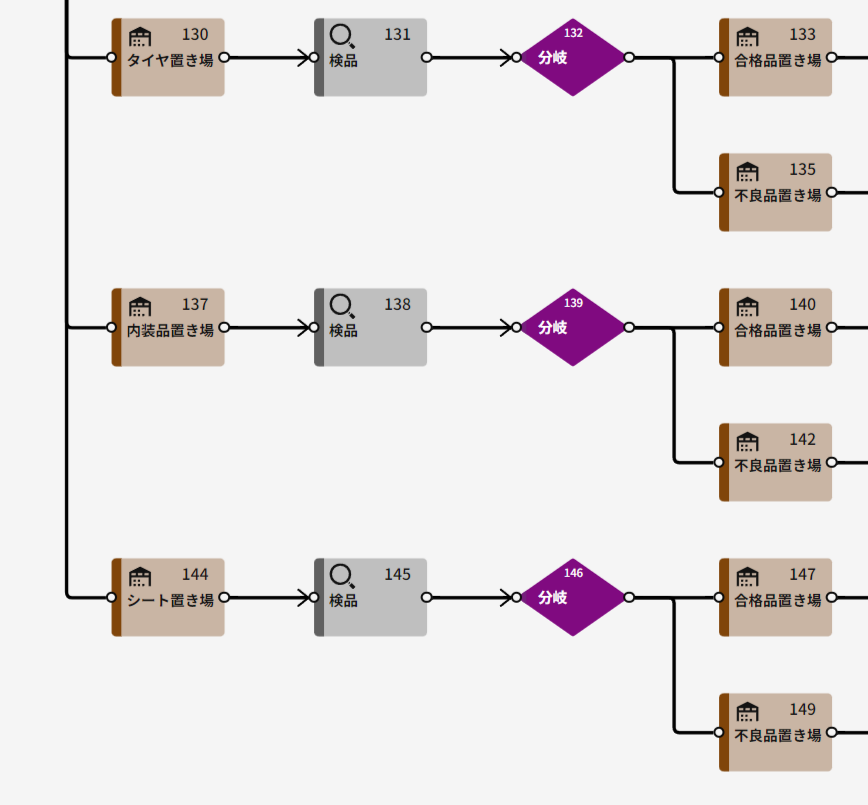
最後に、タイヤ、内装品、シートに対して置き場→検品→分岐と図のようにプロセスを配置します。
タイヤ:
置き場プロセス(再掲):
プロセス名を「タイヤ置き場」へ変更
検品プロセス:
プロセス名を「検品」へ変更
分岐プロセス:
特に変更なし
分岐先2つ:
置き場プロセス(タイヤの管理と不良品処理小ブロックへ):
プロセス名を「合格品置き場」へ変更
置き場プロセス(タイヤの管理と不良品処理小ブロックへ):
プロセス名を「不良品置き場」へ変更
内装品:
置き場プロセス(再掲):
プロセス名を「内装品置き場」へ変更
検品プロセス:
プロセス名を「検品」へ変更
分岐プロセス:
特に変更なし
分岐先2つ:
置き場プロセス(内装品の管理と不良品処理小ブロックへ):
プロセス名を「合格品置き場」へ変更
置き場プロセス(内装品の管理と不良品処理小ブロックへ):
プロセス名を「不良品置き場」へ変更
シート:
置き場プロセス(再掲):
プロセス名を「シート置き場」へ変更
検品プロセス:
プロセス名を「検品」へ変更
分岐プロセス:
特に変更なし
分岐先2つ:
置き場プロセス(シートの管理と不良品処理小ブロックへ):
プロセス名を「合格品置き場」へ変更
置き場プロセス(シートの管理と不良品処理小ブロックへ):
プロセス名を「不良品置き場」へ変更
窓ガラスの管理と不良品処理小ブロック
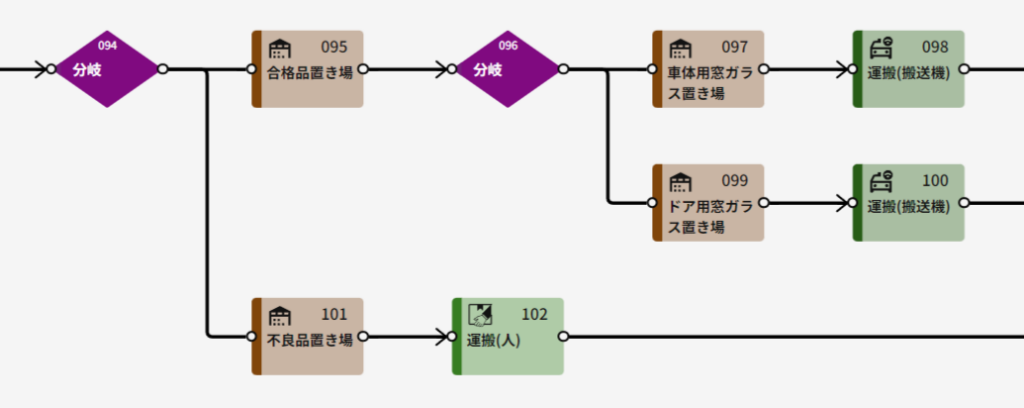
続いて、図のようにそれぞれの部品に対して検査合格品の管理(置き場→分岐→置き場→運搬)と不良品の処理(置き場→運搬)の工程を設定します。図のように窓ガラスの合格品の方はドア用と車体用で2系統に分離します。
窓ガラス合格品:
置き場プロセス(再掲):
プロセス名を「合格品置き場」へ変更
分岐プロセス:
特に変更なし
分岐先として置き場を2カ所設置
(電装品の取付とドア・シートの取付用窓ガラス)置き場プロセス:
プロセス名を「車体用窓ガラス置き場」へ変更
(ドア組立用窓ガラス)置き場プロセス:
プロセス名を「ドア用窓ガラス置き場」へ変更
(電装品の取付とドア・シートの取付用窓ガラス)置き場プロセス(再掲):
プロセス名を「車体用窓ガラス置き場」へ変更
(電装品の取付とドア・シートの取付用窓ガラス)運搬(搬送機):
特に変更なし
(電装品の取付とドア・シートの取付用窓ガラス)運搬プロセス後:
自動車組立ブロックの組立プロセス「電装品・内装取付」へ接続
(ドア組立用窓ガラス)置き場プロセス(再掲):
プロセス名を「ドア用窓ガラス置き場」へ変更
(ドア組立用窓ガラス)運搬(搬送機):
特に変更なし
(ドア組立用電装品)運搬プロセス後:
ドア組立小ブロックの組立プロセス「ドア組立」へ接続
窓ガラス不良品:
置き場プロセス(再掲):
プロセス名を「不良品置き場」へ変更
運搬(人):
特に変更なし
運搬プロセス後:
自動車組立ブロックで設置される出荷プロセス「廃棄」へ接続
電装品の管理と不良品処理小ブロック
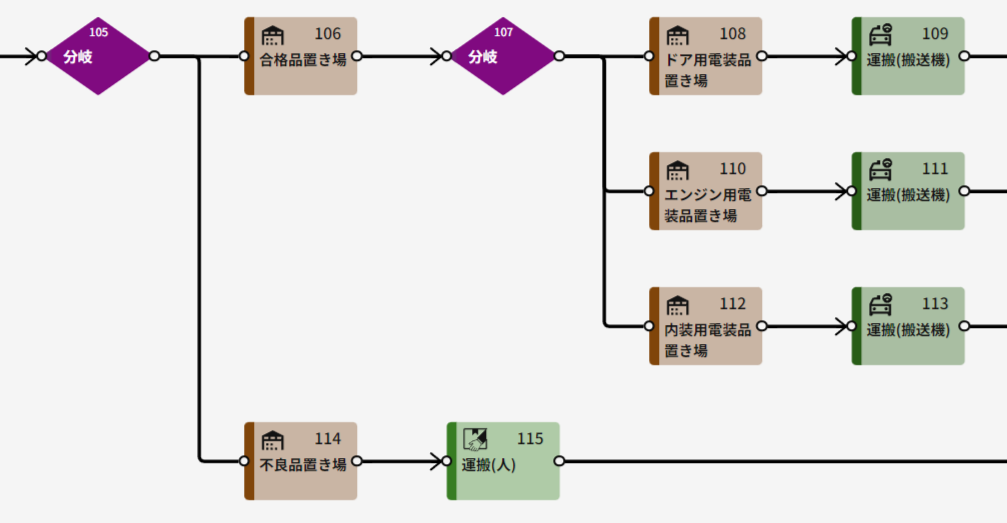
次に、図のように電装品に対して検査合格品の管理(置き場→分岐→置き場→運搬)と不良品の処理(置き場→運搬)の工程を設定します。電装品の合格品の方はドア用と車体用の2系統で合計3系統に分離します。
電装品合格品:
置き場プロセス(再掲):
プロセス名を「合格品置き場」へ変更
分岐プロセス:
特に変更なし
分岐先として置き場を3カ所設定
(ドア組立用電装品)置き場プロセス:
プロセス名を「ドア用電装品置き場」へ変更
(ミッション・電装品・タイヤ取付用電装品)置き場プロセス:
プロセス名を「エンジン用電装品置き場」へ変更
(電装品の取付とドア・シートの取付用電装品)置き場プロセス:
プロセス名を「内装品用置き場」へ変更
(ドア組立用電装品)置き場プロセス(再掲):
プロセス名を「ドア用電装品置き場」へ変更
(ドア組立用電装品)運搬(搬送機):
特に変更なし
(ドア組立用電装品)運搬プロセス後:
ドア組立小ブロックのドア組立プロセスへ接続
(ミッション・電装品・タイヤ取付用電装品)置き場プロセス(再掲):
プロセス名を「エンジン用内装品置き場」へ変更
(ミッション・電装品・タイヤ取付用電装品)運搬(搬送機):
特に変更なし
(ミッション・電装品・タイヤ取付用電装品)運搬プロセス後:
自動車組立ブロックの組立プロセス「ミッション・電装品・タイヤ取付」へ接続
(電装品の取付とドア・シートの取付用電装品)置き場プロセス(再掲):
プロセス名を「内装用電装品置き場」へ変更
(電装品の取付とドア・シートの取付用電装品)運搬(搬送機):
特に変更なし
(電装品の取付とドア・シートの取付用電装品)運搬プロセス後:
自動車組立ブロックの組立プロセス「電装品・内装取付」へ接続
電装品不良品:
置き場プロセス(再掲):
プロセス名を「不良品置き場」へ変更
運搬(人):
特に変更なし
運搬プロセス後:
自動車組立ブロックで設置される廃棄プロセスへ接続
エンジンの管理と不良品処理小ブロック
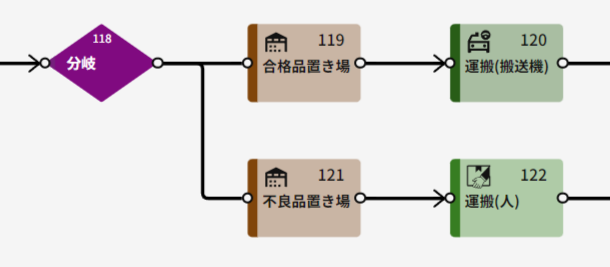
図のようにエンジンに対して検査合格品の管理(置き場→分岐→置き場→運搬)と不良品の処理(置き場→運搬)の工程を配置します。
エンジン合格品:
置き場プロセス(再掲):
プロセス名を「合格品置き場」へ変更
運搬(搬送機):
特に変更なし
運搬プロセス後:
自動車組立ブロックの組立プロセス「エンジン取付」へ接続
エンジン不良品:
置き場プロセス(再掲):
プロセス名を「不良品置き場」へ変更
運搬(人):
特に変更なし
運搬プロセス後:
自動車組立ブロックで設置される出荷プロセス「廃棄」へ接続
ミッションの管理と不良品処理小ブロック
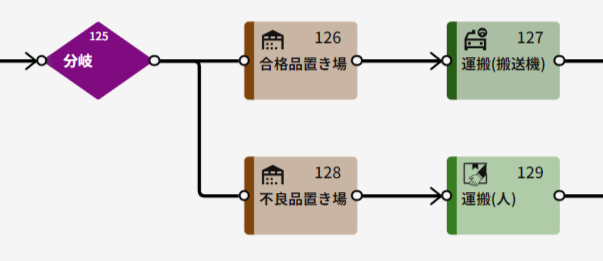
続いて、図のようにミッションに対して検査合格品の管理(置き場→分岐→置き場→運搬)と不良品の処理(置き場→運搬)の工程を配置します。
ミッション合格品:
置き場プロセス(再掲):
プロセス名を「合格品置き場」へ変更
運搬(搬送機):
特に変更なし
運搬プロセス後:
自動車組立ブロックの組立プロセス「ミッション・電装品・タイヤ取付」へ接続
ミッション不良品:
置き場プロセス(再掲):
プロセス名を「不良品置き場」へ変更
運搬(人):
特に変更なし
運搬プロセス後:
自動車組立ブロックで設置される出荷プロセス「廃棄」へ接続
タイヤの管理と不良品処理小ブロック
図のようにタイヤに対して検査合格品の管理(置き場→分岐→置き場→運搬)と不良品の処理(置き場→運搬)の工程を配置します。
タイヤ合格品:
置き場プロセス(再掲):
プロセス名を「合格品置き場」へ変更
運搬(搬送機):
特に変更なし
運搬プロセス後:
自動車組立ブロックの組立プロセス「ミッション・電装品・タイヤ取付」へ接続
タイヤ不良品:
置き場プロセス(再掲):
プロセス名を「不良品置き場」へ変更
運搬(人):
特に変更なし
運搬プロセス後:
自動車組立ブロックで設置される出荷プロセス「廃棄」へ接続
内装品の管理と不良品処理小ブロック
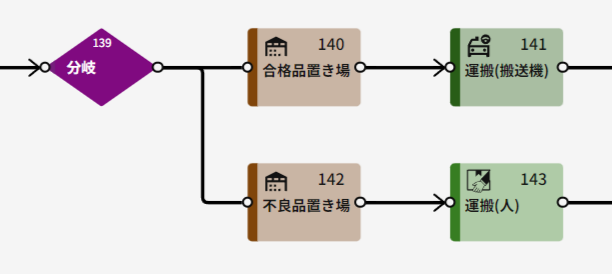
図のように内装品に対して検査合格品の管理(置き場→分岐→置き場→運搬)と不良品の処理(置き場→運搬)の工程を配置します。
内装品合格品:
置き場プロセス(再掲):
プロセス名を「合格置き場」へ変更
運搬(搬送機):
特に変更なし
運搬プロセス後:
自動車組立ブロックの組立プロセス「電装品・内装取付」へ接続
内装品不良品:
置き場プロセス(再掲):
プロセス名を「不良置き場」へ変更
運搬(人):
特に変更なし
運搬プロセス後:
自動車組立ブロックで設置される出荷プロセス「廃棄」へ接続
シートの不良品処理小ブロック
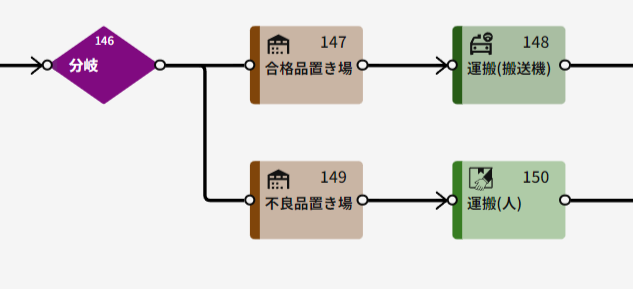
最後にシートに対して検査合格品の管理(置き場→分岐→置き場→運搬)と不良品の処理(置き場→運搬)の工程を配置します。
シート合格品:
置き場プロセス(再掲):
プロセス名を「合格品置き場」へ変更
運搬(搬送機):
特に変更なし
運搬プロセス後:
自動車組立ブロックの組立プロセス「ドア・シート取付」へ接続
シート不良品:
置き場プロセス(再掲):
プロセス名を「不良品置き場」へ変更
運搬(人):
特に変更なし
運搬プロセス後:
自動車組立ブロックで設置される出荷プロセス「廃棄」へ接続
8.自動車組立ブロック
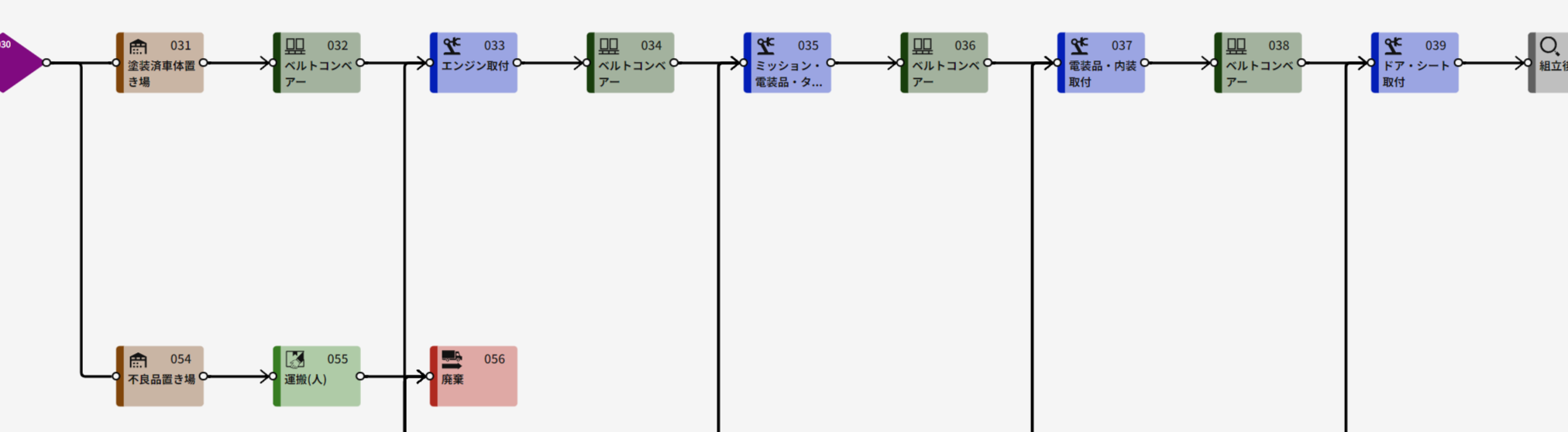
図のようにエンジンの取付とミッションの取付の小ブロック、電装品の取り付けとドアシートの取り付け小ブロックを分けてプロセスを配置し、設定します。それぞれの取付ではアセンブリ側の運搬プロセスから接続を行ってください。また、塗装工程の不良品処理の小ブロックを配置します。
エンジン取付とミッション取付小ブロック
エンジンの取付とミッションの取付工程に(置き場→運搬→組立→運搬→組立→運搬)のようにプロセスを配置します。
置き場プロセス(再掲):
プロセス名を「塗装済み車体置き場」へ変更
ベルトコンベアー:
特に変更なし
組立プロセス:
プロセス名を「エンジン取付」へ変更
ベルトコンベアー:
特に変更なし
組立プロセス:
プロセス名を「ミッション・電装品・タイヤ取付」へ変更
ベルトコンベアー:
特に変更なし
不良品処理小ブロック
車体塗装小ブロックの検品後の分岐から不良品の処理の小ブロック(置き場→運搬)を配置します。
置き場プロセス(再掲):
プロセス名を「不良品置き場」へ変更
運搬(人):
特に変更なし
出荷プロセス:
プロセス名を「廃棄」へ変更
電装品の取付とドア・シートの取付小ブロック
引き続き、電装品とドア・シートの取付工程に(組立→運搬→組立→検品→分岐)のようにプロセスの設置を行います。
組立プロセス:
プロセス名を「電装品・内装取付」へ変更
ベルトコンベアー:
特に変更なし
組立プロセス:
プロセス名を「ドア・シート取付」へ変更
検品プロセス:
プロセス名称を「組立後検査」へ変更
分岐プロセス:
特に変更なし
分岐先2つ:
置き場プロセス(完成品最終検査ブロック):
プロセス名を「完成車置き場」へ変更
置き場プロセス(完成品最終検査ブロック):
プロセス名を「不良品置き場」へ変更
9.完成品最終検査ブロック
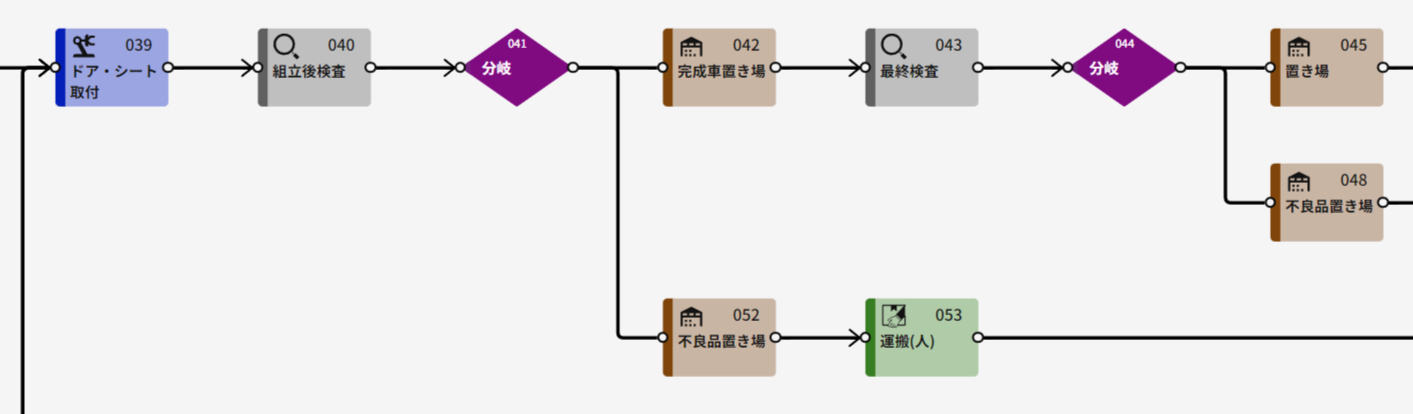
図のように組立後検査での不良品処理(置き場→運搬)と最終検査の小ブロック(置き場→検品→分岐)を配置します。
完成品最終検査小ブロック
置き場→検品→分岐の順にプロセスを配置します。
置き場プロセス(再掲):
プロセス名を「完成車置き場」へ変更
検品プロセス:
プロセス名を「最終検査」へ変更
分岐プロセス:
特に変更なし
分岐先2つ:
置き場プロセス(検査合格車の出荷ブロック):
プロセス名を「置き場」へ変更
置き場プロセス(検査不合格者の再組立小ブロック):
プロセス名を「不良品置き場」へ変更
組立後の不良品処理小ブロック
置き場→運搬の順で不良品処理小ブロックのプロセスを配置します。
置き場プロセス(再掲):
プロセス名を「不良品置き場」へ変更
運搬(人):
特に変更なし
10.出荷ブロック
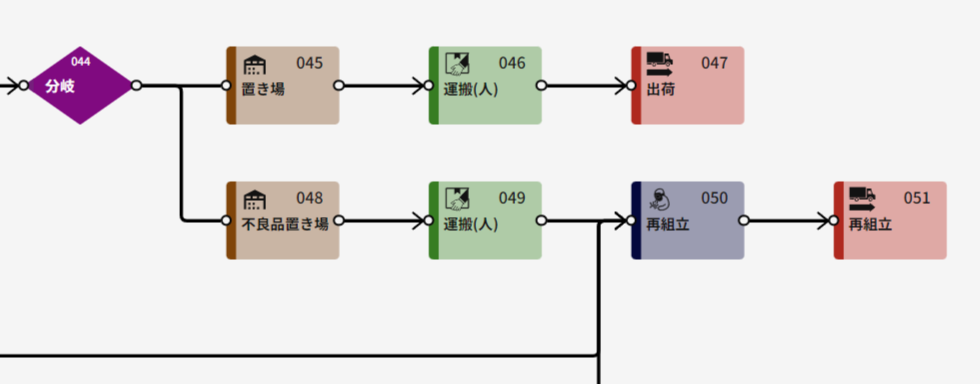
検査合格車の出荷小ブロック(図中上側、置き場→運搬→出荷)と検査不合格車の再組立小ブロック(図中下側、置き場→運搬→加工→出荷)に分けてプロセスを配置します。
検査合格車の出荷小ブロック
置き場→運搬→出荷の順にプロセスを配置します。
置き場プロセス(完成車用の置き場、再掲):
プロセス名を「置き場」へ変更
運搬プロセス(人):
特に変更なし
出荷プロセス:
特に変更なし
検査不合格車の再組立小ブロック
分岐→置き場→運搬→(合流)→加工→出荷の順にプロセスを配置します。
置き場プロセス(再掲):
プロセス名を「不良品置き場」へ変更
運搬(人):
特に変更なし
加工プロセス:
プロセス名を「再組立」へ変更
車組立後検査の不良品側をここに接続
ドア組立後検査の不良品側をここに接続
出荷プロセス:
プロセス名を「再組立」へ変更
STEP2 パラメーターの設定
パラメーターの設定を行います。品目の流れの関係上、プロセス図の作成と一部異なる部分があります。
1.入荷ブロック
以下のようにプロセスを設定します。
001入荷:
入荷パーツを2つ設定
1つ目:
品目「鉄板」、個数「5個」、発生間隔「6分」と設定
2つ目:
品目「コンテナ」、個数「10個」、時間間隔「6分」と設定
002到着品置き場:
容量を「1000個」へ設定
003到着品検査:
不良品率を「1%」、詳細設定に入り、作業員のチェックボックスにチェックを入れ、1回あたりの処理時間を「1分」、作業効率を「1」、作業人数を「10人」と設定
004分岐:
1回あたりの処理時間を「0分」と設定
分岐条件を以下のように3つ設定
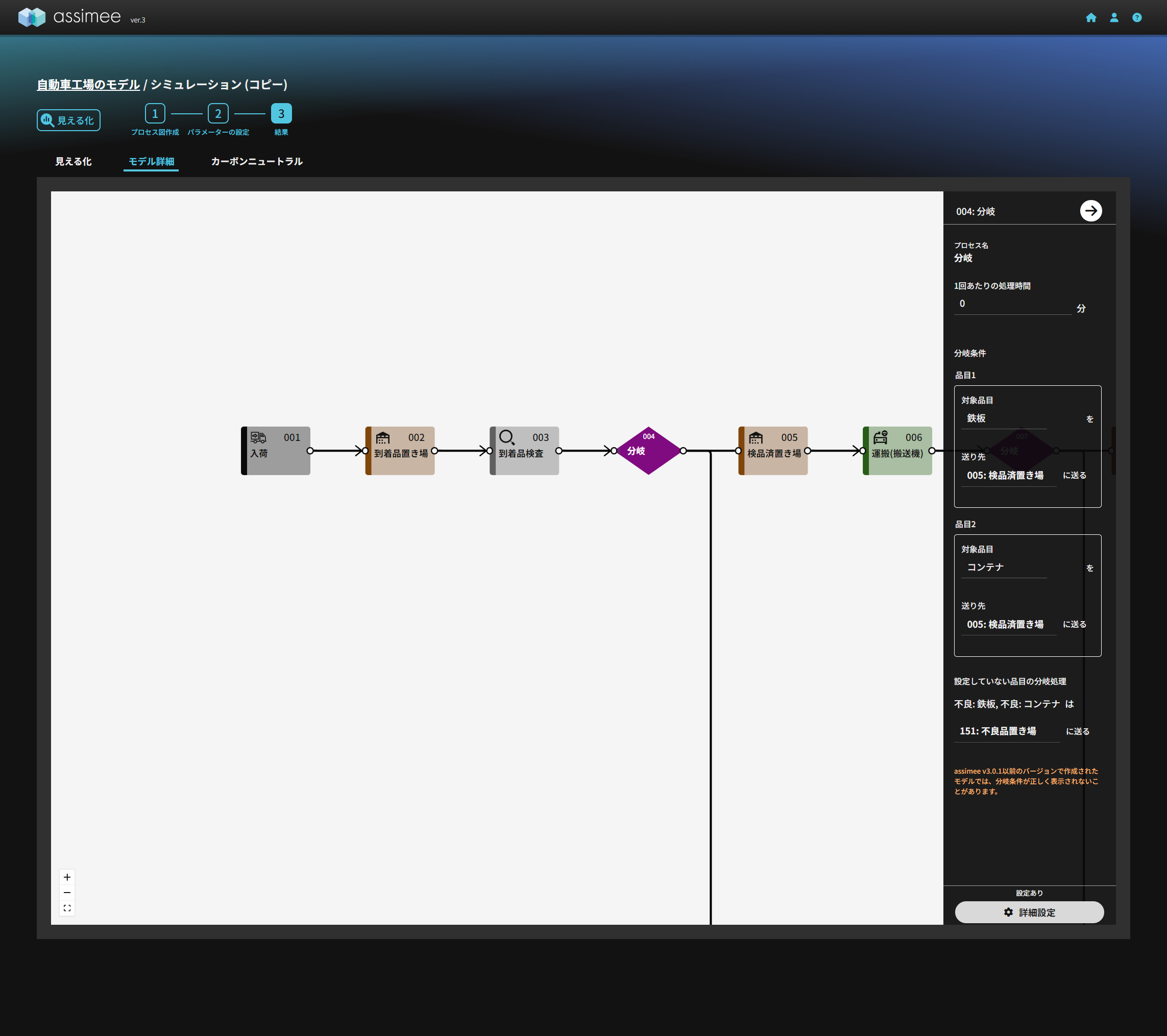
分岐条件1:
対象品目:正常:鉄板
送り先:005検品済置き場
分岐条件2:
対象品目:正常:コンテナ
送り先:005検品済置き場
分岐条件3:
設定していない品目の分岐処理
送り先:151不良品置き場
到着品の不良品処理小ブロック
151置き場プロセス:
容量を「1000個」へ設定
152運搬(人):
最大運搬量を「1個」、人数を「10人」、搬送時間(片道)を「5分」と設定
2.到着品処理ブロック
005検品済置き場(再掲):
容量を「1000個」へ設定
006運搬(搬送機):
最大積載量を「10個」、台数を「20台」、搬送時間(片道)を「10分」と設定
007分岐:
1回あたりの処理時間を「0分」と設定
分岐条件を2つ設定
分岐条件1:
品目:正常:鉄板
送り先:008鉄板置き場
分岐条件2:
品目:正常:コンテナ
送り先:087アセンブリ置き場
3.鉄板加工ブロック
008鉄板置き場:
容量を「1000個」へ設定
009切り出し:
詳細設定に入り、作業員のチェックボックスにチェックを入れ、1回あたりの処理時間を「1分」、作業効率を「1」、作業人数を「20人」と設定
対象品目を「鉄板」、個数を「10個」、
出力パーツを2つ設定
出力品目1つ目:
品目「車体用鉄板」、個数を「100個」と設定
出力品目2つ目:
品目「ドア用鉄板」、個数を「200個」と設定
010部材検査:
不良品率を「1%」、詳細設定に入り、作業員のチェックボックスにチェックを入れ、1回あたりの処理時間を「1分」、作業効率を「1」、作業人数を「40人」と設定
011分岐:
1回あたりの処理時間を「0分」と設定
分岐条件を3つ設定
分岐条件1:
品目:正常:車体用鉄板
送り先:012部材検査後置き場
分岐条件2:
品目:正常:ドア用鉄板
送り先:012部材検査後置き場
分岐条件3:
設定していない品目の分岐処理
送り先:085不良品置き場
切り出しの不良品処理小ブロック
085不良品置き場:
容量を「1000個」へ設定
086運搬(人):
最大積載量を「1個」、人数を「10人」、搬送時間(片道)を「5分」と設定
4.プレス加工ブロック
プレス加工小ブロックとプレス加工後の処理小ブロックに分けて設定を行います。
ブレス加工小ブロック
012部材検査後置き場:
容量を「1000個」へ設定
013運搬(搬送機):
プロセス名を変更せず、最大積載量を「30個」、台数を「10台」、搬送時間(片道)を「5分」と設定
014プレス加工:
詳細設定に入り、下図のように加工パターンを2つ設定、
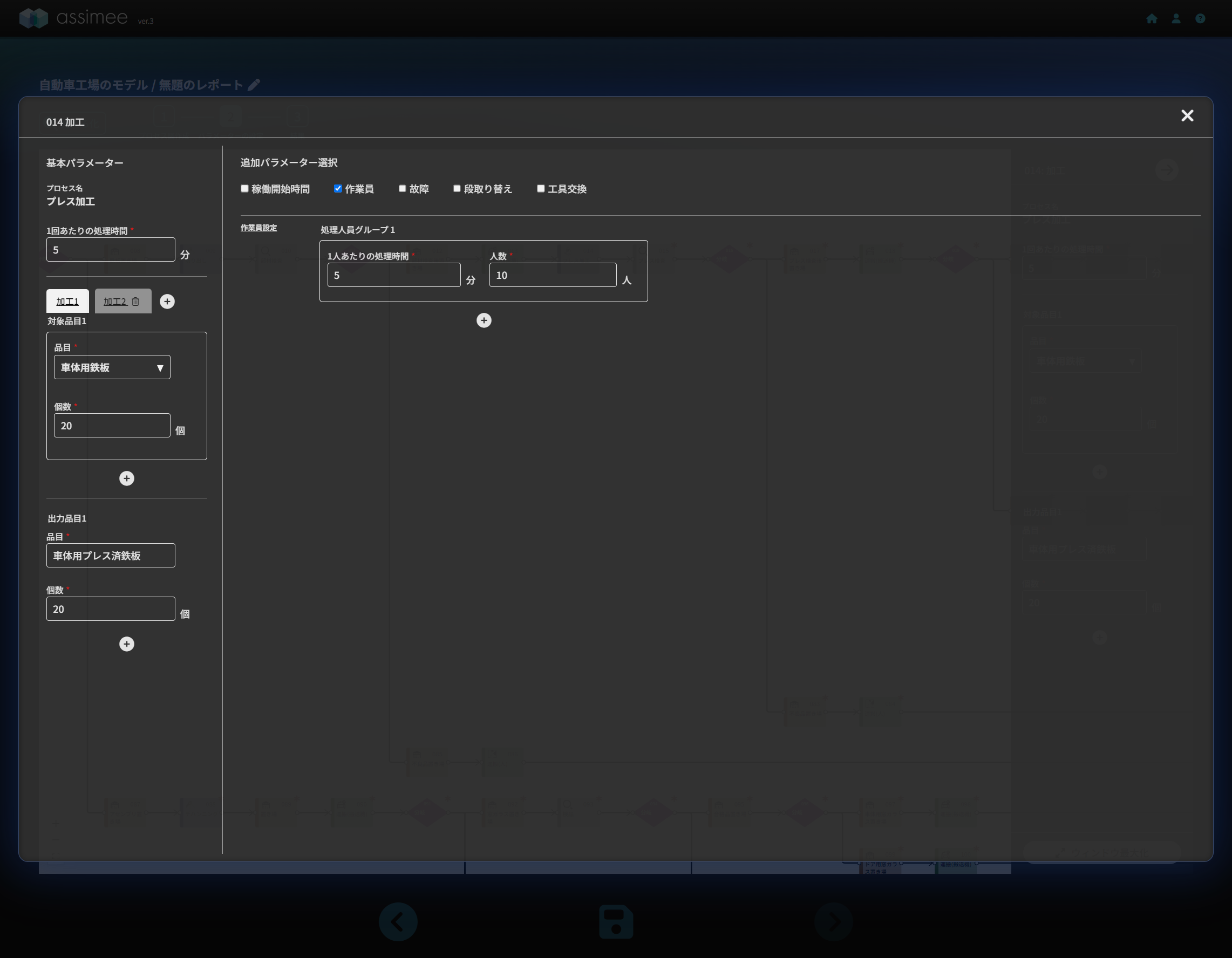
加工パターン1つ目:
作業員のチェックボックスにチェックを入れ、1回あたりの処理時間を「5分」、作業効率を「1」、作業人数を「10人」、
対象品目を「車体用鉄板」、個数を「20個」と設定、
出力品目を「車体用プレス済鉄板」、個数を「20個」と設定
加工パターン2つ目:
作業員にチェックを入れ、1人あたりの処理時間を「5分」、人数を「10人」、
対象品目を「ドア用鉄板」、個数を「40個」と設定、
出力品目を「ドア用プレス済鉄板」、個数を「40個」と設定
015プレス検査:
不良品率を「1%」、詳細設定に入り、作業員のチェックボックスにチェックを入れ、1回あたりの処理時間を「1分」、作業効率を「1」、作業人数を「40人」と設定
016分岐:
1回あたりの処理時間を「0分」と設定
分岐条件を3つ設定
分岐条件1:
品目:正常:車体用プレス済鉄板
送り先:017プレス検査済置き場
分岐条件2:
品目:正常:ドア用プレス済鉄板
送り先:017プレス検査済置き場
分岐条件3:
設定していない品目
送り先:083不良品置き場
プレス加工後の処理小ブロック
017プレス検査後置き場:
容量を「1000個」へ設定
018運搬(搬送機):
最大積載量を「30個」、台数「10台」、搬送時間(片道)を「5分」と設定
019分岐:
1回あたりの処理時間を「0分」と設定
分岐条件を2つ設定
分岐条件1:
品目:車体用プレス済鉄板
送り先:020車体用部材置き場
分岐条件2:
品目:ドア用プレス済鉄板
送り先:059ドア用部材置き場
プレス加工後の不良品処理小ブロック
083不良品置き場:
容量を「1000個」へ設定
084運搬(人):
最大積載量を「1個」、人数を「10人」、搬送時間(片道)を「5分」と設定
5.車体組立ブロック
このブロックではプレス加工後の処理小ブロックで分岐した後、車体の溶接加工を車体溶接小ブロックで塗装を車体塗装小ブロックの設定を行います。
車体溶接小ブロック
020車体用部材置き場:
容量を「1000個」へ設定
021運搬(搬送機):
最大積載量を「20個」、台数を「10台」、搬送時間(片道)を「5分」と設定
022溶接:
詳細設定に入り、作業員のチェックボックスにチェックを入れ、1回あたりの処理時間を「10分」、作業効率を「1」、作業人数を「10人」と設定
対象品目を「車体用プレス済鉄板」、個数を「50個」と設定、
出力品目を「溶接済車体」、個数を「5個」と設定
023溶接後車体置き場:
容量を「1000個」へ設定
024溶接検査:
不良品率を「0.1%」、詳細設定に入り、作業員のチェックボックスにチェックを入れ、1回あたりの処理時間を「1分」、作業効率を「1」、作業人数を「20人」と設定
025分岐:
1回あたりの処理時間を「0分」と設定
分岐条件を2つ設定
分岐条件1:
品目:正常:溶接済車体
送り先:026溶接検査後車体置き場
分岐条件2:
品目:不良:溶接済車体
送り先:057不良品置き場
車体溶接後の不良品処理小ブロック
057不良品置き場:
容量を「1000個」へ設定
058運搬(人):
最大積載量を「1個」、人数を「10人」、搬送時間(片道)を「5分」と設定
車体塗装小ブロック
合格品側塗装工程:
026溶接検査後車体置き場:
容量を「1000個」へ設定
027ベルトコンベアー:
搬送時間「1分」、最大積荷個数を「1個」と設定
028塗装:
詳細設定に入り、作業員のチェックボックスにチェックを入れ、1回あたりの処理時間を「10分」、作業効率を「1」、作業人数を「10人」と設定
対象品目を「溶接済車体」、個数を「1個」と設定、
出力品目を「塗装済車体」、個数を「1個」と設定
029塗装検査:
不良品率を「1%」、細設定に入り、作業員のチェックボックスにチェックを入れ、1回あたりの処理時間を「1分」、作業効率を「1」、作業人数を「10人」と設定
030分岐:
1回あたりの処理時間を「0分」と設定
分岐条件を2つ設定
分岐条件1:
品目:正常:塗装済車体
送り先:031塗装済み車体置き場
分岐条件2:
品目:不良:塗装済車体
送り先:不良品置き場
車体塗装後の不良品処理小ブロック
054不良品置き場:
容量を「1000個」へ設定
055運搬(人):
最大積載量を「1個」、人数を「10人」、搬送時間(片道)を「5分」と設定
056出荷:
特に設定なし
6.ドア組立ブロック
プレス加工後の処理小ブロックで分岐した後、ドアの溶接加工をドア溶接小ブロックでドアの塗装をドア塗装小ブロックで行います。
ドア溶接小ブロック
059ドア用部材置き場:
容量を「1000個」へ設定
060運搬(搬送機):
最大積載量を「20個」、台数を「10台」、搬送時間(片道)を「5分」と設定
061溶接:
詳細設定に入り、作業員のチェックボックスにチェックを入れ、1回あたりの処理時間を「10分」、作業効率を「1」、作業人数を「10人」と設定
対象品目を「ドア用プレス済鉄板」、個数を「40個」、
出力品目を「溶接済ドア」、個数を「20個」と設定
062溶接後ドア置き場:
容量を「1000個」へ設定
063溶接検査:
不良品率を「0.1%」、詳細設定に入り、作業員のチェックボックスにチェックを入れ、1回あたりの処理時間を「1分」、作業効率を「1」、作業人数を「40人」と設定
064分岐:
1回あたりの処理時間を「0分」と設定
分岐条件を2つ設定
分岐条件1:
品目:正常:溶接済ドア
送り先:065溶接検査後ドア置き場
分岐条件2:
品目:不良:溶接済ドア
送り先:081不良品置き場
ドア塗装小ブロック
合格品側塗装工程:
065溶接検査後置き場:
容量を「1000個」へ設定
066ベルトコンベアー:
搬送時間「1分」、最大積荷個数を「10個」と設定
067塗装:
詳細設定に入り、作業員のチェックボックスにチェックを入れ、1回あたりの処理時間を「10分」、作業効率を「1」、作業人数を「10人」と設定
対象品目を「溶接済ドア」、個数を「2個」と設定、
出力品目を「塗装済ドア」、個数を「2個」と設定
068塗装検査:
不良品率を「1%」、詳細設定に入り、作業員のチェックボックスにチェックを入れ、1回あたりの処理時間を「1分」、作業効率を「1」、作業人数を「10人」と設定
069分岐:
1回あたりの処理時間を「0分」と設定
分岐条件を2つ設定
分岐条件1:
品目:正常:塗装済ドア
送り先:070塗装検査跡ドア置き場
分岐条件2:
品目:不良:塗装済ドア
送り先:079不良品置き場
不良品側:
079不良品置き場:
容量を「1000個」へ設定
080運搬(人):
最大積載量を「1個」、人数を「10人」、搬送時間(片道)を「5分」と設定
7.アセンブリ管理ブロック
このブロックでは入荷したコンテナをデバイニングして各部品を取り出す処理を入荷品処理小ブロックで行うほか、各部品に分かれた検品と管理(入庫)、不良品の処理を行います。
入荷品処理小ブロック
087アセンブリ置き場:
容量を「1000個」へ設定
088解包:
詳細設定に入り、作業員のチェックボックスにチェックを入れ、1回あたりの処理時間を「1分」、作業効率を「1」、作業人数を「10人」へ設定
対象品目を「コンテナ」、個数を「1個」、
出力品目を以下の7つ設定
1つ目:
品目を「窓ガラス」、個数を「6個」と設定
2つ目:
品目をパーツ名「電装品」、個数を「10個」と設定
3つ目:
品目を「エンジン」、個数を「1個」と設定
4つ目:
品目を「ミッション」、個数を「1個」と設定
5つ目:
品目を「タイヤ」、個数を「5個」と設定
6つ目:
品目を「内装品」、個数を「10個」と設定
7つ目:
品目を「シート」、個数を「4個」と設定
089置き場:
容量を「1000個」へ設定
090運搬(搬送機):
最大積載量を「50個」、台数「10台」、搬送時間(片道)を「5分」と設定
091分岐:
1回あたりの処理時間を「0分」と設定
分岐条件を7つ設定
分岐条件1:
品目:窓ガラス
送り先:092窓ガラス置き場
分岐条件2:
品目:電装品
送り先:103電装品置き場
分岐条件3:
品目:エンジン
送り先:116エンジン置き場
分岐条件4:
品目:ミッション
送り先:123ミッション置き場
分岐条件5:
品目:タイヤ
送り先:130タイヤ置き場
分岐条件6:
品目:内装品
送り先:137内装品置き場
分岐条件7:
品目:シート
送り先:144シート置き場
窓ガラスと電装品の検品小ブロック
窓ガラス:
092窓ガラス置き場:
容量を「1000個」へ設定
093検品:
不良品率を「1%」、詳細設定に入り、作業員のチェックボックスにチェックを入れ、1回あたりの処理時間を「1分」、作業効率を「1」、作業人数を「20人」と設定
094分岐:
1回あたりの処理時間を「0分」と設定
分岐条件を2つ設定
分岐条件1:
品目:正常:窓ガラス
送り先:095合格品置き場
分岐条件2:
品目:不良:窓ガラス
送り先:101不良品置き場
電装品:
103電装品置き場:
容量を「1000個」へ設定
104検品:
不良品率を「1%」、詳細設定に入り、作業員のチェックボックスにチェックを入れ、1回あたりの処理時間を「1分」、作業効率を「1」、作業人数を「120人」と設定
105分岐:
1回あたりの処理時間を「0分」と設定
分岐条件を2つ設定
分岐条件1:
品目:正常:電装品
送り先:106合格品置き場
分岐条件2:
品目:不良:電装品
送り先:114不良品置き場
エンジンとミッションの検品小ブロック
エンジン:
116エンジン置き場:
容量を「1000個」へ設定
117検品:
不良品率を「1%」、詳細設定に入り、作業員のチェックボックスにチェックを入れ、1回あたりの処理時間を「1分」、作業効率を「1」、作業人数を「10人」と設定
118分岐:
1回あたりの処理時間を「0分」と設定
分岐条件を2つ設定
分岐条件1:
品目:正常:エンジン
送り先:119合格品置き場
分岐条件2:
品目:不良:エンジン
送り先:121不良品置き場
ミッション:
123ミッション置き場:
容量を「1000個」へ設定
124検品:
不良品率を「1%」、詳細設定に入り、作業員のチェックボックスにチェックを入れ、1回あたりの処理時間を「1分」、作業効率を「1」、作業人数を「10人」と設定
125分岐:
1回あたりの処理時間を「0分」と設定
分岐条件を2つ設定
分岐条件1:
品目:正常:ミッション
送り先:126合格品置き場
分岐条件2:
品目:不良:ミッション
送り先:128不良品置き場
タイヤと内装品、シートの検品小ブロック
タイヤ:
130タイヤ置き場:
容量を「1000個」へ設定
131検品:
不良品率を「1%」、詳細設定に入り、作業員のチェックボックスにチェックを入れ、1人あたりの処理時間を「1分」、作業効率を「1」、作業人数を「10人」と設定
132分岐:
1回あたりの処理時間を「0分」と設定
分岐条件を2つ設定
分岐条件1:
品目:正常:タイヤ
送り先:133合格品置き場
分岐条件2:
品目:不良:タイヤ
送り先:135不良品置き場
内装品:
137内装品置き場:
容量を「1000個」へ設定
138検品:
不良品率を「1%」、詳細設定に入り、作業員のチェックボックスにチェックを入れ、1回あたりの処理時間を「1分」、作業効率を「1」、作業人数を「100人」と設定
139分岐:
1回あたりの処理時間を「0分」と設定
分岐条件を2つ設定
分岐条件1:
品目:正常:内装品
送り先:140合格品置き場
分岐条件2:
品目:不良:内装品
送り先:142不良品置き場
シート:
144シート置き場:
容量を「1000個」へ設定
145検品:
不良品率を「1%」、詳細設定に入り、作業員のチェックボックスにチェックを入れ、1回あたりの処理時間を「1分」、作業効率を「1」、作業人数を「10人」と設定
146分岐:
1回あたりの処理時間を「0分」と設定
分岐条件を2つ設定
分岐条件1:
品目:正常:シート
送り先:147合格品置き場
分岐条件2:
品目:不良:シート
送り先:149不良品置き場
窓ガラスの管理と不良品処理小ブロック
窓ガラス合格品:
095合格品置き場:
容量を「1000個」へ設定
096分岐:
1回あたりの処理時間を「0分」と設定
分岐条件:
デフォルト(ランダム)に設定
(電装品の取付とドア・シートの取付用窓ガラス)097車体用窓ガラス置き場:
容量を「1000個」へ設定
(電装品の取付とドア・シートの取付用窓ガラス)098運搬(搬送機):
最大積載量を「50個」、台数を「10台」、搬送時間(片道)を「5分」と設定
(ドア組立用窓ガラス)099ドア用窓ガラス置き場:
容量を「1000個」へ設定
(ドア組立用窓ガラス)100運搬(搬送機):
最大積載量を「50個」、台数を「10台」、搬送時間(片道)を「5分」と設定
窓ガラス不良品:
101不良品置き場:
容量を「1000個」へ設定
102運搬(人):
最大積載量を「1個」、人数を「10人」、搬送時間(片道)を「5分」と設定
電装品の管理と不良品処理小ブロック
電装品合格品:
106合格品置き場プロセス:
容量を「10000個」へ設定
107分岐:
1回あたりの処理時間を「0分」と設定
分岐条件:
デフォルト(ランダム)に設定
(ドア組立用電装品)108ドア用電装品置き場:
容量を「1000個」へ設定
(ドア組立用電装品)109運搬(搬送機):
最大積載量を「50個」、台数を「10台」、搬送時間(片道)を「5分」と設定
(ミッション・電装品・タイヤ取付用電装品)110エンジン用電装品置き場:
容量を「1000個」へ設定
(ミッション・電装品・タイヤ取付用電装品)111運搬(搬送機):
最大積載量を「50個」、台数を「10台」、搬送時間(片道)を「5分」と設定
(電装品の取付とドア・シートの取付用電装品)112内装用電装品置き場:
容量を「1000個」へ設定
(電装品の取付とドア・シートの取付用電装品)113運搬(搬送機):
最大積載量を「50個」、台数を「10台」、搬送時間(片道)を「5分」と設定
電装品不良品:
114不良品置き場:
容量を「1000個」へ設定
115運搬(人):
最大積載量を「100個」、人数を「10人」、搬送時間(片道)を「5分」と設定
エンジンの管理と不良品処理小ブロック
エンジン合格品:
119合格品置き場:
容量を「1000個」へ設定
120運搬(搬送機):
最大積載量を「1個」、台数を「10台」、搬送時間(片道)を「5分」と設定
エンジン不良品:
121不良品置き場:
容量を「1000個」へ設定
122運搬(人):
最大積載量を「1個」、人数を「10人」、搬送時間(片道)を「5分」と設定
ミッションの管理と不良品処理小ブロック
ミッション合格品:
126合格品置き場:
容量を「1000個」へ設定
127運搬(搬送機):
最大積載量を「1個」、台数を「10台」、搬送時間(片道)を「5分」と設定
ミッション不良品:
128不良品置き場:
容量を「1000個」へ設定
129運搬(人):
最大積載量を「1個」、人数を「10人」、搬送時間(片道)を「5分」と設定
タイヤの管理と不良品処理小ブロック
タイヤ合格品:
133合格品置き場:
容量を「1000個」へ設定
134運搬(搬送機):
最大積載量を「5個」、台数を「10台」、搬送時間(片道)を「5分」と設定
タイヤ不良品:
135不良品置き場:
容量を「1000個」へ設定
136運搬(人):
最大積載量を「1個」、人数を「10人」、搬送時間(片道)を「5分」と設定
内装品の管理と不良品処理小ブロック
内装品合格品:
140合格品置き場:
容量を「10000個」へ設定
141運搬(搬送機):
最大積載量を「100個」、台数を「10台」、搬送時間(片道)を「5分」と設定
内装品不良品:
142不良品置き場
容量を「1000個」へ設定
143運搬(人):
最大積載量を「10個」、人数を「10人」、搬送時間(片道)を「5分」と設定
シートの不良品処理小ブロック
シート合格品:
147合格品置き場:
容量を「1000個」へ設定
148運搬(搬送機):
最大積載量を「5個」、台数を「10台」、搬送時間(片道)を「5分」と設定
シート不良品:
149合格品置き場:
容量を「1000個」へ設定
150運搬(人):
最大積載量を「1個」、人数を「10台」、搬送時間(片道)を「5分」と設定
8.自動車組立ブロック
ドアの組立の小ブロック、エンジンの取付とミッションの取付の小ブロック、電装品の取り付けとドアシートの取り付け小ブロックに分けてプロセスの設定をします。
ドア組立小ブロック
合格品側ドア組立工程:
ドアの材料が含まれているアセンブリ管理ブロックの後に設定してください
070塗装済ドア置き場:
容量を「1000個」へ設定
071ベルトコンベアー:
搬送時間「1分」、最大積荷個数を「10個」と設定
072組立:
詳細設定に入り、作業員のチェックボックスにチェックを入れ、1回あたりの処理時間を「1分」、作業効率を「1」、作業人数を「40人」と設定
対象品目を3つ設定
1つ目:
品目を「電装品」、個数を「1個」と設定
2つ目:
品目を「窓ガラス」、個数を「1個」と設定
3つ目:
品目を「塗装済ドア」、個数を「1個」と設定
出力品目を「組立済ドア」、個数を「1個」と設定
073ドア検査:
不良品率を「1%」、詳細設定に入り、作業員のチェックボックスにチェックを入れ、1回あたりの処理時間を「1分」、作業効率を「1」、作業人数を「40人」と設定
074分岐:
1回あたりの処理時間を「0分」と設定
分岐条件を2つ設定
分岐条件1:
品目:正常:組立済ドア
送り先:075完成品ドア置き場
分岐条件2:
品目:不良:組立ドア
送り先:077不良品ドア置き場
不良品側:
081不良品置き場:
容量を「1000個」へ設定
082運搬(人):
最大積荷量を「1個」、人数を「10人」、搬送時間(片道)を「5分」と設定
ドア完成品検査ブロック
合格品側:
075完成品ドア置き場:
容量を「1000個」へ設定
076運搬(搬送機):
最大積載量を「10個」、台数を「10台」、搬送時間(片道)を「5分」と設定
不良品側:
077不良品ドア置き場:
容量を「1000個」へ設定
078運搬(人):
最大積載量を「1個」、人数を「10人」、搬送時間(片道)を「5分」と設定
エンジン取付とミッション取付小ブロック
031塗装済車体置き場:
容量を「1000個」へ設定
032ベルトコンベアー:
搬送時間を「1分」、最大積荷個数を「1個」と設定
033エンジン取付:
詳細設定に入り、作業員のチェックボックスにチェックを入れ、1回あたりの処理時間を「1分」、作業効率を「1」、作業人数を「10人」と設定
対象品目を2つ設定
1つ目:
品目を「エンジン」、個数を「1個」と設定
2つ目:
品目を「塗装済車体」、個数を「1個」と設定
出力品目を「組立中車体」、個数を「1個」と設定
034ベルトコンベアー:
搬送時間を「1分」、最大積荷個数を「1個」と設定
035ミッション・電装品・タイヤ取付:
詳細設定に入り、作業員のチェックボックスにチェックを入れ、1回あたりの処理時間を「1分」、作業効率を「1」、作業人数を「10人」と設定
対象品目を4つ設定
1つ目:
品目を「タイヤ」、個数を「4個」と設定
2つ目:
品目を「電装品」、個数を「3個」と設定
3つ目:
品目を「ミッション」、個数を「1個」と設定
4つ目:
品目を「組立中車体」、個数を「1個」と設定
出力品目を「組立中車体」、個数を「1個」と設定
036ベルトコンベアー:
搬送時間を「1分」、最大積荷個数を「1個」と設定
電装品の取付とドア・シートの取付小ブロック
037電装品・内装取付:
詳細設定に入り、作業員のチェックボックスにチェックを入れ、1回あたりの処理時間を「1分」、作業効率を「1」、作業人数を「10人」と設定
対象品目を4つ設定
1つ目:
品目を「内装品」、個数を「10個」と設定
2つ目:
品目を「電装品」、個数を「3個」と設定
3つ目:
品目を「窓ガラス」、個数を「2個」と設定
4つ目:
品目を「組立中車体」、個数を「1個」と設定
出力品目を「組立中車体」、個数を「1個」と設定
038ベルトコンベアー:
搬送時間を「1分」、最大積荷個数を「1個」と設定
039ドア・シート取付:
詳細設定に入り、作業員のチェックボックスにチェックを入れ、1回あたりの処理時間を「1分」、作業効率を「1」、作業人数を「10人」と設定
対象品目を3つ設定
1つ目:
品目を「シート」、個数を「4個」と設定
2つ目:
品目を「組立中車体」、個数を「1個」と設定
3つ目:
品目を「組立済ドア」、個数を「4個」と設定
出力品目を「組立済車体」、個数を「1個」と設定
040組立後検査:
不良品率を「1%」、詳細設定に入り、作業員のチェックボックスにチェックを入れ、1回あたりの処理時間を「1分」、作業効率を「1」、作業人数を「20人」と設定
041分岐:
1回あたりの処理時間を「0分」と設定
分岐条件を2つ設定
分岐条件1:
品目:正常:組立済車体
送り先:042完成車置き場
分岐条件2:
品目:不良:組立済車体
送り先:052不良品置き場
9.完成品最終検査ブロック
組立後検査での不良品処理と完成品の最終検査の小ブロックを設定します。
完成品最終検査小ブロック
042完成車置き場:
容量を「1000個」へ設定
043最終検査:
不良品率を「1%」、詳細設定に入り、作業員のチェックボックスにチェックを入れ、1回あたりの処理時間を「1分」、作業効率を「1」、作業人数を「10人」と設定
044分岐:
1回あたりの処理時間を「0分」と設定
分岐条件を2つ設定
分岐条件1:
品目:正常:組立済車体
送り先:045置き場
分岐条件2:
品目:不良:組立済車体
送り先:048不良品置き場
組立後の不良品処理小ブロック
052不良品置き場:
容量を「1000個」へ設定
053運搬(人):
最大運搬量を「1個」、人数を「10人」、搬送時間(片道)を「5分」と設定
出荷ブロック
検査合格車の出荷小ブロックと検査不合格車の再組立小ブロックを設定します。
検査合格車の出荷小ブロック
045置き場(完成車用の置き場):
容量を「1000個」へ設定
046運搬(人):
最大積載量「1個」、人数を「10人」、搬送時間を「5分」と設定
047出荷:
特に変更なし
検査不合格車の再組立小ブロック
048不良品置き場:
容量を「1000個」へ設定
049運搬(人):
最大積荷量「1個」、人数を「10人」、搬送時間を「5分」と設定
050再組立:
詳細設定に入り、組立パターンを2つ設定
加工パターン1つ目:
作業員のチェックボックスにチェックを入れ、1回あたりの処理時間を「1分」、作業効率を「1」、作業人数を「10人」と設定
対象品目を「組立済車」、個数を「1個」、
出力品目を「不合格車」、個数を「1個」と設定
加工パターン2つ目:
作業員のチェックボックスにチェックを入れ、1回あたりの処理時間を「1分」、作業効率を「1」、作業人数を「10人」と設定
対象品目を「組立済ドア」、個数を「1個」、
出力品目を「不合格ドア」、個数を「1個」と設定
051再組立:
特に設定なし
シミュレーション
以上のプロセス配置と設定が終わったらシミュレーションを行います。今回はシミュレーション期間として1日にあたる1440分を指定してシミュレーションを実行してみましょう。適切に設定できていれば、以下の様なシミュレーション結果が表示されます。*不良品の発生にランダム変数が含まれるため毎回結果が異なり一致しません。
出力結果には出荷プロセスに接続されているすべてのパーツが含ます。グラフの凡例をクリックすることでON/OFFを切り替えることが可能となっています。
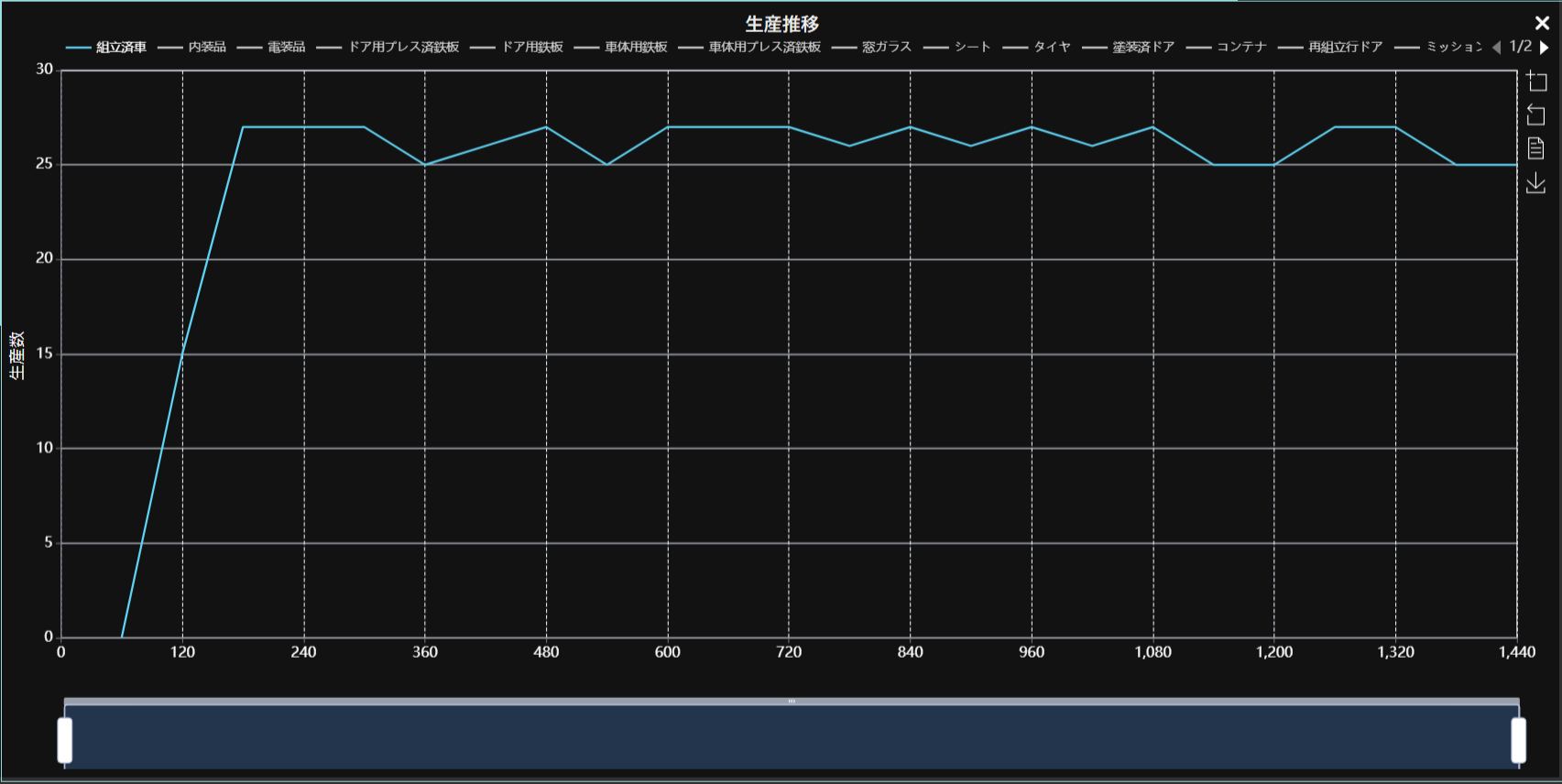
まとめ
今回の記事では自動車の生産ラインを解説しました。今回のモデルはプロセスカードが150枚を超える大規模なモデルとなりました。このようにassimeeでは大規模で自動車の組み立て工場の様な複雑な工程がある場合でもPC上で工程を再現するモデルを簡単に作成して、各種のシミュレーションを行うことが可能です。