概要
最近ではコンビニやスーパーで売られている食品の加工を物流倉庫と一体化したセントラルキッチンで行い、各地の店舗へ配送するケースが増加しています。今回の記事ではこのようなPDC型物流倉庫内に設置された食品工場を想定したモデルを作成します。
モデルの作成
物流倉庫としてはPDCに相当するので、入荷→加工→入庫→出庫→出荷の5段階のプロセスが基本となります。今回は倉庫内で食品の下処理と調理、チルド加工と入庫、ピッキングによる出庫、バンニングと出荷を考える他、複数の食材(人参、玉葱、じゃが芋、牛肉、調味料)から、製品としてカレーと野菜炒め、肉じゃがを調理し、コンビニ、スーパー、レストランと複数の店舗へ向けた出荷を行うモデルを作成します。
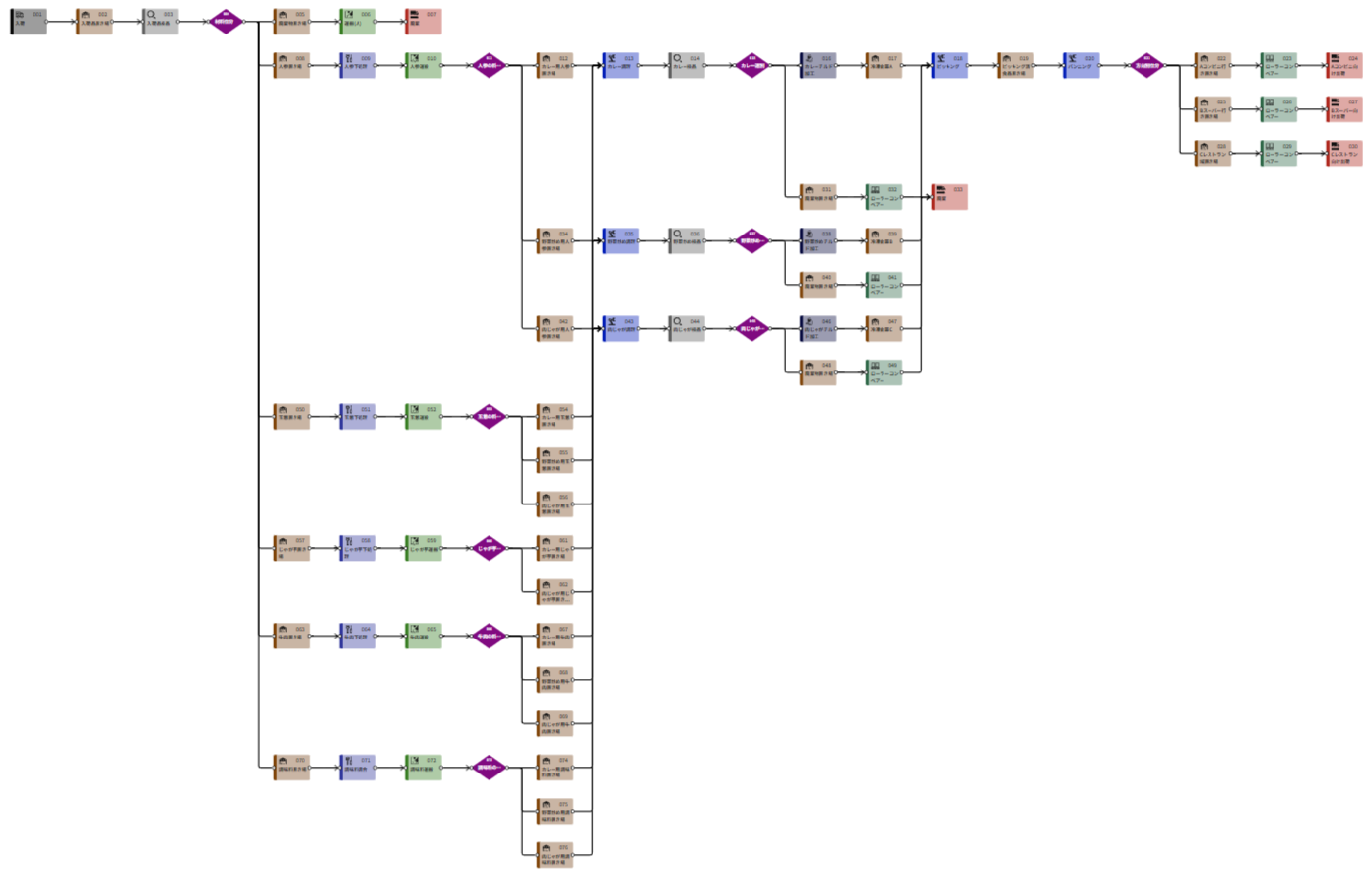
今回のモデルは非常に大きくなるため、以下の4つのブロックに分けてプロセスの設置と設定の解説を行います。
・入荷ブロック
・下処理ブロック
・調理と入庫ブロック
・出庫と出荷ブロック
STEP1 プロセス図の作成

入荷ブロックは入荷→置き場→検品→分岐のプロセスからなり、以下のように配置し設定します。
入荷プロセス:
特に変更なし
置き場プロセス:
プロセス名称を「入荷品置き場」へ変更
検品プロセス:
プロセス名称を「検収」へ変更
分岐プロセス:
プロセス名称を「材料仕分」へ変更
置き場「廃棄物置き場」「人参置き場」「玉葱置き場」「じゃが芋置き場」「牛肉置き場」「調味料置き場」に分岐
下処理ブロック
下処理ブロックは入荷ブロックの材料仕分けの後に配置します。「廃棄物」、「人参」、「玉葱」、「牛肉」、「じゃが芋」、「調味料」の5つの小ブロックに分けて解説します。
廃棄物小ブロック
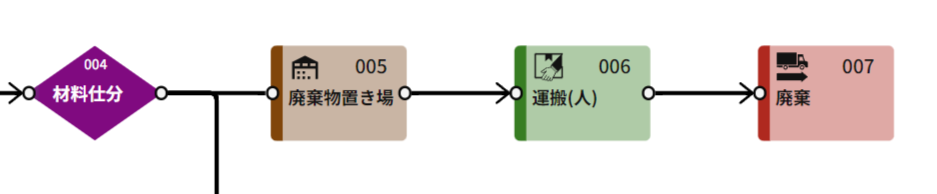
検収時の不合格品の廃棄を想定し、置き場→運搬(人)→出荷の各プロセスを配置します。
置き場プロセス:
プロセス名称を「廃棄物置き場」へ変更
運搬(人)プロセス:
特に変更なし
出荷プロセス:
プロセス名称を「廃棄」へ変更
人参下処理小ブロック
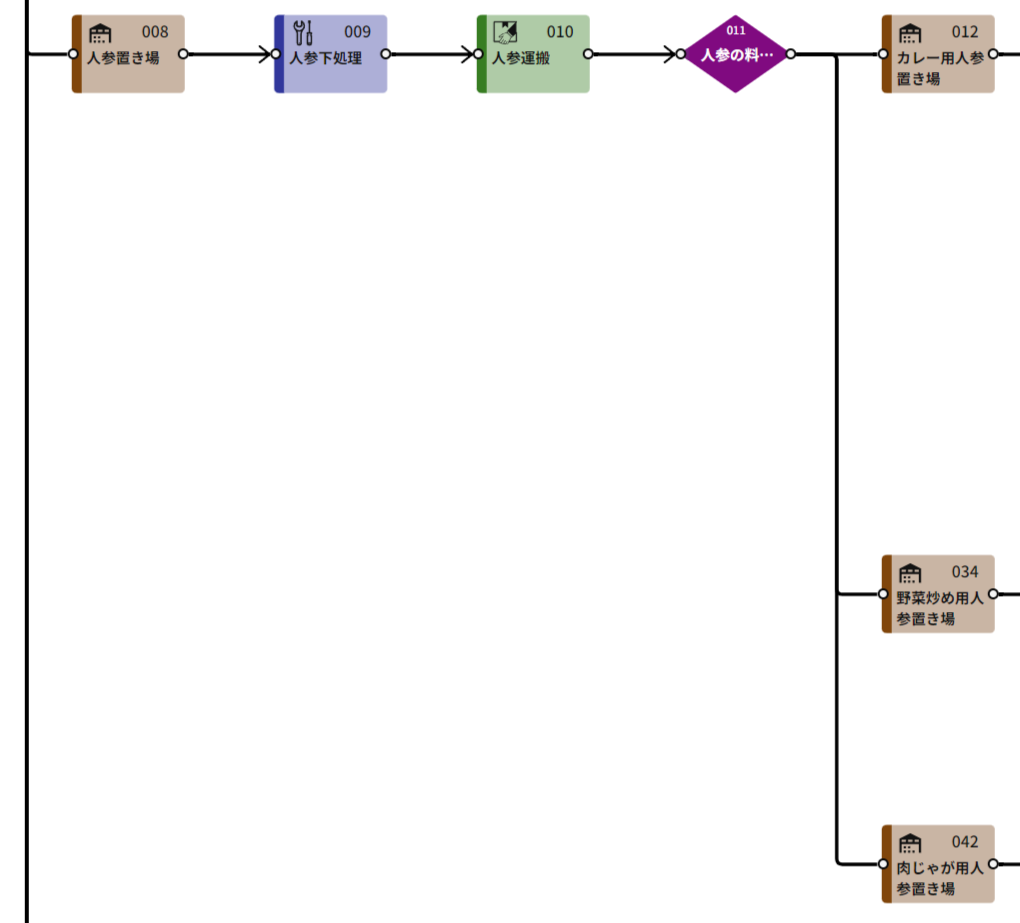
人参の下処理を想定し、置き場→加工→運搬(人)→分岐→置き場の各プロセスを配置します。
置き場プロセス:
プロセス名称を「人参置き場」へ変更
作業プロセス:
プロセス名称を「人参下処理」へ変更
運搬(人)プロセス:
プロセス名称を「人参運搬」へ変更
分岐プロセス:
プロセス名称を「人参の料理別分岐」へ変更
分岐プロセスの分岐先:
料理別になるように以下の3つの置き場を「人参の料理別分岐後」に配置
1つ目の置き場:
・プロセス名称を「カレー用人参置き場」へ変更
2つ目の置き場:
・プロセス名称を「野菜炒め用人参置き場」へ変更
3つ目の置き場:
・プロセス名称を「肉じゃが用人参置き場」へ変更
玉葱下処理小ブロック
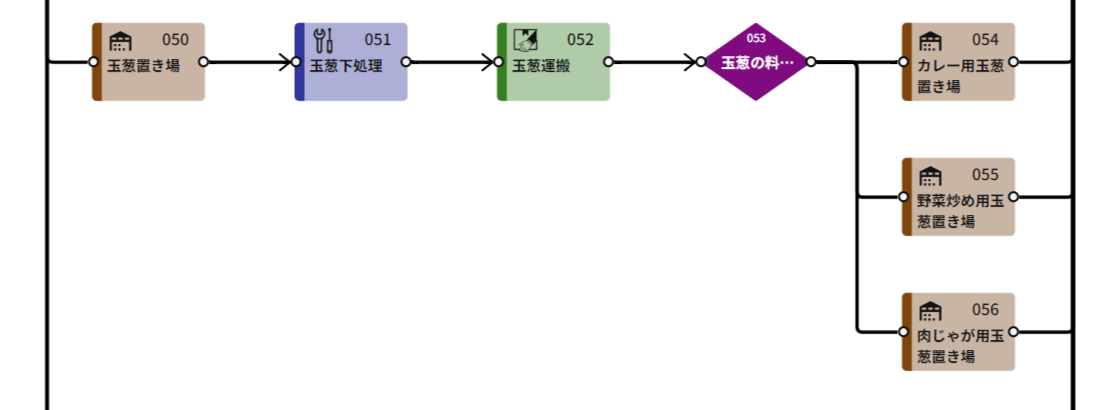
玉葱の下処理を想定し、置き場→加工→運搬(人)→分岐→置き場の各プロセスを配置します。
置き場プロセス:
プロセス名称を「玉葱置き場」へ変更
作業プロセス:
プロセス名称を「玉葱下処理」へ変更
運搬(人)プロセス:
プロセス名称を「玉葱運搬」へ変更
分岐プロセス:
プロセス名称を「料理別分岐」へ変更
分岐プロセスの分岐先:
料理別になるように以下の3つの置き場を「玉葱の料理別分岐」後に配置
1つ目の置き場:
・プロセス名称を「カレー用玉葱置き場」へ変更
2つ目の置き場:
・プロセス名称を「野菜炒め用玉葱置き場」へ変更
3つ目の置き場:
・プロセス名称を「肉じゃが用玉葱置き場」へ変更
じゃが芋下処理小ブロック
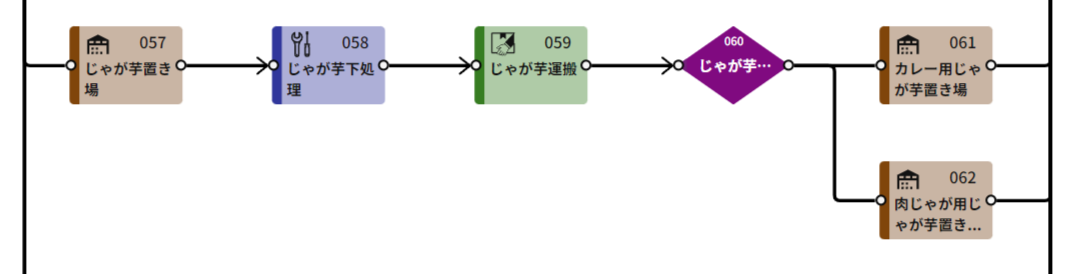
じゃが芋の下処理を想定し、置き場→加工→運搬(人)→分岐→置き場の各プロセスを配置します。
置き場プロセス:
プロセス名称を「じゃが芋置き場」へ変更
作業プロセス:
プロセス名称を「じゃが芋下処理」へ変更
運搬(人)プロセス:
プロセス名称を「じゃが芋運搬」へ変更
分岐プロセス:
プロセス名称を「じゃが芋の料理別分岐」へ変更
分岐プロセスの分岐先:
料理別になるように以下の2つの置き場を「じゃが芋の料理別分岐」後に配置(野菜炒めにはじゃが芋を使わないので2つ)
1つ目の置き場:
・プロセス名称を「カレー用じゃが芋置き場」へ変更
2つ目の置き場:
・プロセス名称を「肉じゃが用じゃが芋置き場」へ変更
牛肉下処理小ブロック
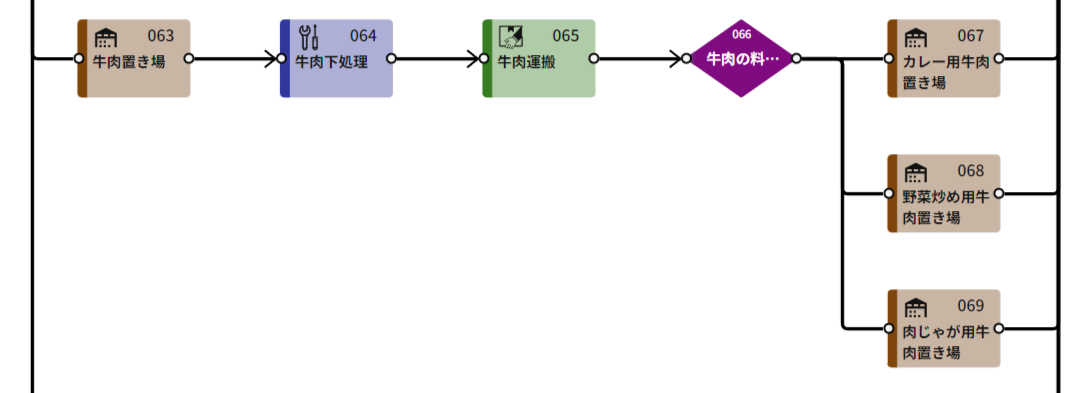
牛肉の下処理を想定し、置き場→加工→運搬(人)→分岐→置き場の各プロセスを配置します。
置き場プロセス:
プロセス名称を「牛肉置き場」へ変更
作業プロセス:
プロセス名称を「牛肉下処理」へ変更
運搬(人)プロセス:
プロセス名称を「牛肉運搬」へ変更
分岐プロセス:
プロセス名称を「牛肉の料理別分岐」へ変更
分岐プロセスの分岐先:
料理別になるように以下の3つの置き場を「牛肉の料理別分岐」後に配置
1つ目の置き場:
・プロセス名称を「カレー用牛肉置き場」へ変更
2つ目の置き場:
・プロセス名称を「野菜炒め用牛肉置き場」へ変更
3つ目の置き場:
・プロセス名称を「肉じゃが用牛肉置き場」へ変更
調味料準備小ブロック
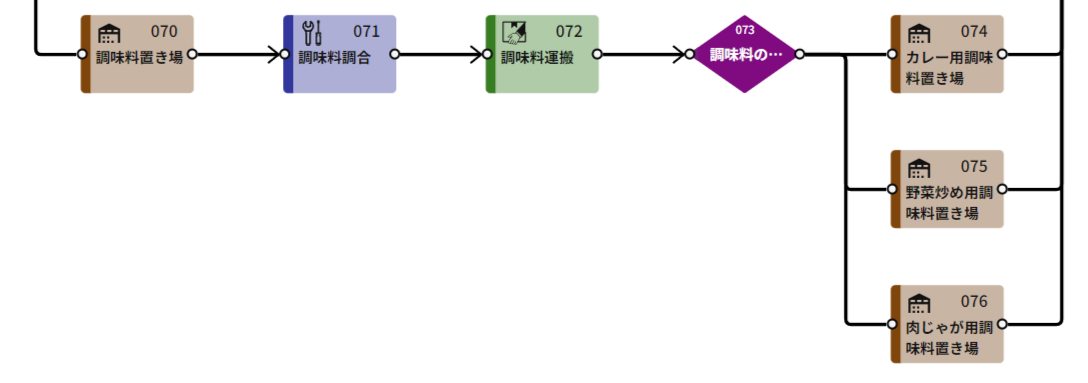
調味料の準備を想定し、置き場→加工→運搬(人)→分岐→置き場の各プロセスを配置します。
置き場プロセス:
プロセス名称を「調味料置き場」へ変更
作業プロセス:
プロセス名称を「調味料調合」へ変更
運搬(人)プロセス:
プロセス名称を「調味料運搬」へ変更
分岐プロセス:
プロセス名称を「調味料の料理別分岐」へ変更
分岐プロセスの分岐先:
料理別になるように以下の3つの置き場を「調味料の料理別分岐」後に配置
1つ目の置き場:
・プロセス名称を「カレー用調味料置き場」へ変更
2つ目の置き場:
・プロセス名称を「野菜炒め用調味料置き場」へ変更
3つ目の置き場:
・プロセス名称を「肉じゃが用調味料置き場」へ変更
調理と入庫ブロック
カレーと野菜炒め、肉じゃがの調理を行います。
下処理ブロックで用意した材料から調理を行い、検品と不良品の破棄、合格品のチルド加工と冷蔵倉庫への入庫までを想定し、組立→検品→分岐→合格品側:加工→置き場(入庫)、廃棄物側:置き場→運搬(ローラーコンベア)→出荷(破棄)のようにプロセスを配置します。
カレー調理小ブロック
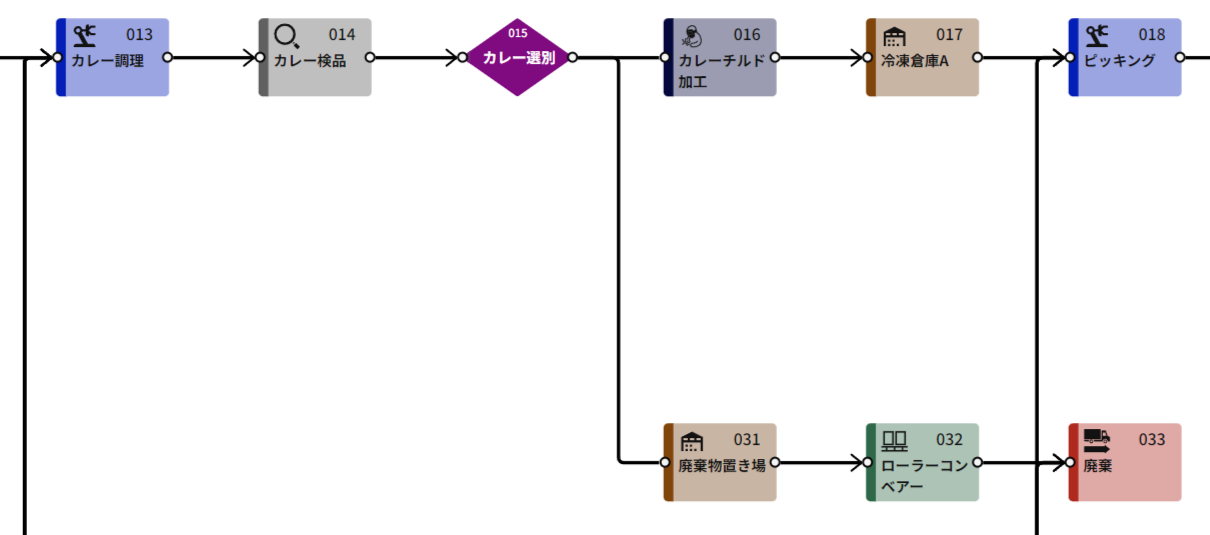
組立プロセス:
プロセス名称を「カレー調理」へ変更
検品プロセス:
プロセス名称を「カレー検品」へ変更
分岐プロセス:
プロセス名称を「合格品カレー選別」へ変更
分岐プロセスの分岐先:
料理別になるように以下の2つのプロセスを「合格品カレー選別」後に配置
1つ目、加工プロセス:
・プロセス名称を「カレーチルド加工」へ変更
2つ目、置き場:
・プロセス名称を「廃棄物置き場」へ変更
(カレーチルド加工の後)置き場プロセス:
プロセス名称を「冷凍倉庫A」へ変更
(廃棄物置き場の後)運搬(ローラーコンベア)プロセス:
特に設定なし
(廃棄物置き場の後)出荷プロセス:
プロセス名を「廃棄」へ変更
野菜炒め調理小ブロック
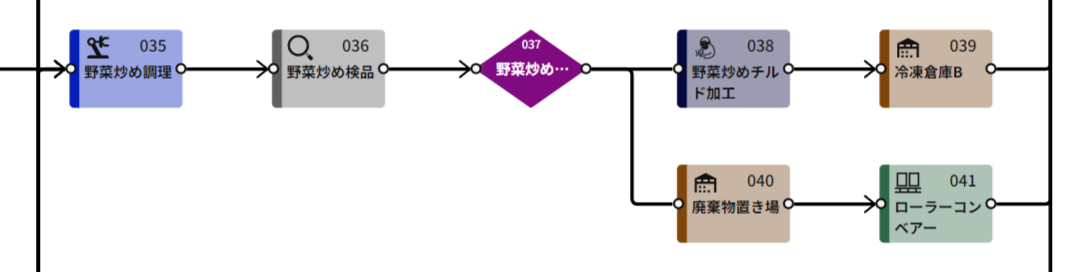
組立プロセス:
プロセス名称を「野菜炒め調理」へ変更
検品プロセス:
プロセス名称を「野菜炒め検品」へ変更
分岐プロセス:
プロセス名称を「合格品野菜炒め選別」へ変更
分岐プロセスの分岐先:
料理別になるように以下の2つのプロセスを「合格品野菜炒め選別」後に配置
1つ目、加工プロセス:
・プロセス名称を「野菜炒めチルド加工」へ変更
2つ目、置き場:
・プロセス名称を「廃棄物置き場」へ変更
(野菜炒めチルド加工の後)置き場プロセス:
プロセス名称を「冷凍倉庫A」へ変更
(廃棄物置き場の後)運搬(ローラーコンベア)プロセス:
特に設定なし
「廃棄」へ接続
肉じゃが小ブロック
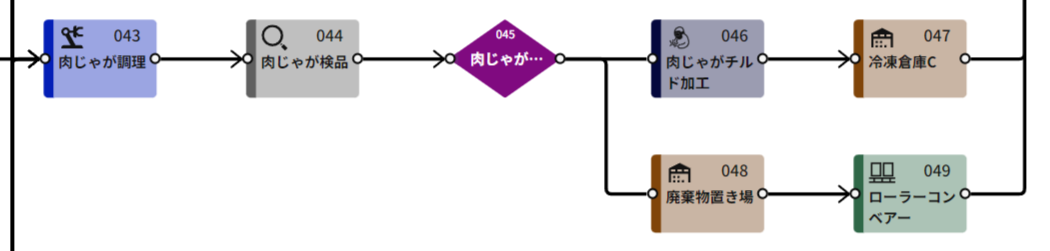
組立プロセス:
プロセス名称を「肉じゃが調理」へ変更
検品プロセス:
プロセス名称を「肉じゃが検品」へ変更
分岐プロセス:
プロセス名称を「合格品肉じゃが選別」へ変更
分岐プロセスの分岐先:
料理別になるように以下の2つのプロセスを「合格品肉じゃが選別」後に配置
1つ目、加工プロセス:
・プロセス名称を「肉じゃがチルド加工」へ変更
2つ目、置き場:
・プロセス名称を「廃棄物置き場」へ変更
(肉じゃがチルド加工の後)置き場プロセス:
プロセス名称を「冷凍倉庫B」へ変更
(廃棄物置き場の後)運搬(ローラーコンベア)プロセス:
特に設定なし
「廃棄」へ接続
出庫と出荷ブロック
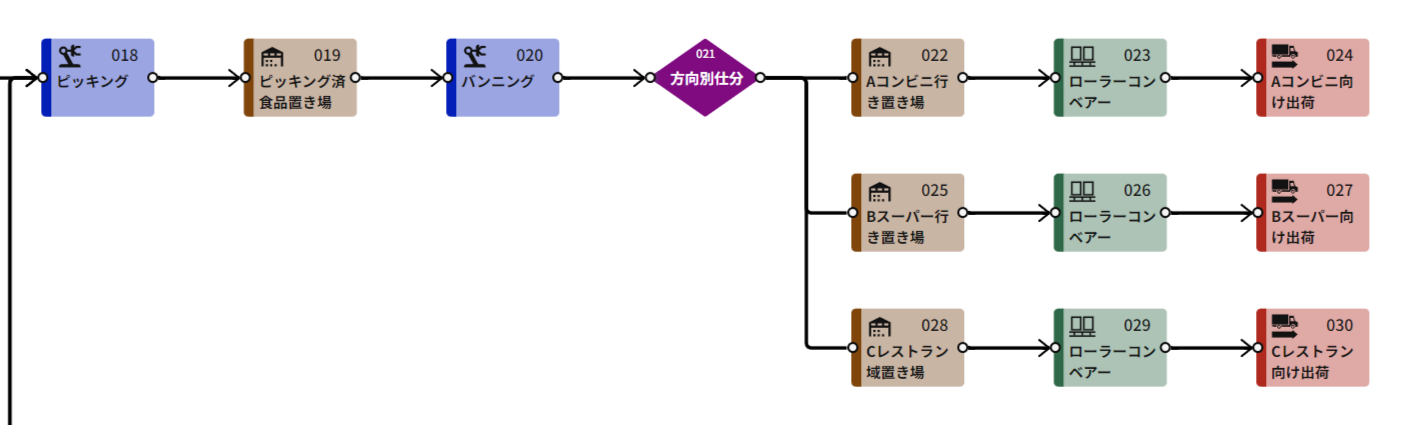
冷凍倉庫3箇所からのピッキングとバンニング、方向別仕分けまでを考えて、合流→組立→置き場→組立→分岐の各プロセスを図のように配置し、設定します。
合流プロセス:*合流プロセスのカードは表示されません。
冷凍倉庫A、冷凍倉庫B、冷凍倉庫Cの各プロセスから組立プロセスへ接続
組立プロセス:
プロセス名称を「ピッキング」へ変更
置き場プロセス:
プロセス名称を「ピッキング済食品置き場」へ変更
組立プロセス:
プロセス名称を「バンニング」へ変更
分岐プロセス:
プロセス名称を「方向別仕分」へ変更
分岐プロセスの分岐先:
料理別になるように以下の3つの置き場を「方向別仕分」後に配置
1つ目の置き場:
・プロセス名称を「Aコンビニ行き置き場」へ変更
2つ目の置き場:
・プロセス名称を「Bスーパー行き置き場」へ変更
3つ目の置き場:
・プロセス名称を「Cレストラン行き置き場」へ変更
次に配置した分岐プロセス以降に3つの行先(Aコンビニ、Bスーパー、Cレストラン)に分け、それぞれに置き場→運搬(ローラーコンベア)→出荷の順に配置します。
Aコンビニ向け
(Aコンビニ)置き場プロセス:
プロセス名称を「Aコンビニ行き置き場」へ変更
(Aコンビニ)運搬(ローラーコンベア)プロセス:
特に変更なし
(Aコンビニ)出荷プロセス:
プロセス名を「Aコンビニ向け出荷」へ変更
Bスーパー向け
(Bスーパー)置き場プロセス:
プロセス名称を「Bスーパー行き置き場」へ変更
(Bスーパー)運搬(ローラーコンベア)プロセス:
特に変更なし
(Bスーパー)出荷プロセス:
プロセス名を「Bスーパー向け出荷」へ変更
Cレストラン向け
(Cレストラン)置き場プロセス:
プロセス名称を「Cレストラン行き置き場」へ変更
(Cレストラン)運搬(ローラーコンベア)プロセス:
特に変更なし
(Cレストラン)出荷プロセス:
プロセス名を「Cレストラン向け出荷」へ変更
STEP2 パラメーターの設定
入荷ブロック
入荷ブロックは入荷→置き場→検品→分岐のプロセスからなり、以下のように配置し設定します。
001 入荷:
入荷品目を5つ設定、
1つ目の品目「人参」、個数「10個」、発生間隔「1分」、
2つ目の品目「玉葱」、個数「10個」、発生間隔「1分」、
3つ目の品目「じゃが芋」、個数「7個」、発生間隔「1分」、
4つ目の品目「牛肉」、個数「10個」、発生間隔「1分」、
5つ目の品目「調味料」、個数「1個」、発生間隔「1分」
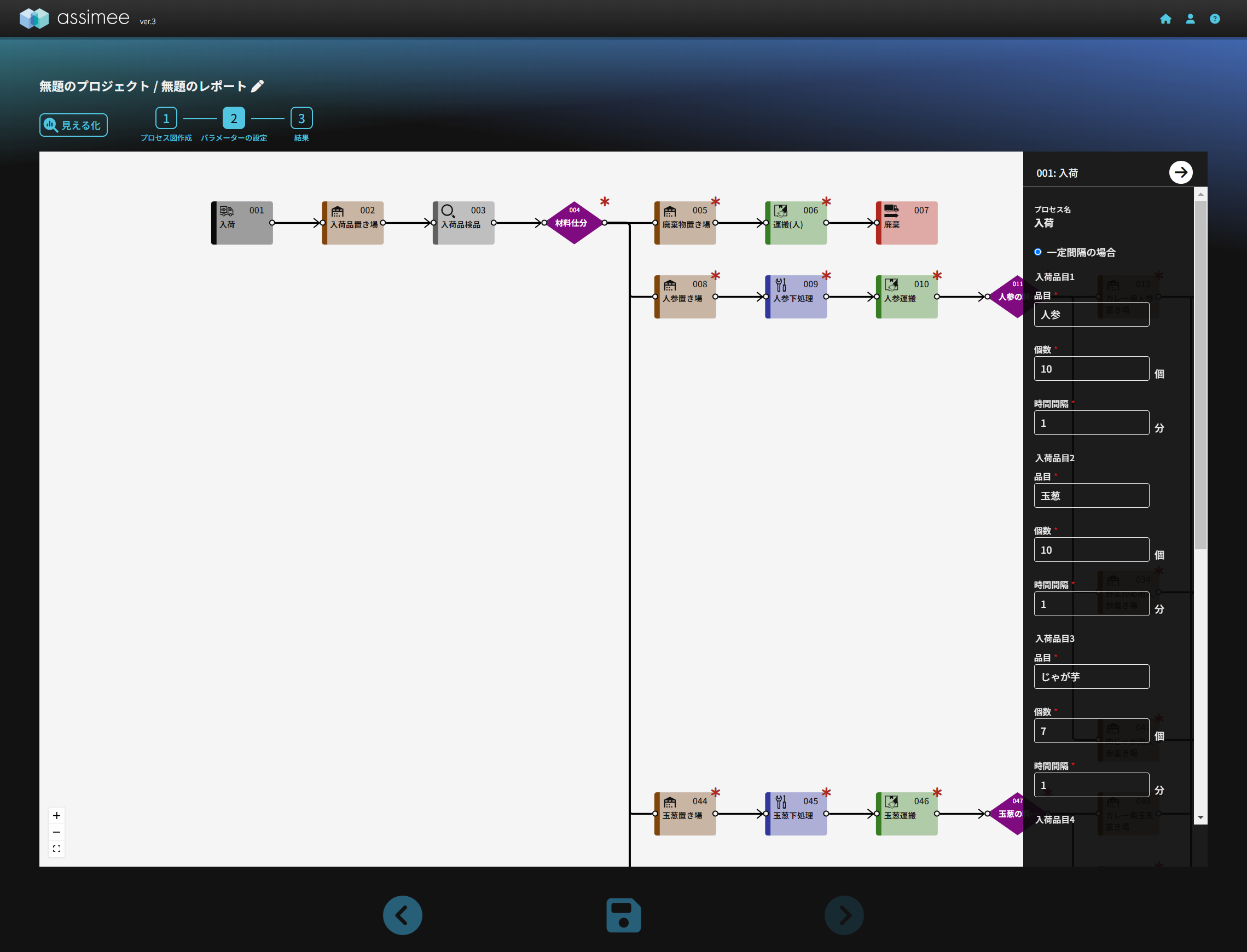
002 入荷品置き場:
容量を「1000個」と設定
003 検収:
不良品率を「1%」と設定、
下図のようにウィンドウ最大化から詳細設定画面を開き、作業員にチェックを入れ、1人あたりの処理時間を「1分」、作業人数を「50人」と設定
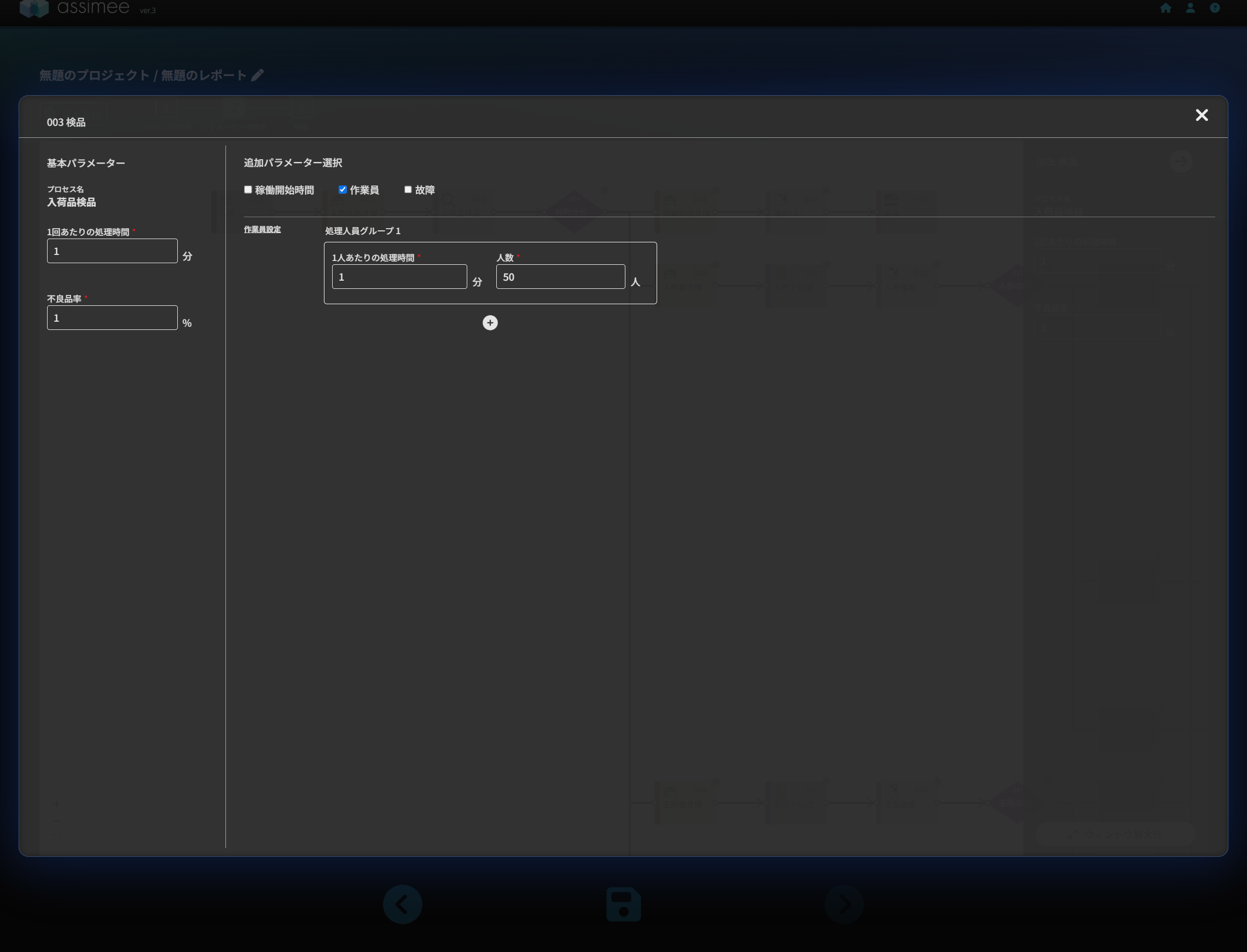
004 材料仕分:
下図の様にウィンドウ最大化から詳細設定画面を開き、作業員にチェックを入れ、1人あたりの処理時間を「1分」、作業人数を「50人」と設定
以下の分岐条件を設定
品目、正常:人参、送り先「008人参置き場」、
品目、不良:人参、送り先「005廃棄物置き場」、
品目、正常:玉葱、送り先「050玉葱置き場」、
品目、不良:玉葱、送り先「005廃棄物置き場」、
品目、正常:じゃが芋、送り先「057じゃが芋置き場」、
品目、不良:じゃが芋、送り先「005廃棄物置き場」、
品目、正常:牛肉、送り先「063牛肉置き場」、
品目、不良:牛肉、送り先「005廃棄物置き場」、
品目、正常:調味料、送り先「070調味料置き場」、
品目、不良:調味料、送り先「005廃棄物置き場」
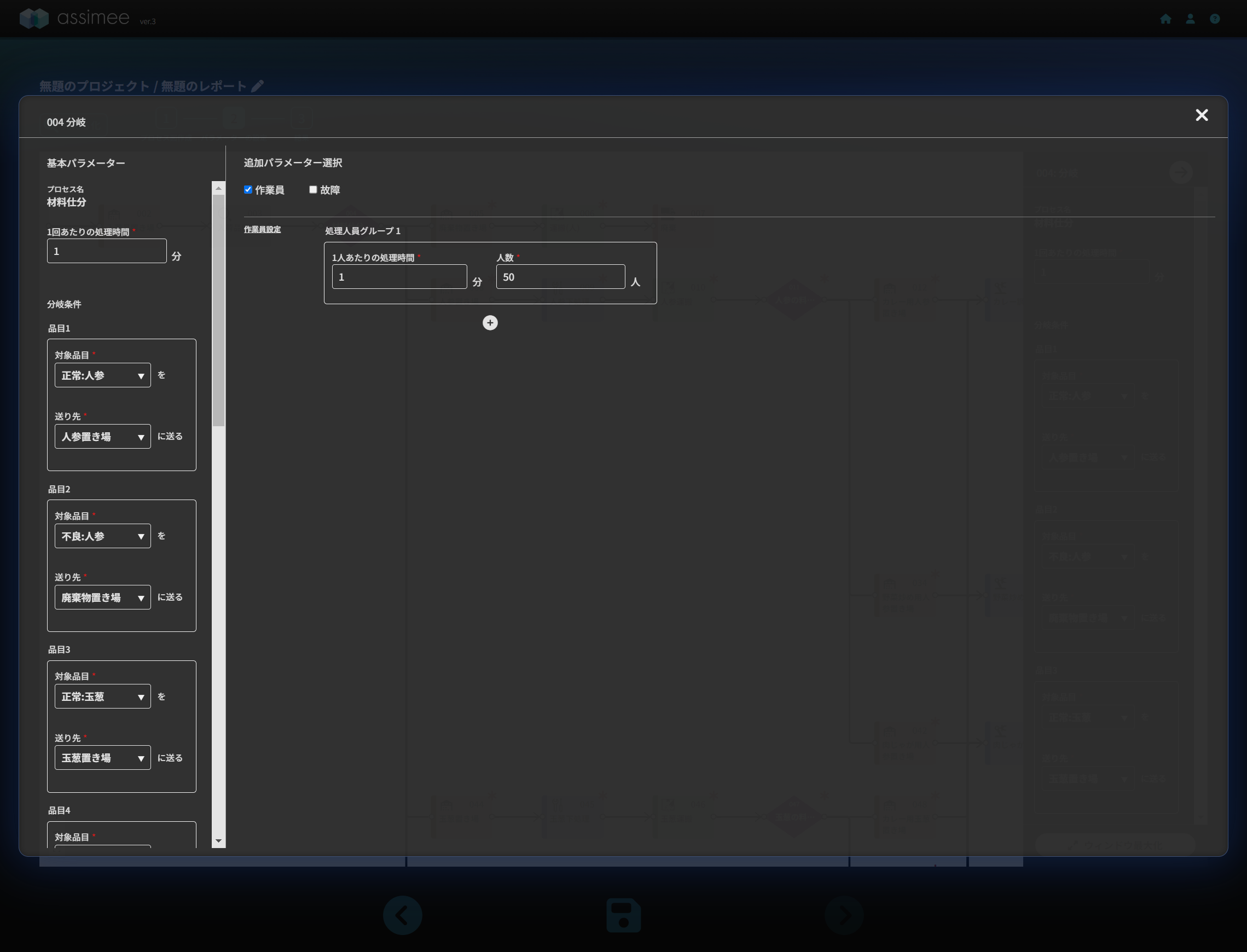
下処理ブロック
廃棄物小ブロック
005 廃棄物置き場:
容量を「1000個」と設定
006 運搬(人):
最大運搬量を「10個」、人数を「10人」、運搬時間(片道)を「1分」と設定
007 廃棄:
特に設定なし
人参下処理小ブロック
008 人参置き場:
容量を「1000個」と設定
009 人参下処理:
対象品目を「人参」、個数を「100個」と設定、
下図の様にウィンドウ最大化から詳細設定画面を開き、作業員にチェックを入れ、1人あたりの処理時間を「1分」、作業人数を「10人」と設定
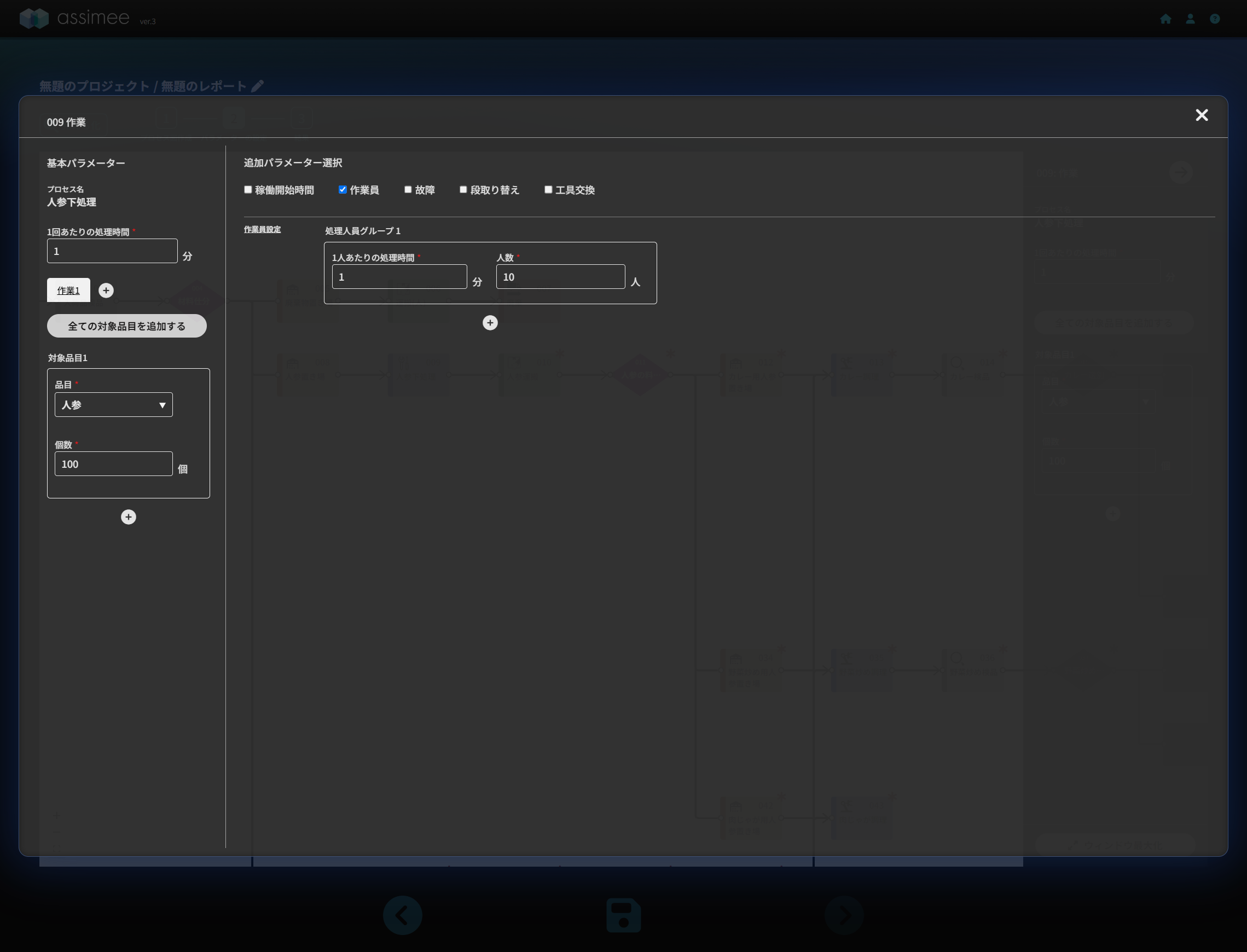
010 人参運搬:
最大運搬量を「150個」、人数を「10人」、運搬時間(片道)を「1分」と設定
011 人参の料理別分岐:
下図の様にウィンドウ最大化から詳細設定画面を開き、作業員にチェックを入れ、1人あたりの処理時間を「1分」、作業人数を「10人」と設定
分岐条件は設定せず(行先はランダム)
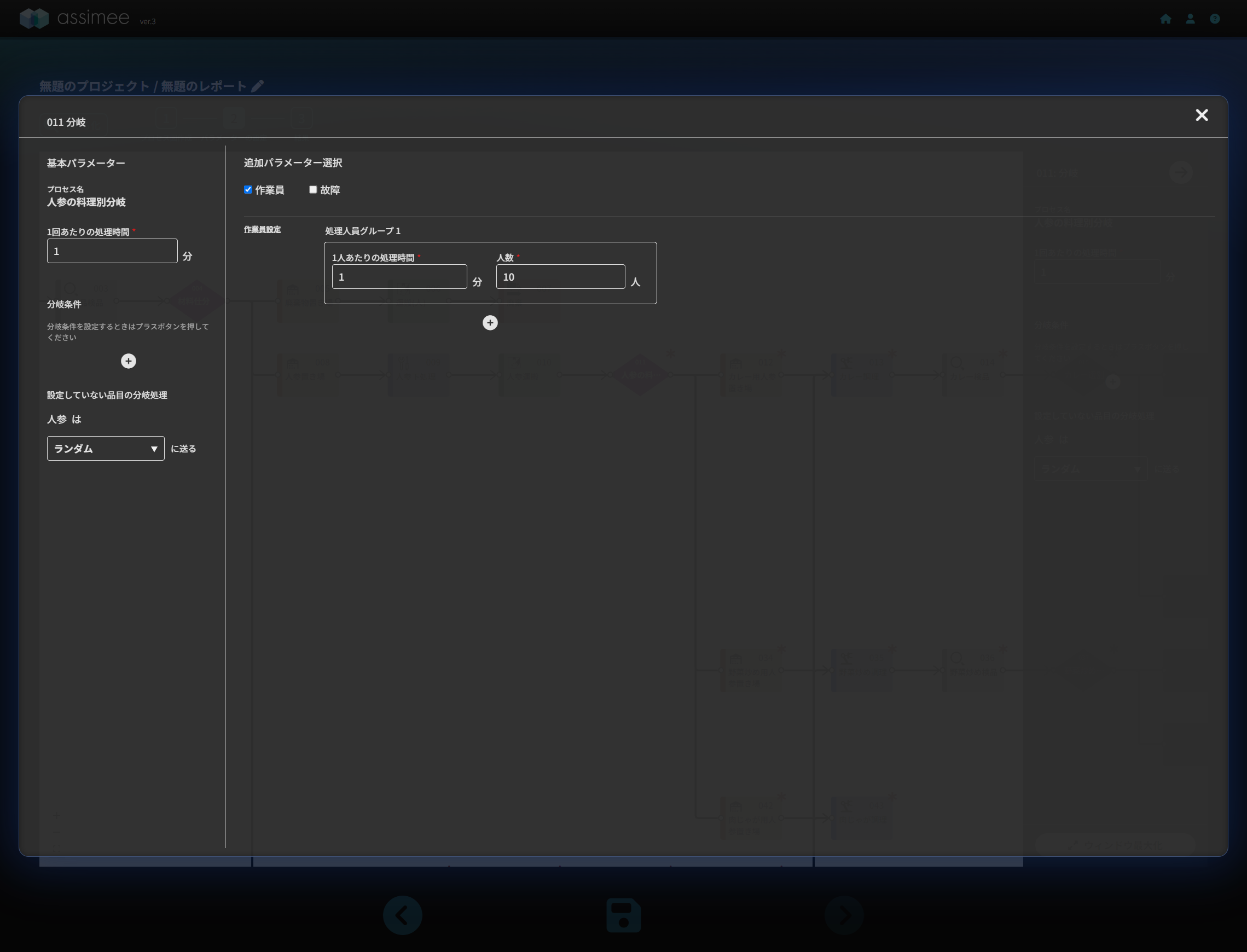
012 カレー用人参置き場:
容量を「1000個」と設定
013 野菜炒め用人参置き場:
容量を「1000個」と設定
014 肉じゃが用人参置き場:
容量を「1000個」と設定
玉葱下処理小ブロック
050 玉葱置き場:
容量を「1000個」と設定
051 玉葱下処理:
対象品目を「玉葱」、個数を「100個」と設定、
ウィンドウ最大化から詳細設定画面を開き、作業員にチェックを入れ、1人あたりの処理時間を「1分」、作業人数を「10人」と設定
052 玉葱運搬:
最大運搬量を「150個」、人数を「10人」、運搬時間(片道)を「1分」と設定
053 玉葱の料理別分岐:
ウィンドウ最大化から詳細設定画面を開き、作業員にチェックを入れ、1人あたりの処理時間を「1分」、作業人数を「10人」と設定
分岐条件は設定せず(行先はランダム)
054 カレー用玉葱置き場:
容量を「1000個」と設定
055 野菜炒め用玉葱置き場:
容量を「1000個」と設定
056 肉じゃが用玉葱置き場:
容量を「1000個」と設定
じゃが芋下処理小ブロック
057 じゃが芋置き場:
容量を「1000個」と設定
058 じゃが芋下処理:
対象品目を「じゃが芋」、個数を「100個」と設定、
ウィンドウ最大化から詳細設定画面を開き、作業員にチェックを入れ、
1人あたりの処理時間を「1分」、作業人数を「10人」と設定
059 じゃが芋運搬:
最大運搬量を「150個」、人数を「10人」、運搬時間(片道)を「1分」と設定
060 じゃが芋の料理別分岐:
ウィンドウ最大化から詳細設定画面を開き、作業員にチェックを入れ、1人あたりの処理時間を「1分」、作業人数を「10人」と設定
分岐条件は設定せず(行先はランダム)
061 カレー用じゃが芋置き場:
容量を「1000個」と設定
062 肉じゃが用じゃが芋置き場:
容量を「1000個」と設定
牛肉下処理小ブロック
063 牛肉置き場:
容量を「1000個」と設定
064 牛肉下処理:
対象品目を「牛肉」、個数を「100個」と設定、
ウィンドウ最大化から詳細設定画面を開き、作業員にチェックを入れ、
1人あたりの処理時間を「1分」、作業人数を「10人」と設定
065 牛肉運搬:
最大運搬量を「150個」、人数を「10人」、運搬時間(片道)を「1分」と設定
066 牛肉の料理別分岐:
ウィンドウ最大化から詳細設定画面を開き、作業員にチェックを入れ、1人あたりの処理時間を「1分」、作業人数を「10人」と設定
分岐条件は設定せず(行先はランダム)
067 カレー用牛肉置き場:
容量を「1000個」と設定
068 野菜炒め用牛肉置き場:
容量を「1000個」と設定
069 肉じゃが用牛肉置き場:
容量を「1000個」と設定
調味料準備小ブロック
070 調味料置き場:
容量を「1000個」と設定
071 調味料調合:
対象品目を「調味料」、個数を「10個」と設定、
ウィンドウ最大化から詳細設定画面を開き、作業員にチェックを入れ、
1人あたりの処理時間を「1分」、作業人数を「10人」と設定
072 調味料運搬:
最大運搬量を「15個」、人数を「10人」、運搬時間(片道)を「1分」と設定
073 調味料の料理別分岐:
ウィンドウ最大化から詳細設定画面を開き、作業員にチェックを入れ、1人あたりの処理時間を「1分」、作業人数を「10人」と設定
分岐条件は設定せず(行先はランダム)
074 カレー用調味料置き場:
容量を「1000個」と設定
075 野菜炒め用調味料置き場:
容量を「1000個」と設定
076 肉じゃが用調味料置き場:
容量を「1000個」と設定
調理と入庫ブロック
カレーと野菜炒め、肉じゃがの調理を行います。
下処理ブロックで用意した材料から調理を行い、検品と不良品の破棄、合格品のチルド加工と冷蔵倉庫への入庫までを想定し、組立→検品→分岐→合格品側:加工→置き場(入庫)、廃棄物側:置き場→運搬(ローラーコンベア)→出荷(破棄)のようにプロセスを配置します。
カレー調理小ブロック
013 カレー調理:
・対象品目を5つ設定
品目「人参」、個数「100個」、
品目「玉葱」、個数「100個」、
品目「じゃが芋」、個数「100個」、
品目「牛肉」、個数「100個」、
品目「調味料」、個数「10個」
・出力品目を「カレー」、個数を「100個」と設定
ウィンドウ最大化から詳細設定に入り、作業員にチェックを入れ、1人あたりの処理時間を「1分」、人数を「10人」と設定、
014 カレー検品:
不良品率を「1%」と設定、
ウィンドウ最大化から詳細設定に入り、作業員にチェックを入れ、1人あたりの処理時間を「1分」、人数を「10人」と設定
015 カレー選別:
ウィンドウ最大化から詳細設定に入り、作業員にチェックを入れ、1人あたりの処理時間を「1分」、人数を「10人」と設定
分岐条件は以下の様に設定
品目、正常:カレー、送り先「016カレーチルド加工」
品目、不良:カレー、送り先「031廃棄物置き場」
016 カレーチルド加工:
処理時間を「1分」、作業人数を「10」人と設定、
・対象品目を「カレー」、個数を「1個」と設定、
・出力品目を「チルドカレー」、個数を「1個」と設定
ウィンドウ最大化から詳細設定に入り、作業員にチェックを入れ、1人あたりの処理時間を「1分」、人数を「10人」と設定
017 冷凍倉庫A:
容量を「1000個」と設定
(廃棄物側)031 廃棄物置き場:
容量を「1000個」と設定
(廃棄物側)032 ローラーコンベアー:
搬送時間を「1分」、最大積荷個数を「10個」と設定
(廃棄物側)033 廃棄:
特に設定なし
野菜炒め調理小ブロック
035 野菜炒め調理:
・対象品目を4つ設定
品目「人参」、個数「100個」、
品目「玉葱」、個数「100個」、
品目「牛肉」、個数「100個」、
品目「調味料」、個数「10個」
・出力品目を「野菜炒め」、個数を「100個」と設定
ウィンドウ最大化から詳細設定に入り、作業員にチェックを入れ、1人あたりの処理時間を「1分」、人数を「10人」と設定、
036 野菜炒め検品:
不良品率を「1%」と設定、
ウィンドウ最大化から詳細設定に入り、作業員にチェックを入れ、1人あたりの処理時間を「1分」、人数を「10人」と設定
037 野菜炒め選別:
ウィンドウ最大化から詳細設定に入り、作業員にチェックを入れ、1人あたりの処理時間を「1分」、人数を「10人」と設定
分岐条件は以下の様に設定
品目、正常:野菜炒め、送り先「038野菜炒めチルド加工」
品目、不良:野菜炒め、送り先「040廃棄物置き場」
038 カレーチルド加工:
処理時間を「1分」、作業人数を「10」人と設定、
・対象品目を「野菜炒め」、個数を「1個」と設定、
・出力品目を「チルド野菜炒め」、個数を「1個」と設定
ウィンドウ最大化から詳細設定に入り、作業員にチェックを入れ、1人あたりの処理時間を「1分」、人数を「10人」と設定
039 冷凍倉庫B:
容量を「1000個」と設定
(廃棄物側)040 廃棄物置き場:
容量を「1000個」と設定
(廃棄物側)041 ローラーコンベアー:
搬送時間を「1分」、最大積荷個数を「10個」と設定
肉じゃが小ブロック
043 肉じゃが調理:
・対象品目を5つ設定
品目「人参」、個数「100個」、
品目「玉葱」、個数「100個」、
品目「じゃが芋」、個数「100個」、
品目「牛肉」、個数「100個」、
品目「調味料」、個数「10個」
・出力品目を「肉じゃが」、個数を「100個」と設定
ウィンドウ最大化から詳細設定に入り、作業員にチェックを入れ、1人あたりの処理時間を「1分」、人数を「10人」と設定、
044 肉じゃが検品:
不良品率を「1%」と設定、
ウィンドウ最大化から詳細設定に入り、作業員にチェックを入れ、1人あたりの処理時間を「1分」、人数を「10人」と設定
045 肉じゃが選別:
ウィンドウ最大化から詳細設定に入り、作業員にチェックを入れ、1人あたりの処理時間を「1分」、人数を「10人」と設定
分岐条件は以下の様に設定
品目、正常:肉じゃが、送り先「046肉じゃがチルド加工」
品目、不良:肉じゃが、送り先「048廃棄物置き場」
046 肉じゃがチルド加工:
処理時間を「1分」、作業人数を「10」人と設定、
・対象品目を「肉じゃが」、個数を「1個」と設定、
・出力品目を「チルド肉じゃが」、個数を「1個」と設定
ウィンドウ最大化から詳細設定に入り、作業員にチェックを入れ、1人あたりの処理時間を「1分」、人数を「10人」と設定
047 冷凍倉庫C:
容量を「1000個」と設定
(廃棄物側)048 廃棄物置き場:
容量を「1000個」と設定
(廃棄物側)049 ローラーコンベアー:
搬送時間を「1分」、最大積荷個数を「10個」と設定
出庫ブロック
018 ピッキング:
対象品目を3つ設定
品目「チルドカレー」、個数「100個」
品目「チルド野菜炒め」、個数「100個」
品目「チルド肉じゃが」、個数「100個」
出力品目を3つ設定
品目「食品セット1」、個数「100個」
品目「食品セット2」、個数「100個」
品目「食品セット3」、個数「100個」
ウィンドウ最大化から詳細設定に入り、作業員にチェックを入れ、1人あたりの処理時間を「1分」、人数を「20人」と設定
019 ピッキング済食品置き場:
容量を「1000個」と設定
020 バンニング:
対象品目を3つ設定:
・対象品目「食品セット1」、個数「25個」
・対象品目「食品セット2」、個数「25個」
・対象品目「食品セット3」、個数「25個」
出力品目を3つ設定:
・出力品目「Aコンビニ行きカラコン」、個数「1個」
・出力品目「Bスーパー行きカラコン」、個数「1個」
・出力品目「Cレストラン行きカラコン」、個数「1個」
ウィンドウ最大化から詳細設定に入り、作業員にチェックを入れ、1人あたりの処理時間を「1分」、人数を「20人」と設定
021 方向別仕分:
ウィンドウ最大化から詳細設定に入り、作業員にチェックを入れ、1人あたりの処理時間を「1分」、人数を「10人」と設定
分岐条件は以下の様に設定
品目、Aコンビニ行きカラコン、送り先「022 Aコンビニ行き置き場」
品目、Bスーパー行きカラコン、送り先「025 Bスーパー行き置き場」
品目、Cレストラン行きカラコン、送り先「028 Cレストラン行き置き場」
出荷ブロック
Aコンビニ向け
(Aコンビニ)022 Aコンビニ行き置き場:
容量を「1000個」と設定
(Aコンビニ)023 ローラーコンベアー:
搬送時間を「0.5分」、最大積荷個数を「10個」と設定
(Aコンビニ)024 Aコンビニ向け出荷:
特に設定なし
Bスーパー向け
(Bスーパー)025 Bスーパー行き置き場:
容量を「1000個」と設定
(Bスーパー)026 ローラーコンベアー:
搬送時間を「0.5分」、最大積荷個数を「10個」と設定
(Bスーパー)027 Bスーパー向け出荷:
特に設定なし
Cレストラン向け
(Cレストラン)028 Cレストラン行き置き場:
容量を「1000個」と設定
(Cレストラン)029 ローラーコンベアー:
搬送時間を「0.5分」、最大積荷個数を「10個」と設定
(Cレストラン)030 Cレストラン向け出荷:
特に設定なし
シミュレーション
以上のプロセス配置と設定が終わったらモデルの保存を行いシミュレーションを行います。今回はシミュレーション時間を8時間にあたる480分に設定してみましょう。適切に設定できていれば、下図の様にダッシュボードが表示されます。
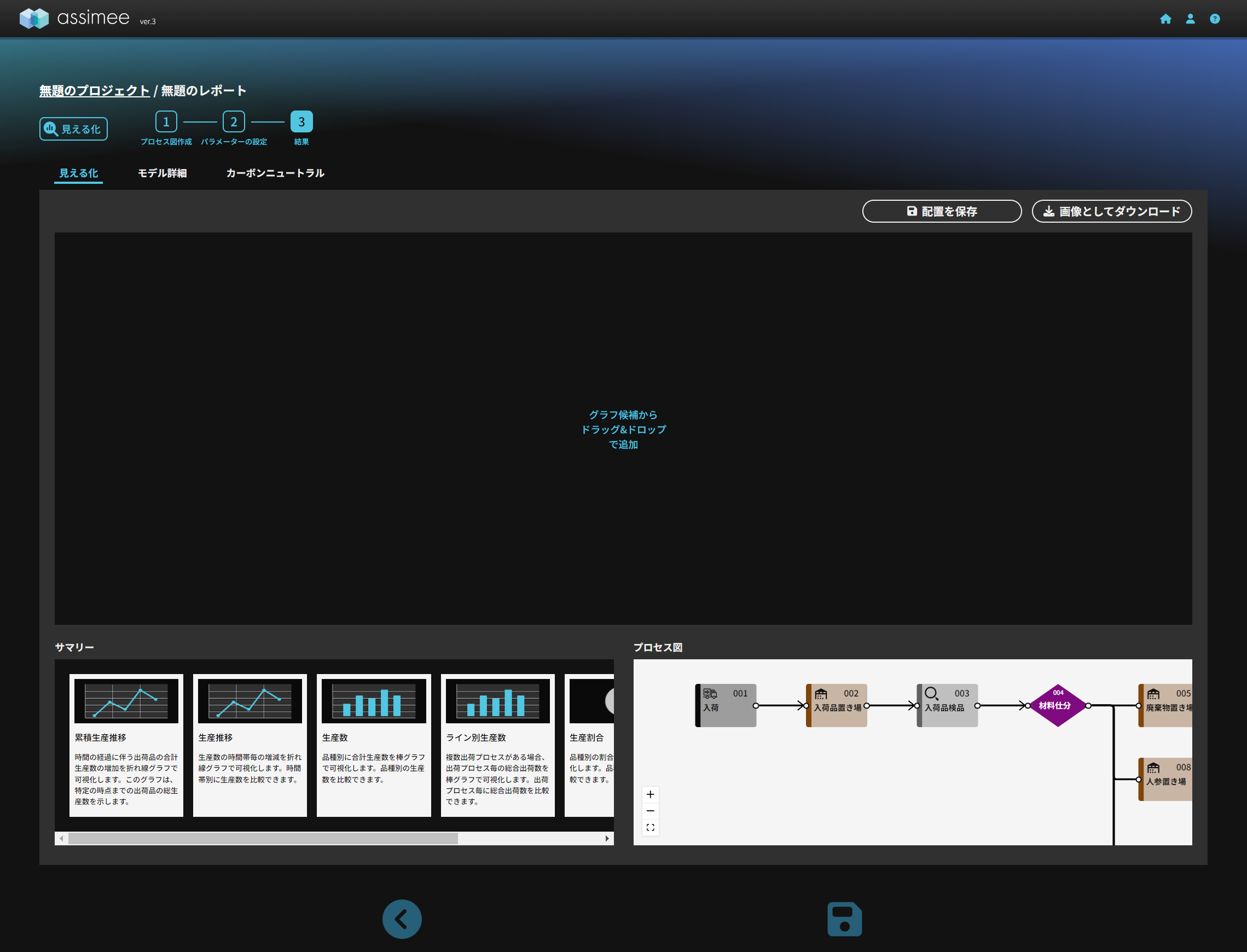
左下のサマリーから「累積生産推移」、「生産推移」、「ライン別生産数」、「生産割合」を選んで表示させます。
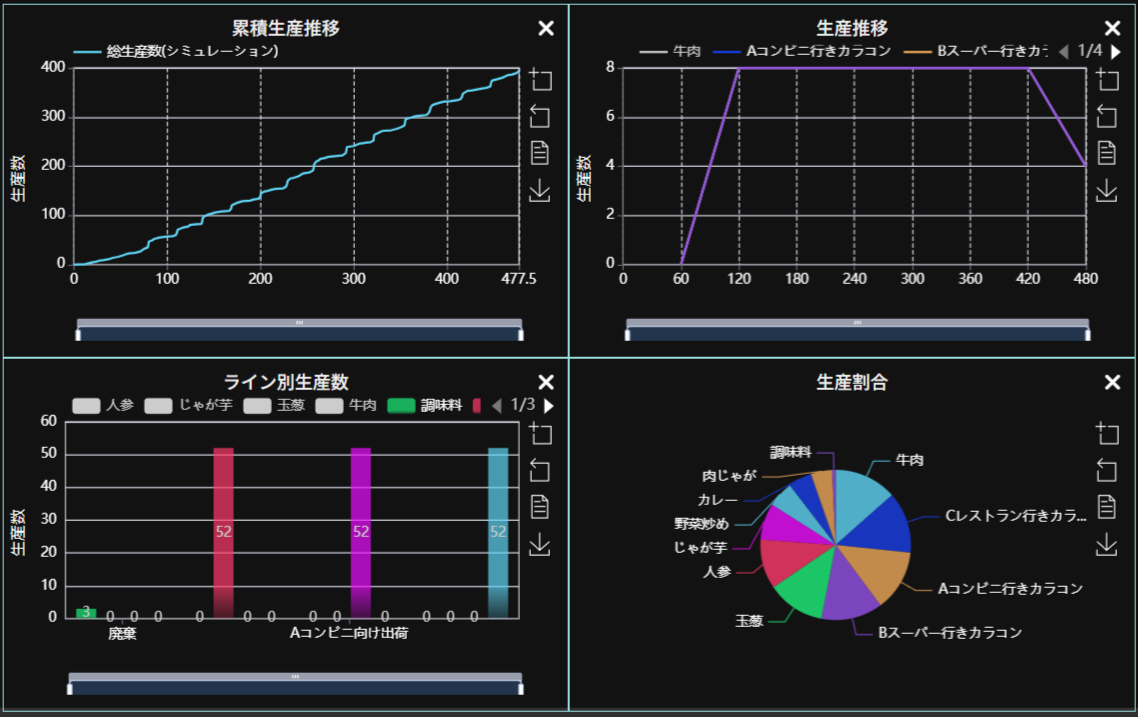
今回のモデルでは食材の運搬に掛かる時間やまとまった数の食材を用いて調理を行う設定としていることから、シミュレーション開始から店舗に向けてカラコンが出荷されるまでの時間が長め(約60分)となっています。*分岐や不良品発生にランダム変数が含まれるため毎回結果が異なり完全に一致はしません。
また、生産割合では最終製品のカラコンだけでなく不良品として途中の検品で弾かれ廃棄された食材や料理も含まれていることに注意してください。
まとめ
今回の記事では食材の調理や加工を行う食品工場(セントラルキッチン)が設置されたPDC型物流倉庫を再現したモデルの作成について解説しました。複数の食品の調理を行うための分岐、材料や食材の検品による不良品の選別、出荷の行先別仕分けといった実際に工場や物流倉庫内で行われる様々なプロセスを再現した巨大なモデルを作り込みました。このようにassimeeではシミュレーションをPC上で手軽に行うことが可能となっています。