概要
生産現場では製品1個当たりの生産工程に必要な正味の時間(サイクルタイム)を知ることが重要です。サイクルタイムを発注数から決まるタクトタイムと比較することで、効率的な生産計画の立案が可能となるため、サイクルタイムの計算は生産ラインの稼働に不可欠です。assimeeで生産ラインのモデルを作成しておけば、現地の生産ラインで測らなくても、生産ラインの設定条件を変えながら比較を行いたい場合や、アクシデントでの生産ライン停止が生産へ及ぼす影響を想定することが、可能になります。今回の記事では、生産ラインのモデルを作成し、生産ライン全体のサイクルタイムの計算を行う他、アクシデント発生を想定した場合の例について解説します。
モデル
以下の図のような生産ラインのモデルを作成します。

今回は、生産ラインで100個の製品を製造する時間をシミュレーションで計算し、その平均をとってサイクルタイムを求めます。いくつのデータで平均を取るか等の設定は生産ラインによって変わってくるので、適宜変更して考えてください。
STEP1 プロセス図を作成する
次のようにプロセスカードを配置してモデルを作成します。
入荷プロセス:
特に変更なし
置き場プロセス:
プロセス名を「置き場A」へ変更
加工プロセス:
プロセス名を「プレス加工A」へ変更
置き場プロセス:
プロセス名を「置き場B」へ変更
加工プロセス:
プロセス名を「曲げ加工」へ変更
置き場プロセス:
プロセス名を「置き場C」へ変更
加工プロセス:
プロセス名を「プレス加工B」へ変更
出荷プロセス:
特に変更なし
STEP2 パラメーターを設定
次のようにモデルにパラメーターを設定して行きます。
001入荷:
「開く」ボタンを押し、入荷品目を「部品」、入荷時刻を「0分」、個数を「100個」と設定
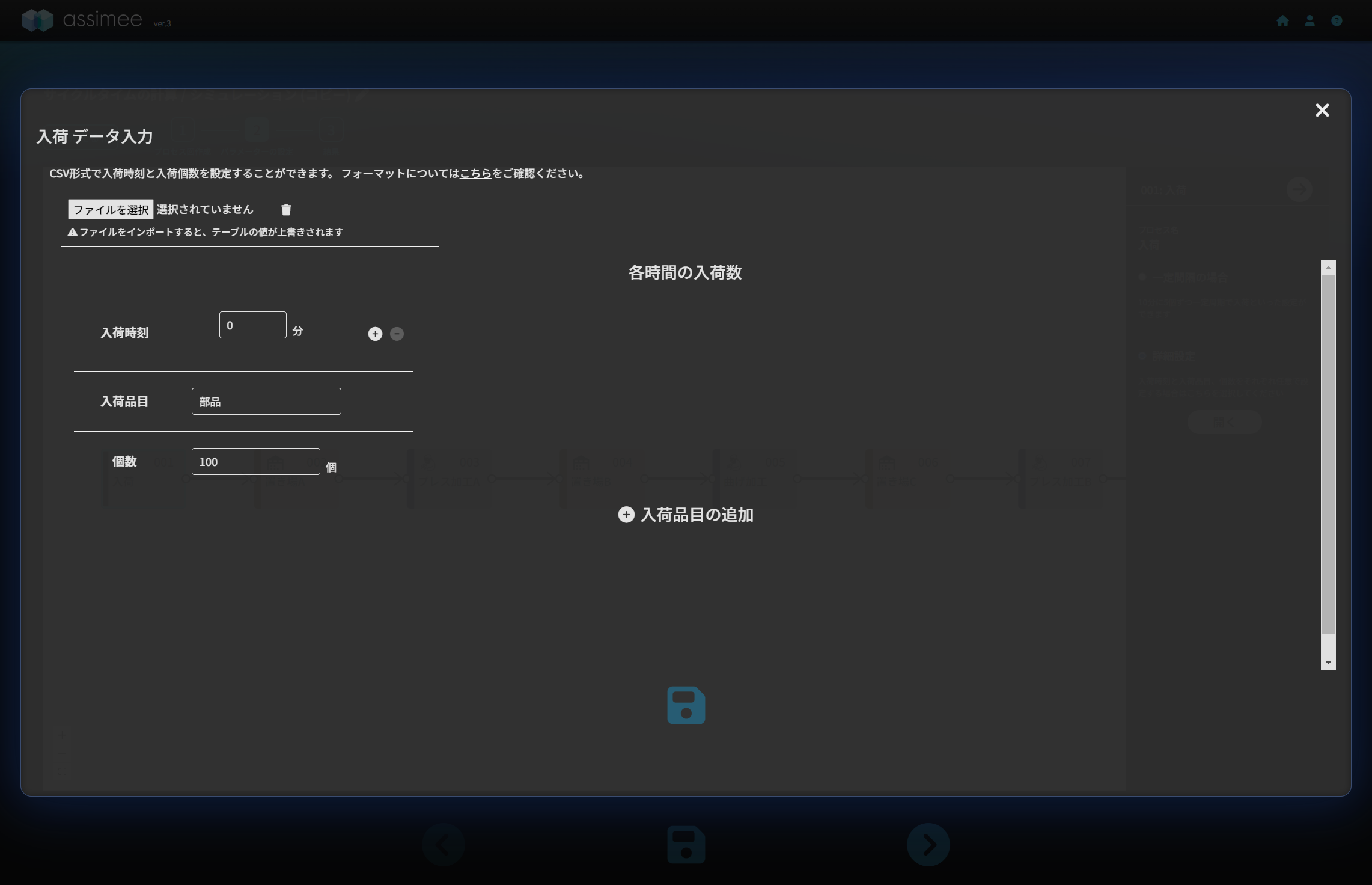
002置き場A:
容量を「1000個」と設定
003加工A:
1回あたりの処理時間を「5分」と設定
対象品目を「部品」、個数を「1個」、
出力品目を「プレス済部品」、個数を「1個」と設定
004置き場B:
容量を「1000個」と設定
005曲げ加工
1回あたりの処理時間を「5分」と設定
対象品目の名称を「プレス済部品」、個数を「1個」、
出力品目の名称を「曲げ加工済部品」、個数を「1個」と設定
006置き場:
容量を「1000個」と設定
007プレス加工B:
1回あたりの処理時間を「5分」と設定
対象品目の名称を「曲げ加工済部品」、個数を「1個」、
出力品目の名称を「完成部品」、個数を「1個」と設定
008出荷:
特に変更なし
設定が終わったらモデルを保存します。
シミュレーション
モデルの作成が終了したら、保存を行った上で、シミュレーションを行います。今回は生産する個数と時間から大雑把に見積もった600分をシミュレーション時間に設定してシミュレーションをします。シミュレーションが終了すると以下のようなグラフが表示されます。表示されない場合はプロセスカードの設定を見直してください。
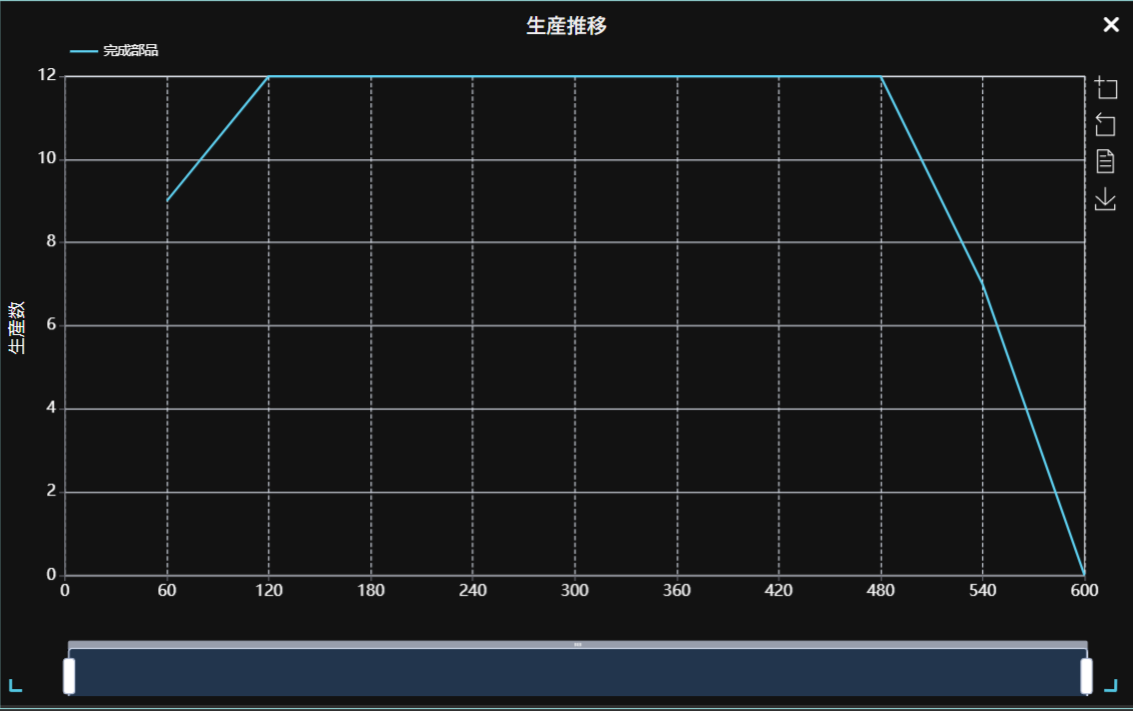
サイクルタイムの計算
サイクルタイムを計算するために、100個の生産にどれだけの時間がかかったかを下記のように「008出荷」のアイテム数推移のグラフから確認します。表示されたグラフにマウスを重ねると数字を読み取ることが出来ます。
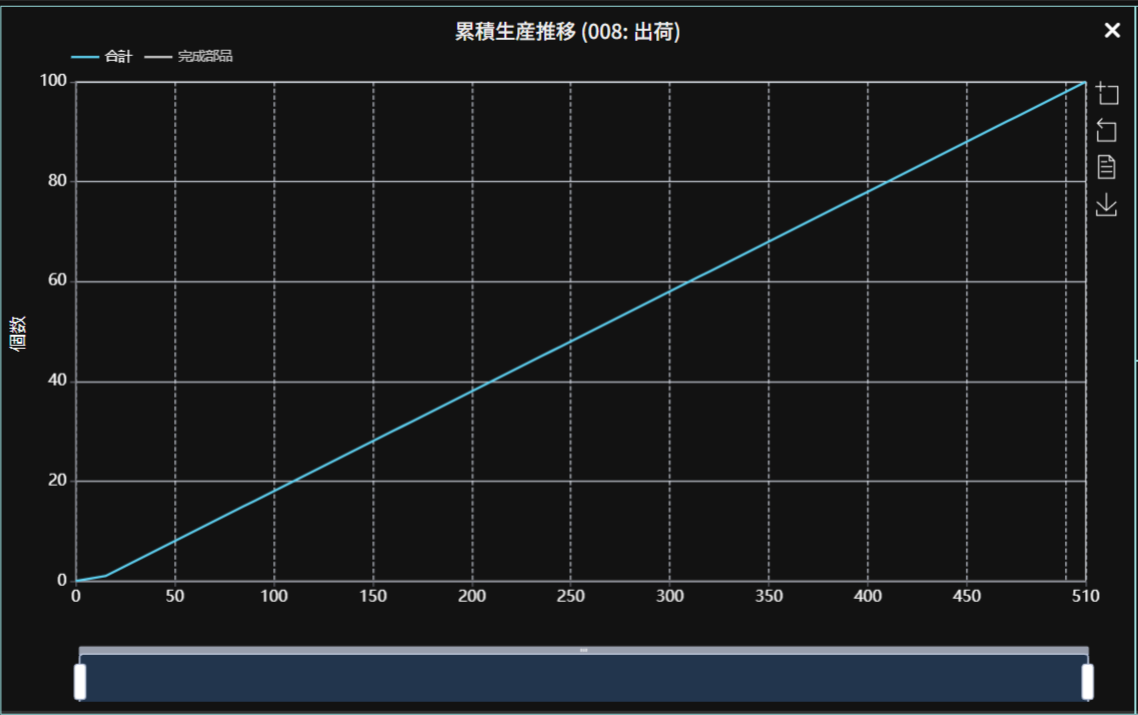
今回の生産ラインでは製品を100個生産するのにかかる時間は510分でした。よって、1個当たりの平均製造時間(サイクルタイム)は5.10分と分かります。
モデルにプロセスを追加
次に生産ラインのモデルを変更した上で再度計算を行なってみましょう。以下の図のようにモデルを変更します。

「001入荷」および3つの加工プロセス(「003プレス加工」、「005曲げ加工」、「007仕上げ加工」)の後に以下のようなローラーコンベアによる運搬プロセスを1つずつ追加し、製造にかかる時間を増やします。ここでは他のプロセスの設定は変更しません。*モデルのコピーを作成し、コピーしたモデルを編集すると作成が便利です。また、プロセスカードの附番は自動的に降り直されます。
ローラコンベアー:
「001入荷」の後に挿入、特に変更なし
ローラコンベアー:
「004プレス加工A」の後に挿入、特に変更なし
ローラコンベアー:
「007曲げ加工」の後に挿入、特に変更なし
ローラコンベアー:
「010プレス加工B」の後に挿入、特に変更なし
次にパラメーターを設定します。
002ローラコンベアー:
搬送時間を「5分」、最大積載個数を「10個」と設定
005ローラコンベアー:
搬送時間を「5分」、最大積載個数を「10個」と設定
008ローラコンベアー:
搬送時間を「5分」、最大積載個数を「10個」と設定
011ローラコンベアー:
搬送時間を「5分」、最大積載個数を「10個」と設定
変更が終わったら、モデルを別な名前で保存します。先ほどと同様に600分でシミュレーションを行い、生産時間を「012出荷」のアイテム数推移のグラフから確認し、サイクルタイムを計算します。
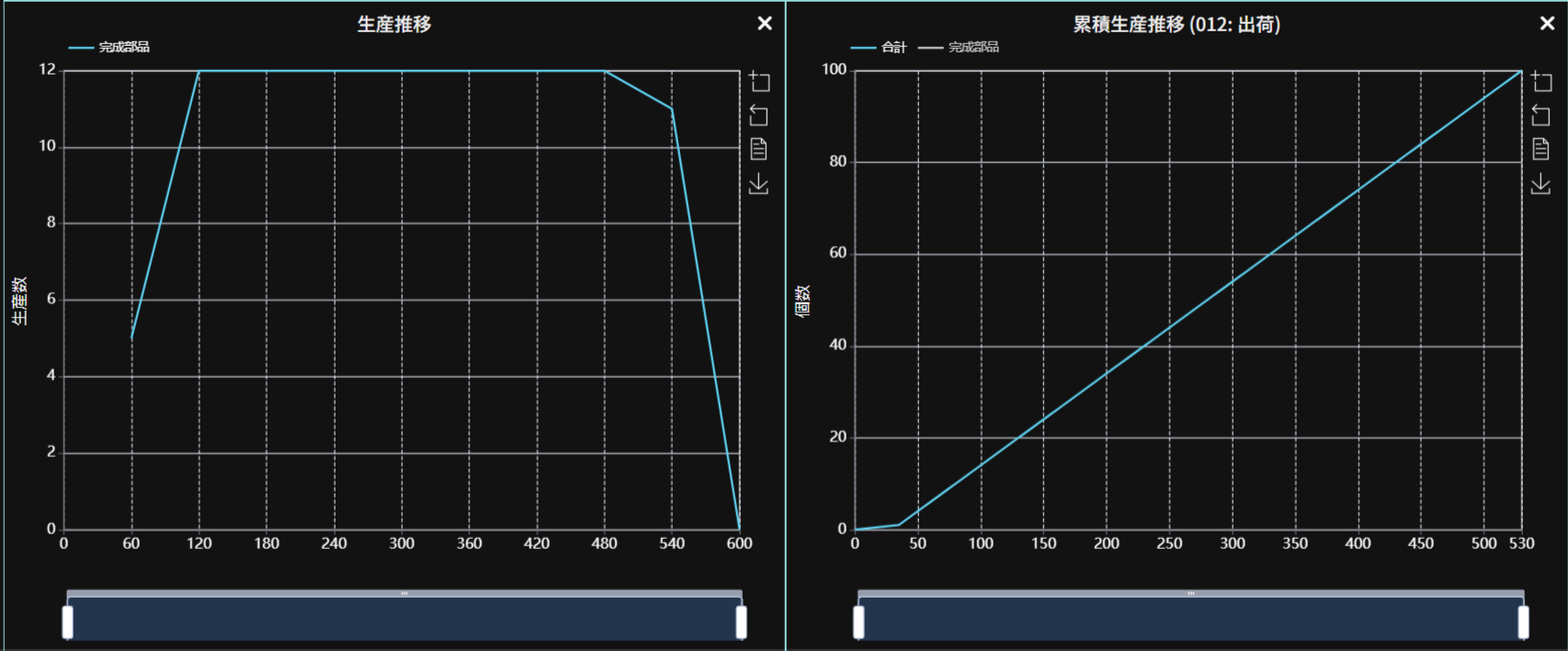
運搬の追加後のモデルでは、運搬プロセスを追加したため製品を100個生産するのにかかる時間は530分となりました。よって、1個当たりの平均製造時間(サイクルタイム)は5.30分と長くなりました。
モデルの処理時間と作業人数を変更
最後にモデルの中の加工プロセスの処理時間や作業人数を変更して計算をしてみましょう。モデルにプロセスは追加しませんが、加工プロセス(「004プレス加工」、「007曲げ加工」、「010プレス加工B」)の作業人数と処理時間を変更します。
004プレス加工A:
1回あたりの処理時間を「10分」、詳細設定から作業員にチェックを入れ、作業効率を「1」、作業人数を「3人」と設定
007曲げ加工:
1回あたりの処理時間を「5分」、詳細設定から作業員にチェックを入れ、作業効率を「1」、作業人数を「3人」と設定
010プレス加工B:
1回あたりの処理時間を「15分」、詳細設定から作業員にチェックを入れ、作業効率を「1」、作業人数を「4人」と設定
変更が終わったら、再度、シミュレーションを600分の設定で行い、「012出荷」のアイテム数推移のグラフを確認します。
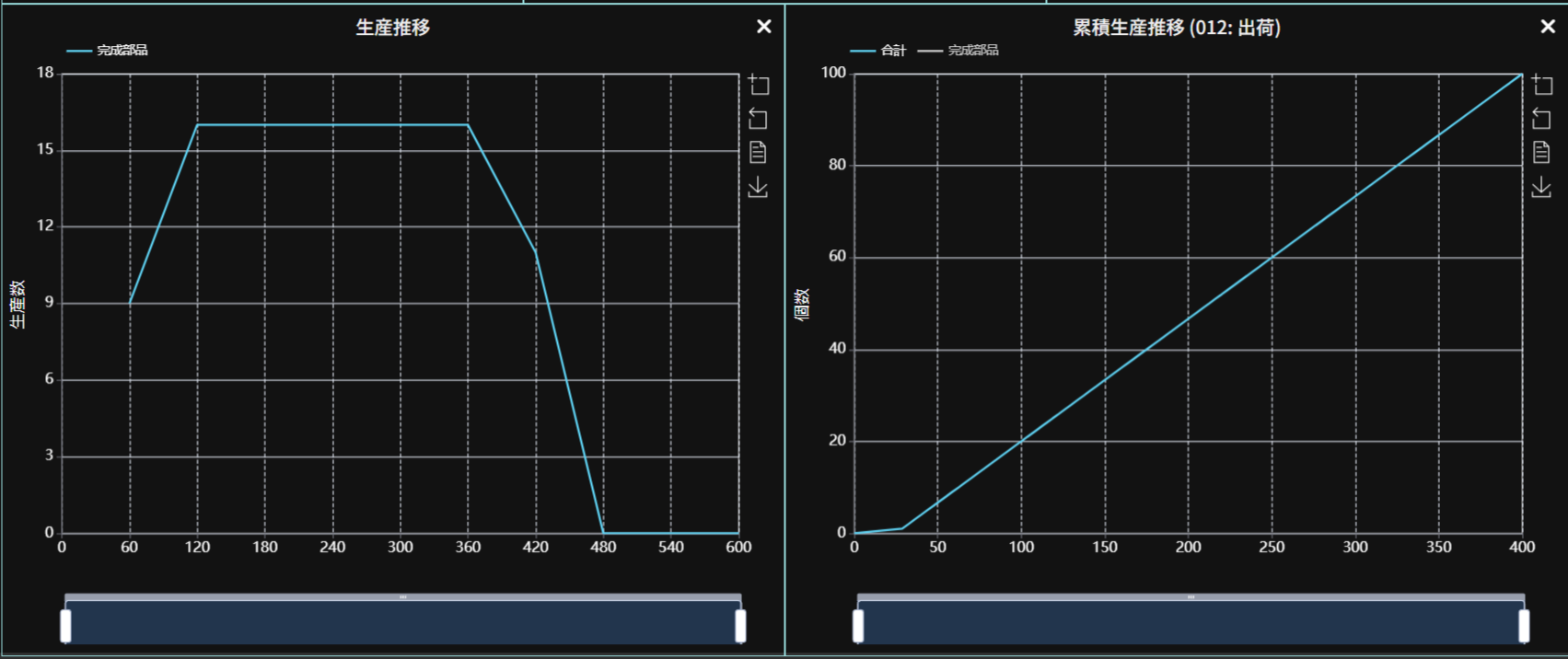
処理時間と作業人数の変更後のモデルでは製品を100個生産するのにかかる時間は400分となりました。よって、1個当たりの平均製造時間(サイクルタイム)は4.00分となります。
アクシデントの想定
次に設備故障などのアクシデントが発生したことを想定して、サイクルタイムへの影響を見積もる方法を解説します。
先ほどのモデルで、「007曲げ加工」で故障が発生して修理で生産がストップすることを想定します。プロセス名「007曲げ加工」の詳細設定から下図のように設定します。
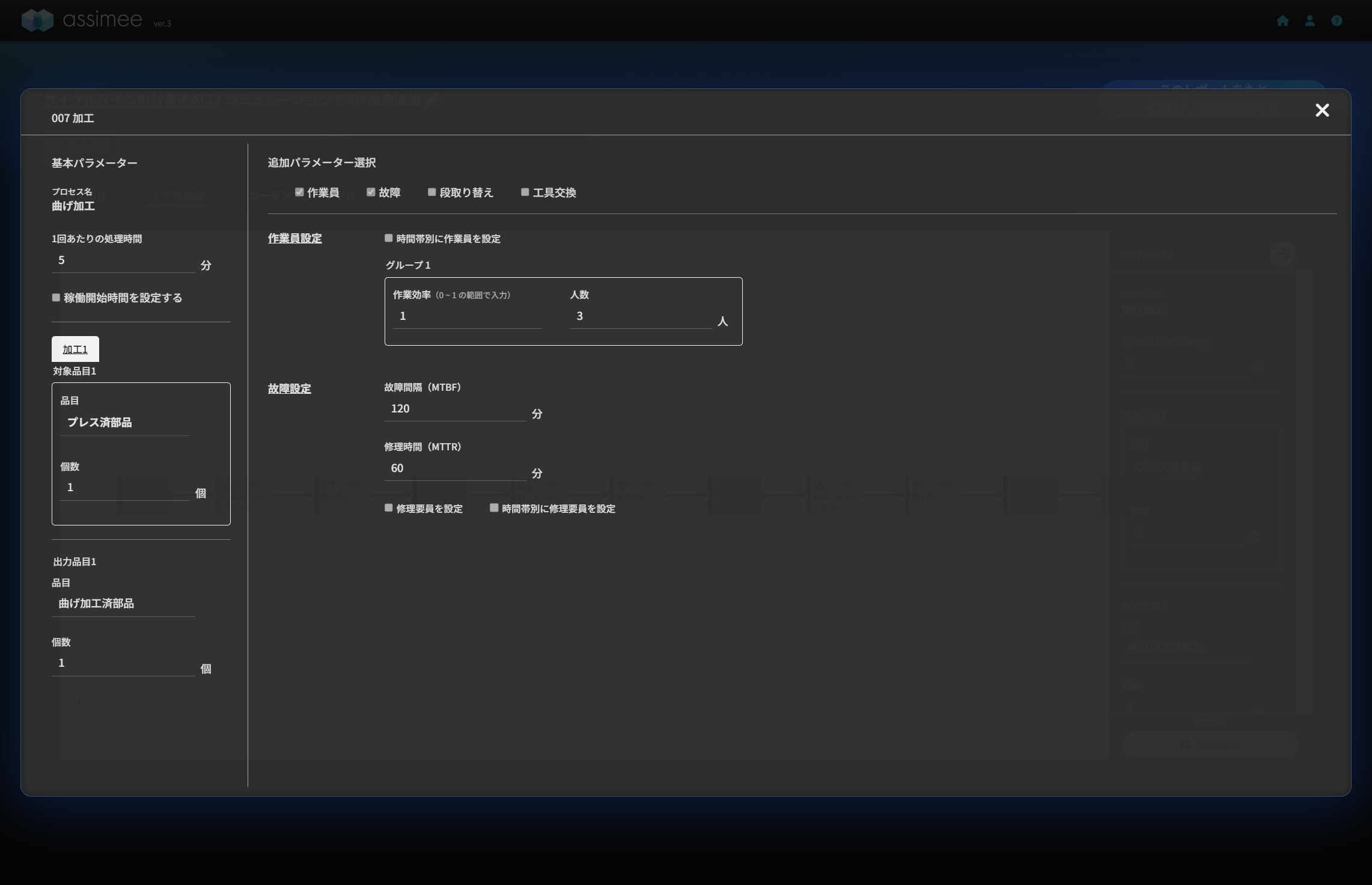
修理時間を「60分」、故障時間を「120分」と設定します。この設定をすることで、「007曲げ加工」の設備稼働から120分後に故障が発生し、60分で修理が行われます。この結果、シミュレーション結果は以下の通りとなりました。
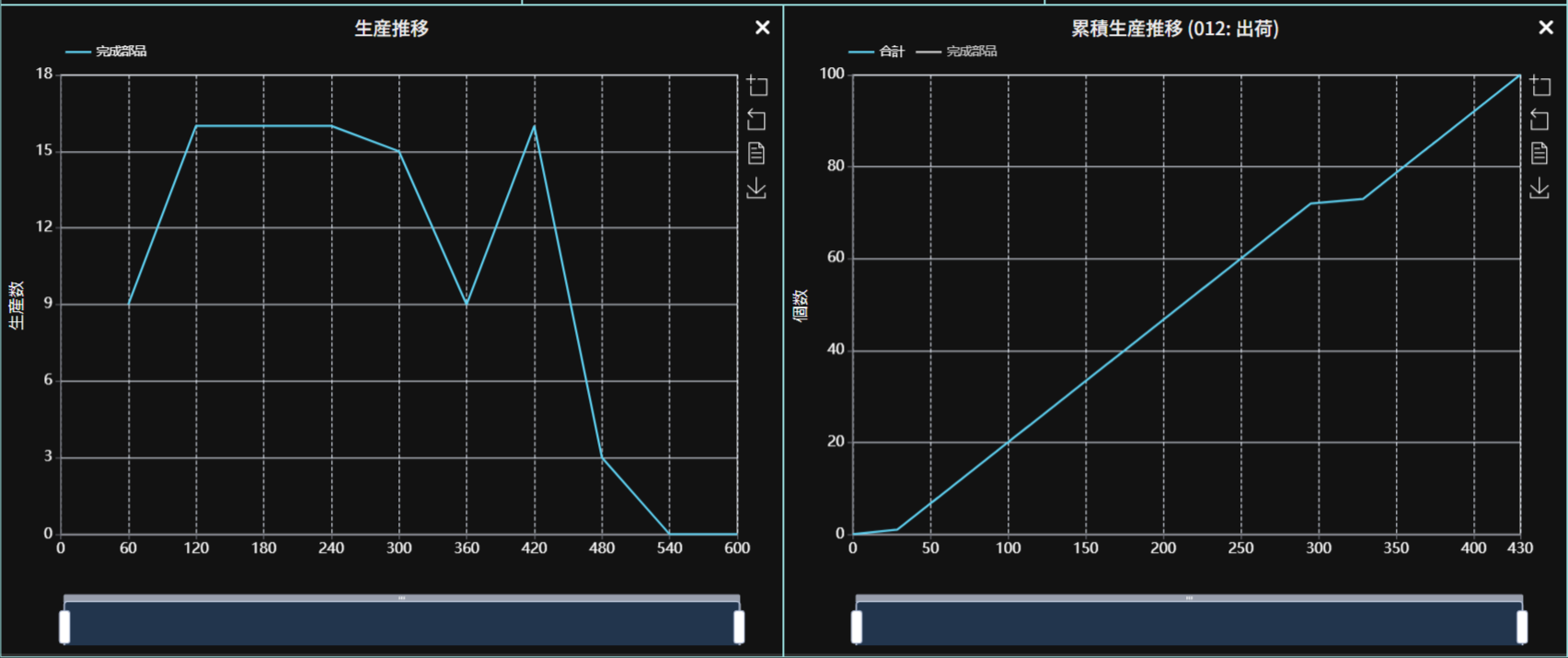
故障とその修理を追加したモデルでは製品を100個生産するのにかかる時間は430分と長くなりました。よって、1個当たりの平均製造時間(サイクルタイム)は4.30分となります。故障の修理に60分掛かりましたが、生産の停止は30分で済みました。これはなぜでしょうか。
「009置き場C」のアイテム数と「007曲げ加工」、「010プレス加工B」の累積加工推移を確認してみます。
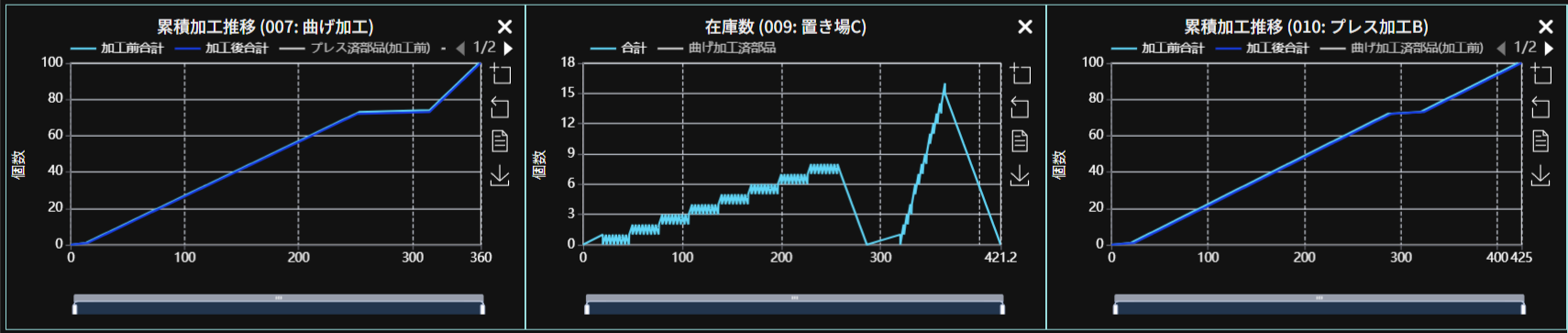
図のように、「007曲げ加工」と「010プレス加工B」の加工時間の違いから、「曲げ加工済部品」の在庫が「009置場C」にできていたことと、この在庫で作業ができる時間があったため「010プレス加工B」がストップする時間が故障復旧のための時間よりも30分短くなっていることが分かります。
*「007曲げ加工」のグラフの傾きが故障修理後に急になっているのは、故障前は稼働率に余裕があったことを示しています。
このように、生産ラインの設定や構成を変えたい時や、アクシデントの生産ラインへの影響を見積もりたい時などに直接ラインで測定しなくても、容易に計算することができます。
*今回は変更していませんが、設備の立ち上げ時間や段取り替えの時間、工具交換の時間などをシミュレーションに設定することも可能です。
まとめ
今回の記事ではassimeeのシミュレーションを使って生産ラインのサイクルタイムを計算する方法について解説しました。1度モデルを作っておくことで、生産ラインの設定の変更やアクシデントの想定など、様々なシナリオを想定したサイクルタイムの計算をPC上で行うことが出来ます。これにより、生産ラインの設定を実際に変更した上でサイクルタイムを測定することは難しいため、担当者の経験や勘に頼った対応を行っていた、これまでの管理業務の改善に繋がります。
assimeeでは、実際の製造プロセスをモデル化し、シミュレーションすることで、プロセスの見える化や潜在的な課題の洗い出しを行うことができます。製造プロセスのデジタル化や課題解決でお悩みの方は、ぜひお問い合わせください。