概要
製造工場では工具の使用時間が長くなるとドリルの刃先など消耗する部品の交換の発生や故障といったトラブルに起因するチョコ停やドカ停、あるいは段取り替え時間が存在します。生産計画を立てる上で、このような停止時間を見込むことは非常に重要です。assimeeでは段取り替え時間や工具交換の時間、修理時間を設定することが可能です。これにより、ラインAが工具交換をしている間にラインBに作業を割り振る、ラインAが再開したらラインBの工具を交換するなど細かな生産計画をシミュレーションしたり、生産計画を達成するするパラメーターを推定することが可能となっています。
モデル作成
今回は以下のようなモデルを使用します。
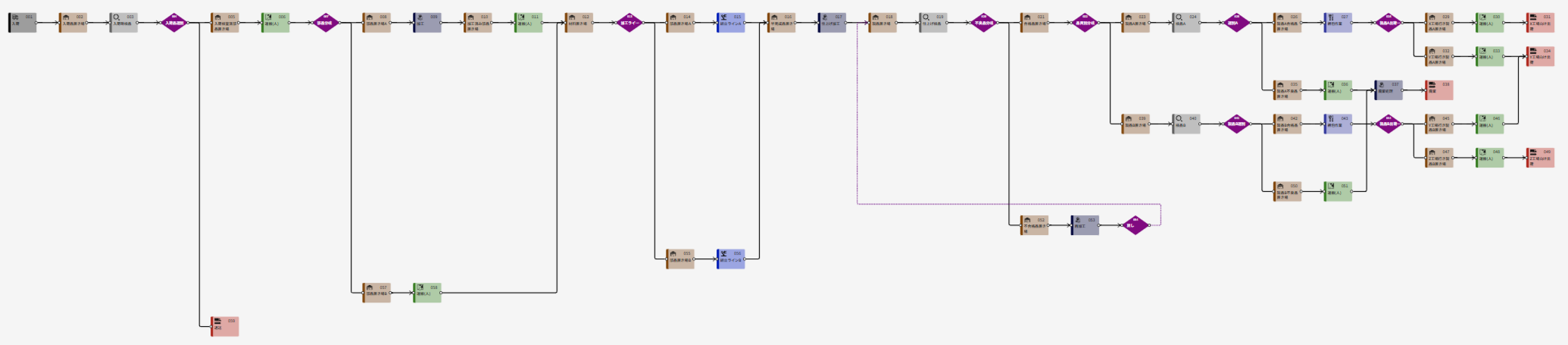
2種類の品目を入荷し、入荷時検品の後、1品目は加工、2品目は無加工で組立に供給します。組立ラインは2つあり、それぞれ同じ製造ラインを想定しています。その後、組み立てた半製品を仕上げ加工で製品Aと製品Bに仕上げ、検品と梱包の上で目的地別の出荷を行う構成となっています。
TOP画面から見える化を選択し、プロセス図を作成しパラメーターを設定して行きます。
今回のモデルの特徴としては、下図のように仕上げ加工で不良と判断したパーツを再加工した後に、合格するまで検品を繰り返すという工程をループを使って再現しています。
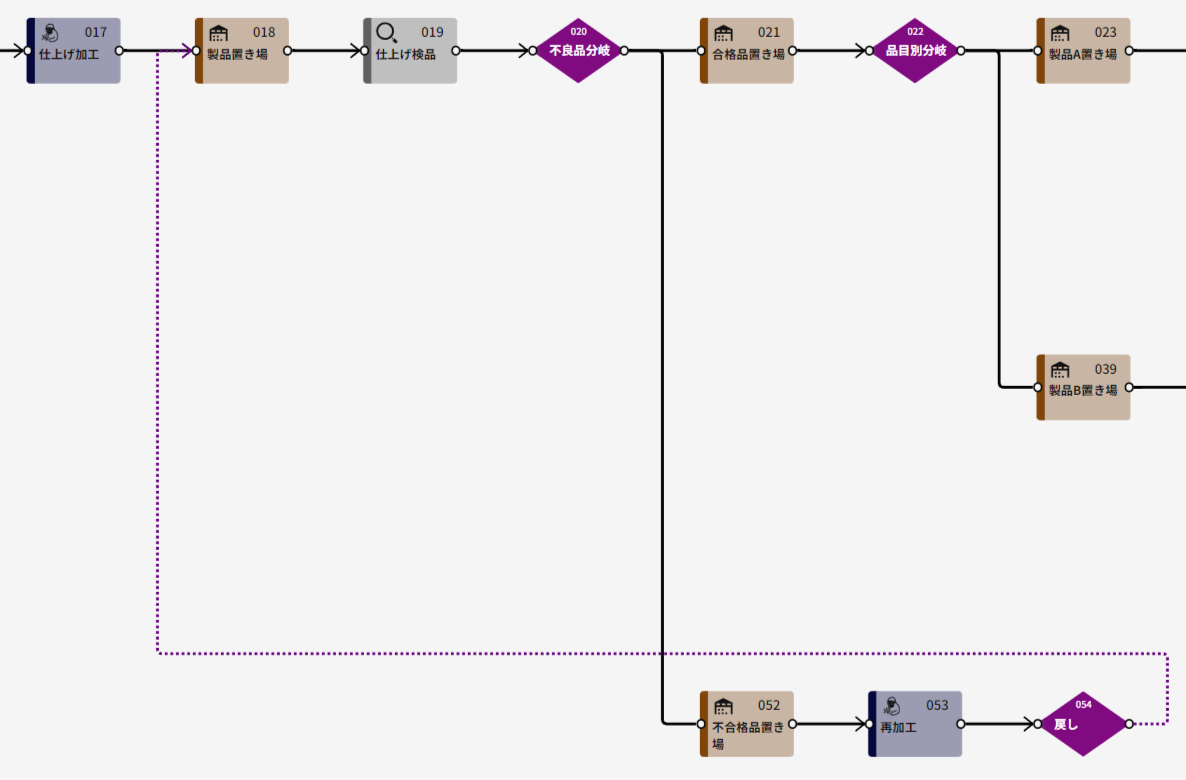
シミュレーション結果と分析
モデルの作成とパラメーターの設定が終了したらシミュレーションを行います。今回は8時間に相当する480分に設定した上で、修理や段取り替え、工具交換といったパラメーターを設定していない状態でシミュレーションを行います。
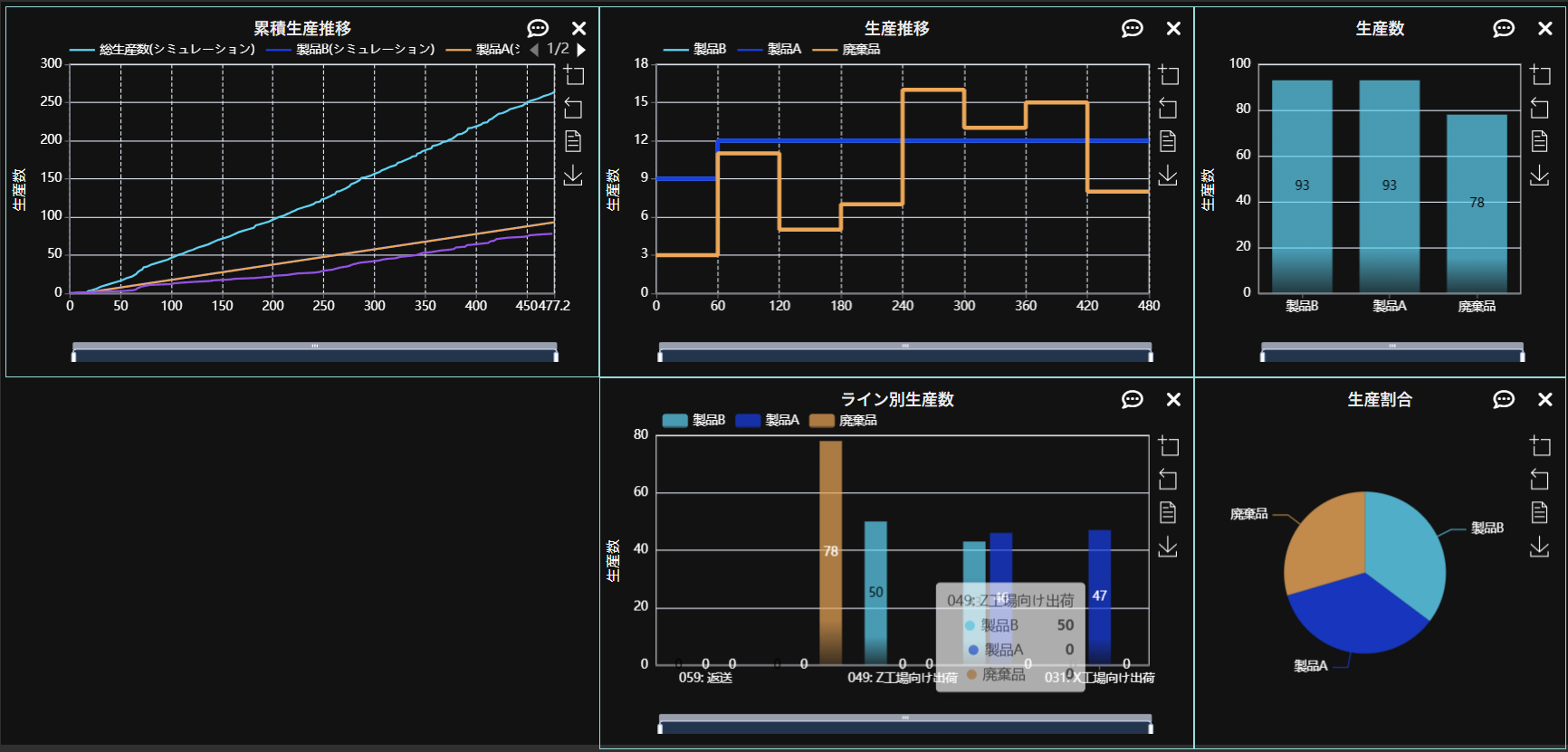
修理間隔と修理時間の設定
まず最初に修理時間を設定し、シミュレーションへの影響を見てみます。
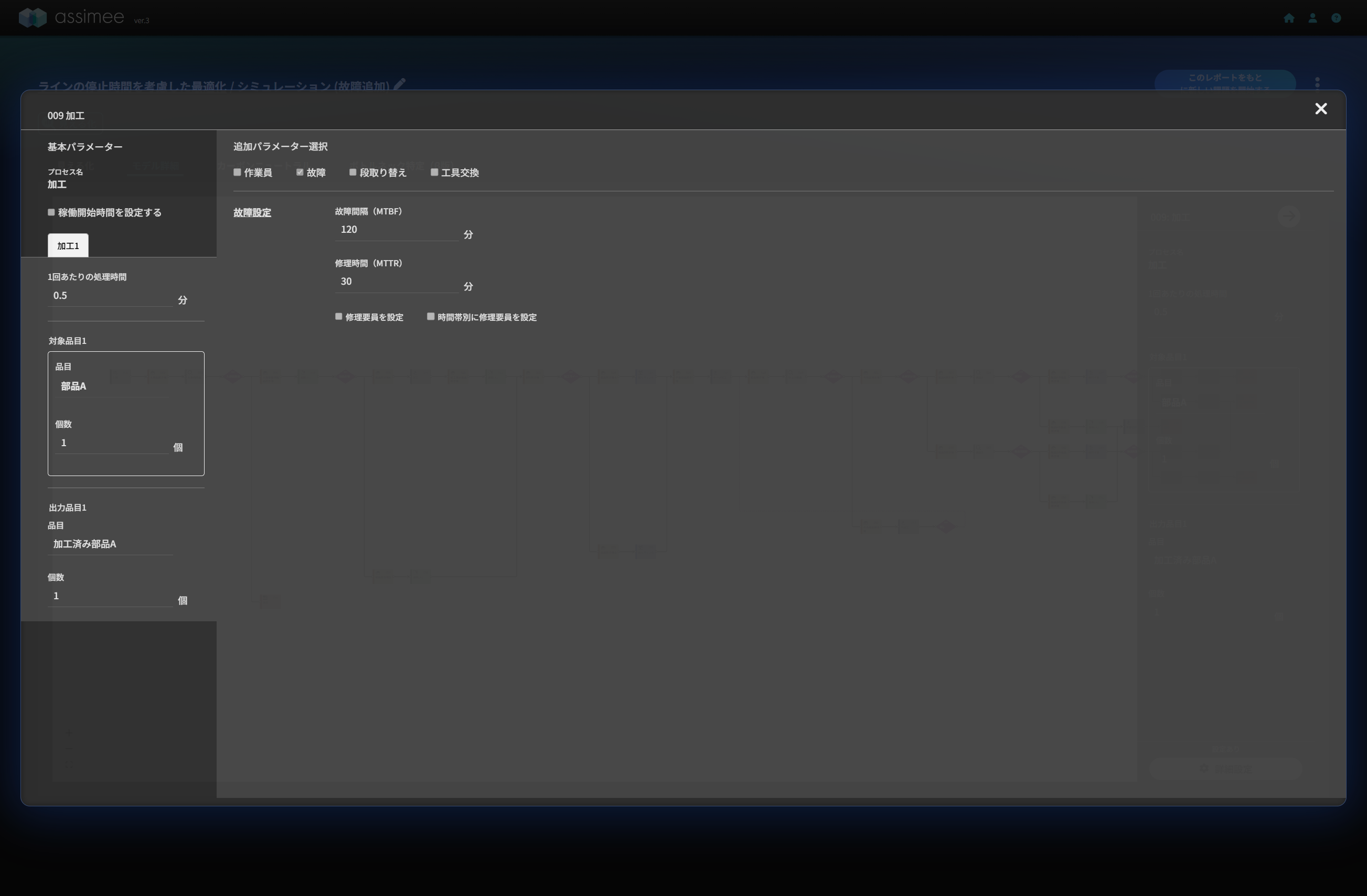
上図のように設定すると、「009加工」に対して120分の稼働対して1回の割合で故障し、故障修理に30分を要するようになります。これにより加工済み部品Aの供給が減るので生産数が減ることが予想されます。実際にどうなるかをシミュレーションで確認してみましょう。
*故障間隔はシミュレーション時間でなくプロセスの稼働時間になります。つまり、稼働率100%のプロセスであれば120分で1回の故障となりますが、稼働率が50%のプロセスであれば240分で1回の故障、稼働率が0%のプロセスであればまったく故障しないことになります。
シミュレーションの結果は以下のようになりました。ステータス推移をみると故障が発生し、修理を行っていることが分かります。しかし、変更前に93個ずつだった製品Aと製品Bの生産数は変わらず93個でした。
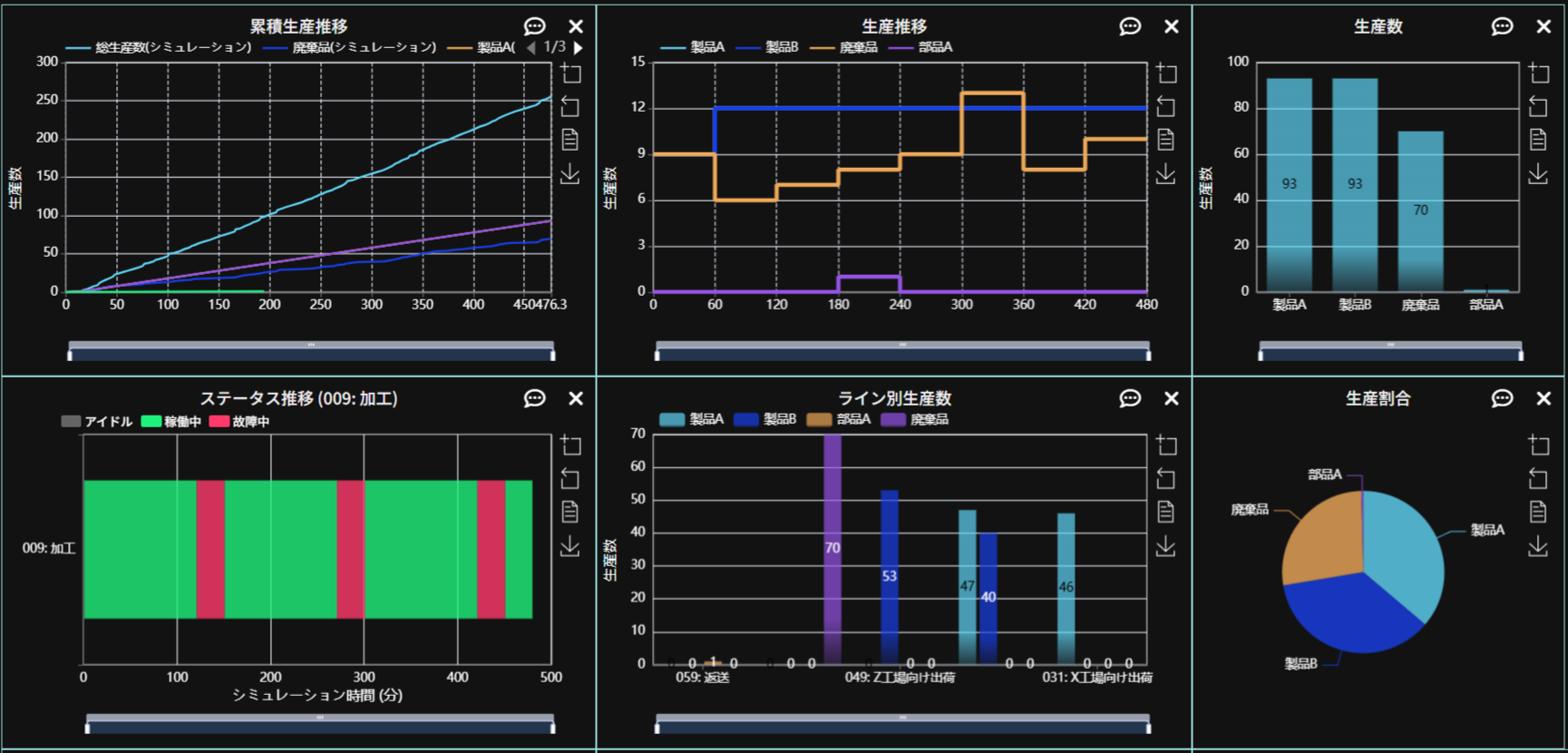
これはなぜでしょうか?なぜ、故障が発生しているのに生産数が減っていないのかを他のプロセスを見て分析してみましょう。
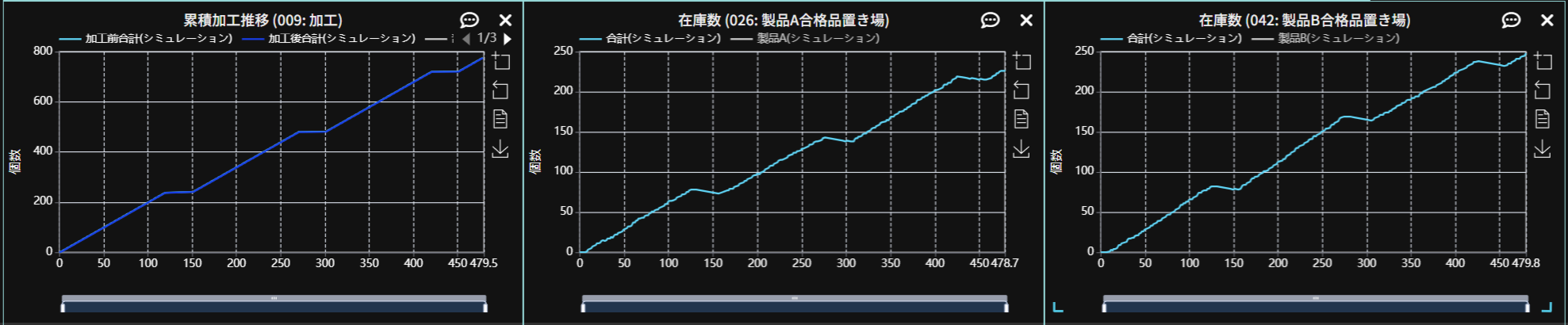
左:「009加工」の累積加工推移
中:「026製品A合格品置き場」の在庫量
右:「042製品B合格品置き場」の在庫量
上図は故障を設定した「009加工」の累積加工推移と、完成品が一時的に置かれる「026製品A合格品置き場」と「042製品B合格品置き場」の在庫量を見たものです。確かに「009」加工には120分に1回30分間の停止が起きていることが分かります。一方で2つの在庫置き場の在庫量がこの生産停止に対して十分にあり、在庫が加工の停止をカバーし、生産の落ち込みを防止していたことが分かりました。
工具交換間隔と時間の設定
初期状態に戻してから、次に「017仕上げ加工」に対して、下図のように稼働時間240分ごとに、30分の時間をかけて工具を交換する設定を行います。これにより製品の供給が減るので生産数が減ることが予想されます。実際にどうなるかをシミュレーションで確認してみましょう。
*この時の工具交換時間も故障間隔と同様にシミュレーション時間でなくプロセスの稼働時間になります。
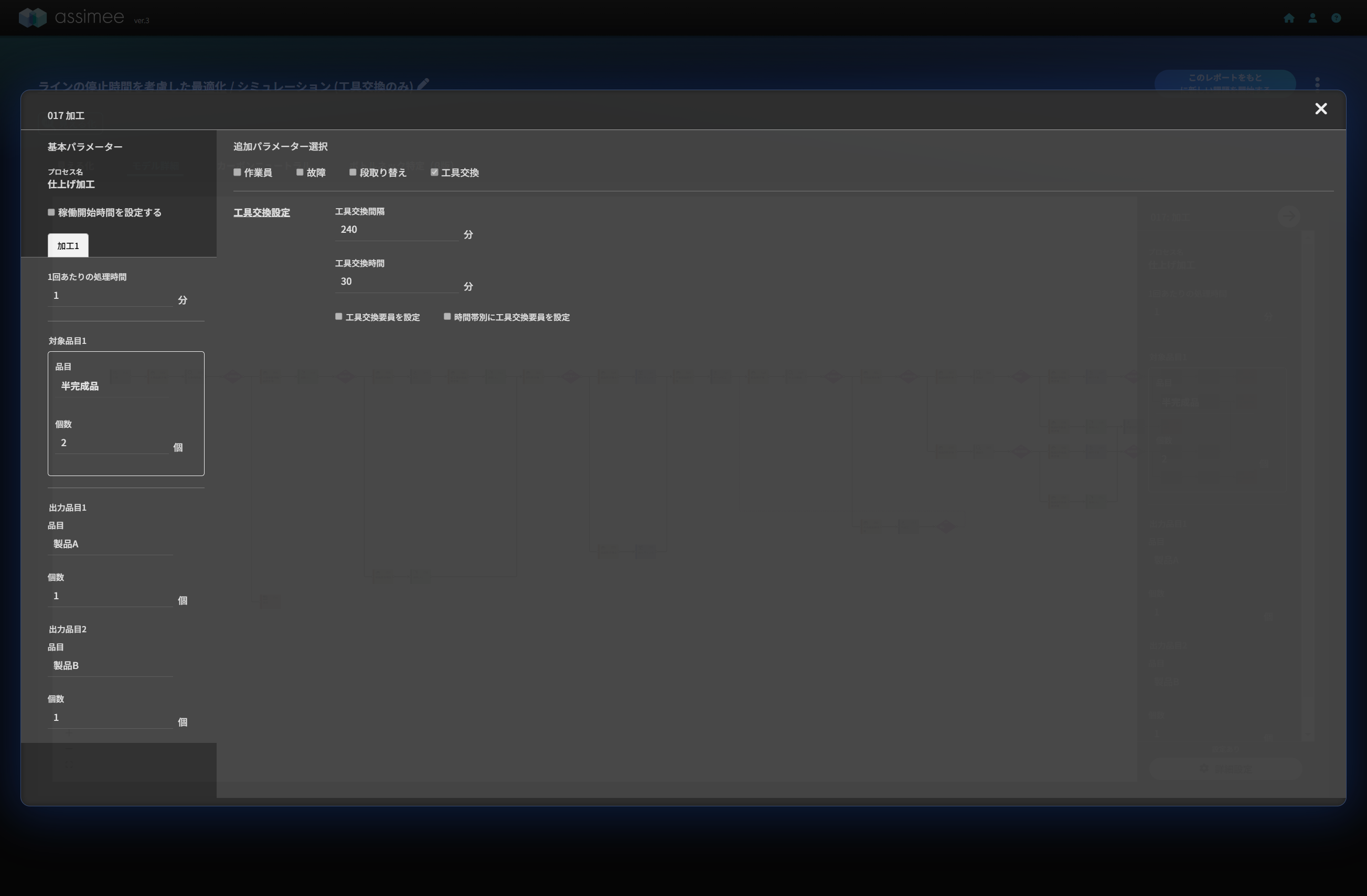
シミュレーションの結果は以下のようになりました。こちらもステータス推移をみると工具交換時間が発生しています。生産数は変更前の93個ずつから変わらず93個でした。*廃棄品が多いですが、こちらはランダムの範囲内です。
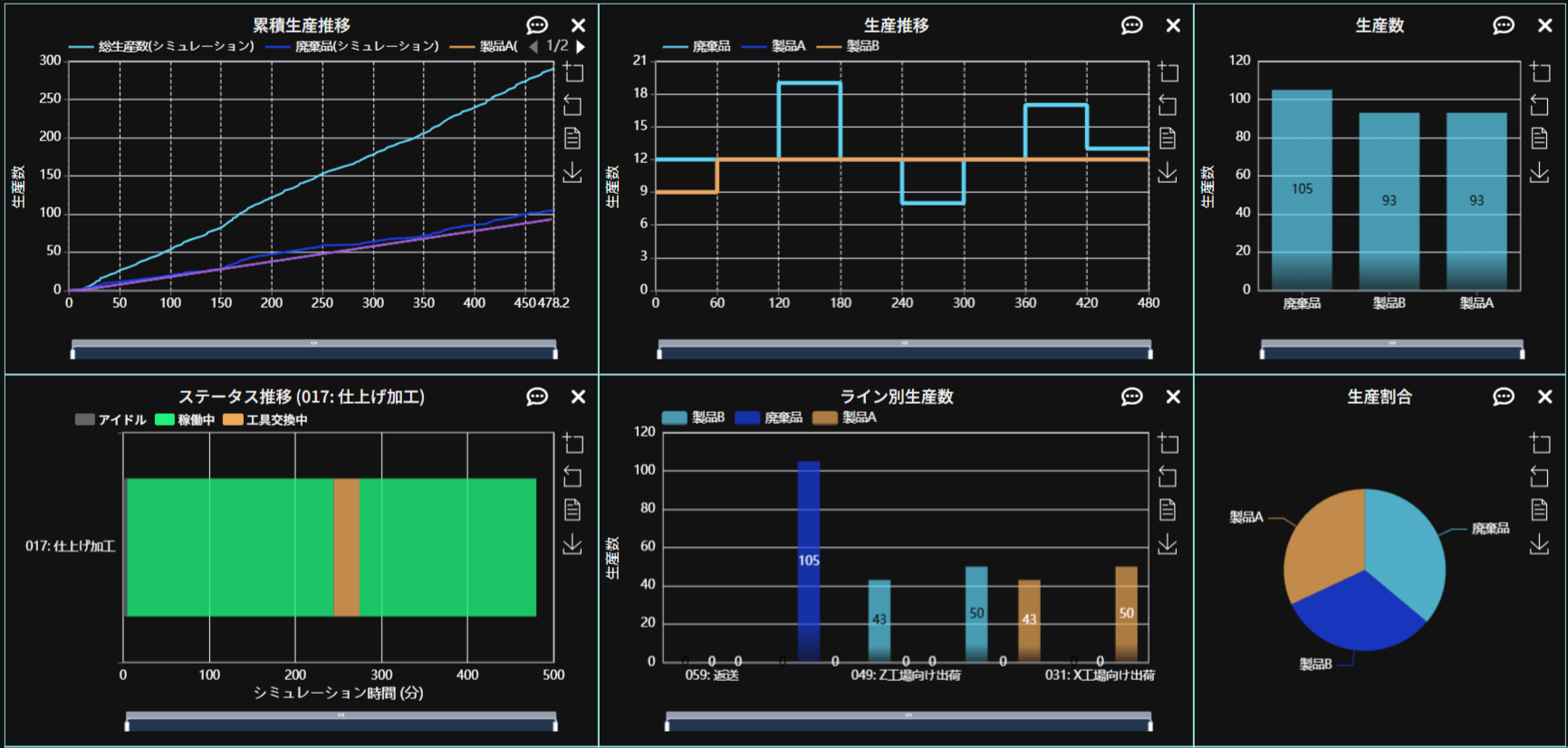
こちらもなぜ出荷が減っていないのかを分析してみます。
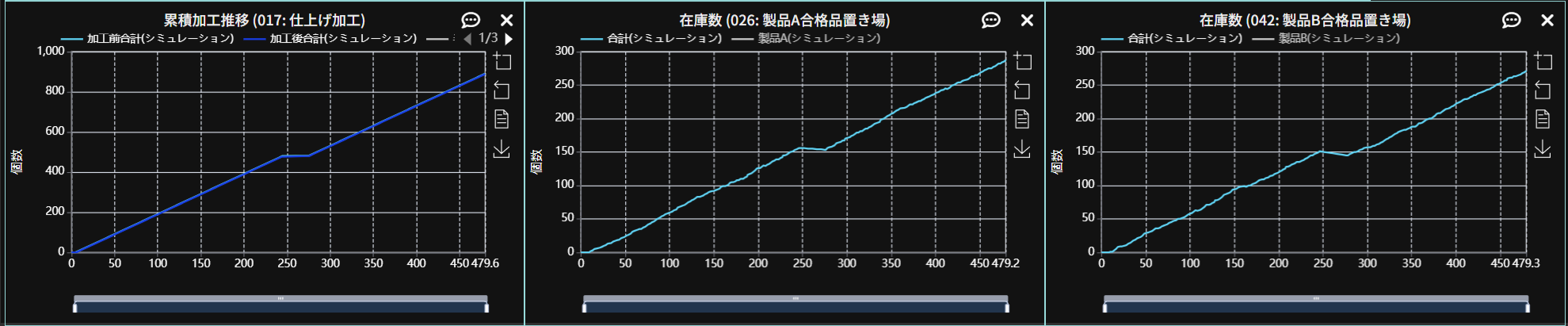
左:「017仕上げ加工」の累積加工推移
中:「026製品A合格品置き場」の在庫量
右:「042製品B合格品置き場」の在庫量
上図は故障を設定した「017仕上げ加工」の累積加工推移と、先ほどと同様に完成品が一時的に置かれる「026製品A合格品置き場」と「042製品B合格品置き場」の在庫量を見たものです。こちらも240分で30分間の停止が起きていることが分かりますが、一方で、2つの在庫置き場の在庫量が生産停止に対して十分にあり、在庫が出荷の落ち込みを防止していたことが分かりました。
段取り替え時間の設定
次に段取り替え時間を設定してみましょう。
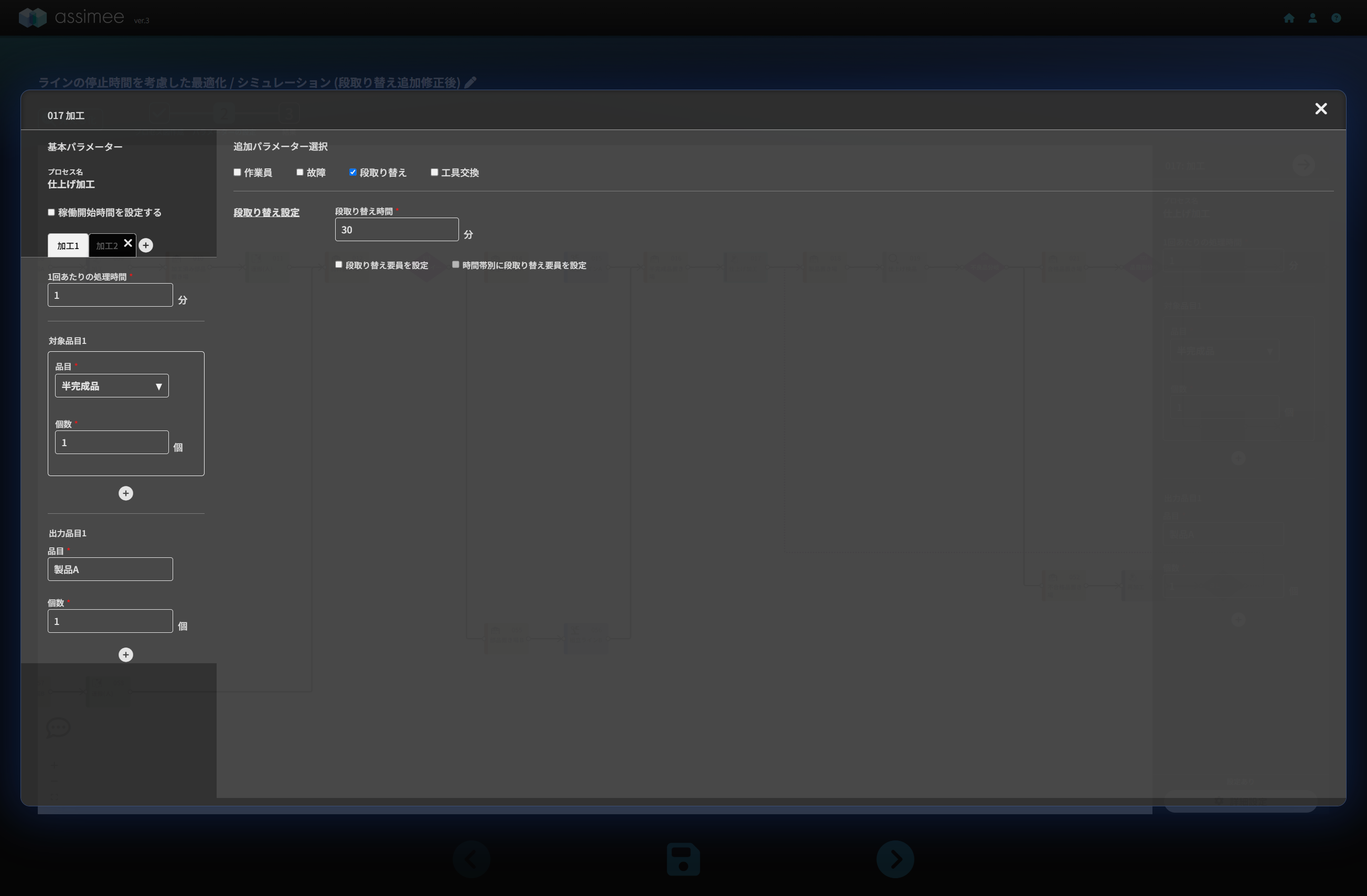
シミュレーションの結果は以下のようになりました。こちらは変更前に93個ずつだった製品Aと製品Bの出荷量が合計で27個まで減っています。
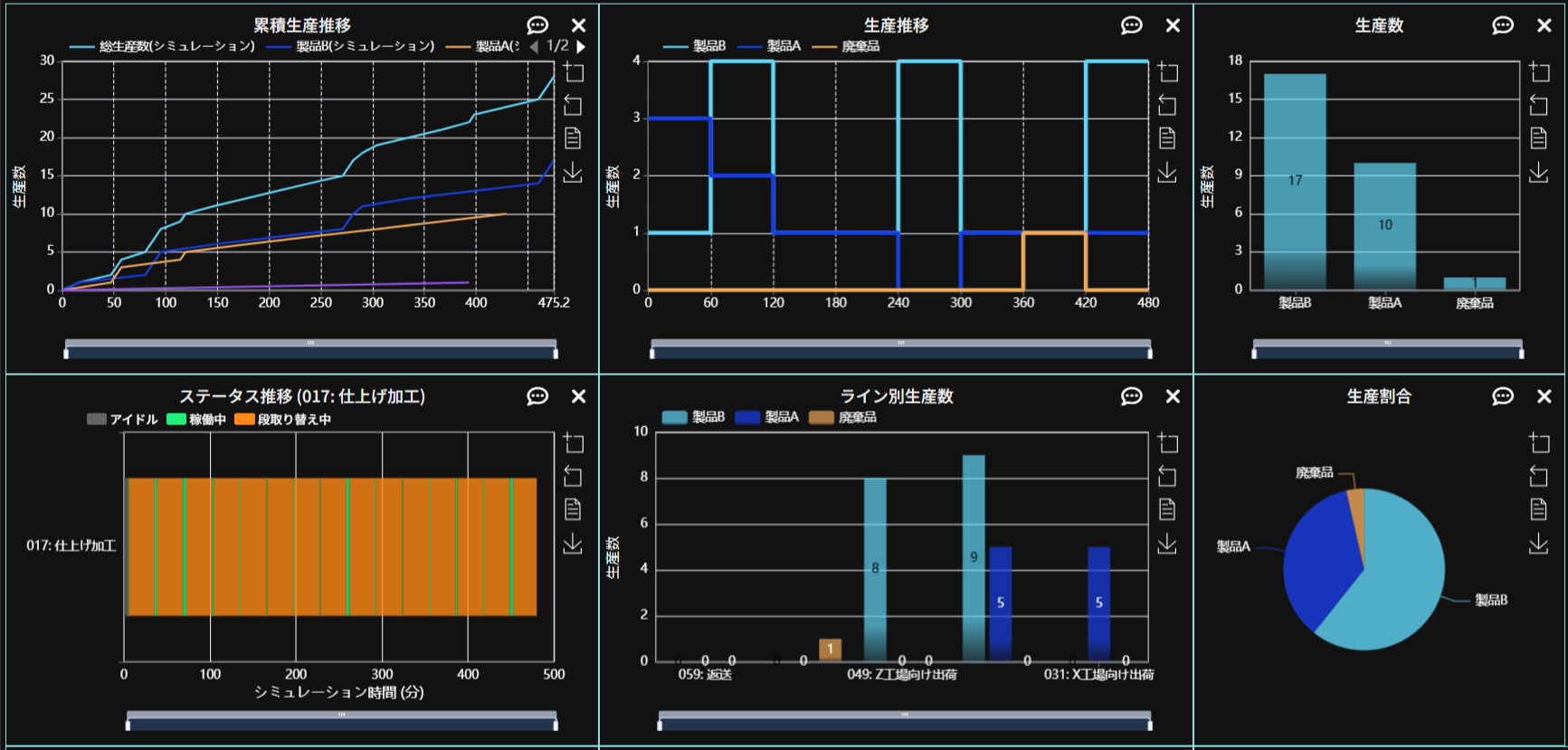
先ほどと同じように分析を行うと、段取り替え時間の設定の結果、ステータス推移は段取り替えが多発して生産があまり行われていないことが分かります。次に「017仕上げ加工」の累積加工推移と「016半完成品置き場」の在庫量を確認します。
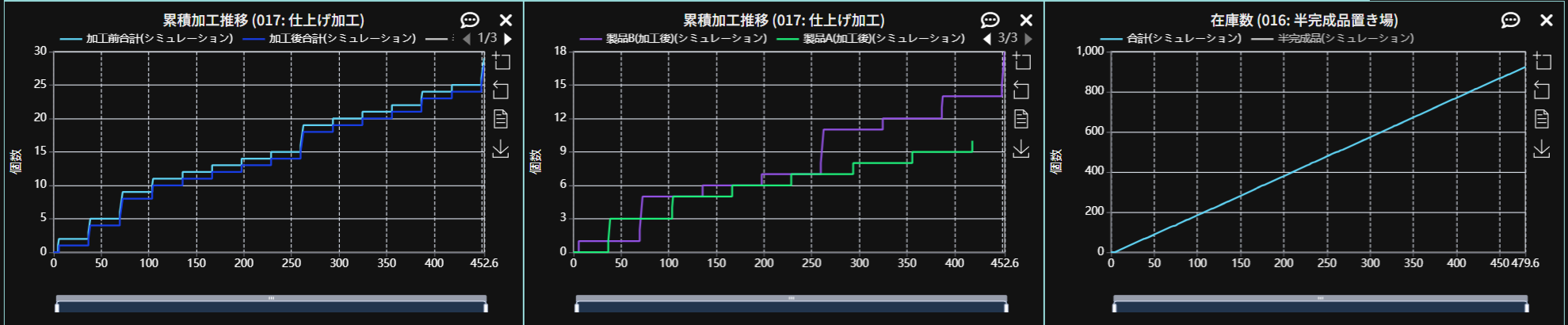
左:「017仕上げ加工」の累積加工推移
中:「017仕上げ加工」の累積加工推移の製品A、製品Bのみ
右:「016半完成品置き場」の在庫量
段取り替え時間を設定した分、製品の生産が遅くなっていることが分かります。加えて段取り替えが1個製品を作るたびに発生していることが分かります。これは、加工に今回のように製品Aのパターンと製品Bのパターンを設定した場合、同時の加工は出来ないので、ランダムに製品を生産することになります。この際にどちらか一方を優先したり、段取り替えが最小になるように加工するわけではないため、ほぼ毎回段取り替えが発生します。
これを解消するには製品AとBのどちらか片方の生産だけを行うように設定し、片方が終わってからもう片方の生産を行うように入荷で生産をコントロールする必要があります。または、分岐を使用して品目(製品A、製品Bそれぞれのラインを用意する)ごとの加工とする方法もあります(この場合もシミュレーションを現実に近づけるには入荷で生産をコントロールする必要があります)。
まとめ
今回の記事では製造工場を想定した比較的大規模なモデルを作成して段取り替えや工具交換のための停止時間が生産に与える影響をシミュレーションで確認する方法を説明しました。assimeeではこのように故障の間隔と修理時間、工具交換の間隔と交換時間、段取り替え時間を細かく設定することが出来ます。次回は同様のモデルを改修した上で修理時間や工具交換の時間を含んだ最適化の方法とその結果の分析について解説します。
assimeeでは、実際の製造プロセスをモデル化し、シミュレーションすることで、プロセスの見える化や潜在的な課題の洗い出しを行うことができます。製造プロセスのデジタル化や課題解決でお悩みの方は、ぜひお問い合わせください。