概要
今回の記事ではassimeeでCO2排出量を計算する方法について解説します。assimeeではプロセスが使う電力や熱、燃料(Scope1やScope2)、部品や製品の輸送(Scope1やScope3)、従業員の通勤時(Scope3)のCO2排出量を計算することが可能となっていますが、今回はプロセスが利用する電力や使用する燃料によるCO2排出量(全温室効果ガスをCO2換算した排出量、以下CO2排出量)を計算します。
モデルの作成
今回、排出量を計算するだけでなく、排出量の多いプロセスを特定出来るように、今回は3本の生産ラインをもつ小規模な工場を想定し、入荷→置き場→分岐→生産ライン(置き場→組立→運搬)→合流→置き場→運搬→出荷のプロセスでモデルを構成します。
加えて、生産ラインの間に導入年度の違いを仮定して意図的に性能の差をつけることで、計算したCO2排出量がどう変わるのかをシミュレートで明らかにします。実際の生産ラインを再現したモデルに対してassimeeの排出量計算機能を使うことで、生産ラインや物流における各プロセスの環境に対する影響を評価することや排出量の多いプロセスの特定が可能となります。
下図が今回用意するモデルとなります。

モデル作成画面から以下のようにプロセスを配置しますが、今回は、3つの生産ラインの内、1つが旧式で電力消費が多く、処理時間が長いという仮定で設定を行います。
STEP1 プロセス図の作成
入荷プロセス:
特に変更なし
置き場プロセス:
プロセス名を「到着品置き場」へ変更
運搬(搬送機)プロセス:
特に変更なし
分岐プロセス:
特に変更なし
上ルート
置き場プロセス:
プロセス名を「ライン1置き場」へ変更
組立プロセス:
プロセス名を「ライン1組立」へ変更
運搬(人)プロセス:
プロセス名を「ライン1運搬(人)」へ変更
中ルート
置き場プロセス:
プロセス名を「ライン2置き場」へ変更
組立プロセス:
プロセス名を「ライン2組立」へ変更
運搬(人)プロセス:
プロセス名を「ライン2運搬(人)」へ変更
下ルート
置き場プロセス:
プロセス名を「ライン3置き場」へ変更
組立プロセス:
プロセス名を「ライン3組立」へ変更
運搬(人)プロセス:
プロセス名を「ライン3運搬(人)」へ変更
合流後
置き場プロセス:
プロセス名を「製品置き場」へ変更
運搬(搬送機)プロセス:
特に変更なし
出荷プロセス:
特に変更なし
STEP2 パラメーターの設定
001入荷:
詳細設定から部品を2つ設定、
1つ目:品目を「部品A」、間隔を「10分」、個数を「10個」と設定
2つ目:品目を「部品B」、間隔を「10分」、個数を「20個」と設定
002到着品置き場:
置き場容量を「1000個」と設定
003運搬(搬送機):
最大積載量を「10個」、人数を「10人」、処理時間を「1分」と設定
004分岐:
1回あたりの処理時間を「1分」、作業人数を「10人」と設定、
分岐先として「005ライン1置き場」(上)、「011ライン2置き場」(中)、「014ライン3置き場」(下)の3ルートを設定、
分岐条件は初期設定のまま変更しない(接続先へランダムに振り分けが行われます)
上ルート
005ライン1置き場:
置き場容量を「1000個」と設定
006ライン1組立:
1回あたりの処理時間を「10分」、人数を「10人」と設定、
対象品目を2つ設定、
1つ目:「部品A」、個数を「1個」、
2つ目:「部品B」、個数を「2個」、
出力品目を「製品」、個数を「1個」と設定
007ライン1運搬(人):
最大積載量を「10個」、人数を「10人」、処理時間を「1分」と設定
中ルート(組立プロセスは古い機械を使っている想定で、処理時間を他の2ルートの2倍の20分とします)
011ライン2置き場:
置き場容量を「1000個」と設定
012ライン2組立:
1回あたりの処理時間を「20分」、人数を「10人」と設定、
対象品目を2つ設定、
1つ目:「部品A」、個数を「1個」、
2つ目:「部品B」、個数を「2個」、
出力品目を「製品」、個数を「1個」と設定
013ライン2運搬(人):
最大積載量を「10個」、人数を「10人」、処理時間を「1分」と設定
下ルート(組立プロセスは上ルートと同等の設定です)
014ライン3置き場:
置き場容量を「1000個」と設定
015ライン3組立:
1回あたりの処理時間を「10分」、人数を「10人」と設定、
対象品目を2つ設定、
1つ目:「部品A」、個数を「1個」、
2つ目:「部品B」、個数を「2個」、
出力品目を「製品」、個数を「1個」と設定
016ライン3運搬(人):
最大積載量を「10個」、人数を「10人」、処理時間を「1分」と設定
合流後
008製品置き場
置き場容量を「1000個」と設定
009運搬(搬送機):
最大積載量を「10個」、人数を「10人」、処理時間を「1分」と設定
010出荷:
特に変更なし
シミュレーション結果
以上の設定を行ったら、シミュレーション時間を300分に設定して、シミュレーションを行います。上記の設定が問題なく行われていれば、下図のような結果が表示されます。分岐にランダム変数が使用されているため、シミュレーション結果は必ずしも一致しません。
*ここで設定したシミュレーション時間が排出量の計算でも利用されます。
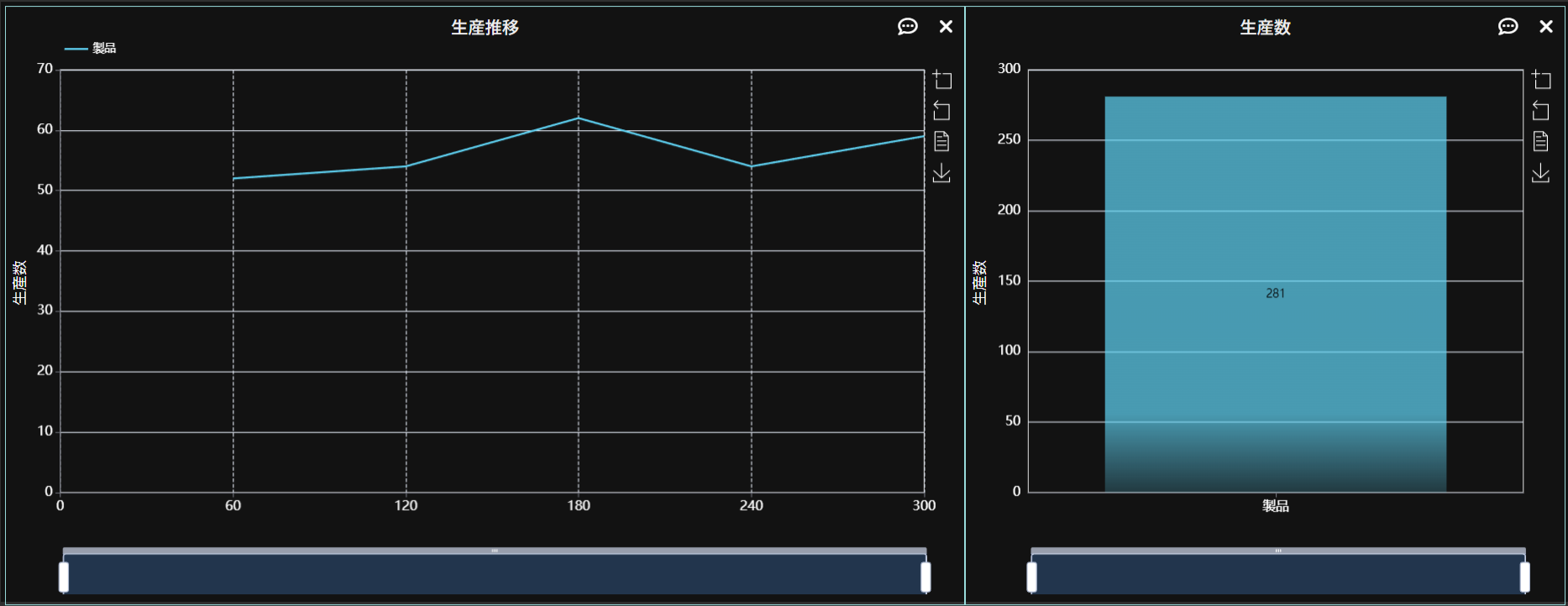
排出量の計算
シミュレーションの実行後に、ダッシュボードにある「カーボンニュートラル」タブをクリックすると計算画面が立ち上がります。
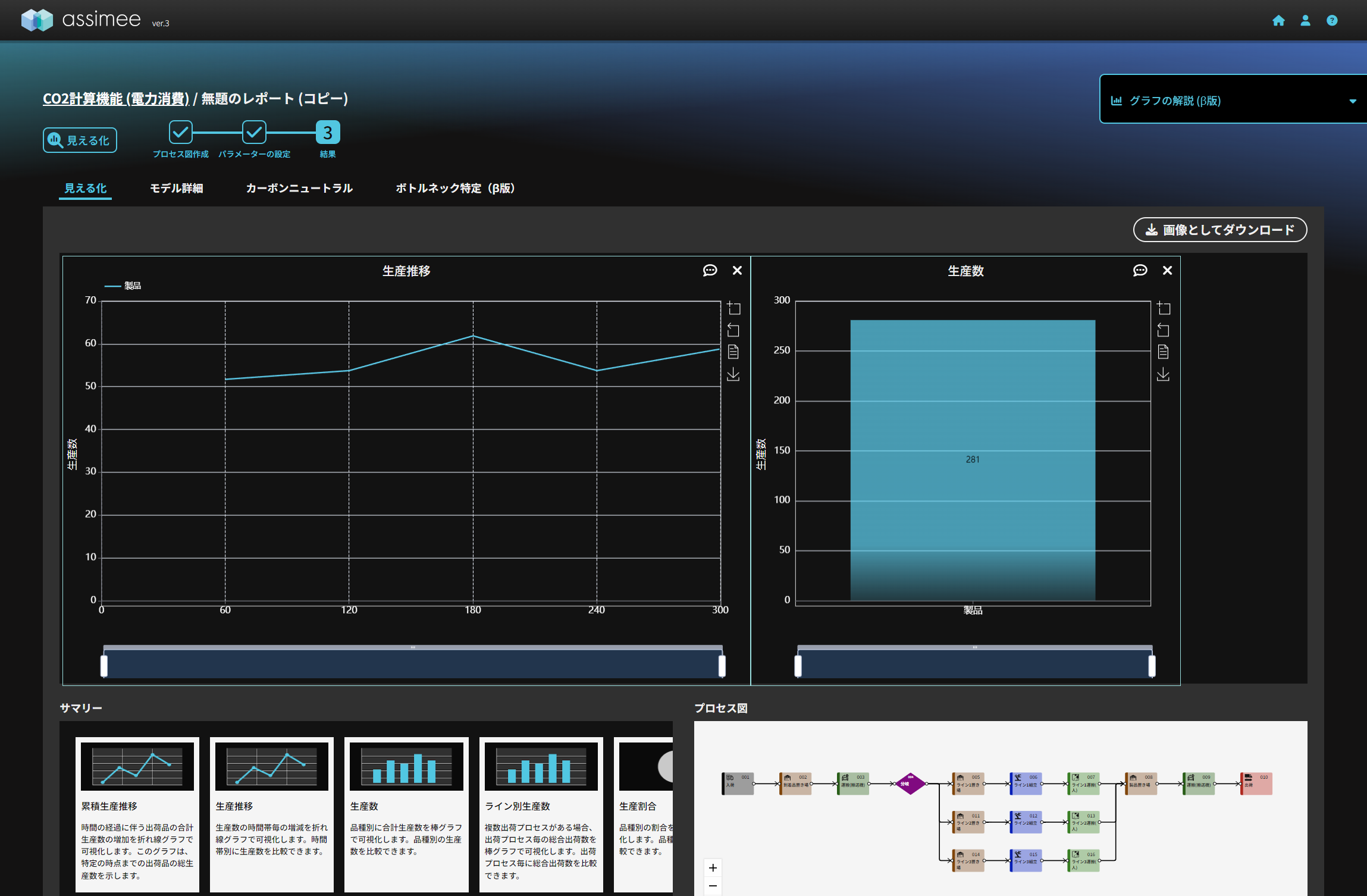
ここで、自家発電(Scope1)と購入電力(Scope2)の割合などを設定します。今回は購入電力を75%、自家発電を25%と設定し、自家発電には太陽光発電を選択しました。自家発電のCO2係数は、環境省が提供する太陽光発電の排出量係数の標準値である0.001「t/kWh」などを入力してください。太陽光発電以外の選択肢としては、火力(発電機)、風力、水力などがドロップダウンメニューから選択できます。
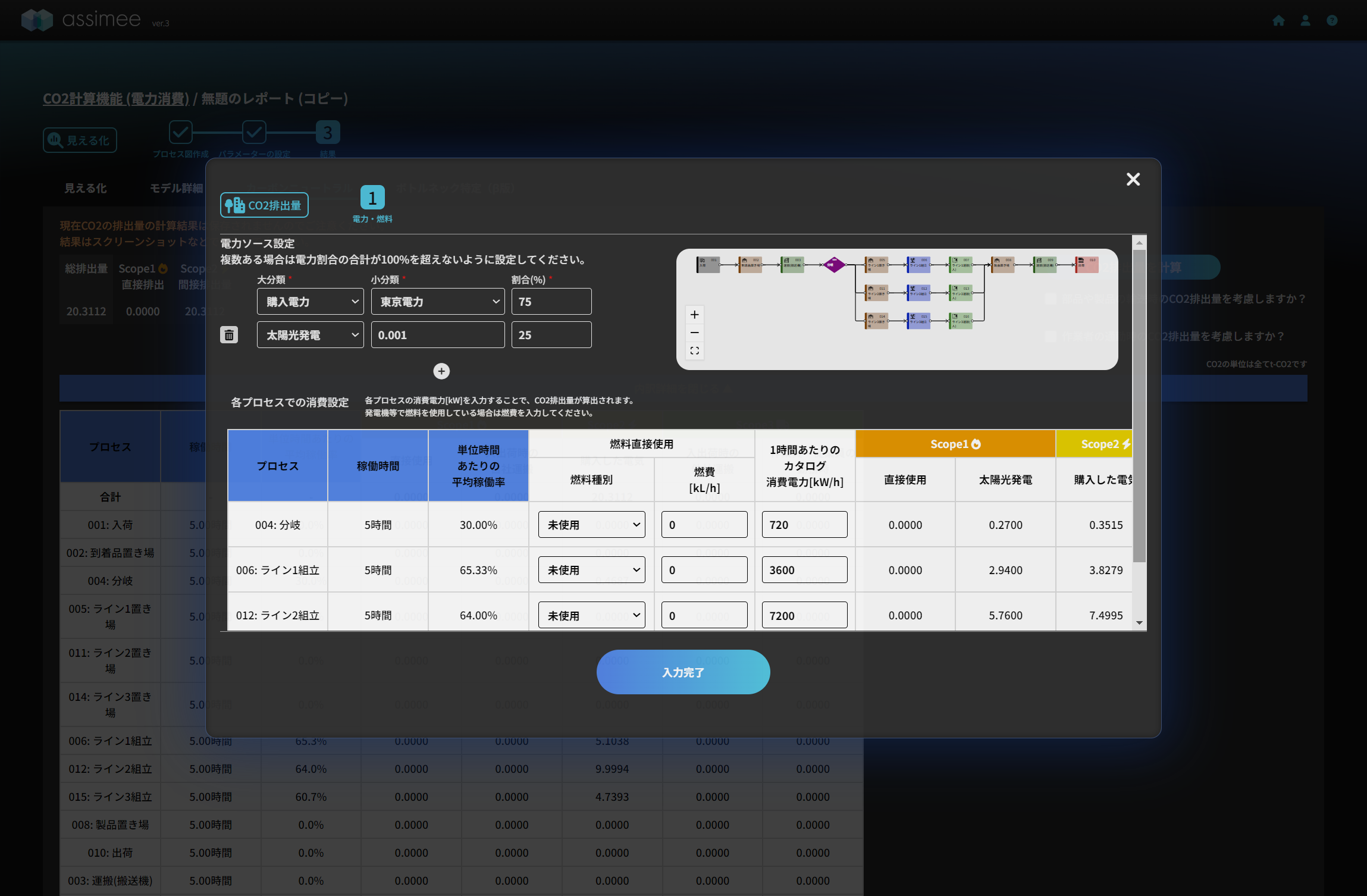
「Scope1,2のCO2排出量」ボタンを押すと下図の表が表示されます。ここで、各プロセスで使用する1時間当たりの消費電力を設定します。今回は以下のような数字としました。「012ライン2組立」は他の「006ライン1組立」や「015ライン3組立」より効率が悪くなるように消費電力も2倍の値を入力しています。
- 「004分岐」:720kW/h(200W使用を想定)
- 「006ライン1組立」:3600kW/h(1000W使用を想定)
- 「012ライン2組立」:7200kW/h(2000W使用を想定)
- 「015ライン3組立」:3600kW/h(1000W使用を想定)
下図のように燃料の直接使用(Scope1)や今回設定した1時間当たりの消費電力を入力すると、稼働率を勘案して計算が行われます。この画面では小計が表示され、「入力完了」を押すとCO2の排出量がダッシュボードに表示されます。
*チェックボックにチェックを入れることで、電力以外のScope1の排出量(自社のトラックによる輸送や構内の輸送車両の燃料消費によるCO2の排出量)を計算することが可能です。
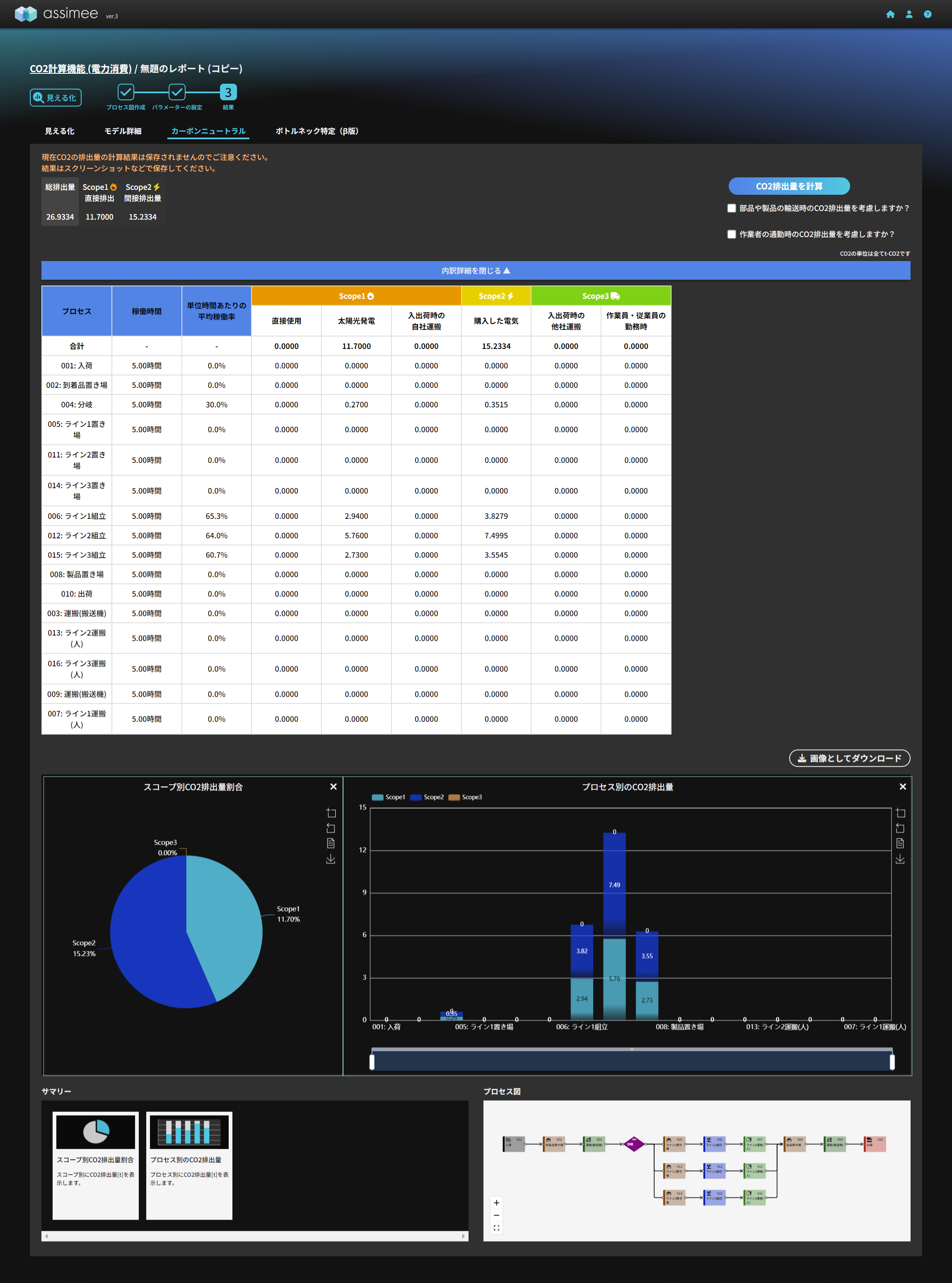
図中の表を見ると、分岐プロセスの排出量が比較的低い一方で、組立用の機械が旧式で電力消費が多く、処理時間が長い「012ライン2組立」のCO2排出量が約13トンとなり、他の「006ライン1組立」や「015ライン3組立」と比較して約6トン多いことがわかりました。今回モデルとした工場のケースでは、「012ライン2組立」を含むラインの排出量を他のラインと同等になるように調整することで、総排出量を約6トン削減することが可能であることが示唆されています。
また、ダッシュボードにグラフを表示させることもできます。上図の下段のようにスコープ別CO2排出量割合やプロセス毎の排出量のグラフを表示できます。
まとめ
今回はassimeeに実装された排出量計算方法の内、Scope1とScope2の電力消費によるCO2の排出量を計算しました。このように排出量をプロセス毎に計算する事で、何処のプロセスのCO2排出量が多く、何処のプロセスを改善すべきなのかが、一目瞭然となります。CO2排出量を計算することは、環境に対する影響を評価し、持続可能性の向上に向けた取り組みの一環として重要です。assimeeの計算結果を使うことで、環境への貢献を促進するための戦略を開発することができます。
assimeeでは、実際の製造プロセスをモデル化し、シミュレーションすることで、プロセスの見える化や潜在的な課題の洗い出しを行うことができます。製造プロセスのデジタル化や課題解決でお悩みの方は、ぜひお問い合わせください。