概要
この記事では、「工程を動かすために複数の条件が揃う必要がある場合」に着目し、そのような条件付きで工程が始動するモデルを作成・検証します。現場では、工程を進めるために単一の要素だけでなく、複数のリソースや条件が揃わなければならないケースが多く存在します。たとえば、物流現場でトラックに荷物を積み込む作業を行う場合を考えてみましょう。この作業には「トラック」「積み込み作業者」「荷物」の少なくとも3つが同時に揃っている必要があります。どれか一つでも欠けていれば、工程は進行できません。
今回はこのような条件依存型の作業の一例として、「ラインから製品を搬出する工程」を題材にします。この工程では、「製品」に加えて「搬送機械(AGV)」と「作業者」の両方が揃わなければ搬出作業を開始できないという動作条件を加えた形でモデル化し、assimeeを用いたシミュレーションを実施します。
さらに、AGV の数を変更した場合に、工程や全体のスループットにどのような影響が出るのかを比較・分析します。
モデル
今回作成したモデルは以下のとおりです。自動組立ラインが3本ある工場を想定しています。組立ラインで完成した製品をSTで作業者がAGVへ積み込みます、出荷エリアへ搬送し、出荷します。
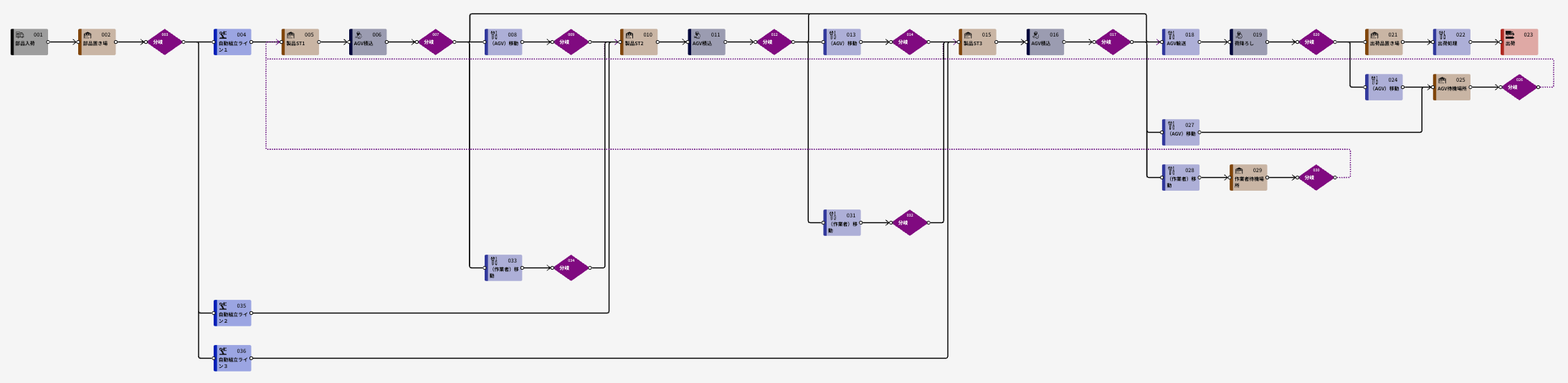
このモデルでは、AGV(無人搬送車)への積み込み作業が以下の3つの条件をすべて満たしたときに実行されます。
- 完成した製品が10個以上蓄積されていること
- 作業者が該当ステーション(以下、ST)に滞在していること
- AGVが同じSTに到着していること
このように、複数のリソース(製品・作業者・AGV)が揃って初めて積み込み作業が可能となる構成です。次に、作業者とAGVの動作ルールについて説明します。
作業者の巡回ルール
作業者はST1 → ST2 → ST3 → ST1 → … の順番で各ステーションを巡回します。
巡回中の挙動には以下のルールが適用されます:
- ST1に到着した際、積み込み条件が満たされていない場合は、作業を行わずにそのまま次のST2へ移動します(スキップ動作)。
- ST1で積み込み作業を行った場合は、その作業を終えたあとに次のST2へ移動します(実施後に移動)。
つまり、作業者は「条件が整っていなければスルー、整っていれば作業後に移動」という判断で巡回を行います。
AGVの巡回ルール
AGVも作業者と同様に、ST1 → ST2 → ST3 → ST1 → … の順番で各STを巡回します。
ただし、以下のように作業者とは異なる挙動ルールが設定されています:
- ST1に到着した際、積み込み条件が満たされていない場合でも、AGVはその場に留まり、条件が揃うまで待機します(待機動作)。
- ST1で積み込み作業を実行した場合は、作業完了後に次のST2へ移動します(実施後に移動)。
AGVは作業者と異なり、条件が整うまでその場を離れないため、タイミング次第で作業者の動きと非同期になる点が特徴です。
このようにして、「複数リソースが揃って初めて作業が可能になる工程」と「作業者とAGVが異なるルールで巡回する環境」を再現するモデルを構築し、シミュレーションを行います。実行結果から、待機戦略の有無や巡回方式の違いが工程効率にどのような影響を与えるかを分析することが目的です。
シミュレーション
モデルの作成が終了したら、シミュレーションを行います。シミュレーション時間を300分に設定します。
シミュレーションが終わると以下のような結果が表示されます。
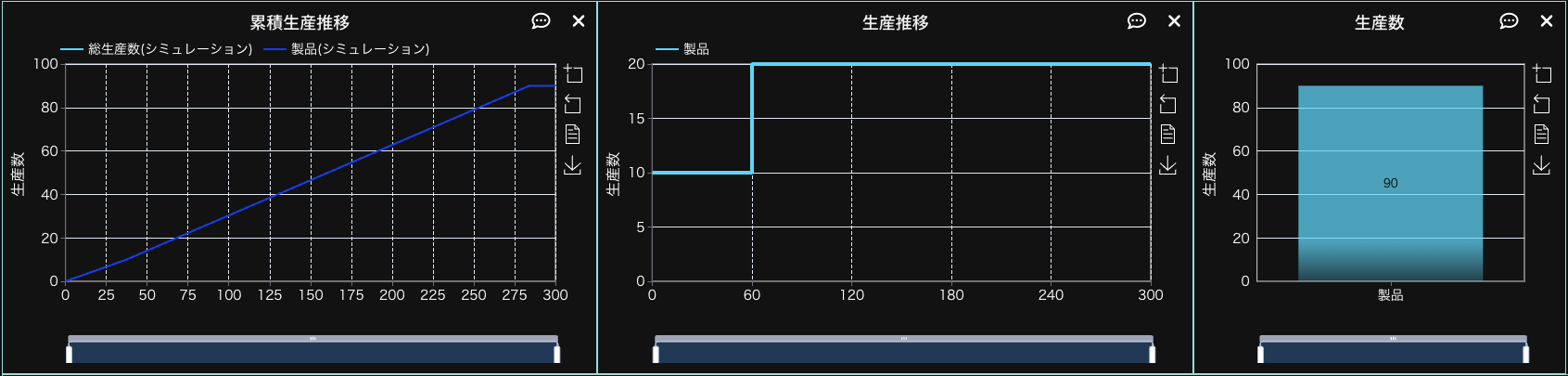
次に想定通りにAGVや作業者が動いているかステータス推移で確認してみます。
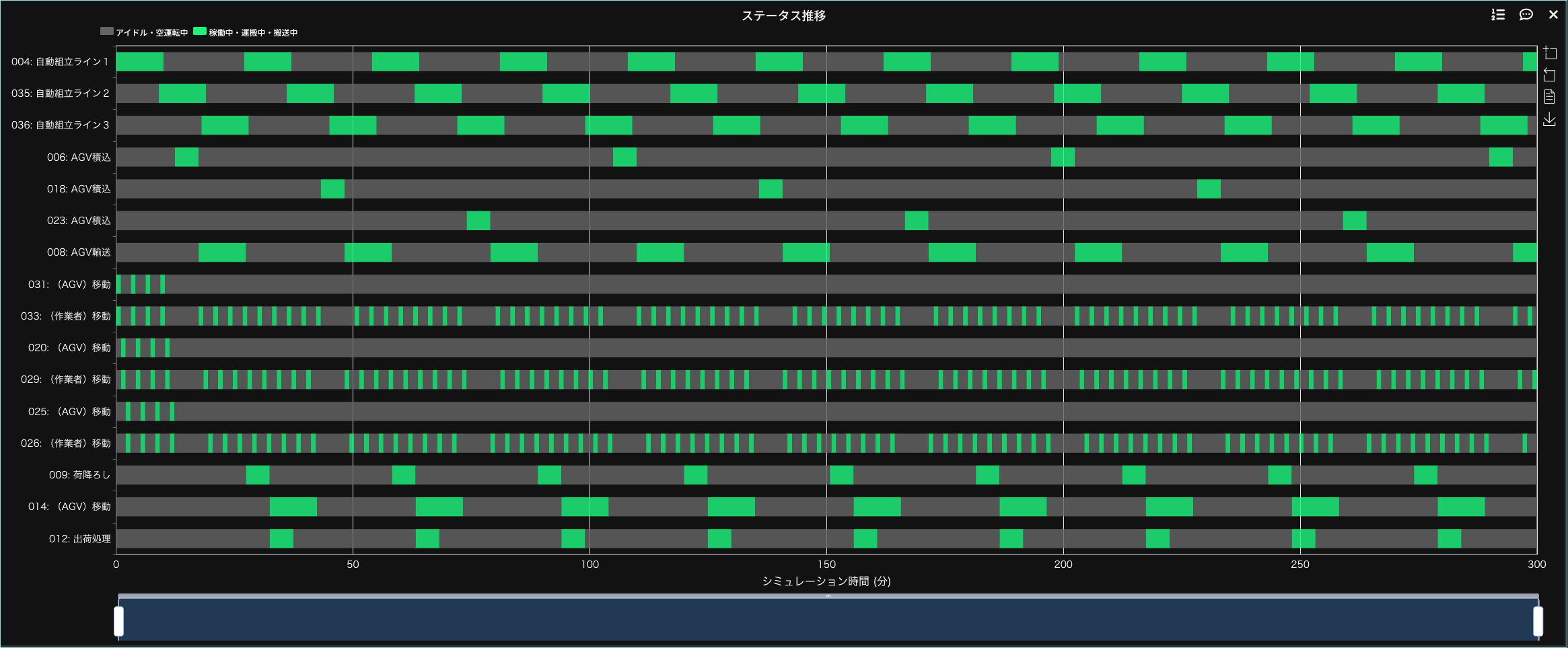
シミュレーションのステータス推移から、以下の点が確認できます。
- 作業者はST1〜ST3を順番に巡回しており、製品・AGV・作業者の3要素がすべて揃ったST1から出荷作業が開始されていること
- その後も、ST2 → ST3と順番に出荷作業が進んでいること
このことから、作業者とAGVがうまく連携することで、各ステーションでの出荷が順調に行われている様子が見て取れます。
次に、AGVの台数を2台に増やしてシミュレーションを行います。
AGVを2台にすることで、1台が製品を搬送中でも、もう1台が次のステーションで出荷作業に対応できるため、搬送の待ち時間が短縮され、全体の出荷数が増加することが期待されます。
AGVを増加させることで、工程の滞留や待ち時間がどのように解消されるか、また、各ステーションの稼働バランスにどのような変化が生じるかを観察することで、ライン構成の最適化に向けた有効な判断材料が得られます。
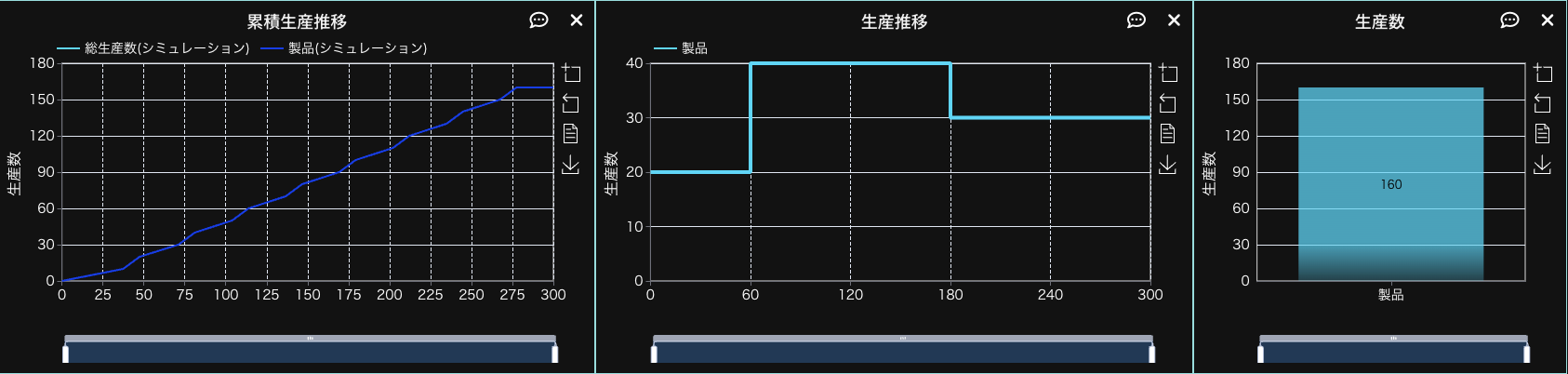
想定通り出荷数が70個増えました。では、ステータス推移はどうでしょうか?
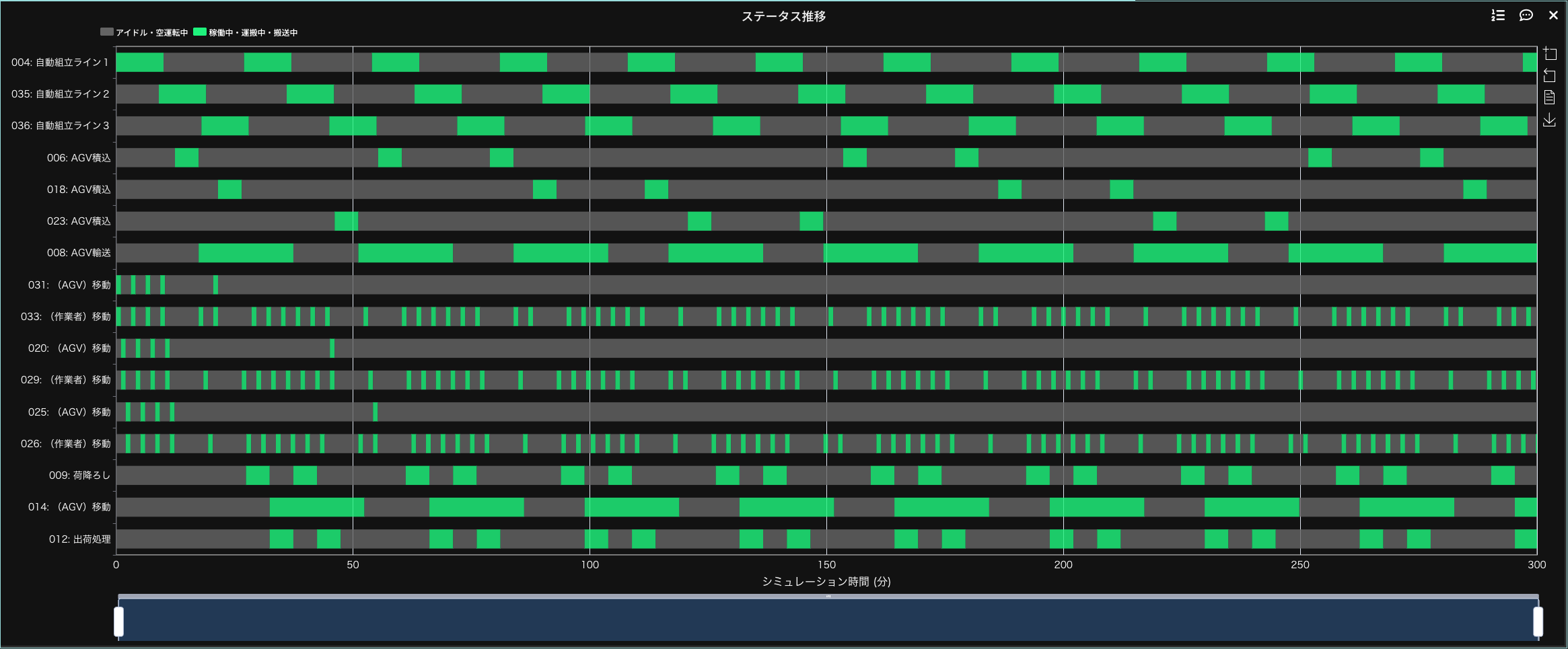
以下のように、文の論理構成や表現を整え、読み手にとって理解しやすく整理しました。シミュレーション結果の観察ポイントと、それに基づく仮説や次の検証ステップが明確になるようにしています。
ステータス推移から、以下のような工程の挙動が確認できます。
- 1台目のAGVは、ST1で最初の出荷作業を行っていること
- 2台目のAGVは、ST2で続けて出荷を実施していること
- ST3での出荷は、AGVが搬送機から戻ってくるのに時間がかかるため、他のSTに比べてやや遅れて開始されること
- 各AGVはST1 → ST2 → ST3 → ST1…という順番で巡回するため、各STで2回連続の搬送が発生する傾向が見られること
これらの挙動は、AGVの巡回順や待機条件、作業者とのタイミングのズレがライン全体の動きに影響を与えることを示しています。
次に、AGVの台数を3台に増やしてシミュレーションを行い、生産量のさらなる増加が見込まれるかを検証します。
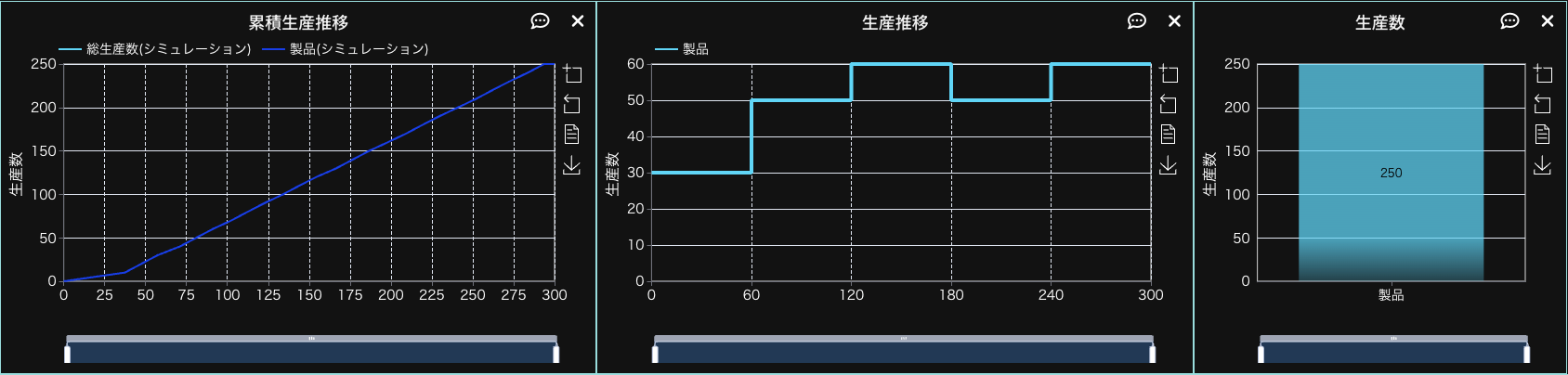
生産数はさらに90個増加し、250個となりました。ステータス推移も確認します。
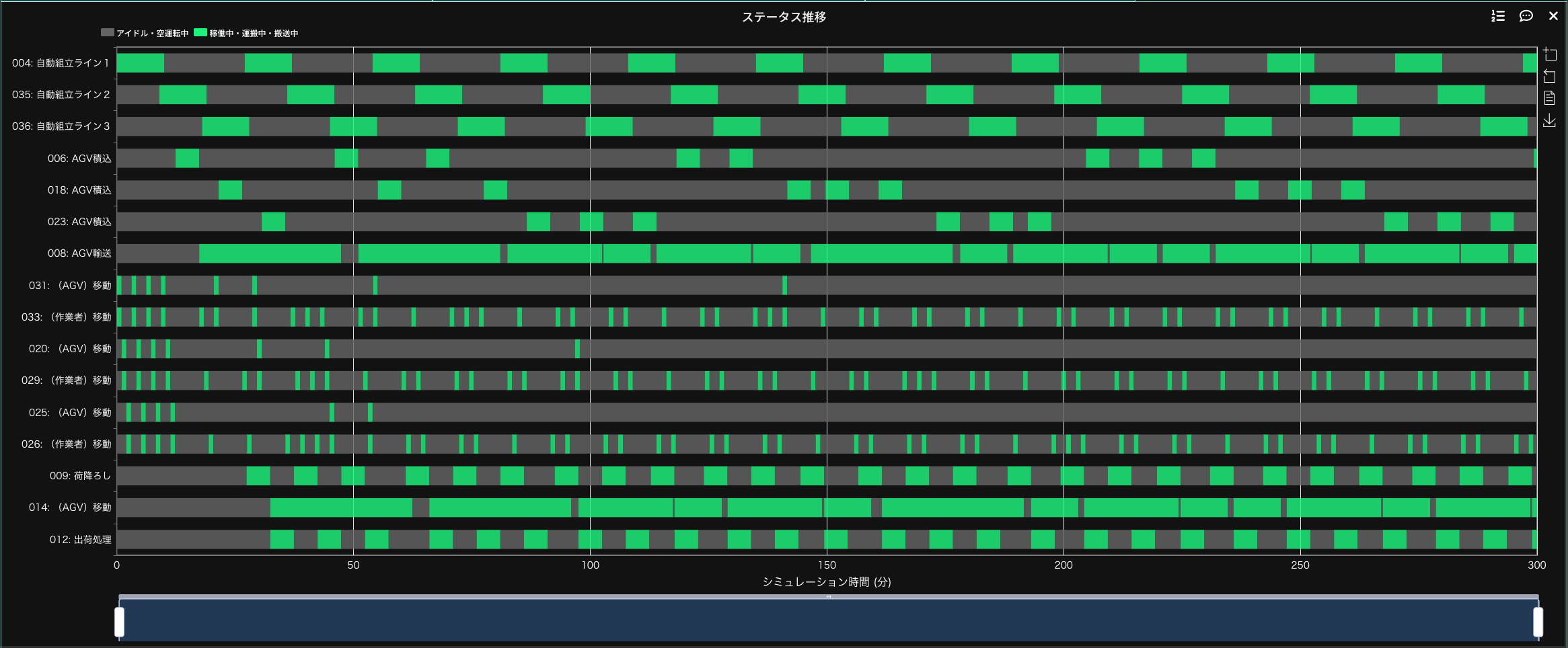
ステータスの推移から、以下のような挙動が確認できます。
- 2台のAGVを使用したケースと同様に、AGVの巡回順が影響し、ある時点から3回連続で同じSTから製品が出荷される現象が見られます。これは、AGVの巡回条件によって出荷の偏りが発生することを示しています。
このように、ラインの稼働条件を柔軟に変更しながらシミュレーションを行うことで、工程の動作傾向やボトルネックの兆候を可視化し、改善に向けた検討を深めることが可能です。今回は詳細な説明は割愛しましたが、たとえば「AGVの台数を変動させ、生産数が最大化する構成を探索する」といった最適化シナリオもassimee上で実現できます。このように、多様な視点からラインの構成や運用条件を検証できる点は、assimeeの大きな強みです。
まとめ
今回の記事では、「工程を動かすために複数の条件が揃う必要がある場合」をテーマに、条件付きの工程モデルを作成し、条件を変更しながらシミュレーションによる結果の検証を行いました。assimeeでは、用意されたさまざまなプロセスカードを柔軟に組み合わせることで、こうした複雑な動作条件を簡単にモデル化することが可能です。これにより、実際の現場に近いリアルな条件設定を反映させたライン構成や作業者の割り当てをモデル上で再現でき、運用方針の違いによる影響をシミュレーションを通じて事前に確認することができます。
また、assimeeは専門的なシミュレーション知識がなくても直感的に操作できる高いユーザビリティを備えており、モデルの作成から実行・分析までをスムーズに進めることができます。そのため、現場改善のためのシナリオ検討や業務設計の効率化に大きく貢献するツールとなっています。
assimeeでは、実際の製造プロセスをモデル化し、シミュレーションすることで、プロセスの見える化や潜在的な課題の洗い出しを行うことができます。製造プロセスのデジタル化や課題解決でお悩みの方は、ぜひお問い合わせください。