概要
バッチピッキングとは、トータルピッキング方式の一つで、複数の注文(バッチ)をまとめて一度にピッキングし、その後に個別の注文ごとに仕分けを行う方法です。注文内容が似ているものをまとめて作業することで、棚へのアクセス回数や移動距離を減らし、作業効率を高めることができます。
この記事では、このバッチピッキングの流れを再現したモデルを作成し、シングルピッキング(注文ごとに個別にピッキングを行う方式)と比較しながら、効率の違いをシミュレーションで確認していきます。
モデル
今回のシミュレーションで使用するピッキングモデルの設定は次の通りです。
- 対象商品は商品Aと商品Bの2種類。
それぞれピッキング後に仕分けされ、出荷品A・出荷品Bとして出荷されます。 - ピッキング指示は、1分間に1件のペースで到着します。
- 作業員は最大4人まで配置可能で、同時に複数のピッキング作業を担当します。
- 商品ごとの作業時間は以下の通りです:
- 商品A:移動時間(片道)1分+棚でのピッキング時間1分
- 商品B:移動時間(片道)2分+棚でのピッキング時間1分
※一度に複数件をまとめてピッキングしても、移動時間とピッキング時間は変わりません。 - ピッキング後の仕分け作業には、1件あたり1分が必要です。
- 仕分け工程には10人の作業員を配置しており、1分間に最大10件の仕分け処理が可能です。
モデルを作成すると以下のようになります。

ピッキングには、次の2つの設定を用意しています。
設定1:バッチピッキング
- 商品A・商品Bそれぞれ120件の注文がそろってから、まとめてピッキングを開始します。
- 一度に120件分をまとめて作業する方式です。
設定2:シングルピッキング
- 商品A・商品Bともに、注文が1件届くたびにその都度ピッキングを行います。
- 1件ずつ個別に作業する方式です。
この2つの方法でピッキングをシミュレーションし、効率の違いを比較します。
シミュレーション
モデルの作成が終わったらシミュレーションを行います。シミュレーション時間は8時間=480分と設定します。シミュレーションが終わったら、結果を表示させ、比較を行います。
設定2:シングルピッキング
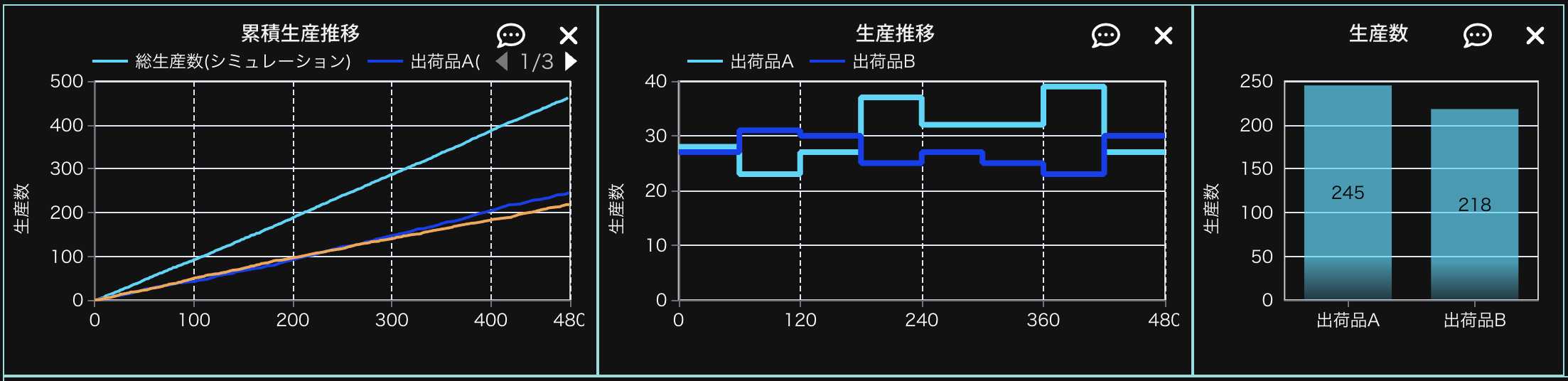
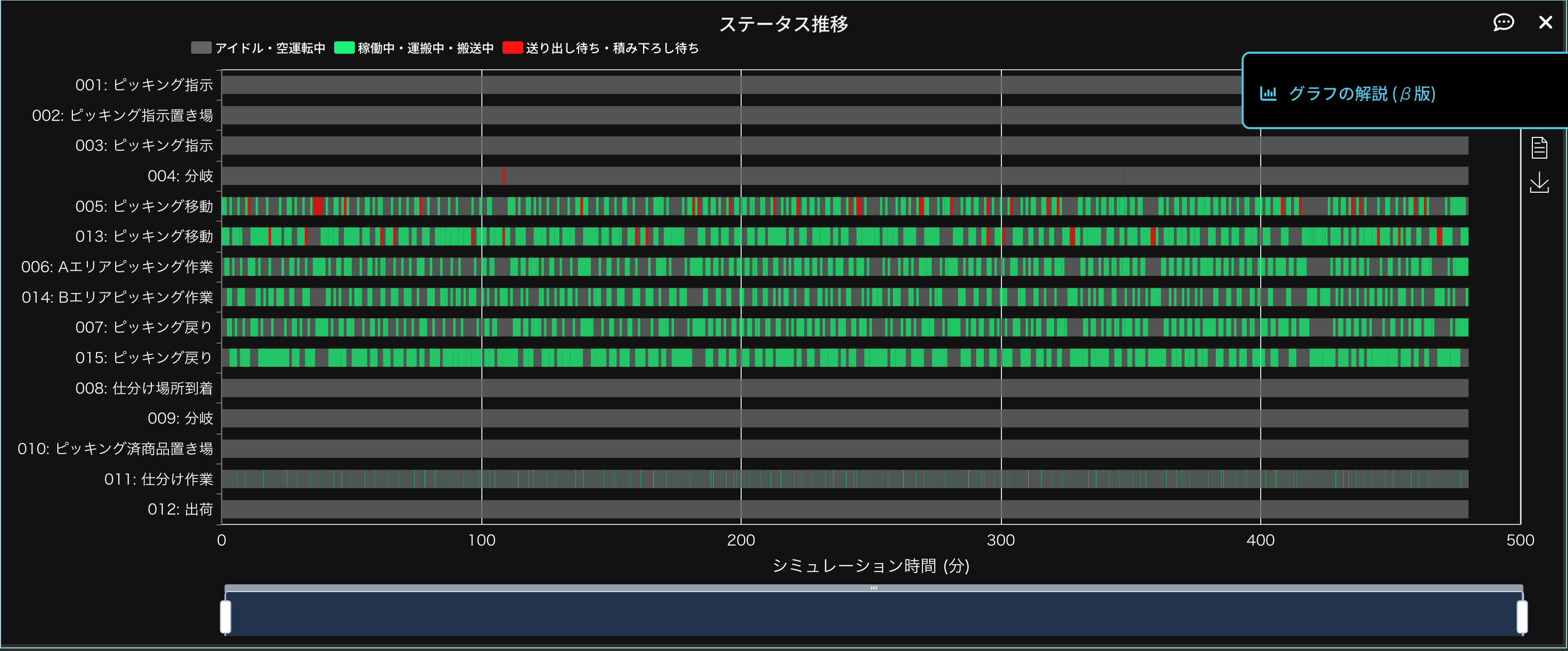
シングルピッキングでは商品Aが245件、商品Bが218件の合計463件の出荷ができました。60分あたりおおよそ60件のピッキングが行われています。
設定1:バッチピッキング
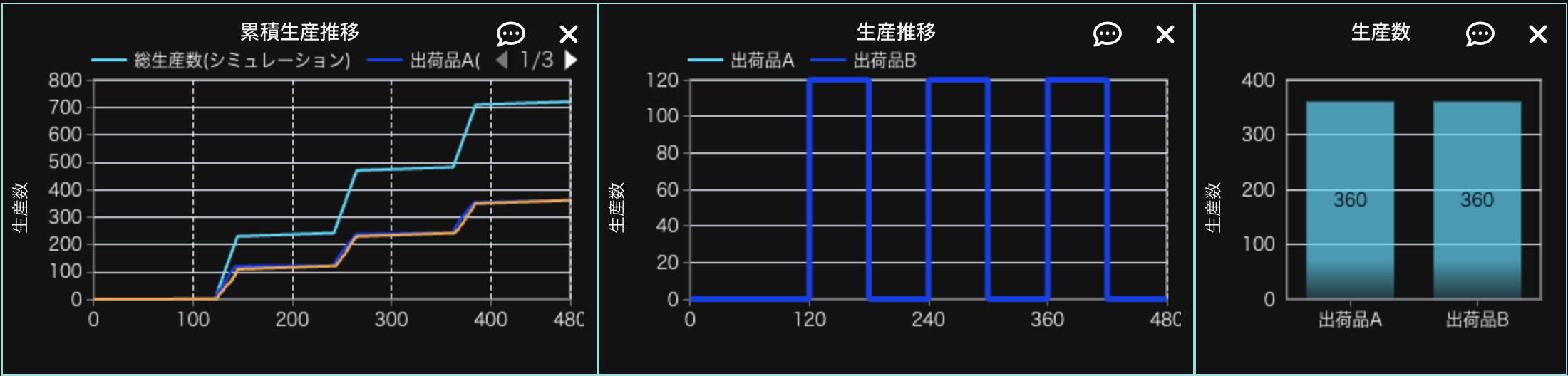
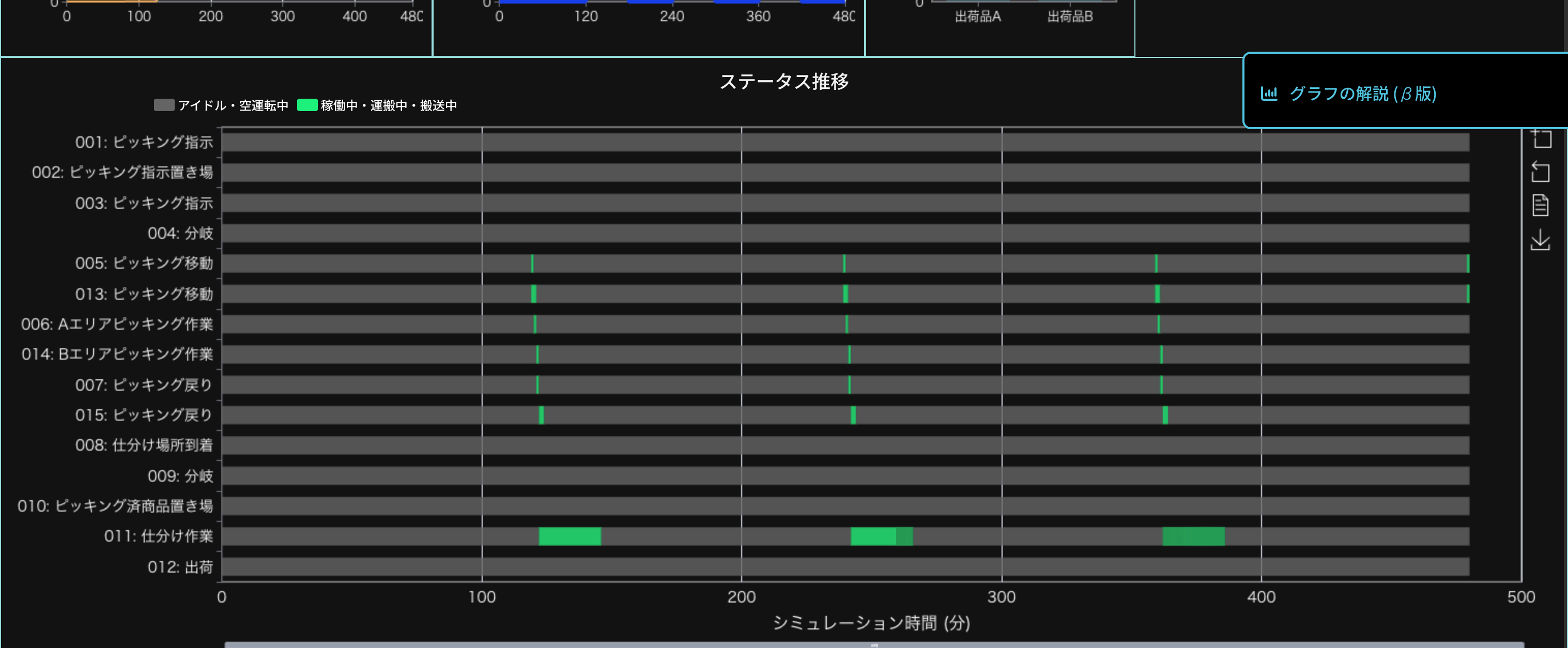
バッチピッキングでは480分で6回だけピッキングが行われますが、商品Aが360件、商品Bが360件の合計720件の出荷ができました。シングルピッキングのおおよそ3倍の出荷を行えました。これはなぜでしょうか、データの分析を行って比較を行ってみましょう。
データの分析
ピッキング
最初にそれぞれのピッキングに要する時間を確認してみます。
シングルピッキングの場合
商品ごとの作業時間は以下の通りです。
- 商品Aのピッキング:移動に2分、棚での作業に1分 → 合計3分/件
- 商品Bのピッキング:移動に4分、棚での作業に1分 → 合計5分/件
このとき、仮に1人の作業員がそれぞれだけをピッキングした場合、
- Aだけの場合:1時間に最大20件
- Bだけの場合:1時間に最大12件
のピッキングが可能です。
したがって、4人で作業すれば1時間あたり48~80件のピッキングが理論上は可能です。この値は、実際のシミュレーションで得られた約60件という実績と一致しており、矛盾はありません。
さらに、未処理のピッキング指示が残っていることから、ピッキング作業員を4人以上に増やせば、さらにピッキング件数を増やせる可能性があると分かります。これは、理論的に考えれば、ピッキング作業員が多ければ多いほど処理できる件数も増えるため、人員配置の見直しが改善ポイントとなることを示しています。
バッチピッキングの場合
商品Aと商品Bそれぞれ120件の指示がそろってから一括でピッキングを行います。ピッキング指示は1分ごとに1件到着するため、120件がそろうにはそれぞれ120分(2時間)かかります。そのため、AとBを交互にピッキングすると、1時間に1回のペースで作業が発生することになります。
ただし、たとえ120件をまとめてピッキングする場合でも、
- 商品Aの1件あたりの作業時間は3分(移動2分+ピッキング1分)
- 商品Bは5分(移動4分+ピッキング1分)
という時間設定は変わりません。この条件で考えると、120件分のピッキングに必要な時間は全体で約6分程度しかなく、1時間あたりの作業時間は非常に短いことになります。
一方で、ピッキング指示がそろうまでの120分間は作業員が待機状態になってしまうのと、360分までに集まったピッキング指示によりピッキング作業が行えていないので、このままでは作業員の稼働率が大きく下がってしまうことが分かります。そのため、たとえば作業員の稼働時間外にピッキング指示をあらかじめ集めておく、作業員の作業時間を後ろにずらすといった改善をすれば、無駄な待機時間を減らし、作業の効率化につなげることができます。
このように、1回あたりのピッキングにかかる時間が少なく、さらに120件まとめても所要時間が変わらないケースでは、バッチピッキングは非常に効果的です。ピッキング作業をまとめて効率よくこなせるため、シングルピッキングと比べて必要な作業員数が少なくて済みます。少ない人数で多くの注文を処理できる、効率の高い方法だといえます。
出荷作業
次に、出荷作業の状況を見てみましょう。出荷工程には10人の作業員を配置しています。1人あたり1分間に1件の出荷処理が可能なため、全体で1時間に最大600件の出荷ができます。
シングルピッキングの場合
ピッキングの最大処理数は1時間に60件程度です。
それに対して出荷能力は600件あるため、出荷処理がボトルネックになることはなく、滞留も発生しません。
このことから、出荷作業員が10人も必要ない=人員が過剰であると分かります。
バッチピッキングの場合
一度に120件ずつピッキングされるため、AとBで合計240件の出荷品が一気に到着します。
これを10人で処理した場合でも、完了には約24分かかります。もし、出荷作業員が1人しかいなかった場合、240件の処理には4時間もかかり、出荷品が長時間滞留する可能性が高くなります。
このように、バッチピッキングでは一時的に出荷作業が集中するため、シングルピッキングに比べて多くの出荷作業員(および作業スペース)が必要になることが分かります。
効率的な出荷を行うためには、ピッキング方法に応じた人員配置の最適化が重要です。
まとめ
この記事では、ピッキング作業をモデル化し、バッチピッキングとシングルピッキングとの比較シミュレーションを実施しました。その結果をもとに、それぞれの方式の特徴や改善のポイントを分析しました。このようにassimeeでは、品目として情報や人を取り扱うことで、これにより、現場の作業を高い精度で再現することが可能です。さらに、モデル上でさまざまな条件を自由に変更しながらシミュレーションを繰り返すことで、実際の現場を変更せずに、レイアウトや運用方法の改善案を検討できるという大きなメリットがあります。
assimeeでは、実際の製造プロセスをモデル化し、シミュレーションすることで、プロセスの見える化や潜在的な課題の洗い出しを行うことができます。製造プロセスのデジタル化や課題解決でお悩みの方は、ぜひお問い合わせください。