概要
製品の製造プロセスでは正常品・不良品をただ仕分けるだけでなく、複数の基準に従って階層的な仕分けを行う場合もあります。今回は、等級別に製品(みかん)の選別と出荷を行う選果場をサンプルに複数のステータスによる仕分けをおこなうモデルを作成し、シミュレーションを行う方法について解説します。
モデルの作成
今回は以下のようにモデルを作成します。assimeeでは検品プロセスを使って2値のステータス分け(正常、不良)が出来ますが、この仕組みを使ってモデル内を流れるパーツに対して2つ以上の複数ステータスの割り振りを行う方法を合わせて解説します。

今回みかんのステータスを割り振るに当たって、(特選品、秀品、優品、良品、加工品)の5つをステータスとして設定します(この他に入荷時検品による破棄品を全体の1%となるように設定)。また、ステータスの割合を実例に基づいて(17%、32%、32%、9%、9%)と設定しました。
選果ブロックの解説
以下の図のように複数の検品と分岐を連続して配置することで複数のステータス分けを行います。assimeeの検品プロセスでは正常と不良へ分けることができますが、ステータスが正常なパーツに対して2段階目の検品を行うことで3つのステータス分岐ができます。このようにして、みかん全体から加工品、良品、優品、秀品、特選品のように品質的に下位側から順に選別することが可能です。
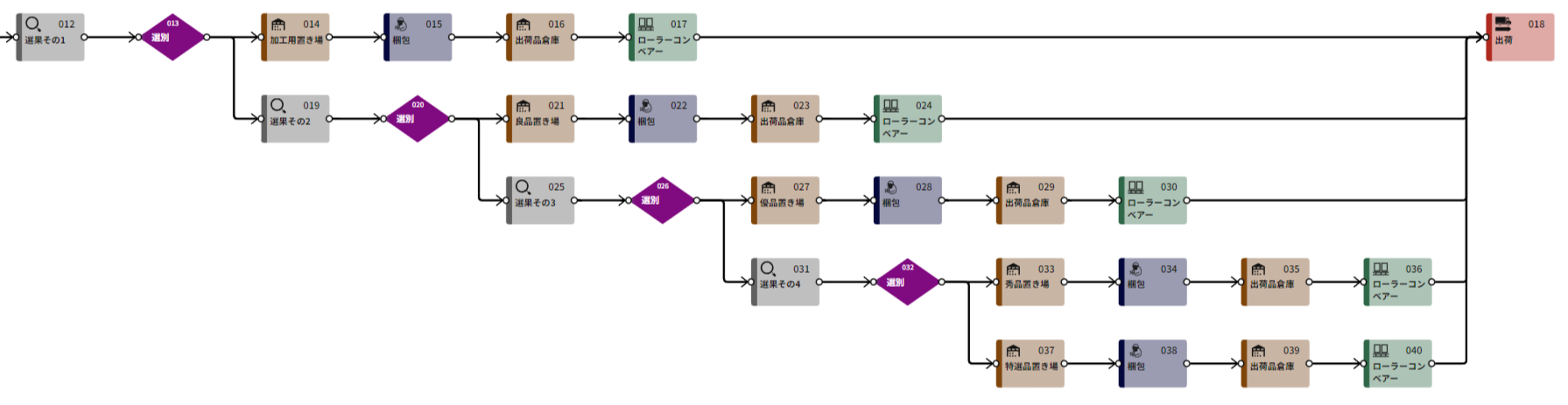
シミュレーションと分析、最適化
モデルの作成とパラメーターの設定が終了したら、シミュレーション時間を8時間に相当する480分に設定してシミュレーションを行います。シミュレーションが終了すると表示されるダッシュボードからシミュレーションの結果を確認するため、「生産推移」と「生産割合」のグラフを選択し表示させたものが下図となります。
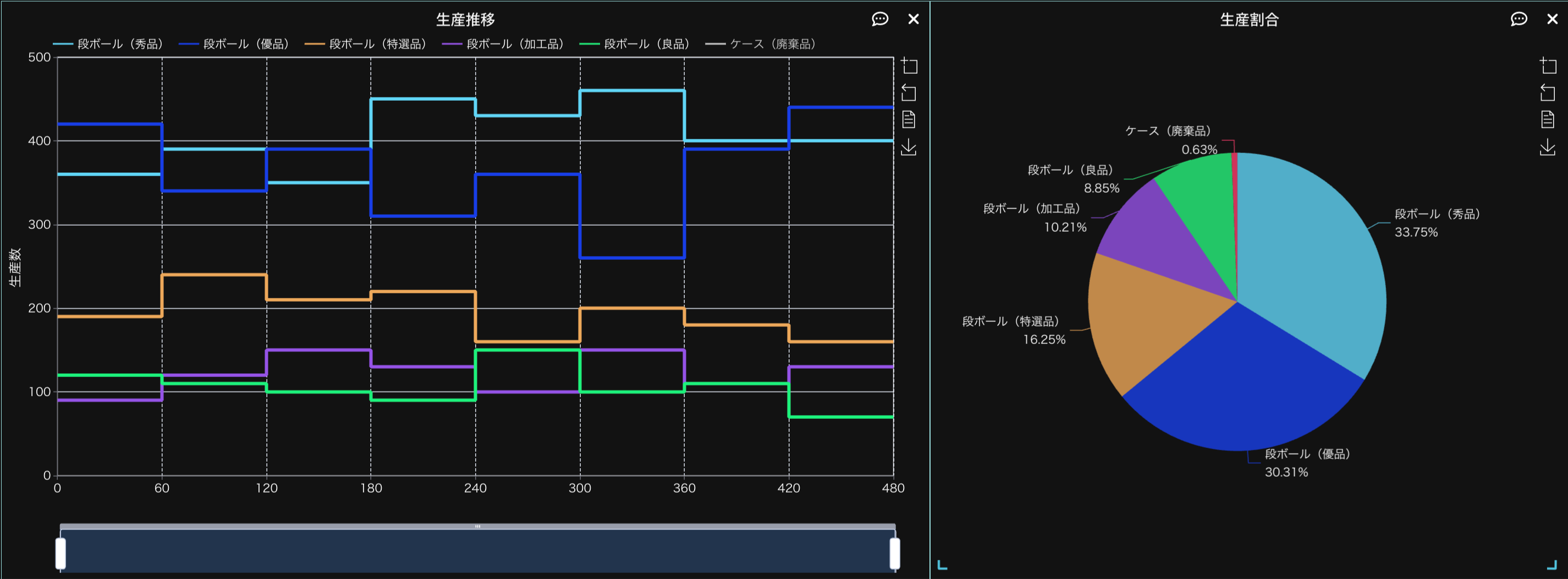
また、右側の円グラフはステータス別(特選品、秀品、優品、良品、加工品、破棄品)の出荷割合を示しています。それぞれの割合は(16%、34%、30%、10%、9%、1%)となっています。検品プロセスでの不良品の検出・ステータスの割り振りには乱数が含まれているために若干のずれがありますが、元々、想定した(17%、32%、32%、9%、9%、1%)とほぼ同じ割合となっていることが分かります。
assimeeでは品目ごとに出荷目標を立てることが出来ます。今回は上のシミュレーション結果を参考に出荷目標を設定して出荷量をコントロールしてみましょう。
最適化対象として、5カ所のみかんの梱包プロセスを選択します。
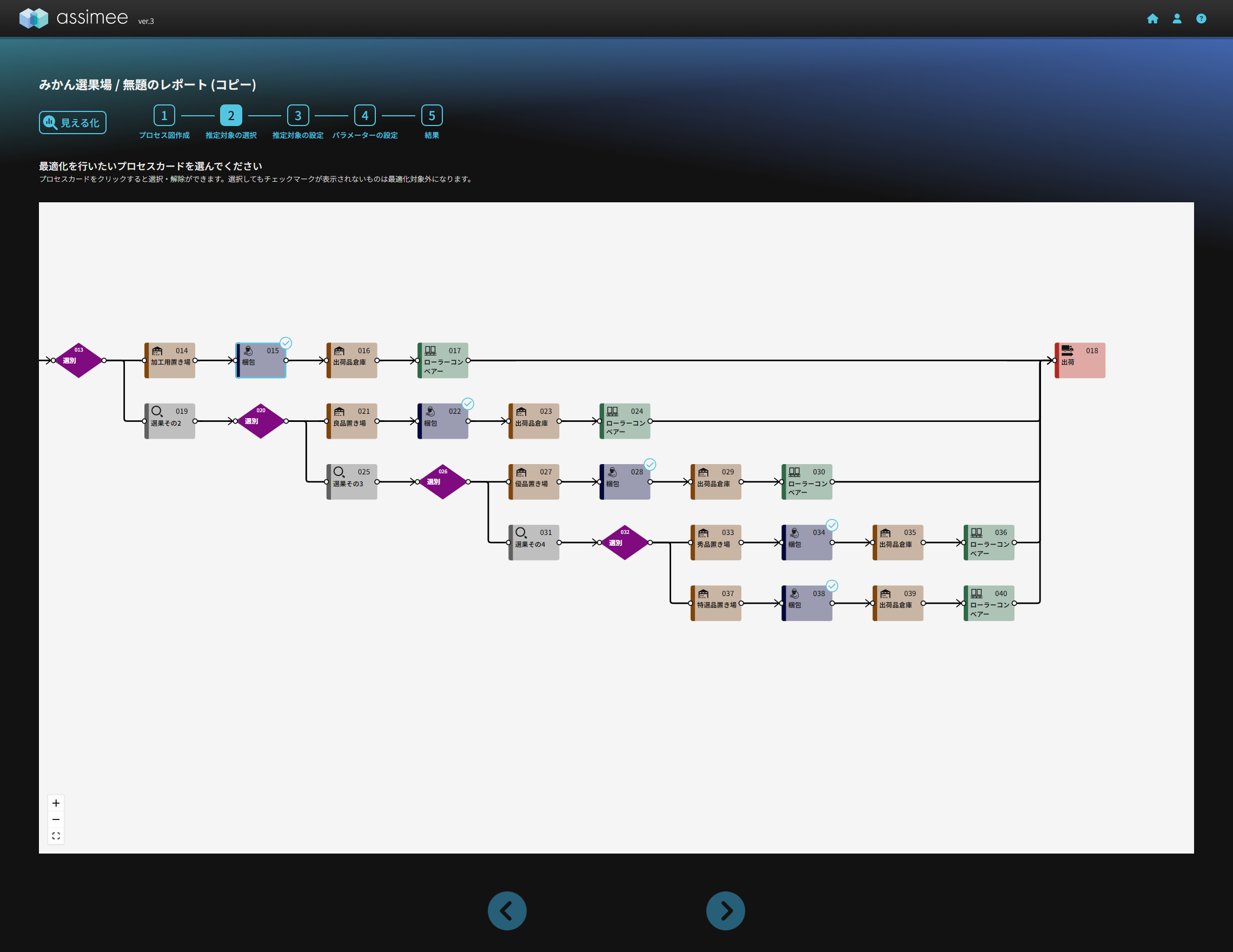
選択した後はパラメーターの範囲と出荷目標を設定します。今回は5カ所の梱包プロセスの処理時間を最適化パラメーターとし、出荷目標は優品と秀品の数をシミュレーション結果の数(約400個)の半分となるよう毎時間200個に、他の品目は維持するように、特選品は毎時間200個、良品と加工品は毎時間100個に設定してみましょう(廃棄品も毎時間10個を設定)。
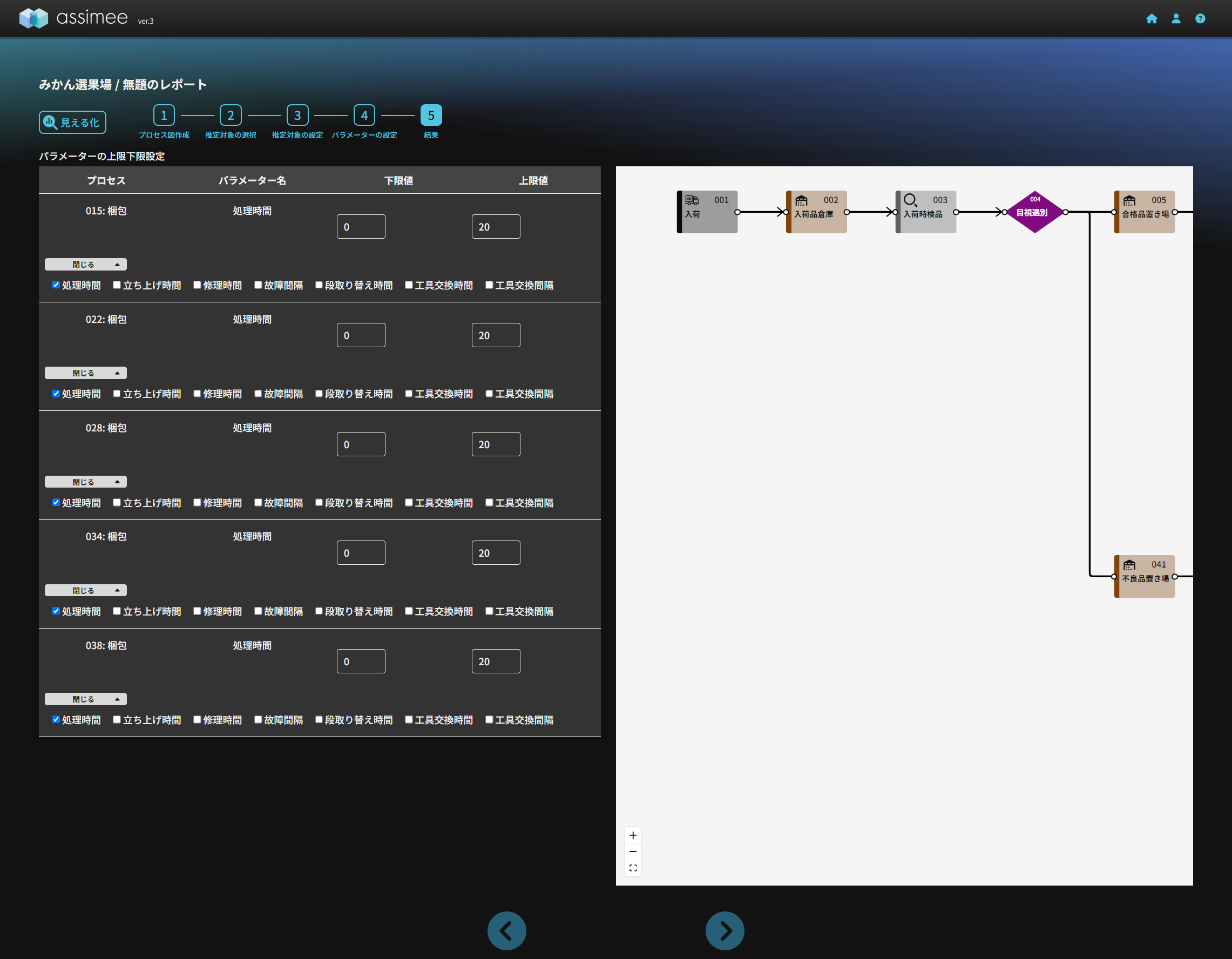
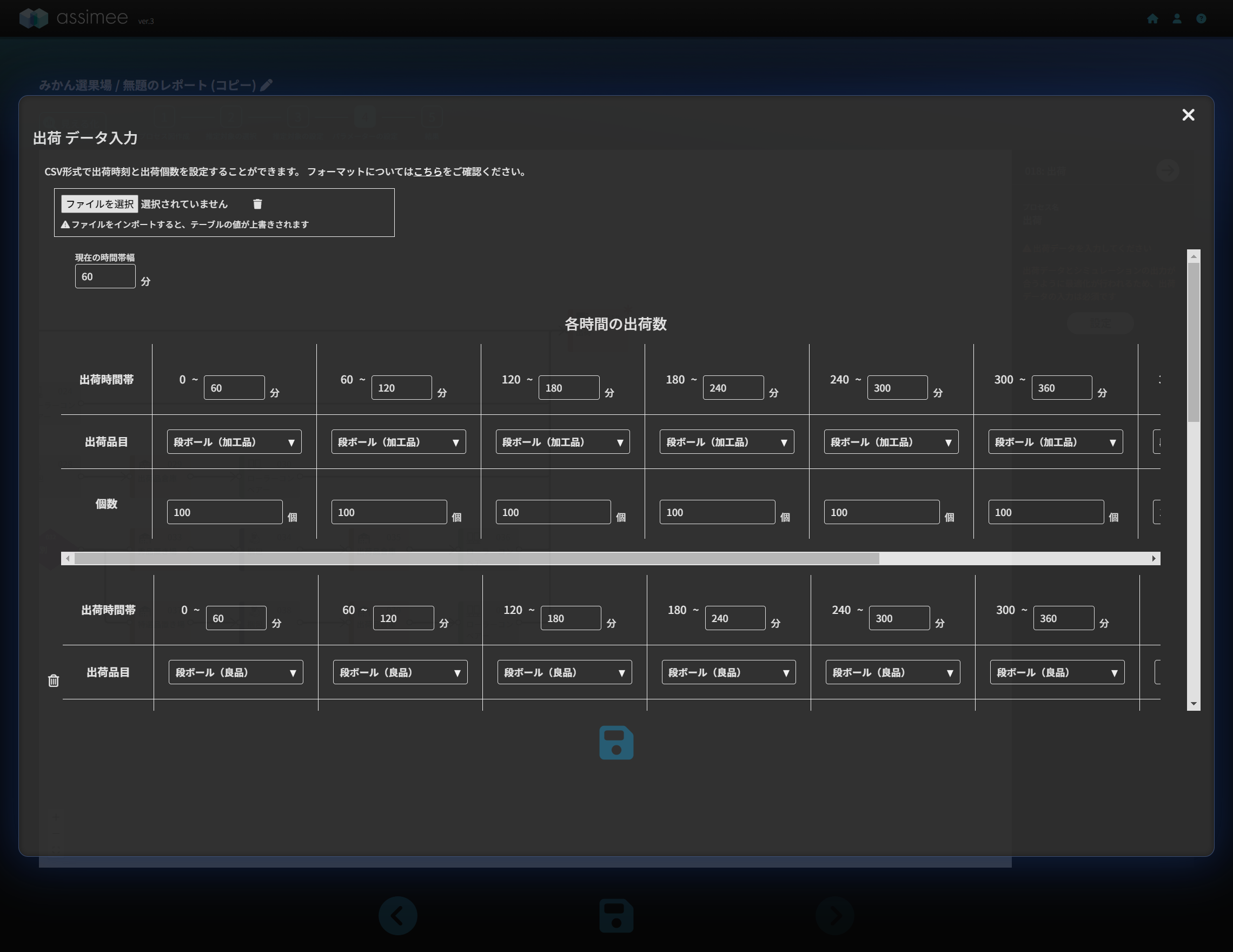
最適化が終了すると以下のようなに出荷目標と実際の出荷量の比較、最適化の結果が表示されます。処理時間が左側のグラフのように変更され、右の図のように出荷目標を達成するようにパラメーターが変更されたことが分かります。
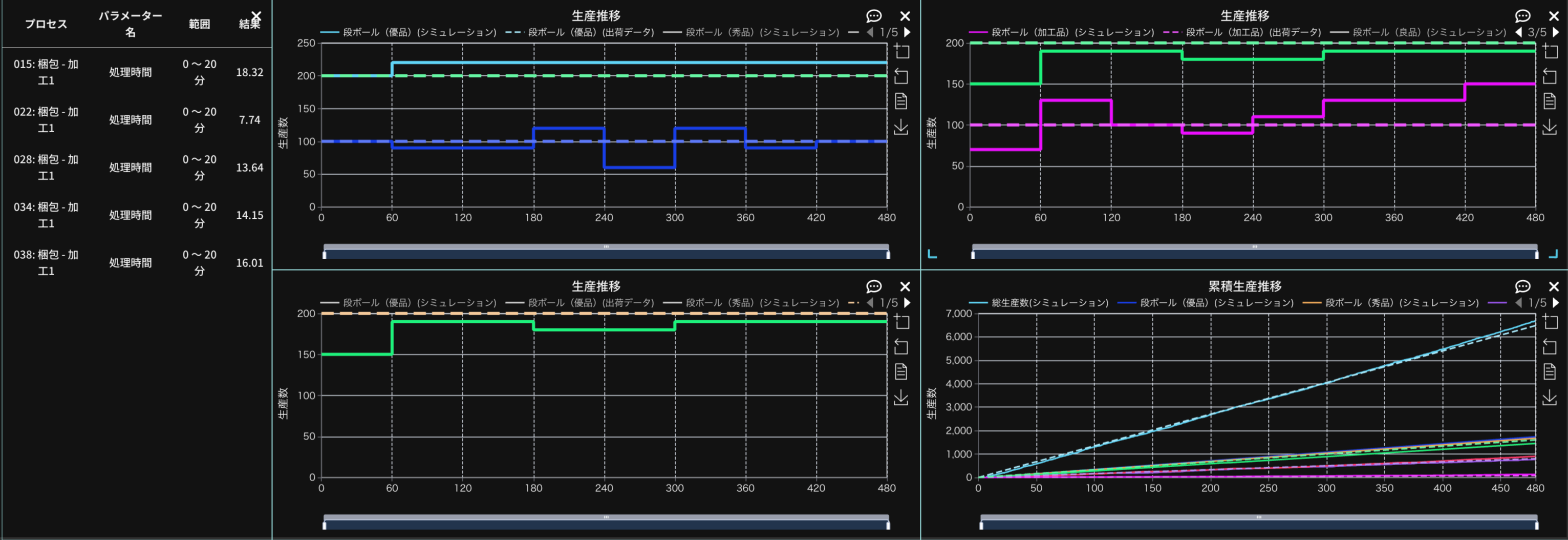
中央上段:優品と良品(実線:結果、破線:出荷目標)、中央下段:秀品(実線:結果、破線:出荷目標)
右上段:特選品と加工品(実線:結果、破線:出荷目標)、右下段:累積生産推移
まとめ
今回の記事ではみかん選果場をサンプルとしたモデルを作成し、複数のステータスを持つ製品のシミュレーションを行う方法について解説しました。このようにassimeeの基本プロセスを上手に組み合わせて使うことで、再現できるモデルの幅が広がります。加えて、それぞれに出荷目標を設定し、作業人員や設備のパラメーターの推定を行うことも可能となっています。
assimeeでは、実際の製造プロセスをモデル化し、シミュレーションすることで、プロセスの見える化や潜在的な課題の洗い出しを行うことができます。製造プロセスのデジタル化や課題解決でお悩みの方は、ぜひお問い合わせください。