概要
リニア搬送は、工場や物流倉庫内で物品や製品を直線的に、かつ高精度に移動させるために用いられる搬送方式です。従来のローラーやベルトコンベアーと比べると以下のようなメリットがあります。
- 高速かつ高精度な搬送
直線モーターやリニアスライドなどを活用することで、搬送物を迅速かつ正確に移動させることが可能です。 - レイアウトの柔軟性
搬送モジュールを独立して制御できるため、設置レイアウトの自由度が高く、多品種生産にも対応できます。 - 省スペース設置
シンプルな構造により、設置スペースを有効に活用でき、省スペースでの設置が可能です。 - 低メンテナンスで長期運用
構造がシンプルなため、メンテナンスが容易で、長期的な運用に適しています。
一方、デメリットとしては、以下の点が挙げられます。
- 初期導入コストの高さ
高精度な搬送を実現するための設備投資が必要となる場合があります。 - システム設計の複雑さ
専用のモジュール制御システムが必要となるため、システム設計が複雑になる可能性があります。
近年の少量多品種生産・物流への対応の点では、リニア搬送の持つ柔軟性や効率性が大きな強みとなるため、生産や物流現場での導入が進んでいます。
リニア搬送の参考情報:
ヤマハ発動機株式会社様HP
THK株式会社様HP
モデル
今回の記事では以下の条件でモデルを作成します。
リニア搬送機にはスライダーを5台使用する
5箇所のSTを定義しスライダーは各STで以下のような動作を行う
ST1(ワーク載せ):ワークをスライダーに載せる
ST2(加工1):ST2に移動して加工1を実行
ST3(加工2):ST3に移動して加工2を実行
ST4(出荷):ワークをスライダーから外し出荷
ST5(返送):スライダーをST1へ返送
それぞれのSTの間の距離の長さに応じて、複数のスライダーが存在可能
完成したモデルは下図のようになります。
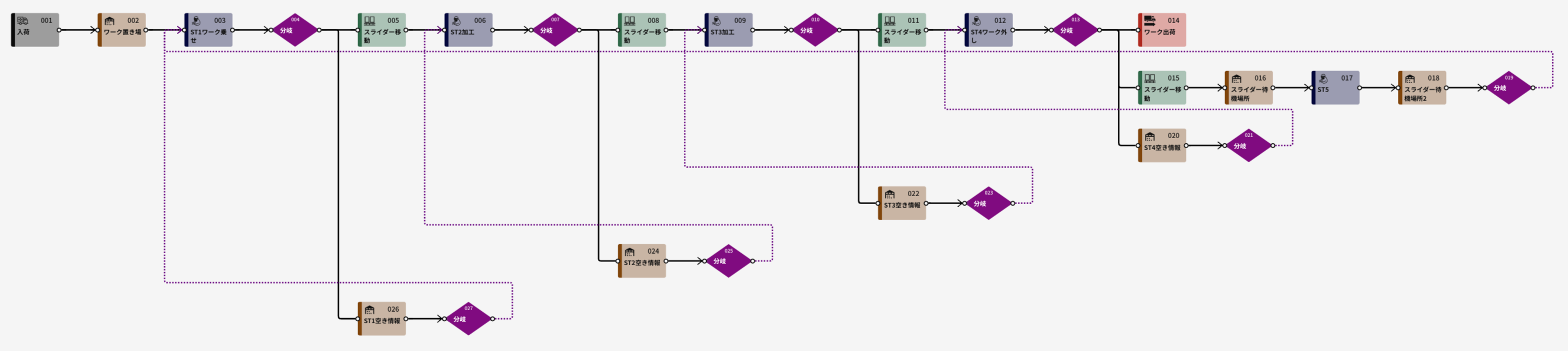
シミュレーション
モデルを作成したらシミュレーションを行います。今回のシミュレーション時間は300分とします。
シミュレーションの結果は以下のようになりました。
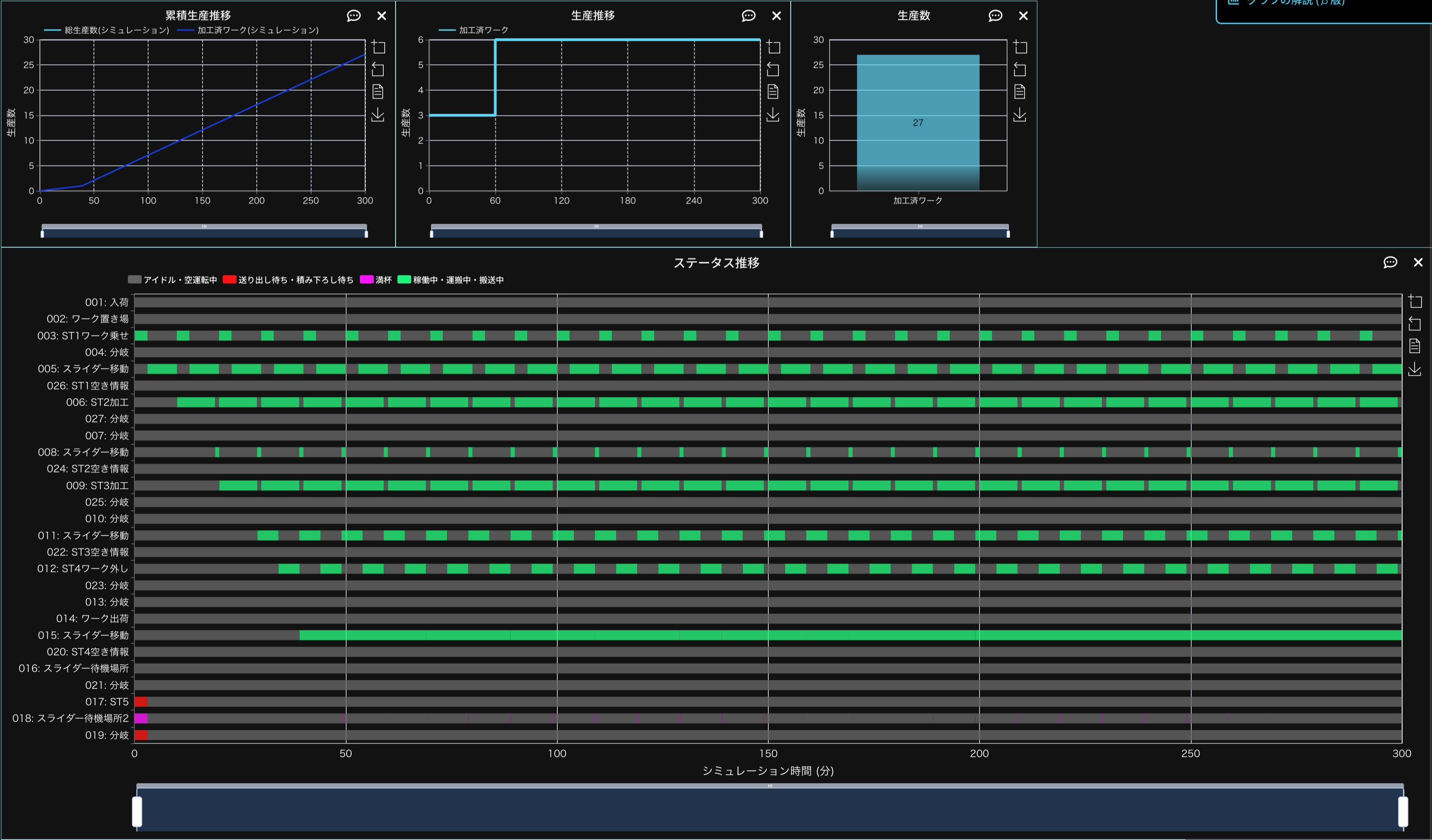
今回は生産数よりも、プロセスのステータス推移図に注目します。ST5から供給される初期配置のスライダーが、ST1(ワーク載せ)→ST2(ワーク加工)→ST3(ワーク加工)→ST4(ワーク外し=出荷)の順に移動し、出荷が連続して行われる定常状態となっていることが確認できます。
次に、各STのアイテム数の推移を見ていきましょう。
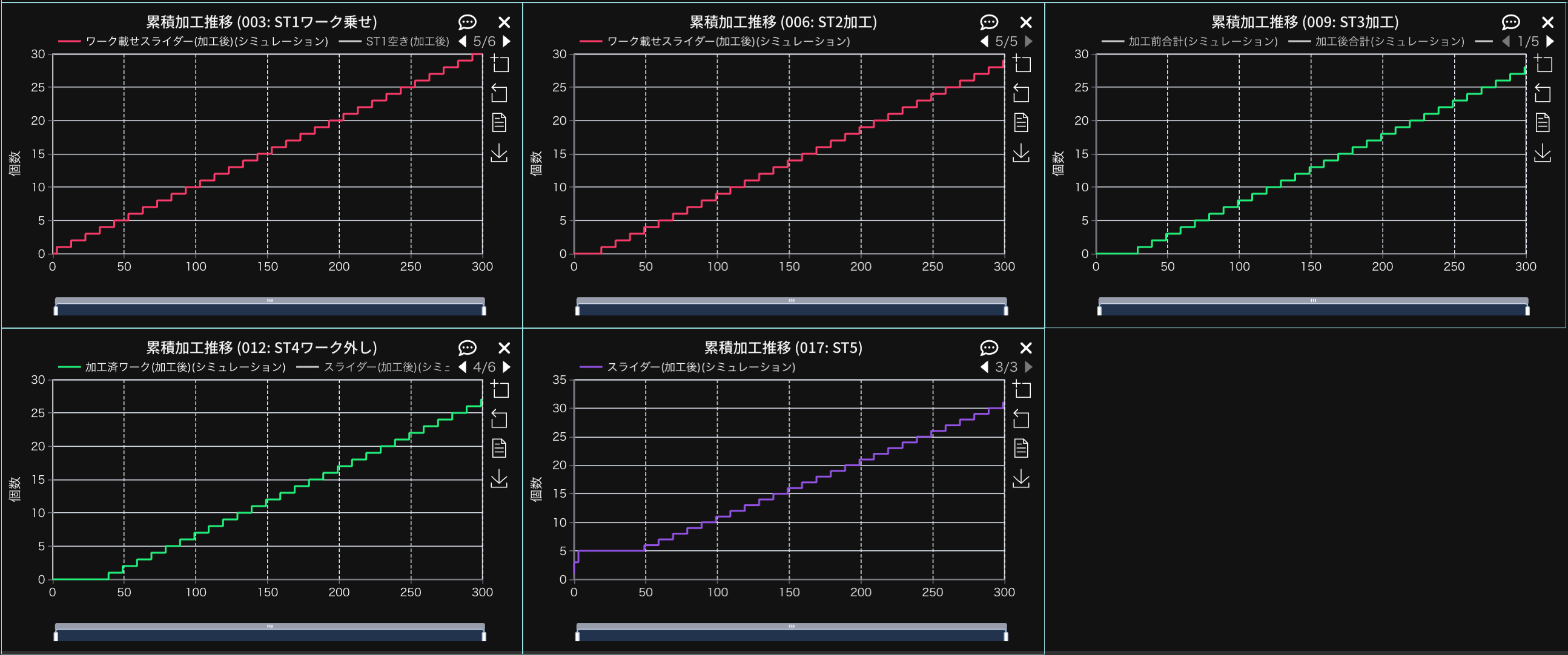
こちらも同様にスライダーが、ST5(スライダー待機場所)→ST1(ワーク載せ)→ST2(ワーク加工)→ST3(ワーク加工)→ST4(ワーク外し=出荷)の順番に移動し、設定した通りに一定間隔でプロセスが実行されていることがわかります。
まとめ
今回の記事では、物流の現場で最近注目されているリニア搬送のモデルを作成し、シミュレーションを行う方法まで解説しました。このように、assimeeではプログラムの知識がなくても直感的な操作を行うことで、さまざまなモデルを作成できます。その上で、手軽にシミュレーションを行い、モデルの性能を確認、検討することができます。
assimeeでは、実際の製造プロセスをモデル化し、シミュレーションすることで、プロセスの見える化や潜在的な課題の洗い出しを行うことができます。製造プロセスのデジタル化や課題解決でお悩みの方は、ぜひお問い合わせください。