概要
今回の記事では前回の記事で見つかったボトルネックを人の最適化で解消する方法について解説します。

前回作成したモデルは上図のようなモデルでした。このラインでは部品A、B、Cを加工して、それぞれ製品A、B、Cとした上で梱包してセットにして出荷しています。1分間に1個入荷する段ボールの1個の中に部品Aが10、部品Bが10、部品Cが5個含まれています。したがって、最も少ない製品Cを基準にしても600分では3000セット程度出荷することが可能だと考えられますが、上のモデルでは僅か26セットほどしか出荷できていません。これは生産ライン内にあるボトルネックが出荷数の増加を妨げているためという結論に前回至りました。今回は前回当たりを付けたプロセスに人の最適化を適用することでボトルネックが解消できるかを見てみます。
シミュレーション結果のおさらい
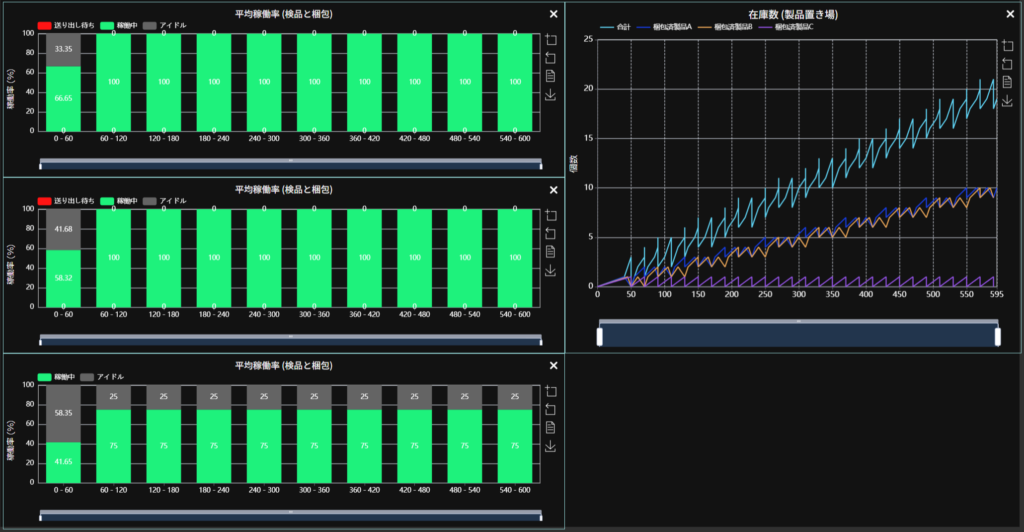
前回の分析(上図)では3カ所の検品と梱包の処理能力が足りないため、プロセスがフル稼働(処理能力不足)になっており、これ以上生産を増やすことが出来ない状態と当たりを付けました。更に詳しく見ていきましょう。各部品の生産ラインの稼働率と検品と梱包の稼働率をならべて見てみます。
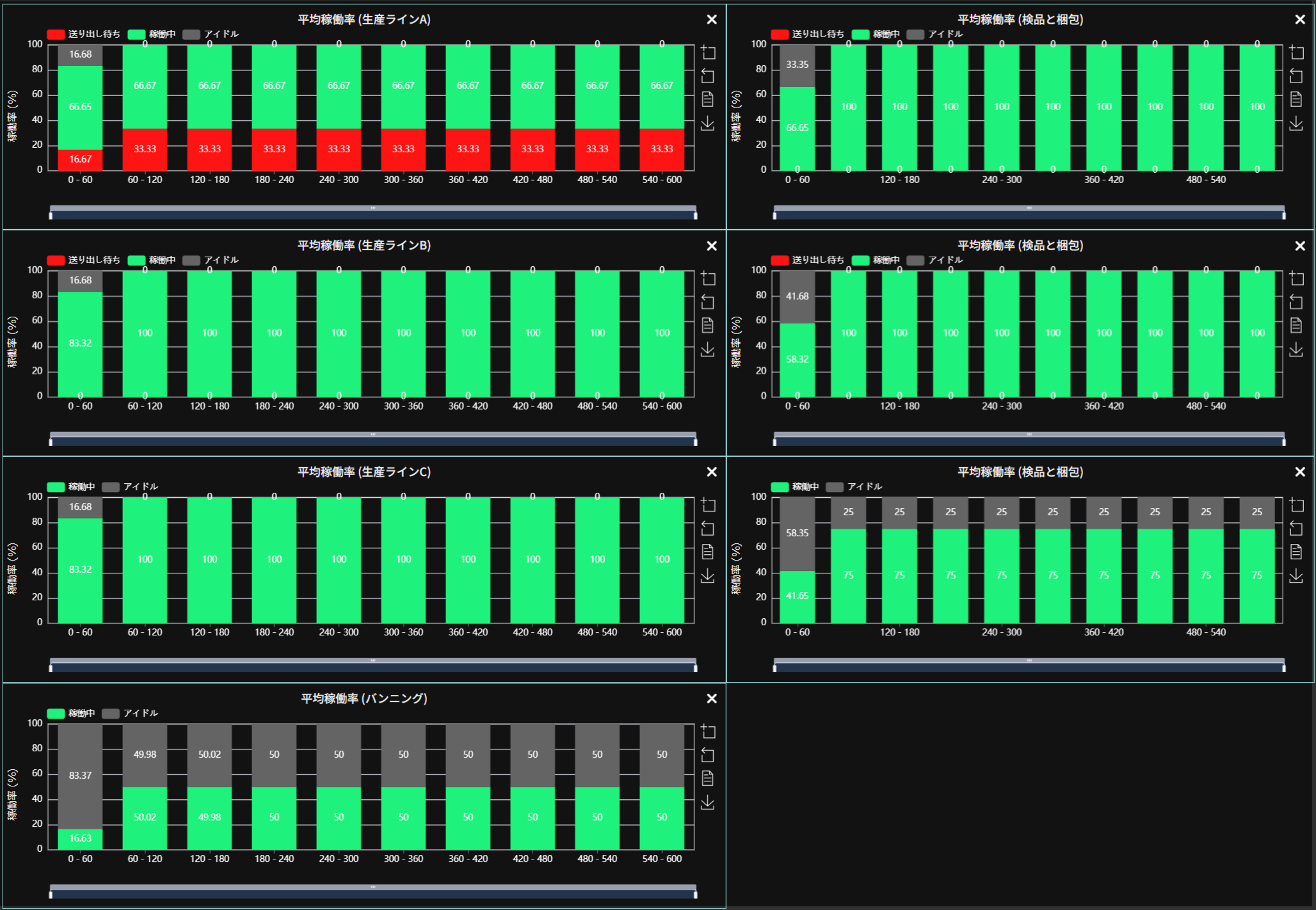
すると以下のようなことが判明しました。
・「007生産ラインA」は基本的に稼働率が高くなっているのに加えて、下流側の梱包と検品へ作った部品が流れず送り出し待ちが生じている
・「016生産ラインB」は基本的に稼働中
・「019生産ラインC」は基本的に稼働中
・「011バンニング」も稼働率にはまだ余裕があるが、倍の生産量(60セット)までしか対応できなさそう
さらに他の部分もないか上流側に遡って調べてみます。入荷品を解包しているデバンニングも調べる必要があります。
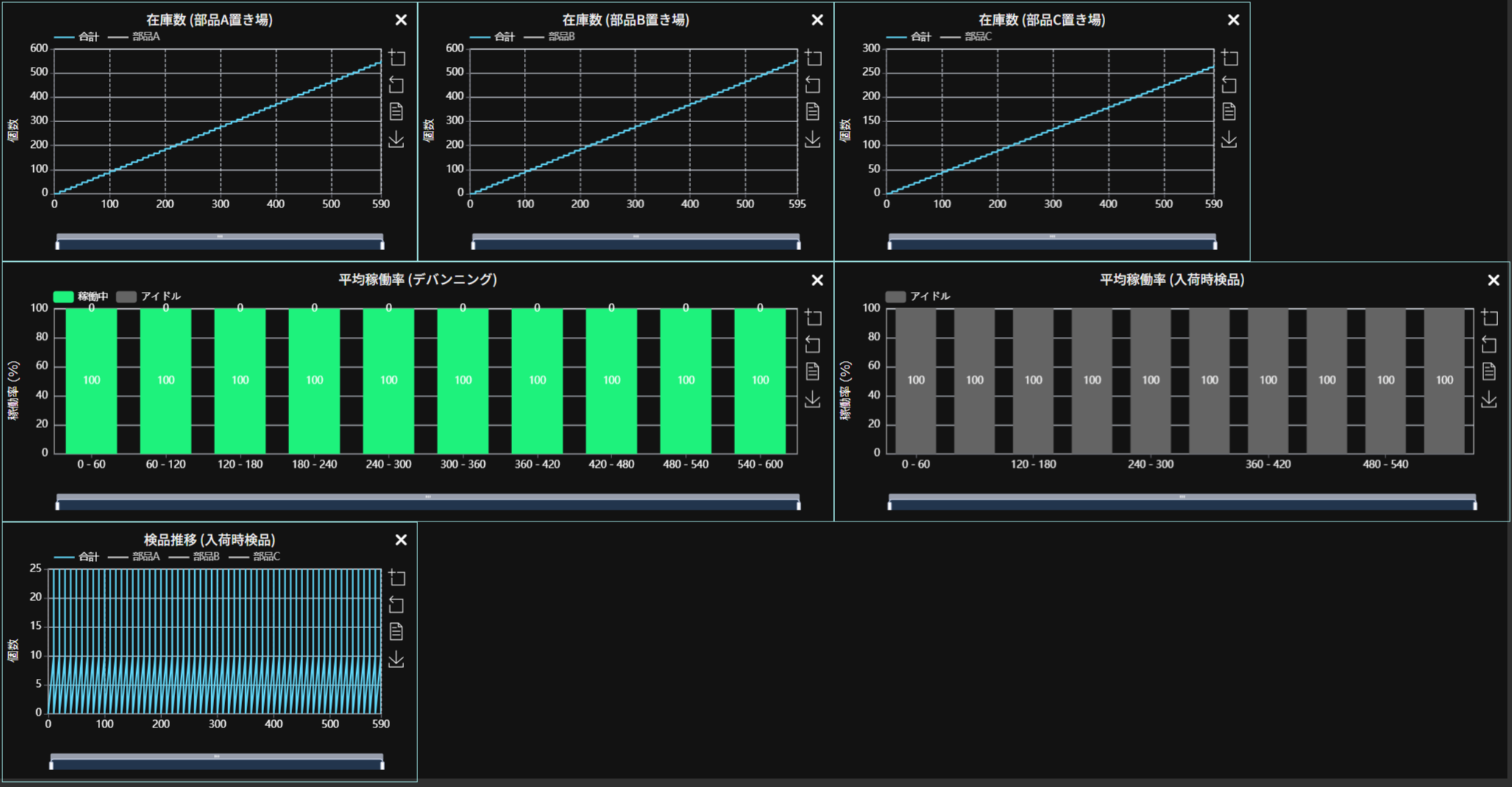
上図は生産ラインの入り口にあたる部品A~Cの置き場の在庫数(「006部品A置き場」、「015部品B置き場」、「018部品C置き場」)、さらに上流側の「002入荷品置き場」の在庫数、「003デバンニング」、「004入荷時検品」の稼働率を示しています。ここから分かることは以下の通りになります。
・3つの置き場の在庫数のグラフから、生産ラインに流れる部品が置いてある部品A~Cの置き場の在庫はほとんど無い
・デバンニングの稼働率のグラフから、デバンニングがほぼbusyで動いており、直上流にある入荷品置き場の在庫が増加している
・入荷時検品にはBlockedが発生していない
よって人員が足りないプロセスは
「003デバンニング」、「007生産ラインA」、「016生産ラインB」、「019生産ラインC」、「008検品と梱包」、「017検品と梱包」、「020検品と梱包」、「011バンニング」となると考えられます。
現在、8つのプロセスの人員数はどれもデフォルト(1人)なので、これを増加させることで、解決してみましょう。
人の最適化
前回保存したモデルから新規課題として新プロジェクトで人の最適化を立ち上げるとパラメーター設定の手間が少なく、効率的に作業を進めることが出来ます。最適化はプロセスカードの選択、上下限値の選択、パラメーターの設定の手順で行います。
まず、最適化を行うプロセスカードを選択します。ここでは「003デバンニング」、「007生産ラインA」、「016生産ラインB」、「019生産ラインC」、「008検品と梱包」、「017検品と梱包」、「020検品と梱包」、「011バンニング」を選択します。
次に人員数の下限値と上限値を決めます。下限値は現在の値である「1人」です。現状の出荷数を10倍へ増やすと考えると、上限値は「10人」で十分そうですが、「019生産ラインC」で20分、「020検品と梱包」で15分が処理にかかっているため、この分も考えて部品Cから製品Cを作るプロセス(「019生産ラインC」と「020検品と梱包」)では多めに見て上限を「20人」としてみます。これは今回は製品Cの材料となる部品Cの入荷量はA、Bと比べても一番少ないにもかかわらず、出荷には製品A、B、Cがそれぞれ1つ必要なことから、製品Cの量が全体の出荷量を決定する要素と考えられるからです。また、今回は時間帯別の配置や人数は無限に増やせると考えて最大人数などは考慮しないことにします。
最後に、人の最適化を行う前に出荷目標を立てます。今回は現状の出荷量の10倍に相当する、60分間に30個の製品を出荷する目標を立てて、これをパラメーター設定の際に出荷プロセスに出荷データとして入力します。
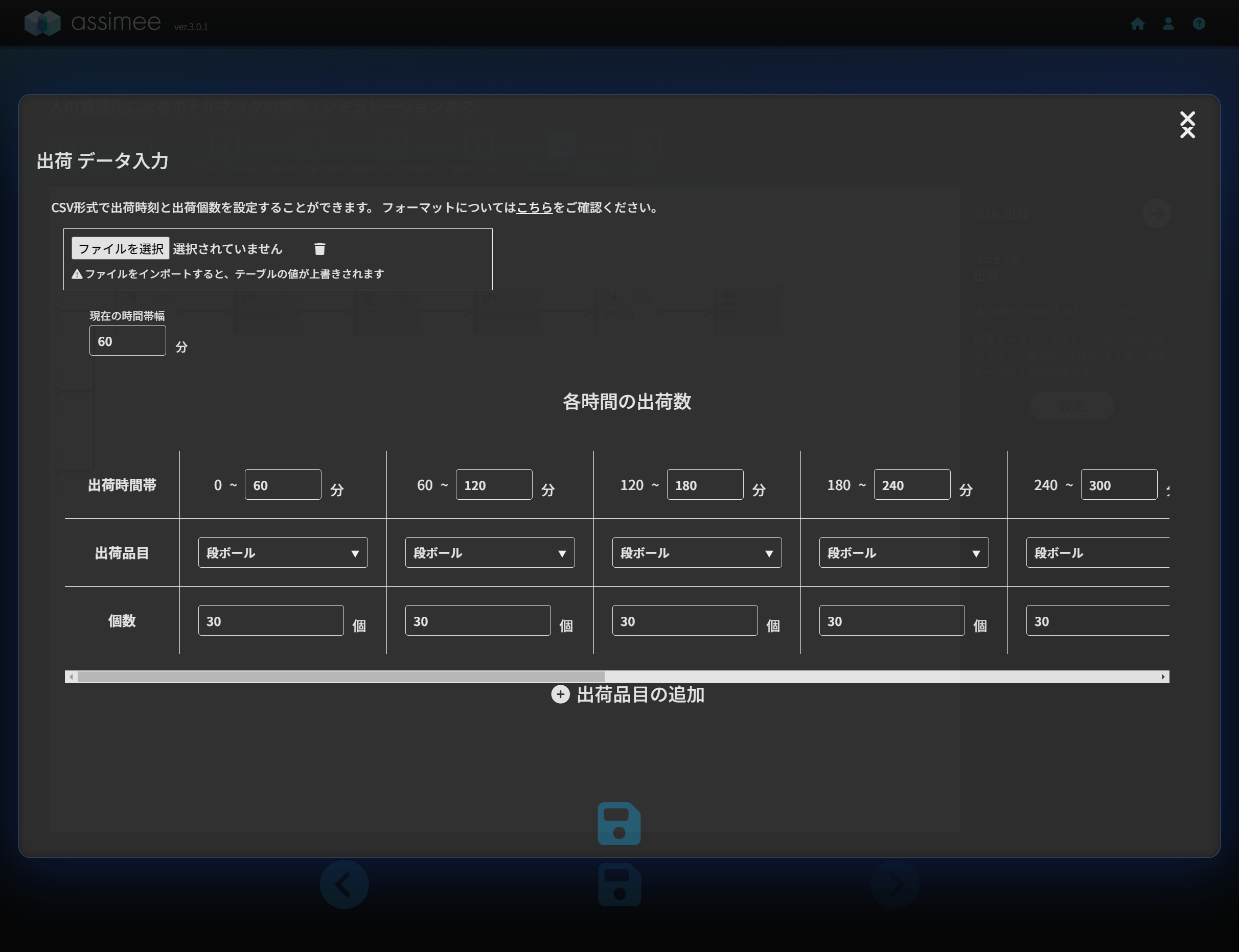
最適化結果
人の最適化の結果は以下のようになりました。
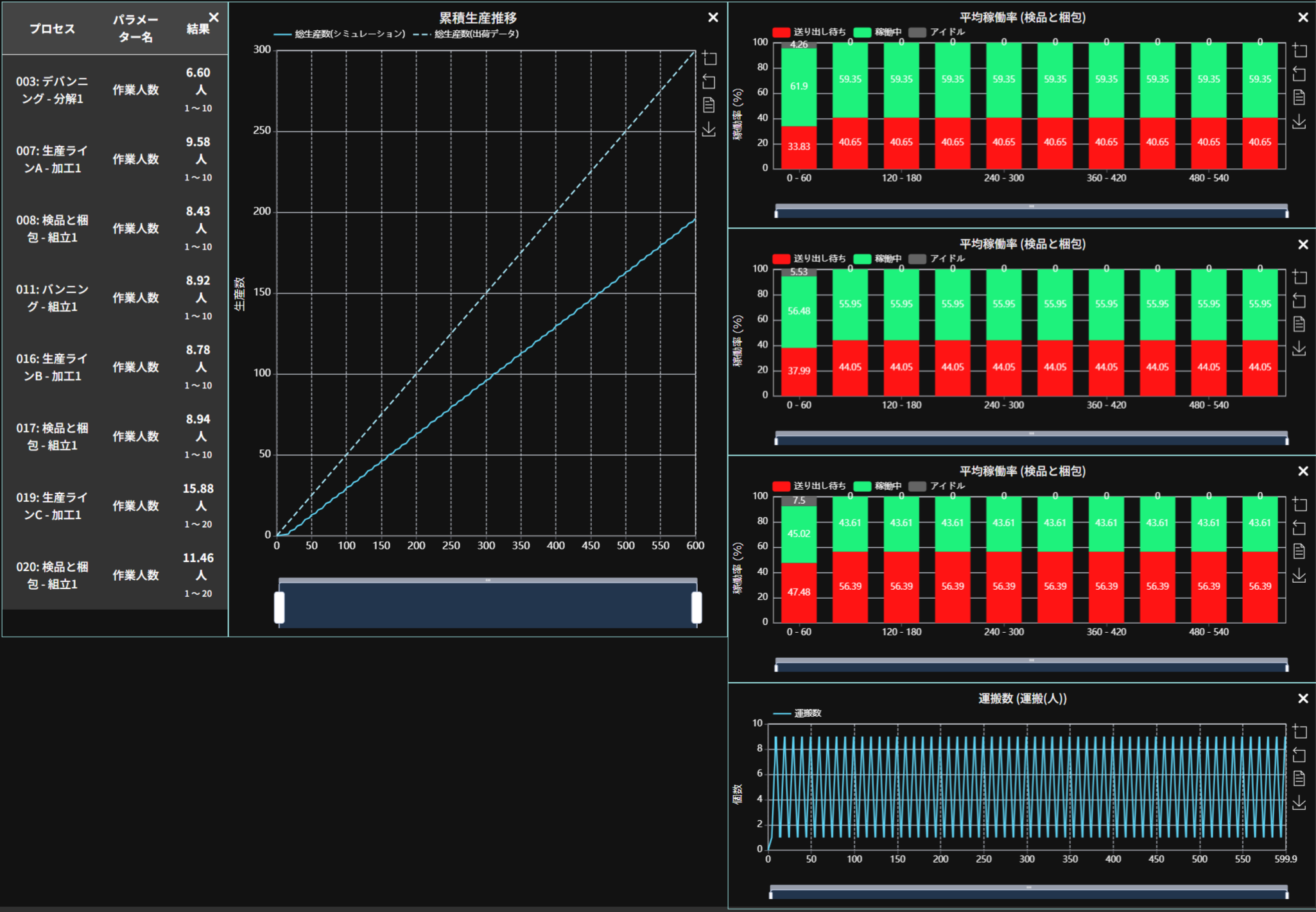
最初の設定よりは出荷量が増えていますが、目標の66%しか達成できていません。状況を再度確認すると、3か所の「検品と梱包」に送り出し待ちが発生しています。原因を調査してみると「009運搬(人)」の処理能力がどうやら足りないことが分かりました。人の最適化では最適化対象に「009運搬(人)」の人数は入れられないので、ここはパラメーター設定を見直し、人数を「20人」、最大運搬量を「20個」に変更します。
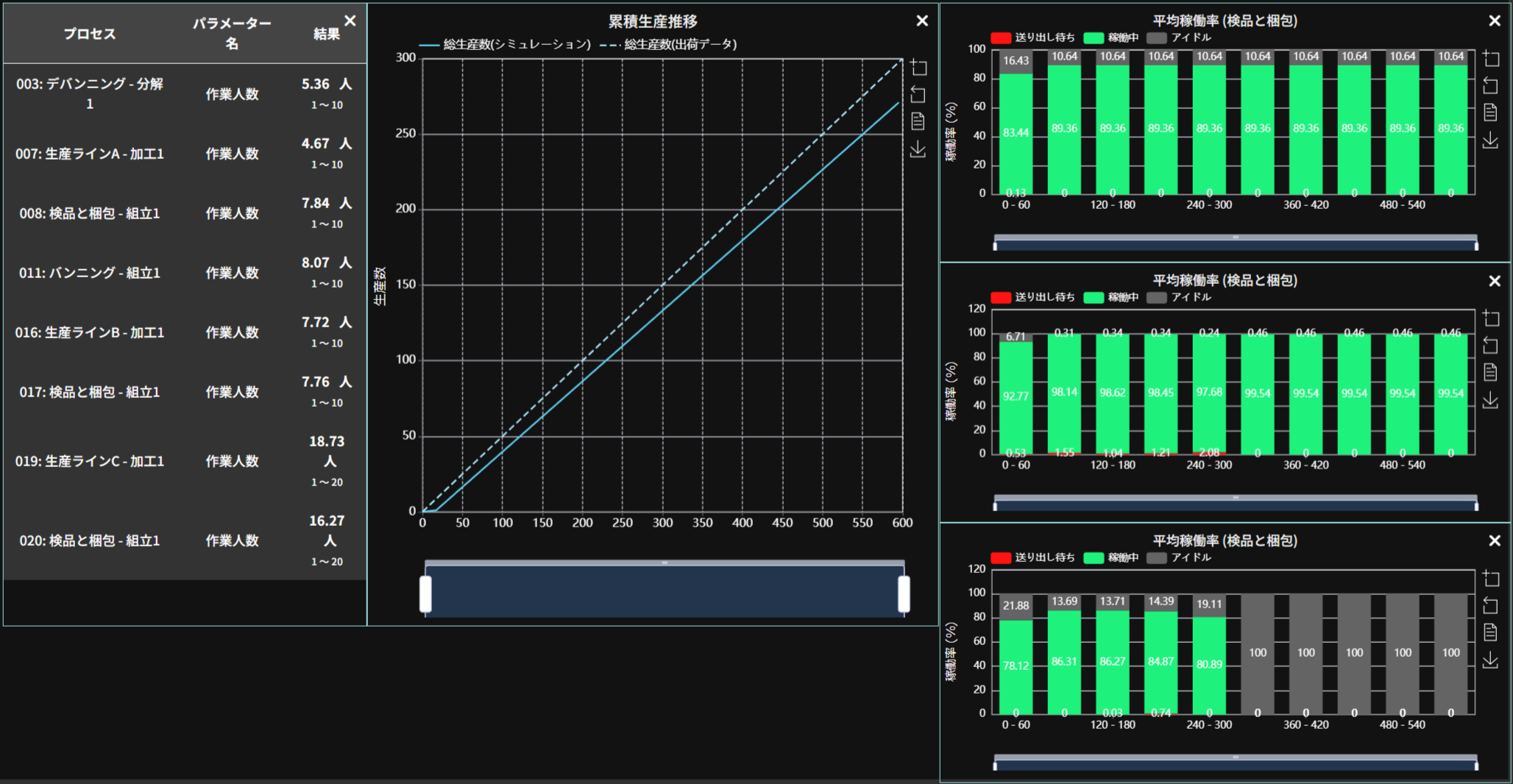
再度の最適化の結果、出荷量300個に対して270個と、目標達成に近づくことが出来ました。このように、ボトルネックとなっている箇所を分析で探しながら、パラメーターの最適化を繰り返すことで、容易に最適な人員数を求めることが出来ました。
まとめ
今回はシミュレーションで見つかったボトルネックを人員増加で解消して出荷量を増やす方法について解説しました。現実には無限に人員を増やすことは難しいため、このようなアプローチが常に無制限に適用可能なわけではありません。出荷目標や人員数の上限を考えて、その都度最善の配置を考える必要があります。今回は使いませんでしたが、assimeeでは人員数の上限などを最適化の際の条件としてかけることも可能なっています。
assimeeはブラウザさえあればどこでも利用可能で、非常に動作が軽いため、このように頻繁に人員配置などを見直す際には大いに役立ちます。
assimeeでは、実際の製造プロセスをモデル化し、シミュレーションすることで、プロセスの見える化や潜在的な課題の洗い出しを行うことができます。製造プロセスのデジタル化や課題解決でお悩みの方は、ぜひお問い合わせください。