概要
この記事では新しく実装された初期仕掛数の最適化機能を使って、入荷数を見積もる方法について解説します。生産現場では製品の生産目標に合わせて部品などの入荷数を決める必要があります。しかし、製品の組立が複雑な場合や、一定の量の不良品が発生するような場合に、生産目標から入荷数を見積もるのは手間のかかる作業で、経験や勘の生きる作業でした。assimeeを上手く使うことで、入荷数を見積もるような業務も効率化を行うことが出来ます。
モデル
今回使用するモデルは以下のようになります。

このモデルは以前の記事で使用したモデルをそのまま使っていますが、入荷する3つの部品を加工して製品を組み立てます。また、入荷する部品と組立後の製品には10%の確率で不良品が発生するモデルとなっています。
今回は入荷の直後にある「002入荷品置き場」の初期仕掛の数を計算することで、出荷目標を達成するのに必要な部品数を割り出します。
モデルのパラメーター設定変更
パラメーター設定は以前のモデルと最適化結果(作業人数)を流用します。
- 「009駆動部品チェック」の作業人数:45人
- 「026内装部品加工」の作業人数:22人
- 「030外装部品加工」の作業人数:46人
最適化のため入荷の数を絞るので、以下の変更が加わります。
001入荷:
品目入荷を3つ設定
1つ目:入荷品目を「駆動部品」、間隔を「60分」、個数を「60個」、
2つ目:入荷品目を「内装部品」、間隔を「60分」、個数を「60個」、
3つ目:入荷品目を「外装部品」、間隔を「60分」、個数を「60個」と設定
これにより480分のシミュレーション・最適化時間内に480個の部品が入荷しますが、この数を最低限の入荷数として今回は480個に上積みする数を最適化で求めます。
また、最適化対象となる「002入荷品置き場」の容量を以下のように変更します。これは初期仕掛品を合計1000個以上置けるようにするための変更です。
002入荷品置き場:
置き場容量:1000個⇒10000個
また、今回のモデルの想定は小量の入荷が定期的にある設定で、最適化時のように初期仕掛に大量の品目を用意すると運搬や検品に負担がかかるので、以下のような変更を入れておきます。
003入荷時検品:
1回あたりの処理時間を「0分」に変更し、パススルー化
006運搬:
最大積荷容量を「1000個」へ変更
初期仕掛数の最適化
置き場の初期仕掛はパラメーター推定機能で最適化することが出来ます。「002入荷品置き場」を選択します。初期仕掛をパラメーターとして指定した場合、パラメーター設定で、以下の図のように初期仕掛品目を設定します。今回は「駆動部品」、「内装部品」、「外装部品」の3つを指定し、個数をそれぞれ1個と設定します。
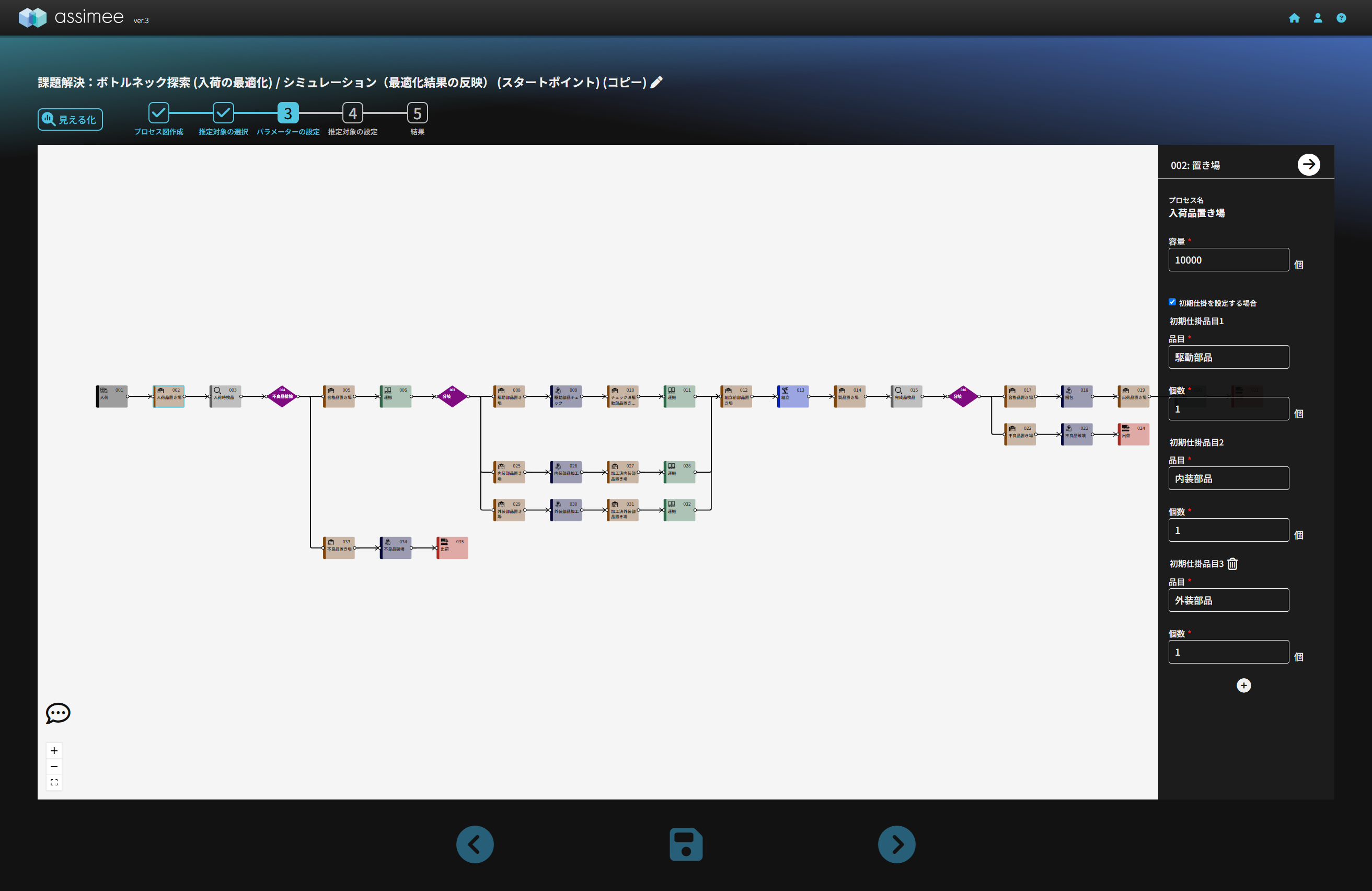
以下の図のようにパラメーターの範囲を指定します。
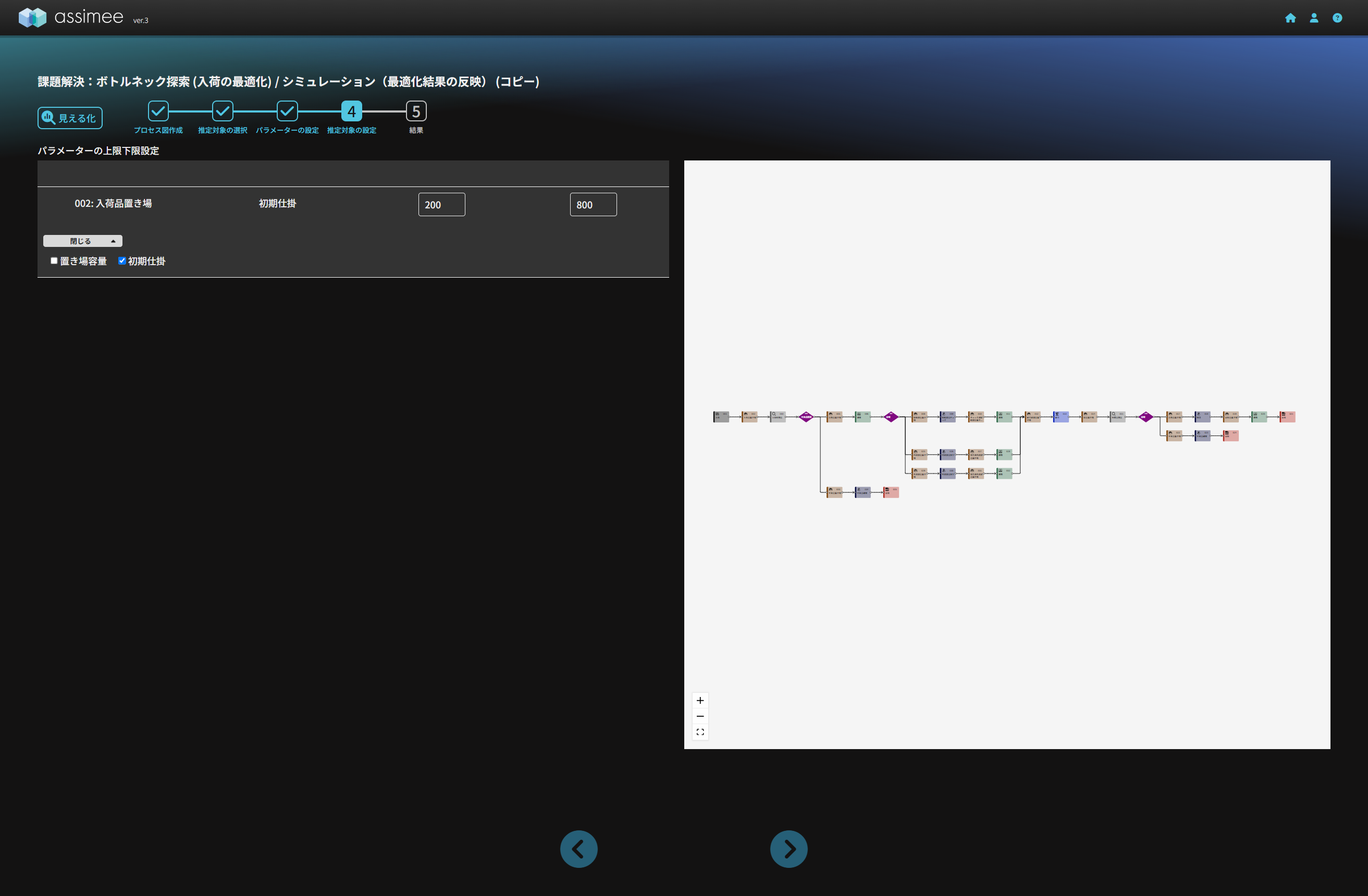
この設定で最適化(最適化時間は480分)を行います。これ以外のパラメーターの設定などについては以前の記事をご覧ください。
最適化が終わると以下の様に結果が表示されます。この結果から必要な入荷数を分析してみましょう。
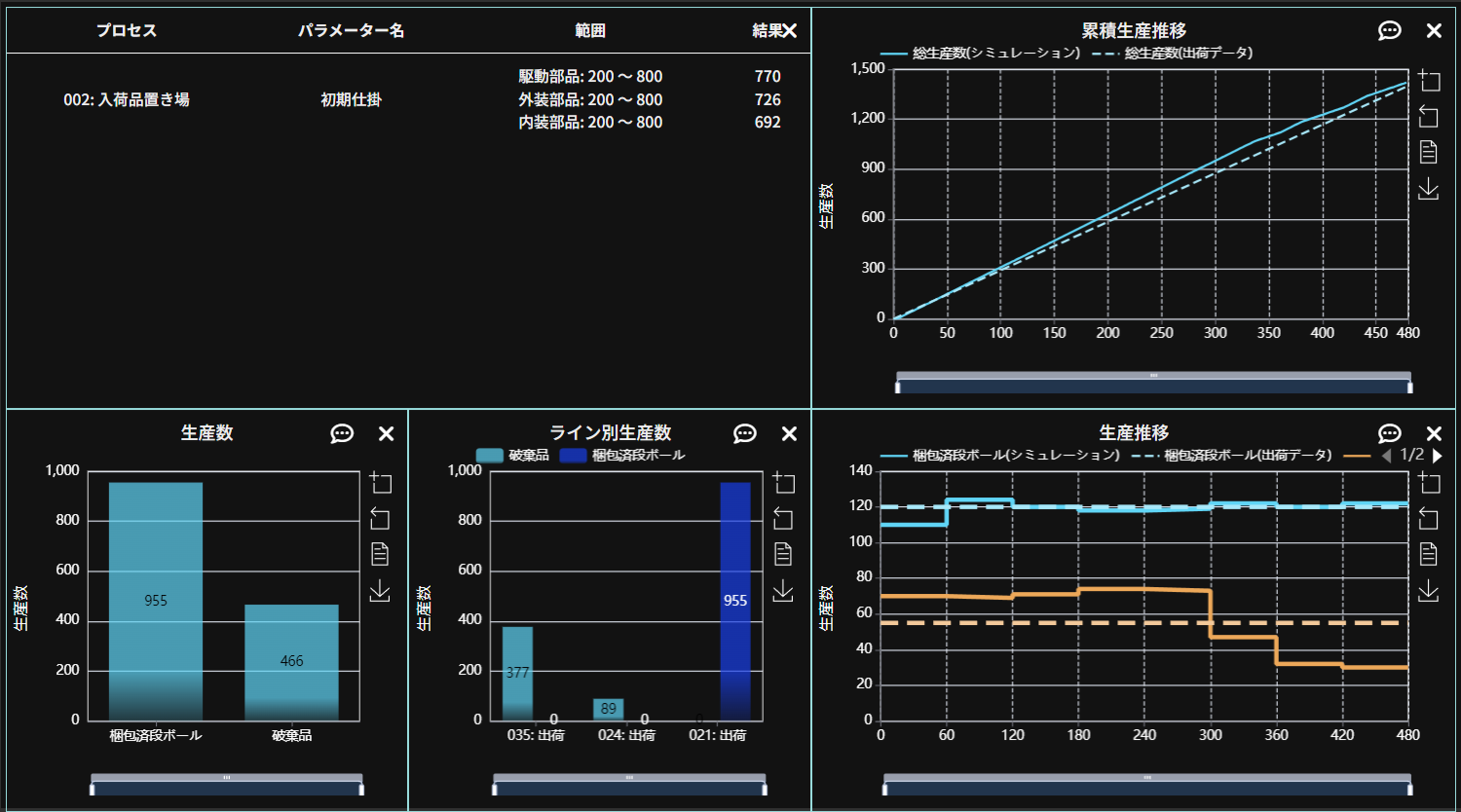
最適化結果を見ると、「累積生産推移」から生産目標(毎時120個で960個)が、ほぼ達成されていることが分かります。この時、「最適化結果」からそれぞれ約700個の部品が初期仕掛に置かれたことが分かります。一方で、「生産推移」をみるとランダムに発生する不良品の数もきちんと見込まれていることも分かります。
加えて入荷に設定した部品が480分で480個あるので、合計で1180個の部品が生産目標を達成できる最低限の数であることが分かります。いくつかに分けて定期的に入荷するように設定するなど、どのように入荷するのかは再度シミュレーションなどを使って考える必要がありますが、複数の部品の組立や不良品の発生するような複雑なモデルでも、最適化により必要な部品数を簡単に割り出すことが出来ました。この数字を基に入荷計画を立てられるので、業務の効率に繋がります。
まとめ
今回の記事では入荷直後に配置した置き場の初期仕掛数を最適化することで、生産目標に合わせて入荷数を決める方法について解説しました。このようにassimeeを上手く使うことで、入荷数を見積もるような業務も誰でもどこでも行うことが可能となり、業務の効率化につながります。また、生産ラインに対する適正な入荷数を決めることにより、ライン内の手持ち在庫数の最適化にもつながります。
assimeeでは、実際の製造プロセスをモデル化し、シミュレーションすることで、プロセスの見える化や潜在的な課題の洗い出しを行うことができます。製造プロセスのデジタル化や課題解決でお悩みの方は、ぜひお問い合わせください。