概要
今回の記事では、生産個数が一定以上になるとランダムに故障が発生するモデルを作成します。
assimeeでは、積算稼働時間に応じて故障が発生する仕組みが用意されています。しかし、実際の生産現場では、生産個数に依存する故障(例えば、一定以上の生産を行うとランダムに故障が発生するケース)を再現したいことがあります。
本記事では、一定以上の生産を行うとランダムに故障が発生するモデルを構築する方法について解説します。
モデル
今回作成するモデルは以下の通りです。

本モデルの主要なプロセスは、入荷した部品を入荷処理し、加工を行い、出荷処理を経て出荷する流れとなっています。今回は、加工時に故障を発生させるとともに、故障発生時には入荷処理を停止するようにモデルを構築します。
- 生産数が85個を超えた場合、5%の確率で「005加工」に故障が発生
- 修理には30分を要する
- 故障が発生すると、修理が完了するまで入荷処理(003搬送作業)を停止
- 修理完了後、003搬送作業と005加工の処理を再開
この条件を実現するため、加工ごとにカウンターへ加工済情報を送り、情報の数が85枚を超えた時点で故障判定を実施します。
- 検品プロセスを使って10%の確率で不良=故障を発生させ、不良の場合は「故障発生」のイベントチケットを発行
- 正常と判定された場合は情報を破棄
- このプロセスを繰り返し、10%の確率で故障が発生する仕組みを再現
また、加工や入荷処理で段取替えが発生すると処理が停止し、終了後に再開する仕組みを活用することで、ステータス推移を用いて故障時間を描画できるように設定します。これにより、視覚的に故障の影響を確認しやすくなります。
シミュレーション
モデルを作成したらシミュレーション時間を分に設定してシミュレーションを行います。長時間のシミュレーションを行うことで、各故障がランダムな時間で発生していることが確認できます。シミュレーション結果は以下の通りとなりました。

ステータス推移を確認すると、故障発生がオレンジで表示されており、11回の故障が発生したことが分かります。また、005加工の上流側に配置した003搬送作業に停止命令を送る設定にしていますが、設定通り、005加工と同期する形で、処理が停止、005加工の修理が終わると同時に処理が再開していることも分かります。
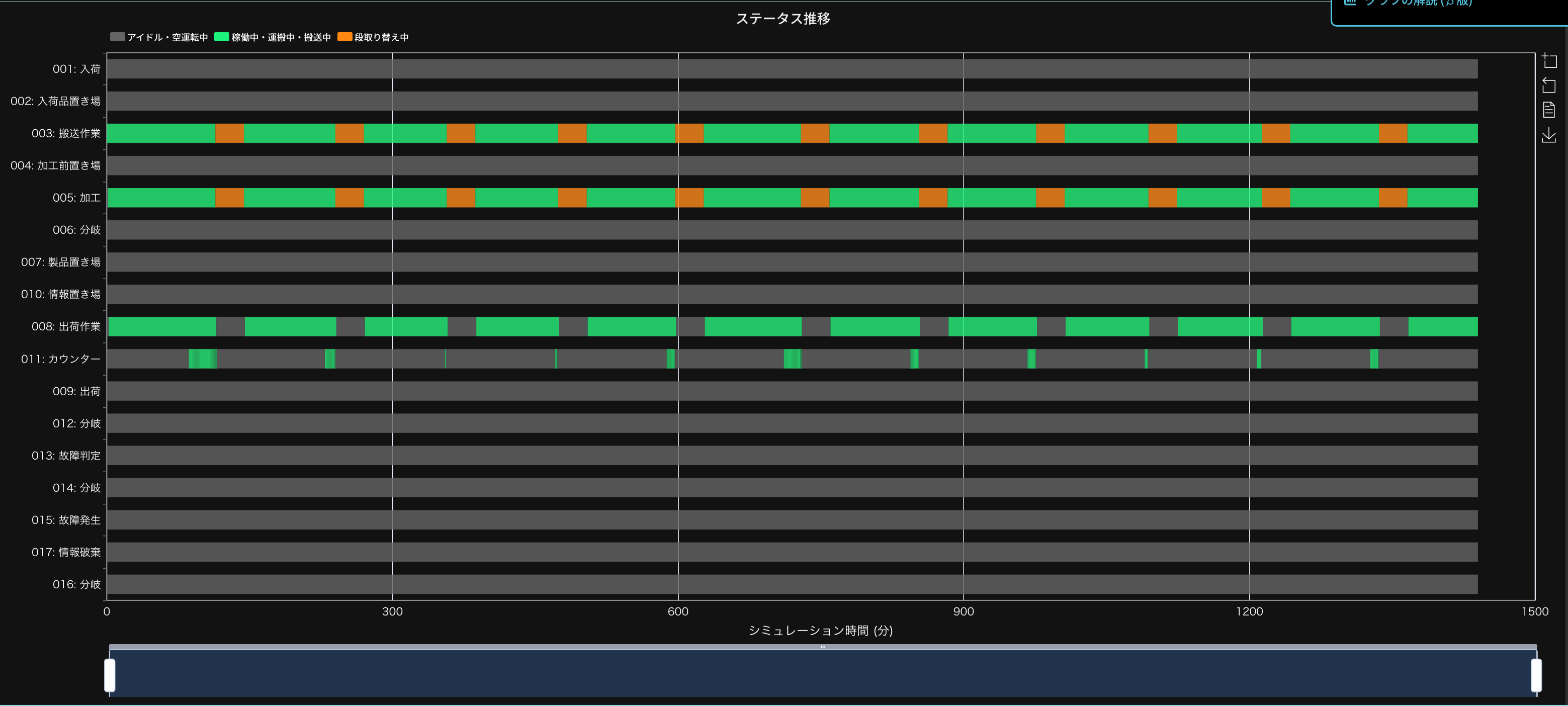
11回の故障までの時間を確認すると以下のようになりました。
故障までの生産数 | |
1回目 | 114 |
2回目 | 96 |
3回目 | 87 |
4回目 | 87 |
5回目 | 93 |
6回目 | 102 |
7回目 | 94 |
8回目 | 93 |
9回目 | 88 |
10回目 | 89 |
11回目 | 93 |
平均 | 94 |
005加工では、94個に1回の割合で故障が発生し、処理時間が1個あたり1分のため、94分に1回の頻度で故障が発生することがわかります。このように、生産数が一定数を超えた際にランダムな故障を発生させる仕組みを再現できました。また、故障発生時に入荷と加工の間の搬送作業を停止させる制御も正しく機能していることが確認できました。
まとめ
この記事では、シミュレーションの実施時にランダムに故障を発生させる方法について解説しました。assimeeでは生産現場で使用されている様々なシステムや現象をモデル化することが可能です。また、完成したモデルを使い、色々な条件を変えながらシミュレーションを行うことで、生産現場の現状や問題点などを手軽に洗い出すことが、可能となっています。
assimeeでは、実際の製造プロセスをモデル化し、シミュレーションすることで、プロセスの見える化や潜在的な課題の洗い出しを行うことができます。製造プロセスのデジタル化や課題解決でお悩みの方は、ぜひお問い合わせください。