概要
今回の記事では、従事する作業員の数が増えるほど生産能力が向上するラインを想定します。これは、食品工場での加工作業やピッキング作業など、作業員の人数に生産量が比例するケースを想定しています。また、ラインで働く作業員は出荷指示に基づいて異なる作業を行い、作業指示に応じて作業場所も異なる状況を想定します。たとえば、製造業では作業指示によってセルやジョブショップの場所が変わる場合、倉庫ではピッキング内容によってピッキングする棚が異なる場合などに相当します。
これまでの記事で、人の数を最適化するには加工などのプロセスに属する作業員数を選択して最適化を行っていました。今回作るモデルでは作業員は部品と共にプロセス間を移動し、加工や検品を行う想定です。このように特定のプロセスに作業員が固定されない時でも人の数の最適化を行うことができます。今回の記事ではその方法を解説していきます。
モデル
今回のモデルは以下の通りです。
入荷した材料は最上段を流れ、3本の生産ラインが存在します。各加工プロセスでは、材料、作業員、生産指示が揃った場合に生産が行われます。作業員は初期仕掛けとして待機場所に配置され、モデル内をループすることで、作業員数の増加に伴って生産量が増える工場の動きを再現します。

シミュレーションと最適化
モデルを作成したら、シミュレーションを実行します。シミュレーション時間は300分とし、初期仕掛けとして10人の作業員を配置してシミュレーションを行った結果、以下のような結果が得られました。
※なお、今回のモデルには出荷指示など複数のランダム要素が含まれているため、結果が完全に一致しない点にご注意ください。
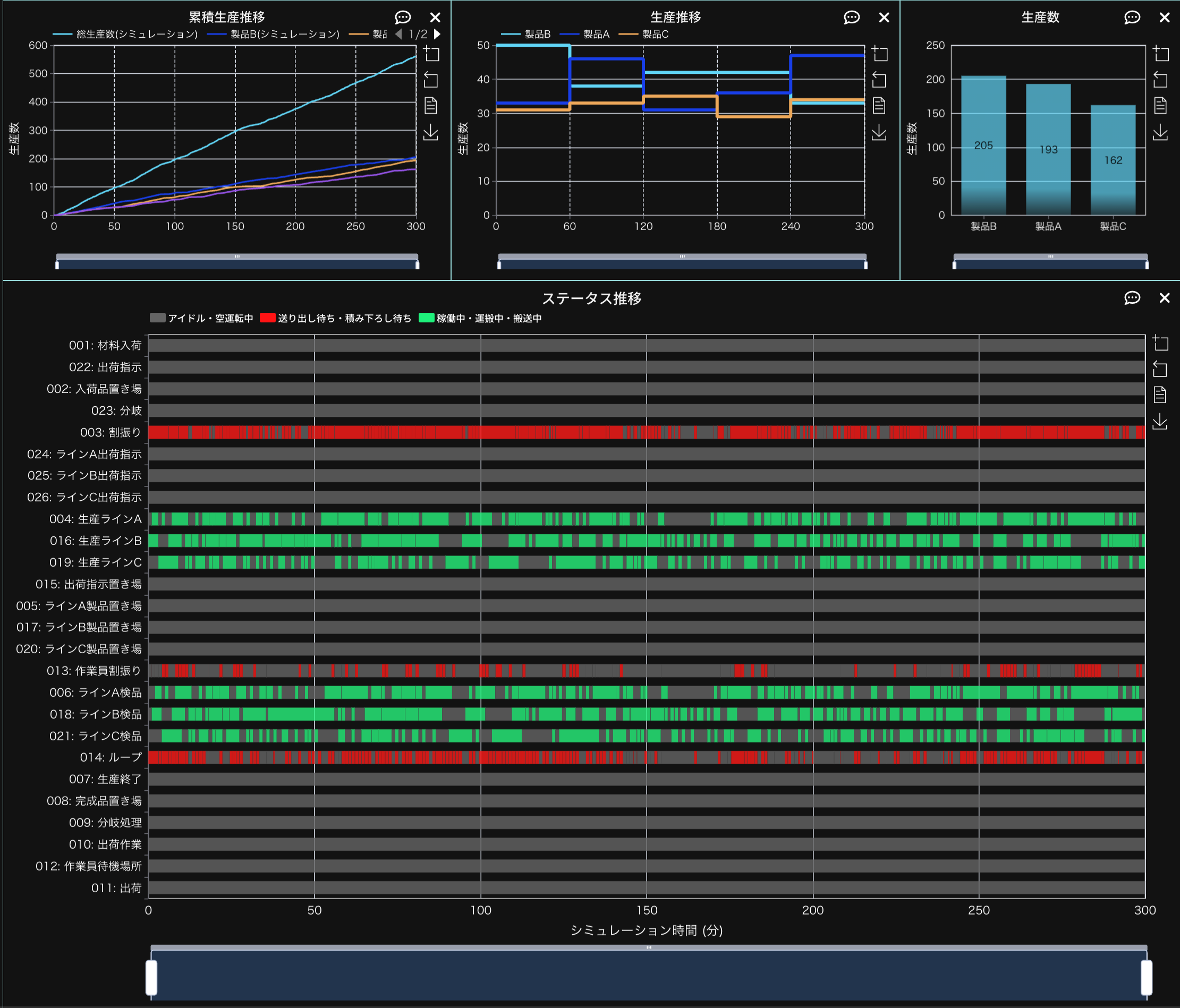
次に、最適化を実行してみましょう。今回の最適化対象は「012作業員待機場所」に配置する初期仕掛けの作業員数です。これによりパラメーター推定を使ってプロセス内を移動する作業員数の最適化を行うことができます。ここで、生産目標は、1時間あたり製品A、製品B、製品Cをそれぞれ50個と設定します。この条件で最適化を進めます。
最適化の結果は以下のようになります。
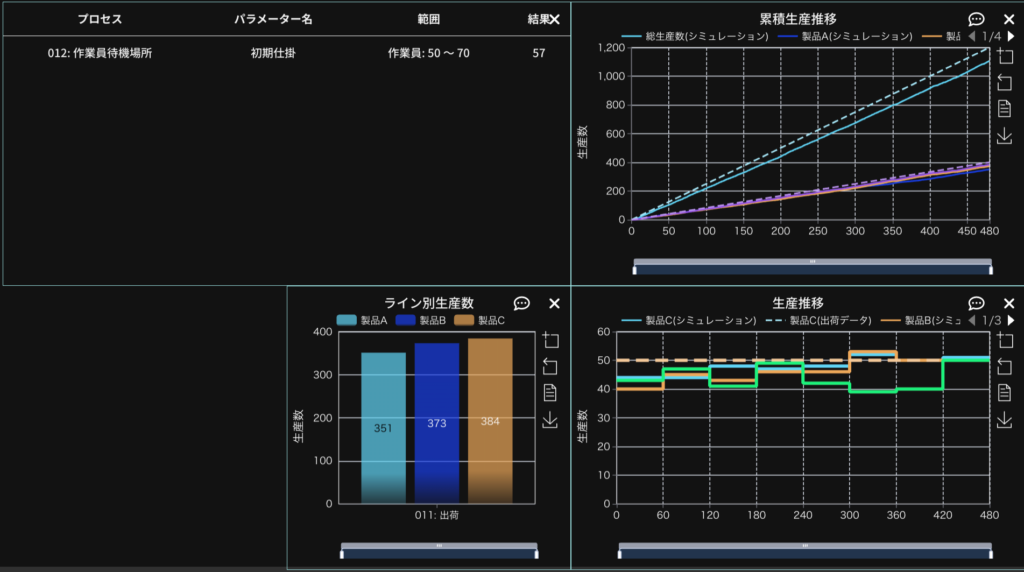
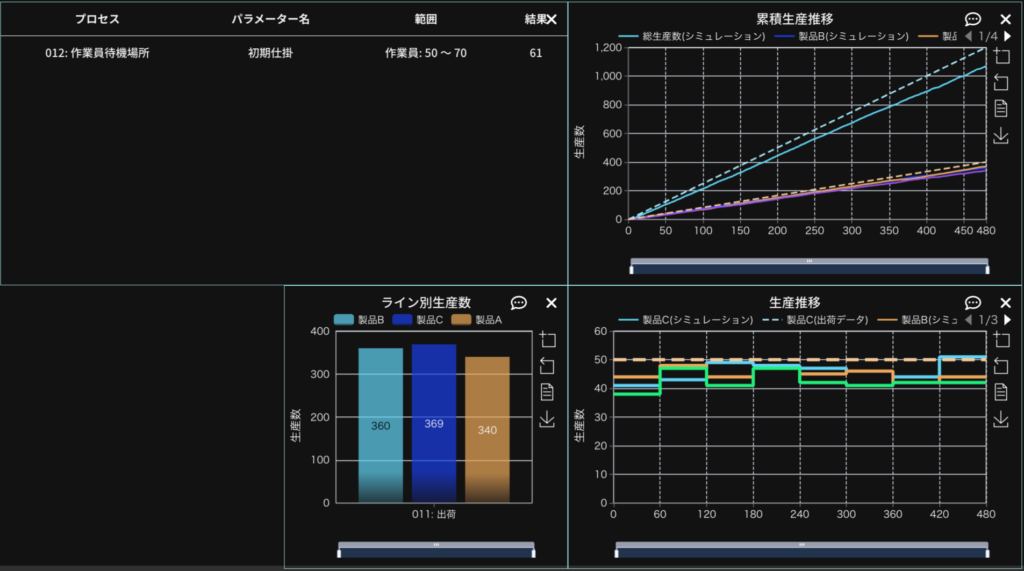
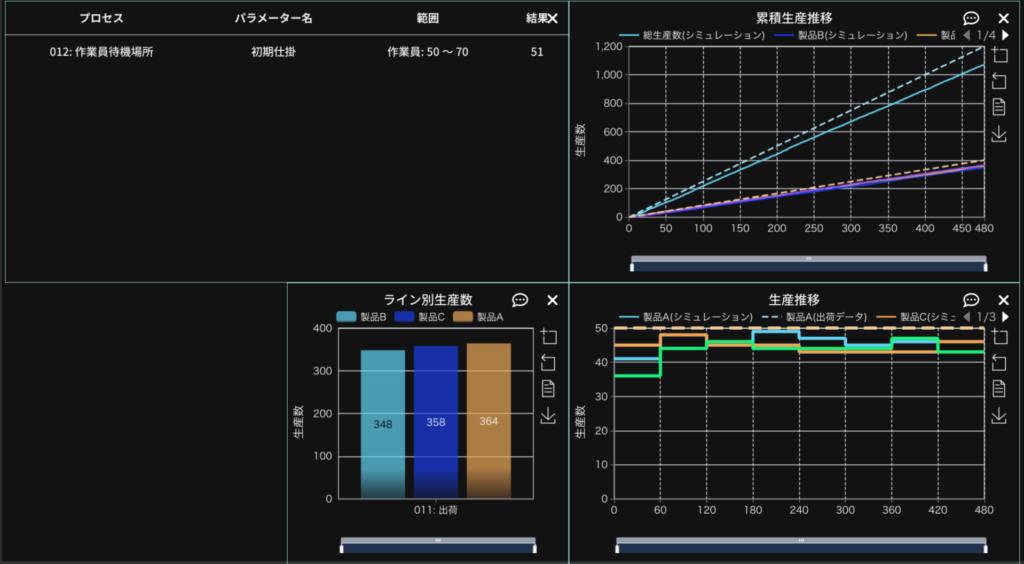
最も誤差の小さい最適化結果は、作業員数が57人のときであり、生産目標をほぼ達成できることがわかりました。一方、作業員数が51人や61人の場合でも、生産量に大きな変動は見られませんでした。これは、生産指示の割り振りなどにランダム変数が使用されており、生産量にランダムな振れ幅が生じるためと考えられます。
このように厳密な解が求められない場合、振れ幅の吸収方法は在庫水準の設定と同様に経営判断によるものです。しかし、assimeeを使用すれば、この振れ幅をより正確に見積もることが可能となります。
また、作業人数を10人から50人以上と倍以上に増やしたにも関わらず、生産量が比例して5倍になっていないこともわかります。これは工程にボトルネックが存在することを示唆しています。次回の記事ではボトルネックを探索し、より生産効率の高いモデルが作れるか検証してみます。
まとめ
この記事では、共通の作業員が完全に異なるプロセスで作業を行う場合の最適化手法について解説しました。今回のモデルのように、人や情報を材料と同じように扱い、プロセス間を移動するように設定することも可能です。このような使い方をすることで、assimeeを用いたシミュレーションや最適化の幅を広げることが可能です。
assimeeでは、実際の製造プロセスをモデル化し、シミュレーションすることで、プロセスの見える化や潜在的な課題の洗い出しを行うことができます。製造プロセスのデジタル化や課題解決でお悩みの方は、ぜひお問い合わせください。