ー概要ー
実際の生産ラインや物流倉庫では、個々の作業員の作業効率は異なっています。特に、ベテラン作業員と新人作業員では大きく作業効率が異なり、作業効率の管理は現場の生産を管理するに当たっての大きな課題となっています。不特定多数の派遣社員を使用する場合など、作業効率が異なる場合には標準作業効率を定義しての管理が行われますが、標準作業効率の定義は経験が必要な業務でした。
一方で、assimeeでは異なる作業効率を持った人員を配置してシミュレーションを行うことが可能であり、より緻密な人員配置計画を容易に立てるのに役立ちます。このようなシミュレーションを通じて、異なる作業効率を持つ作業員の適切な配置や生産ラインの最適化が行われることで、生産性の向上や効率化が実現されると考えられます。
ーモデルの作成ー
使用するのは以下の通りのモデルで、小規模な物流倉庫や工場を想定したモデルです。入荷→置き場→加工→置き場→作業→運搬→出荷の各プロセスからなります。以下が完成したモデルのプロセス図となります。

今回は「005梱包作業」の作業員の作業効率設定を例にとって、他のパラメーターを固定した上で、作業効率を変えながらシミュレーションの結果がどう変わるか分析してみましょう。処理員の作業効率は以下の図のように詳細設定画面から作業効率で設定します。作業効率が「1」の作業員1人は「0.5」の作業員1人の2倍の効率で作業ができることを意味します。*作業効率の上限は1なので、作業効率の異なる人員を混在させる場合は作業効率の高い方を「1」として設定してください。
処理時間を持つ作業員を複数設定したい場合は+ボタンを押すことで、図のようにグループを増やすことが可能です。こうすることで、多種多様な作業員が処理を行う状態を再現できます。
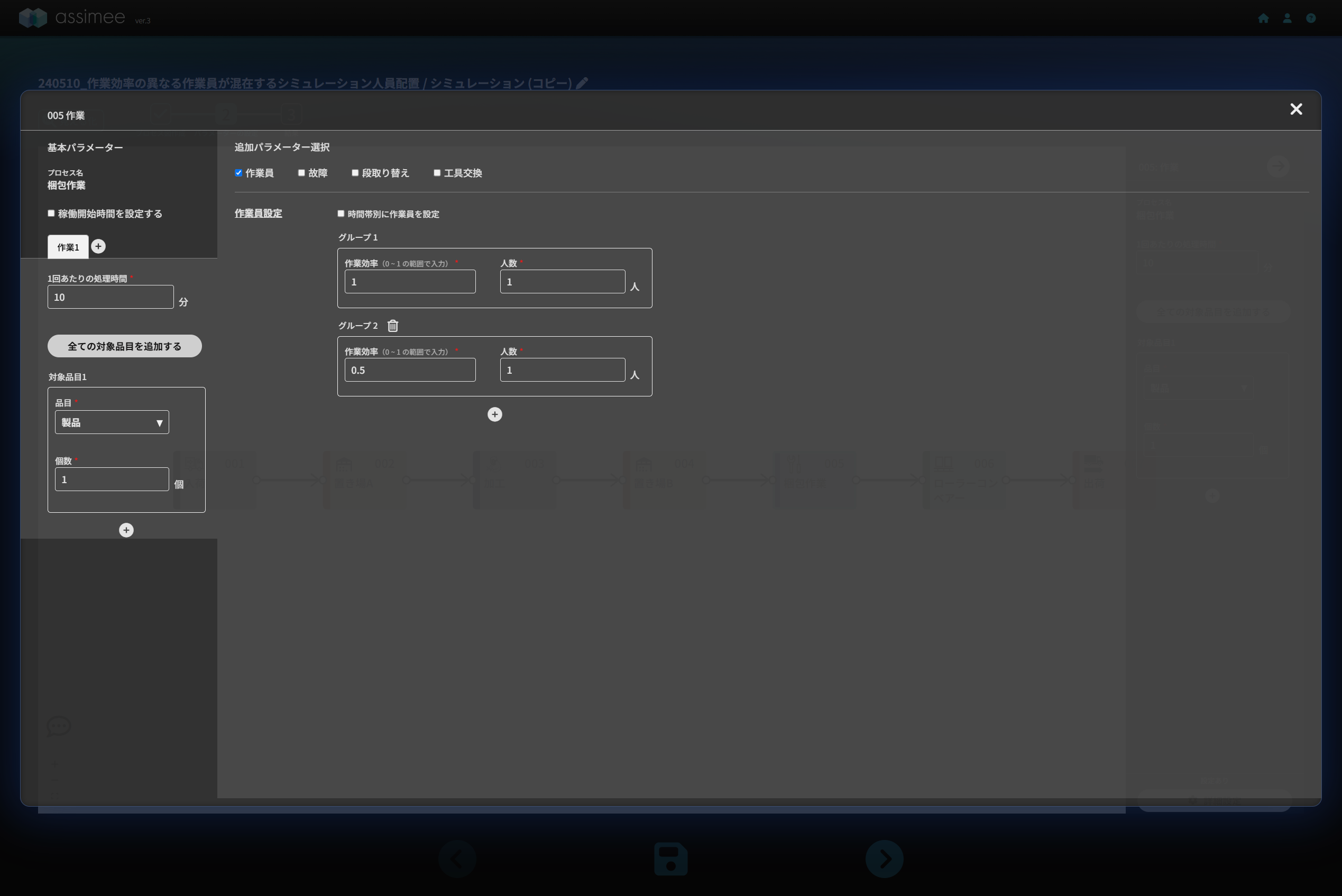
(作業効率「1」の作業員1人、「0.5」の作業員1人の場合)
ーシミュレーションと分析ー
シミュレーションをするにあたって、作業効率が「1」の作業員が2人いる状態を初期状態として、比較を行っていきます。シミュレーション時間は「480分」に設定して、シミュレーションを行うと初期状態では以下の結果が表示されます。
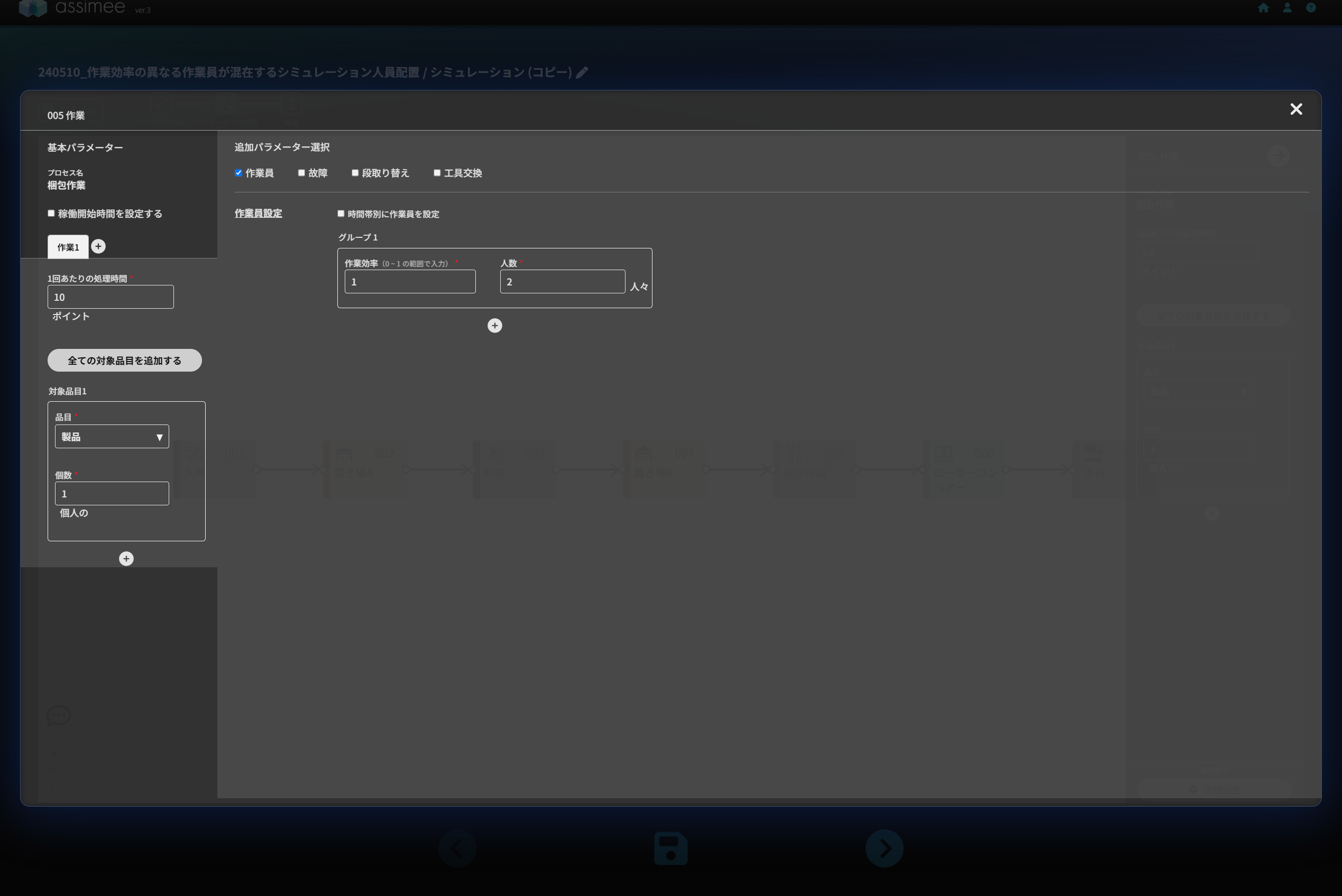
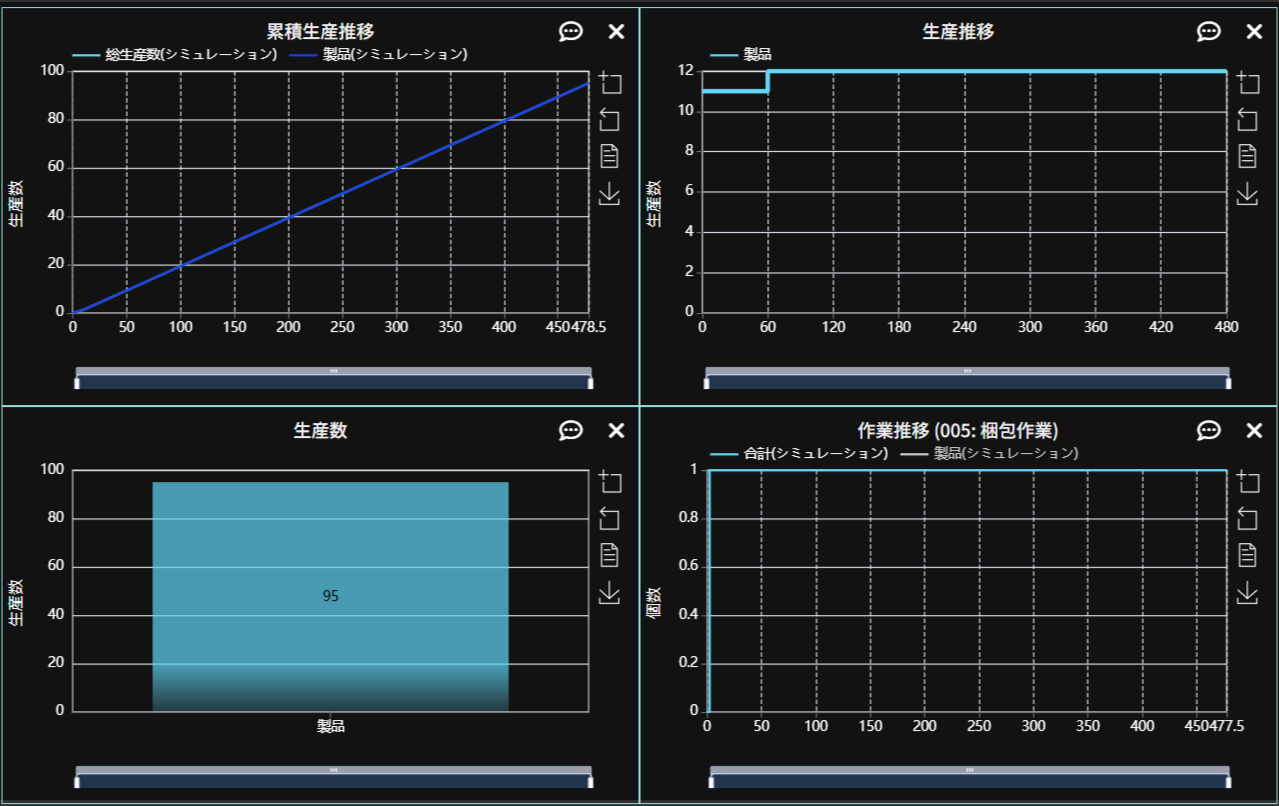
次に、作業効率が「0.5」の作業員が2人いる状態でシミュレーションを行い、その結果と比較してみましょう。作業効率が「0.5」とは「1」の時と比べて1回あたりの処理時間が倍ということになるため、品目の生産量が半分になることが想定されます。

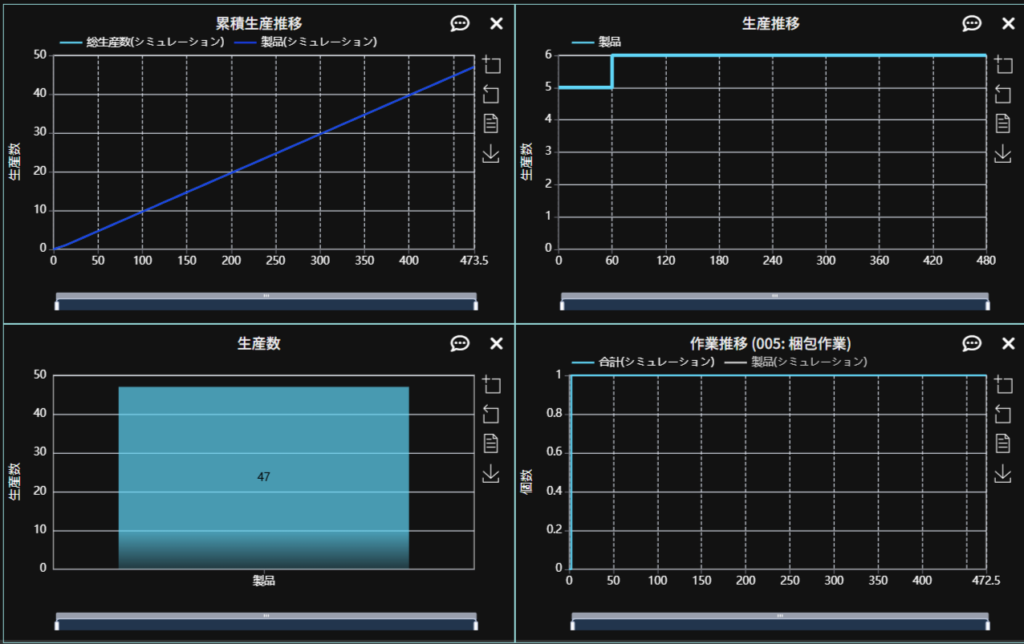
生産個数が想定通り半分になっていることが分かります。次に、作業効率が「1」の作業員1人と「0.5」の作業員1人とし、作業効率の異なる作業員を混在させてシミュレーションを行ってみましょう。今度はどうなるでしょうか?
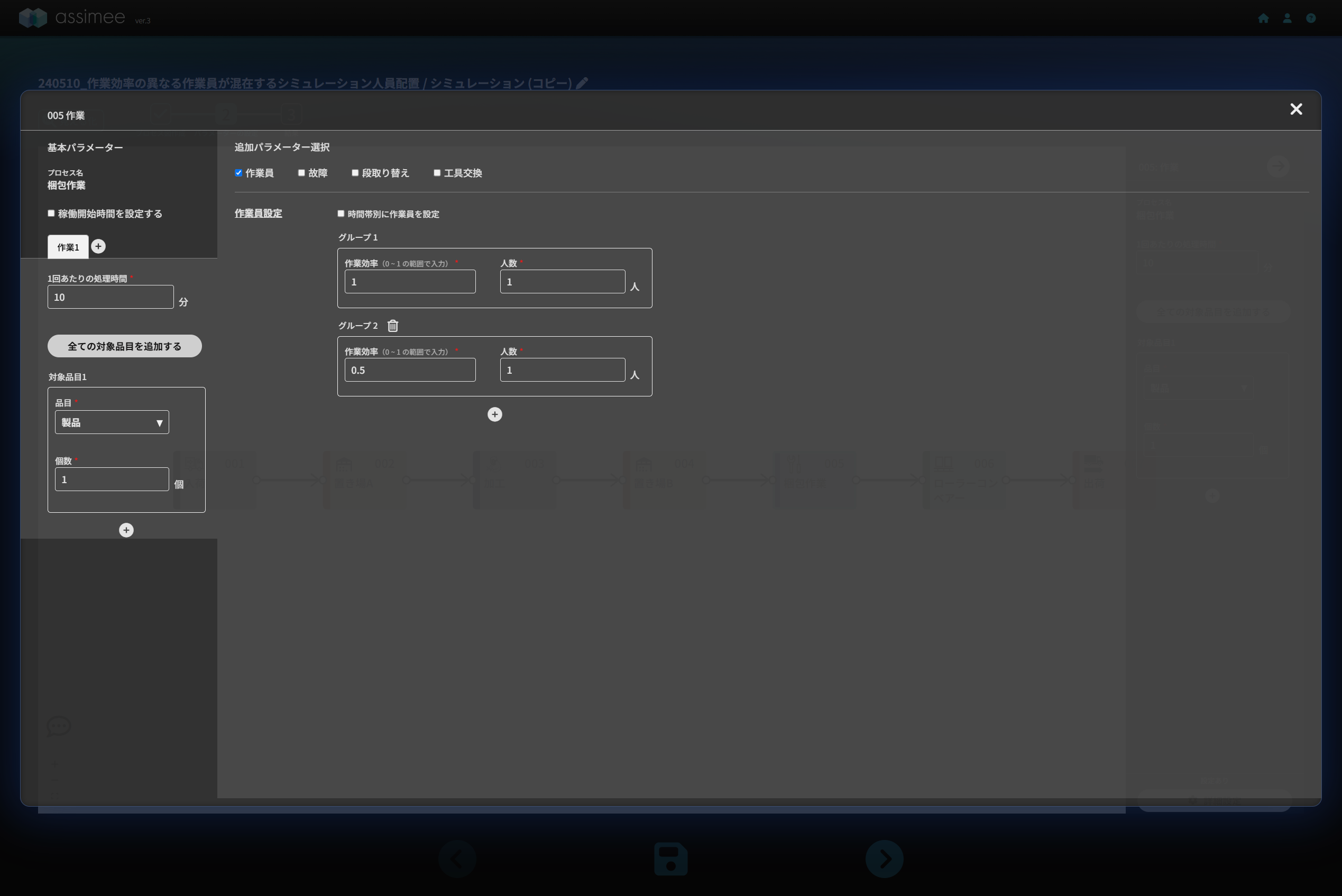
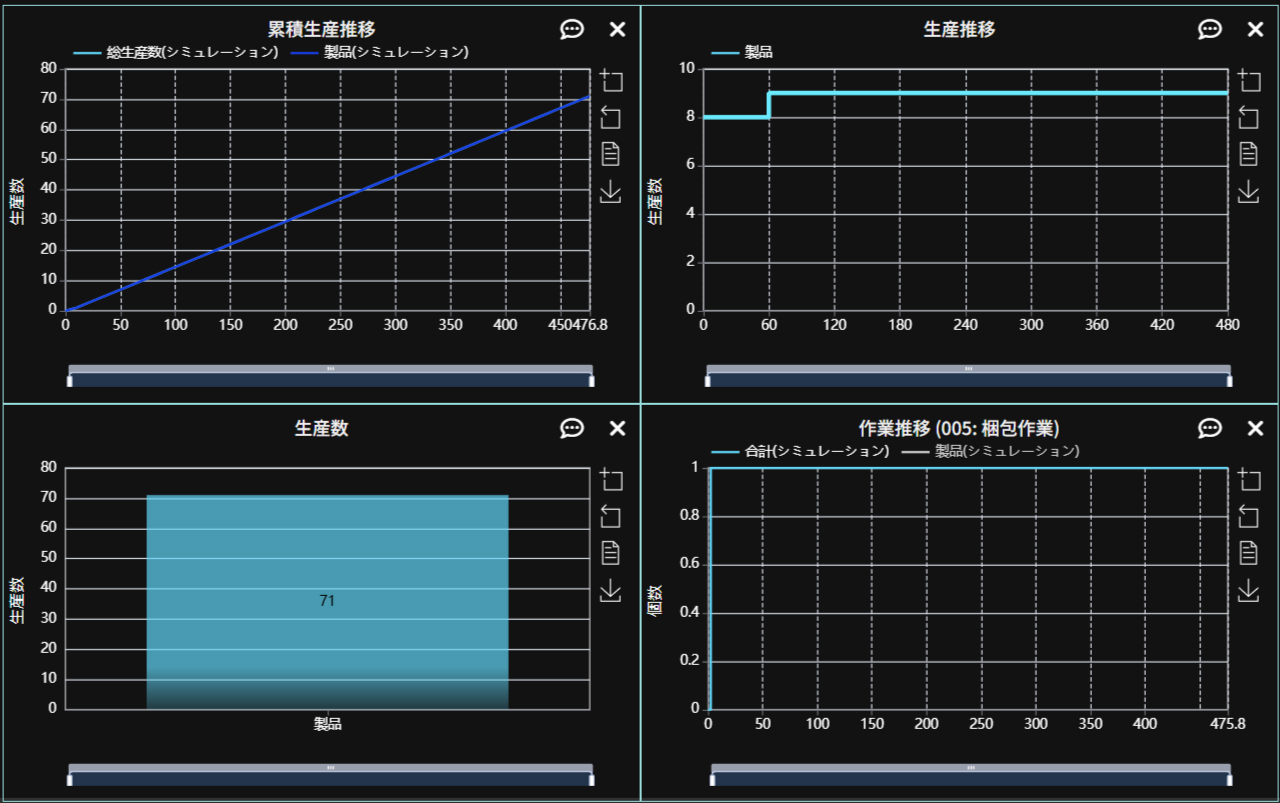
結果を見ると、生産量は最初の結果(作業効率1の作業員2人の場合)と2番目の結果(作業効率0.5の作業員2人の場合)の中間の結果となりました。
このように作業員の作業効率を細かく考慮してシミュレーションを行うことが、生産計画を立てる上で重要であることを示しています。
ーまとめー
今回は小規模な工場や物流倉庫をモデルに、作業効率の異なる人員を配置してシミュレーションを行う方法を解説しました。assimmeでは、1人1人の作業効率が異なるような極端な場合でもシミュレーションを行うことが可能です。少子高齢化による労働者不足が予想される中、1人1人の作業効率も考慮したシミュレーションを行い、人員配置や生産計画の検証を行うことが、これからますます重要になると考えています。
assimeeでは、実際の製造プロセスをモデル化し、シミュレーションすることで、プロセスの見える化や潜在的な課題の洗い出しを行うことができます。製造プロセスのデジタル化や課題解決でお悩みの方は、ぜひお問い合わせください。